Você já se sentiu frustrado com marcas de fusão em produtos moldados por injeção? Acredite em mim, eu também enfrentei isso. O trabalho árduo muitas vezes parece arruinado por defeitos. Realmente desanimador.
Para evitar marcas de fusão em produtos moldados por injeção, otimize o projeto do molde, ajuste as configurações de moldagem, selecione materiais adequados e posicione as portas corretamente. A identificação da velocidade ideal de injeção e o uso de materiais fluidos também melhoram a qualidade do produto.
Minha jornada na moldagem por injeção me mostrou que compreender o projeto do molde é fundamental para lidar com marcas de fusão. Ajustes de processos e escolhas de materiais também são vitais. Esses elementos são importantes para alcançar o acabamento perfeito. Cada parte é muito importante. Ajuda a alcançar ótimos resultados.
Explorar esses detalhes é realmente essencial. Compartilhar insights provavelmente melhorará a qualidade da sua produção.
As marcas de fusão podem ser completamente eliminadas na moldagem por injeção.Falso
Embora as técnicas possam reduzir as marcas de fusão, a eliminação completa muitas vezes é irrealista devido a vários fatores no processo de moldagem.
A seleção do material desempenha um papel fundamental na prevenção de marcas de fusão.Verdadeiro
A escolha dos materiais certos é crucial, pois influencia as taxas de fluxo e resfriamento, afetando assim a formação de marcas de fusão.
Como o design do molde pode ajudar a prevenir marcas de fusão?
Você já pensou em como os pequenos detalhes do design do molde afetam a qualidade do produto? Vamos explorar o interessante mundo da moldagem por injeção. Revele os segredos para impedir essas marcas de fusão irritantes.
O projeto do molde ajuda a evitar marcas de fusão selecionando posições ideais de comporta, ajustando sistemas de canais, usando materiais adequados e ajustando parâmetros de processo, o que melhora o fluxo e a fusão do plástico fundido.
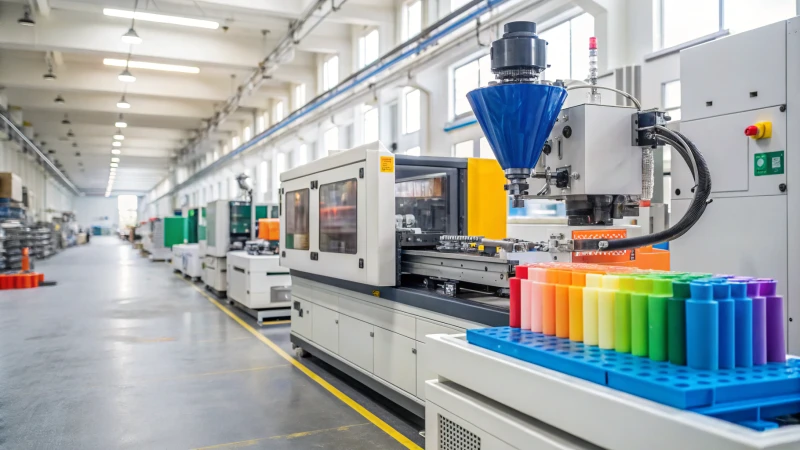
A importância do design do molde na moldagem por injeção
O projeto do molde é crucial no processo de moldagem por injeção, especialmente quando se trata de minimizar defeitos como marcas de fusão. As marcas de fusão ocorrem quando dois fluxos de plástico derretido se encontram, mas não se misturam adequadamente, levando a linhas visíveis ou imperfeições na superfície do produto.
Otimizando a posição e o número do ponto de injeção
Uma das primeiras considerações no projeto do molde é a posição do ponto de injeção . Uma comporta bem posicionada ajuda a melhorar o fluxo do plástico fundido, reduzindo significativamente as marcas de solda. Por exemplo, empregar um design de portão multiponto pode ser benéfico para formas complexas com múltiplas áreas de paredes finas.
Imagine um produto de plástico projetado com três portas localizadas estrategicamente em diferentes posições; esta configuração permite que o fundido preencha a cavidade simultaneamente em várias direções, minimizando assim a possibilidade de marcas de solda.
Tipo de portão | Descrição | Benefícios |
---|---|---|
Portões laterais | Posicionado na lateral do molde, permitindo um fluxo mais direto. | Bom para formas simples. |
Portões precisos | Introduz o fundido em formato de jato, melhorando a dispersão. | Reduz marcas de solda de forma eficaz. |
Portões Latentes | Portões ocultos que se abrem durante a injeção, melhorando a estética e a funcionalidade. | Reduz marcas de bloqueio visíveis. |
Melhorando o Sistema Runner
O sistema de canais também desempenha um papel significativo na prevenção de marcas de fusão. Um sistema de canal balanceado garante um fluxo uniforme do plástico fundido, enquanto fatores como tamanho e rugosidade da superfície podem influenciar a dinâmica do fluxo. Por exemplo, o uso de canais circulares reduz a resistência ao fluxo, permitindo um fluxo mais suave do fundido na cavidade.
Além disso, a incorporação de desviadores ou tampões dentro do canal pode ajudar a distribuir o fundido uniformemente em diferentes canais ramificados, estabilizando o fluxo e minimizando a turbulência na entrada na cavidade. Esta etapa é crucial, pois a turbulência pode levar à fusão incompleta e ao aumento da probabilidade de marcas de fusão.
Ajustando os parâmetros do processo de moldagem por injeção
Além do projeto do molde, o ajuste dos parâmetros do processo é essencial para evitar marcas de fusão. Os principais ajustes incluem:
- Velocidade de injeção: Aumentar a velocidade de injeção pode aumentar a fluidez do fundido, promovendo melhor fusão quando os fluxos convergem. Porém, é necessário cuidado para evitar velocidades excessivas que possam causar problemas de ejeção.
- Pressão de injeção: Pressão suficiente garante o preenchimento completo de todos os cantos da cavidade, evitando problemas como flash. Encontrar uma faixa ideal é vital para manter a qualidade.
- Parâmetros de retenção: Prolongar o tempo de retenção e aumentar a pressão durante o resfriamento ajuda a garantir que áreas de parede mais espessas recebam reposição adequada de material fundido, reduzindo ainda mais as marcas de solda.
Selecionando Materiais para Fluxo Ideal
A seleção do material é outro fator crítico. A escolha de plásticos com boa fluidez pode reduzir significativamente as marcas de solda. Por exemplo:
- Materiais com alta taxa de fluidez, como PP (polipropileno), permitem uma melhor mistura em cavidades.
- A adição de lubrificantes também pode melhorar a fluidez do material, facilitando a fusão correta dos fundidos.
Garantir que os materiais estejam devidamente secos antes do uso é igualmente importante. Para materiais higroscópicos como o Nylon (PA) , é necessário um protocolo de secagem rigoroso (80-90°C durante 4-6 horas) para evitar defeitos que possam contribuir para marcas de solda.
Ao focar nesses aspectos do projeto do molde e dos parâmetros de moldagem por injeção, os fabricantes podem melhorar significativamente a qualidade do produto e reduzir defeitos como marcas de fusão.
A otimização da posição do portão minimiza as marcas de fusão na moldagem.Verdadeiro
A colocação estratégica de comportas melhora o fluxo de fusão, reduzindo as chances de aparecimento de marcas de fusão nos produtos moldados.
A fluidez do material não tem impacto na prevenção de marcas de fusão.Falso
A escolha de materiais com alta fluidez é essencial, pois eles se misturam melhor, reduzindo significativamente a ocorrência de marcas de fusão.
Como posso otimizar os parâmetros do processo de moldagem por injeção?
Você quer melhorar suas habilidades de moldagem por injeção? Comece uma jornada comigo para descobrir como ajustar seu processo para obter melhor eficiência e produtos de alta qualidade. Vamos explorar juntos os detalhes do design do molde, definir alterações e escolher os materiais certos!
Otimize a moldagem por injeção ajustando o projeto do molde, a posição da porta, os sistemas de canais, a velocidade de injeção, a pressão e a temperatura do molde. Utilize materiais com boa fluidez para melhorar a qualidade do produto e reduzir defeitos como marcas de solda.
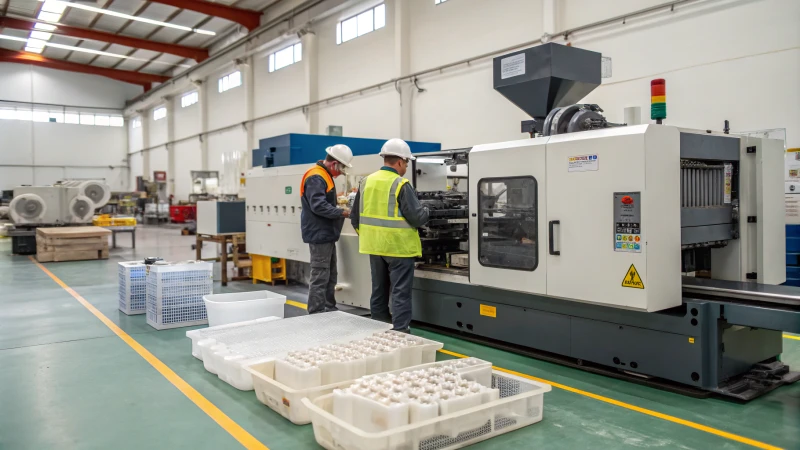
Compreendendo o design de moldes
A otimização do processo de moldagem por injeção começa com um projeto de molde . Os elementos principais incluem:
- Posição e número da comporta : A colocação das comportas afeta o fluxo do plástico fundido. Para formas complexas, considere um projeto de comporta multiponto para melhorar o enchimento do fundido.
Por exemplo, em um invólucro de plástico, o uso de três portas pode ajudar a distribuir o fundido uniformemente, minimizando marcas de solda.
- Sistema Runner : Um sistema de corredor balanceado garante um fluxo uniforme. Um corredor circular é frequentemente preferido devido à menor resistência ao fluxo. O polimento da superfície do canal reduz o atrito, permitindo um fluxo de fusão mais suave.
Ajustando os parâmetros de moldagem por injeção
Em seguida, concentre-se no ajuste dos parâmetros do processo de moldagem por injeção . Considere estes ajustes:
- Velocidade e pressão de injeção : Aumentar a velocidade de injeção mantém temperaturas de fusão mais altas, o que melhora a fusão e reduz marcas de solda. No entanto, a velocidade excessiva pode levar a defeitos como a ejeção.
Parâmetro | Efeito no processo |
---|---|
Maior velocidade de injeção | Maior fluidez de fusão |
Pressão de injeção ideal | Preenchimento completo da cavidade |
- Parâmetros de retenção : Estender o tempo de retenção e aumentar a pressão auxilia na melhor fusão do fundido durante o resfriamento. Para produtos com espessura de parede irregular, ajuste os tempos de espera de acordo.
Seleção e processamento de materiais
A escolha dos materiais certos influencia significativamente os resultados. As principais considerações incluem:
-
Fluidez dos Materiais : Selecione materiais com altas taxas de fluxo de fusão para melhorar o preenchimento da cavidade e reduzir marcas de solda. Por exemplo, PP (polipropileno) com alto MFR pode melhorar o desempenho.
-
Secagem do Material : Certifique-se de que os materiais estejam adequadamente secos para evitar defeitos durante a injeção. Para materiais sensíveis à umidade como o náilon (PA), a secagem a 80-90°C por 4-6 horas é essencial para evitar problemas de qualidade.
Controle da temperatura do molde
Finalmente, controle a temperatura do molde de forma eficaz.
- Manter uma temperatura adequada do molde aumenta a fluidez do fundido e reduz a chance de solidificação que pode causar marcas de solda. Para materiais de alta viscosidade como PC (policarbonato), uma temperatura mais alta do molde facilita uma melhor mistura do fundido.
Concluindo, a otimização da moldagem por injeção envolve uma abordagem multifacetada com foco no projeto do molde, parâmetros do processo, seleção de materiais e controle de temperatura. Ao examinar minuciosamente cada aspecto, os fabricantes podem melhorar a qualidade e a eficiência do produto.
Projetos de portas multiponto melhoram o enchimento por fusão na moldagem por injeção.Verdadeiro
O uso de múltiplas portas no projeto de molde melhora a distribuição do plástico fundido, minimizando marcas de solda e garantindo melhor preenchimento de formas complexas.
Temperaturas mais altas do molde reduzem marcas de solda em produtos moldados por injeção.Verdadeiro
A manutenção de temperaturas de molde adequadas aumenta a fluidez do fundido, reduzindo os riscos de solidificação que podem levar a defeitos como marcas de solda durante o processo de injeção.
Quais materiais você deve escolher para minimizar marcas de fusão?
A escolha do material no corte ou gravação a laser é crucial. Diferentes materiais afetam significativamente o produto final. Descobri isso em muitos projetos. Cada um me ensinou como selecionar o material certo. Essa decisão realmente influencia o resultado. Vamos explorar isso juntos!
Para minimizar marcas de fusão na usinagem a laser, escolha materiais com alta fluidez, seque-os completamente e use aditivos para melhorar as propriedades de fluxo para obter acabamentos mais limpos e melhorar a qualidade geral.
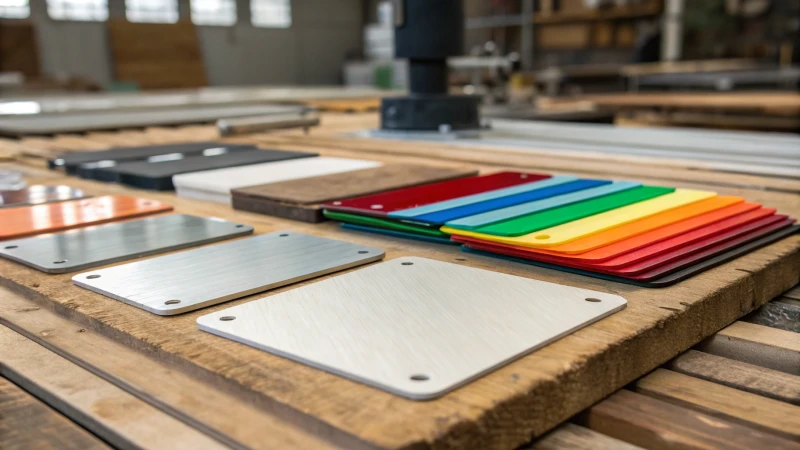
Compreendendo as marcas de fusão
Marcas de fusão são pequenas imperfeições causadas por corte ou gravação a laser. Muitas vezes surgem da interação entre as propriedades de um material e as configurações do laser. Selecionar os materiais certos é minha técnica secreta para minimizar essas marcas, resultando em um acabamento mais limpo.
Propriedades do material que afetam as marcas de fusão
- Fluidez dos
Materiais Materiais com boa fluidez criam uma fusão mais suave durante o processamento.
Aqui está uma tabela mostrando alguns materiais comuns e suas características de fluxo:
Material | Taxa de fluxo de fusão (MFR) | Comentários |
---|---|---|
Polipropileno (PP) | Alto | Excelente para designs complexos |
Policarbonato (PC) | Moderado | Boa resistência ao impacto |
Náilon (PA) | Baixo | Requer secagem completa |
Por exemplo, certa vez usei PP de alto grau de fluidez para um projeto detalhado, o que reduziu bastante as marcas de solda devido às suas propriedades de fluxo superiores.
-
Conteúdo de umidade
A umidade pode realmente arruinar materiais como o náilon, causando bolhas e imperfeições indesejadas.
Garanta uma secagem completa antes de usar:- Temperatura de secagem: 80-90°C
- Duração: 4-6 horas
Esta etapa é essencial para preservar a integridade do material e reduzir marcas de fusão.
-
Aditivos que melhoram a fluidez
Às vezes testo com lubrificantes ou aditivos que melhoram o fluxo.
Estes podem ser muito eficazes, especialmente para projetos complexos ou quando se utilizam materiais difíceis de manusear.
Selecionando o material certo para o seu projeto
Ao selecionar materiais, considere fatores importantes:
- Requisitos de aplicação : Se a aparência é importante, escolho materiais com alto MFR.
- Fatores ambientais : Temperatura e umidade afetam o desempenho; Eu sempre os levo em consideração.
Para obter mais informações sobre seleção de materiais, consulte este recurso sobre propriedades de materiais 1 .
Conclusão sobre seleção de materiais
Finalmente, aprendi que escolher os materiais certos e entendê-los reduz as marcas de fusão. Otimizar as escolhas com base na fluidez, teor de umidade e aditivos é fundamental para obter melhores resultados em corte e gravação a laser.
Materiais de alta fluidez reduzem marcas de fusão no corte a laser.Verdadeiro
Materiais como o polipropileno com alta fluidez permitem melhor fusão do fundido, minimizando imperfeições durante o processamento a laser.
A umidade no náilon aumenta o risco de marcas de fusão.Verdadeiro
O excesso de umidade no náilon pode causar bolhas e imperfeições, piorando as marcas de fusão durante o corte ou gravação a laser.
Quais são as causas comuns de marcas de fusão em moldagem por injeção?
Você já viu aquelas marcas de fusão irritantes em seus produtos moldados por injeção? Eu também tenho. Entender por que eles acontecem realmente nos ajuda a melhorar. Vamos explorar os principais motivos desses defeitos!
As marcas de fusão na moldagem por injeção são comumente causadas por um projeto inadequado do molde, configurações de processo inadequadas ou escolhas de materiais inadequadas, com fatores-chave incluindo posicionamento da porta, velocidade de injeção e umidade do material. Compreender esses fatores melhora a qualidade do produto.
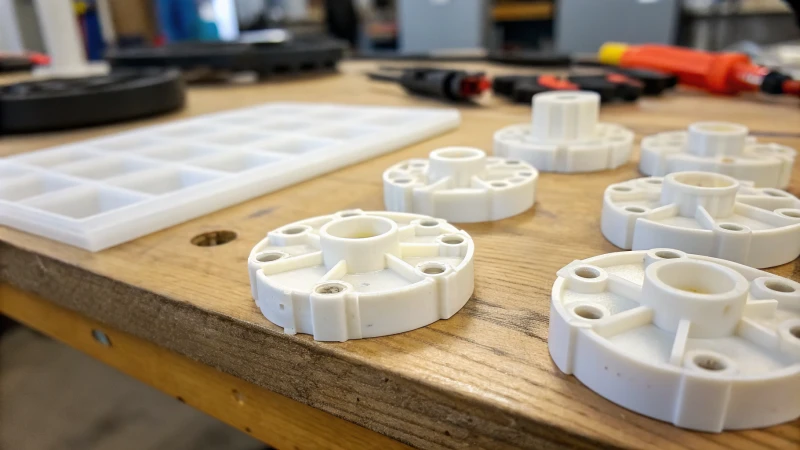
Projeto de molde
O design do molde é um fator crucial na prevenção de marcas de fusão durante a moldagem por injeção. A otimização da posição e do número da comporta pode influenciar significativamente o caminho do fluxo do plástico fundido, minimizando as marcas de solda.
Por exemplo, empregar um design de porta multiponto em produtos complexos pode garantir um enchimento mais uniforme da cavidade do molde. Em um produto de invólucro de plástico, a colocação de três portas em locais diferentes permite que o fundido convirja de várias direções, reduzindo efetivamente a probabilidade de marcas de solda.
Além disso, o tipo de portão desempenha um papel fundamental. Portas pontuais, por exemplo, permitem que o fundido entre na cavidade em forma de jato, promovendo melhor dispersão e fusão do fundido, crucial para produtos com altas demandas estéticas. Minha equipe gostou muito da melhoria da qualidade após essa mudança.
Ajuste de parâmetros do processo de moldagem por injeção
Ajustar os parâmetros do processo, como velocidade e pressão de injeção, é vital para minimizar marcas de fusão. O aumento da velocidade de injeção aumenta a temperatura e a fluidez do fundido dentro da cavidade, o que auxilia na sua convergência e fusão. No entanto, deve-se ter cuidado para não definir velocidades muito altas para evitar problemas de qualidade como a ejeção – uma lição que aprendi bem.
Um exemplo desse ajuste pode ser visto na injeção de produtos plásticos nervurados; aumentar a velocidade na área de confluência permite uma fusão mais rápida dos fundidos. Além disso, otimizar os parâmetros de retenção estendendo o tempo de retenção e aumentando a pressão de retenção pode reduzir significativamente as marcas de solda, garantindo melhor fusão durante o resfriamento.
Seleção e processamento de materiais
Escolher os materiais certos é essencial para evitar marcas de fusão. A seleção de plásticos com altas taxas de fluidez (MFR), como o polipropileno (PP) de alta fluidez, aumenta a fluidez e a mistura do fundido dentro da cavidade, reduzindo assim as marcas de solda.
Além disso, é fundamental garantir que os materiais estejam devidamente secos antes da moldagem por injeção. A umidade nos materiais pode causar defeitos durante o processamento e afetar adversamente a fusão por fusão; tornando crucial que materiais sensíveis à umidade, como o náilon (PA), sejam submetidos a processos completos de secagem.
Fator | Descrição | Exemplo |
---|---|---|
Projeto de molde | Otimize as posições e os tipos de portas para melhorar os caminhos do fluxo | Portões multiponto em formas complexas |
Parâmetros de injeção | Ajuste a velocidade e a pressão para um fluxo de fusão ideal | Maior velocidade para confluência de costelas |
Seleção de Materiais | Utilize materiais com boa fluidez e garanta uma secagem adequada | PP de alto MFR; secagem de náilon a 80-90°C |
Cada um desses aspectos desempenha um papel significativo na minimização de marcas de fusão em produtos moldados por injeção, contribuindo para a qualidade e aparência geral.
A otimização do projeto da porta reduz marcas de fusão nos moldes.Verdadeiro
O posicionamento e o design adequados da comporta melhoram o fluxo de fusão, minimizando marcas de solda durante a moldagem por injeção.
O alto teor de umidade nos materiais causa marcas de fusão.Verdadeiro
O excesso de umidade pode causar defeitos no fundido, afetando a fusão e resultando em marcas visíveis no produto.
Conclusão
Aprenda como minimizar marcas de fusão em produtos moldados por injeção por meio de projeto de molde otimizado, parâmetros de processo precisos e seleção cuidadosa de materiais.
-
Descubra orientações detalhadas sobre como escolher materiais para minimizar marcas de fusão em seus projetos. ↩