Have you ever wondered why some molded parts come out perfectly while others seem flawed? The secret often lies in the clamping force applied during the process!
Clamping force is the maximum force applied by the injection molding machine to keep the mold closed during injection, preventing plastic melt overflow and ensuring product integrity.
While this explanation provides a foundational understanding, exploring the detailed mechanics and implications of clamping force can significantly enhance your molding operations. Read on to discover how optimizing clamping force can prevent defects and improve efficiency.
Clamping force prevents mold defects in injection molding.True
Clamping force keeps the mold closed, preventing defects like flash.
What Are the Key Components of Clamping Force?
Understanding clamping force’s components is vital for optimizing injection molding processes.
Key components of clamping force include the projected area of the plastic product, plastic melt pressure, and mold structure. These elements collectively determine the force required to keep the mold closed during injection, ensuring product quality and preventing defects.
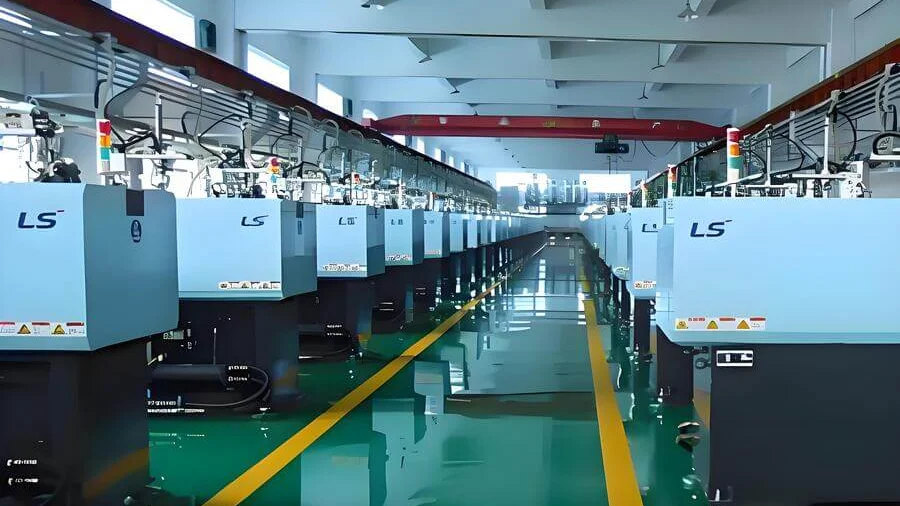
The Role of Projected Area
The projected area of a plastic product is crucial in determining the necessary clamping force. This area is essentially the shadow or silhouette of the part when viewed from above. A larger projected area requires a greater clamping force to counteract the expansion forces during injection molding. Calculating this area accurately ensures that the mold remains tightly sealed, preventing defects like flash and burrs.
Impact of Plastic Melt Pressure
Plastic melt pressure is another key factor influencing clamping force. Higher injection pressures increase the expansion force within the mold, necessitating a corresponding increase in clamping force. Properly balancing these pressures helps maintain the dimensional accuracy of the molded part. For more insights on adjusting melt pressures, consider exploring injection molding pressure adjustments1.
Mold Structure Considerations
The structure of the mold itself, including its complexity and the configuration of parting surfaces, significantly affects clamping force requirements. Complex molds with intricate designs may have multiple parting lines, each needing adequate clamping to prevent leakage. Understanding your mold’s design intricacies is essential for setting the correct clamping parameters.
Calculating Clamping Force
The calculation method for clamping force is straightforward yet critical:
Parameter | Description |
---|---|
Formula | Clamping force (kN) = Projected area (cm²) × Pressure (MPa) ÷ 1000 |
Safety Factor | Include a safety margin based on empirical data |
This formula highlights how both the projected area and melt pressure directly influence the required force. A detailed guide on clamping force calculation2 can provide deeper understanding.
By mastering these components, manufacturers can prevent product defects, enhance efficiency, and extend mold life.
Larger projected areas require more clamping force.True
A larger projected area increases expansion forces needing more clamping.
Mold structure complexity doesn't affect clamping force.False
Complex molds need more clamping to prevent leakage at parting lines.
How Do You Calculate Clamping Force Accurately?
Accurate clamping force calculation is vital for maintaining the quality and precision of injection molded parts.
Calculate clamping force using: Clamping Force (kN) = Projected Area (cm²) × Melt Pressure (MPa) ÷ 1000, adding a safety factor for optimal results.
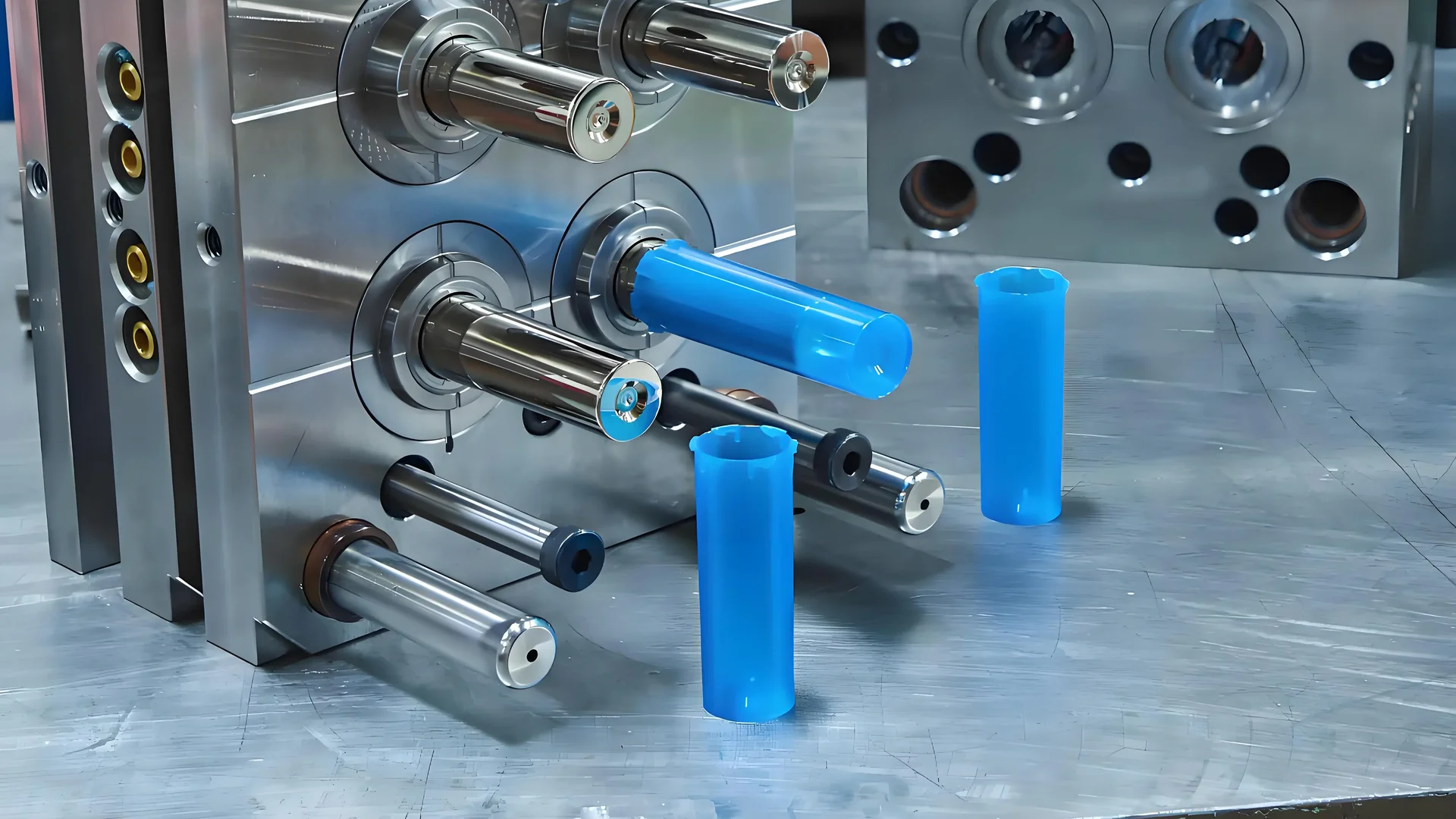
Understanding the Basics of Clamping Force Calculation
In the realm of injection molding3, clamping force is indispensable. It’s defined as the maximum force that the clamping mechanism can exert to keep the mold securely closed during the injection process. This ensures that the molten plastic does not leak, preserving the integrity of the part.
The Formula for Clamping Force
The fundamental formula for calculating clamping force is:
Clamping Force (kN) = Projected Area (cm²) × Melt Pressure (MPa) ÷ 1000
This formula highlights two key variables:
- Projected Area of the Plastic Product: Larger areas require more force to maintain closure.
- Melt Pressure: Higher pressures increase the force needed to prevent mold expansion.
Factors Influencing Clamping Force Calculation
-
Projected Area: The larger the projected area, the more substantial the clamping force required. This is due to increased surface exposure to the expansion forces of the molten plastic.
-
Melt Pressure: As injection pressure rises, so does the force exerted on the mold’s parting surface. Calculating accurately requires precise measurements of these pressures.
-
Mold Structure: Complex molds with intricate designs may require adjustments in the clamping force to ensure even distribution across varying surfaces.
Importance of Safety Factors
In practical applications, incorporating a safety factor into your calculations is crucial. This factor compensates for potential variances in material behavior and ensures that minor fluctuations in processing conditions do not lead to defects or mold damage.
Example Calculation
Consider a scenario where the projected area is 200 cm², and the melt pressure is 80 MPa:
Clamping Force= 200 × 80 ÷ 1000 = 16kN
Adding a safety factor might adjust this to approximately 18 kN to accommodate unforeseen circumstances.
Conclusion: Maximizing Molding Efficiency
Understanding and accurately calculating clamping force not only safeguards against defects such as flash and burrs but also optimizes energy consumption and prolongs mold lifespan. By leveraging precise calculations and appropriate safety factors, manufacturers can achieve superior product quality and operational efficiency.
Clamping force is calculated using projected area and melt pressure.True
The formula for clamping force involves projected area and melt pressure.
Safety factors are unnecessary in clamping force calculations.False
Safety factors account for variances in material behavior and conditions.
What Common Defects Result from Incorrect Clamping Force?
Incorrect clamping force in injection molding can lead to a range of defects affecting product quality and mold integrity.
Common defects from incorrect clamping force include flash, burrs, warping, incomplete filling, and sink marks. These arise when the force is either too high or too low, disrupting the molding process. Correctly adjusting clamping force is crucial to maintaining product precision and reducing production waste.
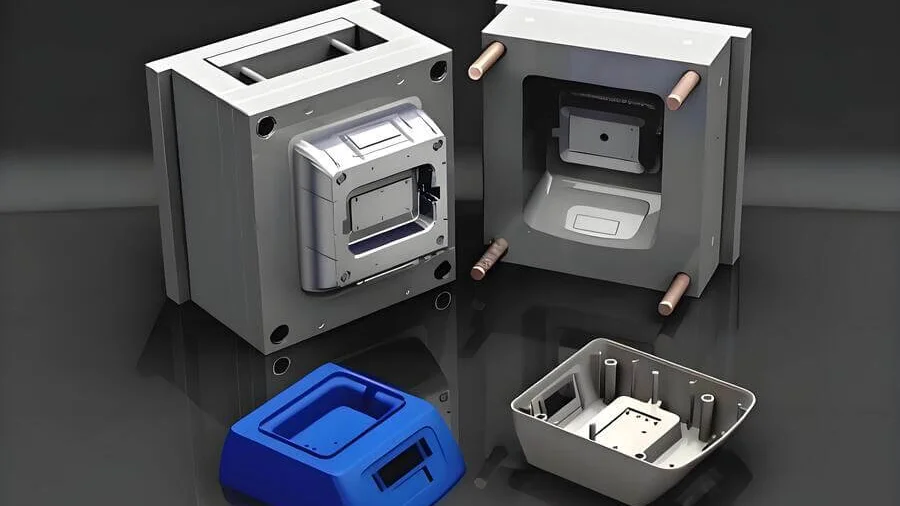
The Role of Clamping Force in Injection Molding
In injection molding, the clamping force4 is essential for ensuring that the mold halves remain tightly closed during the injection process. Insufficient or excessive clamping force can directly impact the quality of the molded parts.
Common Defects from Incorrect Clamping Force
-
Flash and Burrs:
- Insufficient Clamping Force: When the clamping force is too low, the pressure from the injected plastic can cause the mold to slightly open, resulting in excess material around the edges known as flash.
- Impact: Flash not only affects the aesthetic appeal but also requires additional trimming processes, increasing production time and cost.
-
Warping and Deformation:
- Excessive Clamping Force: Applying too much force can compress the mold beyond its optimal state, causing stress on the material as it cools.
- Impact: This may lead to warping or deformation, where parts do not hold their intended shape or dimensions.
-
Incomplete Filling:
- Insufficient Clamping Force: A lack of sufficient force can also cause issues with filling the mold completely, leading to incomplete parts.
- Impact: This defect necessitates a re-mold, wasting materials and time.
-
Sink Marks:
- Excessive Clamping Force: Over-clamping can sometimes lead to sink marks, where the surface of the part appears indented due to uneven cooling.
- Impact: Sink marks compromise structural integrity and surface quality.
Factors Influencing Clamping Force Selection
-
Projected Area and Melt Pressure: The size of the part and injection pressure heavily influence how much clamping force is necessary. An increase in either requires an adjustment in force to prevent defects.
-
Mold Design and Material: Complex mold designs and different materials can alter how clamping force needs to be applied. Ensuring that the mold design accommodates the pressure without compromising integrity is key.
Practical Tips for Adjusting Clamping Force
-
Conduct Regular Testing: Regularly test your molds with different clamping forces to find the optimal setting for each product type.
-
Use Safety Factors: Factor in a safety margin beyond calculated requirements to account for variations in material behavior and machine performance.
By understanding and correctly applying clamping force, manufacturers can significantly reduce defects and improve overall production efficiency.
Flash occurs with excessive clamping force.False
Flash occurs when clamping force is too low, not excessive.
Sink marks result from excessive clamping force.True
Over-clamping can cause uneven cooling, leading to sink marks.
Why Is Optimizing Clamping Force Crucial for Product Quality?
Optimizing clamping force is essential for maintaining high product quality in injection molding.
Optimizing clamping force in injection molding is vital to prevent defects like flash, ensure precise product dimensions, and reduce energy consumption, thereby enhancing the overall quality of the molded products.
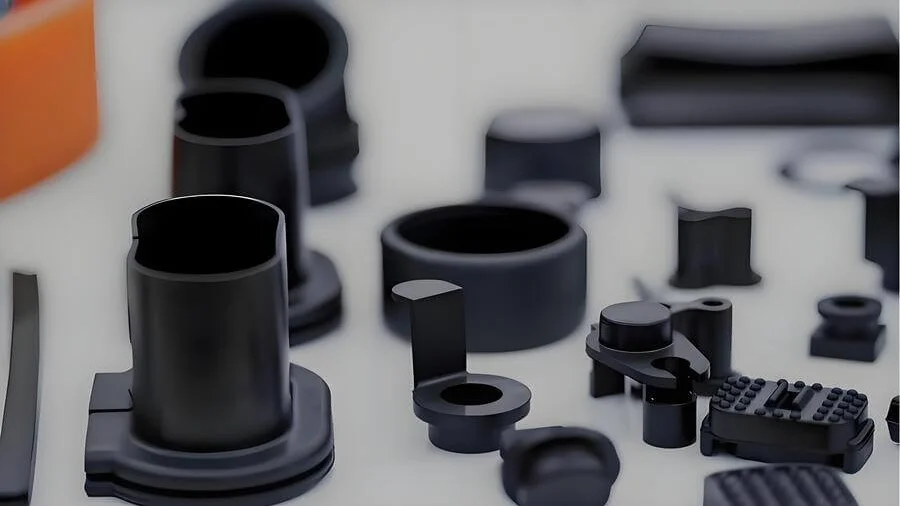
Understanding the Role of Clamping Force in Injection Molding
Clamping force in injection molding refers to the maximum pressure applied to keep the mold halves closed during the injection process. This force is crucial in preventing the plastic melt from leaking through the mold’s parting lines, which can cause defects such as flash and burrs.
The importance of clamping force5 cannot be overstated, as it ensures that the expansion force from the plastic melt is countered effectively, maintaining both dimensional accuracy and surface quality.
Factors Affecting Clamping Force Requirements
Several factors influence the necessary clamping force:
- Projected Area of the Product: Larger projected areas require greater clamping force to prevent mold opening.
- Plastic Melt Pressure: Higher melt pressures necessitate increased clamping force.
- Mold Structure: Complex molds with intricate parting lines might need customized clamping force adjustments.
These factors must be carefully calculated and adjusted for each specific molding operation to maintain product integrity.
Calculating Optimal Clamping Force
The formula for calculating clamping force is:
Clamping Force (kN) = Projected Area (cm²) × Plastic Melt Pressure (MPa) ÷ 1000
This equation provides a baseline, but manufacturers often include a safety factor to accommodate variations in material behavior or unexpected process deviations.
Parameter | Impact on Clamping Force |
---|---|
Projected Area | Directly proportional |
Plastic Melt Pressure | Directly proportional |
Mold Complexity | Varies with structure |
Consequences of Incorrect Clamping Force
Insufficient clamping force can lead to mold opening during injection, causing flash and compromising product dimensions. Conversely, excessive force can increase energy consumption and accelerate mold wear, negatively affecting the internal structure of plastic products.
Properly optimizing clamping force ensures not only better product quality but also enhances efficiency by minimizing waste and reducing operational costs.
By understanding these nuances, manufacturers can fine-tune their operations to balance precision and efficiency effectively. For more details on achieving this balance, see our guide on calculating clamping force accurately6.
Clamping force prevents flash in injection molding.True
Clamping force ensures mold halves stay closed, preventing flash defects.
Excessive clamping force reduces energy consumption.False
Excessive clamping force increases energy use and mold wear.
Conclusion
Mastering clamping force not only ensures product quality but also enhances efficiency and reduces waste. Embrace these insights for optimal results!
-
Learn methods for balancing melt pressure to optimize product quality.: This video goes over how to set the injection pressure on an injection molding press. This is … ↩
-
Explore detailed calculations for accurate clamping force settings.: A simple formula to calculate clamping force is cavity pressure (material injection pressure in kg/cm2) multiplied by the total projection area(cm2). ↩
-
Learn how injection molding shapes various plastic products efficiently.: injectionmolding Learn everything you need to know about injection molding in this video. We … ↩
-
Learn about clamping force basics and its importance in molding.: Clamping force is the force (lbs or kg) needed to hold the mold together during injection and it is applied by the clamping unit of an injection molding machine … ↩
-
Explore how clamping force impacts overall product quality in molding.: Clamping force is the force (lbs or kg) needed to hold the mold together during injection and it is applied by the clamping unit of an injection molding machine … ↩
-
Learn detailed steps for calculating precise clamping force.: Understanding Complex Clamping Force Calculations · The sum of forces in the x direction must equal zero · The sum of forces in the y direction must equal zero … ↩