Biodegradable plastics are revolutionizing the injection molding1 industry by offering sustainable alternatives to traditional petroleum-based plastics. These materials, derived from renewable sources, decompose naturally, reducing environmental impact. However, their integration into injection molding processes requires specific adjustments and considerations.
Biodegradable plastics, such as PLA and PHA2, are increasingly used in injection molding for eco-friendly products, but they demand precise handling due to moisture sensitivity and unique mechanical properties.
Understanding how biodegradable plastics3 affect injection molding is crucial for manufacturers aiming to adopt sustainable practices. This post delves into the key aspects of using these materials, from basic concepts to technical details and practical applications.
Biodegradable plastics can be processed using standard injection molding equipment.True
Most biodegradable plastics are compatible with existing machinery, though adjustments in temperature and drying are often necessary.
Biodegradable plastics always offer the same mechanical properties as traditional plastics.False
Biodegradable plastics often have different strength, flexibility, and thermal properties, requiring design modifications.
- 1. What Are Biodegradable Plastics and How Do They Affect Injection Molding?
- 2. How Are Biodegradable Plastics Classified for Injection Molding?
- 3. What Are the Typical Applications of Biodegradable Plastics in Injection Molding?
- 4. What Are the Key Steps in the Injection Molding Process for Biodegradable Plastics?
- 5. How Do Different Biodegradable Plastics Affect the Injection Molding Process?
- 6. What Are the Practical Considerations for Using Biodegradable Plastics in Injection Molding?
- 7. What Are the Related Technologies and Future Trends in Biodegradable Plastics for Injection Molding?
- 8. Conclusion
What Are Biodegradable Plastics and How Do They Affect Injection Molding?
Biodegradable plastics are materials that decompose naturally through microbial action, typically derived from renewable resources like corn starch or sugarcane. In injection molding, they offer a sustainable alternative but require specific processing conditions.

Biodegradable plastics, including PLA and PHA, are used in injection molding for products like packaging and consumer goods, but their moisture sensitivity and thermal properties4 necessitate adjustments in the molding process.
Material Type | Common Applications | Notes |
---|---|---|
PLA (Polylactic Acid)5 | Food containers, disposable cutlery | Requires drying before processing |
PHA (Polyhydroxyalkanoates)6 | Medical devices, flexible packaging | Offers better flexibility than PLA |
Polylactic Acid (PLA)
PLA is a widely used biodegradable plastic made from fermented plant starch. It is rigid and suitable for products like food containers and utensils. However, PLA is sensitive to moisture and requires thorough drying before injection molding to prevent degradation (Bennett Plastics).
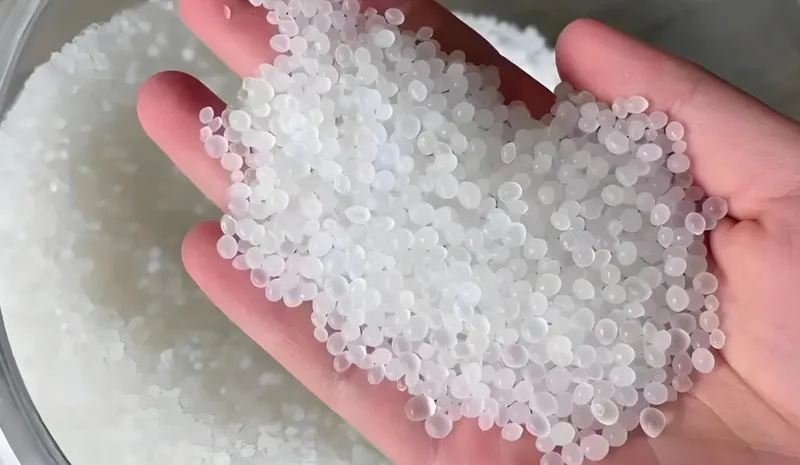
Polyhydroxyalkanoates (PHA)
PHA is produced by bacterial fermentation and is fully biodegradable. It offers greater flexibility than PLA, making it ideal for applications like flexible packaging and medical devices. Like PLA, PHA requires careful handling to avoid moisture-related issues7 (Stelray).
PLA is the most commonly used biodegradable plastic in injection molding.True
PLA is popular due to its availability, cost-effectiveness, and suitability for rigid products.
Biodegradable plastics are always more expensive than traditional plastics.False
While often costlier, prices are decreasing with technological advancements and increased production.
How Are Biodegradable Plastics Classified for Injection Molding?
Understanding the classification of biodegradable plastics helps in selecting the right material for specific injection molding applications8.
Biodegradable plastics are classified by source (bio-based9 or fossil-based), degradability, and application suitability, influencing their use in injection molding for packaging, consumer goods, and technical parts.

By Source
-
Bio-based: Derived from renewable resources (e.g., PLA, PHA).
-
Fossil-based: Petroleum-derived but biodegradable (e.g., PBAT).
By Degradability
-
Biodegradable: Decompose naturally (e.g., PLA, PHA).
-
Non-biodegradable: Bio-based but not degradable (e.g., some bio-based PET).
By Application
-
Packaging: Food containers, bags.
-
Consumer Goods: Cutlery, pens.
-
Technical Parts: Automotive components, medical devices.
All bio-based plastics are biodegradable.False
Some bio-based plastics, like bio-based PET, do not biodegrade.
Biodegradable plastics can be used in high-performance applications.True
Materials like PHA are used in medical devices due to their biocompatibility and strength.
What Are the Typical Applications of Biodegradable Plastics in Injection Molding?
Biodegradable plastics are increasingly used in various industries, offering sustainable solutions without compromising functionality.
Biodegradable plastics are commonly used in packaging, consumer goods, and technical parts, providing eco-friendly alternatives that meet regulatory and consumer demands.
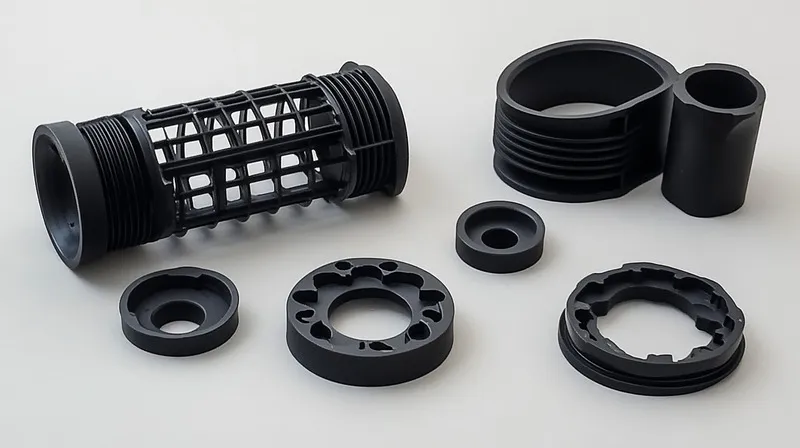
Packaging
Biodegradable plastics like PLA are ideal for food containers, bags, and coffee capsules, where sustainability is a key selling point (BIO-FED).
Consumer Goods
Products such as cutlery, pens, and toys benefit from biodegradable plastics, appealing to environmentally conscious consumers (ENGEL).
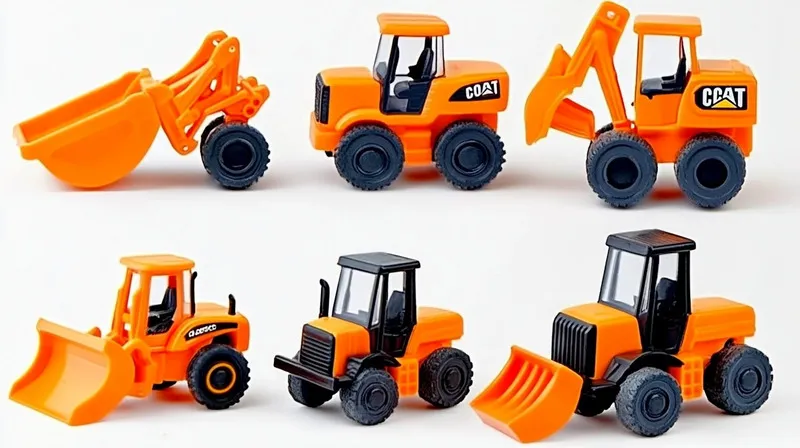
Technical Parts
In industries like automotive and medical, biodegradable plastics are used for components like panels and sutures, where performance and sustainability align (Stelray).
Biodegradable plastics are only suitable for disposable products.False
They are also used in durable goods like automotive parts and medical devices.
Biodegradable plastics reduce environmental impact in all applications.True
They minimize waste and reliance on fossil fuels, though proper disposal is necessary.
What Are the Key Steps in the Injection Molding Process for Biodegradable Plastics?
The injection molding process for biodegradable plastics requires specific adjustments to accommodate their unique properties.
The process involves material selection, drying, melting, injection, cooling, and ejection, with critical attention to moisture control and temperature settings.
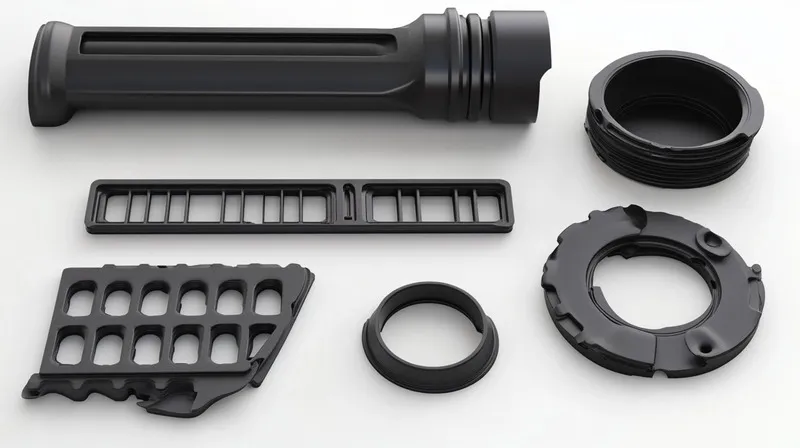
Material Selection
Choose the appropriate biodegradable plastic based on product requirements (e.g., rigidity for PLA, flexibility for PHA).
Drying
Biodegradable plastics are moisture-sensitive and must be thoroughly dried to prevent degradation during processing (Bennett Plastics).
Melting
Adjust temperatures to the material’s melting point (e.g., PLA: 180–220°C), which may differ from traditional plastics.
Injection
Optimize pressure and speed for the material’s flow characteristics, as biodegradable plastics may have unique viscosities.
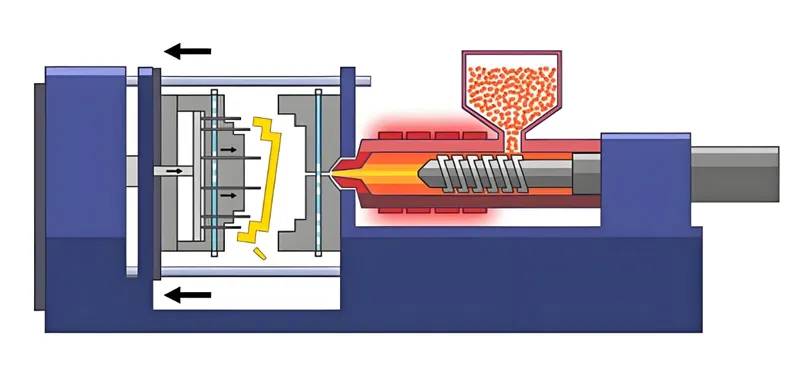
Cooling
Ensure proper cooling to avoid thermal degradation, using tools like agitating hoppers if necessary.
Ejection
Use compatible mold release agents to prevent sticking, considering potential gas emissions from biodegradation.
Biodegradable plastics require longer cycle times in injection molding.False
Cycle times are similar to traditional plastics, though adjustments may be needed for cooling and drying.
Moisture control is critical when processing biodegradable plastics.True
Moisture can cause hydrolysis, leading to material degradation during molding.
How Do Different Biodegradable Plastics Affect the Injection Molding Process?
The choice of biodegradable plastic significantly impacts the injection molding process, from material handling to final product properties.
Different biodegradable plastics, like PLA and PHA, require specific processing conditions due to their varying thermal and mechanical properties.
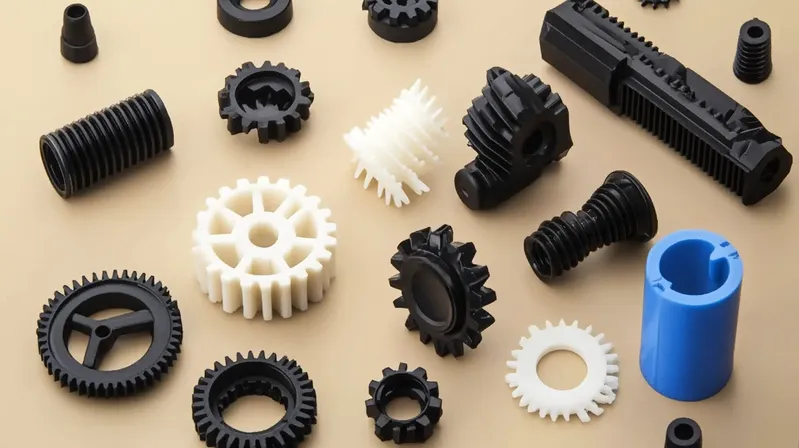
PLA
-
Processing: Requires drying and specific temperature control (180–220°C).
-
Properties: Rigid, suitable for high-strength applications but brittle without modification.
PHA
- Processing: Similar to PLA but with a broader temperature range.

- Properties: More flexible, better for applications requiring durability.
Blends and Composites
Blending PLA with elastomers or other bioplastics can enhance impact strength and flexibility, as shown in studies where PLA blends increased elongation and impact resistance (Green Dot Study).
PLA can be modified to improve its flexibility for injection molding.True
Blending PLA with elastomers enhances its impact strength and flexibility.
All biodegradable plastics have the same processing requirements.False
Each material has unique thermal and mechanical properties, necessitating specific adjustments.
What Are the Practical Considerations for Using Biodegradable Plastics in Injection Molding?
Manufacturers must consider several factors to successfully integrate biodegradable plastics into their injection molding processes.
Key considerations include material compatibility, drying procedures, processing parameters, and design adjustments to accommodate the properties of biodegradable plastics.
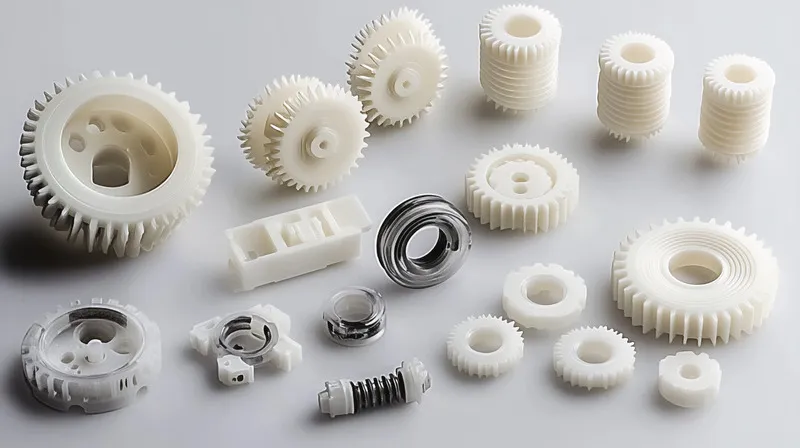
Design Checklist
-
Confirm material compatibility with the application and disposal environment.
-
Implement robust drying procedures for moisture-sensitive bioplastics.
-
Adjust processing parameters (temperature, pressure, cooling time) per material specifications.
-
Account for shrinkage or warpage differences in part design.
-
Ensure mold designs include adequate venting for gases from biodegradable materials.
Process Selection Decision-Making
Biodegradable plastics are suitable when:
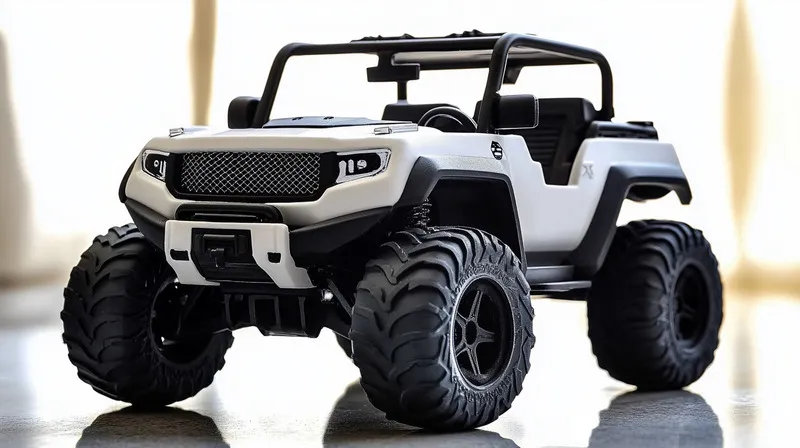
-
Sustainability is a priority.
-
Production volumes justify material costs.
-
Part design aligns with material properties.
Decision Tree:
- Define sustainability goals.
- Assess material properties against product requirements.
- Evaluate production volume and equipment compatibility.
- Verify disposal infrastructure.
Biodegradable plastics can be used without any changes to existing injection molding processes.False
Adjustments in drying, temperature, and design are often necessary.
Proper drying is essential for successful injection molding with biodegradable plastics.True
Moisture can lead to defects and material degradation.
The adoption of biodegradable plastics in injection molding is part of a broader shift towards sustainable manufacturing, with several related technologies and trends emerging.
Related technologies include bioplastic production, composting infrastructure, and design for biodegradability, while future trends point to increased market share and innovation in material properties.

Upstream Technologies
-
Bioplastic production (e.g., fermentation for PHA).
-
Feedstock development (e.g., agricultural waste).
Downstream Technologies
-
Composting facilities for end-of-life management.
-
Recycling technologies, though less common for biodegradable plastics.
Future Trends
-
Growing market demand driven by regulations and consumer preferences.
-
Innovations in material blends to enhance performance (Grand View Research).
The market for biodegradable plastics is expected to grow significantly.True
Increasing environmental awareness and regulatory pressures are driving adoption.
Biodegradable plastics will completely replace traditional plastics in injection molding.False
While adoption is growing, traditional plastics still dominate due to cost and performance advantages in some applications.
Conclusion
Biodegradable plastics are transforming injection molding by offering sustainable alternatives10 to traditional materials. While they require specific handling and processing adjustments, their environmental benefits and growing market demand make them a viable option for manufacturers. As technology advances and costs decrease, biodegradable plastics are poised to play a significant role in the future of injection molding.
-
Discover how injection molding processes adapt to biodegradable plastics for eco-friendly production methods. ↩
-
Learn about PLA and PHA, two key types of biodegradable plastics, and their applications in sustainable manufacturing. ↩
-
Explore this link to understand the advantages of biodegradable plastics in injection molding and their environmental impact. ↩
-
Discover how moisture sensitivity and thermal properties affect the performance of biodegradable plastics in manufacturing. ↩
-
Learn about PLA’s properties and its role in sustainable packaging solutions by visiting this resource. ↩
-
Discover the unique benefits of PHA in medical and flexible packaging applications by checking out this informative link. ↩
-
Understanding how to manage moisture-related issues is crucial for the effective use of biodegradable plastics, making this resource valuable for practical applications. ↩
-
Discover best practices for using biodegradable plastics in injection molding, ensuring optimal performance and sustainability in your applications. ↩
-
Learn about bio-based biodegradable plastics and their advantages, which can help you choose sustainable materials for your projects. ↩
-
Discover various sustainable alternatives to traditional plastics and their benefits for the environment and industry. ↩