射出成形は、小さな消費財から大規模な産業部品まで、正確なプラスチック部品を生産するために広く使用されている製造プロセスです。これらの部品を設計する上で重要な要素は、壁の厚さ1、これは部品の強度、機能、および成形プロセス自体の効率に影響を与えます。壁の厚さは、サイクル時間、材料コスト、およびシンクマークやワーピングなどの欠陥のリスクに影響します。射出成形3に許可された最大壁の厚さ2は何ですか?答えは固定されていません。材料、設計、用途によって異なり、通常は3 mmから25 mmの範囲で、問題を最小限に抑えるために約5 mmの一般的なガイドラインがあります。
射出成形の最大壁の厚さは、通常3 mmから25 mmの範囲の材料特性とパーツ設計に依存しますが、ほとんどのガイドラインは、欠陥を避けるために5 mm未満にとどまることを推奨しています。
この記事では、これらの制限、材料固有の推奨事項、および厚壁の部分に関する実用的な考慮事項について説明します。
射出成形の最大壁の厚さは常に5 mmです。間違い
5 mmは一般的なガイドラインですが、ポリカーボネートのような材料は最大9.35 mmを処理でき、長繊維強化プラスチックは25.4 mmに達する可能性があります。
厚壁の部分は、欠陥なしで成形することは不可能です。間違い
適切な設計とプロセス制御により、厚い壁の部品は正常に成形できますが、注意が必要です。
射出成形で壁の厚さが重要なのはなぜですか?
壁の厚さは、いくつかの理由で射出成形設計の基礎です。
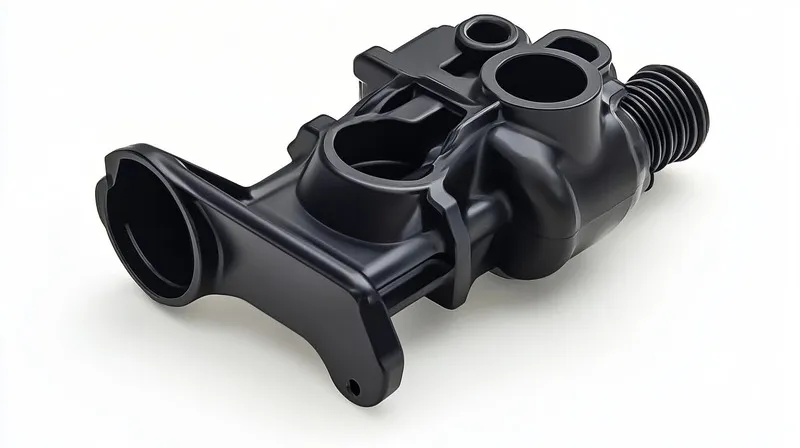
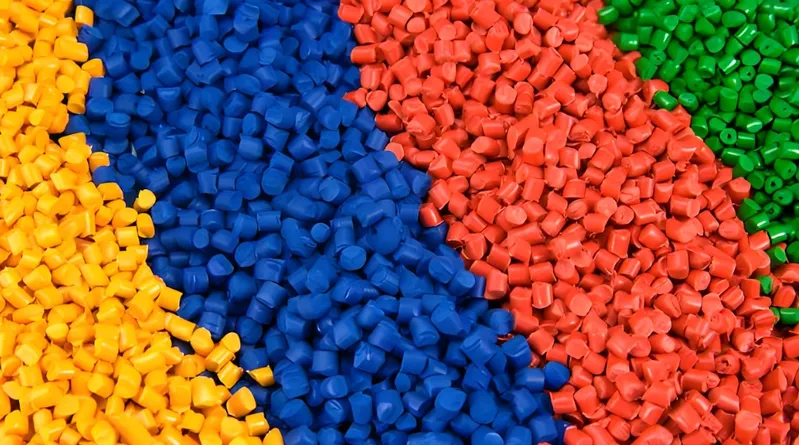
設計者は通常、機能的なニーズを満たす最も薄い壁を目指していますが、一部のアプリケーション(構造的または断熱された部品など)が厚い壁を要求し、射出成形が達成できるものの限界を押し上げます。
壁の厚さの最大の一般的なガイドラインは何ですか?
射出成形には普遍的な最大壁の厚さはありません。材料、部分ジオメトリ、成形条件に基づいて変化します。ただし、業界標準は出発点を提供します。

-
典型的な範囲:ほとんどの熱可塑性プラスチック7、効率的な成形と欠陥のない部品を確保します。
-
上限:長繊維強化プラスチックなどの特殊な材料の場合は最大25.4 mmですが、これには高度な技術が必要です。
5 mm未満に保ち、ワーピングや長期のサイクル時間などの一般的な落とし穴を避けることです。 6 mmを超えると、慎重なプロセスの最適化が必要な課題が生じることがよくあります。
材料の選択は最大壁の厚さにどのように影響しますか?
選択した材料は、壁の厚さに大きく影響します。その理由は次のとおりです。

-
収縮:低微量の材料は、厚いセクションの欠陥のリスクを軽減します。
一般的なガイドラインに基づいて、一般的な射出成形材料の最大壁の厚さの表を次に示します。
材料名 | 最大壁の厚さ(mm) |
---|---|
ABS | 3.18 – 3.56 |
ポリプロピレン(PP) | 4.53 |
ポリカーボネート(PC) | 3.81 – 9.35 |
ナイロン(PA) | 3.18 |
ポリスチレン(PS) | 6.35 |
ポリエチレン(HDPE/LDPE) | 5.08 – 6.35 |
長繊維強化プラスチック10 | 25.4 |
注:これらはおおよその範囲です。特定の設計またはプロセスの調整は、これらの制限を高くまたは低くすることができます。
たとえば、ポリカーボネートは、その強度と流れの特性のおかげで最大9.35 mmを処理できますが、安定性が向上したため、長繊維強化プラスチックは
すべての材料は、壁の厚さと同じです。間違い
収縮や流動性などの材料特性により、最大壁の厚さがプラスチック全体で大きく異なります。
太い壁の部品を成形することでどのような課題がありますか?
厚い壁は、射出成形にユニークな課題をもたらします:
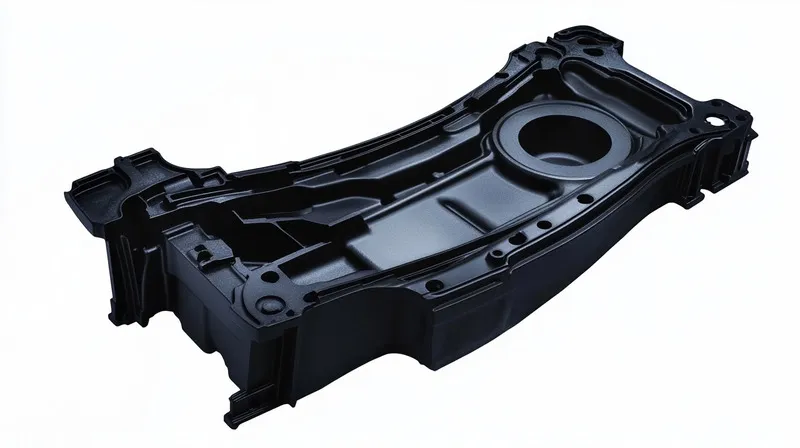
-
より高いコスト:より多くの材料とより長いサイクルが費用を増加させます。
-
充填問題:厚いセクションは、圧力や材料を調整せずに完全に埋めることはできません。
これらのハードルにもかかわらず、解決策は存在します:
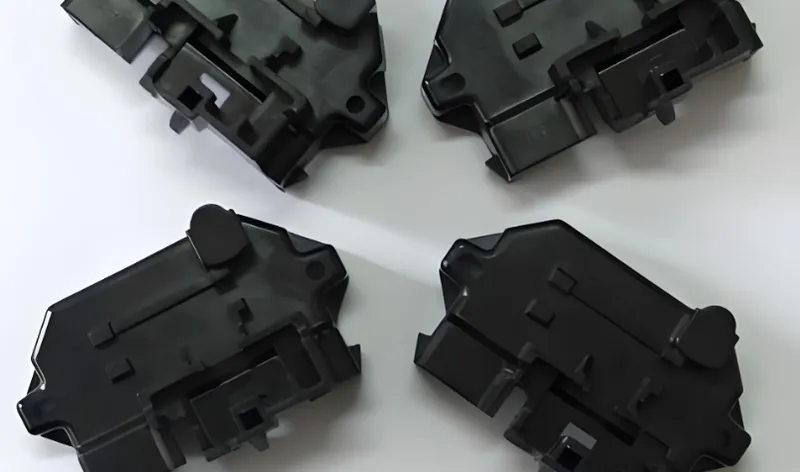
厚壁の部品は常に生産コストを増加させます。真実
より多くの材料とより長い冷却時間は必然的にコストを引き上げますが、スマートデザインはこれを軽減できます。
太い壁の部品はいつ必要ですか?
厚い壁は、特定のシナリオで正当化されます。
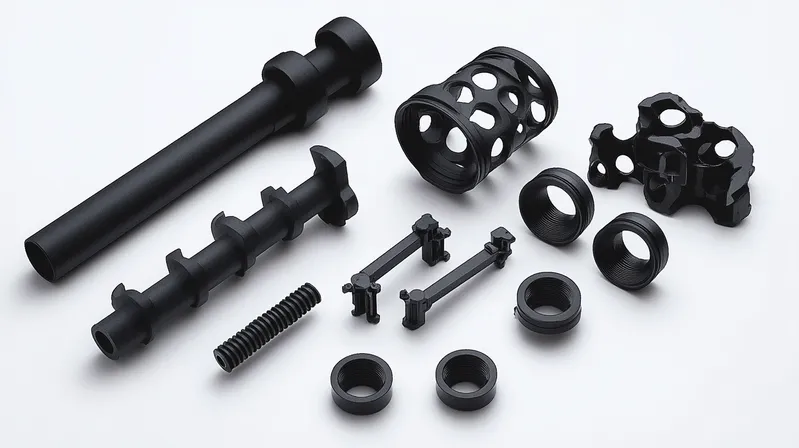
-
構造強度:ダッシュボードやドアパネルなどの自動車部品には剛性が必要です。
-
断熱:厚い壁は、建設成分のように、熱または音響断熱を強化します。
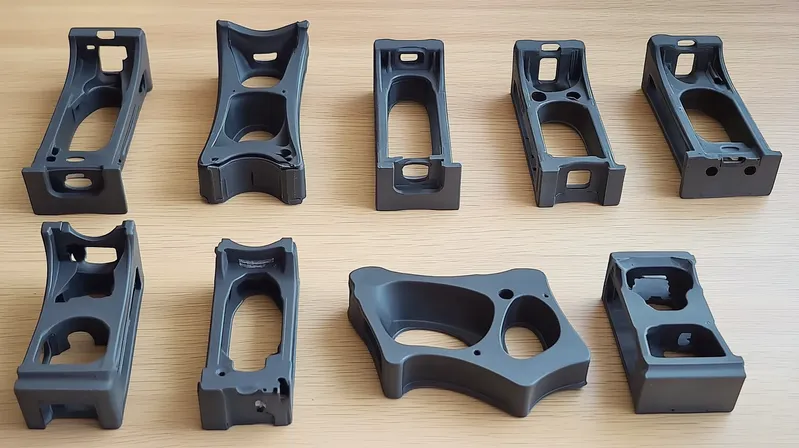
- 耐久性:保護ケーシングまたは頑丈な部品は、厚さを追加することから利益を得ます。
たとえば、自動車産業では、厚壁の部品が金属成分を置き換え、強度を維持しながら重量を削減します。構造では、防音や断熱に使用されます。
太い壁の射出成形部品を設計する方法は?
厚い壁が必要な場合は、次のヒントに従ってください。
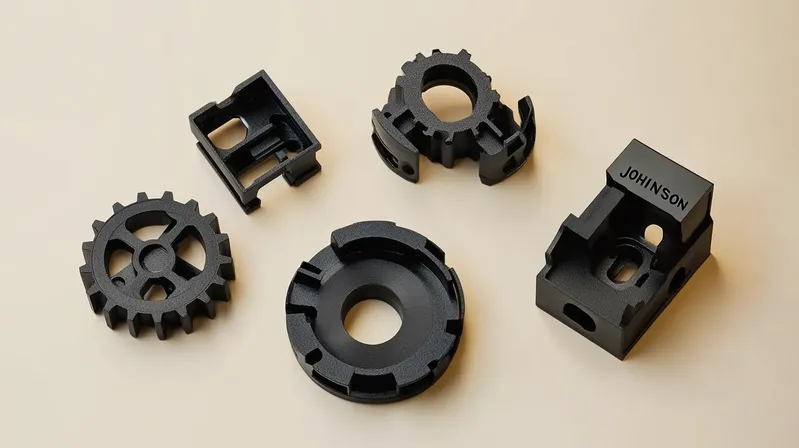
-
賢明な選択:ポリカーボネートや、厚いセクションに適した強化されたプラスチックなどの材料を選択してください。
-
スムーズな遷移:ストレスや冷却の問題を防ぐために、急激な厚さの変化を避けてください。
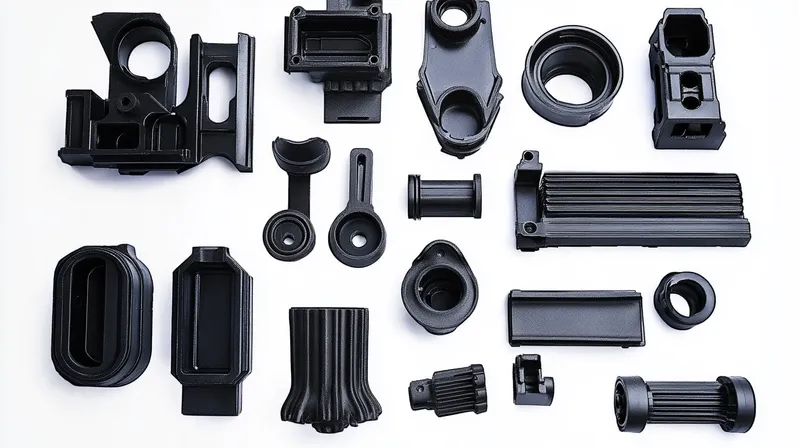
-
金型の強化:効率的な冷却チャネルまたはコンフォーマル冷却を使用して、熱散逸さえします。
-
最初にシミュレートする:金型フロー分析は、生産前に問題を発見する可能性があります。
-
コラボレーション:経験豊富なモルダーと連携して、パラメーターを微調整します。
厚壁の部品は、特別な設計上の考慮事項を必要としません。間違い
彼らは、成功するために特定の材料の選択、カビの設計、およびプロセス調整を要求します。
太い壁の射出成形に代わるものはありますか?
時々、他のプロセスは厚い部分に適しています:
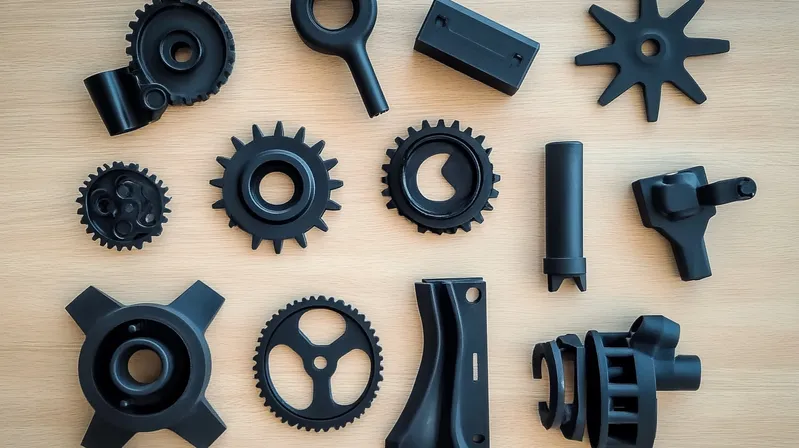
-
回転モールディング:タンクのような大きな中空の厚壁のアイテムに最適です。
-
圧縮モールディング:厚いセクションの熱硬化性に適しています。
-
鋳造:厚い壁に柔軟性を提供しますが、射出成形の精度がありません。
それでも、射出成形は、その速度と汎用性のおかげで、壁が厚い壁であっても、大量の複雑な部品に優れています。
結論
射出成形の最大壁の厚さは単一の数ではなく、材料と設計に応じて3 mmから25 mmの範囲です。 5 mmはほとんどのアプリケーションの実用的なガイドラインですが、高度な材料と技術はこの制限を高くすることができます。設計者は、欠陥やコストなどの課題に対して、より厚い壁(強度や断熱材など)の利点を比較検討する必要があります。適切な素材を選択し、デザインを最適化し、熟練した成形器と提携することにより、厚壁の部品を効果的に生成できます。
-
壁の厚さを理解することは、射出成形プロセスを最適化し、製品の品質を確保するために重要です。詳細な洞察については、このリンクを調べてください。 ↩
-
設計と製造プロセスを強化するために、射出成形の最大壁の厚さに影響を与える要因を発見してください。 ↩
-
効率と製品の品質を改善するための射出成形の重要な要因について学びます。このリソースは貴重な情報を提供します。 ↩
-
冷却効率を理解することは、生産速度を最適化し、射出成形プロセスのコストを削減するために重要です。 ↩
-
欠陥のリスクを最小限に抑える方法を探ると、製造業の高品質の製品が低下し、廃棄物が減少する可能性があります。 ↩
-
部品のパフォーマンスに影響を与える要因について学ぶことは、より強力でより効率的な成形部品の設計に役立ちます。 ↩
-
熱プラスチックについて学ぶことは、材料の選択に関する洞察を提供し、製品の品質を向上させることができます。 ↩
-
熱特性を理解することは、射出成形の壁の厚さを最適化し、パフォーマンスと効率を向上させるために重要です。 ↩
-
流動性を探ることで、材料の行動が成形品質と壁の厚さにどのように影響し、優れたデザインに影響するかを把握するのに役立ちます。 ↩
-
長繊維強化プラスチックの利点、特に堅牢な用途のために厚い壁をサポートする能力を発見してください。 ↩
-
延長された冷却時間を理解することは、生産効率を最適化し、射出成形プロセスのコストを削減するのに役立ちます。 ↩
-
欠陥のリスクを調査することで、製品の品質の向上と製造業の廃棄物の削減に関する洞察を提供できます。 ↩
-
高度な冷却技術について学ぶことで、効率的な射出成形慣行に関する知識を高め、サイクル時間を短縮できます。 ↩