Have you ever thought about how to easily find the cost of injection molding products without stress?
To find the cost of products from an injection molding machine, total the costs of materials, labor and manufacturing. Include equipment wear, energy use and mold costs. This calculation provides a clear view of the money needed to create plastic parts well.
Exploring these cost parts is really interesting. I recall my first time analyzing this area, surrounded by a pile of spreadsheets, trying to understand each detail. Grasping the details such as material costs – think of figuring out how 100 grams of plastic becomes a cup – offers control over your spending. Labor costs work in a similar way. Imagine paying your friend to help you build a Lego set for an hour. Manufacturing expenses also affect costs, with depreciation, energy and mold use contributing to the big picture of production costs. It’s about assembling the pieces to optimize your spending.
Direct labor costs are the largest component in injection molding.False
Material costs typically outweigh labor in injection molding expenses.
Equipment depreciation affects injection molding product cost.True
Depreciation is a significant factor in calculating manufacturing expenses.
What Factors Influence Direct Material Costs?
Some products require more money to produce than others. Direct material costs are the reason.
Direct material costs depend on things like material quality, supplier trustworthiness, market changes and production methods. Handling these aspects well might really reduce manufacturing expenses.
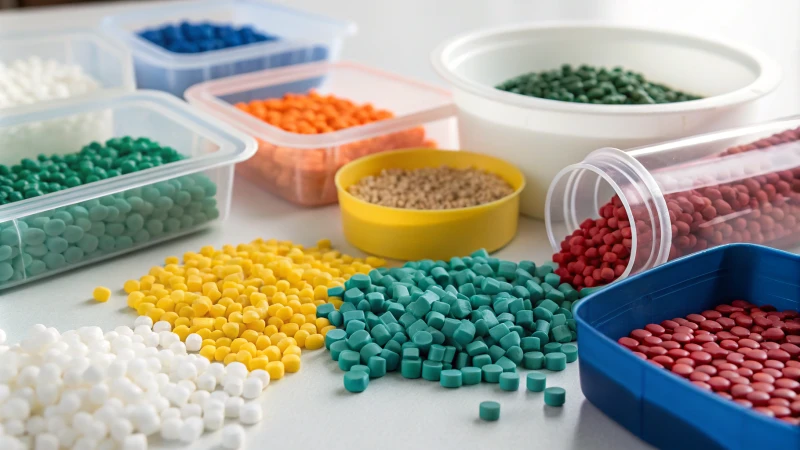
Material Quality and Specifications
Quality acts like a double-edged sword. High-quality materials come with a higher price but reduce waste and improve product performance1. In contrast, cheaper materials might initially seem like a smart choice but often bring defects, which increase expenses. Once, I saved money by choosing a cheaper material, only to face costly quality issues later on.
Supplier Relationships
Strong relationships with suppliers proved very valuable. Engaging in long-term contracts or partnerships often results in bulk discounts and preferential treatment2, helping to stabilize costs even during uncertain market times.
Market Volatility
Raw material prices often change unexpectedly, similar to weather changes, influenced by global demand and political tensions. Staying updated on these changes and having different suppliers is key to managing the risks associated with price volatility3.
Production Techniques
Efficient production techniques marked another turning point. By using lean manufacturing principles and new technologies like CNC machining, wastage was reduced and processes were made smoother. This approach cut our direct material expenses4 significantly.
Factor | Impact on Costs |
---|---|
Material Quality | Affects product quality |
Supplier Relationships | Influences pricing terms |
Market Volatility | Causes price fluctuations |
Production Techniques | Reduces material waste |
Higher-quality materials reduce waste costs.True
High-quality materials lead to fewer defects, reducing waste expenses.
Supplier relationships don't affect material costs.False
Strong supplier relationships can secure better pricing and terms.
How Do You Determine Direct Labor Costs in Injection Molding?
Have you ever thought about capturing those tricky direct labor costs in injection molding? This task is easier than you think. Understanding it is very important for not overspending on your projects.
I calculate direct labor costs in injection molding by multiplying unit product working hours by hourly wages. This calculation gives labor cost per unit. These costs are vital for accurate pricing. Pricing and budgeting rely heavily on this information.
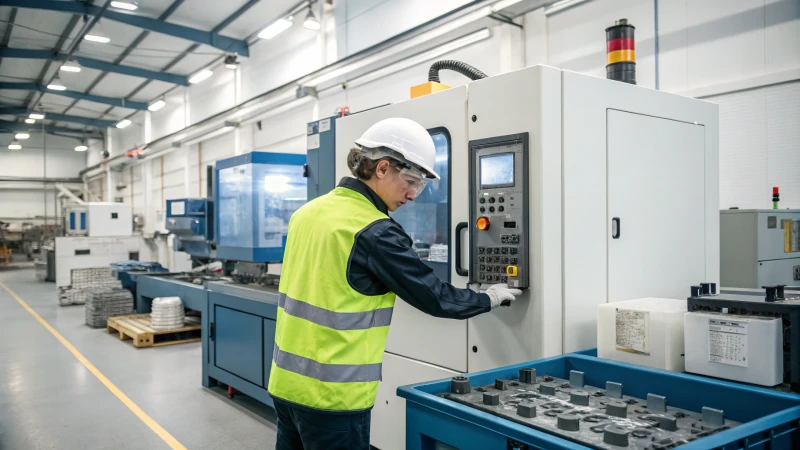
Understanding Direct Labor Costs
Direct labor costs are simple to calculate. Multiply the unit product working hours5 by how much the worker earns per hour. For instance, if making a part takes 0.5 hours and the worker earns $5 per hour, the labor cost for one unit is 0.5 hours × $5 yuan/hour = $2.5.
When I first started doing these kinds of calculations, I felt overwhelmed. But taking it step-by-step helped me understand.
Calculating Unit Product Working Hours
Knowing how much time each unit needs is crucial. You need to look at every step of the process, like setting up machines and finishing the products. Keeping detailed records lets me give a correct cost estimate6.
Setting the Hourly Wage Rate
The hourly wage rate shows the skill and experience required for the job. This means considering not just the basic pay but also benefits and other compensation. A good pay rate attracts skilled workers, which probably improves both quality and efficiency.
Analyzing Impact on Total Product Cost
Direct labor is only one part of the total product cost. Other parts include materials and manufacturing costs. Here is a simple idea:
Cost Component | Calculation Method | Example Cost |
---|---|---|
Direct Material Cost | Material usage × Material unit price | $0.2 |
Direct Labor Cost | Unit hours × Hourly wage | $2 |
Manufacturing Cost | Equipment depreciation + Energy + Mold allocation | $1 |
Total product cost = Direct material + Direct labor + Manufacturing costs = $3.2.
Knowing these parts helps me create better financial plans and set good prices. My production stays stable and competitive.
To find more ways to save on costs, I often read industry case studies7 and learn from experts’ ideas.
Factors Affecting Labor Costs
Labor costs may change due to factors like how efficiently people work, the level of automation, and economic conditions. Investing in technology or improving processes to reduce work time per unit may result in cost savings.
Calculating and managing direct labor costs well keeps my company strong and profitable in the ever-changing world of injection molding.
Direct labor cost is calculated using unit hours and wage rate.True
Direct labor cost is determined by multiplying unit product working hours by the hourly wage rate.
Material costs do not affect total product cost in injection molding.False
Material costs are a key component of the total product cost, alongside labor and manufacturing expenses.
How Do You Calculate Manufacturing Expenses?
Have you ever wondered about the real cost of turning ideas into products you can touch? This guide explores the key expenses in manufacturing, a crucial element of every production plan.
Manufacturing expenses cover costs for materials, labor and overheads such as equipment wear and energy use. Calculating these needs special formulas for each part. This helps find the total cost of making a product.
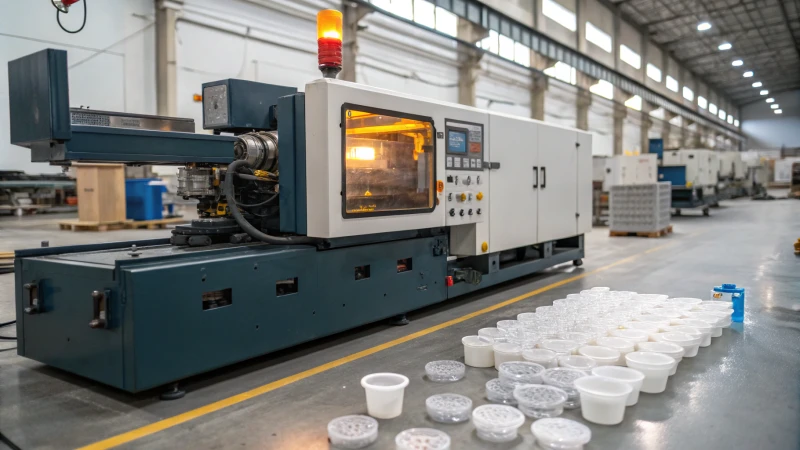
Components of Manufacturing Expenses
Understanding manufacturing expenses involves knowing the parts that create the total cost. At first, it felt like solving a puzzle where each part mattered a lot. Key components include direct material cost8, direct labor cost, and manufacturing overhead.
Direct Material Cost
This is like the essential building blocks of your product. The cost of raw materials used in making products is important. I remember calculating the cost for a plastic piece. It meant finding out how much material was needed for one item and knowing the cost of each unit. The formula was simple:
- Direct Material Cost = Material Usage per Unit Product × Material Unit Price
For example, a plastic cup required 100 grams of plastic. With plastic at $2 per kilogram, each cup cost $0.2 for materials.
Direct Labor Cost
Human effort is involved here. It includes paying people who actually create the product. This reminded me of working with dedicated craftsmen. We calculated it like this:
- Direct Labor Cost = Unit Product Working Hours × Hourly Wage Rate
If making a product took half an hour and the wage was $3 per hour, then the labor cost per unit was $3.
Calculating Manufacturing Overhead
Overhead costs are the hidden expenses that support production. They include things like machinery wear, energy bills, and mold costs.
Overhead Component | Formula | Example Calculation |
---|---|---|
Equipment Depreciation | Total Depreciation ÷ Total Output | $150000 ÷ 10 years = $15000/year ÷ 100,000 units = $0.15/unit |
Energy Consumption | Total Energy Cost ÷ Total Output | $15000/month ÷ 50,000 units = $0.3/unit |
Mold Allocation | Total Mold Cost ÷ Total Output | $80000 ÷ 500,000 units = $0.16/unit |
Total Product Cost
Combining all these expenses reveals what making each product truly costs. It felt like putting together a financial jigsaw puzzle.
- Total Product Cost = Direct Material Cost + Direct Labor Cost + Manufacturing Overhead
With direct material costing $0.2, direct labor at $2 and overhead at $1, the total cost per product added up to $3.2.
Understanding these numbers was not just about math; it meant pricing products correctly to keep business growing. Each part – material, labor and overhead – played a special role in the final cost. This knowledge is really important for financial planning9 and keeping things running smoothly.
Direct material cost includes indirect costs.False
Direct material cost only includes the cost of raw materials directly used.
Total product cost includes overhead expenses.True
Total product cost combines direct material, labor, and overhead costs.
How Can I Optimize Total Product Cost in Injection Molding?
Ever think about ways to cut costs and increase profits in injection molding? Some strategies truly work for lowering expenses and improving efficiency.
I concentrate on reducing material and worker costs in injection molding to lower total product costs. Manufacturing expenses need careful control. Clever design approaches are key. These strategies help raise profits. These ideas really are vital for saving money.
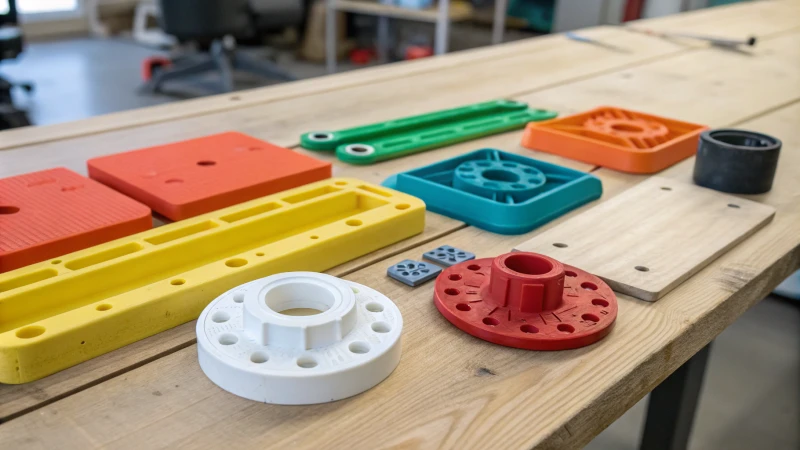
Understanding Direct Material Costs
Material costs constitute a significant portion of injection molding expenses10. Calculate it using the formula: Material Cost = Material Usage per Unit × Material Unit Price. For instance, producing a plastic cup may require 100 grams of plastic at $2/kg, resulting in a $0.2 direct material cost per unit.
Reducing Direct Labor Costs
Labor costs are another key area. Use the formula: Labor Cost = Unit Product Working Hours × Hourly Wage Rate. If production demands 0.5 hours at $3/hour, the direct labor cost is $1.5. Streamlining labor through automation or training can significantly reduce these expenses.
Managing Manufacturing Expenses
Manufacturing expenses include equipment depreciation, energy consumption, and mold allocation.
- Equipment Depreciation: Calculated as Total Equipment Depreciation ÷ Total Product Output. A machine worth 1 million yuan with a 10-year lifespan and 100,000 annual output results in a 1 yuan depreciation cost per unit.
- Energy Consumption: Use Total Energy Cost ÷ Total Output. If energy costs are $15000 for 50,000 products monthly, the unit cost is $0.3.
- Mold Allocation: Calculate as Total Mold Cost ÷ Total Output. A mold costing $80000 yuan for 500,000 products gives a unit cost of $0.16.
Calculating Total Product Cost
The total product cost combines all components:
Cost Component | Calculation | Result |
---|---|---|
Direct Material | 0.1 kg × $2/kg | 0.2 |
Direct Labor | 0.5 hours × $3/hour | $1.5 |
Equipment Depreciation | ($150000 / (10 years *100k units)) | $0.15 |
Energy Consumption | (100k / (50k units)) | $0.3 |
Mold Allocation | (500k / (500k units)) | $0.16 |
Total Product Cost | Sum of all above costs | $2.31 |
Optimizing Design for Cost Efficiency
Enhance designs to reduce material use without sacrificing quality by employing innovative design techniques11. Simplifying part designs can lead to less material waste and faster production times. Exploring lightweight materials or reducing wall thickness can also contribute to cost savings. Employing simulation tools can predict and mitigate costly errors in the design phase.
By understanding these factors and making strategic adjustments, you can effectively optimize your total product cost in injection molding. Consider implementing automation technologies12 to further streamline your production processes and increase efficiency across the board.
Direct material cost is the largest expense in injection molding.True
Material costs are significant due to the volume and price of materials used.
Automation has no impact on reducing labor costs.False
Automation streamlines processes, reducing the need for manual labor.
Conclusion
Learn how to calculate the costs of injection molding products by analyzing material, labor, and manufacturing expenses to optimize production efficiency and reduce overall costs.
-
Learn how material quality affects overall production costs and product performance. ↩
-
Explore how solid supplier relationships can result in better pricing and terms. ↩
-
Understand the impact of market changes on raw material pricing. ↩
-
Discover how optimizing production techniques can lead to cost savings. ↩
-
Learn strategies for determining precise working hours per unit to ensure accurate cost calculations. ↩
-
Discover effective techniques for assessing costs accurately in manufacturing settings. ↩
-
Explore real-world case studies on optimizing injection molding costs to enhance profitability. ↩
-
Learn about how direct material costs affect product pricing and resource management. ↩
-
Understand how financial planning enhances decision-making and efficiency in production. ↩
-
This link offers innovative methods to cut down material expenses in injection molding processes. ↩
-
Explore this link for strategies to design more cost-effective parts in injection molding. ↩
-
Learn about the latest automation technologies that can enhance efficiency and reduce costs. ↩