Crystallinity in polymers plays a crucial role in determining the mechanical properties1, dimensional stability, and overall performance of injection-molded parts. Understanding how crystallinity affects the injection molding process2 is essential for engineers, designers, and manufacturers aiming to optimize product quality and efficiency.
Crystallinity in polymers3 refers to the degree of ordered molecular structure, which significantly influences the strength, stiffness, and shrinkage of molded parts, directly impacting the success of injection molding outcomes.
This article delves into the effects of crystallinity on injection molding, exploring its implications for material selection, process control, and final product performance. Whether you’re working in automotive, packaging, or medical device manufacturing, understanding crystallinity can help you make informed decisions to achieve the desired balance of properties in your molded parts.
Higher crystallinity in polymers always leads to better mechanical properties.False
While higher crystallinity often enhances tensile strength and heat resistance, it can also reduce impact resistance and increase shrinkage, which may not be desirable for all applications.
Crystallinity only affects the mechanical properties of polymers.False
Crystallinity also influences thermal properties, dimensional stability, and processing behavior during injection molding.
- 1. What is Crystallinity in Polymers and Why Does It Matter in Injection Molding?
- 2. How Does Crystallinity Affect the Injection Molding Process?
- 3. What are the Applications of Polymers with Different Crystallinity Levels in Injection Molding?
- 4. How to Select the Right Polymer for Your Injection Molding Project?
- 5. What are the Related Technologies and Processes?
- 6. Conclusion
What is Crystallinity in Polymers and Why Does It Matter in Injection Molding?
Crystallinity refers to the degree of structural order in a polymer’s molecular chains. Polymers can be classified as either amorphous4 (lacking ordered structure) or semi-crystalline5 (containing both ordered and disordered regions). This distinction is critical in injection molding, as it affects how the material behaves during processing and in the final product.
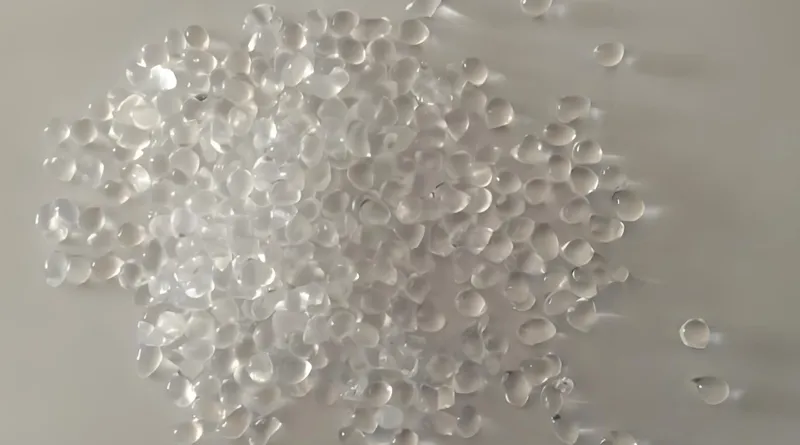
Crystallinity in polymers determines key properties like strength, stiffness, and shrinkage, which are vital for achieving desired outcomes in injection molding6, such as part durability and dimensional accuracy.
Polymer Type | Crystallinity Level | Key Properties |
---|---|---|
Amorphous (e.g., PS, PMMA) | Low | Flexibility, transparency, lower shrinkage |
Semi-crystalline (e.g., PE, PP) | High | Higher strength, stiffness, heat resistance, but greater shrinkage |
Amorphous Polymers
Amorphous polymers, such as polystyrene (PS) and poly(methyl methacrylate) (PMMA), have randomly arranged molecular chains. They are easier to mold due to lower shrinkage and are often chosen for applications requiring transparency or flexibility. However, they typically have lower heat and chemical resistance compared to semi-crystalline polymers.
Semi-crystalline Polymers
Semi-crystalline polymers, like polyethylene (PE) and polypropylene (PP), have regions of ordered molecular chains that enhance strength, stiffness, and heat resistance. However, these materials are prone to higher shrinkage and warpage during cooling, which can complicate the molding process. For example, in polypropylene, higher mold temperatures increase crystallinity, improving tensile strength but reducing impact resistance (Polypropylene Study).
Semi-crystalline polymers are always preferable for injection molding.False
While they offer higher strength and heat resistance, their higher shrinkage and longer cooling times can pose challenges in certain applications.
Amorphous polymers are easier to mold due to their lower shrinkage.True
Amorphous polymers exhibit less shrinkage during cooling, reducing the risk of warpage and simplifying the molding process.
How Does Crystallinity Affect the Injection Molding Process?
The injection molding process involves melting a polymer, injecting it into a mold, cooling it, and ejecting the solidified part. Crystallinity influences each stage, particularly during cooling, where the rate of crystallization affects the final part’s properties and dimensional stability.
Crystallinity affects the cooling phase of injection molding, influencing shrinkage, warpage, and mechanical properties, with higher crystallinity leading to greater shrinkage but improved strength.
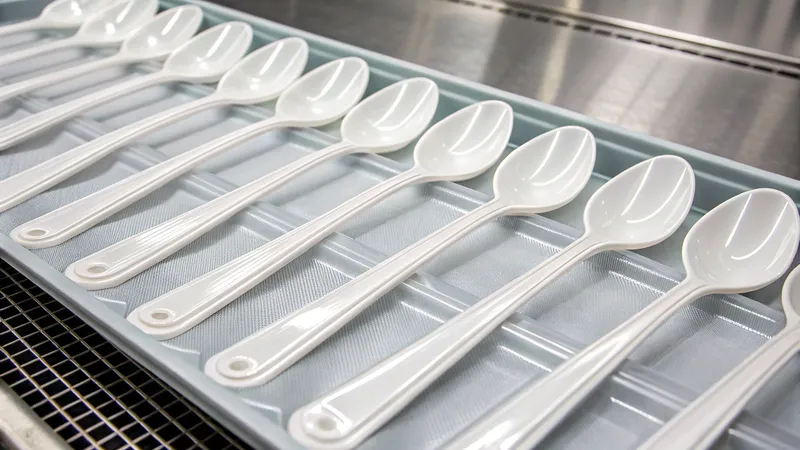
Material Preparation
Selecting the right polymer is crucial. Semi-crystalline polymers require careful consideration of their crystallization behavior, as it impacts processing parameters like mold temperature and cooling time.
Melt Preparation
The polymer is heated to a molten state. For semi-crystalline polymers, precise temperature control is essential to prevent premature crystallization or thermal degradation.
Injection
The molten polymer is injected into the mold. Injection speed and pressure can influence molecular orientation and crystallinity. High injection speeds may induce shear, affecting the crystalline structure in polymers like polypropylene (Polypropylene Study).
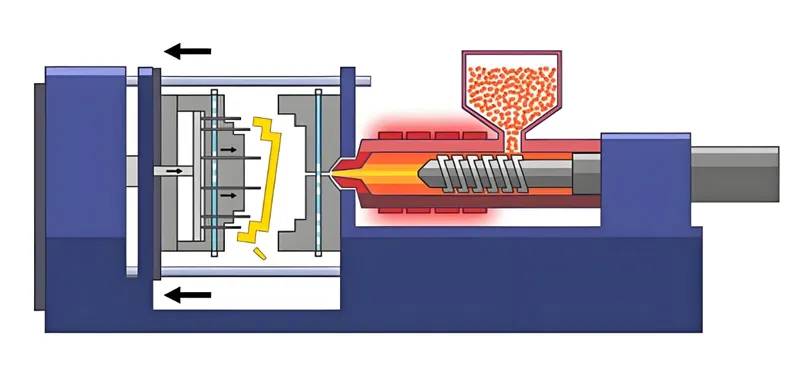
Cooling
Cooling is where crystallinity has the most significant impact. Slower cooling allows more time for crystal formation, increasing strength but also shrinkage. Faster cooling reduces crystallinity, minimizing shrinkage but potentially weakening the part. For instance, in polymer gears, higher mold temperatures and longer cooling times improve crystallinity and geometric quality (Polymer Gears Study).
Ejection
After cooling, the part is ejected from the mold. Residual stresses from crystallization can cause warpage, especially in semi-crystalline polymers, necessitating careful mold design and process control.
Faster cooling always improves part quality in injection molding.False
While faster cooling reduces cycle time, it can also lead to lower crystallinity, potentially weakening the part and increasing internal stresses.
Crystallinity can be controlled by adjusting mold temperature and cooling rate.True
Higher mold temperatures and slower cooling rates promote crystallinity, while lower temperatures and faster cooling reduce it.
What are the Applications of Polymers with Different Crystallinity Levels in Injection Molding?
The choice between amorphous and semi-crystalline polymers depends on the specific requirements of the application. Each type offers distinct advantages and challenges in various industries.
Amorphous polymers are ideal for applications requiring transparency and low shrinkage, while semi-crystalline polymers are suited for high-strength, heat-resistant parts, despite their higher shrinkage.
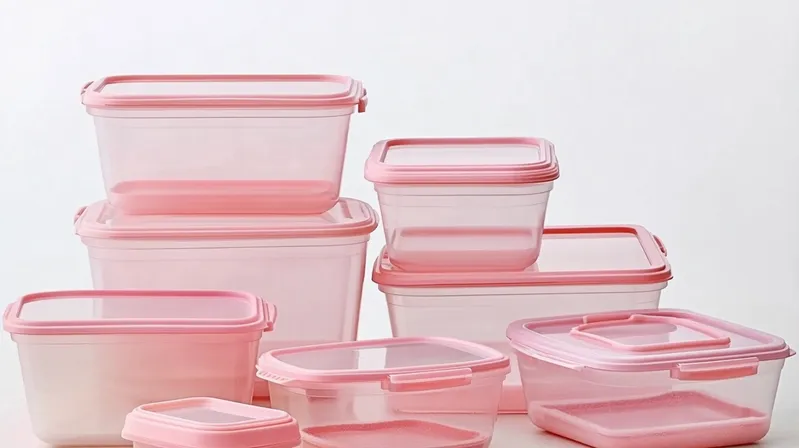
Packaging
-
Amorphous Polymers: Used for clear containers and lids due to their transparency and ease of molding.
-
Semi-crystalline Polymers: High-density polyethylene (HDPE) is used for rigid bottles and containers, benefiting from its strength and chemical resistance.
Automotive
- Semi-crystalline Polymers: Polypropylene and nylon are common for interior parts, under-hood components, and structural elements due to their durability and heat resistance.
Medical Devices
-
Amorphous Polymers: Polycarbonate (PC) is used for transparent medical trays and devices.
-
Semi-crystalline Polymers: Polyethylene and polypropylene are used for syringes and surgical instruments, where strength and sterilization compatibility are crucial.
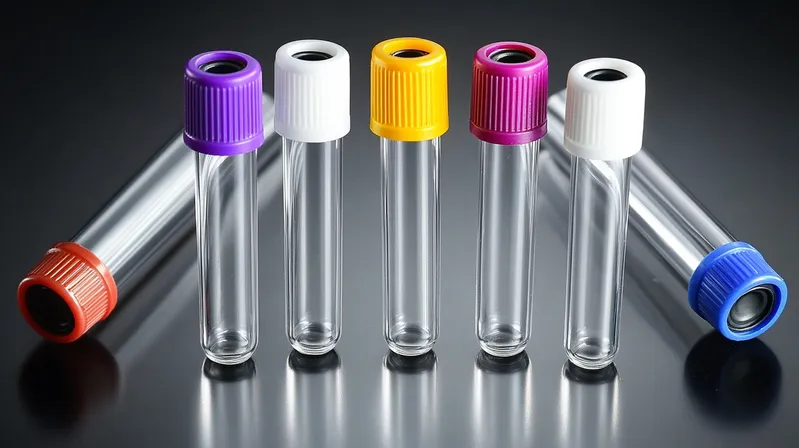
Mechanical Components
- Semi-crystalline Polymers: In applications like gears, higher crystallinity improves wear resistance and service life, though it may reduce impact resistance (Polymer Gears Study).
Amorphous polymers are unsuitable for high-strength applications.True
Amorphous polymers generally have lower strength and heat resistance compared to semi-crystalline polymers, making them less suitable for demanding applications.
Semi-crystalline polymers are always more challenging to mold than amorphous polymers.True
Their higher shrinkage and longer cooling times require more precise process control to avoid defects like warpage.
How to Select the Right Polymer for Your Injection Molding Project?
Choosing the appropriate polymer involves balancing the desired properties of the final part with the processing challenges associated with crystallinity. Below is a decision-making guide to help you select the right polymer type.
Select amorphous polymers for applications requiring low shrinkage and transparency, and semi-crystalline polymers for high strength and heat resistance, considering the trade-offs in processing complexity.
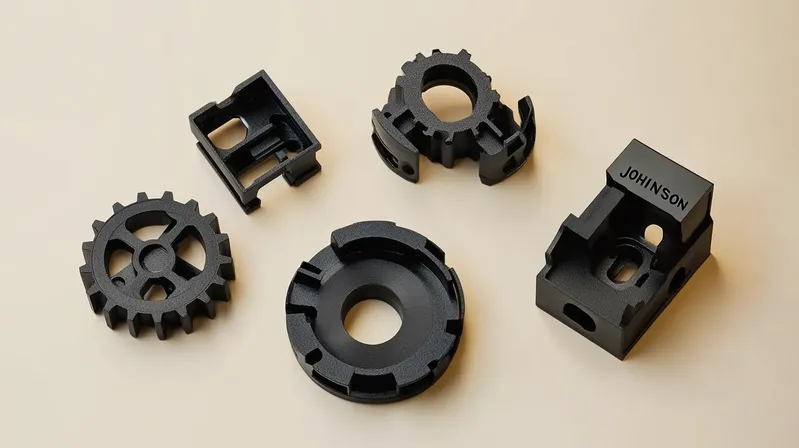
Design Checklist
-
Define Part Requirements: Identify critical properties such as strength, stiffness, heat resistance, transparency, and dimensional stability.
-
Evaluate Shrinkage and Warpage Risks: For semi-crystalline polymers, account for higher shrinkage and potential warpage in mold design.
-
Consider Processing Parameters: Adjust mold temperature, cooling rate, and injection speed to control crystallinity and achieve desired properties.
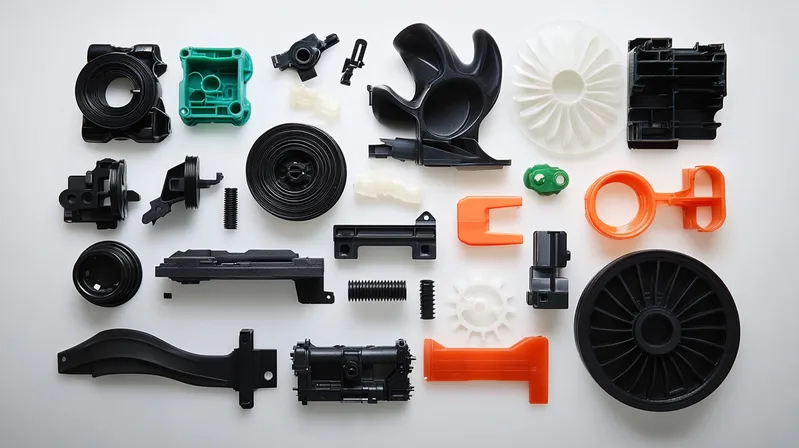
-
Use Simulation Tools: Predict how crystallinity will affect part quality and make necessary design adjustments.
-
Quality Control: Monitor for defects like shrinkage, warpage, or internal stresses during production.
Process Selection Decision-Making
Requirement | Recommended Polymer Type | Considerations |
---|---|---|
High strength, stiffness, heat resistance | Semi-crystalline (e.g., PP, PET) | Manage shrinkage and warpage; optimize cooling rates. |
Transparency, low shrinkage | Amorphous (e.g., PC, PMMA) | Simpler molding but lower strength and heat resistance. |
Fast production cycles | Amorphous or low-crystallinity polymers | Shorter cooling times but potential trade-offs in performance. |
Decision Tree Example:
- Is high strength or heat resistance critical?
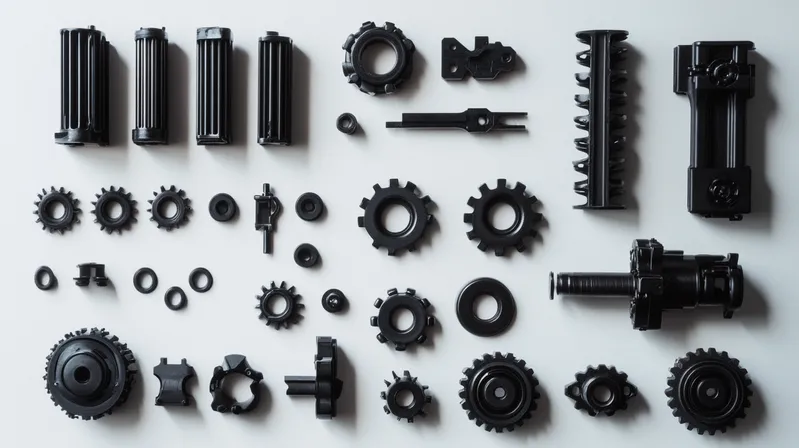
-
Yes → Choose semi-crystalline polymer → Optimize process parameters for crystallinity control.
-
No → Proceed to next question.
- Is transparency or minimal shrinkage critical?
-
Yes → Choose amorphous polymer → Simplify molding process.
-
No → Re-evaluate requirements or consider hybrid solutions.
Polymer selection is the only factor affecting injection molding outcomes.False
While polymer selection is crucial, process parameters like mold temperature, cooling rate, and injection speed also significantly influence outcomes.
Understanding crystallinity can help optimize both material selection and process control.True
By controlling crystallinity through material choice and processing conditions, manufacturers can achieve the desired balance of properties in molded parts.
Crystallinity in polymers is part of a broader ecosystem of technologies and processes that influence the final product. Understanding these can provide a more comprehensive view of polymer processing.
Related technologies include polymer synthesis, material characterization, and downstream processes like part design and application engineering, all of which are influenced by crystallinity.
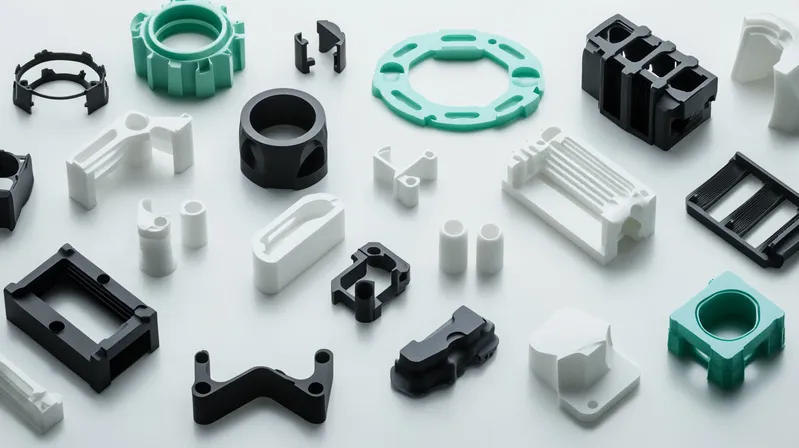
Upstream Technologies
-
Polymer Synthesis: Controlling molecular weight and branching to influence crystallinity.
-
Material Characterization: Techniques like X-ray diffraction to measure crystallinity and predict processing behavior (Polypropylene Study).
Downstream Technologies
- Part Design: Accounting for anisotropy and shrinkage due to crystallinity.
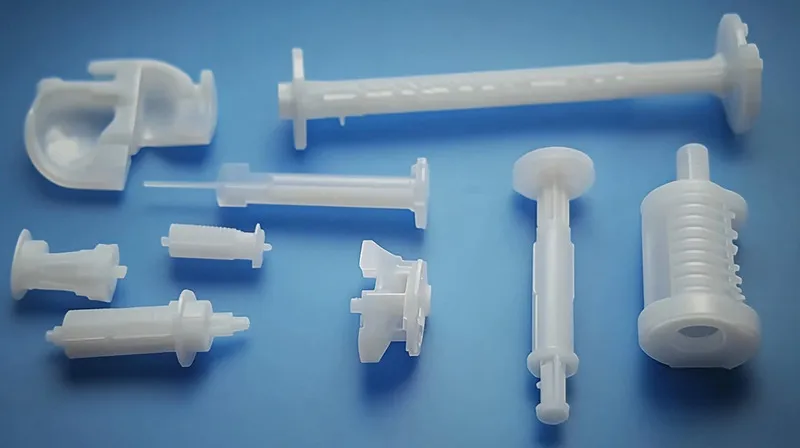
- Application Engineering: Ensuring the part performs as expected in its end-use environment, considering properties influenced by crystallinity.
Alternative Processes
- Extrusion, Blow Molding, Thermoforming: These processes also involve polymers with varying crystallinity levels, but the effects differ based on the specific process mechanics.
Crystallinity only affects injection molding and not other polymer processing methods.False
Crystallinity influences properties in various processing methods, though the specific impacts may vary.
Conclusion
Crystallinity is a fundamental property of polymers that significantly impacts injection molding outcomes. By understanding how crystallinity7 affects mechanical properties, dimensional stability, and processing behavior, manufacturers can make informed decisions about material selection and process control. Whether opting for the strength and heat resistance of semi-crystalline polymers or the ease of molding and transparency of amorphous polymers8, balancing these factors is key to achieving optimal results.
-
Learn about the mechanical properties of polymers and their relationship with crystallinity to enhance your understanding of material performance. ↩
-
This resource will provide insights into the injection molding process and the critical factors influencing its efficiency and product quality. ↩
-
Explore this link to understand how crystallinity impacts the mechanical properties and performance of polymers in injection molding. ↩
-
Exploring this resource will provide insights into the unique characteristics and uses of amorphous polymers, enhancing your understanding of their applications. ↩
-
This link will help you understand the benefits and challenges of using semi-crystalline polymers in various applications, crucial for material selection. ↩
-
Understanding this relationship is key for optimizing injection molding techniques and improving product quality, making this resource invaluable. ↩
-
Understanding crystallinity is crucial for optimizing polymer properties and processing techniques. Explore this link to deepen your knowledge. ↩
-
Learn about the unique properties of amorphous polymers, which can enhance molding ease and transparency in products. ↩