All Posts
blog & article
read our latest newsletter
Whether you’re curious about material selection, product design, mold design, mold making and injection molding, feel free to ask us anything. Our team is ready to provide the guidance and insights you need.

How Does the Cavity Function in Injection Molding?
This article explores the critical role of cavities in injection molding, detailing how they shape products and affect quality. It covers single-cavity versus multi-cavity molds, their applications, and the importance of temperature control and surface finishes. Understanding these elements helps ...
DEVELOPMENT
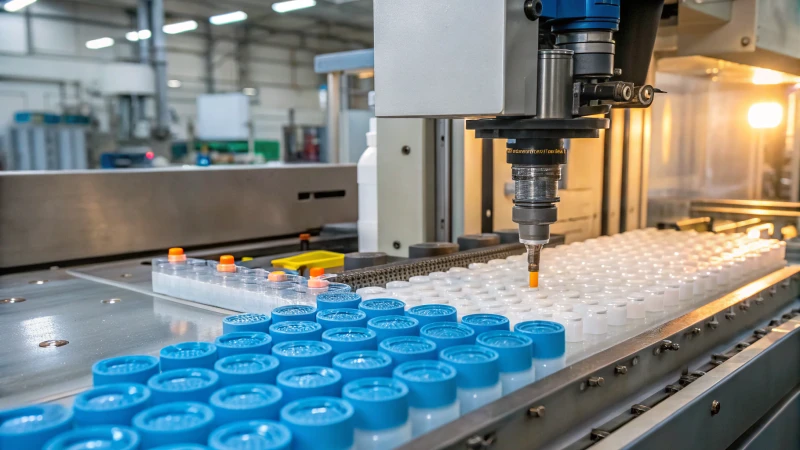
How Do Injection Molding Machines Produce Bottle Caps?
The process of producing bottle caps using injection molding involves designing precise molds, selecting suitable materials like polypropylene, and employing an injection machine to shape the caps. Quality control is crucial to ensure each cap meets industry standards. After molding, ...
MANUFACTURING
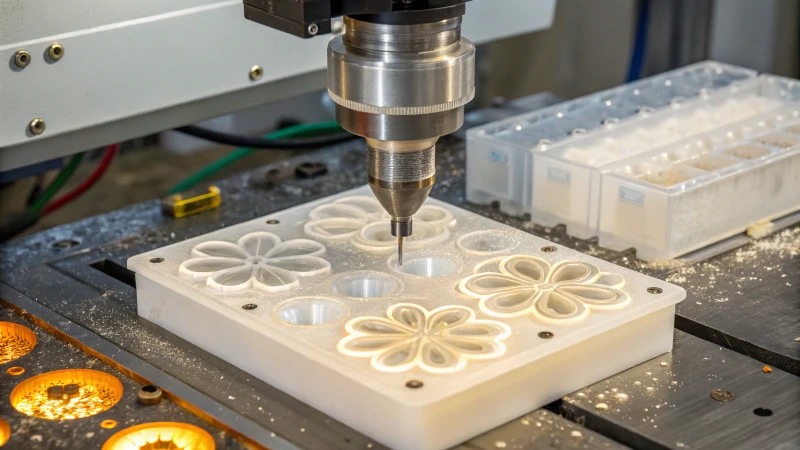
How Do Injection Molding Machines Create Plastic Flowers?
This article explores how injection molding machines bring plastic flowers to life. It delves into the importance of mold design, material selection, and the operational process involved in creating these lifelike floral components. The piece highlights the significance of choosing ...
MANUFACTURING
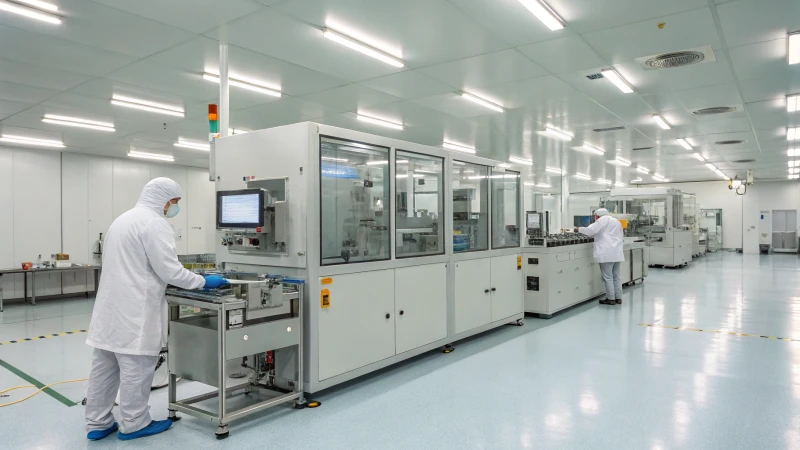
When Should You Use Clean Room Injection Molding?
Clean room injection molding is essential in various industries such as medical devices, pharmaceuticals, electronics, and aerospace. This process ensures that products are free from contaminants like dust and bacteria, which can compromise safety and functionality. In medical device manufacturing, ...
Quality Inspection
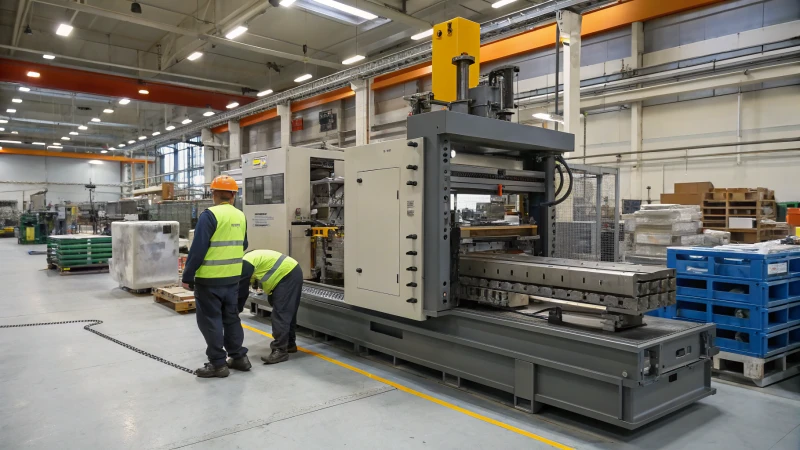
What Size Injection Molding Machine is Needed for an Air Conditioning Shell?
Selecting the appropriate injection molding machine for air conditioning shells involves evaluating several factors including shell dimensions, structural complexity, material type, and mold cavity count. Machines generally require clamping forces between 650 to 1350 tons. Larger or more complex shells ...
MANUFACTURING
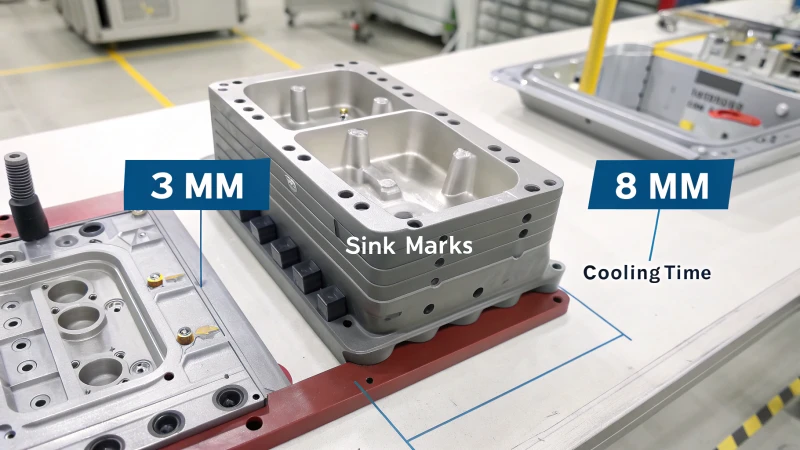
What is the Maximum Wall Thickness Allowed for Injection Molding?
This article explores the optimal wall thickness for injection molding, emphasizing that while the general guideline is 3-4 mm for most thermoplastics, certain materials and designs may allow for thicker walls up to 6-8 mm. Factors such as flow characteristics, ...
DEVELOPMENT
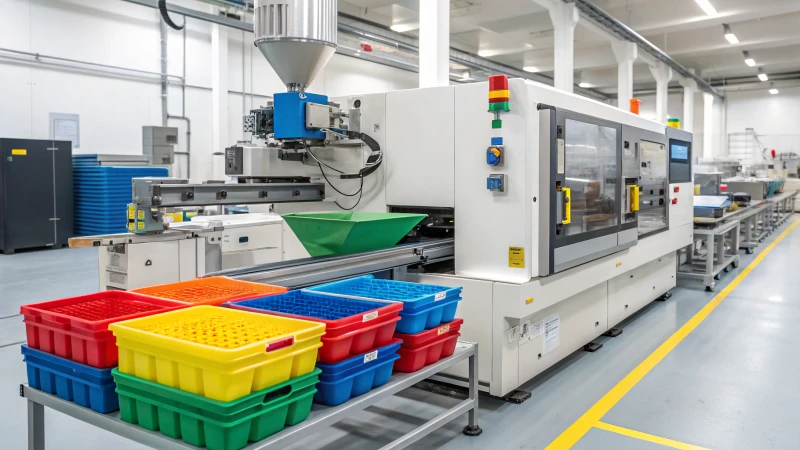
How Efficiently Can Injection Molding Machines Produce Toolboxes?
Injection molding is a powerful method for producing toolboxes quickly and efficiently. This process offers remarkable design flexibility, allowing intricate shapes and features to be created. Materials such as high-density polyethylene (HDPE) and polypropylene (PP) ensure durability while maintaining lightweight ...
Uncategorized
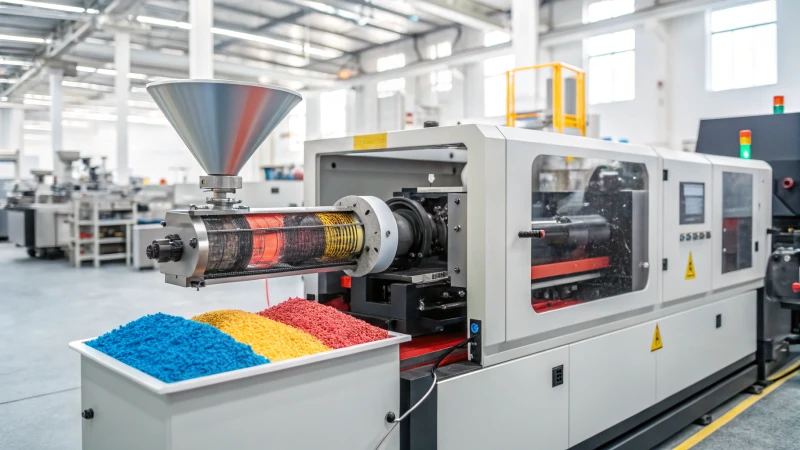
How Much Capacity Does a Plastic Injection Molding Machine Have?
This article explores the essential factors determining the capacity of plastic injection molding machines: clamping force, shot volume, and production rate. Clamping force is vital for maintaining mold integrity during injection; small machines typically exert 5-10 tons while large industrial ...
MANUFACTURING
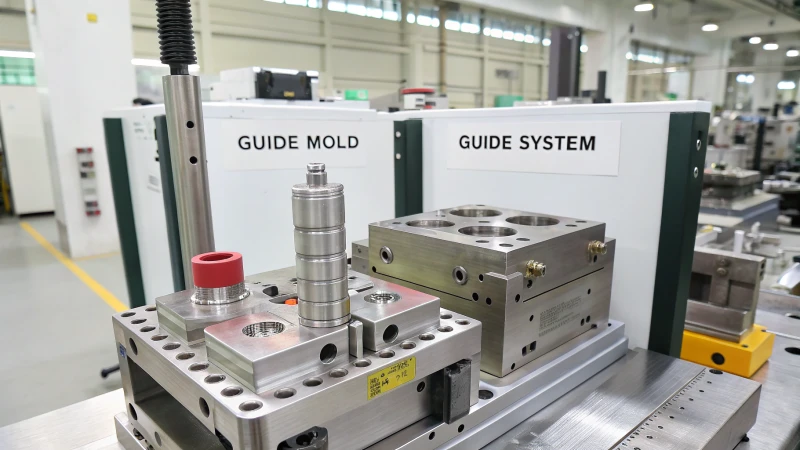
How Does the Injection Mold Guide System Work?
The injection mold guide system is essential for achieving precision in manufacturing. It consists of guide pillars and bushings that ensure accurate mold closure and distribute clamping forces evenly. This prevents wear and tear on molds, enhancing their longevity and ...
Uncategorized

How Can Injection Molded Parts Be Recycled Effectively?
Recycling injection molded parts is essential for sustainability. The process begins with sorting materials using techniques like visual inspection and infrared spectroscopy. Cleaning removes contaminants before reprocessing through mechanical or chemical methods. Mechanical recycling melts plastics into new products, while ...
DEVELOPMENT
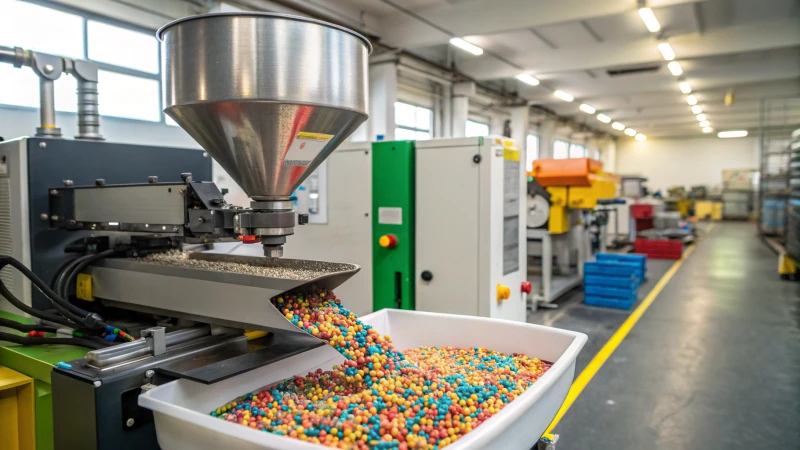
How Can an Injection Molding Machine Produce Plastic Spoons?
This article explores the fascinating process of producing plastic spoons using injection molding machines. It details how these machines melt plastic pellets and inject molten plastic into spoon-shaped molds under high pressure. The method ensures high precision and efficiency while ...
MANUFACTURING
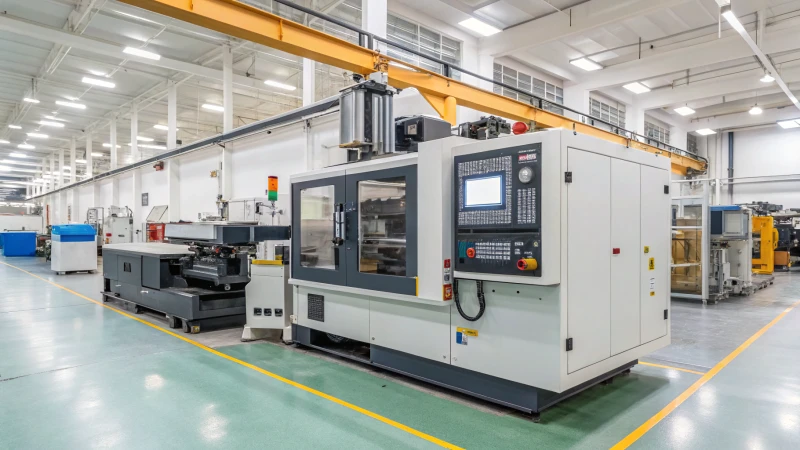
How Do You Determine the Capacity of a Plastic Injection Molding Machine?
Understanding the capacity of plastic injection molding machines involves three key factors: clamping force, shot volume, and production rate. Clamping force, measured in tons, ensures molds remain closed during injection to prevent defects. Shot volume indicates the maximum amount of ...
MANUFACTURING
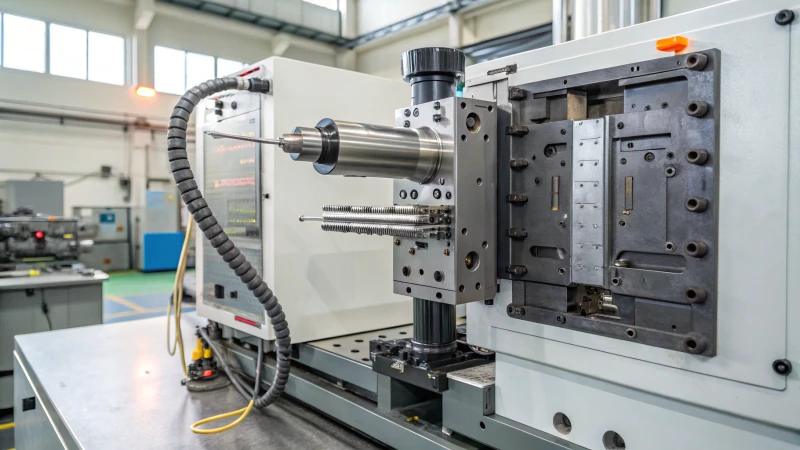
Can One Injection Molding Machine Fit Any Mold?
This article explores why one injection molding machine cannot fit every mold. It discusses critical factors such as clamping force, injection capacity, mold size, and pressure requirements that influence compatibility. Understanding these elements is crucial for product designers to avoid ...
MANUFACTURING
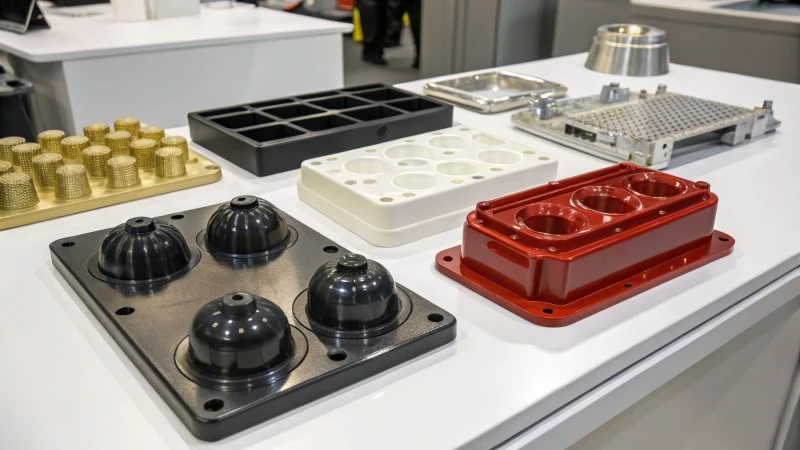
What Are the Most Common Surface Finishing Techniques for Injection Molded Parts?
This article delves into the most common surface finishing techniques for injection molded parts, such as painting, electroplating, hot stamping, silk screening, pad printing, laser engraving, frosting, and polishing. Each method is designed to enhance both the appearance and performance ...
MANUFACTURING
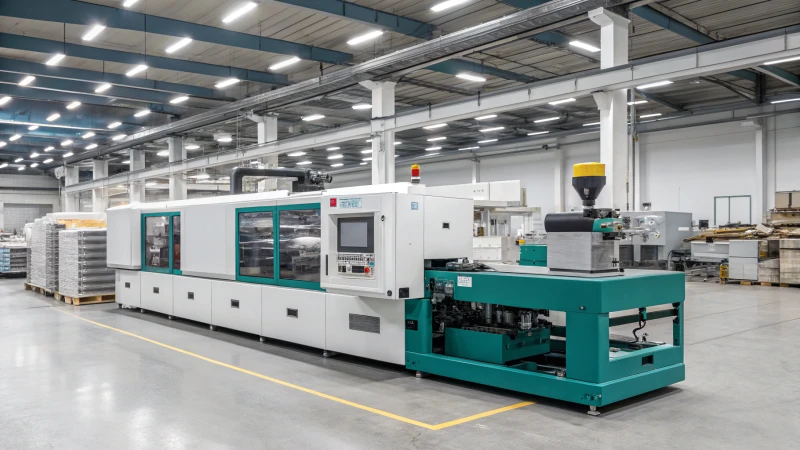
What Impact Will Global Market Trends Have on the Injection Molding Industry?
The injection molding industry is undergoing significant transformation due to global market trends. Increasing demand for lightweight components in the automotive sector, personalized designs in home appliances, and sustainable practices are reshaping manufacturing processes. The rise of electric vehicles necessitates ...
DEVELOPMENT
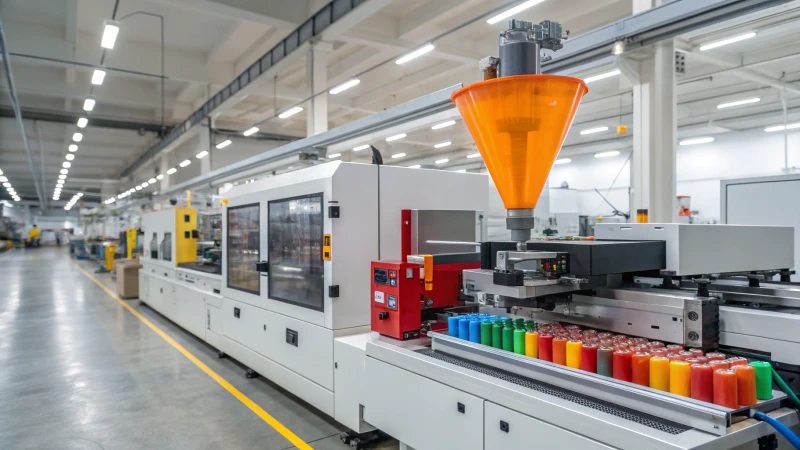
How Does the Injection Rate Affect Injection Molding Efficiency?
Understanding the injection rate is crucial in injection molding as it directly impacts part quality, surface finish, and overall efficiency. A well-calibrated injection rate ensures complete mold filling while minimizing defects such as air entrapment or short shots. Factors influencing ...
MANUFACTURING
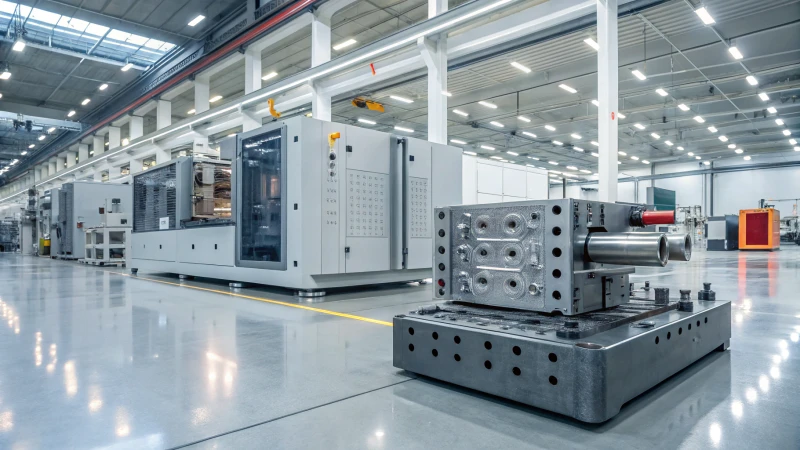
What Challenges Do Startups Face in Injection Molding?
Startups entering the injection molding industry encounter significant hurdles, including exorbitant equipment and mold costs, difficulties in attracting skilled talent, and intense market competition. These challenges necessitate careful strategic planning and effective resource management to ensure growth and sustainability. Funding ...
MANUFACTURING
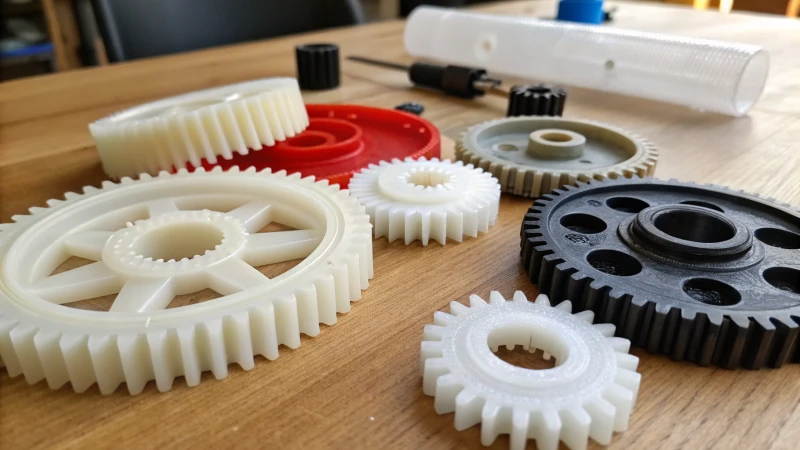
How Can You Texture Injection Molded Surfaces Effectively?
This article delves into various methods for effectively texturing injection molded surfaces. Techniques such as Electrical Discharge Machining (EDM), chemical etching, laser texture processing, and mechanical engraving are explored. Each method offers unique benefits tailored to specific design needs and ...
MANUFACTURING
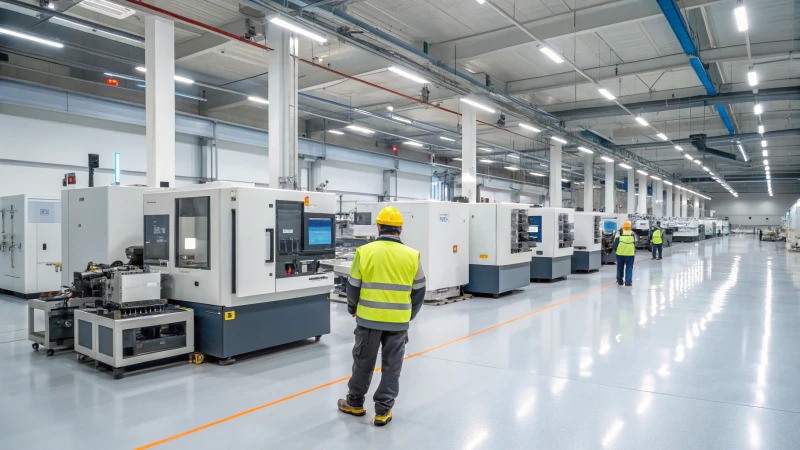
How Can You Ensure Quality Consistency from Suppliers in Injection Molding?
This article explores strategies for ensuring quality consistency from suppliers in injection molding. It emphasizes the importance of thorough supplier evaluations, clear contract agreements detailing quality standards, vigilant production oversight, and ongoing quality improvement measures. By implementing a structured approach ...
Quality Inspection
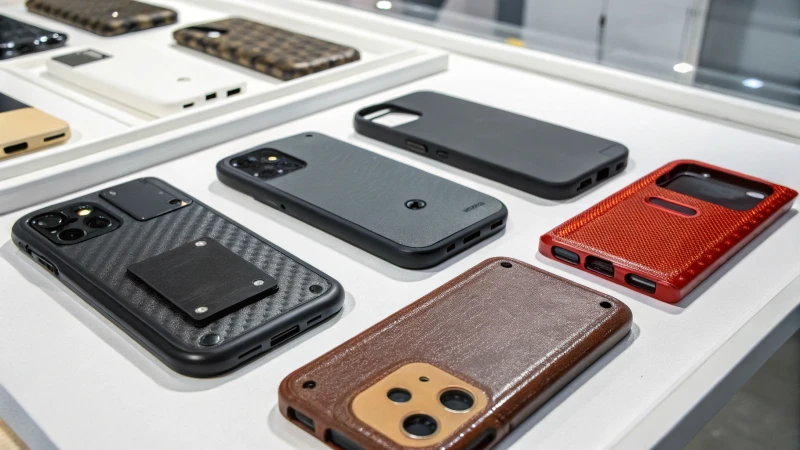
What Are the Key Standards for Injection Molded Electronic Casings?
This article explores the essential standards for designing injection molded electronic casings. It covers critical aspects such as dimension and tolerance controls, material performance requirements, appearance quality considerations, functionality standards like electromagnetic compatibility (EMC), waterproofing ratings, and rigorous quality inspection ...
Quality Inspection
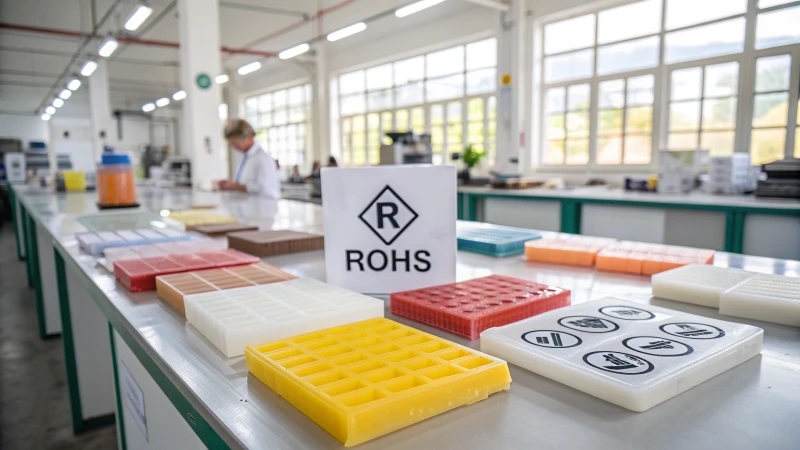
What Impact Do RoHS Directives Have on Injection Molding Materials?
The RoHS Directive significantly influences injection molding materials by enforcing strict restrictions on hazardous substances like heavy metals and brominated flame retardants. This shift compels manufacturers to seek alternative, compliant materials, often leading to increased production costs due to higher ...
MANUFACTURING
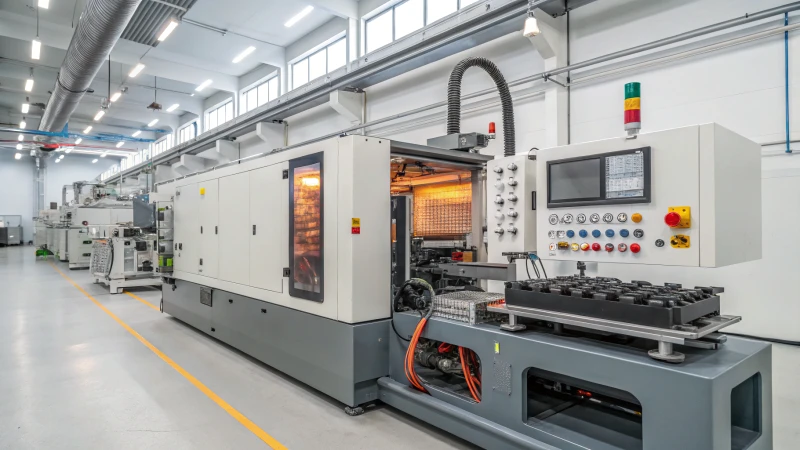
What Key Design Considerations Ensure Success in Injection Molding High-Temperature Parts?
This article explores essential design considerations for injection molding high-temperature parts. It emphasizes the importance of selecting appropriate materials like PPS and PEEK based on temperature tolerance, ensuring uniform wall thickness to prevent thermal stress, and implementing effective heat dissipation ...
DESIGN
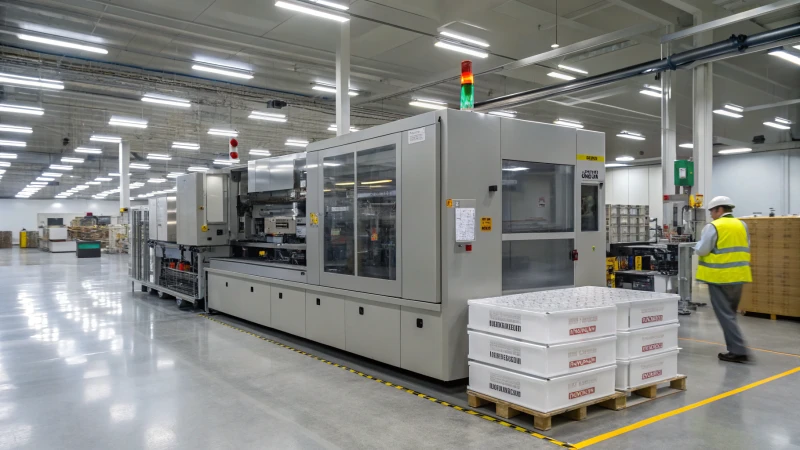
What Are the Steps to Comply with REACH Regulations in Injection Molding?
Navigating REACH compliance in injection molding is crucial for product safety and market access. This article provides a comprehensive overview of the necessary steps, including selecting compliant materials, managing suppliers effectively, maintaining rigorous process controls, and keeping detailed records. By ...
MANUFACTURING
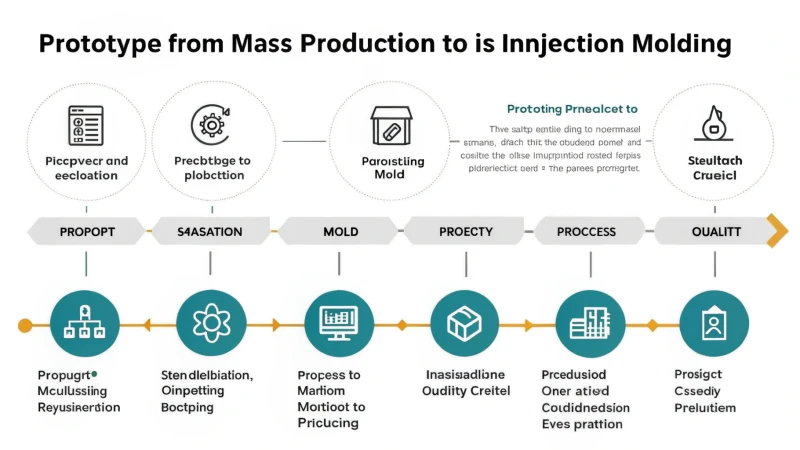
What Are the Key Steps to Transition from Prototype to Mass Production in Injection Molding?
This article outlines the essential steps for transitioning from prototype to mass production in injection molding. Key stages include thorough evaluation of prototypes, optimization of molds based on performance tests, standardization of process parameters through experimental design methods, and establishment ...
MANUFACTURING
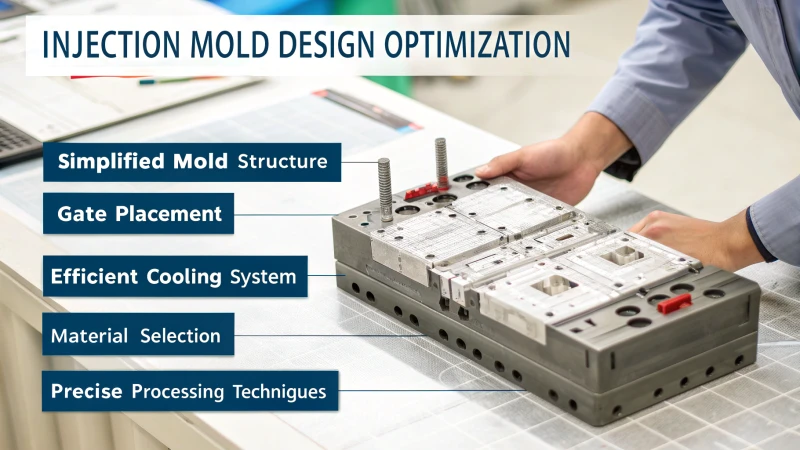
What Are the Key DFM Principles for Optimizing Injection Mold Design?
This article explores essential Design for Manufacturing (DFM) principles crucial for optimizing injection mold design. It emphasizes the importance of simplifying mold structures, strategically placing gates, designing efficient cooling systems, selecting appropriate materials, and ensuring precise processing. Each principle plays ...
MANUFACTURING
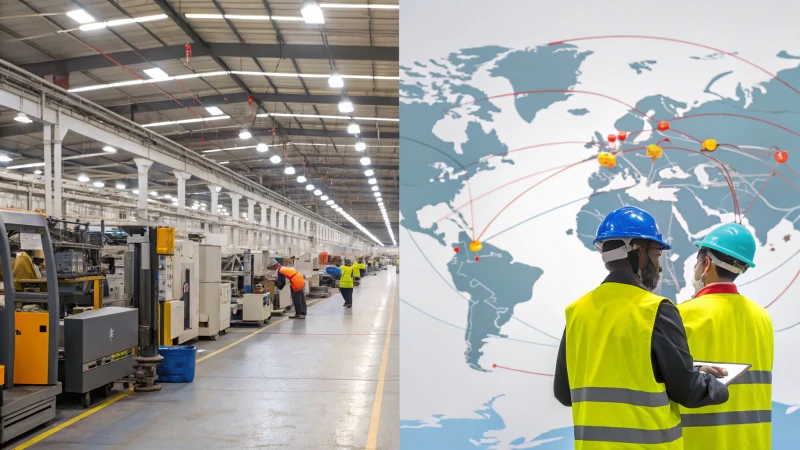
Local vs. Global Suppliers in Injection Molding: What Are the Benefits?
This article explores the advantages of choosing local injection molding suppliers over global ones. Local suppliers provide significant benefits such as lower transportation costs, quicker response times, and better service flexibility. Their proximity reduces risks associated with shipping delays and ...
Find Suppliers
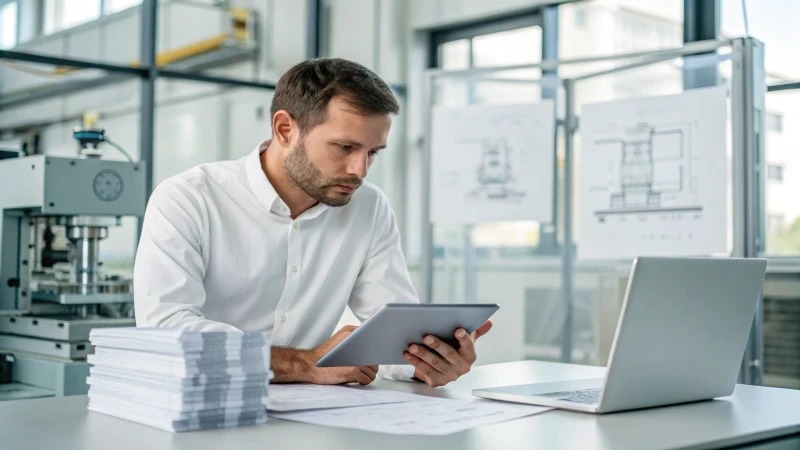
How Do You Calculate the Cost Per Part in Injection Molding?
Calculating the cost per part in injection molding involves understanding various components such as material costs, mold expenses, processing costs (energy and labor), and additional factors like packaging and transportation. By accurately estimating each element—using tools like 3D modeling software ...
Price Evaluation
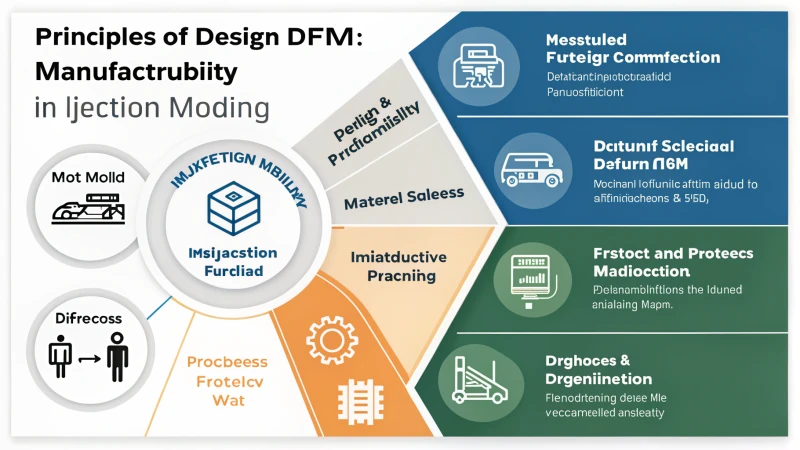
How Does Design for Manufacturability (DFM) Enhance Injection Molding?
This article explores how Design for Manufacturability (DFM) enhances injection molding by focusing on product structure design, mold design, and material selection. Key principles include maintaining uniform wall thickness to prevent defects like warping and shrinkage, strategically designing ribs for ...
MANUFACTURING
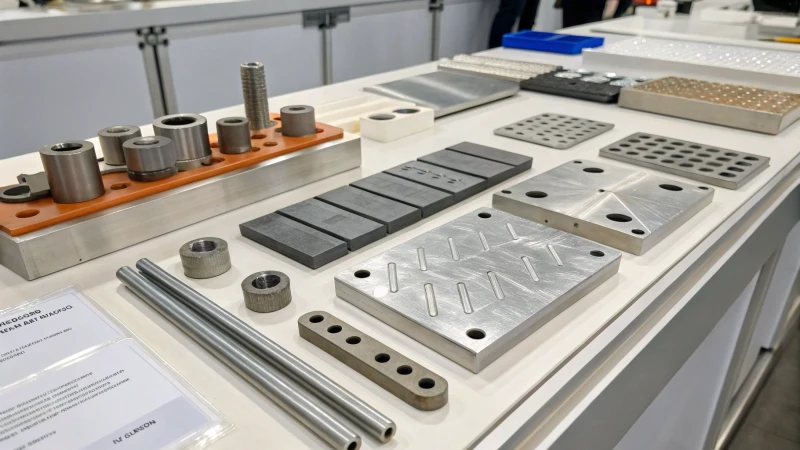
Which Mold Materials Are Ideal for High-Temperature Injection Molding?
Choosing the right mold material is crucial for high-temperature injection molding. Materials such as H13 steel and the HMAX series offer exceptional heat resistance and wear durability. Stainless steel provides corrosion resistance while hard alloys excel in toughness. Ultracur3D® RG3280 ...
Materials Recommendations
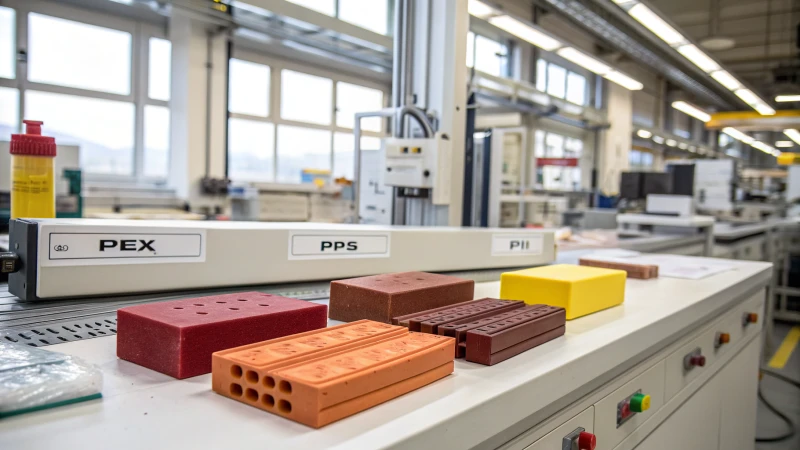
What Are the Best Materials for High-Temperature Injection Molding?
Choosing the right materials for high-temperature injection molding is crucial for project success. This article discusses top materials like PEEK, PPS, and PI while considering factors such as heat resistance, mechanical properties, chemical stability, processing performance, cost-effectiveness, and availability. Understanding ...
Materials Recommendations