Have you ever wondered why some plastic products seem sturdy while others fail unexpectedly? It often comes down to one critical issue: porosity.
Porosity in injection molded plastic products is primarily caused by excessive moisture or volatiles in the resin, improper injection pressure, and poor mold design. Addressing these factors can significantly reduce porosity issues, enhancing product quality and performance.
While understanding these primary causes provides a solid foundation, exploring the intricacies of material selection, process optimization, and mold design will offer deeper insights into tackling porosity effectively.
Excessive moisture in resin causes porosity in plastics.True
Moisture in resin vaporizes during molding, forming pores.
How Does Material Choice Affect Porosity?
Selecting the right materials is crucial in minimizing porosity in injection molded plastics, influencing product integrity.
Material choice impacts porosity by affecting shrinkage rates and moisture content in resins. High moisture or volatile substances in raw materials can lead to pore formation during the molding process. By selecting low-shrinkage and properly dried materials, manufacturers can significantly reduce porosity in their products.
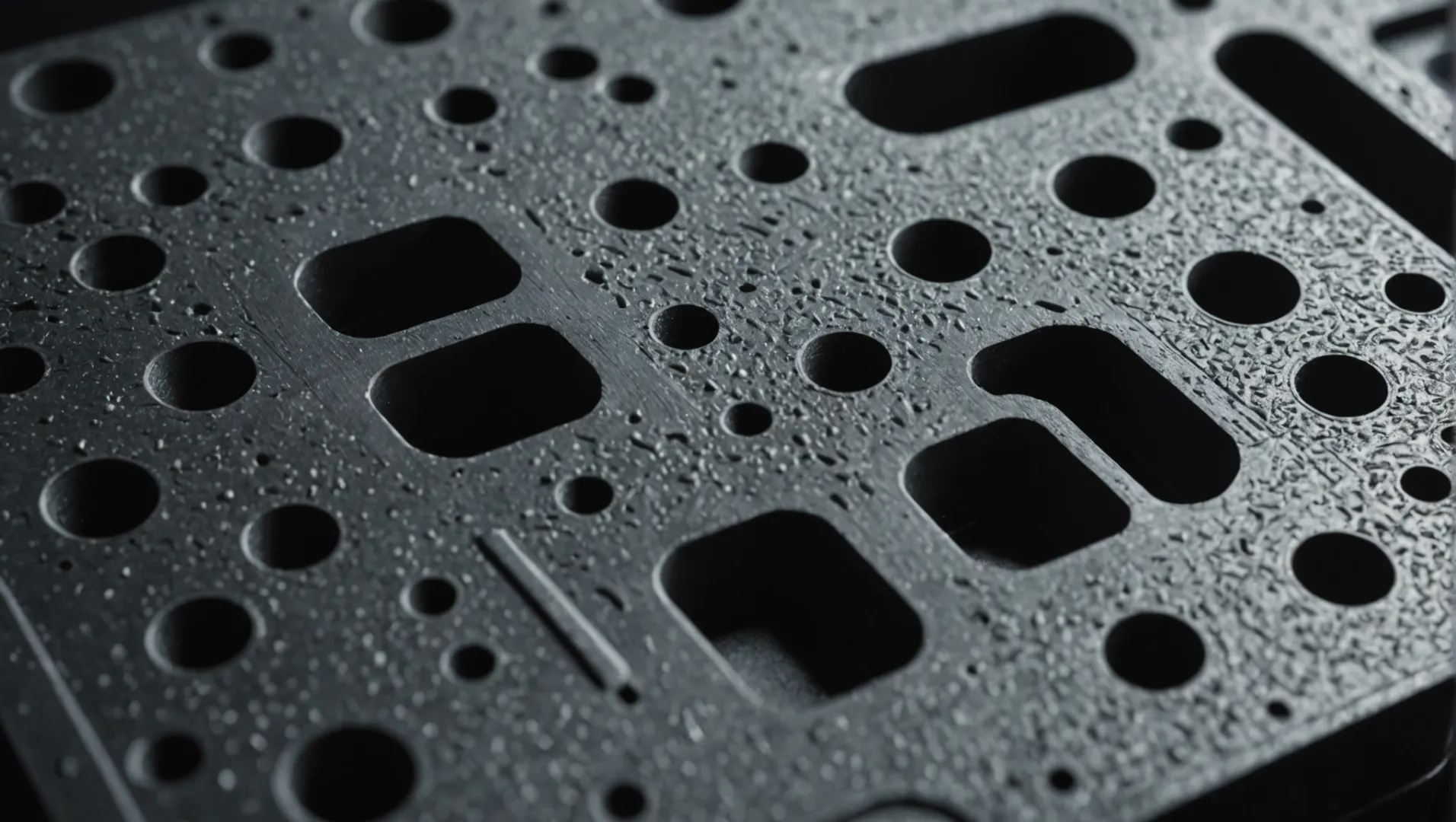
Understanding Material Properties and Their Impact on Porosity
The choice of material is pivotal in controlling the porosity of injection molded plastic products. One of the primary considerations is the moisture content present in the resin. Resins that contain high levels of moisture or volatile substances can create pores during the molding process. When heated, these substances vaporize, leaving voids as they escape from the material.
For instance, some plastic particles require thorough drying before they are used in injection molding. Insufficient drying can lead to rapid evaporation during the high-temperature process, forming pores within the final product. This highlights the importance of selecting materials that are either naturally low in moisture or can be easily dried without compromising their integrity.
Shrinkage Rates and Their Effects
Another critical factor is the shrinkage rate of the plastic material. Different plastics exhibit varying shrinkage rates, which can influence porosity. Crystalline plastics, for example, tend to have larger shrinkage rates compared to non-crystalline plastics. This increased shrinkage can lead to stress during cooling, resulting in pore formation as the material contracts unevenly.
By understanding and selecting materials with appropriate shrinkage characteristics, manufacturers can minimize the stress-induced porosity during the cooling phase of production.
Comparison Table: Material Characteristics and Porosity Risks
Material Type | Moisture Content Risk | Shrinkage Rate | Porosity Risk |
---|---|---|---|
ABS | Low | Moderate | Low |
Polyethylene | High | High | High |
Nylon | Moderate | Moderate | Moderate |
PVC | Low | Low | Low |
This table provides a simplified overview of how different material properties might contribute to porosity risks.
Importance of Material Testing and Quality Control
Selecting the right materials involves more than just choosing based on general properties. Manufacturers must engage in rigorous testing and quality control measures to ensure the chosen materials consistently meet required standards.
Testing for moisture content before processing and analyzing shrinkage characteristics under various conditions can provide valuable insights into potential porosity issues. Such proactive measures can prevent costly manufacturing defects and enhance product performance.
For more insights into material testing techniques, consider exploring material testing processes1. Effective testing ensures quality control across production runs and helps mitigate porosity-related challenges.
High moisture in resins increases porosity risk.True
Moisture vaporizes during molding, creating pores as it escapes.
ABS plastic has a high porosity risk due to shrinkage.False
ABS has low porosity risk with moderate shrinkage and low moisture.
What Role Does Injection Pressure Play in Porosity?
Injection pressure is pivotal in determining the quality of molded plastics, influencing porosity levels and structural integrity.
Injection pressure impacts porosity by ensuring the plastic melt fully fills the mold cavity. Insufficient pressure can lead to air pockets and incomplete filling, resulting in porous areas. Correct pressure settings minimize porosity, enhancing product quality.
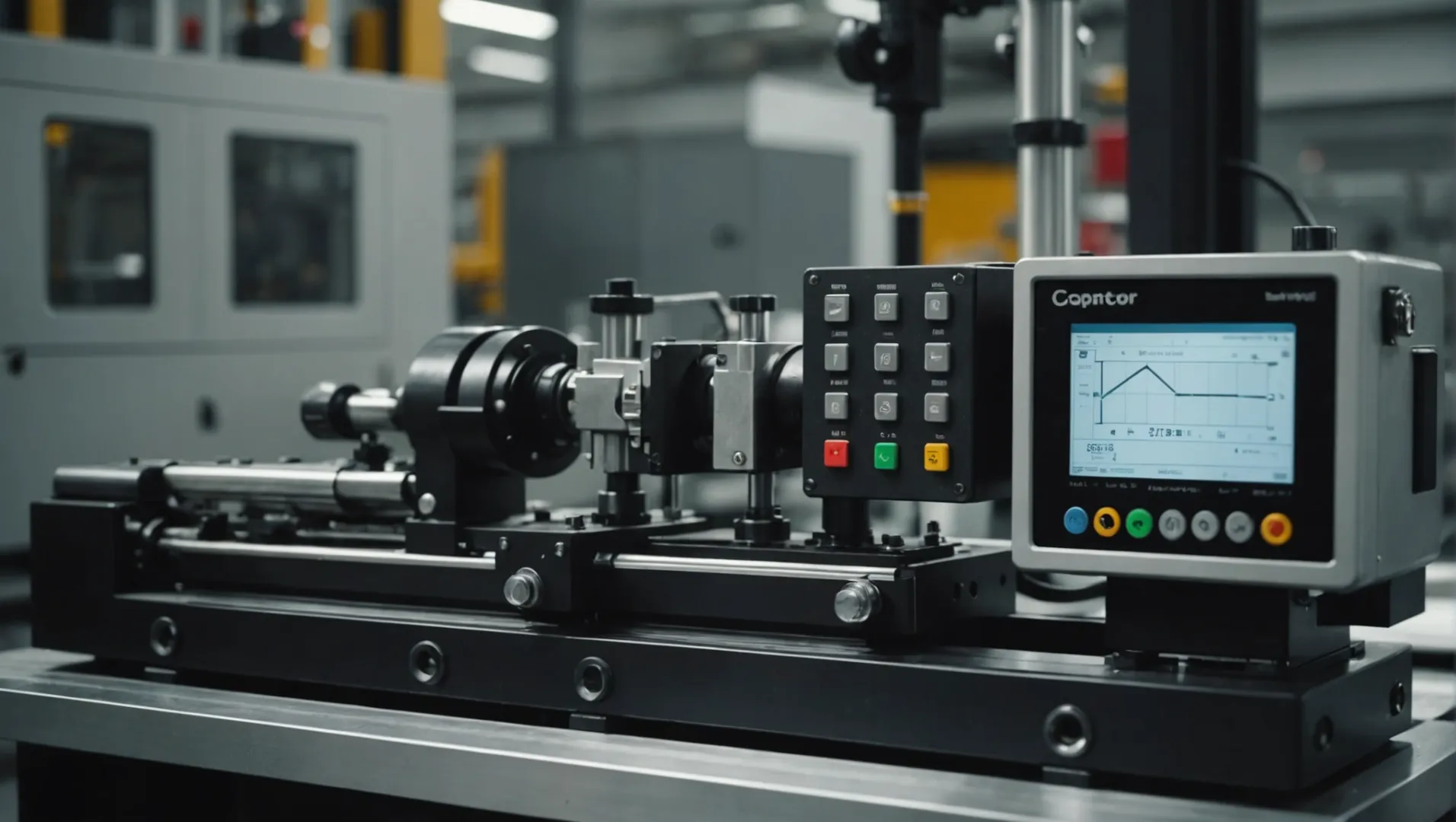
Understanding Injection Pressure in Mold Filling
Injection pressure is the force applied to push molten plastic into the mold cavity. The correct pressure ensures that the material fills the mold entirely, avoiding voids and defects such as porosity. If the injection pressure2 is too low, the melt may not reach all corners of the mold, leading to unfilled sections and air pockets that manifest as pores.
Effects of Insufficient Injection Pressure
When injection pressure is inadequate, several issues can arise:
- Incomplete Filling: The plastic melt may not reach all areas of the mold, especially those farthest from the gate, resulting in incomplete parts.
- Air Entrapment: Low pressure allows air to remain trapped within the material, creating bubbles that form pores upon cooling.
These problems highlight the need for careful calibration3 of injection parameters to ensure quality.
Optimal Pressure Settings
Determining the optimal injection pressure involves balancing several factors:
- Material Properties: Different resins require different pressure levels. For example, high-viscosity plastics need more pressure to flow properly.
- Mold Design: Complex molds with intricate geometries may demand higher pressures to ensure complete filling.
Engineers often use trial and error alongside simulation software to find the best settings for each project.
Adjustments and Solutions
To address porosity issues related to injection pressure, consider these strategies:
- Increase Pressure Gradually: Start with a baseline and slowly increase pressure until the material fills the mold without defects.
- Monitor Melt Temperature: Ensure the melt temperature complements the pressure applied for optimal flow.
- Use Advanced Monitoring Systems: Employ sensors and software that track real-time conditions inside the mold, allowing for adjustments as needed.
Implementing these solutions can reduce porosity, improving product durability and appearance. Learn more about managing injection molding parameters4 for better outcomes.
High injection pressure reduces porosity in molded plastics.True
Proper pressure ensures complete filling, minimizing air pockets.
Low injection pressure increases the risk of air entrapment.True
Insufficient pressure leaves air trapped, forming pores.
Why Is Mold Design Crucial for Reducing Porosity?
Mold design plays a pivotal role in minimizing porosity in injection molded products, ensuring structural integrity and aesthetic quality.
Mold design is essential for reducing porosity in injection molded products by optimizing gate size, ensuring proper exhaust, and maintaining uniform wall thickness. A well-designed mold can prevent air entrapment and ensure even cooling, significantly improving the product’s quality and durability.
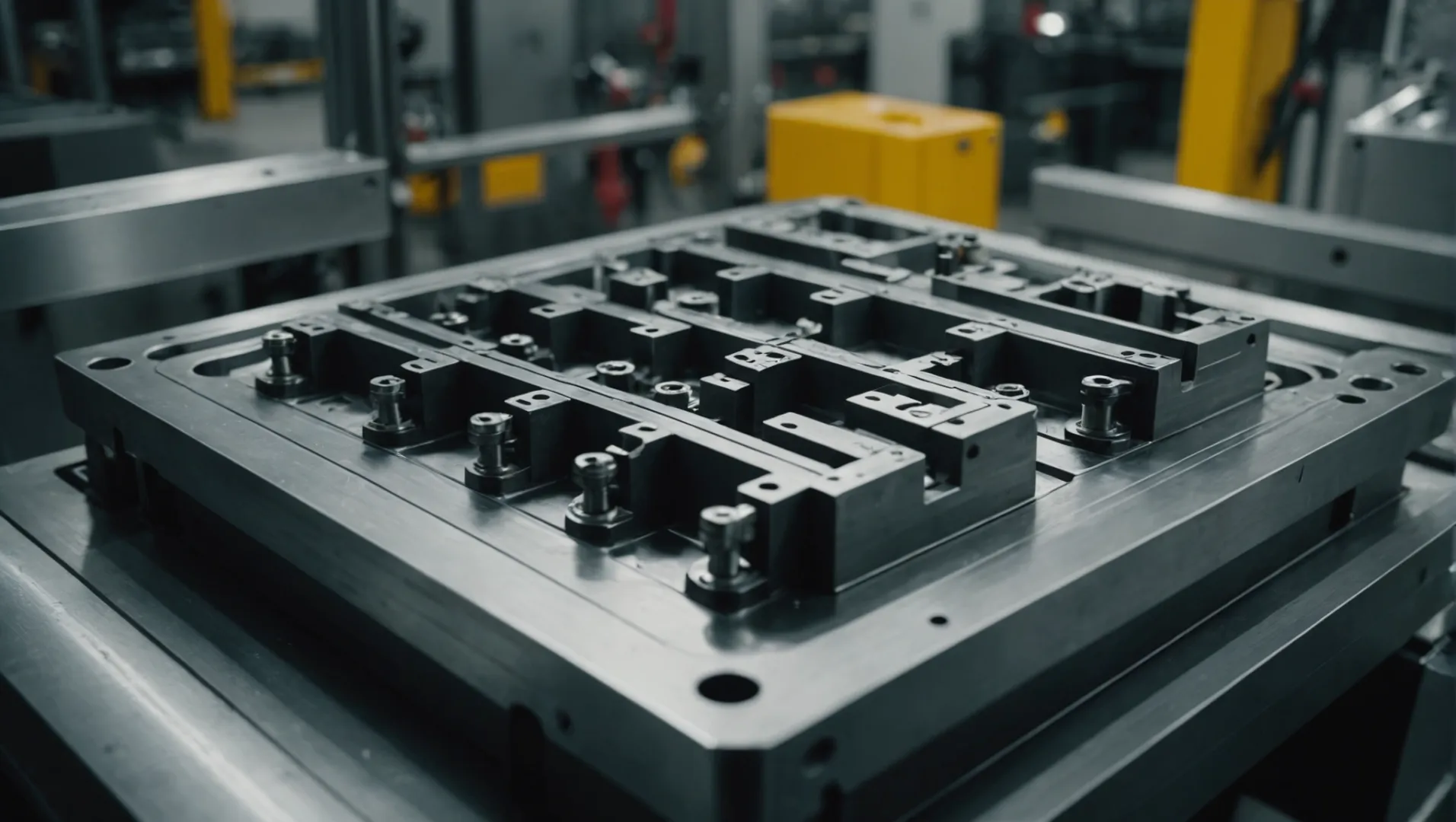
Understanding the Impact of Gate Size
One of the key elements in mold design is the gate size. A gate that is too small can restrict the flow of plastic melt, slowing down the filling process and increasing the likelihood of porosity. This is because restricted flow can lead to turbulence and air entrapment within the mold cavity. Additionally, smaller gates can cause the plastic melt to spray upon entry, which also introduces air into the mix. By optimizing the gate size, manufacturers can ensure a smoother flow, reducing air pockets and porosity.
Importance of Proper Exhaust Systems
An effective exhaust system is crucial for minimizing porosity. During the injection molding process, any trapped air or volatile gases in the plastic melt must be expelled efficiently to prevent them from being compressed into the product as pores. A poor exhaust design can lead to air entrapment, especially in complex or deep cavities. Ensuring adequate venting through strategically placed vents or using vacuum systems can help mitigate this issue, resulting in a denser and more uniform product.
Uniform Wall Thickness Matters
The wall thickness of a product influences its cooling rate and shrinkage behavior. Uneven wall thickness can cause inconsistent cooling, where thicker sections cool slower than thinner areas, leading to differential shrinkage and potential porosity. It also affects how the plastic melt flows through the mold; inconsistent thickness can cause flow hesitation and incomplete filling. Designing molds with consistent wall thicknesses helps achieve uniform cooling and reduces porosity risk by promoting even material distribution.
A well-thought-out mold design not only reduces porosity but also enhances other aspects such as mechanical strength and surface finish. For more insights on optimizing mold designs for different materials, explore advanced mold design techniques5.
Optimizing gate size reduces porosity.True
A well-sized gate ensures smooth plastic flow, minimizing air pockets.
Uneven wall thickness increases porosity risk.True
Inconsistent thickness causes uneven cooling, leading to porosity.
How Can Cooling Time Influence Porosity Formation?
Cooling time in injection molding significantly impacts porosity formation, affecting product integrity and quality.
Cooling time affects porosity in injection molded plastics by influencing shrinkage and solidification rates. Proper cooling ensures uniform solidification, reducing the risk of pores due to uneven shrinkage or residual stress. Adjusting cooling time helps mitigate porosity and enhance product durability.
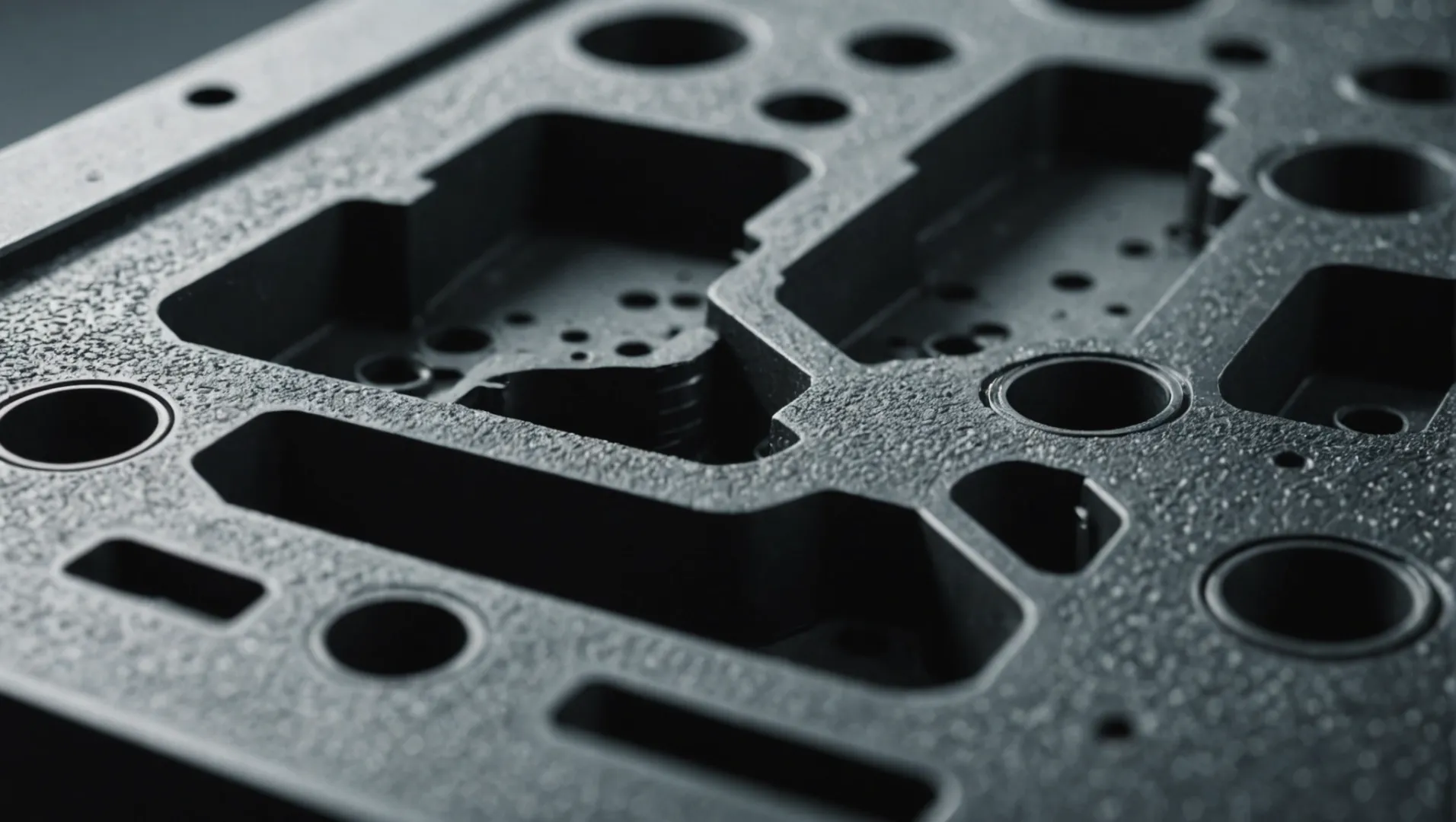
The Role of Cooling Time in Injection Molding
In the injection molding process, cooling time is a critical phase that directly impacts the structural integrity of the final product. It determines how the plastic solidifies within the mold, affecting porosity formation.
-
Impact on Shrinkage: During the cooling phase, plastics tend to shrink. If the cooling is too rapid or too slow, it can lead to uneven shrinkage, resulting in internal stresses that manifest as pores. Properly calibrated cooling times allow for uniform shrinkage, minimizing stress.
-
Solidification Rate: A balanced cooling time ensures that the plastic melt solidifies evenly across the mold. This uniformity prevents areas of differential solidification that can trap air and form pores.
Influence on Mechanical Properties
The mechanical properties of an injection molded part are heavily influenced by its porosity level. Excessive porosity can lead to weakened structural integrity and reduced performance under load.
- Strength and Durability: Products with reduced porosity exhibit enhanced strength and durability. Adjusting cooling time to minimize porosity formation results in a more consistent and reliable product.
Practical Adjustments for Optimal Cooling
To optimize cooling time and reduce porosity, consider:
-
Mold Temperature Control: Precise control of mold temperature can enhance cooling efficiency. It helps maintain a steady temperature gradient, which is crucial for uniform cooling.
-
Cooling Channels Design: The design of cooling channels within the mold is vital. Well-designed channels ensure effective heat dissipation, promoting even cooling.
-
Material-Specific Adjustments: Different materials require specific cooling profiles. Understanding the thermal properties of the chosen plastic helps tailor the cooling time accordingly.
Factors Affecting Cooling Time | Impact on Porosity |
---|---|
Mold Temperature | High temperatures slow cooling, increasing porosity risk. |
Cooling Channel Efficiency | Poorly designed channels lead to uneven cooling and porosity. |
Material Characteristics | Crystalline materials may need longer cooling times to prevent porosity. |
Understanding and controlling cooling time is essential for reducing porosity in injection molded products. For further insights into optimizing injection molding processes, explore cooling time optimization techniques6.
Cooling time affects porosity in injection molding.True
Cooling time impacts shrinkage and solidification, influencing porosity.
Shorter cooling times always reduce porosity.False
Short cooling can cause uneven shrinkage, increasing porosity risk.
Conclusion
Understanding and addressing the causes of porosity in injection molding is essential for producing high-quality products. By focusing on material properties, process adjustments, and mold design, manufacturers can minimize defects and enhance performance.
-
Explore methods for ensuring materials meet quality standards and reduce porosity.: Learn how to select the right material for your injection molding design with this technical overview of thermoplastic resins. ↩
-
Discover how pressure settings affect porosity and product quality.: This may be evidence of intensive plastic porosity in conditions of low plasticizing pressure, and intensive growth of pores in the mold cavity. in molded … ↩
-
Learn methods for accurate injection machine pressure calibration.: If you must calibrate time and pressure, I would recommend a process review by competent technical personnel. Determine what the needed spec is … ↩
-
Explore strategies for optimizing injection molding parameters.: 1. Temperature Control: · 2. Injection Speed: · 3. Cooling Time: · 4. Plastic Material Selection: · 5. Screw Speed and Back Pressure: · 6. Injection … ↩
-
Learn more about optimizing mold designs for various materials.: Create more engaging and efficient parts, plus reduce production costs with these injection molding design tips, including living hinges, bosses, text, & more … ↩
-
Discover methods to refine cooling processes for reduced porosity.: Injection molding cycle time or Cooling time is one of the major factors in improving and maintaining efficiency in the injection molding process. ↩