製造上の選択肢の迷路を進むことは、成功への完璧なレシピを見つけるようなものです。
射出成形とダイカストは、どちらも溶かした材料を金型に注入しますが、材質、適合性、コストが異なります。これらの違いを理解することは、生産効率と製品品質を最適化するために非常に重要です。
初めて射出成形かダイカストのどちらかを選択しなければならなかったときのことを覚えています。それは、同じくらい美味しい 2 つのデザートのどちらかを決めるようなものでした。それぞれの方法には独自の魅力と独特の課題がありました。射出成形は、私がよく取り組んでいた洗練されたスマートフォン ケースの作成のように、精度と細部が譲れないプラスチックに最適であるように思えました。一方、ダイカストは、最も重要な部分に強度を提供する、堅牢な金属コンポーネントの頼りになる選択肢であると感じられました。
これらのプロセスをさらに深く掘り下げていくと、特にプラスチックと金属が融合したハイブリッド デザインにおいて、これらのプロセスがどのように相互に補完し合うことができるかがわかりました。設計目標を達成しながらコストと品質のバランスをとるには、多くの場合、最良の結果を得るためにブレンド技術が必要です。これらの方法がプロジェクトにどのような独自のメリットをもたらすかを見てみましょう。
射出成形は金属部品に最適です。間違い
射出成形は主に金属ではなくプラスチックに使用されます。
ダイカストでは、高圧を使用して金属を成形します。真実
ダイカストでは、溶融金属を高圧で金型に注入します。

射出成形とダイカストではどのような材料が使用されますか?
射出成形とダイカストがなぜ大きく異なるのか疑問に思ったことはありますか?これらの製造の驚異を特徴づけるユニークな素材を探ってみましょう。
射出成形では柔軟性を高めるためにポリプロピレンなどの熱可塑性プラスチックが使用され、ダイカストでは強度のためにアルミニウムなどの金属が使用されます。材料の選択は、コストや耐久性などのプロジェクトのニーズによって異なります。
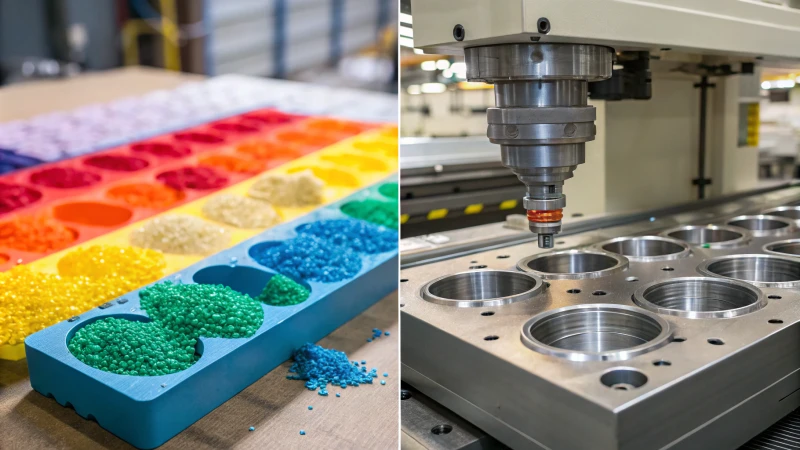
射出成形材料
初めて設計を始めたとき、射出成形がいかに多用途であるかに驚きました。製造業界のカメレオンによく似ており、何度でも溶かして形を変えることができます。
一般的な熱可塑性プラスチック
- ポリプロピレン (PP):折れることなく少し曲げる必要があるものにはこれが最適です。プラスチックのヨガインストラクターのようなものだと考えてください。
- ポリエチレン (PE):衝撃音を聞いたことがある人なら、ポリエチレンの耐衝撃性を理解するでしょう。
- アクリロニトリル ブタジエン スチレン (ABS):ハードシェルのスーツケースを覚えていますか?そう、ABS がその頑丈な外観を実現しているのです。
これらの熱可塑性プラスチックには独自の魅力があり、正確で滑らかな仕上がりの複雑なデザインを作成するのに最適です。これらは家電製品や自動車部品などの定番品です。
材料 | 主要なプロパティ |
---|---|
ポリプロピレン | 柔軟性があり、疲労に強い |
ポリエチレン | 耐衝撃性 |
ABS | 強くて硬い |
ダイカスト材料
反対に、ダイカストは製造業の強力なチャンピオンのようなものです。高圧で金型に押し込むことにより、湿気が最初に加わっても錆びない非鉄金属を使用します。
一般的な金属
- アルミニウム:羽のように軽く、濡れても大丈夫。軽くて丈夫なものが必要な場合に最適です。
- 亜鉛:亜鉛は、いつも時間通りに現れる信頼できる友達だと考えてください。寸法安定性に優れています。
- マグネシウム:驚異的な強度重量比を誇る金属のアスリート。
これらの金属は強度と熱伝導性に優れており、自動車部品や電子機器の筐体に最適です。
材料 | 主要なプロパティ |
---|---|
アルミニウム | 軽量、耐腐食性 |
亜鉛 | 寸法安定性 |
マグネシウム | 高い強度重量比 |
材料特性の比較
では、これら 2 つの中からどのように選択すればよいでしょうか?ここが興味深いところです。
- 耐久性:一生使えるものが必要な場合は、ダイキャストメタルが最適かもしれません。
- 重量: 1 グラム単位が重要なプロジェクトでは、熱可塑性プラスチックが主役になる可能性があります。
- コスト:大規模な生産を計画していますか?熱可塑性プラスチックはコスト競争に勝つことがよくあります。
最終的に、これらのプロパティをプロジェクトの目標2および制約と一致させると、最終製品のパフォーマンスとコスト効率に大きな影響を与える可能性があります。必要なことと実用的なことの間のスイートスポットを見つけることがすべてです。材料の選択3についてさらにカスタマイズされた洞察を得るには、業界固有の要件を詳しく調べることを検討してください。自動車と家庭用電化製品などの分野間で要件がどれほど異なるかに驚かれるでしょう。
射出成形には ABS などの熱可塑性プラスチックが使用されます。真実
ABS は、その強度のために射出成形に使用される一般的な熱可塑性プラスチックです。
ダイカストでは主に鉄金属が使用されます。間違い
ダイカストにはアルミニウム、亜鉛、マグネシウムなどの非鉄金属が使用されます。
最もコスト効率の高い製造プロセスを見つけるにはどうすればよいですか?
製造コストの迷路を進むのは気が遠くなるかもしれませんが、適切なプロセスを見つけることは、隠された宝を発見するようなものです。経費を抑えながら効率を最大化する方法を見てみましょう。
最もコスト効率の高い製造プロセスを見つけるには、材料コスト、労働力、生産量、品質基準を評価します。さまざまな方法を比較して、各プロジェクトに最適な選択肢を特定します。
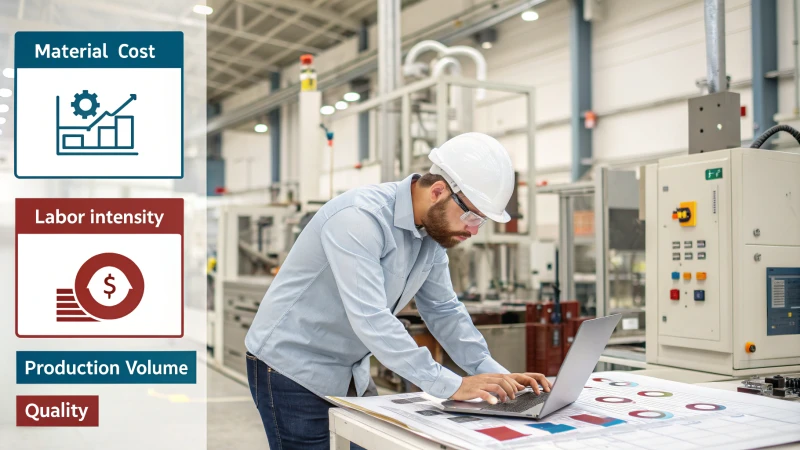
製造における費用対効果の評価
製造に関して言えば、コストと品質のバランスを取ることは単なる作業ではなく、芸術の一種です。小さな調整のように見えることが、長期的には大きな違いを生む可能性があることを学びました。たとえば、射出成形4 は、ユニットあたりのコストが低いため、大きな数字について話すときによく輝きます。
製造工程の比較
私は数え切れないほどの時間を費やして、さまざまな製造プロセスの長所と短所を比較検討してきました。これは私が何年にもわたってまとめた小さなチートシートです。
プロセス | 材料費 | 人件費 | スピード | 品質 |
---|---|---|---|---|
射出成形 | 低い | 中くらい | 速い | 高い |
CNC加工 | 中くらい | 高い | 遅い | 非常に高い |
3D プリント | 高い | 低い | 中くらい | 中くらい |
それぞれのプロセスには独特の魅力があります。たとえば、 CNCマシニング5 が頼りになります。
実際の例
家庭用電化製品に携わる中で、私は正しいプロセスの選択が収益にどのように大きな影響を与えるかをこの目で見てきました。プラスチック部品の製造射出成形とCNC機械加工を、コストと品質の最適な点が得られることを発見したと想像してみてください。こうした洞察が得られると、夜遅くまで仕事をする価値が生まれます。
したがって、これらの側面の評価に取り組むときは常に、プロジェクトの特定のニーズを念頭に置くようにしています。そうすることで、自分のアプローチを調整して、お金を節約するだけでなく、可能な限り最高の結果を確実に達成できるようになります。
射出成形は最も速い製造プロセスです。真実
射出成形は生産速度が速く、大量生産に適しています。
3D プリントは製造における材料コストが最も低くなります。間違い
3D プリントでは通常、他の方法に比べて材料コストが高くなります。
これらの方法のサイクルタイムはどのように比較されますか?
サイクルタイムがどのように生産ラインを変革するのかを初めて真に理解したときのことを覚えています。まるで複雑なパズルがはまっていくのを見ているようでした。
サイクル時間は、メソッドの複雑さ、材料、プロセスによって異なります。各方法の効率を分析することは、メーカーが生産を最適化し、コストを削減するのに役立ちます。
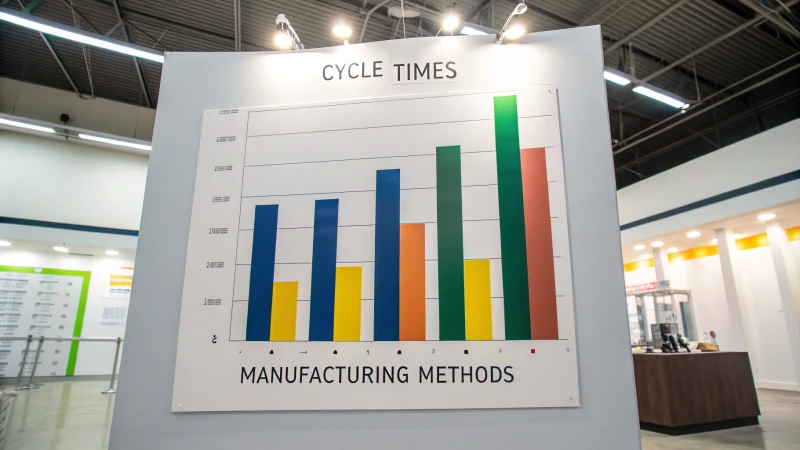
方法論の概要
製造に関しては、サイクル タイムが重要な要素であることがわかりました。 1 つの生産サイクルが完了するまでにかかる時間を指します。各製造方法7 には、異なるステップ、材料、効率といった独自の特徴があり、これらはすべてサイクル タイムに影響を与えます。
射出成形とCNC機械加工
- 射出成形: 複数の部品を同時に生産し、手作業による介入が少ないため、通常は高速化されます。大量のアイテムを素早く生産する必要がある場合に最適です。
- CNC加工: より正確ですが、個々のコンポーネントを順次処理するため、通常は時間がかかります。
方法 | 平均サイクルタイム | 最適な使用シナリオ |
---|---|---|
射出成形 | 30~60秒 | 大量生産 |
CNC加工 | 5~15分 | 精密部品 |
サイクルタイムに影響を与える要因
- マテリアル タイプ: 作業しているマテリアルのタイプによって、ゲームが大きく変わります。材料によっては、加熱または冷却に余分な時間が必要な場合や、異なる切断速度が必要な場合があります。
- 複雑さ: 複雑な設計では多くの処理ステップが必要になることが多く、処理速度が低下する可能性があります。
- 自動化レベル: 自動化を忘れないでください。機械は手作業に比べて作業をスピードアップするコツを持っています。
サイクルタイム最適化手法
私はボトルネックを特定し、ワークフローを改善するために、サイクル タイム データの分析に数え切れないほどの時間を費やしてきました。データ分析8のようなツールは、問題が行き詰まっている場所を特定するのに非常に役立ちます。
現実世界のアプリケーション
現実世界のシナリオを共有しましょう。私が働いていた会社は、電子機器用のプラスチック製筐体を製造していました。
- CNCから射出成形に切り替えることで、サイクル時間を半分以下に短縮し、生産量を大幅に増加しました。
- 部品の積み下ろしを処理するロボット アームなどの自動化ソリューション9も導入し
これらの微妙な違いを理解することで、メーカーはスピード、コスト、品質のバランスをとりながら、ニーズに最適な方法を選択できるようになります。
射出成形は CNC 加工よりも高速です。真実
射出成形では複数の部品が同時に製造されるため、サイクル タイムが短縮されます。
CNC 加工は大量生産に最適です。間違い
CNC 加工は時間がかかり、精密部品に適しています。
さまざまな製造技術がさまざまな業界にどのように適合するのでしょうか?
さまざまな製造技術が製品デザインのパズルにどのように組み込まれるか考えたことはありますか?
CNCなどの製造技術は、自動車やエレクトロニクスなどの産業に不可欠であり、製品の機能性と美観を高めます。
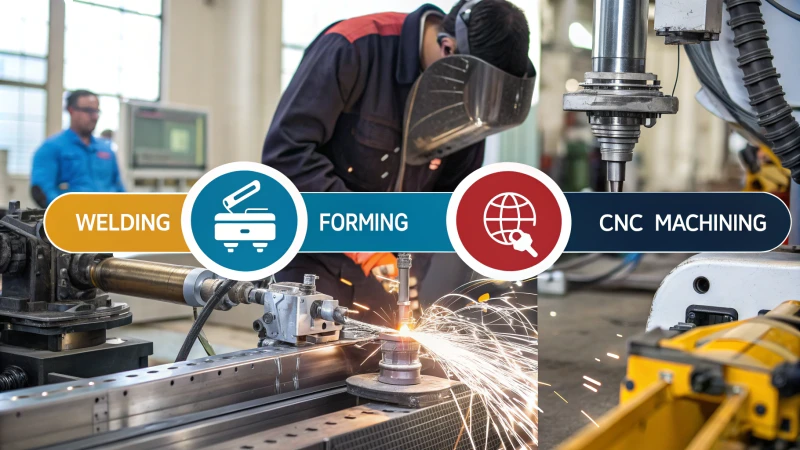
デザイナーとして、私は常に、さまざまなテクニックが製品作成の世界にどのようにシームレスに適合するかに魅了されてきました。それはパズルを組み立てるようなもので、各メソッドが独自のセンスと機能をテーブルにもたらします。これらのテクニックがさまざまな業界でどのように最適な場所を見つけるのかについて、個人的な洞察をいくつか紹介したいと思います。
溶接用途
溶接は、製造業界の縁の下の力持ちのようなものです。組み立てラインで車が組み立てられているのを初めて見たときのことを覚えています。金属部品が結合されて頑丈で信頼性の高いものが形成されるときに火花が散る様子は、とても魅力的でした。自動車産業では、溶接は、時間の試練や道路状況に耐えられる車体を構築するための鍵となります。
航空宇宙において、溶接はまったく新しいレベルの精度と重要性を帯びています。最も過酷な環境に耐える必要がある、軽量でありながら耐久性のある構造物を作ることを想像してみてください。これは簡単な作業ではありませんが、溶接によってそれが可能になります10 。
成形技術
成形のことになると、私の心はしばしばデザイナーとしての初期の頃を思い出し、金属を曲げたり形を整えて役に立つものを作ったりする実験をしていました。これらの技術は、家電部品から HVAC コンポーネントに至るまであらゆるものを作成する金属製造において不可欠です。
家庭用電化製品における成形とは、単に金属を成形することだけではありません。それは、手にぴったりとフィットする人間工学に基づいたデザインを作ることです。あなたのお気に入りのガジェットについて考えてみてください。おそらく、そのガジェットを機能的かつ快適に使用するためには、形状重要な役割を果たしています
CNC加工
CNC加工は私にとって大きな変革をもたらしました。特に精度が交渉の余地のない業界では、その精度は比類のないものです。 CNCマシンが医療機器や電子機器の複雑な部品を削り出すのを見ると、今でも興奮しますアーティストの仕事を見ているようなものですが、レーザーに焦点を当てた精度で行われます。
エレクトロニクス産業は高品質の回路基板を製造する CNC加工12 。この技術により、各コンポーネントがデバイスの機能の全体像に完全に適合することがどのように保証されるのかは興味深いです。
比較表
技術 | 業界への応用 | 主な利点 |
---|---|---|
溶接 | 自動車、航空宇宙 | 構造的完全性 |
形にする | 金属加工、エレクトロニクス | 形状のカスタマイズ |
CNC加工 | 医療機器、電子機器 | 精度と再現性 |
各テクニックはデザイナーのツールキットのツールのようなもので、それぞれに独自の利点と用途があります。これらの方法を理解することで、自分のプロジェクトに適切なアプローチを選択し、美的魅力と優れた機能性の両方を確保できるようになりました。
車体を組み立てるには溶接が欠かせません。真実
溶接により、自動車製造における強度と耐久性が確保されます。
CNC 加工が医療機器の製造に使用されることはほとんどありません。間違い
CNC加工は精密な医療機器の製造に不可欠です。
射出成形とダイカストは併用できますか?
射出成形とダイカストを組み合わせることで生産プロセスに革命をもたらすことができるのではないかと考えたことはありますか?可能性を掘り下げて、これら 2 つの強力なテクニックがどのようにしてあなたが探していたダイナミックなデュオになるのかを見てみましょう。
はい、射出成形とダイカストを組み合わせて生産効率と品質を向上させ、プラスチックと金属のコンポーネントを統合したハイブリッドアセンブリを効果的に作成できます。
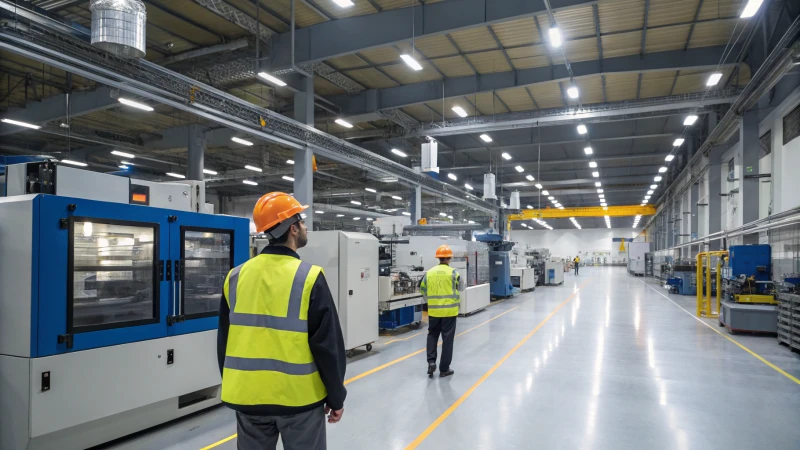
射出成形とダイカストを理解する
私が射出成形に初めて出会ったのは、夏の賑やかな工場でのインターンシップの時でした。溶けたプラスチックが金型に射出されてあらゆる種類の製品が作られる様子は、魔法が繰り広げられるのを目撃しているようでした。このプロセスは、複雑なプラスチック部品を大量に生産するのに最適です。一方、自動車部品のプロジェクトで実際に使われているのを見たダイカスト技術は、溶融金属を使用して複雑な細部を備えた頑丈な部品を作ります。
プロセス | 材質の種類 | 一般的な用途 |
---|---|---|
射出成形 | プラスチック | 家電製品、おもちゃ |
ダイカスト | 金属 | 自動車部品、ハードウェア |
潜在的な相乗効果
これらのテクニックを組み合わせると、非常にエキサイティングなイノベーションが生まれる可能性があります。金属構造が強度を提供し、周囲のプラスチックが柔軟性を高めて重量を軽減する自動車部品を作成することを想像してください。これは単なる理論上の話ではありません。それは現在、自動車などの業界で起こっており、最適なパフォーマンスには両方の材料が不可欠です。射出成形13 により、ダイカストによる金属構造と完全に噛み合う詳細なプラスチック部品の作成が可能になります。
設計上の考慮事項
もちろん、混合プロセスには課題がないわけではありません。共同プロジェクト中に、プラスチックと金属の熱膨張の違いが難しいハードルになる可能性があることを学びました。これに取り組むには、互いに補完し合う材料を選択し、柔軟な接合部を設計することが重要です。両方の方法を使用する場合の初期コストに眉をひそめるかもしれませんが、信じてください。生産効率14と製品品質の長期的な向上により、多くの場合、それを行う価値があります。
実用的なアプリケーション
エレクトロニクスに取り組んでいる私自身の経験では、金属で補強されたプラスチック製のハウジングをよく使用してきました。射出成形とダイカストのこのシームレスな統合は、製品の耐久性を向上させるだけではありません。また、創造的なデザインの柔軟性も可能になります。ケーススタディ15 を詳しく調べると、これらの成功したアプリケーションについての貴重な洞察が得られます。
新しいプロジェクトでこれらのテクニックを検討する場合でも、好奇心からこれらのテクニックを検討する場合でも、最終的には特定の要件によって決まります。さまざまな例16 を検討することで、私のような設計者は、この統合されたアプローチを採用するかどうかについて情報に基づいた決定を下すことができます。
射出成形により金属部品が製造されます。間違い
射出成形は金属部品ではなくプラスチック部品に使用されます。
ダイカストは複雑な形状に適しています。真実
ダイカストは精細で耐久性のある金属部品を作成できます。
結論
射出成形とダイカストは異なる製造プロセスであり、それぞれに独自の材料と用途があります。これらを組み合わせることで、さまざまな業界で生産効率と製品品質を向上させることができます。
-
射出成形の基礎を学び、その応用範囲と利点を理解します。 ↩
-
明確な目標を設定すると、設計プロセスが合理化され、製品の品質が向上します。 ↩
-
コスト、耐久性、用途などの特定の基準に基づいて適切な材料を選択する方法を検討します。 ↩
-
コスト効率と拡張性により、射出成形が大規模生産によく選ばれる理由を学びましょう。 ↩
-
CNC 加工がどのようにして高精度を確保し、複雑なコンポーネントの製造に不可欠となるかをご覧ください。 ↩
-
さまざまな製造プロセスを理解することで、プラスチック部品を効率的に製造するための戦略を探ります。 ↩
-
さまざまな製造方法を調べて、その独自のプロセスとそれがサイクル タイムにどのような影響を与えるかを理解します。 ↩
-
データ分析ツールが、本番環境の非効率性を特定し、サイクル タイムを改善するのにどのように役立つかをご覧ください。 ↩
-
自動化ソリューションがどのようにサイクル時間を短縮し、製造効率を向上させることができるかを学びましょう。 ↩
-
溶接技術が航空宇宙構造の安全性と性能をどのように強化するかをご覧ください。 ↩
-
成形技術が家庭用電化製品の人間工学に基づいたデザインにどのように貢献しているかを学びます。 ↩
-
高品質の電子部品の製造における CNC マシンの役割を理解します。 ↩
-
射出成形がいかに複雑な形状を効率的に作成するのに優れ、複雑なプラスチック部品に適しているかをご覧ください。 ↩
-
さまざまな製造方法を統合して全体的な生産効率を向上させる利点について学びます。 ↩
-
両方のプロセスを併用して優れた製品設計を実現した成功例をご覧ください。 ↩
-
ハイブリッド アセンブリが正常に実装されている実際のアプリケーションをご覧ください。 ↩