Balancing runners in multi-cavity molds1 is a critical aspect of injection molding that ensures each cavity fills uniformly, producing consistent, high-quality parts. In multi-cavity molds, which are designed to produce multiple identical parts in a single cycle, the runner system—the channels that distribute molten plastic from the injection point to each cavity—must be carefully designed to prevent defects like underfilling, overpacking, or warping.
Balancing runners2 ensures uniform filling of all cavities in multi-cavity molds, which is essential for producing identical, high-quality parts in injection molding.
Understanding how to balance runners is crucial for anyone involved in mold design, injection molding3, or manufacturing of plastic parts. This guide will walk you through the fundamentals, practical applications, and advanced techniques to help you achieve optimal results.
Balancing runners reduces material waste in injection molding.True
By ensuring uniform filling, balanced runners minimize defects and reduce the need for rework or scrap, saving material costs.
Balancing is only necessary for large multi-cavity molds.False
Even small multi-cavity molds benefit from balanced runners to maintain part consistency and quality.
What is Runner Balancing in Multi-Cavity Molds?
Runner balancing in multi-cavity molds is the process of designing the runner system so that molten plastic reaches each cavity at the same time and with the same pressure, ensuring uniform part quality.
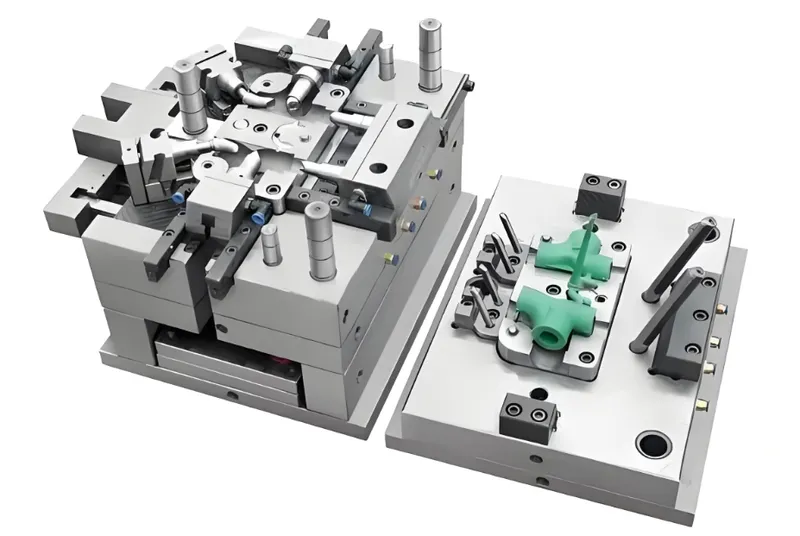
Runner balancing4 ensures equal flow of molten plastic to each cavity in multi-cavity molds, preventing defects and ensuring consistent part quality.
Runner System Type | Description | Notes |
---|---|---|
Cold Runner5 | Plastic in runners solidifies and is removed as waste. | Suitable for lower-volume production. |
Hot Runner6 | Runners remain molten, reducing waste and improving efficiency. | Ideal for high-volume production. |
Key Concepts in Runner Balancing
-
Multi-Cavity Mold: A mold with multiple identical cavities to produce several parts per cycle.
-
Runners: Channels that guide molten plastic from the injection point to the cavities.
-
Balancing7: Designing runners to ensure equal flow path lengths and consistent cross-sections for uniform filling.
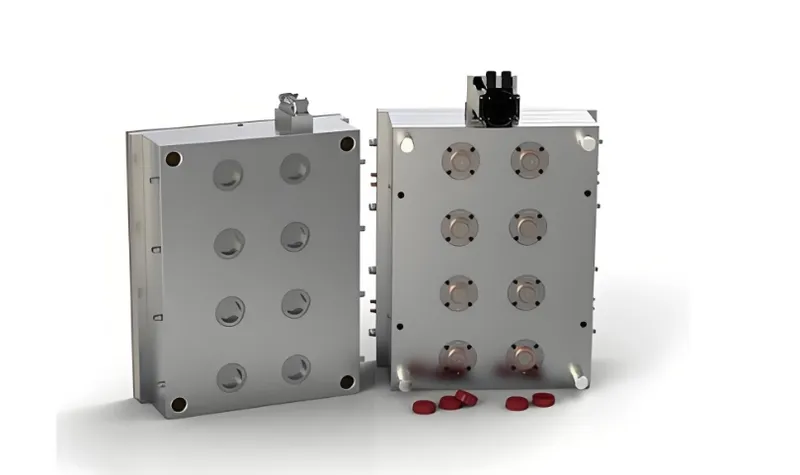
Types of Runner Systems
-
H-Type Runner Systems8: Symmetrical layout, inherently balanced but may require adjustments for larger molds.
-
Fishbone or Arbitrary Layouts: Used for specific designs, requiring precise balancing.
Runner balancing is essential in industries like automotive, packaging, and consumer electronics, where consistent part quality is critical.
Hot runner systems are always better for balancing.False
While hot runners offer better control, cold runners can also be balanced effectively with proper design.
Balanced runners improve production efficiency.True
Uniform filling reduces cycle times and minimizes defects, increasing overall efficiency.
Why is Runner Balancing Important in Injection Molding?
Runner balancing is crucial in injection molding because it directly impacts part quality, production efficiency, and cost-effectiveness.
Balanced runners ensure uniform part quality, reduce defects, and optimize material usage in multi-cavity molds.

Typical Application Scenarios
-
High-Volume Production9: Essential for mass-producing identical parts, such as bottle caps or automotive connectors.
-
Complex Parts: Critical when molding parts with tight tolerances or intricate geometries.
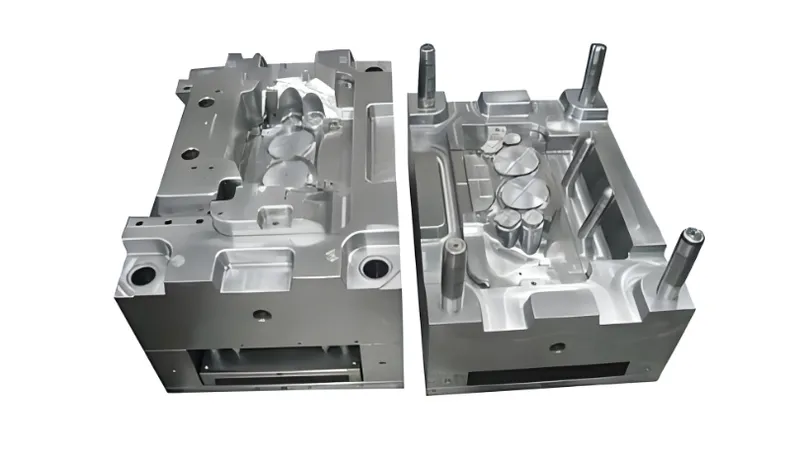
- Cost-Sensitive Projects10: Helps reduce per-part costs by minimizing waste and rework.
Pros and Cons of Balanced Runners
Aspect | Pros | Cons |
---|---|---|
Quality | Consistent part dimensions and properties. | Requires precise design and testing. |
Efficiency | Faster cycle times due to uniform filling. | Higher initial setup costs. |
Cost | Reduced material waste and lower defect rates. | Complex molds may be expensive to modify. |
Compared to unbalanced systems, balanced runners offer significant advantages in quality and efficiency, though they require more upfront investment in design and tooling.
Balanced runners eliminate all molding defects.False
While they reduce many defects, other factors like material properties or machine settings can still cause issues.
Balanced runners are essential for high-quality injection molding.True
They ensure uniform filling, which is critical for producing consistent, defect-free parts.
How to Balance Runners in Multi-Cavity Molds?
Balancing runners in multi-cavity molds involves careful design, material selection, and the use of advanced tools to ensure uniform filling of all cavities.
To balance runners, design equal flow paths, select appropriate materials, and use simulation software or hot runner systems for precise control.

Steps in the Runner Balancing Process
-
Determine Cavity Layout: Arrange cavities symmetrically to minimize flow path differences.
-
Calculate Runner Sizes: Ensure consistent runner diameters and lengths for equal flow resistance.
-
Select Runner System: Choose between cold or hot runners based on production volume and material.
-
Use Simulation Software: Tools like Moldflow predict flow behavior and identify potential imbalances.
-
Conduct Trial Runs: Test the mold and adjust runner sizes or temperatures as needed.
Material Considerations
- Viscosity: High-viscosity materials require larger runners or higher pressures.

-
Melt Flow Rate: Affects how easily the material fills the mold; inconsistent rates can disrupt balance.
-
Thermal Stability: Materials sensitive to temperature changes benefit from hot runner systems.
For example, polycarbonate (PC) has good dimensional stability but requires careful runner design due to its high viscosity.
Simulation software is essential for balancing runners.False
While helpful, experienced mold designers can balance runners without software, though it increases accuracy.
Material selection impacts runner balancing.True
Different materials have varying flow properties, affecting how runners should be designed.
What Tools and Techniques Help in Balancing Runners?
Several tools and techniques are available to assist in balancing runners, from design software to advanced molding technologies.
Simulation software, hot runner systems, and adjustable overflow cavities are key tools for achieving balanced runners in multi-cavity molds.
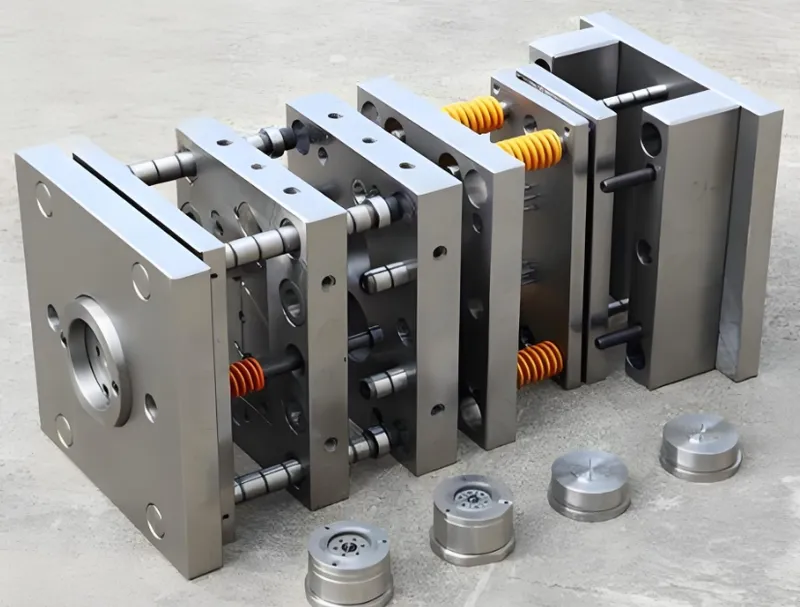
Practical Tools for Runner Balancing
-
Simulation Software: Moldflow or Autodesk Moldflow Insight predict flow behavior and optimize runner design.
-
Hot Runner Systems: Provide precise temperature control, reducing shear effects and improving balance.
-
Valve Gate Technology: Allows individual control of flow to each cavity, ideal for complex molds.
-
Melt Rotation Technologies: Techniques like MeltFlipper adjust melt distribution to address shear-induced imbalances.
Decision-Making Guide
- For High-Volume Production: Use hot runner systems for better control and reduced waste.

-
For Complex Parts: Consider valve gate technology or simulation software to fine-tune flow.
-
For Cost-Sensitive Projects: Start with cold runners and use simulation to optimize design.
Hot runner systems are always necessary for balancing.False
Cold runners can be balanced effectively, especially for lower-volume production.
Simulation software reduces trial and error in mold design.True
It allows designers to predict and correct issues before manufacturing the mold.
What are the Challenges in Balancing Runners?
Balancing runners in multi-cavity molds can be challenging due to factors like shear-induced imbalances and material variations.
Shear effects, material properties, and mold complexity can complicate runner balancing, requiring advanced techniques and careful design.
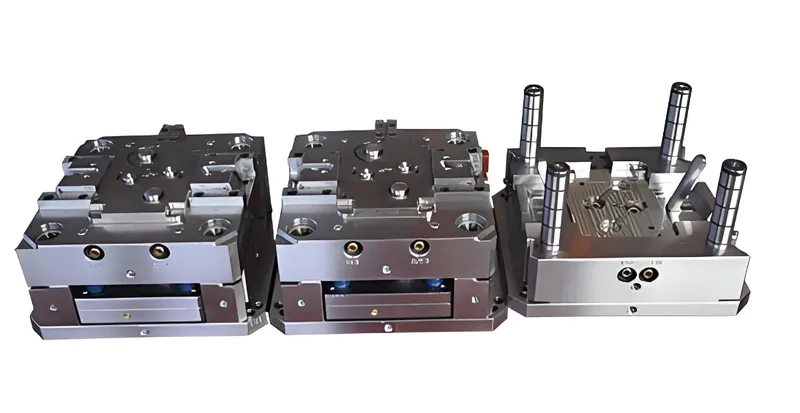
Common Challenges
-
Shear-Induced Imbalances: As plastic flows through runners, shear heat can cause viscosity variations, leading to uneven filling.
-
Material Variations: Differences in melt flow rate or shrink rate can disrupt balance.
-
Mold Complexity: Larger molds with many cavities are harder to balance due to cumulative flow path differences.
Solutions to Overcome Challenges
- Use Hot Runner Systems: Maintain consistent melt temperatures to reduce shear effects.
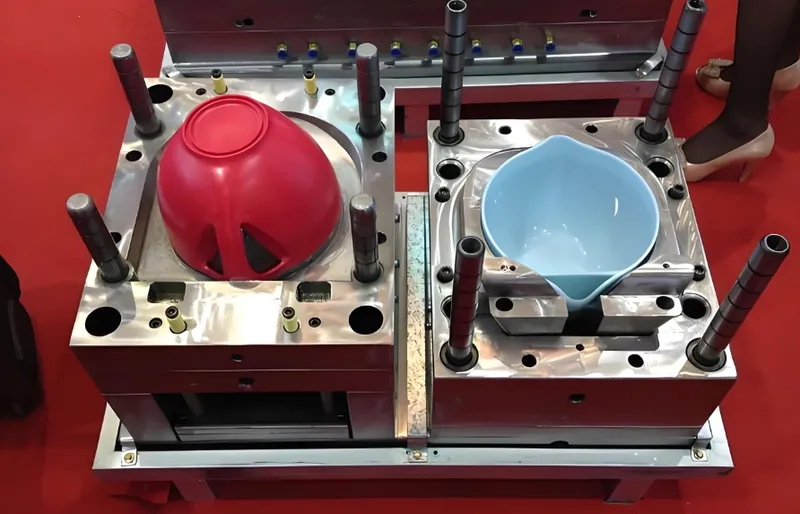
-
Incorporate Balancing Features: Add flow leaders, restrictors, or adjustable overflow cavities to fine-tune flow.
-
Leverage Simulation Software: Predict and address potential issues before mold construction.
For example, in molds with eight or more cavities, inner cavities may fill faster due to shear effects, requiring techniques like melt rotation to correct.
Balancing runners eliminates all production challenges.False
While it addresses flow issues, other factors like machine calibration or material consistency can still affect production.
Advanced techniques like melt rotation can address shear-induced imbalances.True
Technologies like MeltFlipper adjust melt distribution to ensure uniform filling.
Conclusion
Balancing runners in multi-cavity molds is essential for producing high-quality, consistent parts in injection molding. By designing equal flow paths, selecting appropriate materials, and using tools like simulation software and hot runner systems, manufacturers can optimize production and reduce costs. While challenges like shear-induced imbalances exist, advanced techniques and careful planning can overcome them. Understanding the principles and methods of runner balancing is key to success in injection molding.
-
This link will help you understand the advantages of multi-cavity molds and their impact on production efficiency. ↩
-
Exploring this resource will provide you with essential techniques and insights to optimize your injection molding process. ↩
-
Discover cutting-edge technologies and innovations in injection molding that can enhance your manufacturing processes. ↩
-
Understanding runner balancing is crucial for optimizing mold design and ensuring high-quality production. Explore this resource for in-depth insights. ↩
-
Learn about the benefits of cold runner systems, especially for lower-volume production, to enhance your manufacturing process. ↩
-
Discover how hot runner systems can improve efficiency and reduce waste in high-volume production scenarios. ↩
-
Learn about the significance of balancing in injection molding to ensure uniform part quality and efficiency in production. ↩
-
Discover the various runner systems used in injection molding and how they impact the manufacturing process and part quality. ↩
-
This link will help you understand the significance of high-volume production in achieving cost-effectiveness and quality in injection molding. ↩
-
Discover effective strategies to minimize costs in injection molding, especially for projects with budget constraints, by exploring this resource. ↩