क्या आपको कभी अपने इंजेक्शन मोल्डिंग प्रोजेक्ट में कोई समस्या आई है? आइए देखें कि मोल्ड फ्लो विश्लेषण आपके लिए सब कुछ कैसे बदल सकता है!
मोल्ड फ्लो विश्लेषण गेट स्थान, रनर सिस्टम, इंजेक्शन दबाव और शीतलन समय को समायोजित करके इंजेक्शन मोल्डिंग को अनुकूलित करता है, जिससे विनिर्माण दक्षता और चिकनाई बढ़ती है।
मैं उत्पाद डिजाइन में अपनी यात्रा के बारे में सोचता हूं। मुझे याद है कि इंजेक्शन मोल्डिंग प्रक्रिया में समस्याओं को ठीक करने में मैंने कई घंटे बिताए थे। मैंने उस समय मोल्ड फ्लो विश्लेषण की खोज की। यह उपकरण मेरे लिए जीवन रेखा बन गया। मैंने गेट स्थान और इंजेक्शन दबाव जैसे मापदंडों को अनुकूलित किया। मुझे बहुत प्रभावशाली सुधार नज़र आने लगे। गेट के स्थान को समायोजित करने से मुझे जटिल हिस्सों में शॉर्ट शॉट और हवाई जाल से बचने में मदद मिली। टुकड़े एक पहेली की तरह एक साथ फिट होते हैं!
मोल्ड प्रवाह विश्लेषण इंजेक्शन मोल्डिंग दक्षता में सुधार करता है।सत्य
यह दावा सच है क्योंकि मोल्ड फ्लो विश्लेषण मापदंडों को अनुकूलित करने में मदद करता है, जिससे बेहतर विनिर्माण दक्षता प्राप्त होती है।
गेट का स्थान मोल्डिंग में उत्पाद की गुणवत्ता को प्रभावित नहीं करता है।असत्य
यह दावा गलत है क्योंकि गेट का स्थान ढाले गए उत्पाद के प्रवाह और गुणवत्ता पर महत्वपूर्ण प्रभाव डालता है।
- 1. मोल्ड प्रवाह विश्लेषण क्या है और यह महत्वपूर्ण क्यों है?
- 2. गेट का स्थान इंजेक्शन मोल्डिंग को कैसे प्रभावित करता है?
- 3. रनर सिस्टम इंजेक्शन मोल्डिंग में भरने की गुणवत्ता को कैसे प्रभावित करते हैं?
- 4. इंजेक्शन दबाव अनुकूलन दोषों को कैसे कम कर सकता है?
- 5. मैं अपने कूलिंग टाइम मैनेजमेंट को कैसे सुधार सकता हूँ?
- 6. मोल्ड प्रवाह विश्लेषण उत्पादन क्षमता को कैसे बढ़ा सकता है?
- 7. निष्कर्ष
मोल्ड प्रवाह विश्लेषण क्या है और यह महत्वपूर्ण क्यों है?
क्या आपने कभी सोचा है कि निर्माता यह कैसे जाँचते हैं कि उनके द्वारा बनाया गया प्रत्येक प्लास्टिक भाग उत्तम है? मोल्ड प्रवाह विश्लेषण उत्तर देता है। यह उपकरण इंजेक्शन मोल्डिंग प्रक्रिया को अनुकूलित करता है। यह गुणवत्ता की भी गारंटी देता है। इसके प्रयोग से कार्यक्षमता में सुधार होता है। यह सचमुच मायने रखता है!
मोल्ड फ्लो एनालिसिस (एमएफए) गेट प्लेसमेंट, रनर सिस्टम और कूलिंग विधियों को अनुकूलित करने, उच्च गुणवत्ता वाले उत्पादों को सुनिश्चित करने और दोषों को कम करने के लिए इंजेक्शन मोल्डिंग में कंप्यूटर सिमुलेशन का उपयोग करता है।
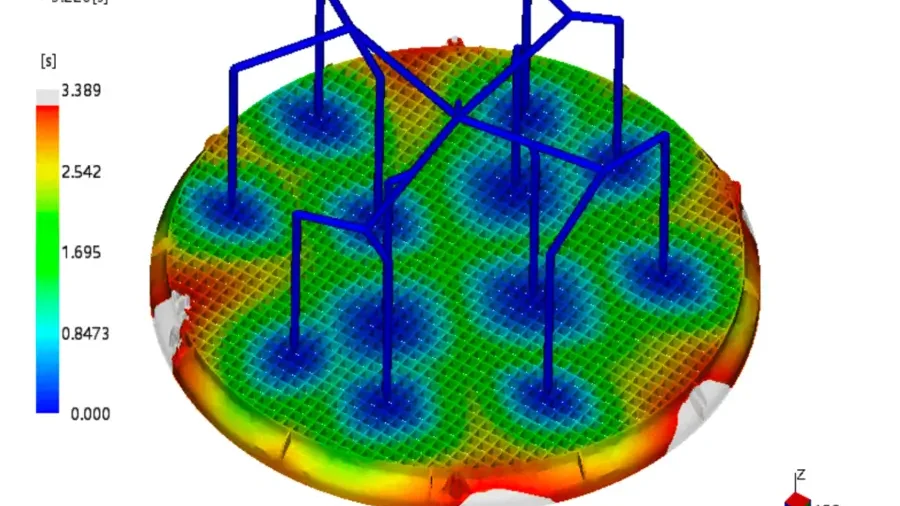
मोल्ड फ्लो एनालिसिस (एमएफए) एक सिमुलेशन तकनीक है जो इंजेक्शन मोल्डिंग प्रक्रिया में महत्वपूर्ण भूमिका निभाती है। यह डिजाइनरों को यह अनुमान लगाने की अनुमति देता है कि पिघला हुआ प्लास्टिक एक सांचे के माध्यम से कैसे बहता है, जिससे इष्टतम भराई, शीतलन और जमना सुनिश्चित होता है। एमएफए को समझने से लागत कम करते हुए उत्पादन की गुणवत्ता में उल्लेखनीय वृद्धि हो सकती है।
गेट स्थान एवं संख्या का महत्व
एमएफए का एक महत्वपूर्ण पहलू गेट स्थान और संख्या का । एक अनुकूलित गेट स्थान यह सुनिश्चित करता है कि पिघल गुहा को समान रूप से भरता है, खासकर जटिल ज्यामितीय आकृतियों में। उदाहरण के लिए, पतले और मोटे दोनों वर्गों के साथ प्लास्टिक के हिस्से का निर्माण करते समय, गेट को पतली दीवार वाले क्षेत्र के करीब रखने से बेहतर प्रवाह प्राप्त करने में मदद मिलती है।
एक प्रोजेक्ट में, मैंने गेट को प्लास्टिक के एक हिस्से के पतले हिस्से के पास रखा। इससे हमें सही प्रवाह मिला और परिणाम में वास्तव में सुधार हुआ।
स्थान के अलावा, एमएफए यह भी संकेत दे सकता है कि एकाधिक द्वारों की आवश्यकता है या नहीं। उदाहरण के लिए, एक कार के डैशबोर्ड को उसकी बड़ी गुहा में एक समान भराव सुनिश्चित करने के लिए कई द्वारों की आवश्यकता हो सकती है। इस अनुकूलन के परिणामस्वरूप अंततः दोष कम होते हैं और उत्पाद की गुणवत्ता बेहतर होती है।
रनर सिस्टम पैरामीटर्स
प्लास्टिक सामग्री के प्रवाह में रनर प्रणाली महत्वपूर्ण भूमिका निभाती है । एमएफए सही धावक आकार और आकार का , जो प्रवाह प्रतिरोध को प्रभावित करता है। एक गोल धावक में आमतौर पर ट्रैपेज़ॉइडल या यू-आकार वाले धावकों की तुलना में कम प्रतिरोध होता है।
धावक आकार | प्रवाह प्रतिरोध | उपयुक्त अनुप्रयोग |
---|---|---|
गोल | कम | सामान्य प्रयोजन |
समलम्बाकार | मध्यम | अलग-अलग मोटाई वाले जटिल हिस्से |
यू आकार | उच्च | उच्च मात्रा में उत्पादन |
इसके अलावा, एमएफए यह सुनिश्चित करता है कि रनर डिज़ाइन मल्टी-कैविटी मोल्ड्स में संतुलित हैं, जिससे प्रत्येक कैविटी को एक साथ भरने में मदद मिलती है। मुझे प्लास्टिक बोतल के ढक्कनों से संबंधित एक परियोजना याद आती है जहां एकरूपता बनाए रखना आवश्यक था; हमें उन्हें एक ही बार में भरने की आवश्यकता थी।
इंजेक्शन दबाव और गति अनुकूलन
एमएफए मोल्ड गुहा के भीतर प्रवाह प्रतिरोध का विश्लेषण करके इंजेक्शन दबाव अनुकूलन को यदि दबाव बहुत अधिक है, तो फ्लैश और डिमोल्डिंग चुनौतियां जैसी समस्याएं उत्पन्न हो सकती हैं, जबकि बहुत कम दबाव के कारण शॉर्ट शॉट हो सकते हैं। इंजेक्शन दबाव को अनुकूलित करना एमएफए का एक और महत्वपूर्ण सबक है; पतली दीवार वाले इलेक्ट्रॉनिक मामलों के लिए सही दबाव निर्धारित करना महत्वपूर्ण था।
इसके अलावा, उत्पादों पर उच्च गुणवत्ता वाली फिनिश प्राप्त करने के लिए इंजेक्शन की गति को विभिन्न गतियाँ प्रवाह के मोर्चे को प्रभावित करती हैं; कारों जैसे दिखने में आकर्षक हिस्सों के लिए, एमएफए सिमुलेशन ने मुझे दोषों के बिना सही सतहों के लिए गति की सलाह दी।
दबाव और समय डालना
शीतलन संकोचन की भरपाई के लिए भरने के बाद होल्डिंग चरण महत्वपूर्ण है। मोल्ड भरने के बाद, यह चरण शीतलन के दौरान सिकुड़न की भरपाई करता है; मैंने आवश्यक होल्डिंग दबाव की ।
उचित धारण समय भी उतना ही आवश्यक है; दीवार की मोटाई और सामग्री गुणों के आधार पर, एमएफए उत्पादन चक्र को अनावश्यक रूप से लंबा किए बिना अखंडता सुनिश्चित करने के लिए इष्टतम समय की गणना करता है।
शीतलन समय और सिस्टम पैरामीटर
अंत में, एमएफए शीतलन प्रक्रियाओं के दौरान तापमान वितरण का विश्लेषण करके
शीतलन समय को यह कदम आंशिक विरूपण को रोकने के साथ-साथ उत्पादन दक्षता बढ़ाने में महत्वपूर्ण रहा है; एक खिलौना परियोजना के दौरान गुणवत्ता बनाए रखते हुए शीतलन समय को कम करने से उत्पादन में काफी वृद्धि हुई। एमएफए बड़े हिस्सों में समान शीतलन सुनिश्चित करने के लिए शीतलन पाइपों के लेआउट, व्यास और प्रवाह दर का मूल्यांकन करके शीतलन प्रणालियों को डिजाइन करने में भी सहायता करता है - एक प्रभावी शीतलन प्रणाली विकृति को रोकती है जो मैंने पिछली परियोजना चुनौतियों के माध्यम से सीखी थी।
हमारे डिजाइन और उत्पादन प्रक्रियाओं में मोल्ड फ्लो विश्लेषण को एकीकृत करने से उत्पाद की गुणवत्ता बढ़ती है जबकि अपशिष्ट कम होता है और समग्र दक्षता बढ़ती है।
मोल्ड प्रवाह विश्लेषण इंजेक्शन मोल्डिंग दक्षता में सुधार करता है।सत्य
एमएफए प्लास्टिक प्रवाह की भविष्यवाणी करके, दक्षता बढ़ाकर और उत्पादन में दोषों को कम करके प्रक्रियाओं को अनुकूलित करता है।
मोल्ड फ्लो विश्लेषण में एकाधिक गेट अनावश्यक हैं।असत्य
एमएफए अक्सर बड़ी गुहाओं में एक समान भराव सुनिश्चित करने के लिए कई द्वारों की आवश्यकता को इंगित करता है, जो गुणवत्ता के लिए महत्वपूर्ण है।
गेट का स्थान इंजेक्शन मोल्डिंग को कैसे प्रभावित करता है?
क्या आपने कभी सोचा कि इंजेक्शन मोल्डिंग में गेट की स्थिति प्रक्रिया को कैसे बदल देती है? यह सचमुच दिलचस्प है! आइए जानें कि यह महत्वपूर्ण विवरण हमारे कार्यों और हम जो उत्पादन करते हैं उसकी गुणवत्ता पर कैसे प्रभाव डालता है।
इंजेक्शन मोल्डिंग में गेट का स्थान पिघल प्रवाह, भरने की दक्षता और दोष दर को प्रभावित करता है। इसे अनुकूलित करने से पार्ट की गुणवत्ता बढ़ती है और उत्पादन संबंधी समस्याएं कम होती हैं।
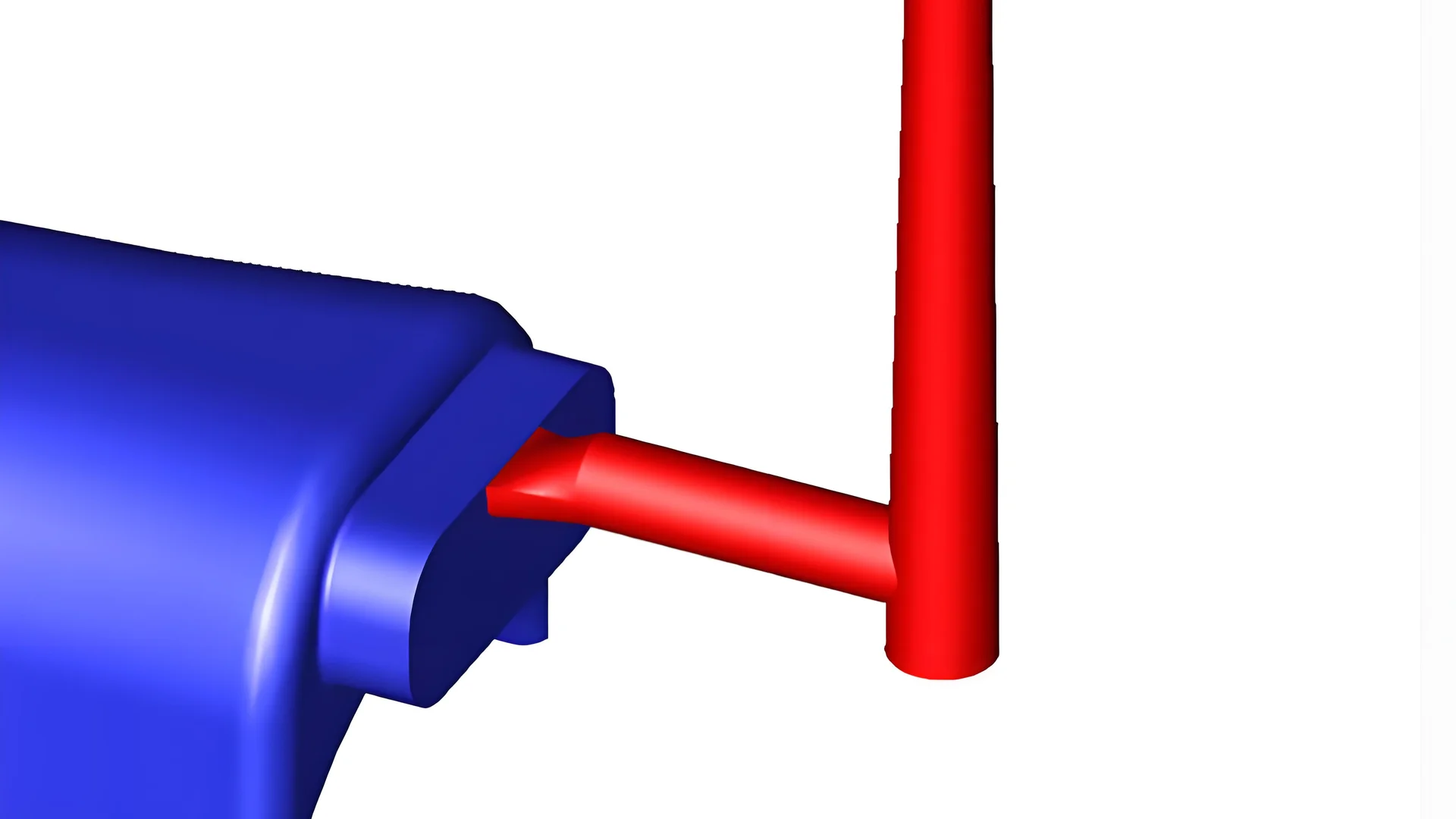
इंजेक्शन मोल्डिंग में गेट स्थान को समझना
इंजेक्शन मोल्डिंग में गेट प्लेसमेंट हमारे मोल्ड किए गए हिस्सों को आकार देता है। मुझे एक परियोजना याद है जहां गेट की स्थिति ने अंतिम उत्पाद को पूरी तरह से बदल दिया। सही गेट पिघले प्रवाह, भरने की क्षमता और दोष दर को बहुत प्रभावित करता है। अच्छा अनुकूलन भाग की गुणवत्ता में सुधार करता है और उत्पादन संबंधी समस्याओं को कम करता है। हर डिज़ाइनर यही चाहता है.
गेट स्थान को अनुकूलित करने से प्रवाह भी सुनिश्चित होता है और शॉर्ट शॉट या एयर ट्रैप जैसे दोषों से बचा जा सकता है। एक बार, मैंने मोटे और पतले दोनों खंडों वाले एक जटिल भाग पर काम किया। गेट को पतले क्षेत्र के पास लगाने से तेजी से भरने में मदद मिली, जिससे फंसी हुई हवा की परेशानी से बचा जा सका।
गेट संख्या समायोजन का महत्व
कभी-कभी, एक गेट पर्याप्त नहीं होता, विशेषकर बड़े या जटिल आकार के लिए। मोल्ड प्रवाह विश्लेषण यह तय करने में महत्वपूर्ण भूमिका निभाता है कि एकाधिक द्वार आवश्यक हैं या नहीं।
एक कार डैशबोर्ड पर विचार करें जहां एक समान पिघल भरना महत्वपूर्ण है। पूरे सांचे में लगातार गुणवत्ता सुनिश्चित करने के लिए अक्सर गेटों की बढ़ी हुई संख्या की निम्नलिखित तालिका इस अवधारणा को दर्शाती है:
भाग प्रकार | अनुशंसित गेट्स | एकाधिक द्वारों का कारण |
---|---|---|
कार डैशबोर्ड | 2-4 | एक समान पिघला हुआ भराव सुनिश्चित करता है |
प्लास्टिक बोतल के ढक्कन | 1-2 | सरलीकृत आकार एकल गेट की अनुमति देता है |
रनर सिस्टम पैरामीटर्स
रनर सिस्टम का डिज़ाइन बहुत मायने रखता है क्योंकि यह तय करता है कि गेट से कैविटी तक पिघल कितनी प्रभावी ढंग से यात्रा करती है। आकार और आकार प्रवाह प्रतिरोध और दबाव हानि को प्रभावित करते हैं। आम तौर पर, गोल धावकों को उनके कम प्रवाह प्रतिरोध के लिए पसंद किया जाता है।
मोल्ड प्रवाह विश्लेषण दबाव हानि के बिना सुचारू संक्रमण के लिए इष्टतम धावक मापदंडों का चयन करने में मदद करता है। यह महत्वपूर्ण है, विशेष रूप से मल्टी-कैविटी सांचों में जहां समान भरने की दर महत्वपूर्ण है।
इंजेक्शन दबाव और गति नियंत्रण
गेट का स्थान मोल्डिंग प्रक्रिया के दौरान उपयोग किए जाने वाले इंजेक्शन दबाव और गति को भी प्रभावित करता है। विभिन्न बिंदुओं पर प्रवाह प्रतिरोध का विश्लेषण करने से मुझे फ्लैश या डिमोल्डिंग कठिनाइयों जैसे दोषों को रोकने के लिए दबावों को अनुकूलित करने की अनुमति मिली।
इंजेक्शन की गति को समायोजित करना भी महत्वपूर्ण है; कार के इंटीरियर जैसे उच्च-गुणवत्ता वाले हिस्से बनाते समय, इंजेक्शन की गति को नियंत्रित करने से भद्दे प्रवाह के निशानों को रोका जा सकता है।
दबाव और समय सेटिंग्स को दबाए रखें
भरने के बाद, सही होल्ड प्रेशर महत्वपूर्ण है। मैंने उच्च-परिशुद्धता वाले गियर के साथ काम किया, जहां पकड़ दबाव की भविष्यवाणी करने से सिकुड़न के निशान और आयामी मुद्दों को कम करने में मदद मिली।
उचित होल्ड समय निर्धारित करना एक संतुलनकारी कार्य है; बहुत छोटा होने के कारण सिकुड़न के निशान दिखाई देते हैं जबकि बहुत लंबा खिंचाव चक्र को अनावश्यक रूप से समय देता है। निम्नलिखित तालिका दीवार की मोटाई के आधार पर इष्टतम पकड़ समय की रूपरेखा देती है:
दीवार की मोटाई (मिमी) | अनुशंसित होल्ड समय (सेकंड) |
---|---|
< 1 | 5-7 |
1-3 | 8-10 |
> 3 | 12-15 |
शीतलन समय अनुकूलन
अंत में, शीतलन समय और सिस्टम पैरामीटर बहुत मायने रखते हैं। क्या आप जानते हैं कि गेट का स्थान शीतलन दक्षता को प्रभावित करता है? मैंने गुणवत्ता खोए बिना दक्षता बढ़ाने के लिए एक समान कूलिंग के लिए कूलिंग पाइप लेआउट डिज़ाइन किया है?
मोल्ड प्रवाह विश्लेषण के माध्यम से शीतलन समय को अनुकूलित करने से भाग की अखंडता से समझौता किए बिना उत्पादन दक्षता में काफी वृद्धि हो सकती है।
उदाहरण के लिए, छोटे प्लास्टिक के खिलौने उचित गुणवत्ता सुनिश्चित करते हुए कम ठंडा समय से लाभान्वित हो सकते हैं।
निष्कर्ष में, यह जानना कि गेट का स्थान कई कारकों को कैसे प्रभावित करता है, भाग की गुणवत्ता और उत्पादन दक्षता को अनुकूलित करने के लिए आवश्यक है। प्रभावी गेट प्लेसमेंट रणनीतियों के बारे में अधिक जानने के लिए, इस विस्तृत गाइड 1 ।
गेट का स्थान इंजेक्शन मोल्डिंग में पिघले प्रवाह पैटर्न को प्रभावित करता है।सत्य
गेटों का स्थान सीधे तौर पर प्रभावित करता है कि पिघला हुआ पदार्थ सांचे में कैसे भरता है, जिससे समग्र भाग की गुणवत्ता और दक्षता प्रभावित होती है।
जटिल मोल्ड डिज़ाइन के लिए एकाधिक गेट अनावश्यक हैं।असत्य
जटिल ज्यामिति में, इंजेक्शन प्रक्रिया के दौरान एकसमान भराव सुनिश्चित करने और दोषों को कम करने के लिए कई द्वार आवश्यक हो सकते हैं।
रनर सिस्टम इंजेक्शन मोल्डिंग में भरने की गुणवत्ता को कैसे प्रभावित करते हैं?
क्या आपने कभी सोचा है कि एक छोटा सा हिस्सा वास्तव में आपके ढाले हुए टुकड़ों की गुणवत्ता को कैसे बदल सकता है? आइए रनर सिस्टम पर नजर डालें और देखें कि वे इंजेक्शन मोल्डिंग में कितने महत्वपूर्ण हैं। ये सिस्टम सांचों को ठीक से भरने में मदद करते हैं।
इंजेक्शन मोल्डिंग में रनर सिस्टम सामग्री प्रवाह, दबाव वितरण और शीतलन को प्रभावित करते हैं। कम दोष वाले उच्च गुणवत्ता वाले भागों के लिए उचित गेट प्लेसमेंट, रनर आकार और इंजेक्शन सेटिंग्स आवश्यक हैं।
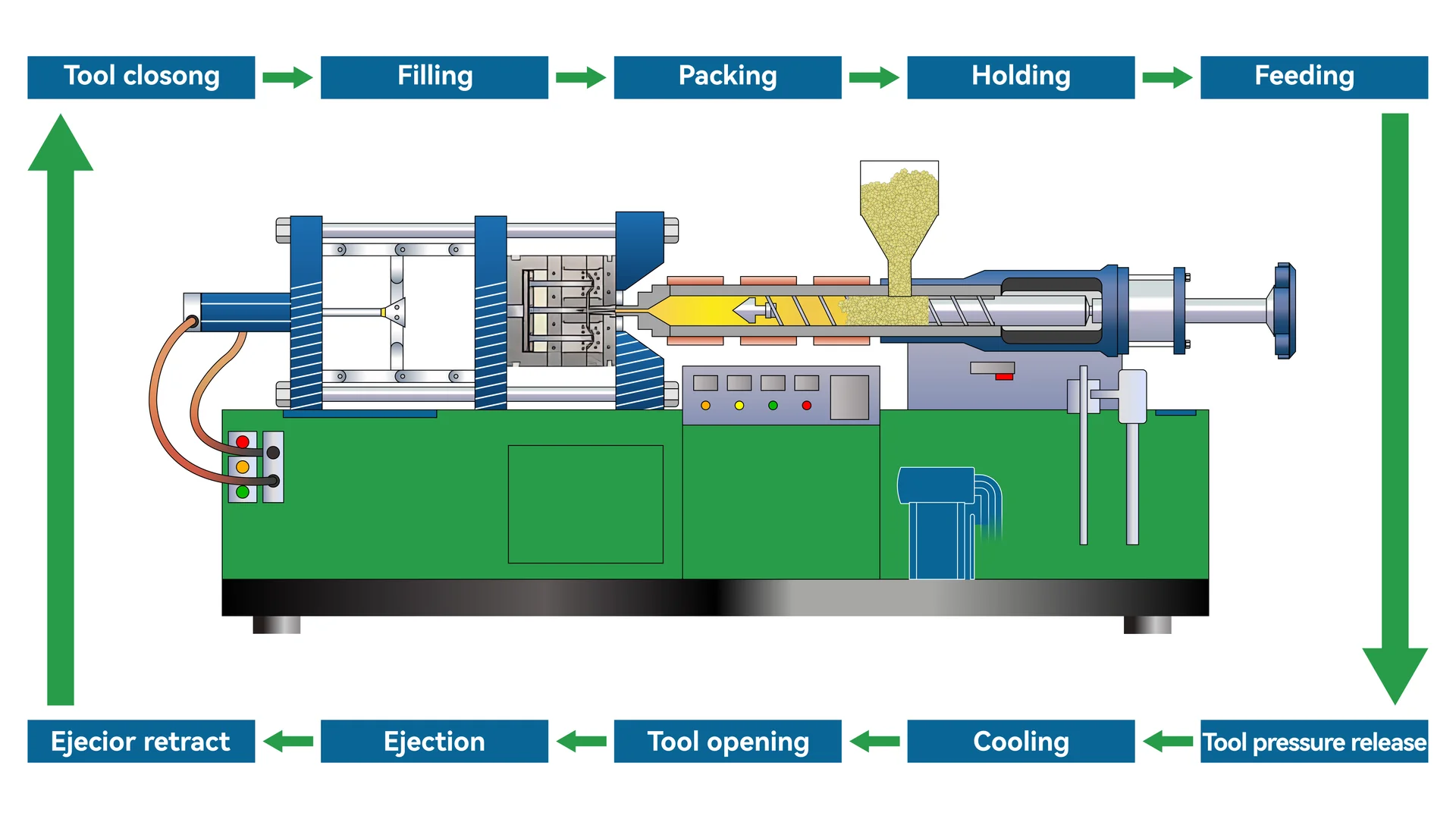
रनर सिस्टम को समझना
रनर सिस्टम इंजेक्शन मोल्डिंग प्रक्रिया में महत्वपूर्ण घटक हैं जो यह सुनिश्चित करने में महत्वपूर्ण भूमिका निभाते हैं कि पिघला हुआ मोल्ड गुहाओं को कुशलतापूर्वक और प्रभावी ढंग से भरता है। रनर सिस्टम का डिज़ाइन प्लास्टिक घटकों की समग्र भरने की गुणवत्ता को प्रभावित कर सकता है।
1. गेट स्थान और संख्या
पिघले हुए वितरण के लिए गेट स्थान को अनुकूलित करना आवश्यक है। जटिल ज्यामिति के लिए, मोल्ड प्रवाह विश्लेषण पिघल के लिए सर्वोत्तम प्रवेश बिंदु निर्धारित कर सकता है।
- उदाहरण : किसी भाग के पतले-दीवार वाले खंड में, इस क्षेत्र के पास गेट लगाने से त्वरित भराव सुनिश्चित होता है, जिससे शॉर्ट शॉट या एयर ट्रैप जैसे दोषों की संभावना कम हो जाती है।
- गेट संख्या : बड़े हिस्सों में एक समान भराव प्राप्त करने के लिए गेटों की संख्या बढ़ाना आवश्यक हो सकता है।
2. धावक प्रणाली पैरामीटर
धावकों का आकार और आकार प्रवाह प्रतिरोध को प्रभावित करते हैं। धावकों को विभिन्न आकारों में डिज़ाइन किया जा सकता है:
धावक आकार | प्रवाह प्रतिरोध | क्षमता |
---|---|---|
गोल | कम | उच्च |
समलम्बाकार | मध्यम | मध्यम |
यू आकार | उच्च | कम |
सही आकार चुनना भी उतना ही महत्वपूर्ण है। एक धावक जो बहुत संकीर्ण है, दबाव हानि का कारण बन सकता है, जबकि जो बहुत चौड़ा है वह सामग्री बर्बाद कर सकता है।
3. इंजेक्शन दबाव और गति
मोल्ड प्रवाह विश्लेषण का उपयोग करके, डिजाइनर फ्लैश या डिमोल्डिंग कठिनाइयों जैसे मुद्दों से बचने के लिए इंजेक्शन दबाव को अनुकूलित कर सकते हैं।
- इंजेक्शन गति नियंत्रण : सतह की गुणवत्ता बनाए रखने के लिए सही गति महत्वपूर्ण है, विशेष रूप से ऑटोमोटिव इंटीरियर जैसे सौंदर्य भागों के लिए। विभिन्न गति पर प्रवाह मोर्चों का विश्लेषण करने से प्रवाह चिह्न जैसे दोषों से बचने के लिए इष्टतम गति निर्धारित करने में मदद मिलती है।
4. दबाव बनाए रखना और समय
गुहा भर जाने के बाद, दबाव बनाए रखना शीतलन संकोचन की भरपाई करता है। ऐसे:
- होल्डिंग दबाव निर्धारण : मोल्ड प्रवाह विश्लेषण का उपयोग करके, डिजाइनर सिकुड़न के निशान को कम करने के लिए आवश्यक होल्डिंग दबाव का अनुमान लगा सकते हैं।
- होल्डिंग समय निर्धारण : इष्टतम होल्डिंग समय की गणना शीतलन के दौरान प्रभावी दबाव क्षतिपूर्ति, दक्षता और लागत को संतुलित करना सुनिश्चित करती है।
5. शीतलन समय और शीतलन प्रणाली पैरामीटर
शीतलन समय सीधे उत्पादन क्षमता को प्रभावित करता है:
- शीतलन समय अनुकूलन : सटीक तापमान वितरण विश्लेषण के माध्यम से शीतलन समय को कम करने से गुणवत्ता से समझौता किए बिना उत्पादकता में वृद्धि हो सकती है।
- शीतलन प्रणाली पैरामीटर समायोजन : शीतलन पाइपों के लेआउट और प्रवाह दर को विरूपण को रोकने के लिए समान शीतलन के लिए सावधानीपूर्वक डिजाइन किया जाना चाहिए।
संक्षेप में, रनर सिस्टम पिघल प्रवाह, दबाव वितरण और शीतलन दक्षता जैसे विभिन्न कारकों को प्रभावित करके भरे हुए सांचों की गुणवत्ता निर्धारित करने में महत्वपूर्ण भूमिका निभाते हैं। सावधानीपूर्वक विश्लेषण के माध्यम से इन तत्वों को अनुकूलित करके, डिज़ाइनर दोषों को कम करते हुए उत्पाद की गुणवत्ता में उल्लेखनीय वृद्धि कर सकते हैं।
रनर सिस्टम इंजेक्शन मोल्डिंग में पिघले प्रवाह को सीधे प्रभावित करते हैं।सत्य
कुशल पिघल प्रवाह सुनिश्चित करने के लिए रनर सिस्टम का डिज़ाइन महत्वपूर्ण है, जो मोल्ड किए गए भागों की भरने की गुणवत्ता को प्रभावित करता है।
गेट संख्या बढ़ाने से हमेशा भरने की गुणवत्ता में सुधार होता है।असत्य
हालाँकि अधिक गेट मदद कर सकते हैं, लेकिन वे हमेशा भरने की गुणवत्ता में सुधार नहीं कर सकते हैं और अगर सही ढंग से अनुकूलित नहीं किया गया तो अक्षमताएं हो सकती हैं।
इंजेक्शन दबाव अनुकूलन दोषों को कैसे कम कर सकता है?
क्या आप परेशान महसूस करते हैं क्योंकि दोषों ने आपके पूरी तरह से डिज़ाइन किए गए उत्पाद को खराब कर दिया है? मैंने भी ऐसा महसूस किया है. दोषों को कम करना वास्तव में मायने रखता है। इंजेक्शन दबाव को अनुकूलित करने से उत्पाद की गुणवत्ता में बहुत सुधार होता है। यह परिवर्तन संभवतः कष्टप्रद दोषों को कम करने में मदद करता है।
मोल्डिंग में इंजेक्शन दबाव को अनुकूलित करने से लगातार पिघला हुआ प्रवाह और नियंत्रित दबाव सुनिश्चित होता है, शॉर्ट शॉट्स और सतह की खामियों जैसे दोष कम होते हैं, जिससे उत्पाद की गुणवत्ता में वृद्धि होती है। इन सुधारों के लिए शीतलन समय को समायोजित करना महत्वपूर्ण है।
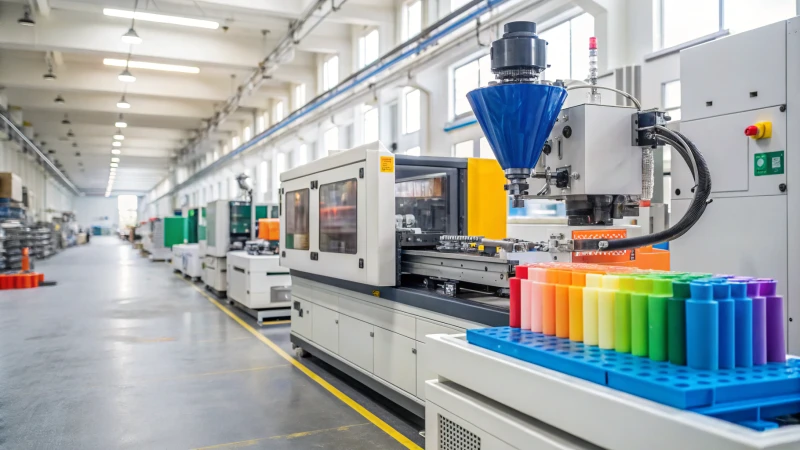
इंजेक्शन दबाव अनुकूलन को समझना
इंजेक्शन मोल्डिंग प्रक्रिया में दोषों को कम करने के लिए इंजेक्शन दबाव को अनुकूलित करना बहुत महत्वपूर्ण है। जिस दबाव पर पिघले हुए प्लास्टिक को सांचे में इंजेक्ट किया जाता है, उसका सावधानीपूर्वक विश्लेषण और समायोजन करके, निर्माता बेहतर भरण पैटर्न प्राप्त कर सकते हैं और शॉर्ट शॉट्स, रिक्तियां और रैपिंग जैसे सामान्य दोषों को कम कर सकते हैं।
उदाहरण के लिए, सही इंजेक्शन दबाव लागू करने से यह सुनिश्चित होता है कि पिघल मोल्ड गुहा को समान रूप से भरता है, खासकर जटिल ज्यामिति में। ऐसे मामलों में जहां हिस्सों में पतली और मोटी दोनों तरह की दीवारें होती हैं, मैंने कुशल फिलिंग सक्षम करने के लिए गेट को पतले क्षेत्रों के पास रखना सीखा। इन इष्टतम स्थानों की पहचान करने में मोल्ड प्रवाह विश्लेषण उपकरण मेरा गुप्त हथियार बन गए।
दोष दर को प्रभावित करने वाले प्रमुख कारक
- इंजेक्शन दबाव
सही दबाव ढूँढना महत्वपूर्ण है। बहुत अधिक दबाव के कारण हटाने के दौरान फ्लैश और समस्याएँ होती हैं। बहुत कम दबाव के परिणामस्वरूप छोटे शॉट और खालीपन आते हैं।
दबाव का स्तर | संभावित दोष |
---|---|
बहुत ऊँचा | फ़्लैश, डिमोल्डिंग कठिनाइयाँ |
बहुत कम | लघु शॉट्स, शून्यता |
-
इंजेक्शन गति नियंत्रण
इंजेक्शन की गति बहुत महत्वपूर्ण है। कार के आंतरिक भागों पर काम करते समय गलत गति के कारण प्रवाह के निशान पड़ गए। मोल्ड प्रवाह विश्लेषण पर आधारित समायोजनों ने हमारे ग्राहकों को संतुष्ट करने वाली चिकनी फिनिश बनाकर इसमें सुधार किया। -
होल्डिंग दबाव और समय
भरने के बाद, ठंडा होने पर सिकुड़न को नियंत्रित करने के लिए सही होल्डिंग दबाव आवश्यक है। बहुत कम दबाव सिकुड़न के निशान देता है जबकि बहुत अधिक दबाव चक्र के समय और लागत को बढ़ाता है।- इष्टतम धारण दबाव : शीतलन के दौरान दोषों को रोकने के लिए सही दबाव बनाए रखता है।
- परिकलित होल्डिंग समय : अनावश्यक रूप से उत्पादन में देरी किए बिना पर्याप्त शीतलन समय की अनुमति देता है।
-
शीतलन समय अनुकूलन
शीतलन हर चीज़ को ठोस बनाता है; ठीक ही होगा! मैंने एक बार यह कदम उठाया और भागों को विकृत होते देखा! मोल्ड प्रवाह विश्लेषण का उपयोग करने से मुझे सही शीतलन समय का पता चला जिससे भागों की सटीकता बनी रही और दक्षता में सुधार हुआ।- ठंडा करने का समय कम हो गया : उत्पादन की गति बढ़ जाती है।
- समान तापमान वितरण : विरूपण जोखिम को कम करता है।
अनुकूलन तकनीकों के व्यावहारिक अनुप्रयोग
इन तकनीकों को लागू करने से उत्पाद की गुणवत्ता में उल्लेखनीय सुधार हुआ। उदाहरण के लिए, कार के डैशबोर्ड को डिजाइन करने में, एकसमान फिलिंग हासिल करने और असमान दबाव वितरण से होने वाले दोषों से बचने के लिए कई गेट महत्वपूर्ण थे।
संक्षेप में, इंजेक्शन दबाव अनुकूलन पर ध्यान केंद्रित करने से इंजेक्शन मोल्डिंग पर मेरा दृष्टिकोण बदल गया। यह आश्चर्यजनक है कि कैसे ये रणनीतियाँ उत्पाद की गुणवत्ता में उल्लेखनीय सुधार करते हुए दोष दर में कटौती करती हैं। इंजेक्शन मोल्डिंग तकनीक देखें ।
इंजेक्शन दबाव, गति और शीतलन से संबंधित प्रत्येक पैरामीटर की लगातार जांच करके, मैंने अपनी प्रक्रियाओं को सुव्यवस्थित किया है जिससे हम उच्च गुणवत्ता वाले प्लास्टिक भागों को बहुत कुशलता से वितरित कर सकते हैं।
इंजेक्शन दबाव को अनुकूलित करने से मोल्डिंग में शॉर्ट शॉट कम हो जाते हैं।सत्य
इंजेक्शन दबाव को उचित रूप से समायोजित करने से पिघला हुआ प्रवाह भी सुनिश्चित होता है, जिससे इंजेक्शन मोल्डिंग प्रक्रिया के दौरान शॉर्ट शॉट्स की घटना काफी कम हो जाती है।
उच्च इंजेक्शन गति हमेशा सतह की गुणवत्ता में सुधार करती है।असत्य
उच्च इंजेक्शन गति अशांति पैदा कर सकती है, जिससे गुणवत्ता में सुधार के बजाय सतह की खामियां पैदा हो सकती हैं, जिससे यह दावा गलत हो जाता है।
मैं अपने कूलिंग टाइम मैनेजमेंट को कैसे सुधार सकता हूँ?
विनिर्माण में कूलिंग टाइम का प्रबंधन करना बहुत महत्वपूर्ण है। यह इंजेक्शन मोल्डिंग के लिए विशेष रूप से सच है। मैं कुछ सर्वोत्तम प्रथाएँ साझा करना चाहता हूँ। इनसे न केवल उत्पादन की गति में सुधार होता है बल्कि उत्पादों की गुणवत्ता में भी सुधार होता है। आइए इन विचारों को एक साथ खोजें!
गेट स्थानों में सुधार करके, रनर सेटिंग्स को समायोजित करके, इंजेक्शन मापदंडों को नियंत्रित करके, होल्डिंग दबाव और समय को सटीक रूप से सेट करके और कूलिंग सिस्टम को परिष्कृत करके विनिर्माण में शीतलन समय को अनुकूलित करें।
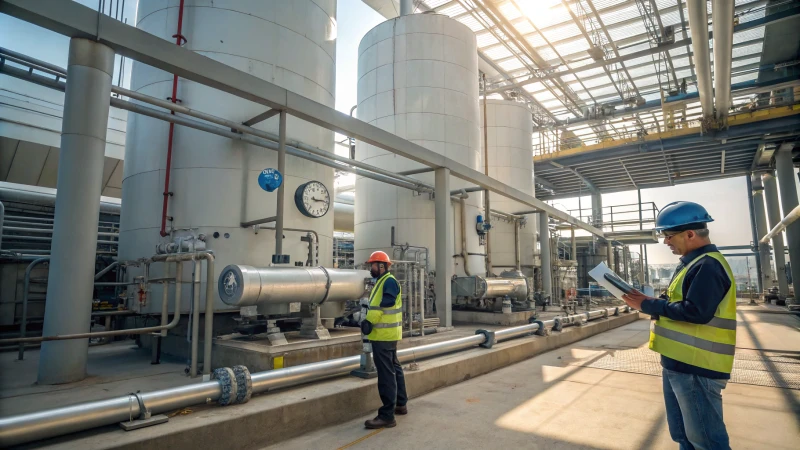
कूलिंग टाइम मैनेजमेंट को समझना
कूलिंग टाइम मैनेजमेंट सिर्फ एक तकनीकी जरूरत नहीं है। यह शीर्ष उत्पाद बनाने का एक महत्वपूर्ण हिस्सा है जिसे मैंने एक डिजाइनर के रूप में महत्व देना सीखा है। मैंने इसे एक बार नजरअंदाज कर दिया और बाद में देखा कि इसका मेरे काम पर कितना असर पड़ा। अच्छी कूलिंग से दक्षता और उत्पाद की गुणवत्ता बढ़ती है। हमारे जैसे निर्माता गुणवत्ता खोए बिना उत्पादन समय कम करने और पैसे बचाने का प्रबंधन करते हैं।
कूलिंग टाइम मैनेजमेंट में अच्छा होने के लिए, कुछ सर्वोत्तम अभ्यास वास्तव में मदद करते हैं:
1. गेट स्थान और संख्या को अनुकूलित करें
उचित शीतलन के लिए गेट का स्थान और सांचे में गिनती महत्वपूर्ण है।
-
गेट स्थान अनुकूलन : मोल्ड प्रवाह विश्लेषण ने मुझे सर्वोत्तम गेट स्पॉट दिखाए। इसने साँचे की गुहिका को समान रूप से भरना सुनिश्चित किया। जटिल आकृतियों के लिए, पतले खंडों के पास गेट लगाने से भरने में आसानी होती है और दोष कम होते हैं।
-
गेट नंबर समायोजन : कभी-कभी बड़े हिस्सों को एक से अधिक गेट की आवश्यकता होती है। कार के डैशबोर्ड पर काम करते समय, हमने समान भराव सुनिश्चित करने के लिए कई गेटों का उपयोग किया। इस दृष्टिकोण ने हमारे उत्पादों को सुसंगत रखते हुए, शीतलन विविधताओं में महत्वपूर्ण रूप से कटौती की।
2. रनर सिस्टम पैरामीटर समायोजित करें
धावकों ने प्लास्टिक को पिघलाकर साँचे में ढाला। उनका डिज़ाइन शीतलन समय को बहुत प्रभावित करता है।
धावक आकार | प्रवाह प्रतिरोध | अनुशंसित अनुप्रयोग |
---|---|---|
गोल | कम | अधिकांश अनुप्रयोग |
समलम्बाकार | मध्यम | जटिल आकार |
यू आकार | उच्च | बड़े हिस्से |
- संतुलित डिज़ाइन : मल्टी-कैविटी साँचे में, सभी कैविटी को एक साथ भरने के लिए एक संतुलित रनर सिस्टम महत्वपूर्ण है। मोल्ड प्रवाह विश्लेषण ने रनर डिज़ाइन को समायोजित करने में मदद की, जो समान बोतल कैप बनाने के लिए महत्वपूर्ण था।
3. इंजेक्शन दबाव और गति को अनुकूलित करें
इंजेक्शन का दबाव और गति न केवल भरने बल्कि शीतलन दर पर भी प्रभाव डालती है।
-
इंजेक्शन दबाव अनुकूलन : एक परियोजना में, प्रवाह प्रतिरोध का आकलन करने से इष्टतम इंजेक्शन दबाव निर्धारित करने में मदद मिली। उच्च दबाव के कारण फ्लैश जैसे दोष उत्पन्न हुए; कम दबाव के कारण अधूरा भराव हुआ। पतली दीवार वाले इलेक्ट्रॉनिक भागों के लिए, सटीक बदलाव मायने रखते हैं।
-
इंजेक्शन गति नियंत्रण : बेहतर सतह गुणवत्ता के लिए इंजेक्शन गति को नियंत्रित करना महत्वपूर्ण है। कार्य को बनाए रखते हुए खामियों से बचने के लिए इस गति को समायोजित करना महत्वपूर्ण है।
4. होल्डिंग दबाव और समय निर्धारित करें
गुहा भरने के बाद, सिकुड़न को रोकने के लिए दबाव बनाए रखना महत्वपूर्ण हो जाता है।
-
होल्डिंग दबाव निर्धारण : मोल्ड प्रवाह विश्लेषण आवश्यक होल्डिंग दबाव की भविष्यवाणी करता है। गियर जैसे सटीक टुकड़ों पर सिकुड़न के निशान को कम करने के लिए यह महत्वपूर्ण है; आयामों को सटीक रखने के लिए सही दबाव महत्वपूर्ण है।
-
होल्डिंग समय निर्धारित करना : सही होल्डिंग समय ढूंढना महत्वपूर्ण है; बहुत छोटा होने से दोष उत्पन्न होता है जबकि बहुत लंबा होने से चक्र का समय बढ़ जाता है। सटीक समायोजन के लिए मैं अक्सर दीवार की मोटाई और सामग्री गुणों की जांच करता हूं।
5. शीतलन समय और सिस्टम पैरामीटर अनुकूलन
शीतलन समय को अनुकूलित करने से उत्पादकता में काफी वृद्धि होती है।
-
शीतलन समय अनुकूलन : विस्तृत विश्लेषण ने गुणवत्ता को उच्च रखते हुए न्यूनतम शीतलन समय की गणना करने में मदद की; छोटे खिलौनों को ढालते समय, छोटे चक्रों ने अखंडता खोए बिना दक्षता को बढ़ाया।
-
कूलिंग सिस्टम पैरामीटर्स को समायोजित करें : कूलिंग चैनलों के लेआउट, व्यास और प्रवाह दर को बदलने से तापमान वितरण में भी मदद मिलती है; मैंने देखा कि कैसे स्मार्ट डिज़ाइन कूलिंग के दौरान ख़राब होने से बचाता है।
उन्नत कूलिंग तकनीकों या मोल्ड डिज़ाइन 2 जाँच करें । मुझे अपने अनुभव साझा करने का शौक है - आइए मिलकर अपनी कला में सुधार करें!
गेट स्थान को अनुकूलित करने से मोल्डिंग में शीतलन दक्षता में सुधार होता है।सत्य
रणनीतिक गेट प्लेसमेंट इंजेक्शन मोल्डिंग प्रक्रिया के दौरान समान पिघल वितरण, दोषों को कम करने और शीतलन दक्षता को बढ़ाने को सुनिश्चित करता है।
छोटे ढाले भागों के लिए एकाधिक द्वार अनावश्यक हैं।असत्य
बड़े घटकों के लिए, गुणवत्ता संबंधी समस्याओं को रोकने के लिए एकसमान भराई और लगातार शीतलन प्राप्त करने के लिए कई गेटों का उपयोग करना आवश्यक है।
मोल्ड प्रवाह विश्लेषण उत्पादन क्षमता को कैसे बढ़ा सकता है?
क्या आपने कभी सोचा है कि कारखाने अपने इंजेक्शन मोल्डिंग तरीकों को सही बनाने के लिए कैसे समायोजित करते हैं? मोल्ड फ्लो विश्लेषण (एमएफए) वास्तव में आकर्षक है। यह उद्योग को बदल देता है। यह उपकरण कारखानों को उत्पादन क्षमता में पहले से बेहतर सुधार करने की अनुमति देता है। आइए एक साथ मिलकर इस अद्भुत टूल का अन्वेषण करें!
मोल्ड फ्लो विश्लेषण गेट स्थानों, रनर सिस्टम, इंजेक्शन दबाव और शीतलन समय को अनुकूलित करके, दोषों को कम करने, चक्र समय में सुधार करने और विनिर्माण में उच्च गुणवत्ता वाले आउटपुट सुनिश्चित करके उत्पादन दक्षता को बढ़ाता है।
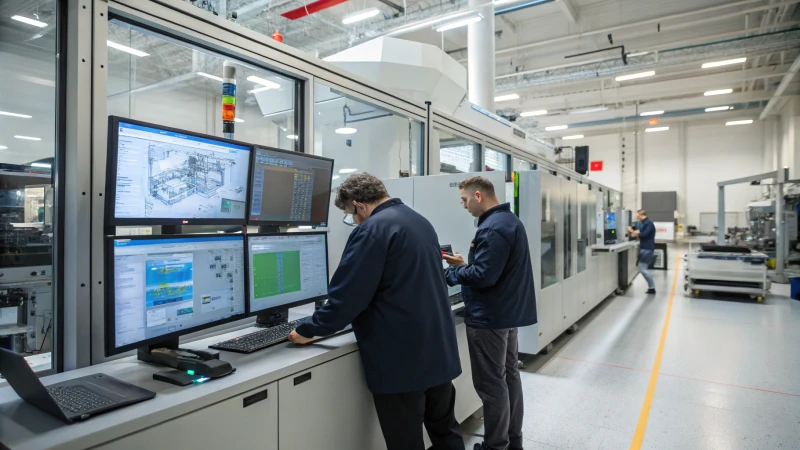
मोल्ड प्रवाह विश्लेषण को समझना
मोल्ड प्रवाह विश्लेषण (एमएफए) एक शक्तिशाली उपकरण है जो निर्माताओं को वास्तविक उत्पादन शुरू होने से पहले इंजेक्शन मोल्डिंग प्रक्रिया का अनुकरण करने की अनुमति देता है। यह तकनीक संभावित दोषों की पहचान करने और उत्पादन दक्षता बढ़ाने के लिए डिज़ाइन मापदंडों को अनुकूलित करने में मदद करती है।
एमएफए का उपयोग करके , डिजाइनर विभिन्न कारकों जैसे पिघल प्रवाह, शीतलन समय और मोल्ड के भीतर दबाव वितरण का विश्लेषण कर सकते हैं। यह पूर्वानुमानित क्षमता डिज़ाइन प्रक्रिया में अधिक सूचित निर्णय लेने की ओर ले जाती है।
गेट स्थान अनुकूलन
गेट का स्थान और संख्या इंजेक्शन मोल्डिंग प्रक्रिया में महत्वपूर्ण भूमिका निभाते हैं।
- गेट स्थान : गेट स्थान को अनुकूलित करने से यह सुनिश्चित होता है कि पिघल गुहा में समान रूप से भर जाता है, जिससे शॉर्ट शॉट या फंसी हवा जैसी समस्याओं को रोका जा सकता है। उदाहरण के लिए, गेट को पतली दीवारों वाले खंडों के करीब रखने से भरने की दक्षता में सुधार होता है। मैंने एक ऐसे प्रोजेक्ट पर काम किया जहां समान पिघला हुआ भराव के लिए गेट लगाना महत्वपूर्ण था। हमारे आइटम के पतले हिस्सों के पास गेट लगाने से शॉर्ट शॉट रुक गए और हवा फंस गई। मैंने यह पाठ कठिन तरीके से सीखा!
- गेट नंबर : बड़े या जटिल हिस्सों के मामले में, कई गेटों का उपयोग करना आवश्यक हो सकता है। उदाहरण के लिए, एक कार डैशबोर्ड को डिज़ाइन करते समय मुझे एक बार पता चला कि एक गेट अपर्याप्त था। एमएफए ने मुझे यह देखने में मदद की कि पिघल को समान रूप से फैलाने के लिए कई द्वारों की आवश्यकता थी, जिससे परिणाम में काफी सुधार हुआ।
रनर सिस्टम पैरामीटर्स
मोल्ड गुहाओं में पिघल के प्रवाह को नियंत्रित करने के लिए रनर प्रणाली आवश्यक है।
पैरामीटर | विवरण | उत्पादन पर प्रभाव |
---|---|---|
धावक आकार | विभिन्न आकार (गोल, यू-आकार) प्रवाह प्रतिरोध को प्रभावित करते हैं। | गोल धावकों में आम तौर पर कम प्रतिरोध होता है, जो सुचारू प्रवाह में सहायता करता है। |
धावक का आकार | व्यास दबाव ड्रॉप को प्रभावित करता है; बहुत संकीर्ण होने से अतिरिक्त दबाव का नुकसान होता है। | प्रवाह दर में दक्षता बनाए रखने के लिए उचित आकार महत्वपूर्ण है। |
एक संतुलित धावक डिज़ाइन यह सुनिश्चित करता है कि सभी गुहाएँ एक साथ भरें, जो बहु-गुहा सांचों में महत्वपूर्ण है। मुझे मल्टी-कैविटी बोतल कैप मोल्ड में रनर सेटिंग्स बदलना स्पष्ट रूप से याद है; एक ही समय में प्रत्येक गुहा को भरना एक आदर्श सिम्फनी का संचालन करने जैसा महसूस हुआ!
इंजेक्शन दबाव और गति नियंत्रण
एक अन्य प्रमुख क्षेत्र जहां मोल्ड प्रवाह विश्लेषण उत्पादन दक्षता को बढ़ाता है वह इंजेक्शन दबाव और गति के अनुकूलन के माध्यम से होता है।
- इंजेक्शन दबाव : प्रवाह प्रतिरोध का विश्लेषण करने से इष्टतम इंजेक्शन दबाव निर्धारित करने में मदद मिलती है, जिससे पूर्ण भरने को सुनिश्चित करने के मुकाबले फ्लैश जैसे दोषों का जोखिम संतुलित हो जाता है। प्रवाह प्रतिरोध की जांच करके, मैंने विभिन्न परियोजनाओं के लिए सर्वोत्तम इंजेक्शन दबाव की खोज की; बहुत अधिक के कारण दोष उत्पन्न हुए जबकि बहुत कम के कारण छोटे शॉट हुए।
- इंजेक्शन गति : उच्च गुणवत्ता वाली सतह फिनिश सुनिश्चित करने के लिए फ्लो फ्रंट उन्नति को विभिन्न गति पर अनुकरण किया जा सकता है, विशेष रूप से ऑटोमोटिव इंटीरियर जैसे सख्त सौंदर्य आवश्यकताओं वाले हिस्सों में महत्वपूर्ण है। सतह की खामियों से बचने के लिए एक ऑटोमोटिव इंटीरियर प्रोजेक्ट को विशिष्ट गति की आवश्यकता होती है; एमएफए ने मुझे अलग-अलग गति का परीक्षण करने और एक आदर्श फिनिश हासिल करने की अनुमति दी।
होल्डिंग दबाव और समय सेटिंग
आयामी सटीकता बनाए रखने और दोषों को कम करने के लिए भरने के बाद उचित होल्डिंग दबाव और समय निर्धारित करना महत्वपूर्ण है।
- होल्डिंग दबाव : पर्याप्त होल्डिंग दबाव शीतलन के दौरान सिकुड़न की भरपाई करता है, जो गियर जैसे उच्च परिशुद्धता वाले घटकों के लिए महत्वपूर्ण है। गियर जैसे उच्च-सटीक भागों के साथ काम करते समय, मैंने सिकुड़न से बचने के लिए सही होल्डिंग दबाव खोजने के लिए एमएफए का उपयोग किया; इसे बिल्कुल फिट देखना बहुत फायदेमंद था।
- होल्डिंग समय : गणना किया गया होल्डिंग समय यह सुनिश्चित करता है कि हिस्से बिना किसी विकृति या सिकुड़न के निशान के समान रूप से ठंडे हों। आदर्श होल्डिंग समय ढूँढना मुश्किल है; यदि बहुत कम समय में दोष दिखाई देते हैं जबकि यदि बहुत लंबे समय में दोष दिखाई देते हैं तो लागत बढ़ जाती है। एमएफए के साथ, मैंने सर्वोत्तम परिणामों तक पहुंचने के लिए डिजाइनों की गणना की।
शीतलन समय और सिस्टम पैरामीटर
मोल्ड प्रवाह विश्लेषण भी शीतलन समय और प्रणालियों को अनुकूलित करने में महत्वपूर्ण योगदान देता है।
- शीतलन समय अनुकूलन : एमएफए तापमान वितरण की भविष्यवाणी करता है और डिजाइनरों को न्यूनतम आवश्यक शीतलन समय की गणना करने की अनुमति देता है जिससे चक्र समय में सुधार होता है। शीतलन समय को अनुकूलित करने से एक बार छोटे प्लास्टिक के खिलौनों के लिए मेरा चक्र बदल गया; न्यूनतम शीतलन समय की गणना करने से वास्तव में भागों की गुणवत्ता को बरकरार रखते हुए दक्षता में वृद्धि हुई है।
- कूलिंग सिस्टम लेआउट : कूलिंग चैनलों के लेआउट और आकार को समायोजित किया जा सकता है ताकि विरूपण को रोकने के लिए समान कूलिंग सुनिश्चित की जा सके। एमएफए के साथ कूलिंग चैनल लेआउट को समायोजित करना स्वाभाविक हो गया; यहां तक कि ठंडा करने से भी विशेष रूप से बड़े टुकड़ों में विकृति रोकी जा सकती है।
निष्कर्ष में, उत्पादन प्रक्रियाओं में मोल्ड प्रवाह विश्लेषण को नियोजित करने से न केवल संभावित मुद्दों की पहचान होती है बल्कि वृद्धि का मार्ग भी प्रशस्त होता है जिससे दक्षता में वृद्धि होती है और लागत कम होती है। उन्नत तकनीक 3 देखें ।
मोल्ड प्रवाह विश्लेषण इंजेक्शन मोल्डिंग में दोषों को रोकने में मदद करता है।सत्य
इंजेक्शन प्रक्रिया का अनुकरण करके, मोल्ड प्रवाह विश्लेषण संभावित दोषों की पहचान करता है, जिससे उत्पादित भागों की समग्र गुणवत्ता में वृद्धि होती है।
गेट स्थानों को अनुकूलित करने से उत्पादन चक्र का समय बढ़ जाता है।असत्य
गेट की सही स्थिति पिघलने के प्रवाह में सुधार करती है और चक्र के समय को कम करती है, जिससे अधिक कुशल उत्पादन प्रक्रियाएं होती हैं।
निष्कर्ष
मोल्ड फ्लो विश्लेषण दक्षता और उत्पाद की गुणवत्ता में सुधार के लिए गेट स्थानों, रनर सिस्टम, इंजेक्शन दबाव और शीतलन समय को अनुकूलित करके इंजेक्शन मोल्डिंग को बढ़ाता है।
-
यह लिंक बेहतर मोल्ड डिज़ाइन परिणामों के लिए गेट स्थानों को अनुकूलित करने पर गहन विश्लेषण प्रदान करता है। ↩
-
अपनी उत्पादन दक्षता बढ़ाने के लिए प्रभावी कूलिंग टाइम प्रबंधन प्रथाओं पर विशेषज्ञ अंतर्दृष्टि और रणनीतियों की खोज करें। ↩
-
जानें कि कैसे एमएफए आपकी विनिर्माण प्रक्रियाओं में उल्लेखनीय सुधार कर सकता है और लागत को प्रभावी ढंग से कम कर सकता है। ↩