Molding high-impact resistant materials feels like an intricate dance of precision and patience.
Molding high-impact resistant materials involves challenges like selecting suitable materials, designing appropriate molds, and preventing defects such as warping and sink marks, all crucial for product durability and successful manufacturing.
While these challenges seem straightforward, each brings its own set of hurdles. Selecting the right material often feels like a game of chess, where one wrong move could mean the difference between a sturdy product and a brittle failure. Designing molds that can handle these materials requires not just technical skill but also a bit of artistry—it’s about finding that sweet spot where function meets form. And then there are the defects like warping and sink marks, which can feel like unwelcome guests at an otherwise flawless party. But each obstacle is also an opportunity to learn, adapt, and innovate in ways that make future designs even better.
Selecting the right material is the main challenge.True
Choosing materials that meet strength and flexibility needs is crucial.
Sink marks are not a concern in high-impact molding.False
Sink marks are common defects that affect surface finish quality.
- 1. How Does Material Selection Impact Molding Processes?
- 2. What are the common mold design issues with high-impact materials?
- 3. How Can You Prevent Defects in Injection Molding?
- 4. How Does Temperature Influence Molding High-Impact Materials?
- 5. How Can You Optimize Cooling Time for Better Molded Products?
- 6. What Are the Best Practices for Quality Control in Molding?
- 7. Conclusion
How Does Material Selection Impact Molding Processes?
Have you ever wondered how choosing the right material could make or break your molding project?
Material selection in molding impacts product attributes like strength and durability and influences processing efficiency, quality, and costs, as each material requires unique conditions.
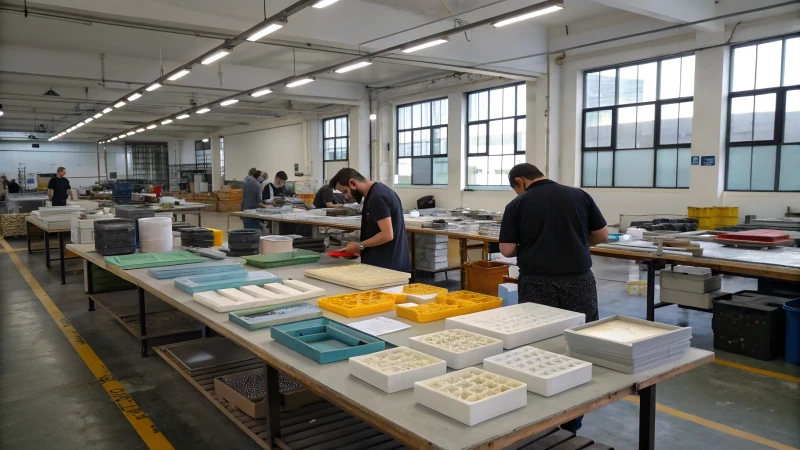
I remember the first time I had to choose a material for a new project. It was a whirlwind of options and specifications. But then, I realized that the material you choose isn’t just about ticking boxes—it’s about shaping the future of your product.
Material Properties and Their Influence
Think of material properties like thermal stability, viscosity, and shrinkage as the unsung heroes in molding. For instance, when working with thermoplastics, I always have to adjust temperature settings meticulously. It’s like setting the perfect oven temperature for a cake—get it wrong, and it can affect everything from cycle times to energy use. Understanding these properties ensures optimal processing conditions1 and high-quality outputs.
Comparing Material Types
Material | Strength | Flexibility | Durability | Cost |
---|---|---|---|---|
Polypropylene | Moderate | High | Moderate | Low |
ABS | High | Moderate | High | Medium |
Nylon | High | Low | High | High |
Every time I weigh my options between polypropylene, ABS, and nylon, it’s like choosing the right tool for the job. Each has its perks depending on what the final product needs to do and the budget I’m working with.
Impact on Molding Efficiency
Material choice can be a game-changer for cycle times and mold longevity. In my experience, high-viscosity materials often extend cooling times, which in turn affects how fast we can get things moving on the production line. Picking the right material is crucial for keeping operational costs2 in check by minimizing downtime.
Design Considerations
When it comes to mold design, knowing how a material behaves under stress is like understanding how a character reacts in a story. Some materials expand or shrink unexpectedly, and if you’re not prepared, it can throw off your mold dimensions and final product accuracy. So I make sure to incorporate proper design adjustments3 to account for these quirks.
Environmental Considerations
With the world going green, I’ve noticed a rise in interest around eco-friendly materials. Using biodegradable plastics not only helps in reducing our environmental footprint but also meets strict regulatory standards. Opting for sustainable materials can significantly boost brand reputation while aligning with environmental policies4.
Thermoplastics require specific temperature settings.True
Thermoplastics' thermal properties necessitate controlled temperatures for optimal molding.
Polypropylene is more costly than nylon.False
Polypropylene is low cost, while nylon is high, as per the material table.
What are the common mold design issues with high-impact materials?
Ever found yourself wrestling with mold design issues, especially when dealing with high-impact materials? You’re definitely not alone!
Common mold design issues with high-impact materials include warping, shrinkage, flow problems, and poor surface finish, which can be addressed through optimizing temperature control, material selection, and mold design parameters.
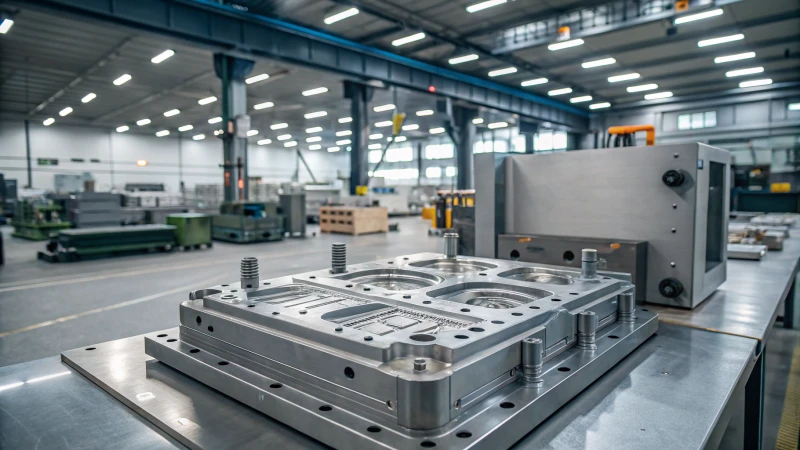
I remember the first time I faced a mold design challenge with high-impact materials. It felt like trying to solve a Rubik’s cube blindfolded—frustrating and seemingly impossible! But over time, I learned that understanding these issues was like finding the map to buried treasure, leading to better designs and smoother production.
Warping and Shrinkage
Warping—it’s like watching your perfect soufflé collapse in the oven. This happens when uneven cooling causes distortion. To combat this, I ensure uniform temperature control5 across the mold. Then there’s shrinkage, which sneaks in due to incorrect material choices or not enough packing pressure, leaving my designs slightly off-kilter.
Issue | Cause | Solution |
---|---|---|
Warping | Uneven cooling | Uniform temperature control |
Shrinkage | Incorrect material selection | Optimal material choice |
Material Flow Problems
High-impact materials are like that stubborn friend who refuses to go with the flow. If not managed properly, they can cause incomplete filling or pesky air traps. I’ve found that adjusting gate location and size can really help manage these flow issues6.
- Gate Location: A strategic spot minimizes flow resistance.
- Gate Size: Adjust it based on how viscous the material is.
Poor Surface Finish
Imagine spending hours on a sculpture only for the finish to be as rough as sandpaper. High-impact materials can leave surfaces looking less than stellar due to poor mold surface quality or cooling mishaps. Regular maintenance and design tweaks are my go-to strategies for improving surface finish7.
Mold Wear and Tear
These materials can be like that favorite pair of jeans that wear out too fast. They are abrasive, leading to mold wear. Choosing durable materials for mold construction and sticking to a regular maintenance schedule keeps things in check.
I’m always on the lookout for the latest innovations in mold technology. Keeping up-to-date with industry standards helps me overcome these challenges and continuously improve my designs. Exploring resources on latest mold technologies8 is part of my strategy to stay ahead in the game.
Uneven cooling leads to warping in molds.True
Warping occurs due to uneven cooling, which distorts the mold.
Incorrect gate size improves material flow.False
Incorrect gate size can hinder flow, causing incomplete filling.
How Can You Prevent Defects in Injection Molding?
Ever faced the frustration of injection molding defects? I sure have. Let me share some insights on how to prevent these issues and ensure your production line runs smoothly.
Prevent defects in injection molding by optimizing design, choosing appropriate materials, adjusting process parameters, maintaining mold temperature, ensuring venting, and using consistent materials. Regular maintenance and monitoring are essential.
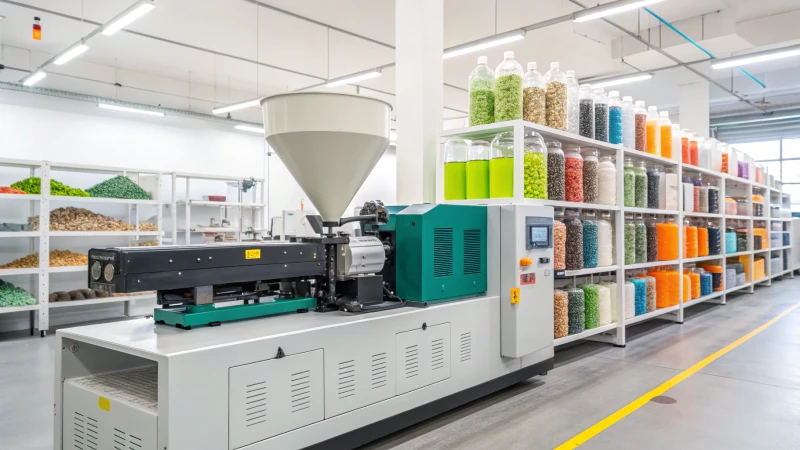
Understanding Common Defects
You know those moments when you’re holding your breath, hoping that the product comes out perfect? Injection molding can sometimes feel like a suspense thriller with defects like warping or sink marks waiting to surprise you. Trust me, I’ve been there. Understanding these issues is the first step in tackling them head-on. Many common injection molding defects9 stem from choices made early on, like material selection or process control slip-ups.
Optimizing Design
Back when I started, a mentor once told me, "Good design is like a good joke – if you have to explain it, it’s not that good." This stuck with me, especially when working on mold designs. Ensuring uniform wall thickness and incorporating adequate draft angles are just some basics that can save you headaches down the road. Like how uniform wall thickness10 reduces stress concentration and prevents warping, it’s all about nailing the fundamentals.
Design Aspect | Recommendation |
---|---|
Wall Thickness | Maintain uniformity |
Draft Angles | Ensure adequate angles |
Ribs & Gussets | Use to support structural integrity |
Material Selection
Choosing the right material feels like matchmaking – it’s got to be just right! I’ve learned the hard way that consistent material properties are non-negotiable for quality output. Factors like melt flow rate and thermal properties are crucial. It’s always worth referring to a material selection guide11 to ensure you’re making the best choice for your project.
Process Parameters
This is where the magic happens—or falls apart if not done right. Managing process parameters such as temperature, pressure, and cooling time is essential. I remember once overlooking a slight temperature variation, which taught me never to underestimate the power of consistent monitoring. Ensuring parameters remain within set limits can prevent major issues like short shots or flash.
Example Parameters:
- Temperature: Ensure the melt temperature is optimal for the material used.
- Pressure: Maintain adequate pressure to fill the mold completely.
- Cooling Time: Allow sufficient time for proper solidification.
Regular Maintenance and Monitoring
Regular maintenance might not sound exciting, but it’s the backbone of preventing wear and tear that could lead to defects. Picture this: just like keeping your car running smoothly with regular oil changes, cleaning vents and lubricating moving parts keep your molds in top shape. Implementing a maintenance schedule12 makes tracking these tasks manageable.
By focusing on these critical areas—design, material selection, and process optimization—you can dramatically reduce defects in injection molding. Trust me, doing this not only boosts product quality but also cuts down on waste and frustrations along the way.
Uniform wall thickness prevents warping in injection molding.True
Uniform wall thickness reduces stress concentration, minimizing warping.
Inconsistent material batches improve injection molding quality.False
Inconsistent material batches can lead to variable product quality.
How Does Temperature Influence Molding High-Impact Materials?
Ever tried molding materials and felt like you were cooking without a recipe? That’s how crucial temperature is in the process.
Temperature is crucial in molding high-impact materials, as it ensures uniform flow and mold filling, reducing defects and enhancing product strength, efficiency, and quality by maintaining optimal conditions.
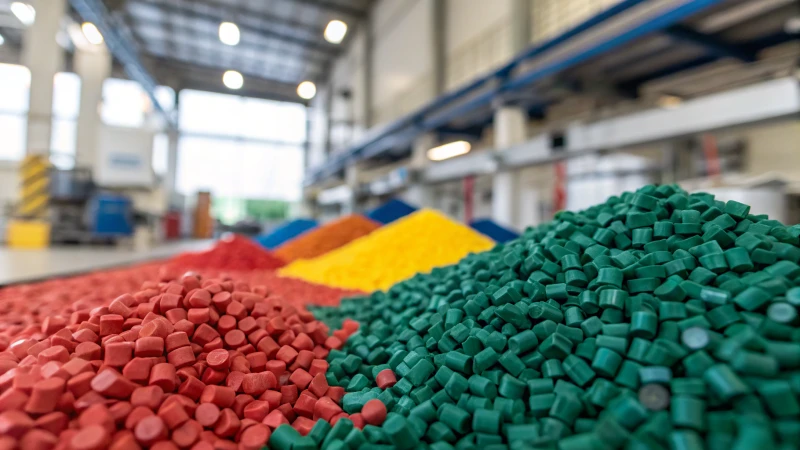
The Science of Temperature in Molding
Remember the first time you tried to mold something and it just didn’t fill out right? That’s probably because the temperature was off. It affects the molecular dance of materials, influencing how easily they slip into every nook and cranny of a mold. Get it right, and you avoid those annoying defects like warping or incomplete molds.
Temperature | Effect on Material |
---|---|
Low | Increases viscosity, leading to poor flow and incomplete molds |
Optimal | Balances viscosity for smooth flow, ensuring full mold completion |
High | Reduces viscosity too much, causing potential overheating issues |
Impact on Material Properties
Think about the time you worked with polymers and needed them to be as tough as a superhero’s armor. It’s all about precise temperature control. Get it wrong, and you’re left with brittle materials that just don’t cut it in demanding applications.
Different materials require specific temperature settings to achieve desired properties. For example, polymers might need precise thermal management to maintain high-impact resistance13. Deviations can lead to brittleness or reduced performance.
Temperature Control Techniques
In my years of tweaking designs, I’ve seen how modern manufacturing employs some pretty cool techniques to keep temperatures just where they need to be:
- Heated Platen Systems: These beauties ensure consistent heat distribution across the mold surface.
- Cooling Channels: They’re strategically placed within molds to dissipate excess heat efficiently.
These techniques have transformed how I maintain optimal temperature ranges and consistently hit the sweet spot in product quality.
Real-World Applications
Let me tell you, in practice, companies that nail this are like wizards in consumer electronics. They pre-heat molds to perfection before injection, slashing cycle times and production defects. The result? Happy balance sheets and products that shine in quality.
By meticulously monitoring temperatures, I’ve found ways to significantly enhance product durability—especially in sectors where this is non-negotiable, like automotive and aerospace. Understanding these interactions has been crucial for me, encouraging a deep dive into new material innovations14 to push the boundaries of what high-impact materials can achieve.
Low temperature increases material viscosity.True
Low temperatures make materials thicker, hindering mold filling.
High temperature enhances material brittleness.False
High temperatures reduce viscosity, but do not directly cause brittleness.
How Can You Optimize Cooling Time for Better Molded Products?
Ever feel like you’re always chasing the perfect mold? I know I have. Let’s dive into how optimizing cooling time can be a game-changer in molding.
Optimize injection molding cooling time by adjusting process parameters, improving mold designs, and using advanced cooling technologies to reduce cycle times and enhance product quality.
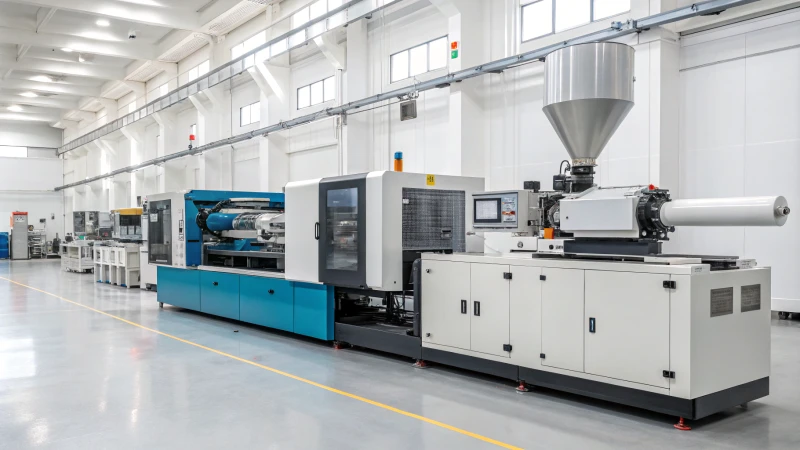
Understanding the Importance of Cooling Time
I remember my early days in the mold industry when I realized that cooling time was consuming a huge chunk of the production cycle. It was like a hidden thief stealing away precious minutes. In fact, it can make up about 80% of the total cycle time! That’s why cracking the code to optimize this phase is crucial. When you nail this part, not only do you ramp up productivity, but you also save on production costs without sacrificing quality.
Techniques to Optimize Cooling Channels
Designing efficient cooling channels felt like solving a complex puzzle for me. The challenge? Achieving uniform temperature across the mold. One breakthrough moment was when I stumbled upon conformal cooling techniques. These channels are custom-tailored to fit the part’s geometry, which drastically slashes cycle times and boosts product quality15. I’ve also tried using baffles or bubblers—simple tweaks that significantly improve heat transfer within the mold core.
Utilizing Advanced Cooling Technologies
Sometimes it feels like technology is light-years ahead, and keeping up is a race. But incorporating rapid tooling and variotherm systems was like finding a secret weapon. Rapid tooling uses materials with high thermal conductivity, which helps dissipate heat faster than I could’ve imagined. And variotherm systems? They allow precise control over heating and cooling cycles, improving surface finish and reducing residual stress. It’s thrilling to see how these innovations can boost efficiency16.
Adjusting Process Parameters for Optimal Results
I’ve spent countless hours fine-tuning process parameters like mold temperature and coolant flow rates. Believe me, even small adjustments can lead to massive improvements in cooling efficiency. Using computational tools such as Moldflow simulation has been a revelation—it’s like having a crystal ball that predicts potential hotspots and helps optimize the cooling cycle. This analysis significantly cuts down on defects like warping or shrinkage, making all that effort worth it.
Table: Comparative Overview of Cooling Techniques
Technique | Key Features | Benefits |
---|---|---|
Conformal Cooling | Custom channel design | Uniform cooling, reduced cycle |
Baffles/Bubblers | Enhances heat transfer | Better core cooling |
Rapid Tooling | High thermal conductivity materials | Faster heat dissipation |
Variotherm Systems | Controlled heating/cooling cycles | Improved surface finish |
Exploring these strategies is like opening a treasure chest of possibilities for enhancing productivity17 and achieving superior molded products. It’s all about finding that sweet spot where quality meets efficiency.
Cooling time is 80% of injection molding cycle time.True
Cooling time dominates the cycle, affecting productivity and cost.
Conformal cooling reduces cycle times by 50%.False
Conformal cooling improves efficiency but doesn't halve cycle times.
What Are the Best Practices for Quality Control in Molding?
Quality control in molding isn’t just about precision—it’s about passion and persistence. But what really makes a difference when striving for excellence?
Quality control in molding involves clear procedures, advanced inspection tools, and team communication, ensuring components meet high standards.
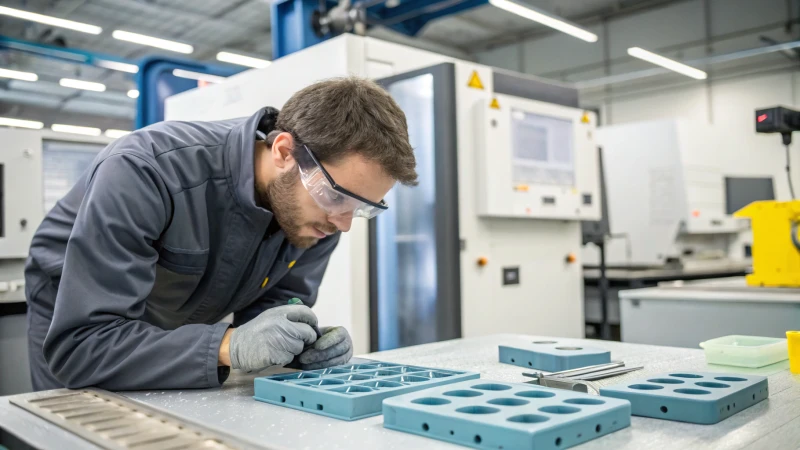
Understanding Quality Control in Molding
When I first stepped into the world of molding, I quickly realized it wasn’t just about getting the shape right—it was about ensuring every product met stringent quality standards. Quality control is more than a checklist; it’s a commitment to excellence, ensuring every molded piece aligns with specific requirements through standardized processes, thorough inspections, and addressing any deviations head-on.
Standardized Procedures
I learned early on that having a standardized procedure is like having a trusted recipe. It begins with laying down clear, detailed specifications for each part of the molding process. This includes:
- Material Selection: It’s like choosing ingredients for a dish; picking the right polymers is crucial for both durability and functionality.
- Process Parameters: Setting the right temperature, pressure, and time can make or break the process.
- Measurement Tools: Precision is key, so using calibrated instruments ensures we hit those exact dimensions every time.
Advanced Inspection Technologies
I remember the first time I saw a 3D scanner in action—it was like witnessing magic! Advanced technologies like these, along with CT imaging, have revolutionized how we detect flaws. They help spot:
- Micro-defects that are impossible to see with the naked eye.
- Variations in thickness or density that could compromise integrity.
- Design discrepancies18 that might slip through other checks.
Consistent Team Communication
Communication might seem obvious, but it’s the glue that holds everything together. Regular meetings and feedback loops aren’t just formalities—they’re lifelines that keep us all on the same page. This collaborative spirit enables us to:
- Share insights and updates on process improvements.
- Address concerns about mold design19 or production hiccups before they become bigger issues.
- Encourage solutions that are proactive rather than reactive.
Practice | Description |
---|---|
Standardized Procedures | Clear guidelines for materials, processes, and measurements. |
Advanced Inspection Tech | Use of 3D scanning and imaging for detailed defect detection. |
Consistent Team Communication | Collaborative approach to continuously improve quality standards. |
By focusing on these practices, I’ve seen firsthand how they elevate the quality of our products. They aren’t just guidelines—they’re part of a philosophy that ensures we not only meet but often exceed industry standards, ultimately leading to products we can all be proud of.
Standardized procedures improve molding quality.True
Standardized procedures ensure consistency and adherence to specifications.
3D scanners cannot detect micro-defects in molds.False
3D scanners are specifically used to identify micro-defects in components.
Conclusion
Molding high-impact resistant materials presents challenges like material selection, mold design, and defect prevention. Mastering these aspects ensures product durability and manufacturing efficiency.
-
Explore how different thermoplastics require specific temperature settings to ensure high-quality molding outcomes. ↩
-
Learn strategies to minimize downtime and operational expenses in injection molding through material selection. ↩
-
Discover how to adjust mold designs to account for material expansion and contraction. ↩
-
Understand how choosing sustainable materials can align with current environmental regulations. ↩
-
Explore techniques for maintaining consistent temperature in molds to reduce warping issues. ↩
-
Learn how optimizing gate location and size can solve material flow problems. ↩
-
Discover strategies to enhance surface finish quality for high-impact materials. ↩
-
Stay updated with recent advancements in mold technologies for better solutions. ↩
-
Discover detailed explanations of common injection molding defects and their causes to better address these issues in your processes. ↩
-
Learn how maintaining uniform wall thickness can reduce warping and improve product integrity in injection molding. ↩
-
Explore comprehensive guides on selecting materials for injection molding to ensure high-quality production. ↩
-
Find practical schedules and checklists for regular mold maintenance to prevent defects and prolong mold life. ↩
-
Learn why managing temperature is crucial for maintaining impact resistance in polymers. ↩
-
Discover new advancements in molding technology that enhance high-impact material performance. ↩
-
Understand how conformal cooling enhances product quality by reducing cycle times and ensuring uniform temperature distribution. ↩
-
Discover innovative cooling technologies that boost efficiency by integrating rapid tooling and variotherm systems. ↩
-
Explore strategies that enhance productivity by effectively optimizing cooling time in the molding process. ↩
-
Learn how 3D scanning technology can detect subtle flaws, enhancing overall product quality. ↩
-
Discover strategies for improving communication within teams to boost efficiency and problem-solving capabilities. ↩