Я помню, как первый раз, когда я надел шлем - казалось, что вступил в мир безопасности и приключений. Задумывались ли вы, как созданы эти важные инструменты безопасности?
Машины для литья под давлением создают шлемы, выбирая точные материалы, проектируя подробные формы и выполняя строгие проверки качества, чтобы обеспечить как безопасность, так и эффективность.
Когда я впервые углубился в мир производства шлема, сложность выбора таких материалов, как поликарбонат или пресс, поразила меня. Эти материалы не только предлагают необходимую прочность и ясность, но и обеспечивают экономическую эффективность. Путешествие проектирования формы, которая подходит для замысловатых кривых головы, было одинаково увлекательным. Это как скульптировать шедевр, который обещает защиту. А затем, наблюдая за тем, как расплавленный пластик охлаждается в твердой форме - весь шлем, выходящий из его плесени в качестве хранителя для головы владельца, - по -прежнему подчеркнул магию, стоящую за литьем инъекции. Этот тщательный процесс не просто делает шлемы; это формирует безопасность.
Инъекционное формование используется для изготовления оболочек шлема.Истинный
Инъекционное формование создает точные, прочные оболочки шлема эффективно.
Шлемы изготавливаются только один тип пластика.ЛОЖЬ
Различные пластмассы выбраны для их свойств и деталей шлема.
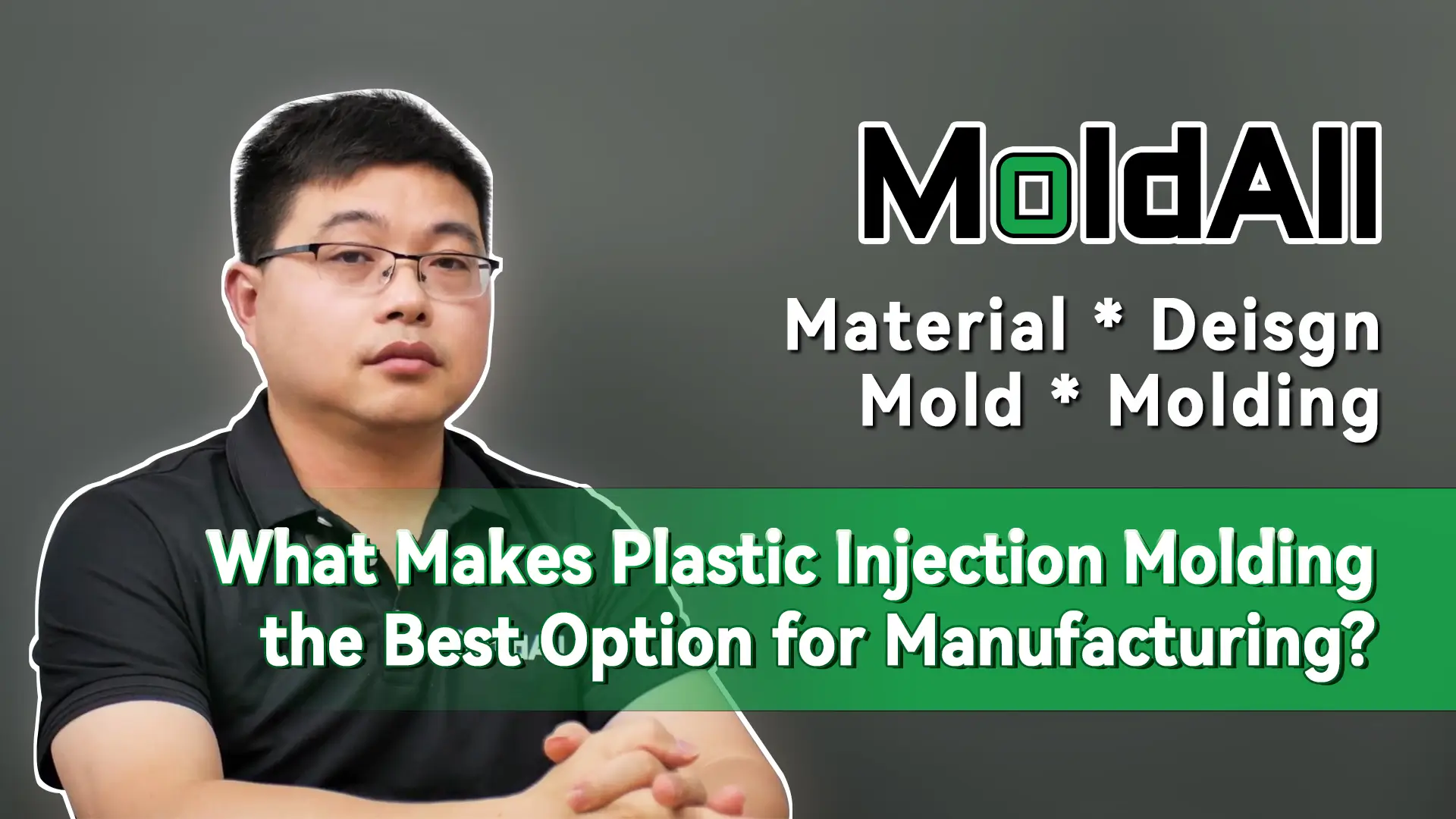
- 1. Какие материалы лучше всего подходят для формования впрыскивания шлема?
- 2. Как дизайн плесени влияет на качество шлема?
- 3. Как управляются шлемы с использованием литья под давлением?
- 4. Почему контроль качества имеет решающее значение в производстве шлемов?
- 5. Как стандарты безопасности влияют на производство шлема?
- 6. Заключение
Какие материалы лучше всего подходят для формования впрыскивания шлема?
Я помню, как впервые разобрался с шлемом, чтобы увидеть, что сделало его таким сильным и безопасным. Удивительно, как правильные материалы могут превратить простую плесень в спасительную часть снаряжения.
Поликарбонат и акрилонитрил-бутадиен-стирол ( ABS ) идеально подходят для формования впрыскивания шлема, обеспечивая превосходную сопротивление воздействия, долговечность и затратную эффективность, повышение прочности и эффективности шлема.
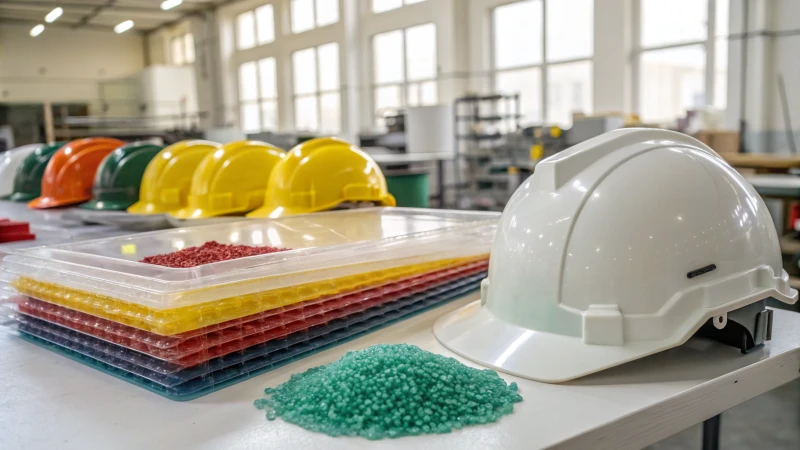
Когда я впервые начал возиться с дизайнами плесени, я был очарован искусством выбора правильных материалов. Это как найти идеальный баланс в рецепте, чтобы гарантировать, что конечный продукт не только долговечен, но и безопасен.
Почему выбирают поликарбонат?
Поликарбонат ( ПК ) быстро стал фаворитом в моем наборе инструментов. Его высокая ударная стойкость и оптическая ясность делают его незаменимым для производства шлема 1 . Думайте об этом, как ношение очков; Вы должны ясно видеть, не жертвуя безопасностью. ПК против силы означает, что когда все становится грубым, он сильна, чтобы защитить владельца.
- Устойчивость к воздействию: ПК похож на невидимый щит, поглощая удары без растрескивания.
- Оптическая ясность: необходимо для шлемов с козырьками; Как будто вы смотрите через кристально чистое окно.
- Механическая прочность: построенная до длительного времени, он сохраняет шлем нетронутым во времени и использовании.
Преимущества пресса
Затем есть акрилонитрил-бутадиен-стирол ( ABS ), который мне нравится думать как прочная основа производства шлема. Это доступно, но жестко, предлагая прочную основу, которая придерживается ежедневного износа.
- Прочность и жесткость: представьте себе устойчивость хорошо построенного дома-он предназначен для выдержания элементов.
- Экономическая эффективность: думайте о ABS как о том, чтобы дать вам больше отдачи за ваши деньги, особенно в крупномасштабном производстве.
- Простота обработки: материал мечты для эффективных производственных циклов, что делает производство меньше головной боли.
Материал | Ударопрочность | Расходы | технологичность |
---|---|---|---|
Поликарбонат | Высокий | Умеренный | Хороший |
АБС | Умеренный | Низкий | Отличный |
Объединение ПК и пресса
Смешивая поликарбонат и ABS 2 , это все равно, что сочетать арахисовое масло и желе - это приносит что -то особенное на стол. Эта смесь улучшает прочность, облегчает формирование сложных форм, а уравновешивает прекрасно.
Факторы, влияющие на выбор материала
Всякий раз, когда я глубоко в фазе проектирования, несколько факторов направляют мой выбор материалов:
- Стандарты безопасности: соответствие правилам безопасности не подлежит обсуждению; Эти шлемы должны защищать любой ценой. Изучите больше о стандартах безопасности 3 и о том, как эти материалы соответствуют строгим правилам для обеспечения оптимальной защиты.
- Дизайн шлема: сложные конструкции часто вызывают гибкие возможности ПК / АБС .
- Объем производства: для массового производства экономически эффективные материалы, такие как ABS, занимают центральное место.
Понимание этих элементов помогает создавать шлемы, которые не только соответствуют ожиданиям производительности, но и обеспечивают безопасность и комфорт пользователей. Так же, как создание шедевра, каждая деталь учитывается.
Поликарбонат предлагает высокую оптическую ясность для козырьков шлема.Истинный
Поликарбонат известен своей оптической ясностью, что делает его идеальным для четких козырьков.
ABS дороже поликарбонат для производства шлема.ЛОЖЬ
ABS, как правило, более рентабельный, чем поликарбонат, что делает его популярным для массового производства.
Как дизайн плесени влияет на качество шлема?
Вы когда-нибудь задумывались над тем, чтобы сделать высококачественный шлем? Давайте погрузимся в критическую роль дизайна плесени в формировании превосходства шлемов.
Конструкция плесени жизненно важна для производства шлема, влияя на структурную целостность, посадок и безопасность шлема. Точность в форме улучшает комфорт, эстетику и защитные характеристики шлема, обеспечивая высококачественную производительность.
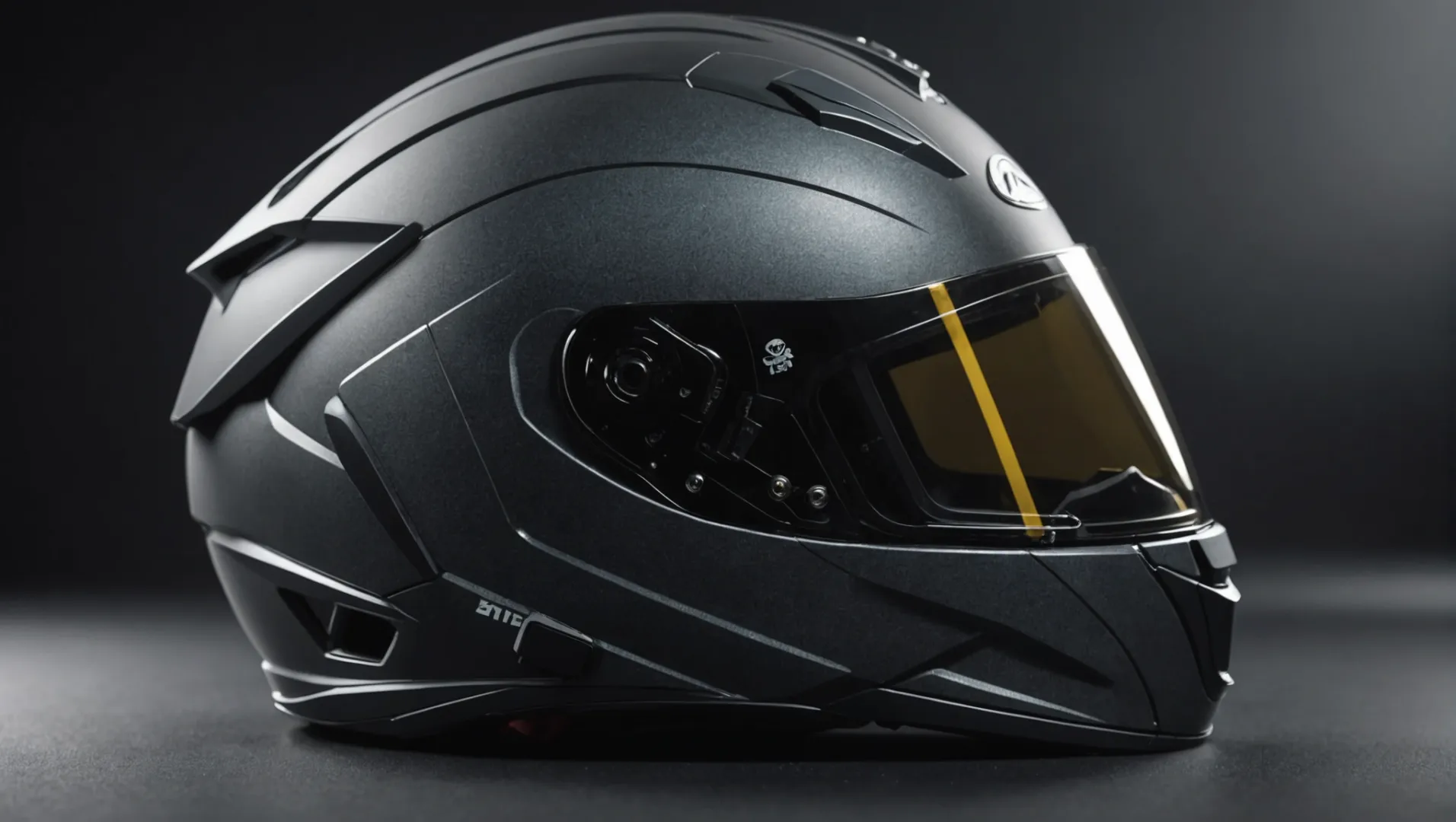
Выбор материала и его влияние
Когда я впервые начал работать с производством шлемов, я быстро узнал, что выбор правильных материалов - это все равно, что найти идеальные ингредиенты для рецепта - он может сделать или сломать конечный продукт. Мы обычно используем поликарбонат ( ПК ) и акрилонитрил-бутадиен-стирол ( ABS ), потому что они обеспечивают большой баланс воздействия и простоты обработки. ПК -это наше время для его выносливости, в то время как ABS помогает нам контролировать расходы без ущерба для качества.
Таблица, иллюстрирующая свойства материала:
Материал | Ударопрочность | технологичность | Экономическая эффективность |
---|---|---|---|
ПК | Высокий | Умеренный | Высокий |
АБС | Умеренный | Высокий | Умеренный |
Тонкости дизайна плесени
Стадия дизайна плесени ощущается как создание сложной головоломки. Каждый кусок, от кривизны шлема 4 до аэродинамической формы, должен идеально подходить. Я помню, как в первый раз, когда я увидел вентиляционные отверстия, встроенные в форму-это изменил правила игры для комфорта и функциональности, что позволяет улучшить воздушный поток.
Ключевые компоненты формы:
- Плесень корпуса шлема: это важно как для защиты, так и для внешнего вида.
- Внутренняя подкладочная плесень: Думайте об этом, как удобная подушка, которая оборачивается вокруг вашей головы.
- Система выброса: правильно размещенные выводы эжектора гарантируют, что шлем не выскакивает без повреждений.
Процесс литья под давлением
Инъекционное формование - это место, где происходит магия. Я все еще взволнован, наблюдая, как пластиковые гранулы превращаются в твердые шлемы. Например, мы плавим ПК при 280-320 ° C. Увлекательно видеть, как регулировочное давление впрыска 5 и скорость может повлиять на конечный продукт.
Этапы процесса:
- Плавание и инъекция: гранулы нагреваются, пока они не текут, как сироп.
- Охлаждение: шлем обретает форму, когда он охлаждается - время - это все здесь.
- Выброс: выходит новый блестящий новый шлем, готов к проверке.
Качественные соображения в дизайне плесени
Стандарты безопасности соблюдения не подлежат обсуждению в нашей линии работы. Я воочию видел, как гладкая отделка может предотвратить раздражение кожи, что дает точность в дизайне плесени, решающей для комфорта и безопасности.
Вот наш контрольный список для обеспечения первоклассного качества шлема:
- Устойчивость к воздействию: должен пройти строгие тесты безопасности.
- Поверхностная отделка 6 : гладкий шелк для максимального комфорта.
- Точность подходит: гарантирует, что шлем сидит прямо на вашей голове.
В конце концов, дизайн плесени - это не только эффективность, а в создании шлемов, которым люди могут доверять своей безопасности и комфорту.
Polycarbonate обеспечивает высокую ударную стойкость в шлемах.Истинный
Поликарбонат известен своей высокой сопротивлением, что делает его идеальным для шлемов.
ABS обеспечивает лучшую воздействие, чем поликарбонат.ЛОЖЬ
ABS обеспечивает умеренную ударную стойкость, в то время как поликарбонат обеспечивает высокую сопротивление.
Как управляются шлемы с использованием литья под давлением?
Вы когда -нибудь задумывались, как эти крепкие шлемы, которым мы так доверяем, оживают?
Инъекционное формование для шлемов включает в себя выбор материалов, проектирование плесени, плавление и инъекцию пластика, охлаждение, выброс шлема и тщательные проверки качества для обеспечения долговечности и безопасности.
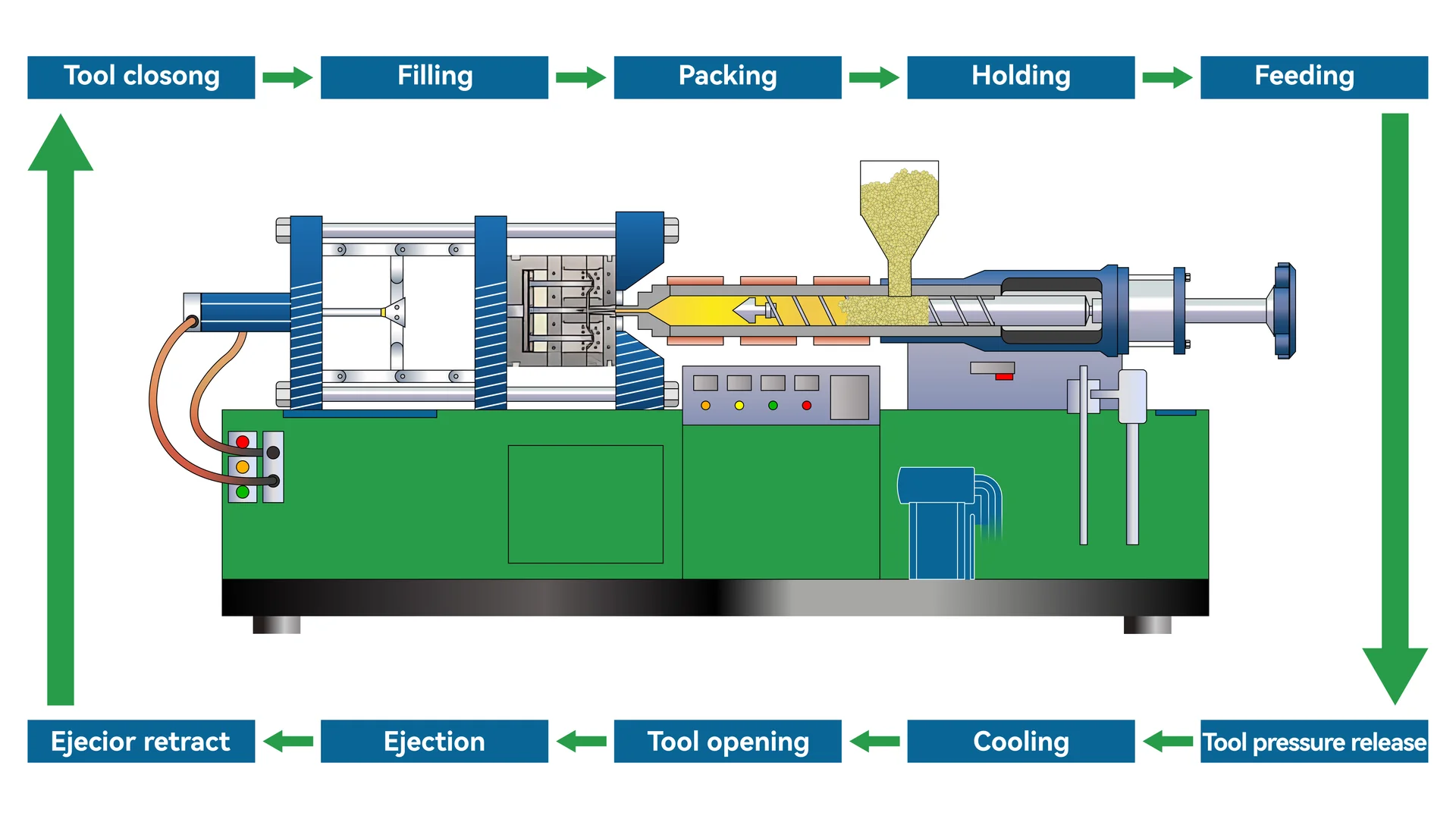
Выбор материала
Я помню, как впервые вошел на фабрику плесени; Это был собственный мир. Ключ к созданию отличного шлема начинается с выбора правильных материалов. Подумайте об этом, как выбор лучших ингредиентов для вашего любимого блюда. Для шлемов я часто смотрю на поликарбонат ( ПК ) на его первоклассный ударный сопротивление и ясность, или акрилонитрил-бутадиен-стирол ( ABS ), потому что он жесткий и экономичный. Смешивание этих двух может быть похоже на то, чтобы получить лучшее из обоих миров.
Материал | Характеристики |
---|---|
ПК | Высокая ударопрочность, прозрачность |
АБС | Прочность, экономически эффективная |
Дизайн пресс-формы
Плесень корпуса шлема:
Проектирование формы - это все равно, что создавать чертежи для нового дома. Это должно идеально отразить сложную форму шлема, факторинг в аэродинамике и безопасности. При проектировании для таких функций, как вентиляционные отверстия, крайне важно, чтобы они легко интегрированы в форму, чтобы обеспечить правильный поток воздуха.
Внутренняя плесень подкладки:
Для шлемов, которые требуют удобной внутренней подкладки, я использую отдельную форму, чтобы создать эту часть более мягкими материалами.
Система выброса:
И давайте не будем забывать о системе выброса - те крошечные выводы, должны быть размещены прямо, чтобы вытащить шлем из плесени без зацепления. Размещение основано на форме шлема, чтобы равномерно распределить силы выброса.
Процесс литья под давлением
Таяние и инъекция:
Теперь на главном событии! Все дело в том, чтобы нагревать эти пластиковые гранулы до тех пор, пока они не растают - с помощью гладкого шоколадного фонда, а затем вводят их в форму под высоким давлением. Для поликарбоната это означает, что температура взлетает до 320 ° C!
Материал | Точка плавления (°С) |
---|---|
Поликарбонат | 280-320 |
АБС | 200-260 |
Охлаждение и выброс:
После охлаждения и затвердевания удивительно наблюдать, как каждый шлем появляется из формы, готовый к действию.
Этот цикл повторяется для массового производства.
Вопросы качества
Наконец, проверки качества не подлежат обсуждению. Каждый шлем должен соответствовать строгим стандартам безопасности 7 ; В конце концов, мы говорим о защите жизни здесь. Поверхность должна быть гладкой, чтобы избежать раздражения при ношении. И поверьте мне, точность в формировании - это не просто внешность - это о том, чтобы каждый шлем был верным компаньоном, когда это необходимо больше всего.
Размышляя о моем путешествии в этой области, мне напоминают о том, как каждый шаг способствует созданию надежных шлемов, от которых зависят люди во всем мире для безопасности.
Поликарбонат плавится при 280-320 ° C в литье под давлением.Истинный
Точка плавления поликарбоната действительно находится в пределах этого ассортимента, подходящей для литья.
ABS используется для его оптической ясности в шлемах.ЛОЖЬ
ABS выбирается для выносливости и экономической эффективности, а не оптической ясности.
Почему контроль качества имеет решающее значение в производстве шлемов?
Вы когда -нибудь задумывались над тем, что на самом деле идет на создание шлема?
Контроль качества в производстве шлемов обеспечивает безопасность, долговечность и соблюдение стандартов посредством строгого тестирования, гарантируя эффективную защиту пользователей.
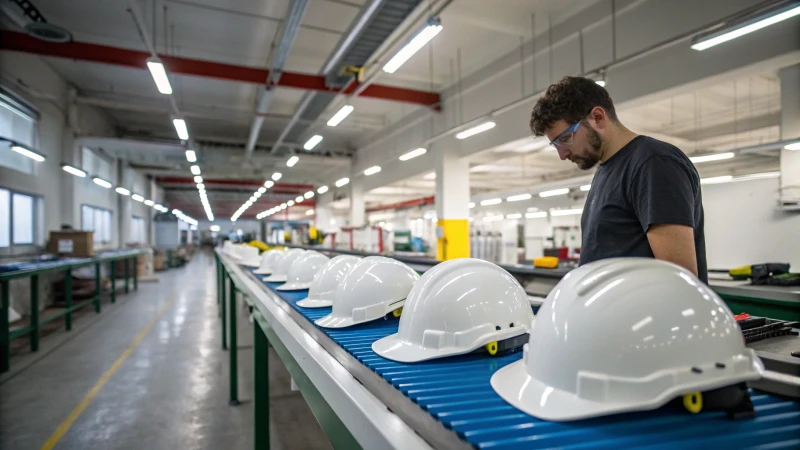
Выбор материала и важность
Я помню, как впервые увидел, как шлем прошел через его шаги в лаборатории управления качеством. Меня поразило, насколько много думает о выборе правильных материалов, таких как поликарбонат ( ПК ) и акрилонитрил-бутадиен-стирол ( АБС ). ПК обеспечивает невероятное воздействие, в то время как ABS предлагает жесткость и экономическую эффективность, необходимую для повседневного использования. В сочетании они создают сверхпрочный щит, который имеет решающее значение для повышения качества шлема 8 .
Значение дизайна плесени
В свои первые годы я узнал, что дизайн плесени - это все. Формы должны разместить каждую кривую и вентиляционное отверстие шлема, чтобы обеспечить его аэродинамику и обеспечивает первокласную защиту от удара.
Особенности дизайна плесени | Преимущества |
---|---|
Корпус шлема | Аэродинамическая форма и защита |
Внутренняя подкладка | Комфорт и амортизатор |
Система выброса | Удаление без повреждений |
Представьте, что вы проектируете внутреннюю подкладку, настолько уютную, что ощущается как подушка к вашей голове - это то, к чему мы стремимся с различными материалами для шокового поглощения 9 .
Процесс литья под давлением
Позвольте мне провести вас через магию процесса литья под давлением. Представьте себе: крошечные пластиковые гранулы преобразуются под теплом в форму шлема. Все дело в точке-поликарбонат плавится при 280-320 ° C, в то время как ABS нуждается в 200-260 ° C. После формирования эти шлемы охлаждают, прежде чем они выскочивают, готовые к производству шлема 10 .
Обеспечение стандартов безопасности
Стандарты безопасности не просто требование; Это ответственность, которую мы относимся к всерьез. Шлемы подвергаются батареи тестов на ударное сопротивление и стабильность, чтобы гарантировать, что они накапливаются. Даже поверхностная отделка имеет значение - никто не хочет зудящего, неудобного шлема! Внимание к деталям во время процесса обеспечения качества 11 гарантирует, что каждый шлем не только выглядит хорошо, но и прекрасно.
Шлемы ПК обеспечивают лучшую воздействие, чем шлемы ABS.Истинный
Поликарбонат (ПК) обладает более высокой воздействием по сравнению с акрилонитрил-бутадиен-стиролом (АБС).
ABS дороже, чем ПК в производстве шлема.ЛОЖЬ
ABS, как правило, более рентабельный, чем поликарбонат (ПК) в производстве.
Как стандарты безопасности влияют на производство шлема?
Вы когда -нибудь задумывались, как стандарты безопасности формируют способ, которым делаются шлемы? Он более сложный, чем вы думаете, влияя на все, от выбора материалов до крошечных деталей дизайна.
Стандарты безопасности влияют на производство шлема, устанавливая строгие критерии для материалов, проектирования и тестирования, чтобы обеспечить оптимальное воздействие и сопротивление проникновению.
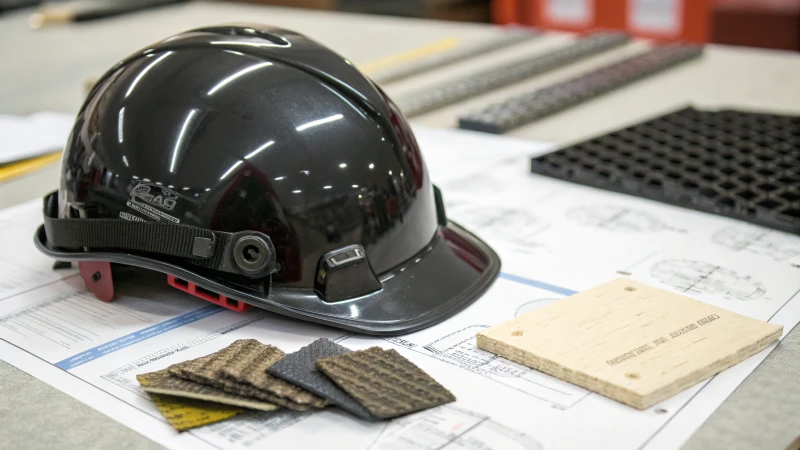
Выбор материалов и стандарты безопасности
Я помню, как впервые я держал шлем из поликарбоната ( ПК ) и акрилонитрил-бутадиен-стирола ( АБС ). Эти материалы увлекательны, потому что они сочетают в себе выносливость с способностью поглощать удары во время столкновений - вроде дуэта супергероя!
- Polycarbonate ( ПК ): это похоже на незамеченного героя, предлагая высокую ударную сопротивление 12 и оптическую ясность.
- Акрилонитрил-бутадиен-стирол ( ABS ): он приносит прочность и является бюджетным.
- Комбинация: Использование оба дает нам шлем, который может обрабатывать жесткие воздействия при снижении затрат.
Дизайн плесени под влиянием стандартов
Проектирование формы шлема похоже на создание таможенной перчатки. Плесень должна обнять каждую кривую головы, чтобы обеспечить как комфорт, так и безопасность. Однажды я наблюдал за дизайнером, тщательно расположенным вентиляционными отверстиями, чтобы разрешить воздушный поток без компромисса безопасности. Именно эти мелкие детали имеют такую большую разницу!
- Область головы: обеспечивает комфорт и безопасность.
- Аэродинамическая форма: уменьшает сопротивление при сохранении защиты.
- Вентиляционное размещение: позволяет воздушный поток без компромисса безопасности.
Внутренняя подкладка использует более мягкие материалы для комфорта и дополнительного амортизатора.
Процесс литья и соблюдение инъекции
Свидетельство о процессе литья инъекции, похоже на то, что волшебство разворачивается. Машина растает пластиковые гранулы и с точностью вводит их в формы. Стандарты определяют давление 13 и скорость, обеспечивая, чтобы шлемы соответствовали этим требованиям к критическому воздействию.
Этап | Описание |
---|---|
Плавление и инъекция | Пластиковые гранулы растоплены и впрыскивают в плесени. |
Охлаждение и выброс | Шлемы прохладны, прежде чем их выбросили из плесени. |
Контроль качества на основе стандартов
Каждый шлем тщательно протестирован, чтобы обеспечить соответствие стандартам безопасности. Я видел, как они проходили тесты на сопротивление воздействия, которые имитируют реальные аварии-это интенсивно, но необходимо.
- Устойчивость к воздействию: протестировано на защиту во время аварий.
- Сопротивление проникновения: не гарантирует, что острые объекты не могут проникнуть в шлем.
- Поверхностная отделка: гладкая отделка предотвращает раздражение кожи.
Подгонка, под влиянием точного литья, необходима для безопасности пользователей и комфорта.
Роль стандартов безопасности в инновациях
Стандарты безопасности - это не только соответствие; Они также об инновациях. Они подталкивают производителей изучить новые материалы 14 и процессы, которые повышают защиту, придерживаясь строгих правил. Этот поиск инноваций приводит к более безопасным и удобным шлемам-беспроигрышный вариант для всех участников.
Размышляя об этих аспектах, я вижу, как руководствует производителей стандартов безопасности производителей в создании шлемов, которые защищают жизни. По мере развития технологий эти стандарты будут развиваться, продолжая оспаривать и вдохновлять нас на создание вечно оформленных шлемов.
Поликарбонат выбирается для его оптической ясности в шлемах.Истинный
Поликарбонат известен своей высокой воздействием и оптической ясностью.
ABS дороже, чем поликарбонат в производстве шлема.ЛОЖЬ
ABS предлагает прочность и экономическую эффективность, что делает его дешевле.
Заключение
Машины для литья под давлением создают шлемы, выбирая такие материалы, как поликарбонат и ABS , проектируя плесени, впрыскивая расплавленный пластик, охлаждая продукт и обеспечивая качество в соответствии с строгими стандартами безопасности.
-
Узнайте, почему поликарбонат предпочитается в производстве шлема за его воздействие и ясность. ↩
-
Поймите, как смешивание ПК и ABS повышает прочность на шлем и эффективность процесса. ↩
-
Узнайте, как различные материалы соответствуют стандартам безопасности, необходимыми для производства шлемов. ↩
-
Изучение этой ссылки даст представление о том, как формы плесени влияют на производительность и безопасность шлема. ↩
-
Узнав больше о давлении впрыска поможет понять его роль в достижении последовательного качества шлема. ↩
-
Нажатие на эту ссылку покажет, почему отделка поверхности имеет решающее значение для безопасности шлема и комфорта пользователя. ↩
-
Заведите необходимые стандарты безопасности, чтобы обеспечить надежность шлема во время воздействия. ↩
-
Узнайте, как комбинирование ПК и ABS повышает долговечность и безопасность шлема. ↩
-
Узнайте, почему хорошо разработанные формы необходимы для целостности шлема. ↩
-
Исследуйте шаги, связанные с точным литьем подъема шлемов. ↩
-
Поймите строгие тестирующие шлемы, чтобы соответствовать стандартам безопасности. ↩
-
Узнайте, как материалы поликарбоната и ABS повышают безопасность шлема за счет превосходной ударов. ↩
-
Узнайте об оптимальных настройках давления впрыска, которые имеют решающее значение для производства шлемов, соответствующих стандартам безопасности. ↩
-
Исследуйте передовые материалы, ведущие инновации в производстве шлемов, обеспечивая при этом соответствие стандартам безопасности. ↩