Achieving perfect color consistency1 in injection molded parts is a critical aspect of manufacturing that ensures every part produced has the same color, with no noticeable variations. This uniformity is essential for maintaining product quality, brand identity, and compliance with industry standards. Whether in automotive parts, consumer goods, or medical devices, color consistency can impact aesthetics, functionality, and regulatory adherence.
Perfect color consistency in injection molded parts2 ensures uniform color across all products, enhancing aesthetics, brand identity, and compliance with industry standards.
Understanding the factors that influence color consistency is key to optimizing your manufacturing process. Delve deeper to explore how material selection3, process control, and quality measures affect the final product’s color.
Color consistency is only important for aesthetic reasons.False
In industries like medical devices, color can indicate functionality or compliance with regulations, making it crucial beyond aesthetics.
Using masterbatches always guarantees perfect color consistency.False
While masterbatches provide consistent color, factors like process parameters and material quality also play a significant role.
- 1. What Are the Common Materials Used in Injection Molding for Color Consistency?
- 2. What Are the Key Steps to Achieving Color Consistency in Injection Molding?
- 3. What Are the Three Main Factors Influencing Color Consistency in Injection Molding?
- 4. What Are the Applications Where Color Consistency Is Critical?
- 5. What Are the Differences Between Masterbatch and Compounding for Color Consistency?
- 6. Conclusion
What Are the Common Materials Used in Injection Molding for Color Consistency?
Material selection is pivotal in achieving color consistency, as different plastics and colorants interact uniquely during the molding process.
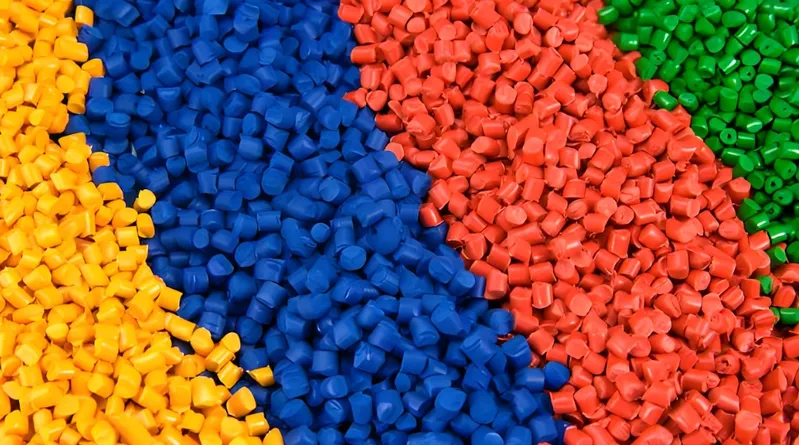
Common materials include ABS, polycarbonate, polypropylene, and colorants like pigments, dyes, and masterbatches, each affecting color stability and uniformity.
Material Type | Color Stability | Notes |
---|---|---|
ABS | Moderate | Prone to stress discoloration |
Polycarbonate (PC) | High | UV-sensitive, requires stabilizers |
Polypropylene (PP) | Low | Challenging with some pigments |
Masterbatches | High | Consistent color, requires precise mixing |
ABS (Acrylonitrile Butadiene Styrene)
ABS is widely used for its strength and versatility but can experience stress discoloration4, affecting color consistency. Proper temperature control during molding minimizes variations.
Polycarbonate (PC)
Polycarbonate offers excellent thermal stability but is sensitive to UV exposure, which can alter color over time. Using UV stabilizers5 or pre-colored resins helps maintain consistency.
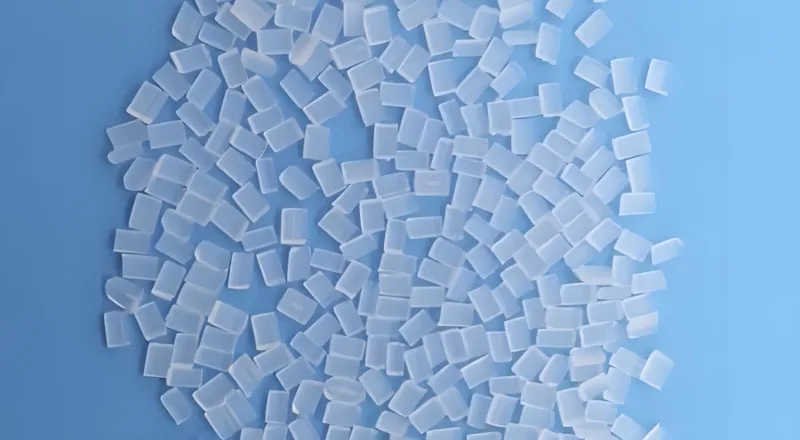
Polypropylene (PP)
PP’s crystalline structure6 complicates pigment dispersion, potentially leading to uneven color. Compatible colorants and precise process control are critical for uniformity.
Colorants: Pigments, Dyes, and Masterbatches
Colorants such as pigments, dyes, and masterbatches are added to resins to achieve desired colors. Pigments and dyes allow for custom hues, while masterbatches—concentrated pigments in a carrier resin—provide consistent results for large production runs.
All plastics behave the same way when colored.False
Different plastics have unique properties that affect how they interact with colorants, requiring tailored approaches for each material.
Masterbatches are the most reliable method for achieving color consistency.True
Masterbatches offer consistent color dispersion and are ideal for large production volumes.
What Are the Key Steps to Achieving Color Consistency in Injection Molding?
Achieving color consistency requires meticulous attention to material preparation, process control, and quality measures throughout the injection molding workflow.
Key steps include selecting compatible materials, precise colorant mixing, controlling process parameters, and implementing rigorous quality control.
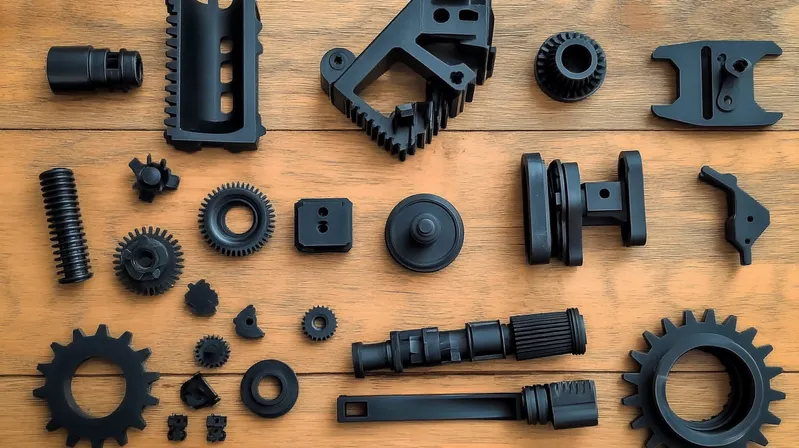
Material Preparation
-
Resin and Colorant Selection: Choose high-quality, compatible resins and colorants to avoid inconsistencies.
-
Inspection and Drying: Inspect raw materials for contamination and dry resins to control humidity, which can affect color dispersion.
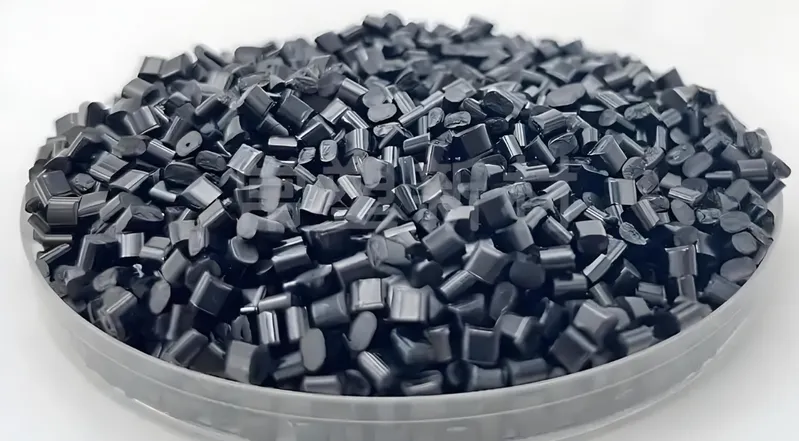
Colorant Mixing
-
Metering Equipment: Use precise equipment like gravimetric blenders for accurate resin-to-colorant ratios.
-
Mixing Methods:
- Masterbatching: Ideal for large volumes, typically mixed at a 1:24 ratio.
- Compounding: Pre-colored resins for medium to high volumes.
- Dry Pigment Mixing: Suitable for small batches but prone to inconsistency.
Injection Molding Process
- Temperature Control: Maintain consistent barrel and mold temperatures to prevent color shifts.
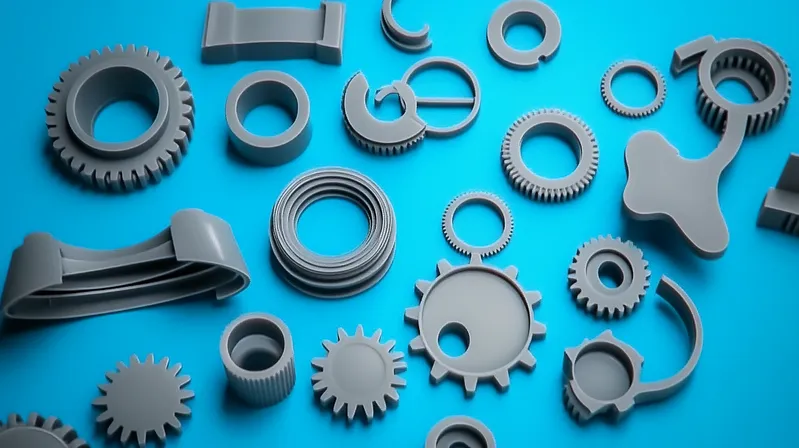
-
Injection Speed and Pressure: Use multi-stage injection to minimize shear heating and ensure uniform color.
-
Cooling: Ensure uniform cooling to avoid variations in crystallinity that affect color.
Quality Control
-
Color Measurement: Use standardized systems like Pantone or RAL and tools like colorimeters to verify consistency.
-
Process Monitoring: Regularly adjust parameters to maintain uniformity.
Perfect color consistency can be achieved without quality control measures.False
Quality control is essential to detect and correct variations in color during production.
Precise control of process parameters is crucial for color uniformity.True
Factors like temperature and pressure directly impact how colorants disperse and stabilize in the molded part.
What Are the Three Main Factors Influencing Color Consistency in Injection Molding?
Three critical factors—material compatibility, process control, and quality assurance—determine the success of achieving color consistency in injection molded parts.
Material compatibility, process control, and quality assurance are the three main factors influencing color consistency, each affecting how colorants integrate and stabilize in the final product.
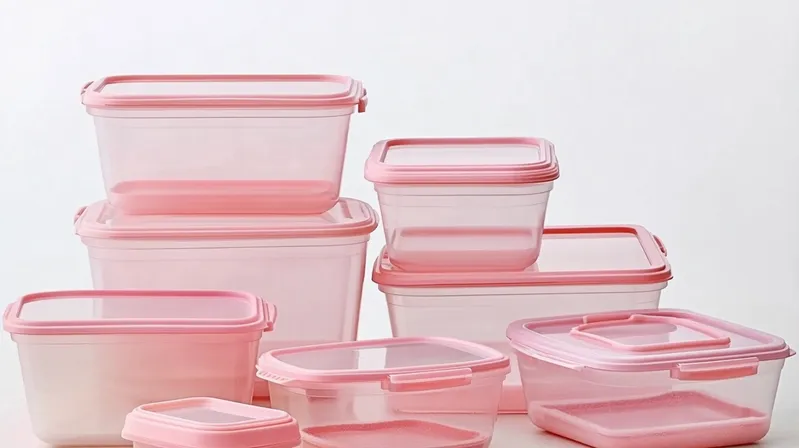
Material Compatibility
The interaction between resin and colorant is foundational. Incompatible materials can lead to poor dispersion, causing streaks or uneven color. For example, polypropylene requires specific pigments for uniform results due to its crystalline structure.
Process Control
Precise control of molding parameters is vital:
-
Temperature: Affects resin viscosity and colorant dispersion.
-
Pressure: High pressure can cause shear heating, leading to inconsistencies.
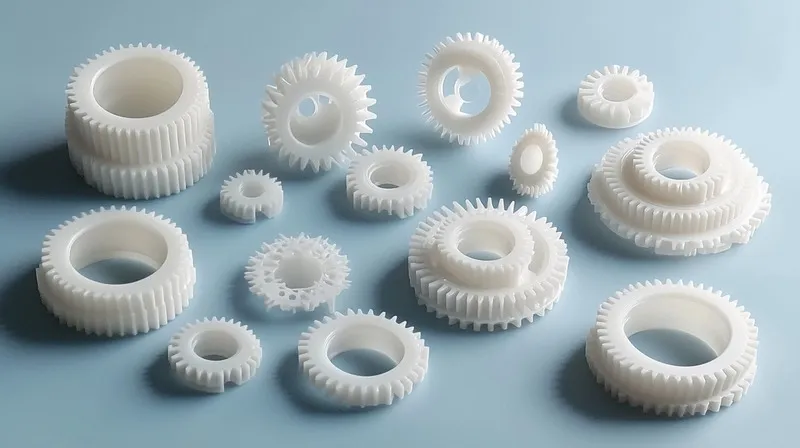
- Cooling Rate: Uneven cooling can cause color variations due to crystallinity differences.
Quality Assurance
Rigorous quality checks ensure consistency:
- Color Measurement: Use colorimeters or spectrophotometers to quantify differences.
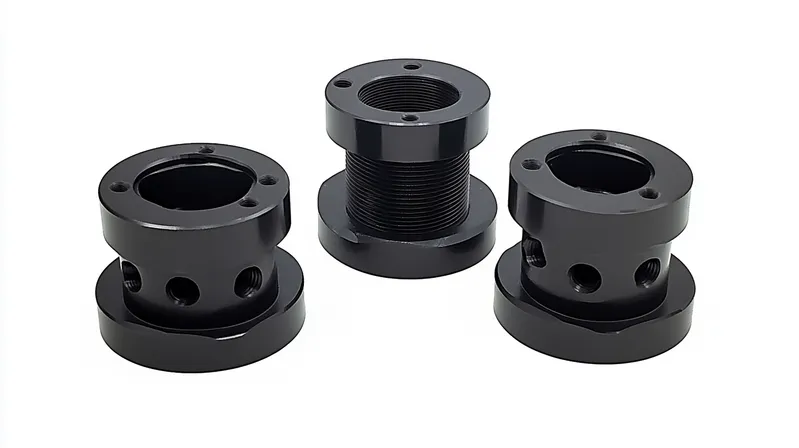
-
Standardization: Adopt color standards like Pantone or RAL.
-
Batch Testing: Regular sampling to detect and correct deviations.
Material compatibility is the only factor that affects color consistency.False
While important, process control and quality assurance are equally critical in achieving uniform color.
Standardized color systems like Pantone ensure perfect color matching across different batches.True
These systems provide a universal reference, reducing the risk of color variations.
What Are the Applications Where Color Consistency Is Critical?
Color consistency is crucial in industries where aesthetics, branding, and functionality depend on uniform color across products.
Industries like automotive, consumer goods, medical devices, and packaging rely on color consistency for branding, functionality, and compliance.
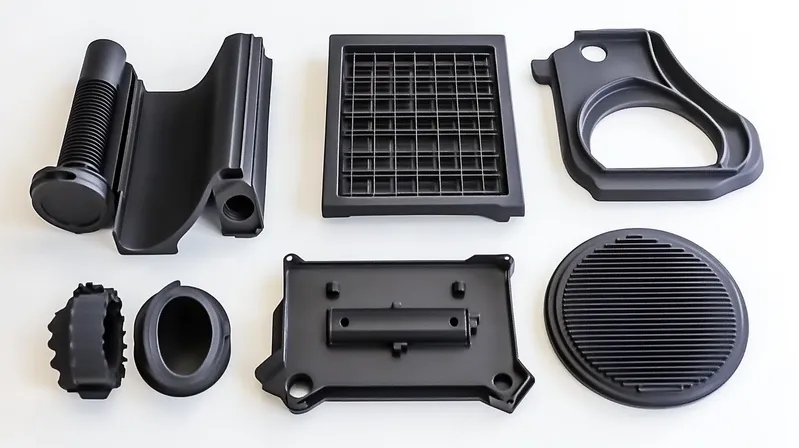
Automotive Industry
In automotive manufacturing7, color consistency is vital for interior and exterior parts. Mismatched dashboards, panels, or trim can detract from appearance and perceived quality.
Consumer Goods
For electronics, toys, and appliances, consistent color ensures brand recognition and customer satisfaction. Companies like Apple or LEGO rely on precise color matching.
Medical Devices
In medical applications, color can indicate functionality (e.g., sizes) or compliance with standards. FDA-compliant materials8 often require consistent color for safety and identification.
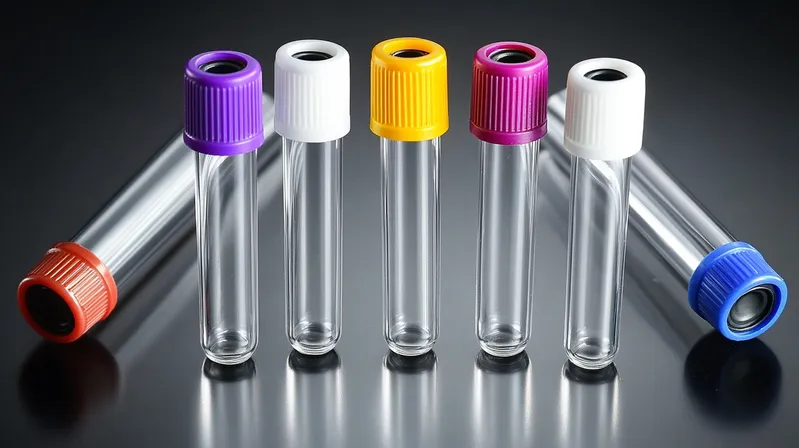
Packaging
In packaging, especially for food and beverages, consistent color is key for brand recognition. Coca-Cola’s iconic red must be uniform across all packaging.
Color consistency is only critical in high-end consumer products.False
It is equally important in industries like medical devices and packaging, where functionality and compliance are at stake.
Inconsistent color can lead to product recalls in regulated industries.True
In sectors like medical devices, color variations can result in non-compliance with safety standards.
What Are the Differences Between Masterbatch and Compounding for Color Consistency?
Masterbatch and compounding are two common methods for adding color to injection molded parts, each with distinct advantages and limitations.
Masterbatch9 involves mixing concentrated colorants10 with resin during molding, while compounding uses pre-colored resins, each suited to different production scales and color needs.
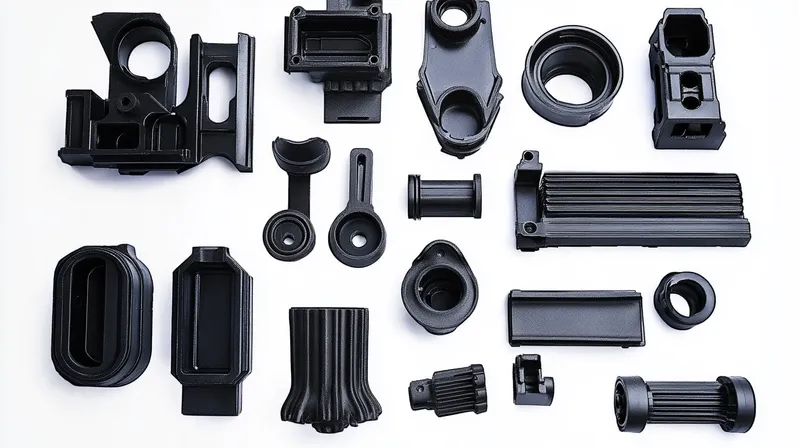
Masterbatch
-
Process: Colorants are concentrated in a carrier resin and mixed with the base resin during molding.
-
Advantages: Consistent color, cost-effective for large volumes, easy to switch colors.
-
Disadvantages: Requires precise mixing, high minimum order quantities (e.g., 2 tons).
Compounding
- Process: Resins are pre-colored by suppliers before molding.
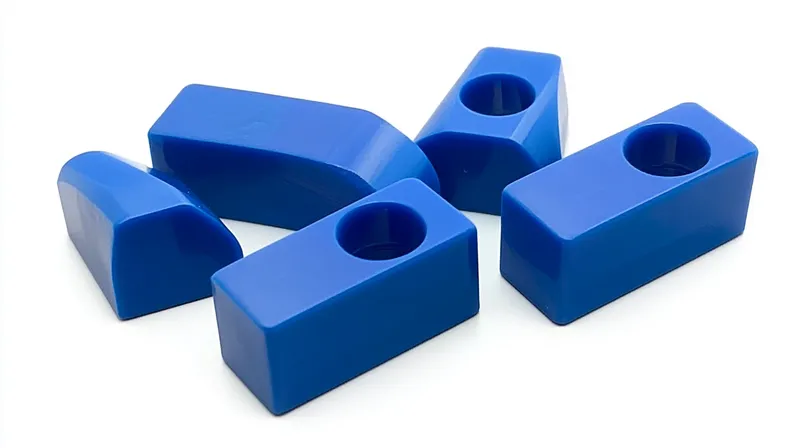
-
Advantages: Custom colors, suitable for medium to high volumes, consistent results.
-
Disadvantages: Higher costs for small batches, less flexibility in color changes.
Method | Best For | Limitations |
---|---|---|
Masterbatch | Large production runs | High minimum orders |
Compounding11 | Custom colors | Expensive for small batches |
Masterbatch is always the best choice for color consistency.False
While effective for large volumes, compounding may be better for custom colors or smaller batches.
Compounding offers more flexibility in color selection.True
It allows for precise customization of colors, which is beneficial for unique branding needs.
Conclusion
Achieving perfect color consistency in injection molded parts requires a comprehensive approach integrating material selection, precise process control, and rigorous quality assurance. By understanding the interplay between resins, colorants, and molding parameters, manufacturers can produce parts that meet the highest standards of uniformity and quality. Attention to detail at every stage—from material preparation to final inspection—is essential for success.
-
Explore this resource to learn effective strategies for ensuring color consistency in your injection molded products, enhancing quality and brand identity. ↩
-
This link will provide insights into the manufacturing process of injection molded parts, crucial for understanding quality control and consistency. ↩
-
Discover why material selection is vital in injection molding, impacting color consistency and overall product quality. ↩
-
Understanding the causes of stress discoloration can help in selecting the right materials and processes to avoid it. ↩
-
Learning about UV stabilizers can enhance your knowledge of maintaining color consistency in polycarbonate materials. ↩
-
Exploring the effects of crystalline structure on color can improve your understanding of polypropylene processing and colorant selection. ↩
-
Explore how color consistency impacts the automotive industry, affecting both aesthetics and perceived quality of vehicles. ↩
-
Learn about the critical standards for color consistency in medical devices to ensure safety and compliance with regulations. ↩
-
Explore this link to understand the Masterbatch process and its benefits in injection molding, enhancing your knowledge of color application. ↩
-
Learn about the different types of colorants used in injection molding, which can improve your understanding of color application techniques. ↩
-
Discover the Compounding method and its advantages for custom colors in injection molding, which can help you make informed production choices. ↩