無駄のない製造1つの原則を射出成形に適用すると廃棄物2、コストを削減し、効率を改善することにより、生産を最適化し、自動車や消費財などの産業に最適です。
リーン製造は、プロセスを合理化し、廃棄物を削減し、生産性を高める射出、大量の製造に大きな利点をもたらします。
無駄のない原則が射出成形とどのように統合されるかを理解することで、生産戦略を変えることができます。このガイドに飛び込み、これらの方法論がどのように連携して高品質の部品を効率的に配信するかを調査します。
リーン製造は、射出成形の生産コストを削減します。真実
過剰な在庫や欠陥などの廃棄物を最小限に抑えることにより、リーンは材料と運用コストを下げます。
リーン原則は、大規模なメーカーにのみ適用できます。間違い
リーンは、効率を改善することにより、あらゆる規模の企業に利益をもたらすことができますが、実装は規模によって異なる場合があります。
射出成形における無駄のない製造とは何ですか?
リーン製造は、生産性と品質を向上させながら、廃棄物(最終製品に価値を加えないもの)を排除することに焦点を当てた方法論です。射出成形では、溶融物質が金型に注入されて正確な部品を作成するプロセスで、リーン原理は操作を合理化して、それらをより速く、より安く、より信頼性を高めることができます。
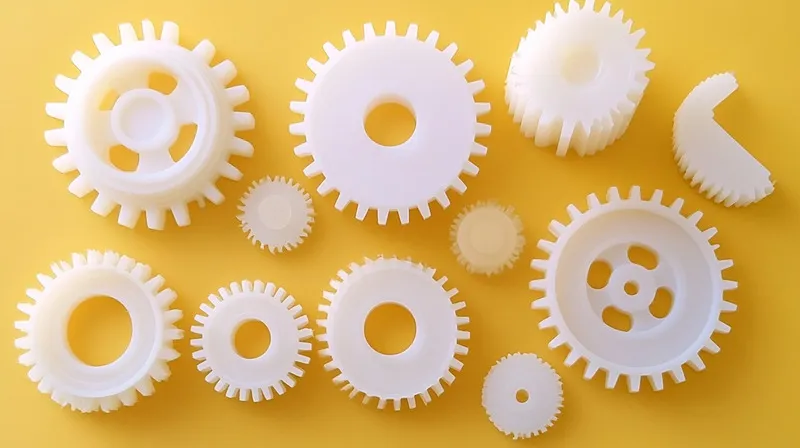
リーン製造4は、廃棄物を排除し、サイクル時間を削減し、一部の品質を改善し、自動車、医療、消費財などの産業に利益をもたらします。
リーン原則 | 射出成形への適用 | 利点 |
---|---|---|
ジャストインタイム(jit)5 | 必要なものだけを生産します | 在庫コストを削減します |
5S方法論6 | ワークスペースを整理します | 効率が向上します |
カイゼン | 継続的な改善 | プロセスの品質を向上させます |
無駄のない製造
トヨタの生産システムを担当したリーンは、廃棄物の削減を通じて効率を強調しています。射出成形では、待機、在庫、輸送、動き、過剰加工、過剰生産、欠陥の7つの廃棄物をターゲットにしています。たとえば、アイドルマシンの時間を短縮するか、過剰な材料の使用を直接向上させると、収益性が向上します(無駄のない製造プロセス)。
射出成形
射出成形には、溶融材料、通常は腹筋やポリプロピレンなどの熱可塑性科学物質を注入することが含まれます。その精度とスケーラビリティに広く使用されています。リーンは、材料の選択から排出(プラスチック射出成形)まで、各ステップを最適化することにより、これを強化します。
リーン製造により、射出成形効率が向上します。真実
ワークフローを合理化し、ダウンタイムを短縮することにより、リーンはスループットとリソースの使用をブーストします。
射出成形は、自動化なしではリーンの恩恵を受けることはできません。間違い
自動化は役立ちますが、5秒やJITなどの無駄のない改善を手動で適用して、重要な結果を得ることができます。
リーンを使用した射出成形プロセスのステップは何ですか?
射出成形プロセス7は、無駄のない原理と組み合わせると、最小限の廃棄物で高品質の部品を生産するための非常に効率的なシステムになります。
リーン原則8廃棄物を削減し、サイクル時間を改善することにより、射撃、噴射、冷却、排出物(閉鎖、噴射、冷却、排出)を最適化します。
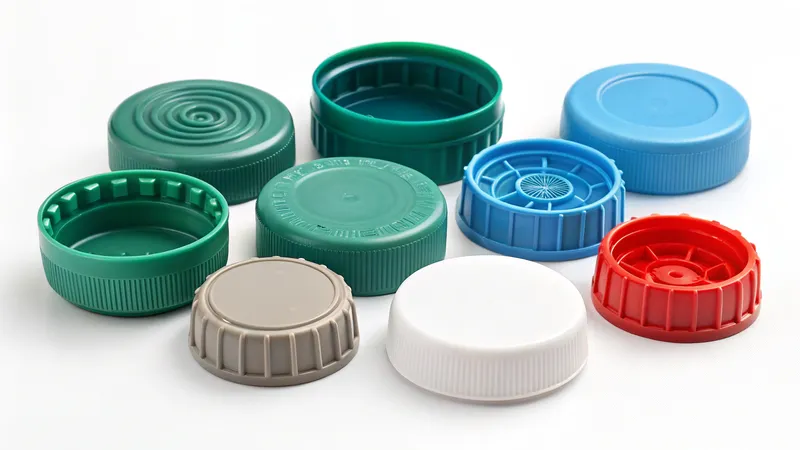
クランピング
型は閉じて固定されています。 LEANは、クイックチェンジツールを適用してセットアップ時間を削減し、生産ラン間のより速い移行を確保します。
注射
溶融物質が型に注入されます。リーンは、圧力や速度などのパラメーターを最適化して、材料の廃棄物と欠陥を減らします。
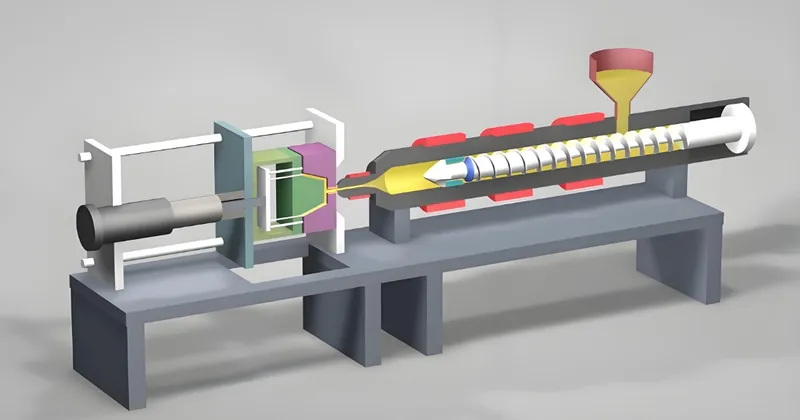
冷却
材料は固まります。 leanせたバランスの冷却時間とサイクル効率、コンフォーマル冷却9品質を維持します。
排出
部品は金型から削除されます。リーンは、スマートデザインを通じて滑らかな排出を保証し、損傷とリワークを最小限に抑えます。
リーンは、射出成形のサイクル時間を短縮します。真実
セットアップとプロセスステップの最適化品質を犠牲にすることなく、生産サイクルを短くします。
リーンは、射出成形のすべての欠陥を排除します。間違い
リーンは欠陥を大幅に減らしますが、材料または機器の要因により、ある程度の変動性が持続する可能性があります。
無駄のない射出成形を適用することの重要な要因は何ですか?
射出成形に無駄のない適用プロセスの最適化、労働力のトレーニング、および材料の選択に依存して、効率と品質を最大化します。
無駄のない射出成形は、廃棄物の削減とコスト削減を達成するためのプロセス効率、従業員のトレーニング、材料の互換性に依存します。
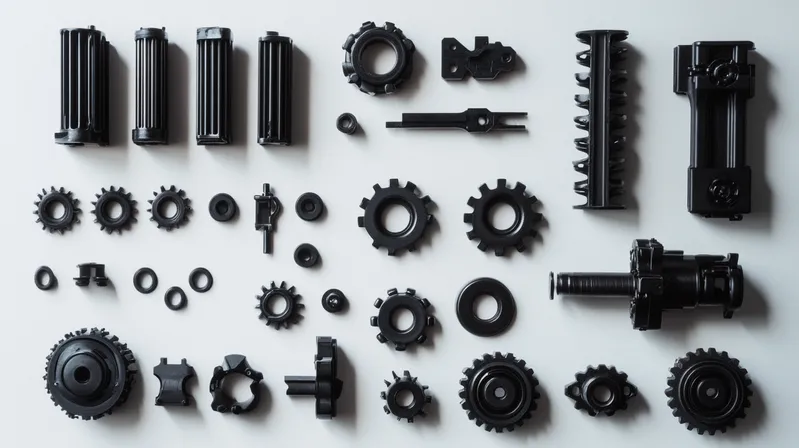
プロセス効率
5秒や総生産メンテナンス(TPM)などのリーンツールは、マシンをスムーズに動作させ、ワークスペースを整理し、ダウンタイムを削減し、出力を増やします(リーン原則)。
従業員研修
リーンには文化的な変化が必要です。 Kaizenのような原則に関する包括的なトレーニングにより、スタッフは廃棄物を特定して排除できることを保証しますが、変化に対する抵抗はハードルになる可能性があります。
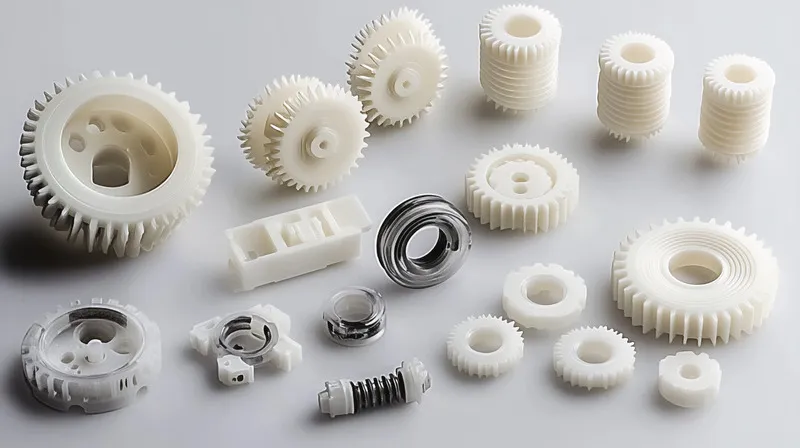
材質の適合性
最適な流れと最小限の収縮(熱可塑性形成など)を選択すると、スクラップとリワークを減らすことで無駄のない結果を強化します(材料選択)。
射出成形で無駄のない成功にはトレーニングが不可欠です。真実
よく訓練されたスタッフは、無駄のない戦略を効果的に実施し、継続的な改善を促進することができます。
リーンは、すべての材料と同様にうまく機能します。間違い
材料特性は、無駄のない結果に影響します。廃棄物を最小限に抑えるために、より多くの調整が必要なものもあります。
射出成形中のリーンのアプリケーションは何ですか?
射出成形の無駄のない製造は、特定のニーズに合わせた効率的で高品質の生産を提供することにより、幅広い産業をサポートします。
無駄のない射出成形は、費用対効果の高い大量生産のために、自動車、消費財、医療産業に適用されます。
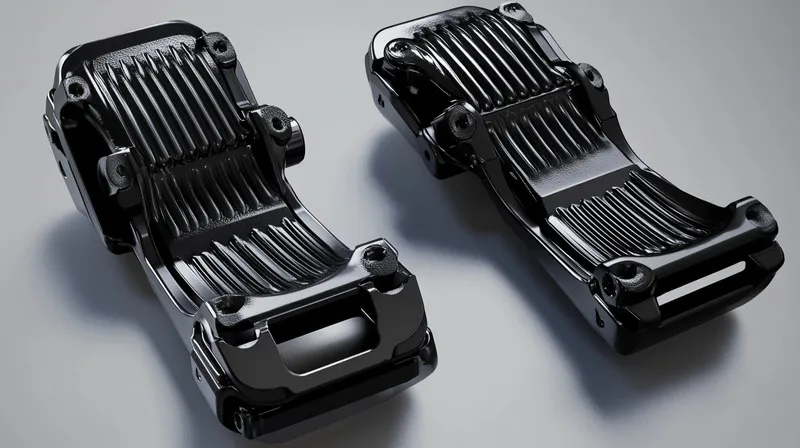
自動車産業
リーンはサイクル時間を短縮し、ダッシュボードやバンパーなどの部品の一貫した品質を保証します。これは、組立ラインにとって重要です(リーンゴール)。
消費財
JIT生産は在庫を最小限に抑え、アプライアンスハウジングやおもちゃなどのアイテムの需要の変動を満たします。
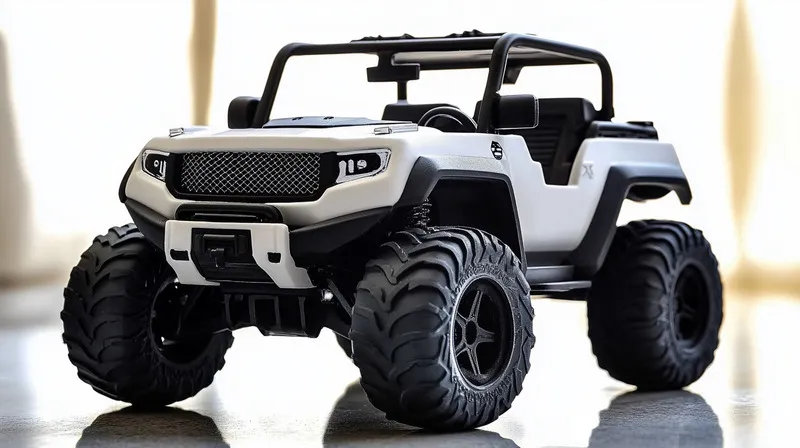
医療機器
リーンは、シリンジなどのコンポーネントの品質制御を強化し、重要なアプリケーションの欠陥を軽減します。
リーンは、射出成形の競争力を向上させます。真実
コストの削減と高品質により、メーカーはグローバル市場で優位に立つことができます。
リーンは、大量の生産にのみ役立ちます。間違い
無駄のない利益も、廃棄物を減らし、柔軟性を向上させることにより、低音量で実行されます。
リーンと従来の射出成形の違いは何ですか?
プロセスアプローチ
従来の成形は、多くの場合、非効率性を許容する出力に焦点を当てています。リーンは価値を優先し、すべてのステップで廃棄物を体系的に削減します。
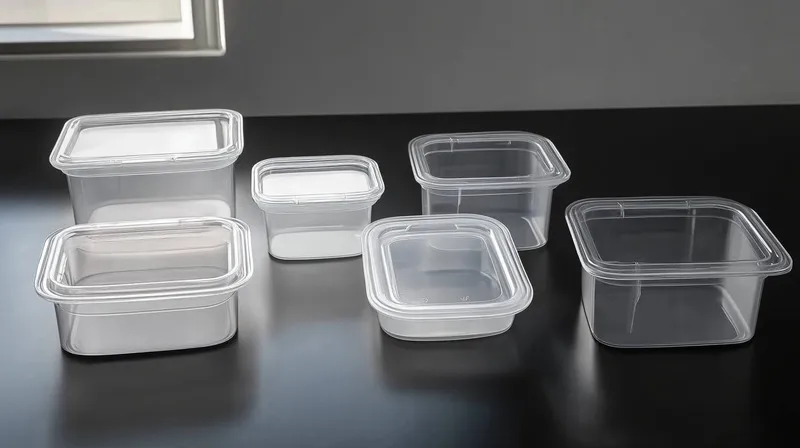
効率
リーンはサイクル時間を短くし、リソースの使用を削減しますが、従来の方法にはセットアップが長くなり、スクラップレートが高くなる場合があります。
コストへの影響
リーンは廃棄物の削減によりコストを削減します。従来の成形は、過剰生産または欠陥のためにより高い費用が発生する可能性があります(無駄のない利点)。
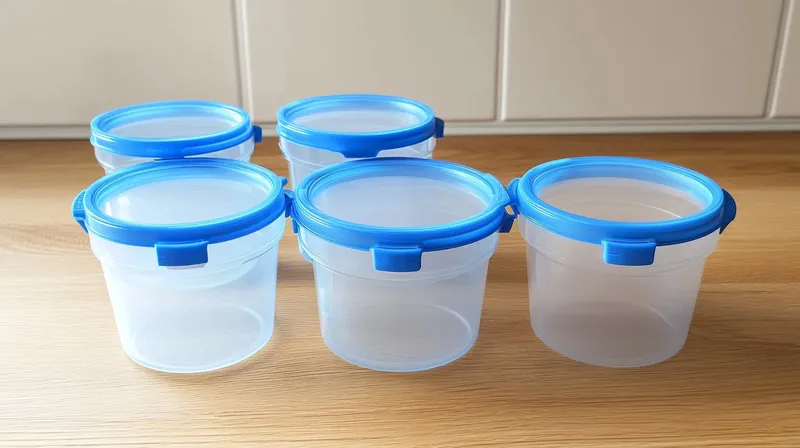
結論
無駄のない製造を射出成形に適用すると、廃棄物を排除し、品質を向上させ、コストを削減することで生産に革命をもたらします。自動車から医療アプリケーションまで、リーンは効率的でスケーラブルなソリューションを提供します。ワークスペースを5秒で整理し、チームを訓練し、プロセスを最適化する小さなステップから始めて、その潜在能力を最大限に発揮します(無駄のない実装)。
-
無駄のない製造が射出成形プロセスに革命を起こし、効率を向上させる方法を探ります。 ↩
-
射出成形と収益性の向上における廃棄物の排除の重要な役割について学びます。 ↩
-
より良い結果を得るために、無駄のない原則を通じて射出成形の生産性を高めるための効果的な戦略を発見します。 ↩
-
無駄のない製造が射出成形プロセスを変換し、生産の効率と品質を向上させる方法を探ります。 ↩
-
Just-in-Time(JIT)アプローチと、コストの削減と在庫管理の改善に大きな影響を与えることについて学びます。 ↩
-
5Sの方法論と、効率と生産性を最大限に活用するためのワークスペースの整理におけるその役割を発見してください。 ↩
-
射出成形プロセスを探索すると、さまざまな業界での効率と用途に関する洞察が得られます。 ↩
-
無駄のない原則を理解することで、効率的な製造プロセスと廃棄物削減戦略に関する知識を高めることができます。 ↩
-
コンフォーマル冷却について学ぶことは、成形部品の効率と品質を改善する高度な技術を理解するのに役立ちます。 ↩