射出成形は、自動車から医療機器に至るまでの産業向けのプラスチック部品を生産する近代的な製造の基礎です。希望する品質、外観、機能を満たすために、後処理1として知られている追加の操作が必要です過剰な材料のトリミング、表面仕上げの適用、コンポーネントの組み立て、検査の実施など、これらの手順は、最終製品が業界の基準を満たすために重要です。
後処理は射出成形部品2の、生産に時間とコストを追加することもできます。したがって、後処理を効果的に理解し、管理することは、品質と効率性3の。このブログでは、射出成形における後処理を管理するためのベストプラクティスを探り、基本的な概念から実用的なツールや関連技術まで、すべてをカバーしています。
射出成形の後処理とは何ですか?
射出成形の後処理とは、プラスチック部品の品質、外観、機能性を改善するために、成形プロセスの後に実行された操作を指します。これらの操作は、表面欠陥などの成形プロセスの制限に対処し、審美的または機能的な強化により価値を追加します。
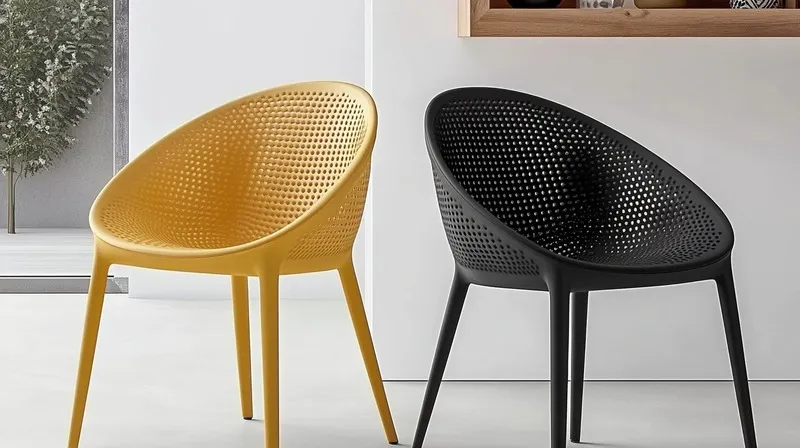
-
技術名とエイリアス:後処理は、しばしば「セカンダリオペレーション4 」または「仕上げ操作5 」と呼ばれます。特定の技術には、ゲートトリミング、討論、スプレーペインティング、パウダーコーティング、パッド印刷、レーザーマーキング、UV印刷、熱ステーキング、超音波溶接、金型テクスチャリングが含まれます。
-
コア原則:主な目標は、パーツが審美的、機能的、規制要件を満たすことを保証することです。後処理は、成形の欠陥を修正し、耐久性や視覚的魅力を高め、複雑なアセンブリを可能にします。コストが追加されますが、成形中に高価なツールや材料を使用するよりも経済的になる場合があります。
射出成形に後処理はどのように分類されますか?
後処理技術は、プロセスの種類、物質的な考慮事項、およびアプリケーション領域に基づいて分類できます。
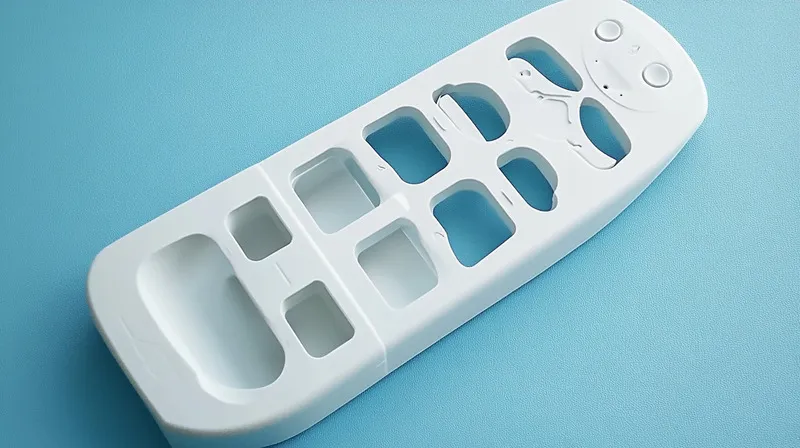
- プロセス別:
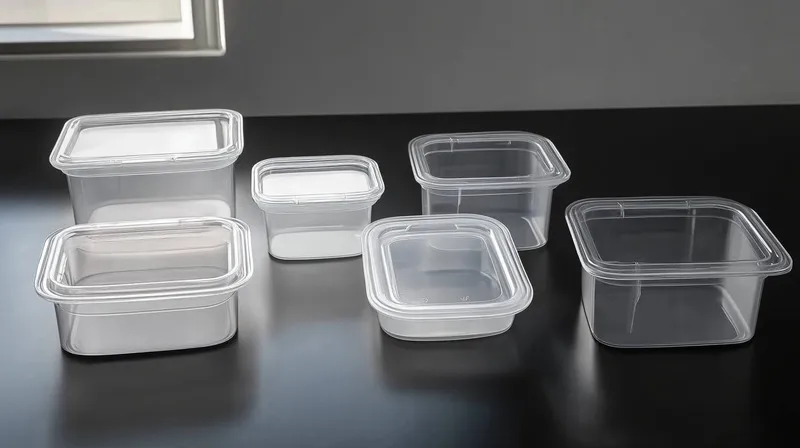
-
材料による:技術は、表面エネルギーや耐熱性など、プラスチックの特性によって異なります。たとえば、ポリエチレンのような低表面エネルギープラスチックは、塗料の接着に血漿処理7を
-
アプリケーションによる生体適合性仕上げ8 )、家電(ブランディング)、航空宇宙(精密機械加工)などの業界のニーズに合わせて調整されています
後処理の典型的なアプリケーションシナリオは何ですか?
後処理は、一部の品質、美学、または規制のコンプライアンスが最重要である業界で重要です。重要なシナリオには次のものがあります。
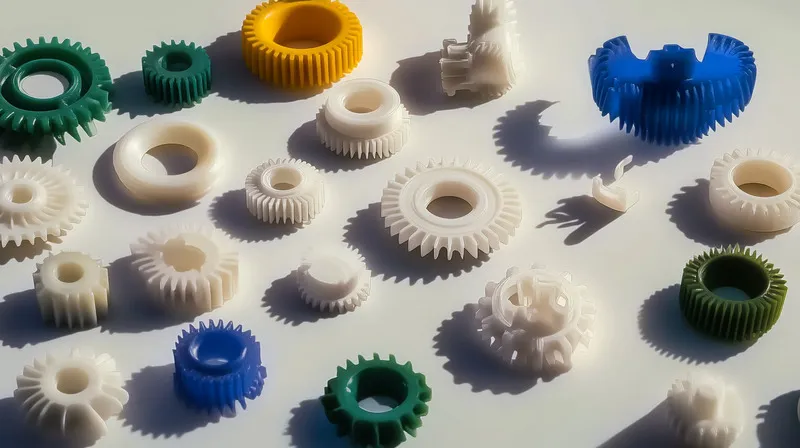
-
自動車:内部および外部コンポーネントの塗装やテクスチャリング、溶接による機能アセンブリ、耐久性のためのUV耐性コーティングなどの美的仕上げ。
-
医療機器:精密仕上げ、滅菌、および溶媒のないアセンブリのための超音波溶接やトレーサビリティのためのレーザーマーキングなどの生体適合プロセス。
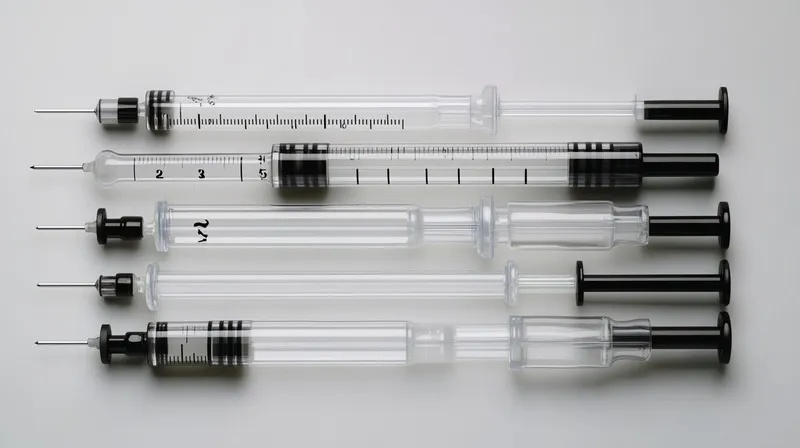
-
コンシューマーエレクトロニクス:ブランディング用の表面仕上げ(例:パッド印刷ロゴなど)、機能性のためのアセンブリ(熱ステーキングなど)、および小型化用のコンパクトデザイン。
-
航空宇宙:高精度の機械加工、環境抵抗のための特殊なコーティング、厳しい基準を満たすための厳密な検査。
他の技術と比較した後処理の長所と短所は何ですか?
射出成形の後処理は、CNC加工や3D印刷などの他の製造方法としばしば比較されます。これが簡単な比較です:
側面 | 射出成形の後処理 | CNC加工9 | 3D プリント10 |
---|---|---|---|
料金 | 大量生産に費用対効果が高いが、後処理コストを追加します。 | 低容積または複雑な部品のコストが高くなります。 | プロトタイプには費用対効果が高いですが、スケーリングには高価です。 |
精度 | 中程度の精度;後処理は精度を向上させます。 | 複雑な機能の高精度。 | 多様。多くの場合、仕上げには広範な後処理が必要です。 |
スケーラビリティ | 大量生産に非常にスケーラブル。 | 時間とコストによる限られたスケーラビリティ。 | 低容量またはカスタムパーツに最適です。 |
後処理ニーズ | 欠陥、美学、またはアセンブリに必要です。 | 部品がしばしば終了するため、最小限です。 | 表面の品質と強度のために広範な。 |
- 射出成形におけるポスト処理の長所11:
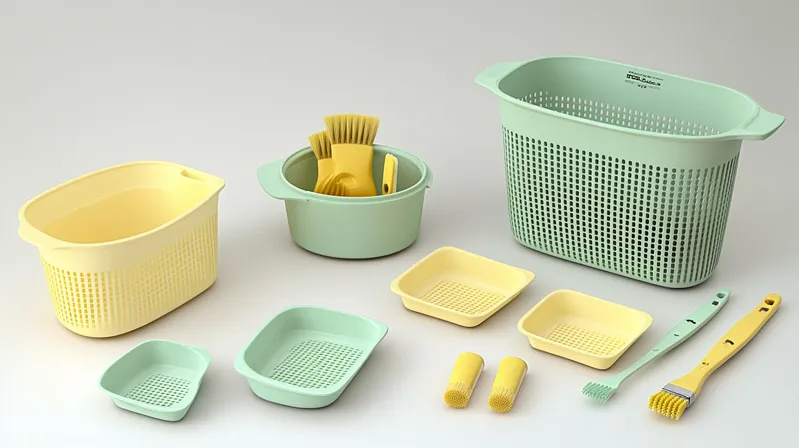
- 美学、機能、耐久性を高めます。
- カスタマイズ(例えば、ロゴ、色)およびブランディングを有効にします。
- 多くの場合、金型を変更したり、プレミアム材料を使用したりするよりも費用対効果が高くなります。
- 短所:
- 生産時間とコストを増加させます。
- 変動を避けるために慎重に計画する必要があります。
- 特殊な機器や専門知識が必要になる場合があります。
射出成形における後処理の完全なワークフローは何ですか?
射出成形における後処理ワークフローには、いくつかの重要なステップが含まれ、それぞれに特定の手法とパラメーターがあります。
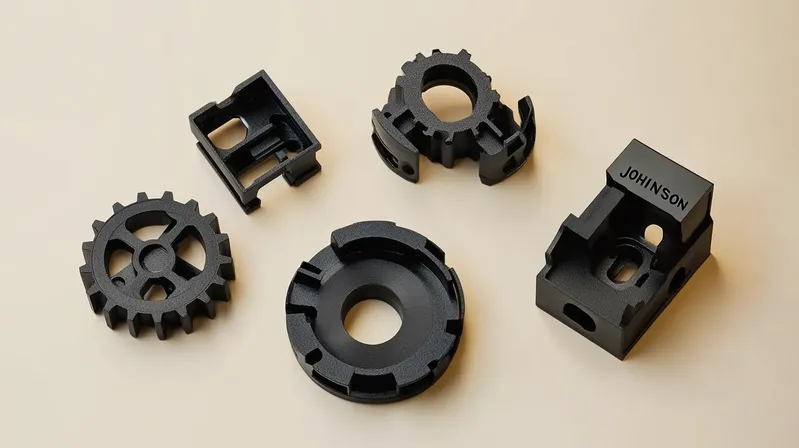
- 冷却:
- 目的:均一な固化を保証して、反り、収縮、欠陥を最小限に抑えます。
- 重要なパラメーター:冷却時間(サイクル時間の最大80%)、カビの温度、および材料の熱伝導率。
- ベストプラクティス:コンフォーマル冷却チャネルを使用し、均一な壁の厚さを維持し、正確な温度制御のためにバリオターやパルス冷却などの高度な技術を採用します。
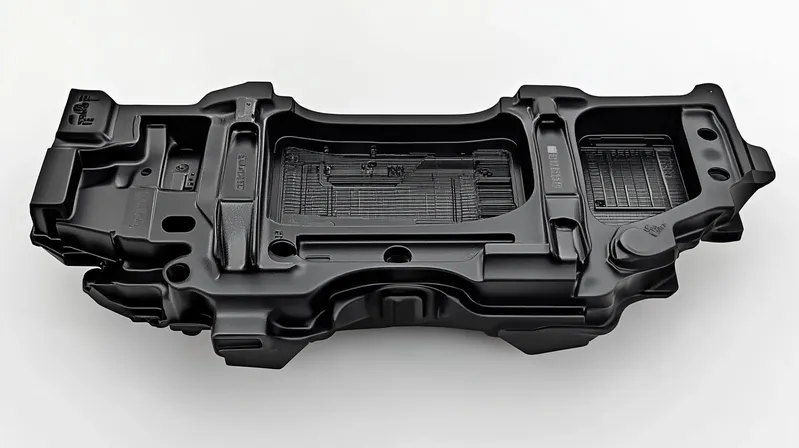
-
排出:
- 目的:損傷なしに金型から部品を削除します。
- 重要なパラメーター:排出力、カビ放出剤、および自動化設定。
- ベストプラクティス:自動排出システムを使用して、一貫性を確保し、表面損傷を防ぎます。
-
トリミング/burring:
- 目的:余分な材料(フラッシュ、ゲート)を除去し、エッジを滑らかにします。
- テクニック:手動スクレイピング、タンブリング、熱エネルギーdeburring(TED)、精密粉砕。
- 重要なパラメーター:ツールの精度、材料硬度、安全プロトコル。
- ベストプラクティス:アクセスできないエリアにTEDを使用し、適切な個人保護具(PPE)を確保します。
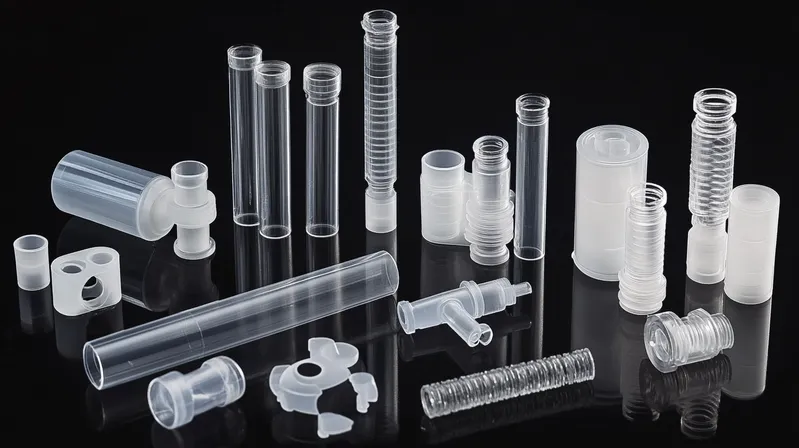
-
表面仕上げ:
- 目的:美学、耐久性、および機能性(グリップ、UV抵抗など)が強化されます。
- テクニック:スプレー塗装(セルフケアリングまたはUV硬化)、パウダーコーティング、パッド印刷、レーザー彫刻、UV印刷。
- 重要なパラメーター:表面の準備(洗浄、サンディング、プラズマ治療)、コーティングの厚さ、硬化時間。
- ベストプラクティスプラズマ治療)のために、プラズマ処理で低表面エネルギープラスチックを準備します
-
組み立て:
- 目的:機能的または構造的な目的で部品に参加します。
- 技術:超音波溶接(20,000〜40,000 Hzの振動)、熱ステーク(インサート用のプラスチックを柔らかくする)、ねじ付き挿入インストール。
- 重要なパラメーター:溶接周波数、挿入力、および材料の互換性。
- ベストプラクティス:溶媒を避けるために、生体適合性医療機器に超音波溶接を使用します。
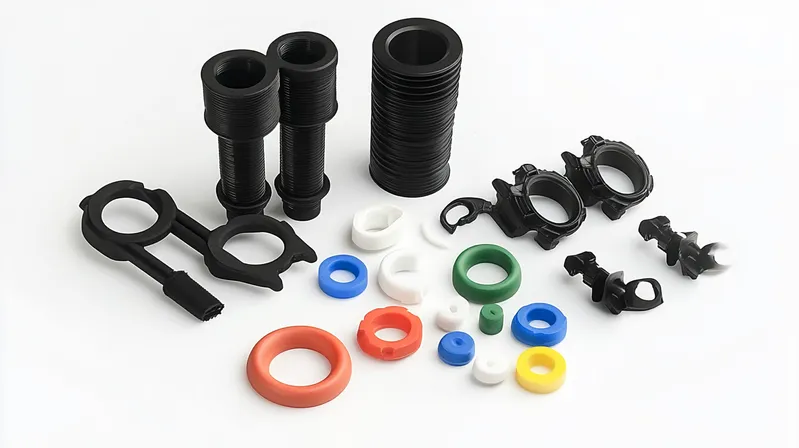
- 検査:
- 目的:部品が品質と規制基準を満たすことを保証します。
- 技術:目視検査(表面欠陥)、寸法測定(精度)、NDT(内部完全性)。
- 重要なパラメーター:検査頻度、自動化レベル、および許容限度。
- ベストプラクティス:効率と一貫性のために自動検査システムを実装します。
材料の互換性は後処理にどのように影響しますか?
後処理技術の選択は、プラスチックの特性に依存します。

-
熱可塑性科学:射出成形で最も一般的です(例、ABS、ポリカーボネート、ポリエチレン)。低表面エネルギー熱可塑性物質(例、ポリエチレン、ポリプロピレン)は、塗装またはコーティングの接着に血漿処理を必要とします。高温熱可塑性プラスチック(たとえば、ピーク)には、特殊な溶接技術が必要になる場合があります。
-
サーモセット:高温用途(例、エポキシ、フェノール)に使用されます。それらの架橋構造は、再溶解を制限し、精密粉砕や特殊なコーティングなどのユニークな仕上げ方法を必要とします。
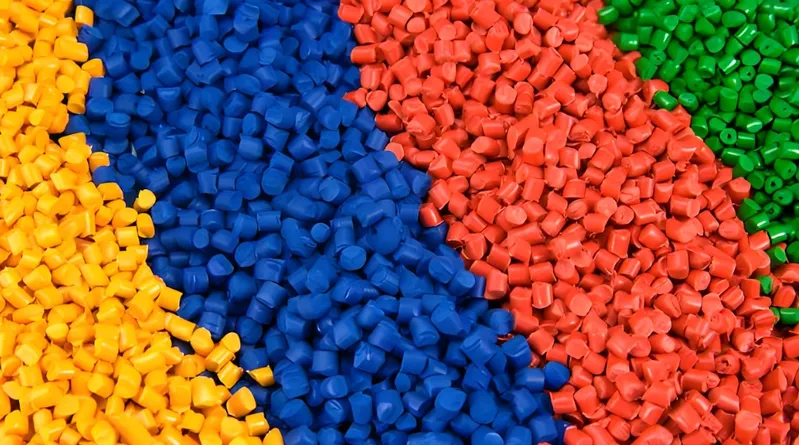
- エラストマー:柔軟な部品に使用されます(例、TPE、シリコン)。後処理は、穏やかな否定または互換性のあるコーティングを使用して、弾力性を維持する必要があります。
後処理を念頭に置いて部品を設計するためのベストプラクティスは何ですか?
後処理を最適化するには、パーツ設計中に以下を検討してください。
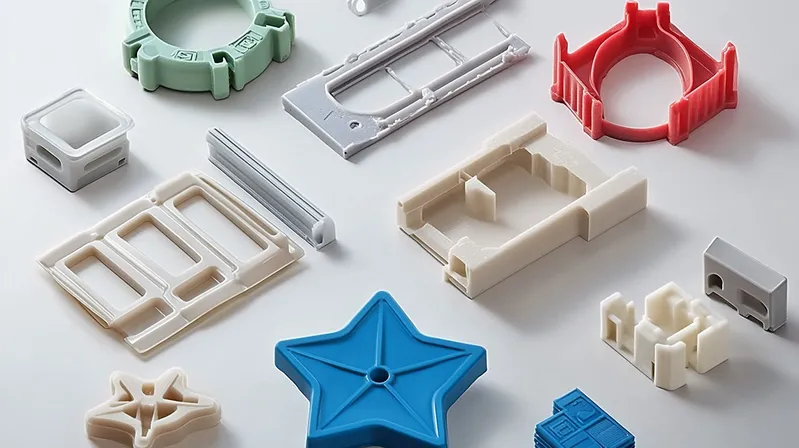
-
材料の選択:目的の後処理(塗装可能な腹筋、溶接可能ポリカーボネート)と互換性のあるプラスチックを選択します。
-
部品設計:冷却とトリミングを簡素化するために均一な壁の厚さを確保し、簡単にフラッシュを取り外すためにアクセス可能なゲートを設計します。
-
寛容と適合:組み立て中の適合性の問題を回避するための後処理公差を説明します。
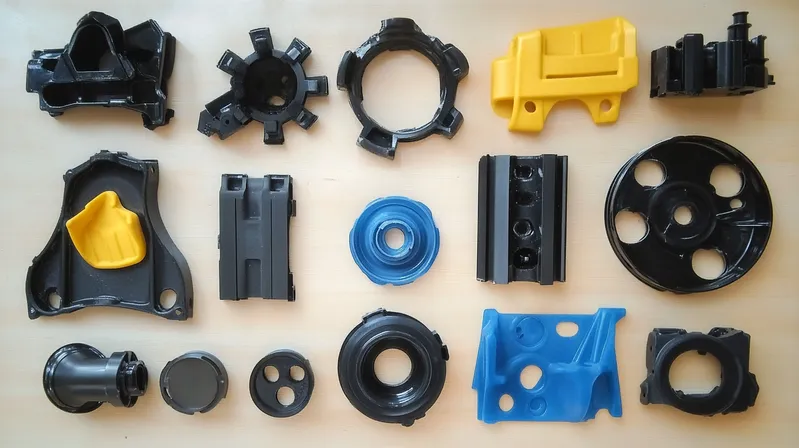
-
コストと時間:処理後のニーズと生産予算とタイムラインのバランス。
-
プロセスの制限:テクニックの制約を認識します(たとえば、塗装には特定のプラスチックの表面処理が必要になる場合があります)。
適切な後処理技術を選択する方法は?
適切な後処理技術を選択するには、構造化されたアプローチが含まれます。
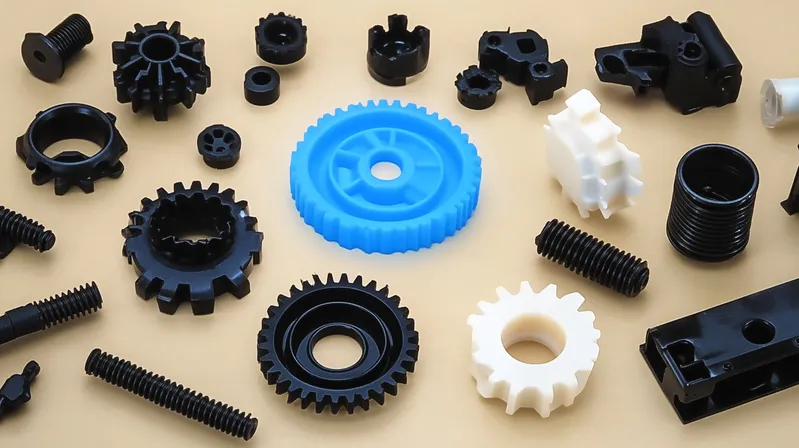
-
要件を特定する:部品の機能(例、強度)、美的(色)、および規制(例えば、生体適合性)のニーズを決定します。
-
オプションを評価する:コスト、時間、材料の互換性、生産量に基づいてテクニックを比較します。たとえば、レーザーマーキングはツールレスで正確ですが、パッド印刷よりも費用がかかる場合があります。
-
計画の統合:可能な場合は自動化を使用して、ポストプロセッシングが製造ワークフローにスムーズに統合されるようにします。
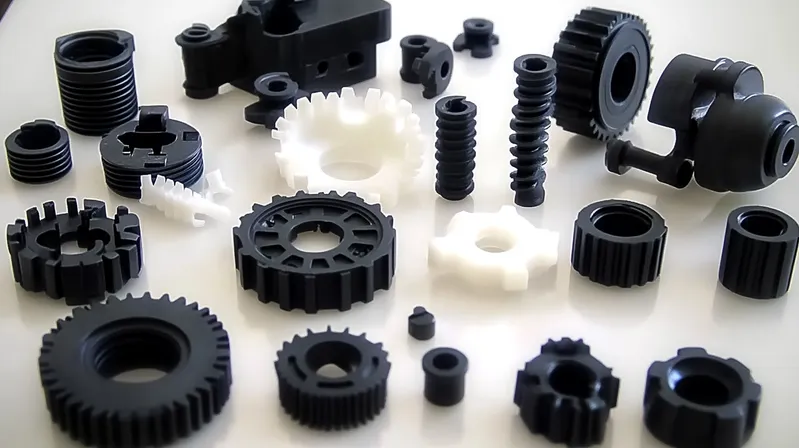
- 決定ツリー:
- 美的ニーズ? →塗装、パッド印刷、またはレーザーマーキングを検討してください。
- 機能アセンブリ? →熱し、超音波溶接、またはインサートを評価します。
- 欠陥補正? →トリミング、burring、または表面仕上げの優先順位付け。
- 品質が重要ですか? →視覚、寸法、またはNDT検査を実装します。
決定要因 | 修正(例えば、トリミング) | 装飾(例えば、絵画) | 機能的(例えば、溶接) | 品質管理(例、検査) |
---|---|---|---|---|
料金 | 低から中程度 | 中程度から高程度 | 中程度から高程度 | 低から高(自動化されたシステム) |
時間 | 速い | 適度 | 適度 | Varies(手動と自動化) |
物質的な影響 | 最小限 | 表面準備が必要です | 素材特有の | 最小限 |
アプリケーション | すべての産業 | 自動車、電子機器 | 医療、自動車 | すべての産業 |
射出成形における後処理は、より広範な製造エコシステムに接続します。
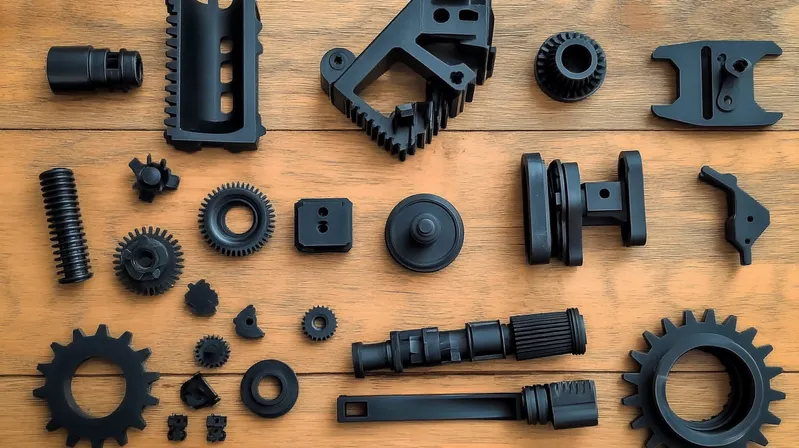
- 上流のテクノロジー:
- 射出成形機:正確な制御を備えた高度な機械は、欠陥を軽減し、後処理のニーズを最小限に抑えます。
- 金型設計ソフトウェア:CAD/CAMなどのツールは、排出とトリミングを容易にするために金型設計を最適化します。
- 材料科学:表面特性や溶接性が向上したプラスチックの研究により、後処理効率が向上します。
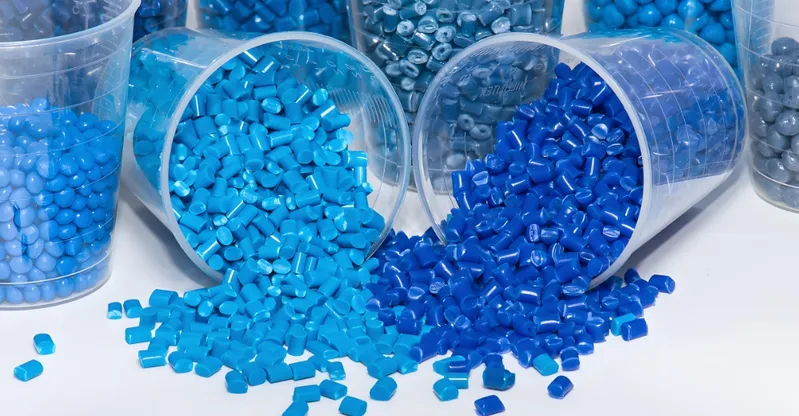
-
ダウンストリームテクノロジー:
- 自動アセンブリライン:溶接や挿入のインストールなどの後処理タスクを合理化します。
- パッケージングソリューション:カスタムパッケージング(たとえば、フォーム、バーコード)は、配布中に完成した部品を保護します。
- ロジスティクス:効率的な流通システムは、後処理された部品のタイムリーな配信を保証します。
-
補完的な技術:
- CNC加工:モールディング後の正確な特徴(穴、糸など)を追加(プロトラブ加工)を追加します。
- 3D印刷:プロトタイプまたは複雑なジオメトリに役立ちますが、異なる後処理が必要です。
- ロボットシステム:一貫性のためにトリミング、塗装、または検査を自動化します。
- 自動検査:ビジョンシステムまたはNDTを使用して品質制御を強化します。
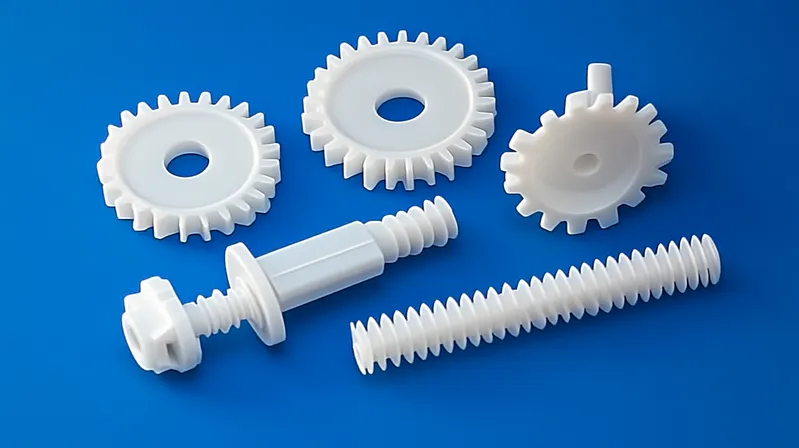
結論
射出成形における後処理の管理は、業界の基準を満たす高品質のプラスチック部品を生産するために不可欠です。概念的なフレームワーク、アプリケーションシナリオ、技術的なワークフロー、実用的なツールを理解することにより、メーカーはプロセスを最適化し、情報に基づいた意思決定を行うことができます。早期の計画、材料の互換性、自動化は、品質と効率のバランスをとるための鍵です。
後処理は、すべての射出成形部品に不可欠です。間違い
一部の部品は、金型から直接品質基準を満たしている場合、後処理を必要としない場合があります。
後処理を自動化すると、生産コストが削減される可能性があります。真実
自動化は効率と一貫性を高め、全体的なコストを削減する可能性があります。
-
後処理のためのベストプラクティスを探ることは、製造業者が生産の品質と効率を向上させるのに役立ちます。 ↩
-
後処理がどのように射出成形部品を改善するかを理解することで、製造の結果が向上する可能性があります。 ↩
-
品質と効率のバランスをとるための学習戦略は、製造プロセスと結果を大幅に改善できます。 ↩
-
二次操作は、成形部品の強化に重要な役割を果たします。これらのテクニックとその利点について詳しく発見してください。 ↩
-
成形部品で望ましい美学と機能を達成するためには、仕上げ操作が不可欠です。これらのプロセスの詳細をご覧ください。 ↩
-
このリンクを探索して、製品の品質を高め、欠陥を排除するさまざまな修正プロセスを理解してください。 ↩
-
効果的なコーティングに不可欠な低表面エネルギープラスチックの接着を強化する上での血漿治療の役割について学びます。 ↩
-
医療機器における生体適合性仕上げの重要性を発見し、ヘルスケアアプリケーションの安全性とコンプライアンスを確保します。 ↩
-
CNCの機械加工を探索すると、他の方法と比較して、その精度と効率に関する洞察を提供できます。 ↩
-
3D印刷について学ぶことは、プロトタイプとカスタムパーツの独自の利点を明らかにすることができます。 ↩
-
射出成形における後処理を理解することは、製造技術とその利点に関する知識を高めることができます。 ↩