I.基本的な認知レベル:概念フレームワークの確立
最適化する前に、理解する必要があります。
明確な定義
- 射出成形冷却時間:
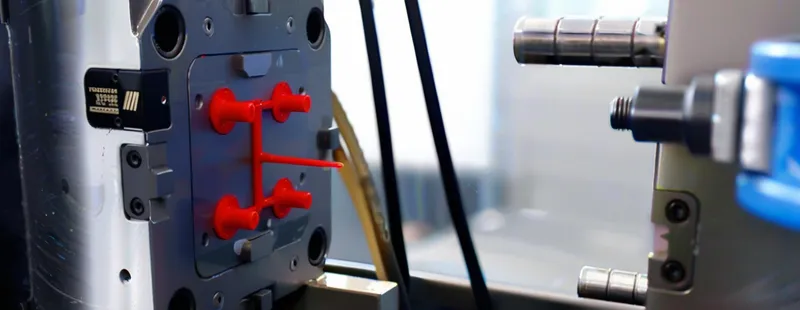
分類(冷却時間に影響する要因)
冷却時間は固定値ではありません。それは、広く分類できる要因の合流の影響を受けています。
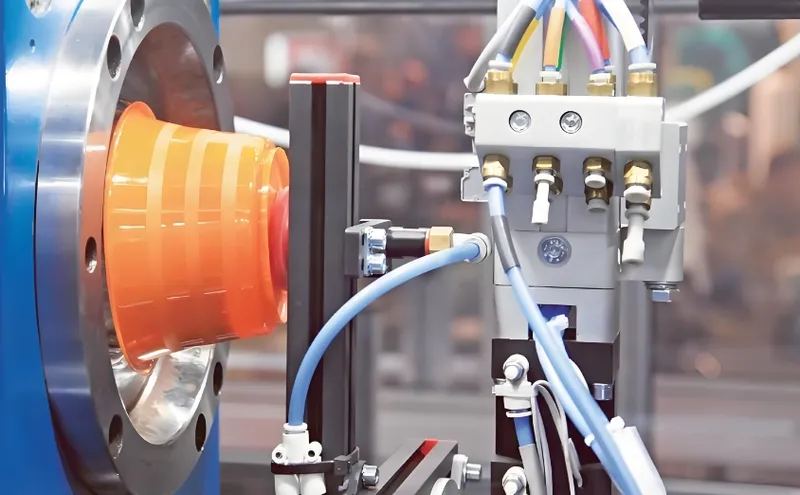
-
物質中心:
-
パーツデザイン中心:
- 壁の厚さ:最も支配的な要因。冷却時間は、最も厚い壁のセクションの正方形にほぼ比例します。
- パーツジオメトリ:複雑な形状、rib骨、ボス、および不均一な壁の厚さは、ホットスポットと差動冷却を作成する可能性があります。
-
カビのデザイン中心:
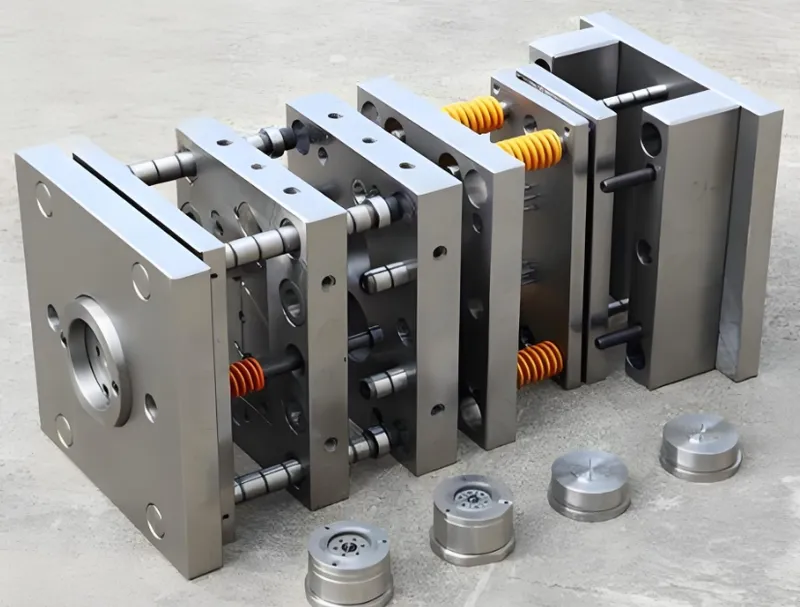
- 冷却チャネル設計5 :レイアウト、直径、キャビティの近接性、およびタイプ(たとえば、従来の掘削ライン、コンフォーマル冷却チャネル)。
- カビ材料:より高い熱伝導率カビ材料(たとえば、ベリリウム銅インサート対P20鋼など)は、冷却時間を短縮できます。
- ベント:適切な通気止めにより、閉じ込められた空気が逃げることができ、冷却が延長される可能性のある断熱効果を防ぎます。
- プロセスパラメーター中心:
ii。アプリケーション分析レベル:ユーザーの意思決定の問題の解決
冷却時間を理解することは、さまざまなアプリケーションに情報に基づいた決定を下すのに役立ちます。
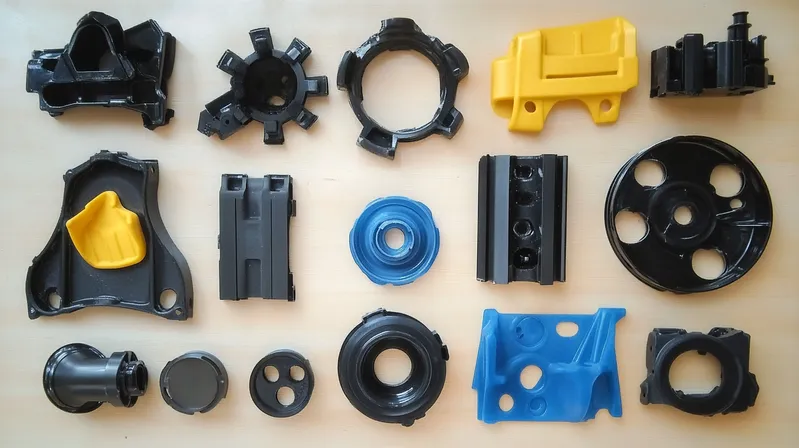
典型的なアプリケーションシナリオ
- 大量の薄壁のパッケージ(例えば、食品容器、キャップ - しばしばpp、pe):
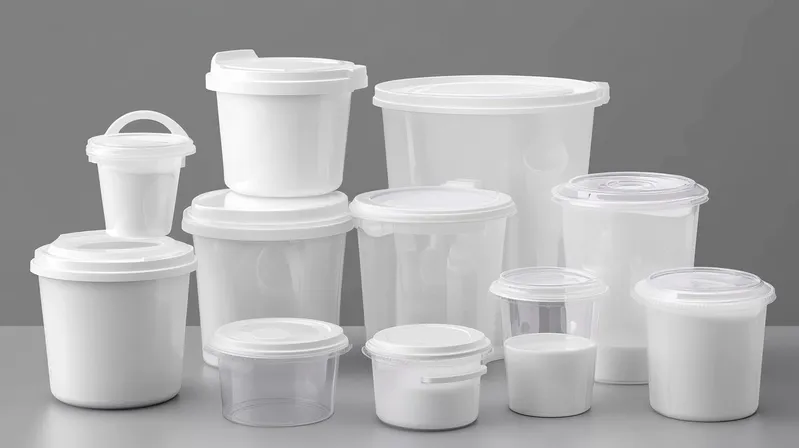
- 提案:サイクル時間の冷却時間が最重要です。高導電性カビ材料、効率的な冷却チャネル設計、および潜在的に低い(しかし制御された)カビの温度を使用した迅速な冷却を最適化します。材料の選択は、高速サイクリンググレードを支持します。
- 医療機器(たとえば、注射器、診断コンポーネント - 多くの場合PC、ピーク、COC):
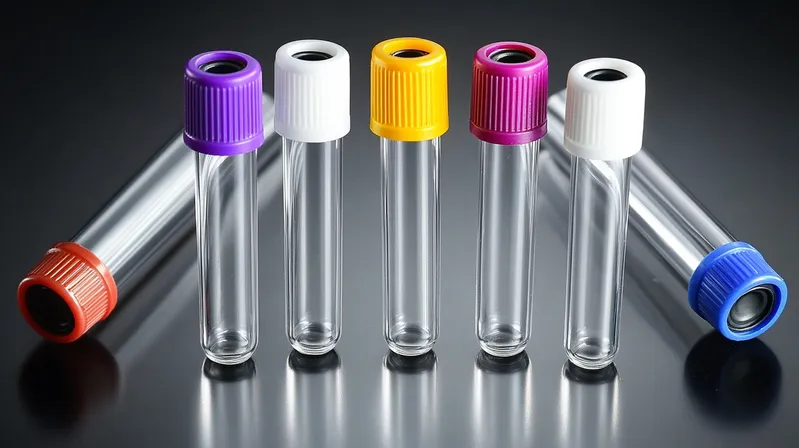
- 提案:精度と材料の完全性が重要です。内部応力を最小限に抑え、次元の精度を確保するために、冷却は均一でなければなりません。より長く、より制御された冷却は、重要な許容範囲を達成するために受け入れられるかもしれません。
- 家電ハウジング(例えば、電話ケース、リモートコントロール - 多くの場合ABS、PC):
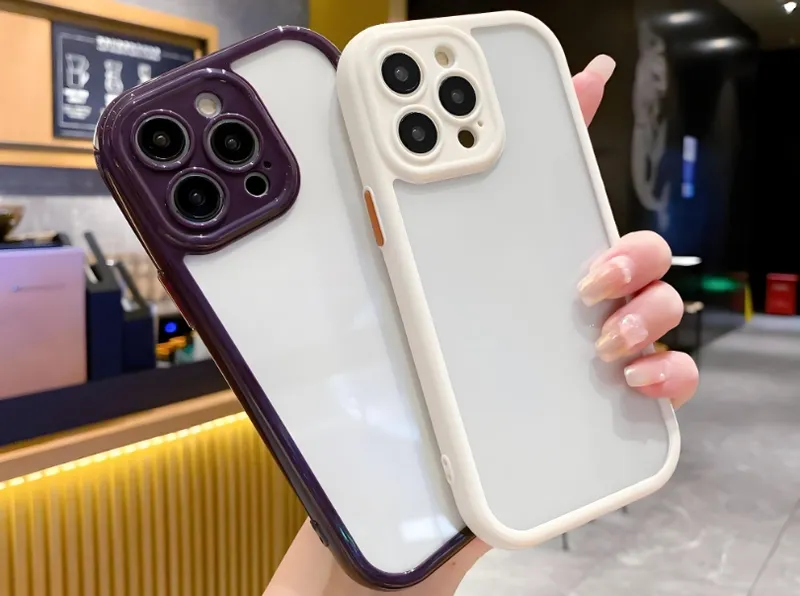
- 提案:美学(表面仕上げ)と構造の完全性が重要です。冷却は、シンクマークを避け、適合と感触を確保するために管理する必要があります。最適化された冷却チャネル設計が重要です。
- シリコンゴム製品(LSR成形):
- 提案: Zetarmoldはシリコンも処理しますが、その「冷却」は実際には熱を介して「硬化」しています。カビは熱く、「冷却」と同等のものは、架橋反応が完了するのにかかる時間です。熱伝達と均一性の原理は依然として適用されますが、目的は固化のために除去するのではなく、硬化の熱を維持することです。
長所と短所の比較(冷却時間の影響)
特徴 | より短い冷却時間 | より長い冷却時間 |
---|---|---|
長所 | - サイクル時間の短縮 | - より良い寸法安定性 |
- 生産性の向上 | - 部品品質の改善(シンクマークの少なく、歪みが少ない) | |
- パートあたりのコストが低い | - 内部応力の減少 | |
短所 | - 欠陥のリスク(反り、シンクマーク、ショートショット) | - サイクル時間の増加 |
- 排出に固執または変形する部品の可能性 | - 生産性の低下 | |
- 急速に/不均一に冷却された場合、より高い内部応力 | - パートあたりのコストが高くなります | |
- より堅牢な排出システムが必要になる場合があります | - 圧力を保持している場合の可能性のあるオーバーパッキングの問題は、冷却に長すぎると維持されています |
iii。技術的なディープレベル:プロの読者のニーズに応える
ニッティグリッティに入りましょう。
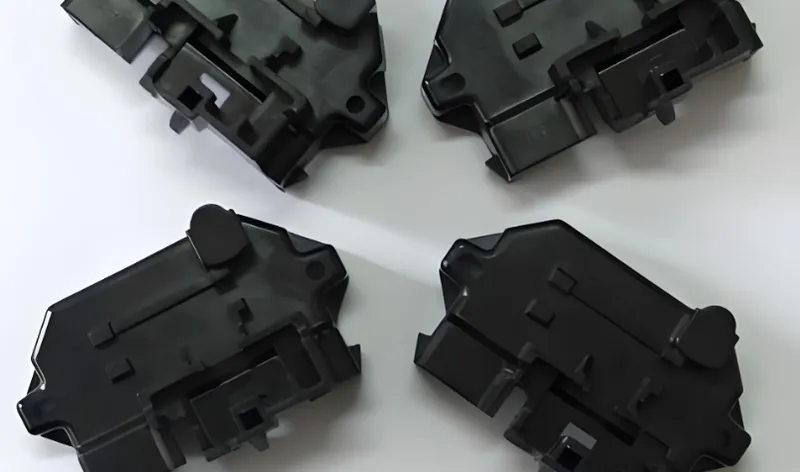
完全なワークフローの内訳を処理する(冷却に焦点を合わせます)
-
カビの閉鎖とクランプ:金型の2つの半分は、しっかりと閉じられてクランプされています。
-
注入:溶融プラスチックが高圧下でカビの空洞に注入されます。
-
梱包/保持:キャビティがほとんど満たされた後、材料がカビの壁の近くで冷却して固化し始めると、収縮を補うために追加の材料が圧力を受けて詰められます。
- キーパラメーター:梱包圧力、梱包時間。
-
冷却段階:
-
金型の開口部:セット冷却時間が経過し、部品が十分に剛性になると、クランプが金型を開きます。
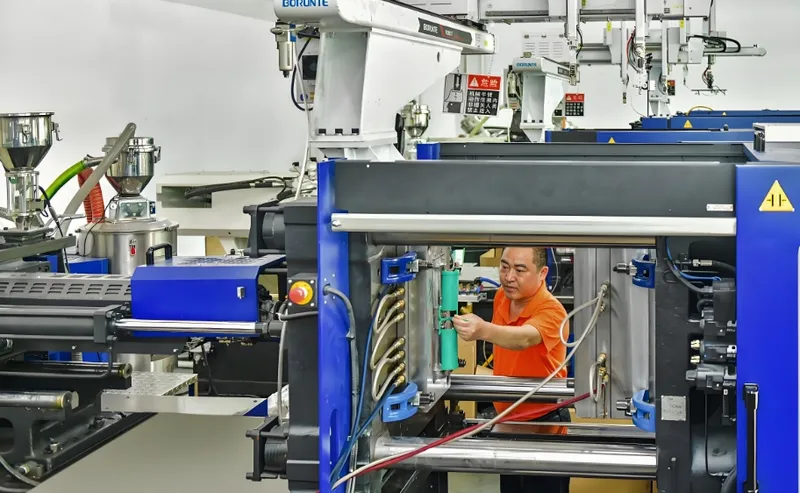
- 排出:固化した部分は、イジェクターシステム(ピン、袖、プレート)によってカビの空洞から押し出されます。
監視および制御するための主要な冷却パラメーター:
-
クーラント入口/出口温度差(Delta T):除去される熱の量を示します。非常に小さなデルタTは、不十分な流れや熱接触が不十分であることを示唆するかもしれません。
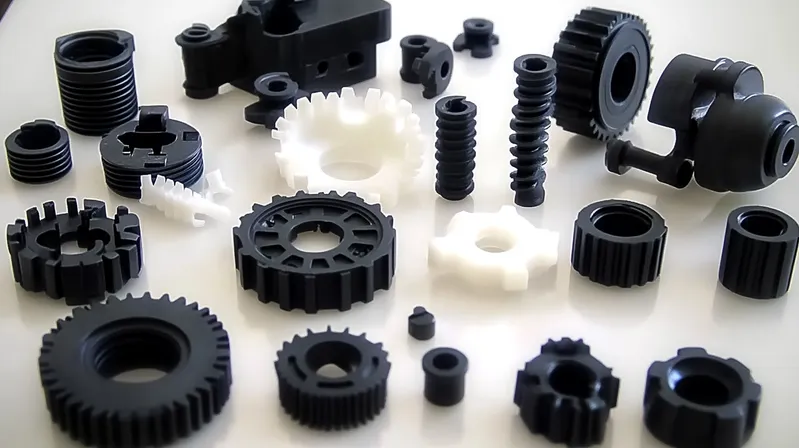
材料互換性の説明
プラスチック材料の熱特性は、その冷却挙動の基本です。
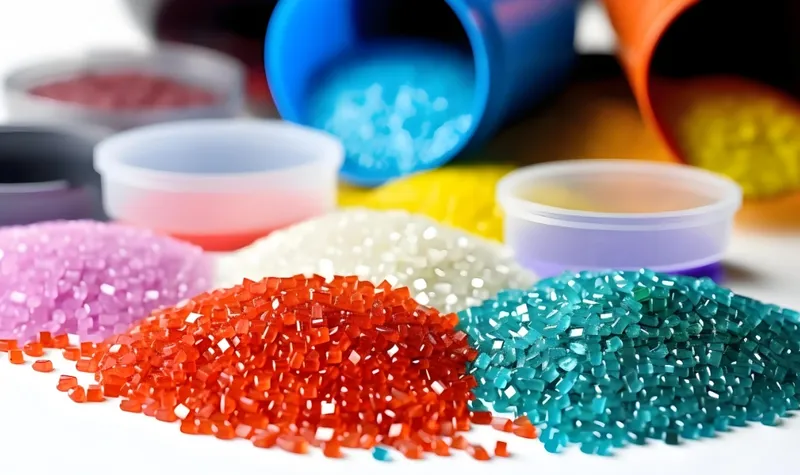
-
アモルファスポリマー(例、ポリスチレン(PS)、ポリカーボネート(PC)、ABS):
- シャープな融点はありません。温度範囲で柔らかくなります。
- 一般に、半結晶よりも低い収縮。
- 冷却とは、剛性を達成するために、材料をガラス遷移温度(TG)の下に置くことです。
- 迅速に冷却されている場合、内部応力を抑える傾向があります。
-
半結晶ポリマー(例、ポリプロピレン(PP)、ポリエチレン(PE)、ナイロン(PA)、PET、PBT):
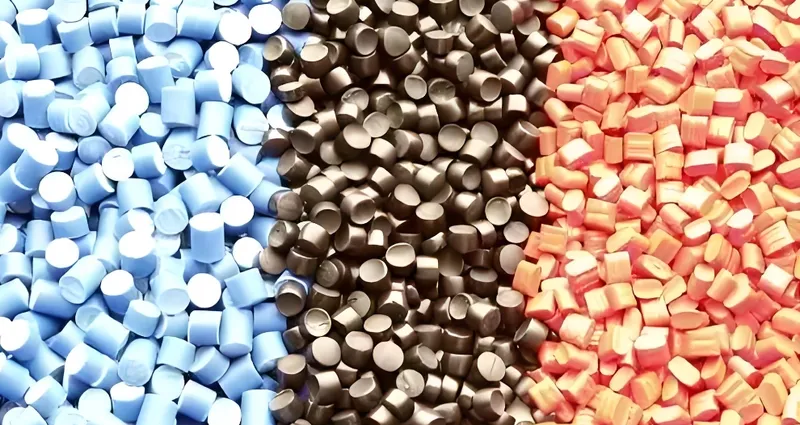
- シャープ融点(TM)。
- 秩序化された結晶構造の形成により、より高い収縮。このプロセスは、融合の潜在熱も放出し、除去する必要があります。
- 冷却速度は結晶化度に影響を与え、機械的特性に影響を与えます。迅速な冷却は、より小さな球体につながり、時には靭性が改善されますが、潜在的にはより多くのwarpageにつながる可能性があります。
- 反りと寸法の安定性を管理するために、慎重な冷却制御が必要です。
- 液体シリコンゴム(LSR - 比較のため):
- サーモセット材料。カビは加熱されます(通常は170〜210°C)。
- 「冷却時間」は、実際には材料が架橋する「硬化時間」です。部品は熱く排出されます。熱伝達は依然として重要ですが、硬化温度を均一に維持するためです。
IV。実用的なツールレベル:コンテンツの操作性の向上
あなたのプロジェクトのための実用的な洞察。
デザインチェックリスト(冷却のためのプロセス制限のリマインダー)
射出成形用の部品を設計するときは、冷却を最適化するためにこれらを検討してください。
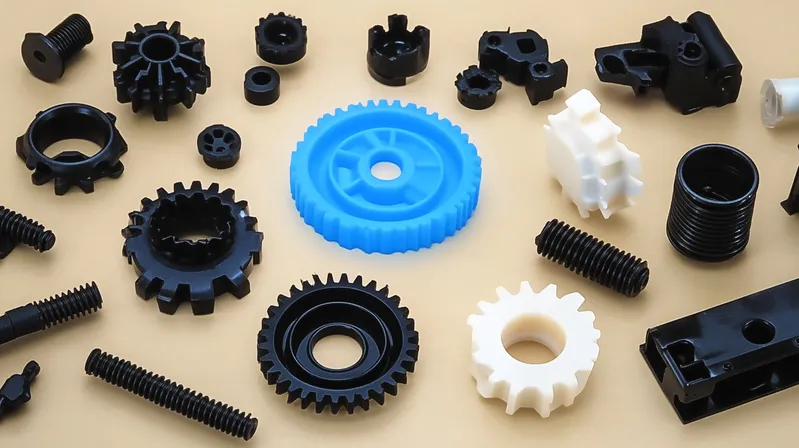
-
均一な壁の厚さ:部品全体の一貫した壁の厚さを目指します。これは、管理可能な冷却の第1位のルールです。
-
厚いセクションを避けてください:避けられない場合は、それらをコアアウトするか、ガスアシストなどの機能を使用してください。
-
寛大な半径:鋭利な縁の代わりに角の内側と外側に半径を使用して、ストレス集中を防ぎ、流れ/冷却を改善します。
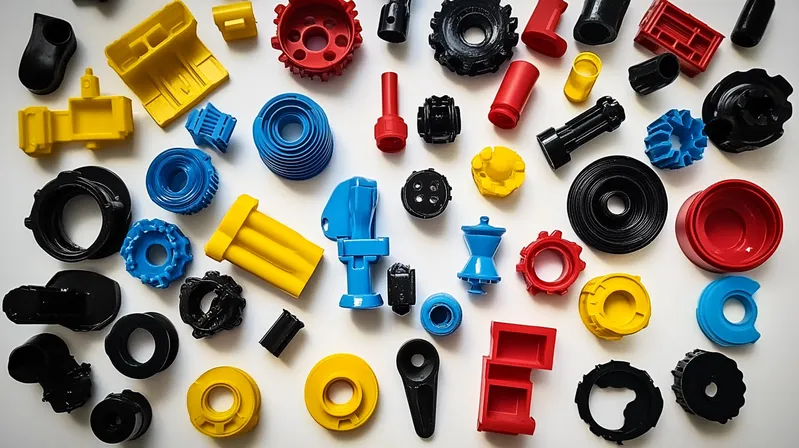
-
段階的な遷移:厚さの変化が必要な場合は、それらを段階的にします。
-
リブ/ボスの設計:リブの厚さは、シンクマークを防ぐために公称壁の約50〜70%でなければなりません。ボスをコアする必要があります。
-
材料の選択:サイクル時間が重要な場合は、熱伝導率または低い処理温度の材料を検討してください。
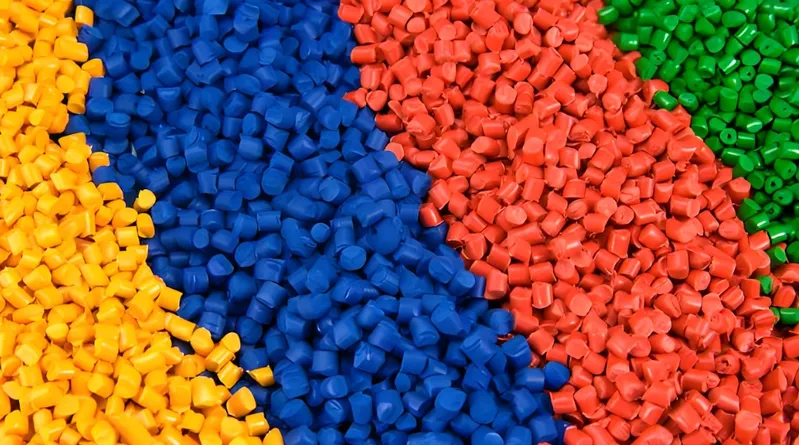
-
ゲートの場所:最初に厚いセクションを埋めるためにゲートを配置するか、温度の変動を最小限に抑えます。
-
カビの冷却の実現可能性を考慮してください:効果的な冷却チャネルを従来に実装することは不可能であるため、部品設計は非常に複雑ですか? (これはコンフォーマル冷却に向かってプッシュするかもしれません)。
プロセス選択意思決定(冷却時間の最適化)
これは、冷却時間を最適化するための基本的な思考プロセスです。
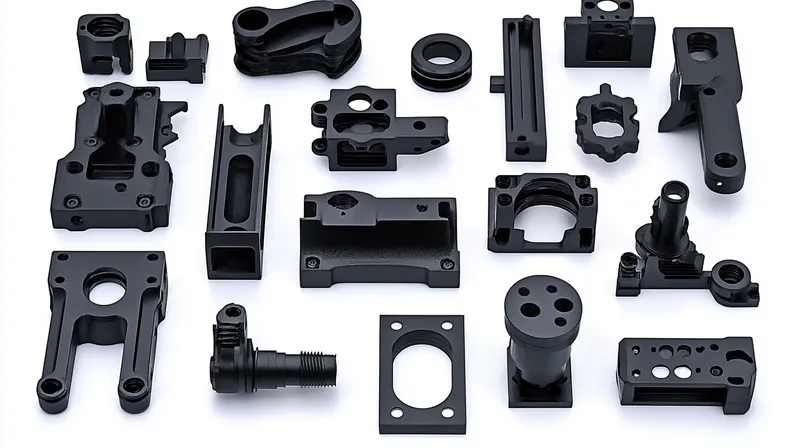
-
現在の冷却時間は過剰で、高コストまたは低出力につながりますか?
- はい:分析に進みます。
- いいえ: 部品品質(縦糸、シンク、寸法)は問題ですか?
- はい:冷却が短すぎるか不均一になる可能性があります。分析に進みます。
- いいえ:現在の冷却が適切である可能性があります。定期的に監視します。
-
部品設計を分析します:
- 壁の厚さは不均一ですか?アクション:均一な壁については、DFMでお客様にアドバイスします。
- 回避可能な厚いセクションはありますか?アクション:コアリングをアドバイスします。
-
材料の分析:
- サイクルタイムターゲットに適切ですか?アクション:実現可能な場合は、代替グレードまたは材料を探索します。
- 材料の推奨排出温度と熱特性に注意してください。
-
カビの設計と状態を分析します:
- 冷却チャネルは適切です(サイズ、数、配置)?アクション:金型フローシミュレーションを使用します。複雑な部品または重要なアプリケーションのコンフォーマル冷却を検討してください。
- チャンネルは明確で、規模がありませんか?アクション:定期的な金型メンテナンスを実装します。
- 金型材料は、熱伝達のニーズに適していますか?アクション:ホットスポットエリアのより高い導電率材料の挿入を検討してください。
-
プロセスパラメーターを分析します:
- 溶融温度は必要以上に高くなっていますか?アクション:充填を監視し、徐々に減らします。
- カビの温度は最適ですか? (低すぎると他の問題を引き起こす可能性があります)。アクション:材料サプライヤーの推奨範囲内で実験します。
- クーラントの流量と温度は最適化されていますか?アクション:乱流を確保します。適切かつ費用対効果が高い場合は、冷水を使用してください。
決定ツリースニペット:
-
部品に厚いセクションがあり、冷却が長い場合は、コアアウトまたはガスアシストの使用を検討してください。
-
部品が反りと冷却が短いことを示している場合、冷却時間を増やすか、冷却の均一性を改善します(たとえば、コンフォーマル冷却)。
-
サイクル時間が重要で、部分品質が可能な場合は、オプションを探索して、冷却(最適化された金型、パラメーター)を慎重に減らします。
V.拡張レベル:知識ネットワークの構築
冷却時間は真空に存在しません。
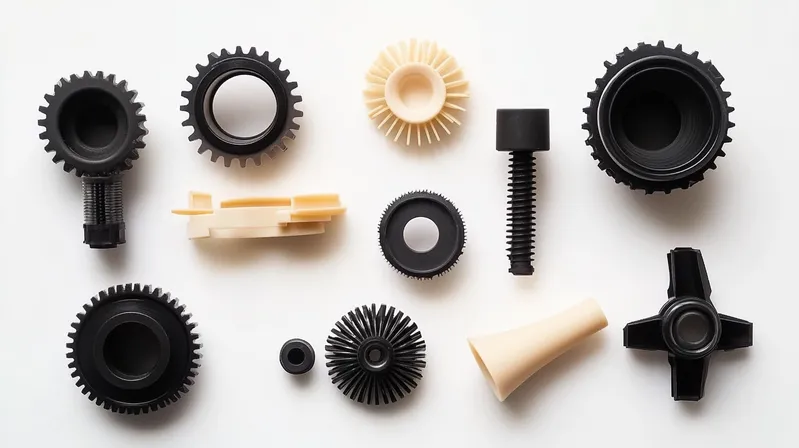
関連技術ナビゲーション
- 上流のテクノロジー:
- 部品設計(DFM - 製造可能性のための設計):ここで行われた決定は、冷却に大きく影響します。
- 材料の選択:熱特性は、冷却計算に固有のものです。
- 金型フロー分析(シミュレーション): Moldflow、Solidworksプラスチックなどのソフトウェアは、冷却時間を予測し、ホットスポットを特定し、鋼が切断される前にこれは非常に貴重です。
- 金型設計:適切な金型材料を使用して、効率的な冷却チャネルレイアウトを組み込みます。
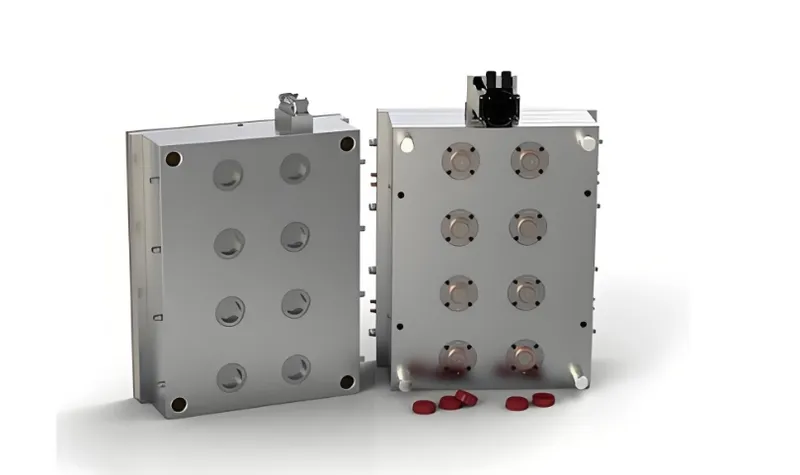
-
ダウンストリームテクノロジー/考慮事項:
- 移動後の操作:高い内部ストレスのある部品にはアニーリングが必要になる場合があり、時には急速または不均一な冷却によって悪化することがあります。
- 品質制御(QC):寸法チェック、反り分析、およびストレステストは、冷却プロセスの影響を受けます。
-
並列/拡張技術:
- コンフォーマル冷却:カビの輪郭に続く冷却チャネルは、はるかに均一で効率的な冷却を提供します。多くの場合、添加剤の製造(金属の3D印刷)を使用して構築されています。
- パルス冷却/バリオサム(熱&クールモールディング):噴射中にカビの表面を急速に加熱して、表面仕上げと流れを改善し、急速に冷却します。複雑ですが、特定の問題を解決できます。
- ホットランナーシステム:直接冷却されていませんが、ランナーを溶け続け、ランナーの冷却時間と材料廃棄物を排除し、全体的な効率に影響を与えます。
- カビの温度コントローラー(TCU):正確なクーラント温度と流れを維持するために不可欠です。
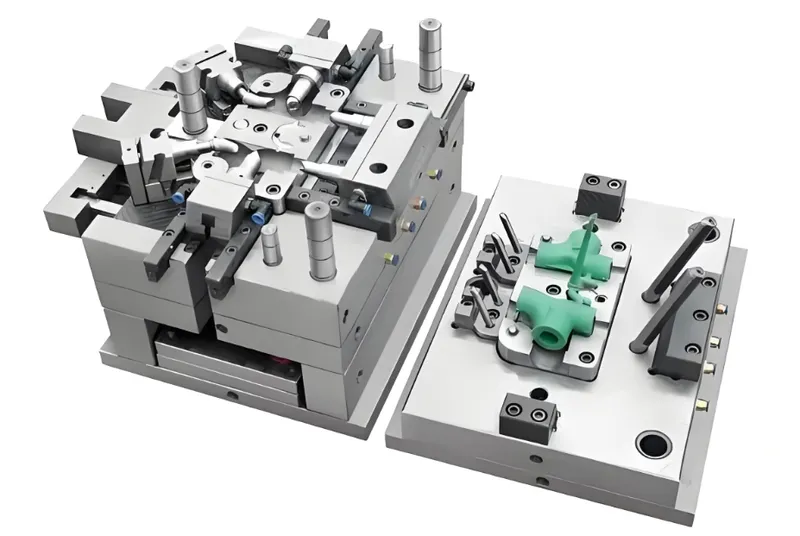
結論:Zetarmoldでの冷却時間の習得
Zetarmoldでは、射出成形冷却時間の習得は科学、経験、最先端の技術の融合であることを認識しています。これは、私たちが国際的なクライアントに高品質で費用対効果の高い射出成形とシリコンのゴム製品を細心の注意を払って届けることが重要な要素です。
基礎を理解し、アプリケーションを分析し、技術的な詳細に飛び込み、実用的なツールを利用することで、優れた結果の冷却プロセスをまとめて最適化できます。
-
射出成形プロセスを最適化し、製品の品質を向上させるには、冷却時間を理解することが重要です。 ↩
-
凝固時間について学ぶことは、成形プロセスをよりよく制御し、高品質の製品を確保することにつながる可能性があります。 ↩
-
射出成形サイクルの調査は、製造プロセス全体を把握し、効率と出力を向上させるのに役立ちます。 ↩
-
製造プロセスの冷却時間を最適化するには、ポリマーの種類を理解することが重要です。詳細な洞察については、このリンクを調べてください。 ↩
-
冷却チャネルの設計は、冷却効率に大きな影響を与えます。この分野でベストプラクティスと革新を発見してください。 ↩
-
溶融温度は、冷却効率に重要な役割を果たします。生産プロセスへの影響について詳しく知ります。 ↩
-
収縮補償について学ぶことは、成形部品の寸法の精度と品質を確保し、冷却中の欠陥を防ぐために不可欠です。 ↩
-
カビの表面温度を理解することは、熱抽出を最適化し、成形部品で高品質の表面仕上げを達成するために重要です。 ↩
-
クーラント流量の影響を調査することで、射出成形プロセスの熱伝達効率と全体的な生産品質を改善するのに役立ちます。 ↩