Do you ever think about how new discoveries in materials science change manufacturing? These advancements transform how products get produced. Factories really benefit from using these cutting-edge materials. They probably create better and more efficient items. Complex tasks become simpler with these breakthroughs. The manufacturing world never stays the same. It constantly evolves and adapts.
Innovations in materials science are changing extrusion and injection molding. These advancements expand material options and improve product quality. New high-performance materials allow the creation of components that meet today’s industrial needs. Manufacturing processes are really improving. These changes are for the better.
In my journey as a designer, I have seen how these advancements unlock exciting possibilities. It’s like watching a magic show! Materials seem to transform before your eyes. The introduction of high-performance polymers, like PEEK, helps us create components for extreme conditions. Imagine parts that really surpass industry standards!
This blog post explores how these innovations change our work. They change material properties and promote sustainable practices. I hope to share insights that speak to all of us in this dynamic field.
Materials science advancements improve injection molding quality.True
Recent advancements in materials science have led to enhanced quality in injection molding processes, resulting in better product performance and durability.
Extrusion capabilities have not changed with new materials.False
Contrary to this claim, advancements in materials science have significantly enhanced extrusion capabilities, allowing for a wider range of applications and improved outcomes.
- 1. What New Materials Are Emerging in Extrusion and Injection Molding?
- 2. How Do Material Innovations Affect Product Design and Performance?
- 3. How is Sustainability Changing the Game in Modern Molding Techniques?
- 4. How Can Manufacturers Leverage Advanced Materials for Competitive Advantage?
- 5. Conclusion
What New Materials Are Emerging in Extrusion and Injection Molding?
Have you ever thought about how new materials are changing extrusion and injection molding? It is really interesting to see how inventive materials, like advanced plastics and eco-friendly composites, are changing the way we manufacture products.
Emerging materials such as PEEK, PPS, LCPs and thermoplastic elastomers improve extrusion and injection molding capabilities. They increase performance, quality and sustainability. These advancements really increase production efficiency. They also allow the creation of specialized components. These components are tailored to modern demands.
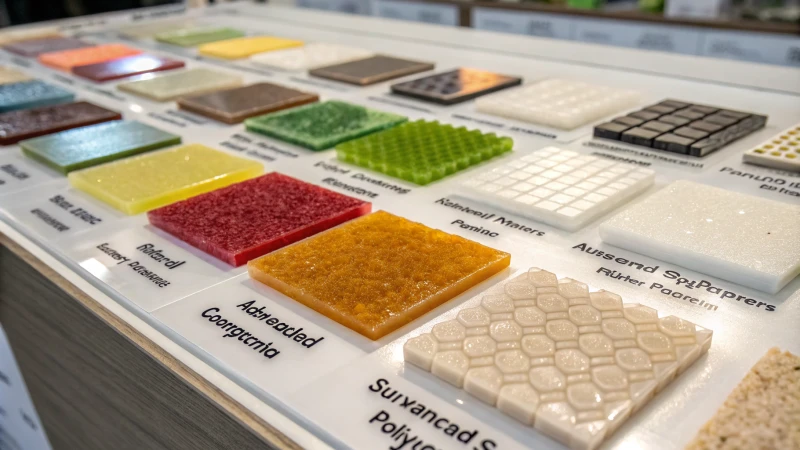
Expanding Available Materials
Materials science advancements have greatly widened the range of materials used in extrusion and injection molding. New plastics, composites, and high-performance polymers like PEEK (Polyetheretherketone) and PPS (Polyphenylene Sulfide) show incredible traits. These materials are really heat-resistant and have great strength and rigidity, making them suitable for tough applications such as:
Application | Material | Key Properties |
---|---|---|
Aerospace pipes | PEEK | High-temperature resistance |
Electrical insulation | PPS | High-performance rigidity |
This progress lets manufacturers make more specialized components that very strictly meet industry standards, like high-quality insulation profiles in electronics.
Improving Product Quality
I am really amazed by how new materials and better modification techniques increase product quality in extrusion molding. Adding reinforcing materials like nanoparticles or fibers leads to:
- Better mechanical strength
- Improved wear resistance
- Higher corrosion resistance
Recently, I spoke with a colleague about how advanced techniques improved polymers. They succeeded in lowering defects like bubbles and cracks during extrusion. This resulted in better surface quality and shape precision. Seeing such innovations driven by materials science is very inspiring. It plays a key role in efficient production lines.
Innovations in Extrusion Processes
As I explore extrusion technologies more, materials with unique features continue to drive new innovations. Certain materials need adjustments in both process settings and equipment structures. Reaction extrusion technology is notably advanced. It involves:
- High temperature and pressure within the extruder for chemical reactions during extrusion.
- In-situ modification of materials for better performance.
This technology leads to new applications for extrusion molding, making products previously thought impossible feasible. This is truly exciting for future possibilities.
Increasing Production Efficiency
I have witnessed how advanced material formulations really change production efficiency. By lowering material viscosity and enhancing fluidity, manufacturers achieve:
- Faster extrusion speed and output
- Optimal process settings due to broader thermal stability of new materials
These improvements lead to smooth manufacturing, cost savings, and increased productivity. Reflecting on my experiences, it’s obvious how these developments impact our everyday operations.
Diversifying Molding Materials
In injection molding, progress in material science has enriched available materials. Designers now have more choices among high-performance thermoplastics, thermosetting plastics, elastomers, and their composites. Notable examples include:
- Liquid Crystal Polymers (LCP): They have great heat resistance and strength, making them suitable for precise electronic parts.
- Thermoplastic Elastomers: They mix plastic and rubber traits, making them ideal for flexible automotive parts.
Making Complex Products
Research in new materials makes injection molding able to create complex product designs. Materials with high fluidity and low shrinkage enable:
- Better filling of molds
- Detailed feature replication
This is very important in industries like electronics and medical devices where complex geometries are often necessary. Once, I worked on mobile phone housings; high-performance plastics allowed us to create precise structures through injection molding—it was a real game-changer!
Improving Dimensional Accuracy and Surface Quality
Ongoing progress in materials science really improves the precision and surface quality of injection molded items. Incredibly, designers use new molecular structures along with specific additives to help minimize shrinkage and warpage during the injection molding process while treatment technologies achieve very shiny surfaces without needing extra finishing.
Indeed, it’s rewarding to observe the clear influence of these advancements on our designs.
Adapting Injection Molding Processes to Material Needs
different materials require specific processing conditions which calls for adaptable injection molding processes. Lately developments allow setting parameters for thick or heat-sensitive materials while techniques also involve injecting at lower temperatures followed by quick cooling methods that prevent material damage.
furthermore the industry is seeking recyclable eco-friendly materials; it’s encouraging to see efforts shifting toward sustainability! For those curious about advancing their manufacturing check out resources on new material technologies1 or sustainable practices in molding2. Innovation really holds the key to our manufacturing future.
PEEK is used for high-temperature aerospace applications.True
PEEK's high-temperature resistance makes it suitable for aerospace pipes, enhancing safety and performance in extreme conditions.
Thermoplastic elastomers combine plastic and rubber properties.True
Thermoplastic elastomers offer flexibility and durability, making them ideal for automotive components requiring both characteristics.
How Do Material Innovations Affect Product Design and Performance?
Do you ever think about how our choice of materials changes designs? It’s exciting to see how new materials influence both the usefulness and attractiveness of the items we produce. Materials are very powerful. They transform designs entirely.
Innovative materials revolutionize product design and performance. They improve how products are manufactured and increase durability. New materials also support sustainability. Designers like me use them to create functional and attractive products. These products really connect with what modern consumers want.
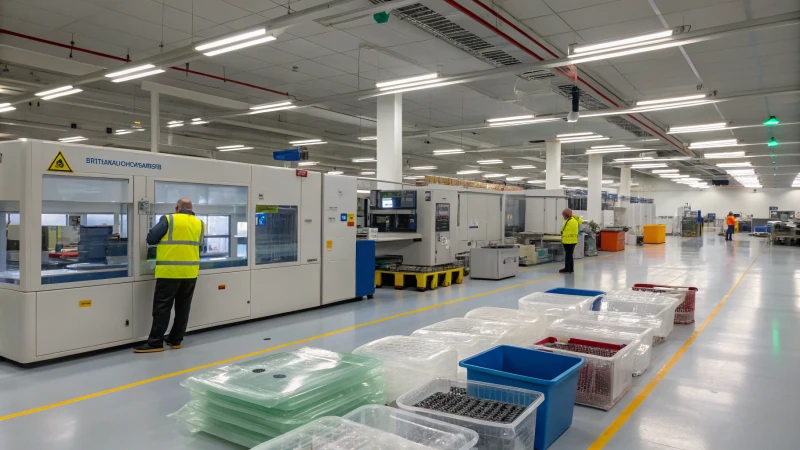
The Role of Material Innovations in Product Design
Material innovations greatly affect product design and performance. They allow advanced manufacturing processes. These innovations improve durability, promote sustainability, and permit complex shapes to meet today’s consumer needs. I find the connection between materials and design very intriguing. It feels like discovering a new set of colors that unlocks endless creative opportunities.
Advancements in Manufacturing Processes
Innovations in material science have directly impacted manufacturing processes like extrusion and injection molding. The development of materials has expanded the range of processable materials, which directly influences production capabilities.
Process Type | Impact of Material Innovations |
---|---|
Extrusion Molding | New engineering plastics allow for high-performance products, such as high-temperature pipes used in aerospace. |
Injection Molding | Advanced thermoplastics enable complex product structures with precision, crucial for industries like electronics. |
By embracing these advancements, designers can produce parts with improved performance characteristics, such as enhanced mechanical strength and reduced weight. For more insights into specific materials used in extrusion and injection molding, check out this resource3.
Enhancing Product Performance
Material innovations not only facilitate new designs but also enhance overall product performance. The introduction of nanoparticles and fiber reinforcements can significantly boost the mechanical properties of products. This is particularly important in competitive markets where durability and reliability are key selling points.
For example, using composites with enhanced wear resistance can lead to longer-lasting products, which aligns with consumer demands for sustainability. This trend is growing, as consumers increasingly prefer products that are durable and environmentally friendly.
Sustainability and Environmental Considerations
As material innovations continue to evolve, there is a growing emphasis on sustainability. New materials are being developed with a focus on recyclability and environmental impact, prompting a shift in how products are designed from the ground up.
Designers now face the challenge of balancing performance with ecological responsibility. Innovative materials like bioplastics not only serve functional purposes but also cater to eco-conscious consumers. For further exploration of sustainable materials, consider reading about green manufacturing techniques .
The Future of Material Innovations
Looking ahead, material science promises to continue reshaping product design and performance. As we explore new frontiers such as smart materials that respond to environmental stimuli, the possibilities for innovative product design will expand exponentially.
Understanding how to leverage these innovations will be crucial for designers aiming to stay ahead in their fields. As new materials emerge, they will undoubtedly create opportunities for unique designs that enhance user experience while meeting rigorous performance standards.
Material innovations enhance product durability and performance.True
New materials like high-performance polymers improve durability, enabling products to withstand extreme conditions while enhancing overall performance.
Sustainability is not a priority in material innovations today.False
Current trends show a significant focus on developing sustainable materials, contradicting the claim that sustainability is unimportant in innovations.
How is Sustainability Changing the Game in Modern Molding Techniques?
Do you wonder how sustainability affects product creation today? Take a journey with me to explore the very important changes in modern production. Factories now use innovative materials for products. They focus on energy-saving methods. Waste reduction strategies play a big role.
Sustainability plays a vital role in today’s molding techniques. The focus lies on eco-friendly materials. Companies also strive for greater energy efficiency. Less waste is an important goal during production. Adopting these practices helps manufacturers meet global sustainability objectives. It leads to high-quality products. The balance between sustainability and quality is really important.
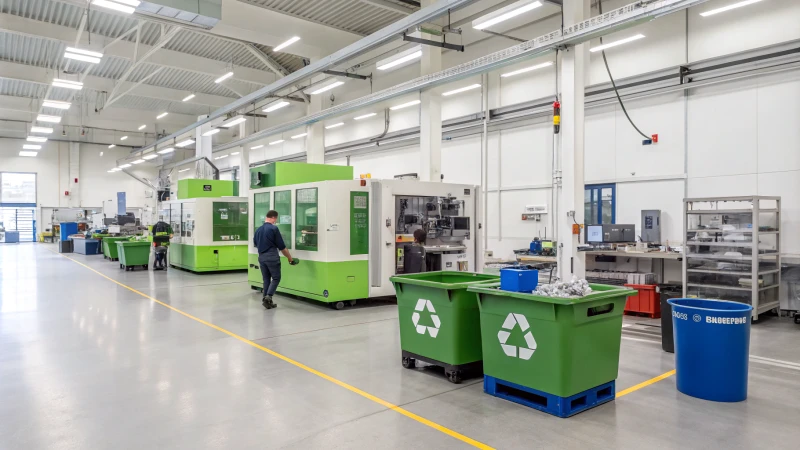
Understanding Sustainability in Molding Techniques
Sustainability is not only a popular term; it has become a guiding star for the manufacturing world. This change shapes our methods and actions. As more people worry about the environment, I see companies changing how they produce goods. They use sustainable ways to reduce waste and increase efficiency. It’s inspiring to watch these transformations.
Innovations in Materials Science
Advancements in materials science are thrilling. I attended a workshop that explored new eco-friendly materials. These materials perform well and have minimal impact on nature. For example, bioplastics made from renewable resources now replace traditional plastics, decreasing reliance on fossil fuels. Moreover, using recycled materials4 also changes the game by reducing waste and lowering energy needed for new production.
Energy Efficiency in Production
Modern molding techniques focus on using less energy while maintaining productivity. Companies invest in advanced machinery that saves energy without sacrificing output quality. Innovations such as energy-efficient injection molding machines5 help lower the carbon footprint of production processes while ensuring product quality.
Energy-Efficient Machines | Traditional Machines |
---|---|
Lower energy consumption | Higher energy consumption |
Reduced operational costs | Increased operational costs |
Enhanced product quality | Variable product quality |
Waste Reduction Strategies
Waste reduction plays a crucial role in sustainability. Precision molding minimizes material waste during production. Closed-loop systems help recycle scrap materials back into use, further enhancing sustainability efforts. The adoption of lean manufacturing principles6 can also lead to significant reductions in waste and inefficiencies.
Life Cycle Assessment (LCA)
Life Cycle Assessment (LCA) helps understand the environmental impact of products from cradle to grave. It looks at every stage—from raw material extraction to disposal—allowing designers to find improvement areas and make better sustainable choices in materials and methods.
The Future of Sustainable Molding
The future of molding will focus more on sustainability as a core value. Companies apply circular economy principles more widely, designing products to last, be easily repaired, and recyclable. This approach meets consumer requests for eco-friendly items while positioning businesses as industry sustainability leaders. The integration of sustainable practices7 will likely continue evolving due to regulations and changing customer tastes.
Sustainability is a key principle in modern molding techniques.True
Modern molding practices prioritize sustainability, integrating eco-friendly materials and reducing waste to align with global environmental goals.
Energy-efficient machines increase production costs significantly.False
Contrary to this claim, energy-efficient machines actually reduce operational costs while maintaining productivity in molding processes.
How Can Manufacturers Leverage Advanced Materials for Competitive Advantage?
Do you ever think about how some manufacturers always stay ahead of others? They use advanced materials very smartly. Let’s learn how to use these innovations to gain your own advantage!
Manufacturers probably gain an advantage by using advanced materials like high-performance polymers in production. This results in better product quality. Production efficiency really improves. These materials allow for innovative features designed for specific uses.
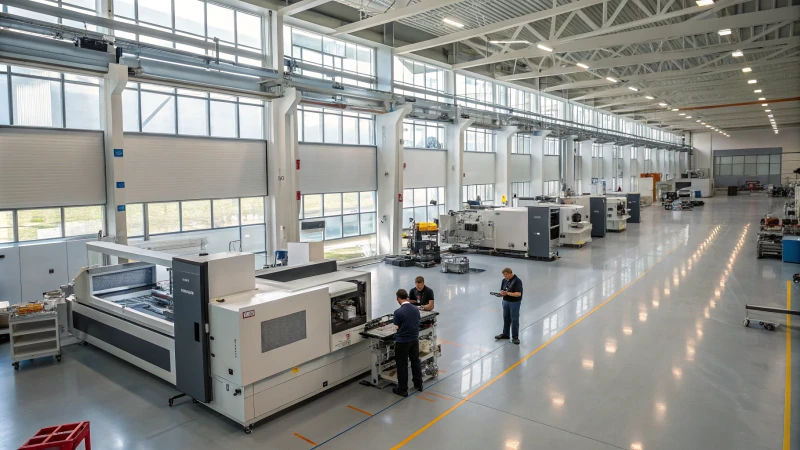
Expanding Material Options for Production
I remember when I started working in manufacturing. I felt amazed by how the right materials changed everything. An early project of mine involved creating a part for an electronic device. We faced big challenges with heat resistance. Then, I learned about high-performance polymers like PEEK and PPS. Using these materials solved our problems and gave us an edge in the market. Very impressive!
Manufacturers can significantly enhance their competitive edge by leveraging advanced materials such as high-performance polymers and composites.
These materials not only expand the range of processable options but also improve product attributes. For instance, engineering plastics like PEEK and PPS exhibit properties like high temperature resistance and rigidity, making them ideal for critical applications in aerospace and electronics.
For more on these materials, check out advanced material options8.
Enhancing Product Quality and Performance
Advanced materials really give manufacturers a wider range of choices. High-performance polymers and composites like PEEK and PPS truly change the game. They offer high-temperature resistance and durability. These traits make them ideal for tough industries like aerospace and electronics. I felt thrilled watching my team test these materials. The results were simply incredible.
By utilizing advanced materials, manufacturers can improve the mechanical properties and durability of their products. The incorporation of reinforcement materials such as nanoparticles and fibers can enhance wear resistance and minimize defects during production.
Property | Traditional Material | Advanced Material |
---|---|---|
Temperature Resistance | Low | High (PEEK, PPS) |
Strength | Moderate | High |
Rigidity | Low | High |
As these materials undergo continuous development, manufacturers should stay updated on the latest innovations to fully capitalize on quality improvements. Explore more about enhancing product quality here9.
Innovating Production Processes
I believe that innovation leads to success. Material science evolution has led to new production methods such as extrusion and injection molding. Reaction extrusion caught my eye; it allows in-situ polymer modification, improving material properties. Watching these innovations in our production line was unforgettable.
The evolution of material science has driven innovation in production processes such as extrusion and injection molding. For example, reaction extrusion technology enables in-situ modification of polymers, resulting in enhanced material properties and broader application fields.
Moreover, specialized rheological characteristics of new materials necessitate tailored processing techniques, leading to advancements that could optimize efficiency. To delve deeper into these innovative processes, visit innovative production techniques10.
Boosting Efficiency and Sustainability
Advanced materials streamlined our operations; they really cut costs! New formulations improved fluidity allowing us to increase extrusion speeds without losing quality while adopting eco-friendly materials made me feel a strong pride in our sustainability efforts.
Advanced materials allow manufacturers to streamline operations and reduce costs by enhancing production efficiency. New formulations improve fluidity and reduce viscosity, enabling faster extrusion speeds without compromising quality. Additionally, the development of environmentally friendly materials is becoming increasingly vital.
To learn more about sustainability in manufacturing practices, check out sustainable manufacturing11.
Adapting to Complex Demands
Meeting complex demands is crucial today; advanced materials help manufacturers create precise intricate designs! I saw this when we developed mobile phone casings with complex internal structures—our quick adaptation proved to be a major victory! High-performance thermoplastics allowed us to meet market needs efficiently while maintaining high quality as our goal.
With the rapid pace of technological change, manufacturers are tasked with meeting increasingly complex product requirements. Advanced materials provide solutions for producing intricate designs with high precision.
For instance, high-performance thermoplastics can be used for producing mobile phone casings with complex internal structures—this adaptability ensures that manufacturers can respond effectively to market demands while maintaining quality and efficiency! Learn about adapting to market changes here12.
Advanced materials enhance product durability and performance.True
Utilizing advanced materials like PEEK and PPS significantly improves the mechanical properties and longevity of manufactured products, providing a competitive edge.
Traditional materials are more cost-effective than advanced materials.False
While traditional materials may seem cheaper, advanced materials often lead to reduced production costs through efficiency gains and durability, ultimately saving money.
Conclusion
Innovations in materials science enhance extrusion and injection molding capabilities, improving product quality, expanding material choices, increasing production efficiency, and supporting sustainable practices.
-
Explore innovative materials that can enhance your manufacturing processes. This link provides insights into cutting-edge advancements tailored for product designers. ↩
-
Discover sustainable practices in molding that align with current industry trends. This resource offers valuable knowledge for environmentally conscious manufacturing. ↩
-
Explore how material advancements can lead to improved product design and efficiency. Discover valuable insights that could enhance your projects. ↩
-
Learn how sustainable practices can enhance efficiency and reduce environmental impact in molding processes. ↩
-
Discover innovative materials that promote sustainability in manufacturing and their benefits. ↩
-
Explore strategies for reducing waste and increasing energy efficiency in molding techniques. ↩
-
Understand the importance of Life Cycle Assessment (LCA) in evaluating the sustainability of molded products. ↩
-
Clicking this link will provide insights into advanced materials that can revolutionize your manufacturing processes. ↩
-
This link discusses how advanced materials can enhance product performance and quality. ↩
-
Explore innovative production techniques using advanced materials for better efficiency. ↩
-
Learn about sustainable manufacturing practices that utilize advanced materials effectively. ↩
-
Find out how to adapt to complex market demands using advanced materials. ↩