When designing plastic parts for injection molding, one of the critical aspects to consider is the selection of B side features1. These features, located on the non-visible side of the part, play a vital role in the functionality and assembly of the final product. However, they can also complicate the manufacturing process if not chosen carefully. This guide will walk you through the key factors to consider when selecting B side features, ensuring your design is both functional and cost-effective.
B side features, such as screw bosses2, ribs, and undercuts, are essential for the structural integrity and assembly of plastic parts but can increase mold complexity3 and production costs if not properly designed.
Understanding how to balance functionality, manufacturability, and cost is crucial for any designer or engineer working with injection molded parts. This article will delve into the types of B side features, the factors influencing their selection, their impact on the molding process, and their applications across various industries.
B side features are only necessary for complex assemblies.False
Even simple parts may require B side features like ribs for structural support or bosses for mounting.
Properly designed B side features can reduce overall production costs.True
By optimizing features for manufacturability, you can minimize mold complexity and reduce cycle times.
- 1. What are Plastic B Side Features?
- 2. What are the Common Types of B Side Features?
- 3. What Factors Should You Consider When Choosing B Side Features?
- 4. How Do B Side Features Impact the Injection Molding Process?
- 5. What are the Applications of B Side Features?
- 6. What are the Differences Between B Side and A Side Features?
- 7. Conclusion
What are Plastic B Side Features?
In injection molding, the mold consists of two halves: the A side and the B side. The A side typically forms the visible or cosmetic surface of the part, while the B side forms the non-visible or functional surface. B side features are design elements incorporated into the B side of the part, such as screw bosses, ribs, dog houses, and undercuts. These features are crucial for:
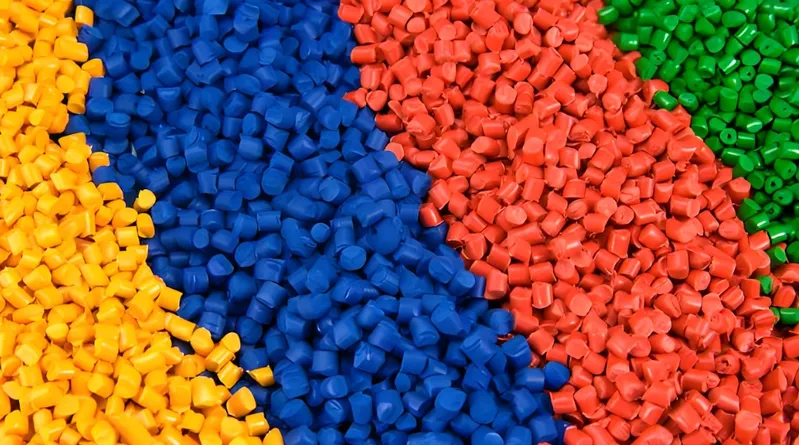
-
Structural Integrity: Ribs and gussets provide additional strength without adding significant weight.
-
Assembly: Screw bosses and snap fits enable easy fastening and joining of components.
-
Functionality: Features like clips, hinges, and mounting points add utility to the part.
However, B side features can also introduce challenges in the molding process, such as increased mold complexity, longer cycle times, and potential defects like sink marks or warpage. Therefore, selecting the right B side features requires careful consideration of various factors.
B side features are always hidden in the final product.False
While typically non-visible, some B side features may be partially exposed depending on the part's design and application.
What are the Common Types of B Side Features?
Several types of B side features are commonly used in plastic part design:
- Screw Bosses: Raised cylindrical features that provide a mounting point for screws or other fasteners. They must be designed with appropriate wall thickness and draft angles to ensure strength and ease of molding.
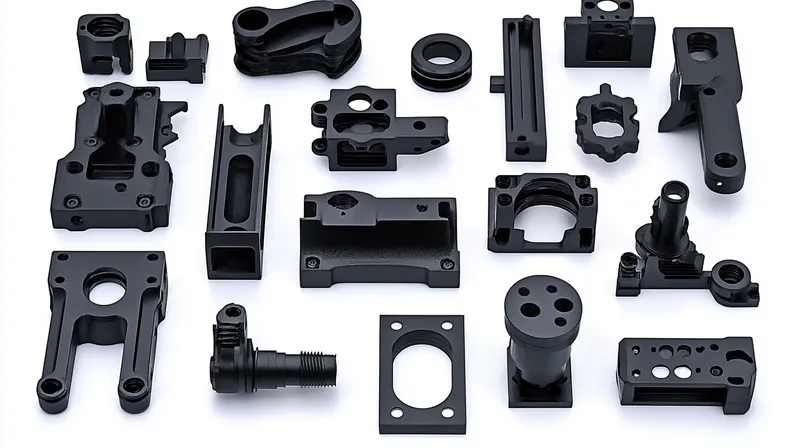
-
Ribs4: Thin, vertical walls that add structural support to the part. Proper design is crucial to avoid sink marks on the A side.
-
Dog Houses: Protrusions that house or secure other components, often used in automotive and consumer electronics.
-
Undercuts: Features that prevent the part from being ejected directly from the mold, requiring side actions or other mold mechanisms.
-
Snap Fits5: Flexible features that allow parts to be snapped together without additional fasteners.
Each of these features serves a specific purpose and must be designed with consideration for the molding process.
Feature Type | Purpose | Key Design Considerations |
---|---|---|
Screw Boss | Fastening | Wall thickness, draft angle, height |
Rib | Structural support | Height-to-thickness ratio, spacing |
Dog House | Component housing | Size, shape, alignment |
Undercut | Snap fits, clips | Mold complexity, side actions |
Snap Fit | Assembly without fasteners | Flexibility, engagement depth |
This table provides a quick overview of the most common B side features and the factors to consider when designing them.
All B side features require complex mold designs.False
Simple features like ribs or bosses can often be accommodated with standard mold designs, while undercuts and snap fits may require additional mechanisms.
What Factors Should You Consider When Choosing B Side Features?
Selecting the right B side features involves balancing several factors to ensure the part meets functional requirements while remaining cost-effective to produce. The primary factors to consider are:
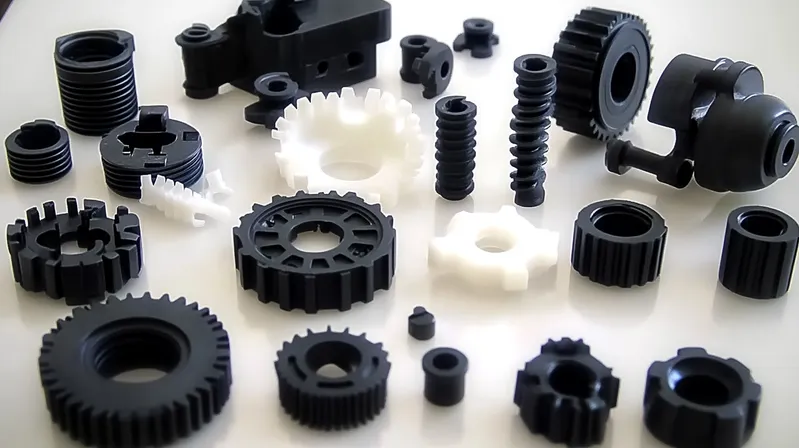
- Material Properties6
The choice of plastic material significantly impacts the performance of B side features. Key properties to consider include:- Tensile Strength: Ensures features like screw bosses can withstand fastening forces.
- Shrinkage: Affects dimensional accuracy, especially for features with tight tolerances.
- Thermal Resistance: Important for parts exposed to heat, as it prevents deformation.
For example, ABS is a common choice for its balance of strength and cost, while polycarbonate offers higher impact resistance for demanding applications.
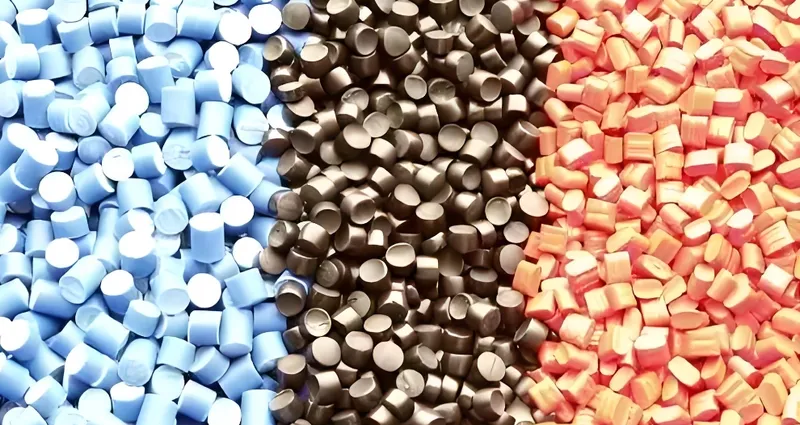
-
Structural Integrity7
B side features must be designed to withstand mechanical stresses without causing defects. For instance:- Ribs should have a height-to-thickness ratio that prevents sink marks on the A side.
- Screw Bosses need sufficient wall thickness to avoid cracking under load.
Proper design ensures the part remains durable throughout its lifecycle.
-
Manufacturability
The complexity of B side features directly affects the mold design and production process. Considerations include:- Draft Angles: Features should have draft angles of 1°–3° to facilitate ejection from the mold.
- Undercuts: Require side actions or sliding shutoffs, increasing mold costs.
Simplifying features where possible can reduce production expenses and lead times.
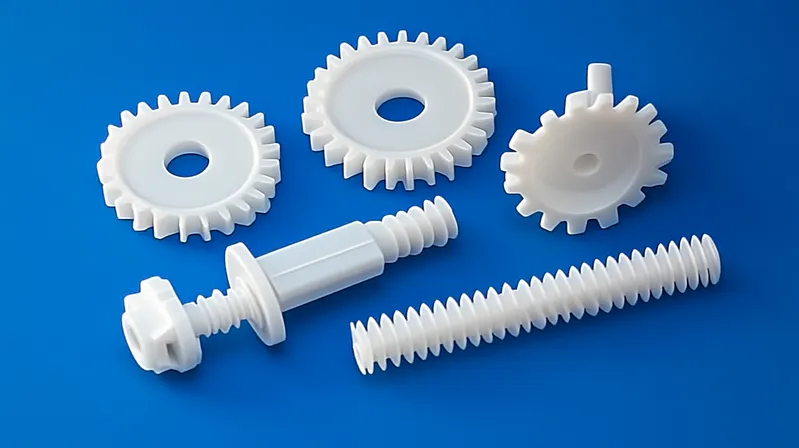
- Cost Efficiency8
Balancing functionality with cost is essential. Strategies to minimize costs include:- Material Selection: Choosing cost-effective plastics that meet performance requirements.
- Feature Optimization: Reducing the number and complexity of B side features to lower mold and production costs.
A "Design to Cost" approach helps maintain financial viability without compromising quality.
Material selection is the most critical factor in B side feature design.False
While important, material selection must be balanced with structural integrity, manufacturability, and cost considerations.
Simplifying B side features always leads to better manufacturability.True
Reducing complexity minimizes mold costs and production challenges, though some features are necessary for functionality.
How Do B Side Features Impact the Injection Molding Process?
B side features can significantly influence the injection molding process in several ways:
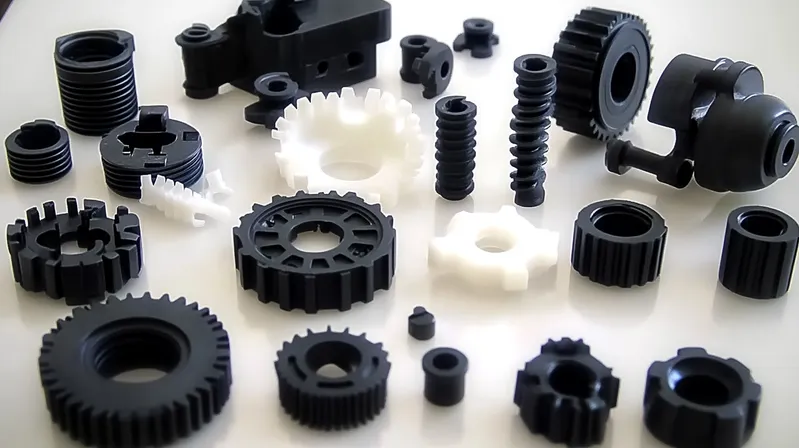
-
Mold Design: Features like undercuts require additional mold components, such as side-action cams or sliding shutoffs, increasing complexity and cost.
-
Cycle Time: Complex features may require longer cooling times or additional steps, slowing down production.
-
Defect Risks: Poorly designed features can lead to defects like warpage, sink marks, short shotor, incomplete filling.
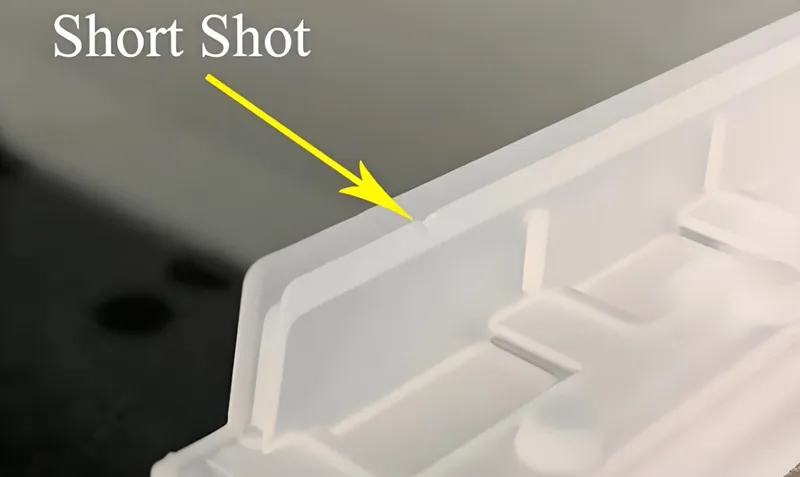
To mitigate these impacts, designers should:
-
Optimize Feature Geometry: Use appropriate draft angles and avoid sharp corners.
-
Simulate the Process: Use mold flow analysis software to predict and address potential issues.
-
Collaborate with Manufacturers: Work closely with mold makers and production teams to ensure designs are feasible.
By considering these factors early in the design phase, you can streamline the manufacturing process and reduce the risk of costly redesigns.
B side features always increase cycle times in injection molding.False
Well-designed features can be molded efficiently, while poorly designed ones may indeed slow down production.
What are the Applications of B Side Features?
B side features are utilized across various industries to enhance product functionality and assembly:
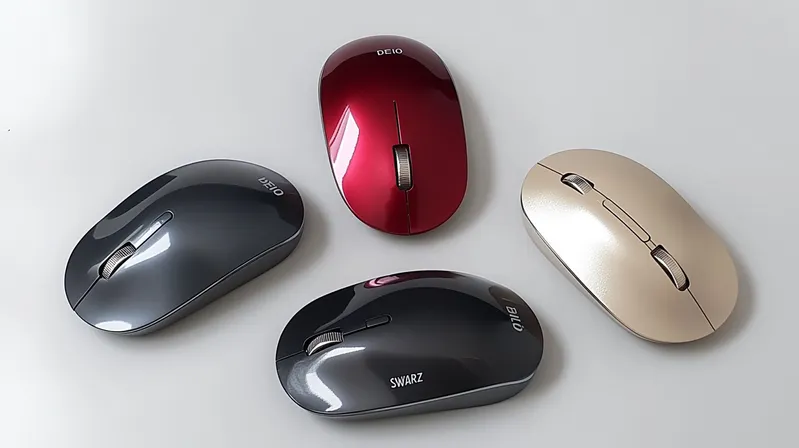
-
Automotive: Mounting points, structural reinforcements, and clips are common in dashboards, consoles, and interior panels.
-
Consumer Goods: Handles, hinges, and snap fits in appliances and toys improve usability and reduce assembly time.
-
Electronics: Component housings, thermal management features, and EMI shielding protect and support internal components.
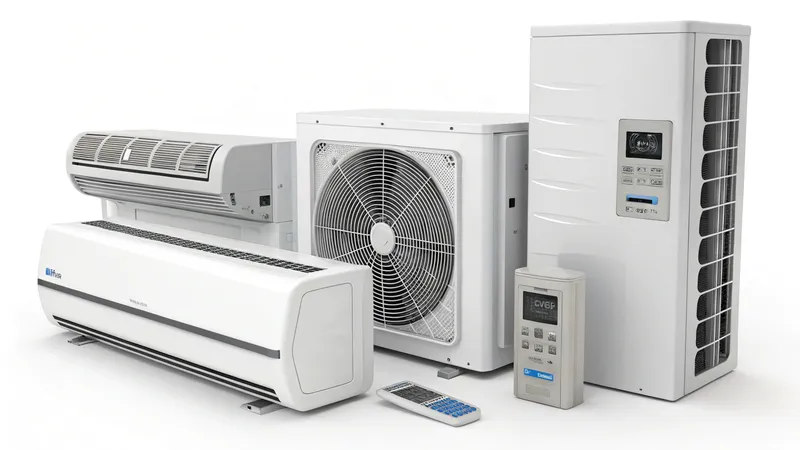
In each case, B side features enable complex assemblies and add value to the final product without compromising aesthetics.
B side features are only used in high-volume production.False
While common in mass production, B side features are also used in low-volume applications where functionality is critical.
What are the Differences Between B Side and A Side Features?
In injection molding, A side and B side features serve different purposes:
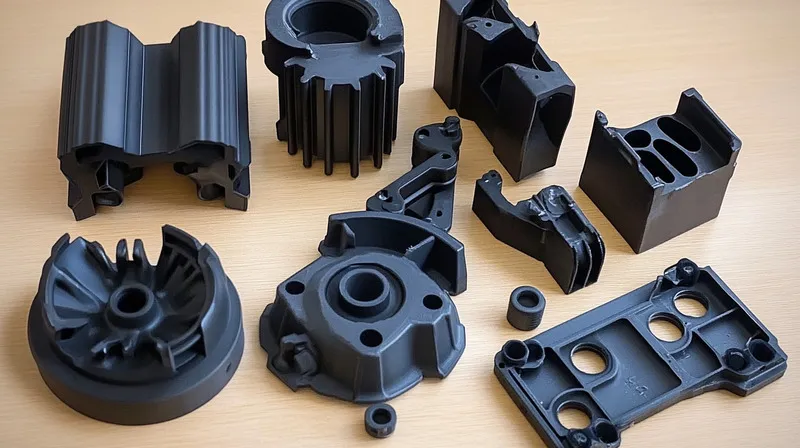
-
A Side Features: Typically the visible or cosmetic surface, focusing on aesthetics and surface finish.
-
B Side Features: The non-visible side, emphasizing functionality, structural support, and assembly features.
While A side features are designed for appearance, B side features are engineered for performance. However, both must be considered together to ensure the part meets all requirements.
A side features are always more complex than B side features.False
Complexity depends on the design; B side features can be more intricate due to functional requirements.
Conclusion
Choosing the right plastic B side features is a critical step in designing injection molded parts9. By understanding the types of features available, the factors influencing their selection, and their impact on the manufacturing process, you can create designs that are both functional and cost-effective. Whether you’re working in automotive, consumer goods, or electronics, mastering B side feature design will enhance your products and streamline production.
Remember to collaborate with your manufacturing partners and use simulation tools10 to validate your designs. With careful planning, you can leverage B side features to add value to your products without unnecessary complexity.
-
Explore this link to gain a deeper understanding of B side features and their importance in injection molding design. ↩
-
Learn about screw bosses and how they contribute to the structural integrity of molded parts by visiting this resource. ↩
-
Understanding mold complexity is key to optimizing production; check this link for insights on managing it effectively. ↩
-
Ribs are crucial for maintaining the integrity of plastic parts. Discover best practices for rib design to avoid common pitfalls. ↩
-
Snap fits can simplify assembly and reduce costs. Learn more about their benefits and design tips to optimize your projects. ↩
-
Understanding material properties is crucial for selecting the right plastics that ensure durability and performance in B side features. ↩
-
Exploring structural integrity helps in designing B side features that withstand mechanical stresses, ensuring long-lasting performance. ↩
-
Learning about cost efficiency strategies can help manufacturers balance quality and expenses, leading to better financial outcomes. ↩
-
Exploring the design process of injection molded parts can provide insights into best practices and innovative techniques. ↩
-
Using the right simulation tools can significantly improve your design accuracy and efficiency in injection molding. ↩