初めて射出成形の世界に足を踏み入れたとき、細部が製品の成功を左右することにすぐに気づきました。その詳細のうちの 1 つでしょうか?補強リブのデザイン。
射出成形品の強度を最大限に高め、欠陥を防ぐには、効果的な補強リブを設計することが不可欠です。主な考慮事項には、リブの厚さ、高さ、角度、レイアウト、および材料の選択が含まれます。
しかし、基本を知るだけでは意味がありません。各要素をさらに深く掘り下げて、それらが現実世界のアプリケーションにどのような影響を与えるかを明らかにしましょう。
リブの厚さは壁の厚さの 50% を超えてはなりません。真実
リブの厚みを50%以下に抑えることで、反りなどの不良を防ぎます。
リブの厚さは射出成形にどのような影響を与えますか?
リブの厚さは射出成形における重要な要素であり、成形製品の構造的完全性と美的品質に影響を与えます。
リブの厚さは、冷却速度、収縮、反りなどの欠陥の可能性に影響を与えるため、射出成形に影響を与えます。理想的には、均一な冷却を維持し、欠陥を防ぐために、リブの厚さは製品の壁の厚さの 50% を超えてはなりません。
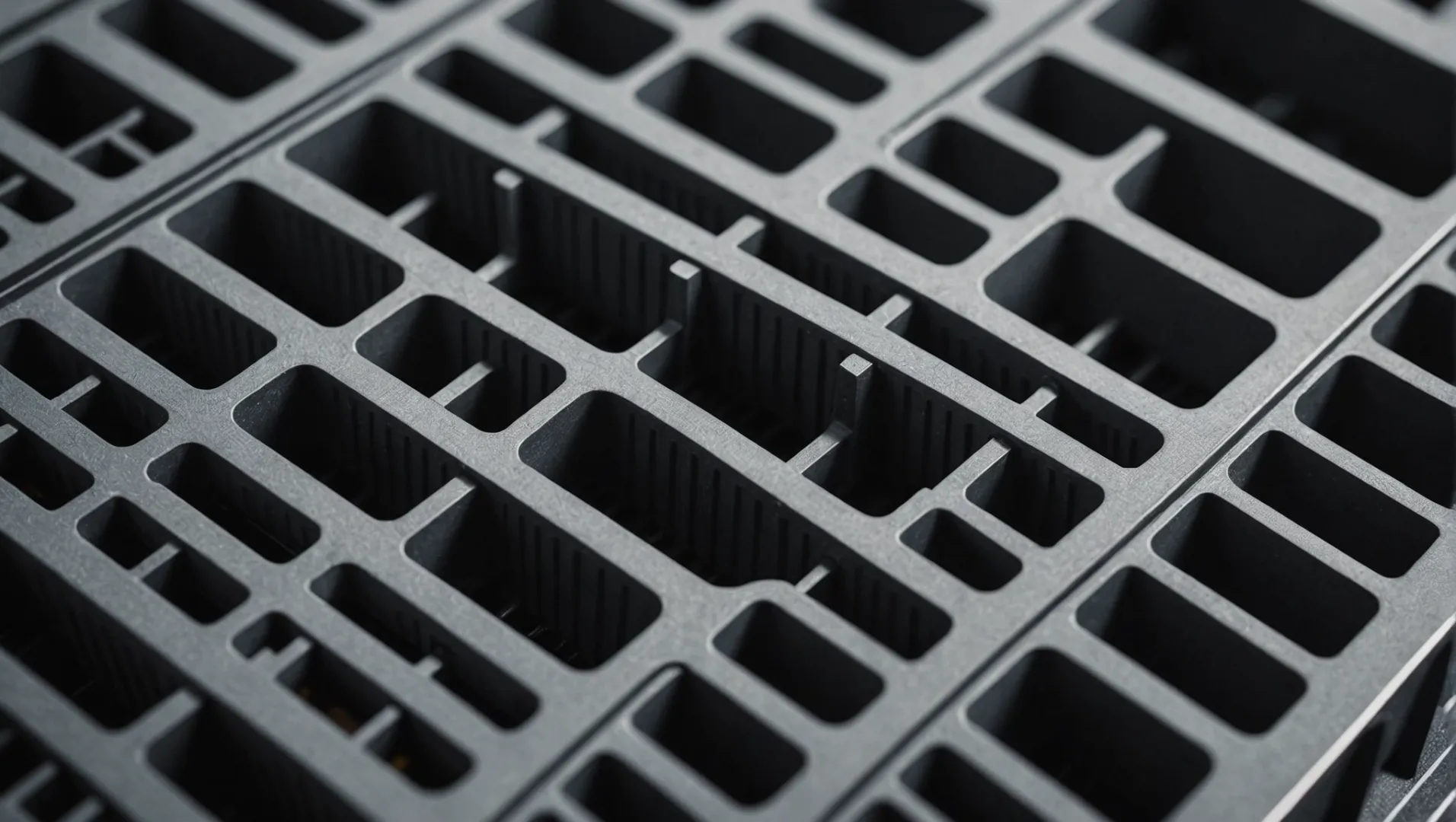
リブの厚さとその意味を理解する
射出成形では、リブの厚さは単なる設計上の選択ではありません。これは、成形プロセス全体の成功を左右する重要なパラメータです。リブは、重量や材料使用量を大幅に増やすことなく、成形部品の強度と剛性を高めるために不可欠です。ただし、厚さが不適切だと、収縮マーク、反り、さらには構造上の欠陥などの欠陥が発生する可能性があります。
比例したリブの厚さの重要性
リブの厚さの一般的なガイドラインは、主要コンポーネントの壁の厚さの 50% を超えないようにすることです。この比率により、冷却が成形品全体で均一に行われるようになります。不均一な冷却は収縮差を引き起こし、反りや歪みとして現れる内部応力を引き起こす可能性があります。さらに、リブが厚すぎると冷却時間が長くなり、サイクルタイムと生産コストが増加する可能性があります。
リブの厚さが壁の厚さに比べて大きすぎるシナリオを考えてみましょう。このような場合、厚い部分は薄い部分よりもゆっくりと冷却され、冷却速度に勾配が生じます。この不一致により部品内に内部応力が発生し、最終的には動作条件下での反りや亀裂につながる可能性があります。
リブの厚さと構造上のニーズのバランスをとる
適切なリブの厚さを維持することは不可欠ですが、これと製品の構造要件のバランスを取ることも同様に重要です。たとえば、高い剛性が要求されるアプリケーションでは、リブをより厚くする必要がある場合があります。ここで、より高い強度対重量比の材料を使用すると、構造上の要求を満たしながら、リブをより薄くすることが可能になります。高い強度重量比を持つ材料について詳しく調べてください1 。
場合によっては、設計段階でシミュレーション ツールを使用すると、リブ寸法を最適化し、厚さの違いが最終製品にどのような影響を与えるかを予測するのに役立ちます。これらのツールは、潜在的な欠陥領域に関する貴重な洞察を提供し、設計者が実際の生産前にパラメータを調整できるようにします。
実用化: ケーススタディ
構造サポートを追加するためにリブが必要な自動車部品を考えてみましょう。メーカーは、リブの厚さを壁の厚さの 50% 以下に維持することで、目に見える表面のヒケなどの外観上の欠陥がコンポーネントに発生しないことを保証します。さらに、リブの配置と厚さを最適化することで、部品の美観や製造効率を損なうことなく、必要な機械的特性を実現できます。
結論として、リブの厚さは射出成形において極めて重要な役割を果たします。リブ寸法に関するベストプラクティスに従うことで、メーカーは一般的な欠陥を軽減し、高品質の結果を保証できます。
リブの厚さは壁の厚さの 50% を超える必要があります。間違い
50%を超えると冷却が不均一になり、反りなどの不良が発生します。
リブが厚いと、射出成形のサイクル時間が長くなる可能性があります。真実
リブが厚いと冷却が遅くなり、全体の生産サイクル時間が長くなります。
リブのレイアウトは構造の完全性においてどのような役割を果たしますか?
リブのレイアウトは射出成形製品の構造的完全性の基本的な側面であり、製品の強度と耐久性に大きく影響します。
リブのレイアウトは、応力の分散と射出成形製品の全体的な安定性に影響を与えるため、構造の完全性にとって非常に重要です。適切なリブ配置により応力が均一に分散され、歪みが最小限に抑えられ、剛性が向上します。
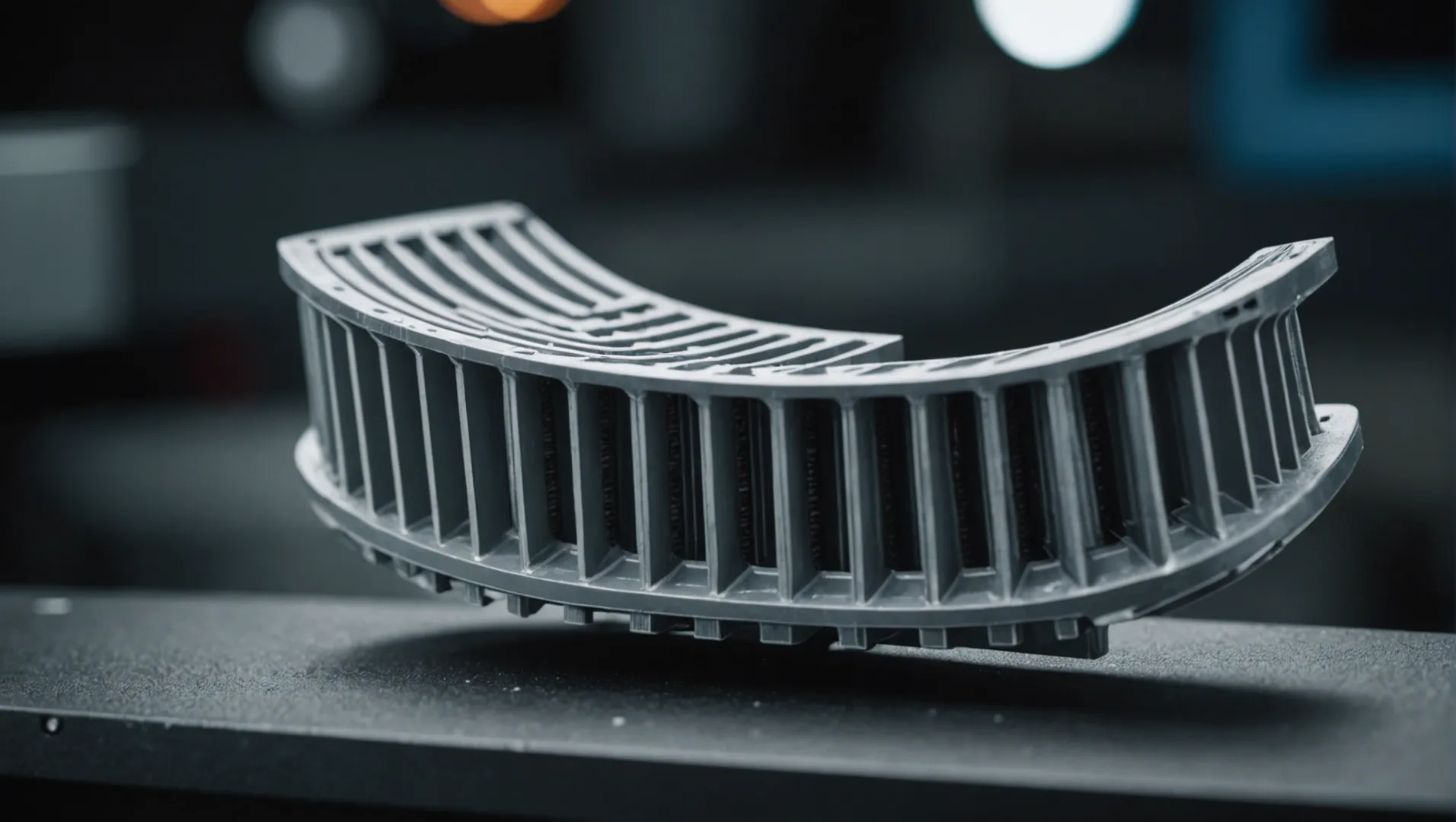
リブレイアウトの重要性を理解する
リブのレイアウトは、製品全体にただ無計画にリブを配置するだけではありません。これには、コンポーネントの構造的完全性を最大限に高めるための戦略的な配置が含まれます。レイアウトは製品全体に応力がどのように分散されるかに影響を与え、ひいては負荷時のパフォーマンスに影響を与えます。
-
均一な分布: 単一の領域に過剰な応力がかからないよう、補強リブは製品全体に均等に分布する必要があります。不均一な分布は、射出成形プロセス2 。
-
数量と位置: リブの数とその位置は、製品の形状と予想される応力点に基づいて決定する必要があります。たとえば、より高い負荷がかかる領域には、補強のために追加のリブが必要になる場合があります。
最大限の効果をもたらす最適な間隔
リブ間の間隔も重要な要素です。理想的には、リブの間隔は製品の壁厚の約 2 ~ 3 倍である必要があります。この間隔は、サポートの提供と溶接跡などの問題の回避との間のバランスを維持するのに役立ちます。
表: 推奨リブ間隔
肉厚 | 推奨リブ間隔 |
---|---|
1mm | 2~3mm |
2mm | 4~6mm |
3mm | 6~9mm |
製品壁面との接続
応力集中を避けるためには、リブと製品壁の間の滑らかな移行が必要です。これは、リブの厚さの一部の半径を持つフィレット遷移を使用して実現できます。さらに、約 0.5° ~ 1° の脱型傾斜を組み込むことにより、金型からの取り外しが容易になり、損傷を防ぎます。
実際のアプリケーションと例
リブのレイアウトが重要な役割を果たす自動車部品を考えてみましょう。ダッシュボードやバンパーなどの部品では、適切に設計されたリブ レイアウトにより、これらのコンポーネントが変形することなく長期にわたる衝撃や応力に耐えることができます。この原則は、航空宇宙や家電などのさまざまな業界に適用できます。
リブ レイアウトのこれらの側面を理解することで、設計者は現実の要求に耐える、より堅牢で信頼性の高い射出成形製品を作成できます。
リブのレイアウトにより、製品内の応力が均一に分散されます。真実
戦略的なリブの配置により応力が均等に分散され、製品の安定性が向上します。
最良の結果を得るには、リブの間隔は常に壁の厚さと一致する必要があります。間違い
最適なリブ間隔は壁厚と等しくなく、壁厚の 2 ~ 3 倍です。
リブの補強に材料の選択が重要なのはなぜですか?
リブを補強するための適切な材料を選択することは、射出成形製品の耐久性と品質を確保するための鍵となります。
補強リブの材料の選択は、リブの強度、剛性、収縮に影響を与え、製品の品質と機能に影響を与えます。
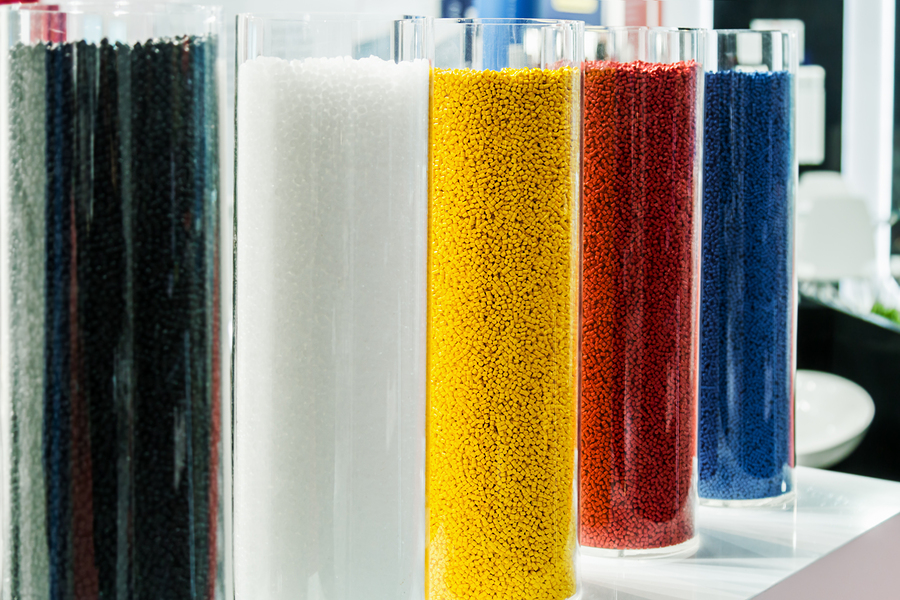
材料特性の重要性
補強リブに適切な材料を選択することは、最終製品の強度3製品の構造的完全性を維持するには、通常、ポリカーボネートやガラス繊維入りナイロンなどの高強度と剛性を備えた材料が好まれます。
-
強度と剛性: これらの特性により、リブは変形することなく外力に耐えることができます。 ABS などの材料は、靭性と剛性のバランスが優れているため、耐衝撃性が必要な部品に最適です。
-
収縮: 低収縮材料は、正確な寸法を維持するために重要な、反りや位置ずれのリスクを最小限に抑えます。これらのリスクを軽減するために、熱膨張係数の低いポリマーが選択されることがよくあります。
製造プロセスとの互換性
また、材料は高温と高圧を必要とする射出成形プロセスにも適合する必要があります。材料の熱安定性によって、劣化せずに成形できるかどうかが決まります。
-
射出圧力と射出速度: 材料は、品質を損なうことなく高い射出圧力に耐える必要があります。たとえば、ポリプロピレンは高速と高圧にうまく対応できるため、サイクルタイムが短縮され、効率が向上します。
-
金型温度: 亀裂や表面欠陥などの問題を防ぐには、さまざまな金型温度に耐えられる材料を選択することが不可欠です。
費用対効果と可用性
パフォーマンスは最優先ですが、費用対効果も無視できません。選択された材料は、コストと望ましい特性の間のバランスを提供する必要があります。
-
コスト: ポリプロピレンなどの一般的な材料は経済的でありながら、適度な強度と柔軟性を備えています。
-
入手可能性: 生産の遅れを避けるために、材料はすぐに入手できる必要があります。現地で入手できるため、配送コストとリードタイムも削減されます。
環境への配慮
選択プロセスにおいて、材料の環境への影響がますます考慮されるようになってきています。
-
リサイクル可能性: リサイクル可能な素材を選択すると、廃棄物が削減され、持続可能性の目標に沿ったものになります。再生 PET (ポリエチレン テレフタレート) などの素材は、品質を損なうことなく環境に優しいオプションを提供します。
-
生分解性: 場合によっては、環境への影響が重大な懸念事項となる用途には生分解性材料が選択されます。
結論として、リブを強化するための材料の選択は、射出成形製品の性能と品質だけでなく、生産効率と環境の持続可能性に影響を与える多面的な決定です。これらの要因を理解することで、メーカーは情報に基づいた選択を行うことができ、優れた製品の成果につながります。
ポリカーボネートはリブの補強に最適です。真実
ポリカーボネートは強度と剛性が高く、リブに適しています。
ABS は射出成形での収縮が大きいです。間違い
ABS は、靭性と低収縮のバランスが優れています。
射出成形パラメータはリブの品質にどのような影響を与えるのでしょうか?
射出成形パラメータは、成形製品のリブの品質を決定する上で極めて重要な役割を果たし、強度と完全性に影響を与えます。
高品質のリブを実現するには、圧力、速度、温度などの射出成形パラメータを最適化することが重要です。これらのパラメータにより、材料の流れが均一になり、反りや収縮などの欠陥が最小限に抑えられるため、リブの構造性能が向上します。
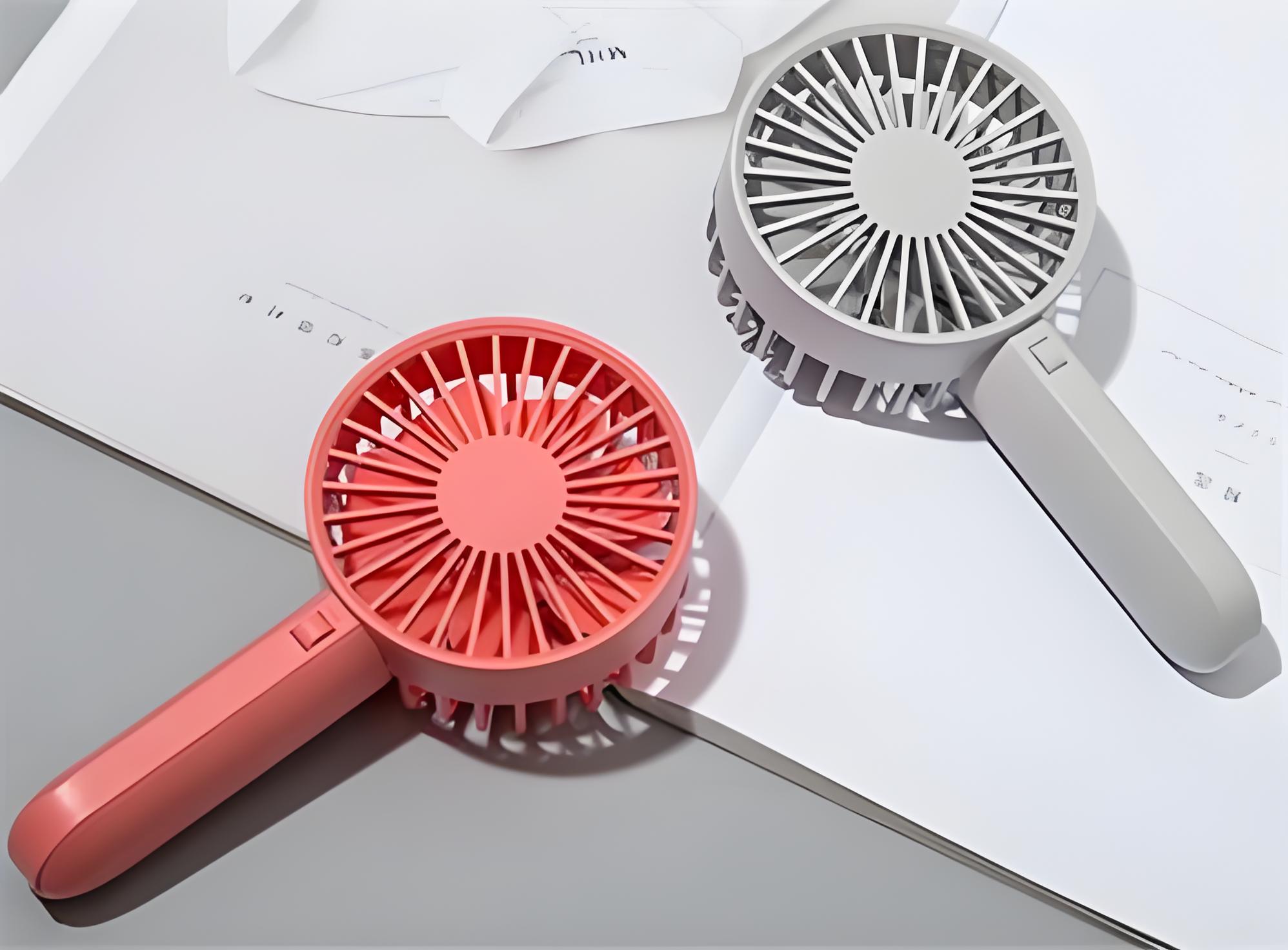
射出圧力と射出速度の役割
射出圧力と射出速度は、リブの最終品質に直接影響を与える重要なパラメータです。高い射出圧力により、溶融材料が複雑なリブ形状を完全に充填し、不完全な充填や空隙のリスクを軽減します。
ただし、過度の圧力はリブ内のバリや応力の増加につながり、反りを引き起こす可能性があります。同様に、射出速度4、材料の流れをより適切に制御できるようになります。これは、複雑なリブ形状の場合に特に重要です。
金型温度に関する考慮事項
金型温度は冷却速度に大きく影響し、その結果リブの寸法安定性に大きく影響します。金型温度を高くすると、より緩やかな冷却プロセスが可能になるため、表面仕上げが向上し、内部応力が軽減されます。
逆に、金型温度が高すぎると、サイクル時間が長くなり、生産コストが増加する可能性があります。したがって、効率を維持しながらリブの品質を最適化するには、金型温度のバランスをとることが不可欠です。
冷却時間の最適化
冷却段階は、リブの形状と寸法を固化させるため、非常に重要です。冷却時間が不十分だと、反りや残留応力などの欠陥が発生する可能性があり、過剰な冷却はサイクルタイムとコストの増加につながる可能性があります。
シミュレーション ツールを利用して最適な冷却時間を決定すると、バッチ全体でリブの完全性と均一性を維持するのに役立ちます。
マテリアルフローとリブデザイン
リブ自体の設計は、射出時の材料の流れに影響を与えます。リブの厚さと間隔が適切であることを確認すると、欠陥のない一貫した充填を達成するのに役立ちます。
たとえば、リブの厚さが製品肉厚の 50% を超えると、収縮マークが発生する可能性があります。対照的に、適切に調整されたリブ設計では、材料の流れがよりスムーズになり、応力集中が軽減され、部品全体の品質が向上します。リブと壁5を組み込むことも、型から外す際に応力をより均一に分散するのに役立ちます。
これらのパラメータとリブ設計との相互作用を理解することで、メーカーは射出成形部品の品質を大幅に向上させることができます。
高い射出圧力によりリブ内のボイドが減少します。真実
高圧により、溶融した材料が複雑なリブ形状に完全に充填されます。
金型温度が高すぎるとサイクルタイムが短くなります。間違い
金型温度が高いとサイクル時間が長くなり、生産コストが増加します。
結論
リブ設計をマスターすることで、射出成形製品が強度があるだけでなく、信頼性と効率性も確保できるようになります。
-
強度を損なうことなくリブを薄くできる材料を見つけてください。: 主な特徴: 高剛性 • 傷に対する耐性 • 良好な強度重量比 • 高い溶接性。用途: ABS は製造現場で広く使用されています… ↩
-
リブのレイアウトが射出成形の効率と製品の品質にどのような影響を与えるかをご覧ください。: リブは、射出成形部品にサポートと剛性を加える薄壁のような構造です。それらは一次壁よりも薄く、これらをサポートするために使用されます。 ↩
-
どの材料が強度と剛性を効果的に強化するかを確認します。: この記事では、重要な機能の 1 つである射出成形リブを設計するためのベスト プラクティスについて説明します。 ↩
-
速度調整によって材料の流れが最適化され、欠陥が低減される仕組みを学びましょう。: 高速射出によって金型キャビティ内の溶融温度の差が最小限に抑えられ、成形サイクルが短縮され、成形品の品質が向上します。 ↩
-
フィレット遷移が応力を均等に分散するのにどのように役立つかをご覧ください。: 美的: フィレットはパーツの外観を向上させることができます。滑らかで丸みを帯びた遷移は、多くの場合視覚的に美しく、触覚的にもより安全な表面を提供します。サイズ … ↩