Draft angles might seem like a minor detail, but they are truly the unsung heroes of the injection molding world!
Draft angles are vital in injection molding, typically ranging from 0.5° to 3°. They ensure smooth demolding, minimize defects, and optimize production costs by considering material shrinkage and product complexity.
But this is just the tip of the iceberg! Join me as we explore the fascinating nuances of draft angles and how they can transform your injection molding projects.
Draft angles in injection molding range from 0.5° to 3°.True
Optimal draft angles depend on material shrinkage, product complexity, and mold structure.
How Do Material Properties Affect Draft Angle Selection?
Material properties significantly influence draft angle choices in injection molding.
Material properties like shrinkage and fluidity dictate the optimal draft angle for injection molding. High-shrinkage materials may require angles between 1° to 2°, while good fluidity materials allow for smaller angles. These properties ensure smooth demolding and minimal defects.
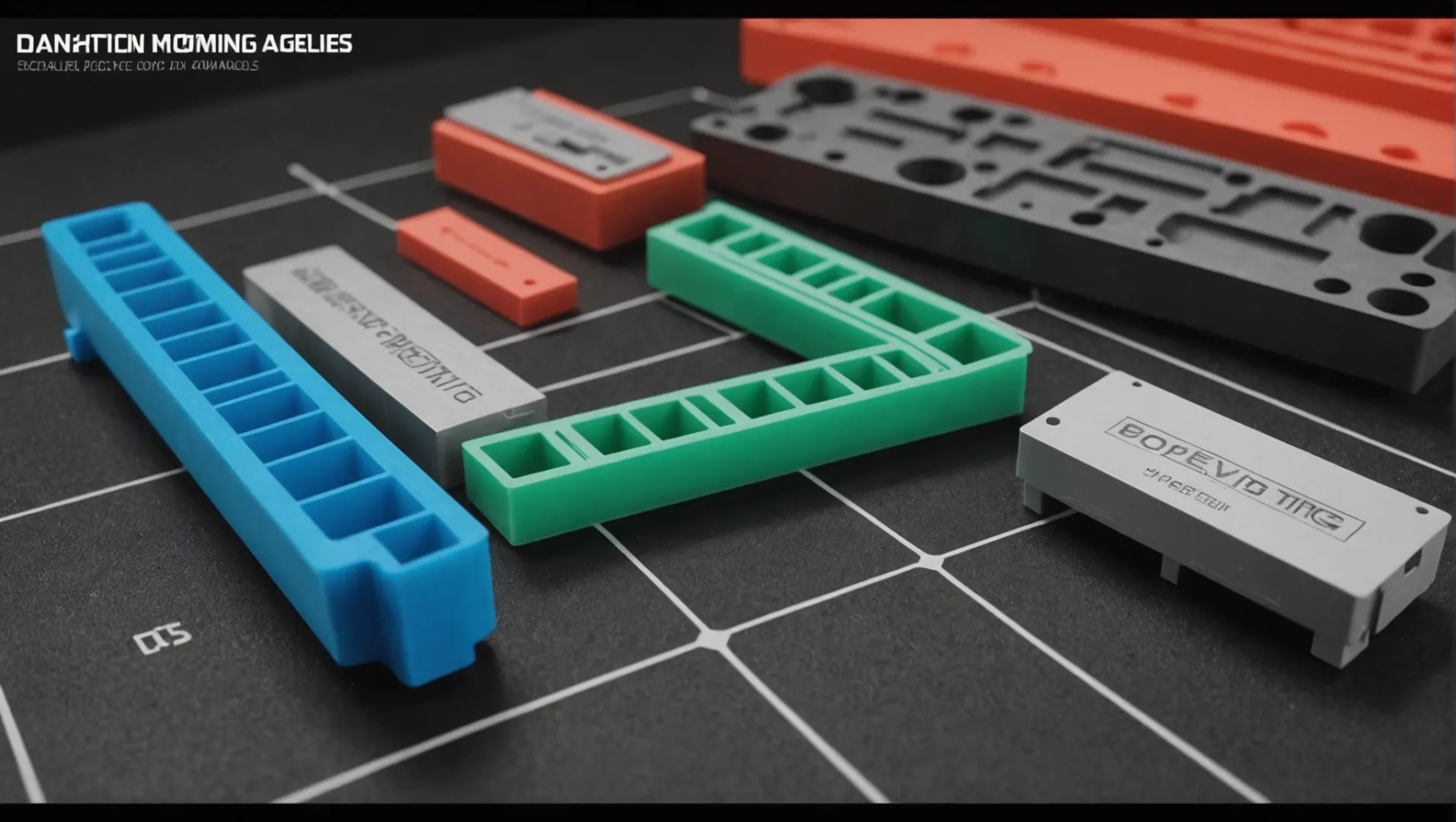
The Role of Shrinkage in Draft Angle Determination
One of the most significant factors1 influencing draft angle selection is the shrinkage rate of the plastic material. During cooling, plastics tend to shrink, potentially causing the product to stick within the mold if not properly accounted for. For instance, materials such as polyethylene and polypropylene, known for their high shrinkage rates, typically necessitate larger draft angles ranging from 1° to 2° to facilitate easy removal.
How Fluidity Impacts Draft Angle
The fluidity of a material, or its ability to flow and fill a mold, also plays a crucial role in determining the draft angle. Materials with high fluidity require smaller draft angles because they smoothly fill mold cavities and demold effortlessly. Conversely, materials with lower fluidity may demand more substantial draft angles to ensure that the product can be easily ejected without damage.
Comparing Material Properties in Draft Angle Selection
Material | Shrinkage Rate | Typical Draft Angle |
---|---|---|
Polyethylene | High | 1° – 2° |
Polypropylene | High | 1° – 2° |
ABS | Moderate | 0.5° – 1° |
Nylon | Low | <0.5° |
Case Studies: Material Influence on Draft Angles
Consider the example2 of a polyethylene product versus an ABS plastic component. While the polyethylene part requires a draft angle of at least 1°, an ABS part might only need a 0.5° angle due to its moderate shrinkage and better fluidity.
Understanding these material properties allows designers to optimize draft angles, reducing the likelihood of defects and enhancing overall production efficiency.
Polyethylene requires a draft angle of at least 1°.True
Due to its high shrinkage rate, polyethylene typically needs 1°-2° angles.
Complex shapes require larger draft angles for demolding.True
Complex geometries increase friction, necessitating larger draft angles.
Simple flat surfaces need a 3°-5° draft angle.False
Simple flat surfaces typically require a 0.5°-1° draft angle.
How Can Mold Design Influence Draft Angle Requirements?
Mold design intricacies significantly affect draft angle requirements, impacting demolding success and product integrity.
Mold design dictates draft angle requirements by accommodating mold structures, surface finishes, and demolding forces. Proper mold design optimizes draft angles to enhance demolding efficiency and product quality.
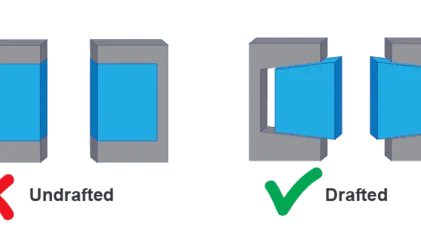
Understanding Mold Design’s Role
The mold design is a crucial factor in determining the appropriate draft angle requirements. By incorporating specific design elements such as sliders, bevel tops, and surface finishes, mold designers can optimize draft angles to facilitate smoother demolding processes. This section explores how these design components influence draft angle selection.
Mold Structures and Their Impact
-
Use of Sliders and Bevel Tops: These components in mold design can significantly reduce the need for larger draft angles. By providing additional demolding force, they help in smoothly ejecting the product, even with minimal draft angles.
-
Surface Finish Considerations: A high surface finish on the mold can allow for smaller draft angles. The smooth surface reduces friction during demolding, making it easier for the product to be released without sticking or damaging.
Mold Structure | Impact on Draft Angle |
---|---|
Sliders | Allows smaller angles |
Bevel Tops | Eases demolding |
High Finish | Reduces friction |
Designing for Efficient Demolding
The mold design process should carefully consider all elements that influence the draft angle to ensure efficient production. This involves:
- Analyzing Product Geometry: Complex shapes might require innovative mold designs to maintain optimal draft angles while ensuring structural integrity.
- Assessing Material Compatibility: Different materials interact uniquely with mold surfaces, necessitating adjustments in mold design to accommodate these variations.
Conclusion
By meticulously designing molds with attention to structural components and surface finishes, manufacturers can adjust draft angles effectively. This not only improves the efficiency of the demolding process but also enhances the overall quality and cost-effectiveness of injection-molded products. Exploring the impact of mold design further reveals its pivotal role in shaping draft angle requirements and ensuring manufacturing success.
For additional insights, consider exploring how mold structural components5 affect manufacturing outcomes or understanding the benefits of high surface finish molds6.
Sliders reduce the need for larger draft angles.True
Sliders provide additional demolding force, allowing smaller angles.
High surface finish increases draft angle requirements.False
A high surface finish reduces friction, allowing smaller angles.
What Are the Common Methods for Marking Draft Angles on Drawings?
Draft angles are critical in ensuring smooth demolding in injection molding, and accurate marking on drawings is essential.
Draft angles on drawings are typically marked using either direct angle notation, like "1.5°", or slope representation, such as "1:50" for a 1° angle. These methods ensure clear communication and prevent manufacturing errors.
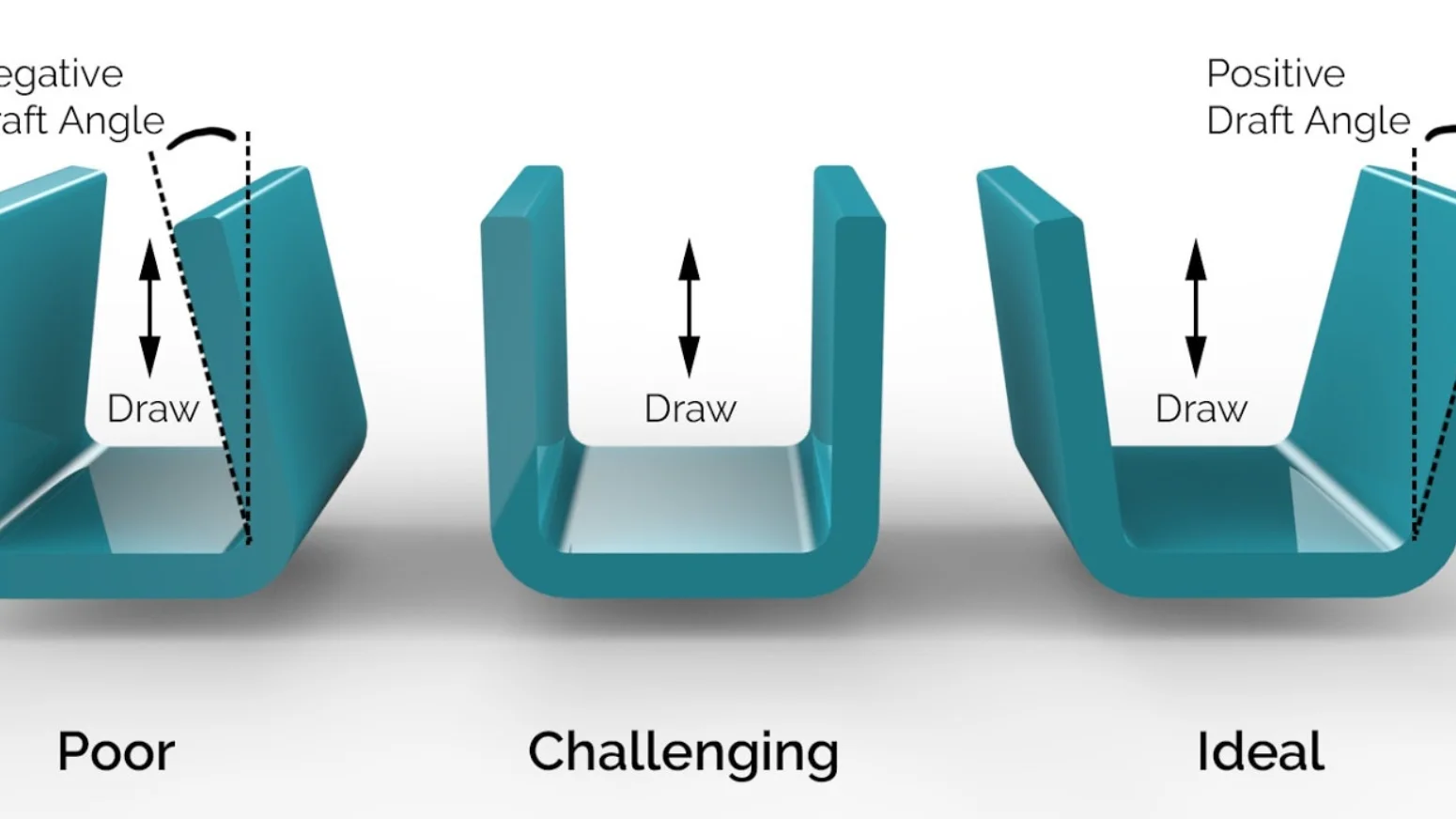
The Importance of Accurate Draft Angle Marking
Draft angle marking on technical drawings plays a crucial role in the injection molding process7. Precise markings guide mold designers and manufacturers to avoid errors that could lead to poor product quality or increased production costs.
Direct Angle Notation
One of the simplest methods to mark draft angles is through direct notation. Here, the draft angle is explicitly mentioned on the drawing, for example, "draft angle 1.5°". This method is straightforward and minimizes ambiguity, ensuring all parties involved have a clear understanding of the specifications.
Pros:
- Easy to understand
- Reduces risk of misinterpretation
Cons:
- Requires careful attention to placement and direction to prevent confusion
Slope Representation
The slope method uses ratios to express draft angles, such as "1:50" for a 1° draft. This technique can be more intuitive for those familiar with slopes, as it visually represents the angle’s gradient.
Pros:
- Offers a visual representation of the angle
- Useful in complex designs where visual guidance is beneficial
Cons:
- Requires understanding of slope ratios
Method | Example | Benefits |
---|---|---|
Direct Angle Notation | 1.5° | Simple and clear |
Slope Representation | 1:50 | Intuitive for complex structures |
Considerations for Effective Draft Angle Marking
When employing these methods, it’s essential to consider factors such as the overall design complexity8 and the potential for miscommunication among the manufacturing team.
- Attention to Detail: Ensure that angles are marked consistently and visibly to prevent misunderstandings.
- Clear Communication: Use notes or legends on drawings to explain uncommon markings or when switching between methods.
Understanding these methods and their applications can significantly impact the efficiency and success of your injection molding projects.
Direct angle notation is always clearer than slope representation.False
While direct notation is straightforward, slope can be clearer in complex designs.
Slope representation is useful in complex designs for visual guidance.True
Slope ratios visually represent gradients, aiding understanding in intricate designs.
Conclusion
Understanding draft angles can significantly enhance production efficiency and product quality. Let’s apply these insights to elevate our injection molding practices.
-
Explore various factors influencing draft angle choice in detail.: Several factors influence the selection of draft angles. These factors include wall thickness, wall depth, shrink rates, material selection, … ↩
-
Learn about how various materials impact draft angle needs.: Factors like wall thickness, material selection, ejection, shrink rates, finish/texture, wall depth, and manufacturing capabilities all come into play. ↩
-
Learn how intricate product shapes dictate necessary draft angles.: When designing a part, apply as much draft angle as possible—a general rule of thumb is 1 degree of draft per 1 inch of cavity depth, but that can change with … ↩
-
Discover mold adaptations that allow smaller draft angles for complex designs.: Consider the overall geometry of the part. Complex shapes or intricate details may require adjustments in wall thickness to maintain moldability … ↩
-
Explore how sliders and bevel tops reduce draft angles.: Reducing Warping: During injection molding, uneven mold temperatures or uneven melting of the plastic can cause product deformation. Proper … ↩
-
Understand how surface finishes ease demolding.: Likewise, a faster filling through mold cavities can reduce weld line visibility. Thus, it improves the overall appearance of plastic finishes. ↩
-
Discover how draft angles affect injection molding efficiency and quality.: Improve injection-molded parts with the use of draft. Applying proper draft—a slight taper to help release parts more easily—early can save you time and … ↩
-
Learn how complex designs influence draft angle decisions.: Numerous factors come into play when selecting draft angles. These include wall thickness, depth, shrinkage rates, material choice, part complexity, finish, … ↩