इंजेक्शन मोल्डिंग आधुनिक विनिर्माण की आधारशिला है, फिर भी इष्टतम दक्षता प्राप्त करना एक चुनौती बनी हुई है।
मोल्ड में पिघले हुए प्लास्टिक के प्रवाह को अनुकूलित करके इंजेक्शन मोल्डिंग दक्षता को बढ़ाने में रनर डिज़ाइन महत्वपूर्ण भूमिका निभाता है। उचित रूप से डिज़ाइन किए गए धावक चक्र के समय को कम कर सकते हैं, अपशिष्ट को कम कर सकते हैं और लगातार उत्पाद की गुणवत्ता सुनिश्चित कर सकते हैं, अंततः मोल्डिंग प्रक्रिया की समग्र दक्षता को बढ़ा सकते हैं।
जबकि रनर डिज़ाइन के बुनियादी सिद्धांतों को समझना महत्वपूर्ण है, विस्तृत रणनीतियों और सर्वोत्तम प्रथाओं की खोज आपके इंजेक्शन मोल्डिंग संचालन को महत्वपूर्ण रूप से बढ़ा सकती है। आइए विशिष्ट रनर डिज़ाइन तकनीकों के बारे में गहराई से जानें जो आपकी विनिर्माण दक्षता को बदल सकती हैं।
हॉट रनर सिस्टम इंजेक्शन मोल्डिंग में सामग्री की बर्बादी को कम करता है।सत्य
हॉट रनर प्लास्टिक को पिघलाए रखते हैं, ठोस कचरे को खत्म करते हैं, दक्षता बढ़ाते हैं।
हॉट और कोल्ड रनर सिस्टम के बीच मुख्य अंतर क्या हैं?
गर्म और ठंडे रनर सिस्टम मोल्डिंग में महत्वपूर्ण हैं, प्रत्येक विभिन्न अनुप्रयोगों के लिए अद्वितीय लाभ प्रदान करते हैं।
हॉट रनर सिस्टम मोल्ड के भीतर प्लास्टिक को पिघली हुई अवस्था में बनाए रखता है, अपशिष्ट को खत्म करता है और चक्र समय में सुधार करता है। दूसरी ओर, कोल्ड रनर सिस्टम को प्रत्येक चक्र के साथ ठोस धावकों को बाहर निकालने की आवश्यकता होती है, जिससे अधिक सामग्री बर्बाद होती है लेकिन अक्सर प्रारंभिक लागत कम होती है।
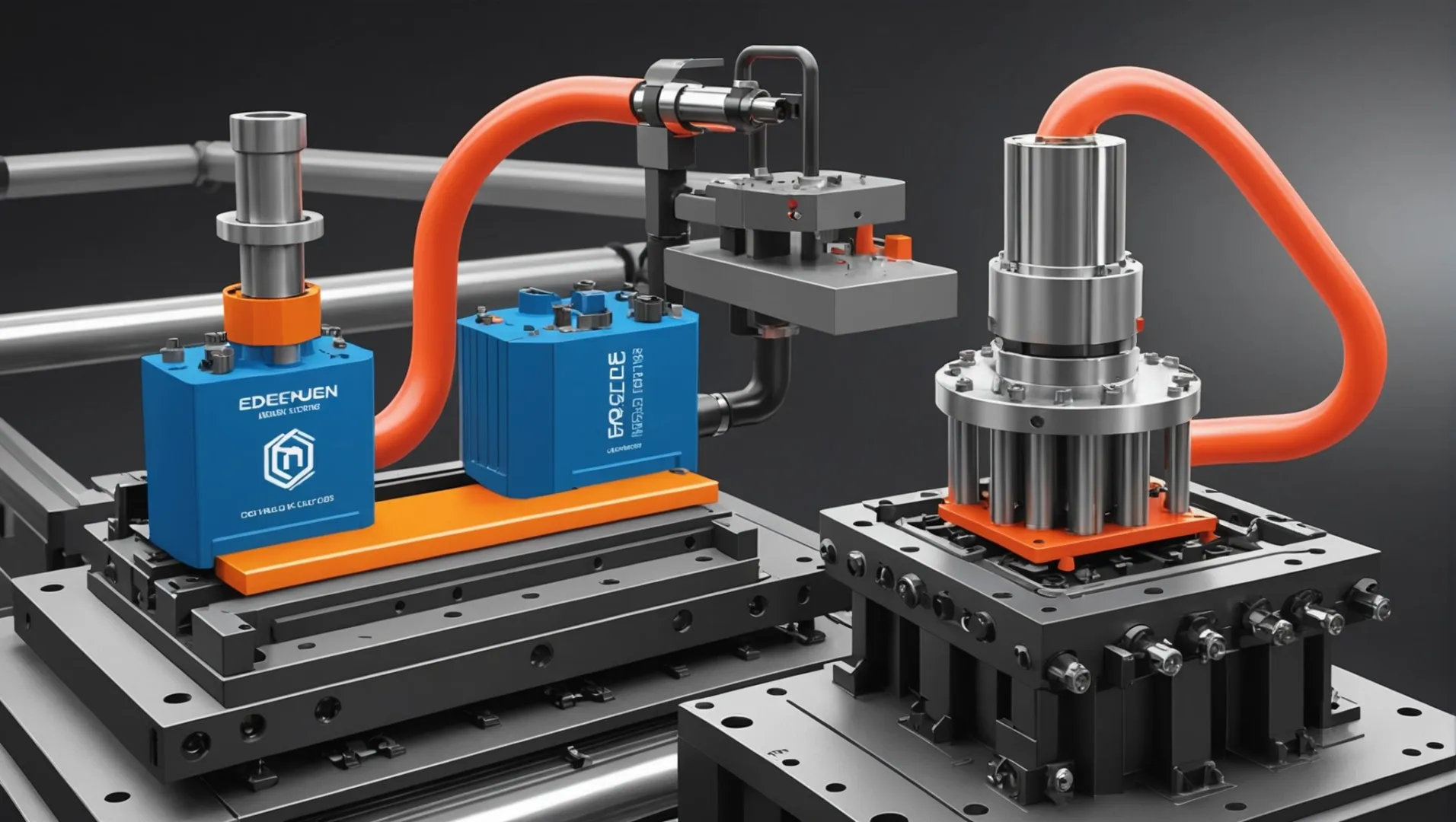
हॉट रनर सिस्टम की खोज
हॉट रनर सिस्टम को प्लास्टिक सामग्री को गर्म और तरल अवस्था में रखने के लिए डिज़ाइन किया गया है, जबकि यह रनर के माध्यम से मोल्ड कैविटी में प्रवाहित होती है। कई फायदों के कारण यह प्रणाली बड़े पैमाने पर उत्पादन के लिए अत्यधिक कुशल हो सकती है:
- अपशिष्ट में कमी : चूंकि प्रत्येक चक्र के साथ बाहर निकलने के लिए कोई ठोस धावक नहीं है, इसलिए सामग्री अपशिष्ट कम हो जाता है।
- बेहतर चक्र समय : एक स्थिर तापमान बनाए रखकर, गर्म धावक शीतलन चरण को छोटा कर देते हैं, जिससे समग्र चक्र समय कम हो जाता है।
- सुसंगत गुणवत्ता : स्थिर पिघला हुआ तापमान उत्पादित प्रत्येक भाग में एकरूपता सुनिश्चित करता है।
उदाहरण के लिए, बम्पर जैसे बड़े ऑटोमोटिव घटकों के निर्माण में, एक हॉट रनर सिस्टम पूरी प्रक्रिया के दौरान इष्टतम पिघल प्रवाह को बनाए रख सकता है, जिससे दक्षता और उत्पाद की गुणवत्ता दोनों में वृद्धि होती है।
कोल्ड रनर सिस्टम को समझना
कोल्ड रनर प्रणालियाँ आम तौर पर अधिक सीधी होती हैं और इसमें साँचे में काटा गया एक साधारण चैनल होता है जो पिघले हुए प्लास्टिक को गुहाओं में निर्देशित करता है। धावक भागों के साथ ठोस हो जाते हैं और प्रत्येक चक्र के अंत में बाहर निकल जाते हैं। प्रमुख विशेषताओं में शामिल हैं:
- कम प्रारंभिक लागत : कोल्ड रनर मोल्ड्स की सादगी आम तौर पर उन्हें उत्पादन करने के लिए सस्ता बनाती है।
- सामग्री के उपयोग में लचीलापन : गर्म धावक की तुलना में ठंडे धावक सामग्री की एक विस्तृत श्रृंखला के साथ संगत होते हैं।
- डिज़ाइन अनुकूलन : डिज़ाइन को अनुकूलित करके - छोटे, सीधे धावकों का उपयोग करके या इष्टतम क्रॉस-सेक्शन आकृतियों का चयन करके - दक्षता में काफी वृद्धि की जा सकती है।
ऐसे परिदृश्य पर विचार करें जहां कैप या बटन जैसी छोटी प्लास्टिक वस्तुओं का उत्पादन किया जाता है; कोल्ड रनर प्रणाली का उपयोग करना लागत प्रभावी हो सकता है और साथ ही रनर डिज़ाइन को परिष्कृत करके उचित दक्षता भी प्राप्त कर सकता है।
तुलनात्मक विश्लेषण: हॉट बनाम कोल्ड रनर सिस्टम
विशेषता | हॉट रनर सिस्टम | कोल्ड रनर सिस्टम |
---|---|---|
सामग्री अपशिष्ट | न्यूनतम (यदि मौजूद हो तो केवल स्प्रू) | उच्च (धावक बेकार हैं) |
प्रारंभिक लागत | उच्चतर (जटिल प्रणाली) | निचला (सरल डिज़ाइन) |
समय चक्र | तेज़ (ठोस धावकों को ठंडा करने की कोई ज़रूरत नहीं) | धीमा (धावकों को ठंडा होना आवश्यक है) |
सामग्री अनुकूलता | थर्मोप्लास्टिक्स तक सीमित जो उच्च तापमान सहन कर सकते हैं | थर्मोप्लास्टिक्स की विस्तृत श्रृंखला |
रखरखाव | हीटर और मैनिफोल्ड सिस्टम के कारण अधिक जटिल | सरल, कम रखरखाव की आवश्यकता |
अंततः, गर्म और ठंडे धावक प्रणालियों के बीच चयन करना उत्पादन की मात्रा, सामग्री की पसंद और लागत पर विचार जैसे कारकों पर निर्भर करता है। उच्च दक्षता और न्यूनतम अपशिष्ट की आवश्यकता वाले बड़े पैमाने के संचालन के लिए, हॉट रनर को अक्सर प्राथमिकता दी जाती है। इस बीच, छोटे उत्पादन कार्यों के लिए या जब प्रारंभिक लागत को कम करने की आवश्यकता होती है, तो कोल्ड रनर एक उत्कृष्ट विकल्प हो सकते हैं। अंतरों को समझकर 1 , निर्माता इष्टतम दक्षता प्राप्त करने के लिए अपनी प्रक्रियाओं को बेहतर ढंग से तैयार कर सकते हैं।
हॉट रनर सिस्टम ठोस रनर को खत्म करके सामग्री की बर्बादी को कम करते हैं।सत्य
हॉट रनर प्लास्टिक को पिघलाकर रखते हैं, जिससे रनर के ठोस अपशिष्ट को रोका जा सकता है।
गर्म धावकों की तुलना में ठंडे धावक प्रणालियों का रखरखाव अधिक महंगा होता है।असत्य
ठंडे धावक सरल होते हैं, गर्म धावकों की तुलना में कम रखरखाव की आवश्यकता होती है।
रनर का आकार इंजेक्शन मोल्डिंग दक्षता को कैसे प्रभावित करता है?
इंजेक्शन मोल्डिंग में रनर का आकार महत्वपूर्ण होता है, जो दक्षता और उत्पाद की गुणवत्ता दोनों को प्रभावित करता है।
रनर आकार को समायोजित करने से प्रवाह प्रतिरोध और सामग्री के उपयोग को संतुलित करके इंजेक्शन मोल्डिंग दक्षता पर प्रभाव पड़ता है। एक इष्टतम धावक आकार न्यूनतम दबाव हानि और कुशल सामग्री प्रवाह सुनिश्चित करता है, चक्र के समय को कम करता है और उत्पाद की स्थिरता को बढ़ाता है।
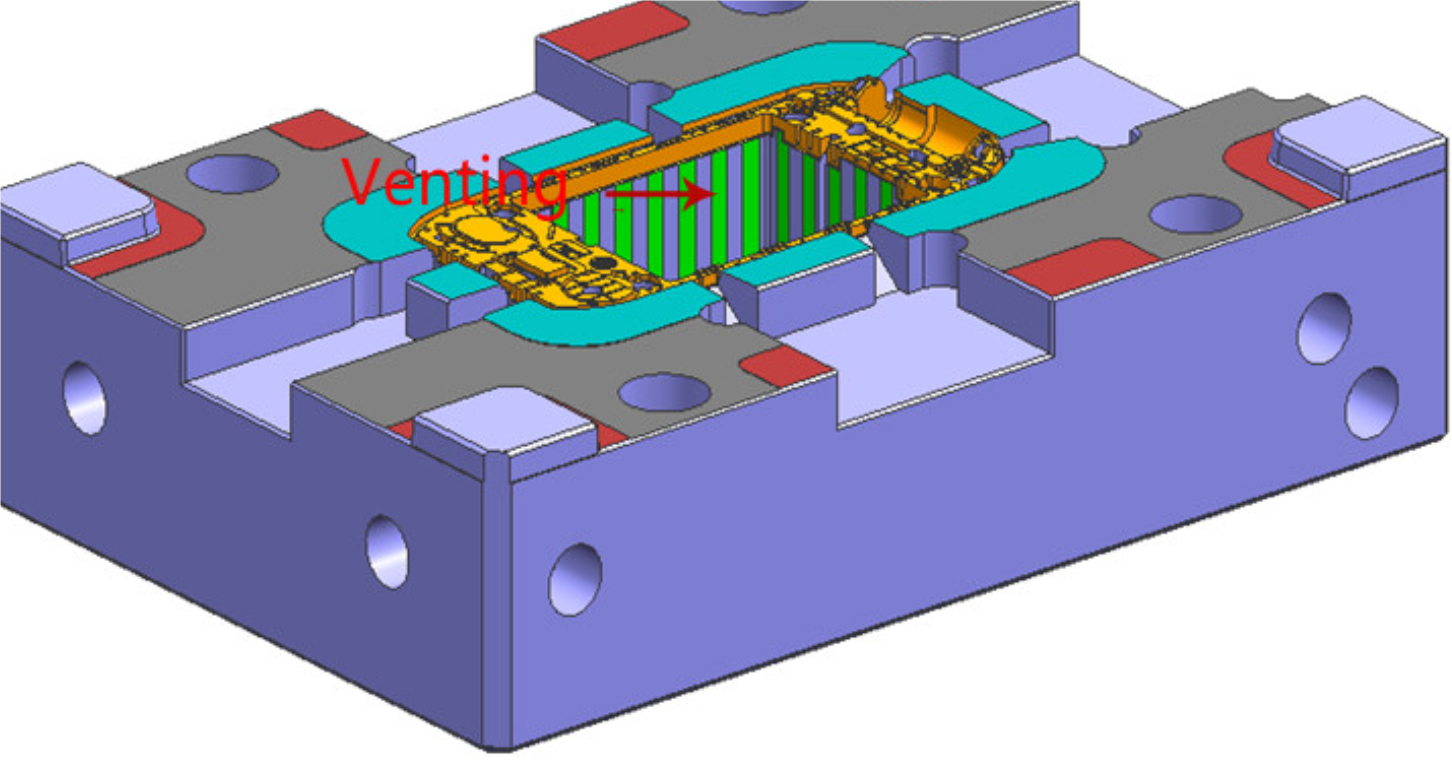
धावक व्यास के प्रभाव को समझना
इंजेक्शन मोल्डिंग प्रक्रिया 2 में प्रवाह प्रतिरोध और इंजेक्शन दबाव को प्रभावित करता है । एक अच्छी तरह से चुना गया व्यास प्लास्टिक के प्रवाह को अनुकूलित करता है, जो उच्च दक्षता प्राप्त करने के लिए महत्वपूर्ण है।
- छोटा रनर व्यास: छोटे भागों और अच्छी तरलता वाले प्लास्टिक के लिए आदर्श, यह विकल्प सामग्री की बर्बादी को कम करता है। हालाँकि, अगर सावधानी से नहीं चुना गया तो यह प्रवाह प्रतिरोध को बढ़ा सकता है, जिससे चक्र समय प्रभावित हो सकता है।
- बड़े रनर व्यास: बड़े भागों और खराब तरलता वाले प्लास्टिक के लिए उपयुक्त। हालाँकि यह प्रवाह प्रतिरोध को कम करता है, लेकिन बहुत अधिक होने पर इसके परिणामस्वरूप सामग्री की बर्बादी हो सकती है।
उदाहरण के लिए, मोबाइल फोन केस जैसी छोटी वस्तुओं के उत्पादन के लिए अक्सर 2-4 मिमी व्यास की आवश्यकता होती है, जबकि कार बंपर जैसी बड़ी वस्तुओं के लिए 10 मिमी से अधिक की आवश्यकता हो सकती है।
धावक की लंबाई का महत्व
दबाव हानि को कम करने और प्लास्टिक को समय से पहले ठंडा होने से रोकने के लिए रनर की लंबाई कम से कम की जानी चाहिए।
- लघु धावक: ये कुशल हैं क्योंकि ये प्रवाह समय को कम करते हैं, जो त्वरित चक्र की आवश्यकता वाले भागों के लिए महत्वपूर्ण है।
- लंबे समय तक चलने वाले: कैविटी भरने से पहले प्लास्टिक जम सकता है, जिससे गुणवत्ता और दक्षता प्रभावित हो सकती है।
मल्टी-पॉइंट इंजेक्शन विधि को लागू करने से धावक की लंबाई को कुशलतापूर्वक छोटा किया जा सकता है।
दक्षता के लिए रनर लेआउट का अनुकूलन
एक सुनियोजित रनर लेआउट संतुलित भराव और न्यूनतम प्रवाह प्रतिरोध सुनिश्चित करके दक्षता में उल्लेखनीय वृद्धि कर सकता है।
- संतुलित धावक डिजाइन: यह दृष्टिकोण ओवरफिलिंग या अंडरफिलिंग से बचने के लिए गुहाओं में समान दबाव वितरण सुनिश्चित करता है।
- सुचारू प्रवाह चैनल: धावक डिजाइन में मोड़ और कोनों को कम करने से प्रतिरोध कम हो जाता है, प्रवाह दर बढ़ जाती है।
रनर बैलेंसिंग सॉफ़्टवेयर 3 उपयोग करने से एक आदर्श लेआउट प्राप्त करने में मदद मिल सकती है।
भौतिक गुणों का मूल्यांकन
तरलता और सिकुड़न जैसी सामग्री की विशेषताएं धावक के आकार के निर्णयों को महत्वपूर्ण रूप से प्रभावित करती हैं।
- तरलता संबंधी विचार: उच्च तरलता वाले प्लास्टिक में छोटे धावकों का उपयोग किया जा सकता है; कम तरलता वाले लोगों को दक्षता बनाए रखने के लिए बड़े आकार की आवश्यकता होती है।
- संकोचन कारक: मोल्डिंग के बाद आयामी स्थिरता सुनिश्चित करने के लिए उच्च-संकोचन सामग्री को रनर डिज़ाइन में समायोजन की आवश्यकता हो सकती है।
इन कारकों पर विचार करने से यह सुनिश्चित होता है कि चुना गया धावक आकार इष्टतम इंजेक्शन मोल्डिंग परिणामों का समर्थन करता है।
छोटे धावक इंजेक्शन मोल्डिंग में सामग्री की बर्बादी को कम करते हैं।सत्य
छोटे धावक सामग्री के उपयोग को कम करते हैं लेकिन प्रवाह प्रतिरोध को बढ़ा सकते हैं।
बड़े धावक व्यास हमेशा इंजेक्शन मोल्डिंग दक्षता को बढ़ाते हैं।असत्य
बड़े धावक प्रतिरोध को कम करते हैं लेकिन बड़े आकार के होने पर सामग्री बर्बाद कर सकते हैं।
लगातार गुणवत्ता के लिए संतुलित रनर लेआउट क्यों आवश्यक है?
इंजेक्शन मोल्डिंग में लगातार गुणवत्ता सुनिश्चित करना एक अच्छी तरह से संतुलित रनर लेआउट पर निर्भर करता है।
इंजेक्शन मोल्डिंग में लगातार गुणवत्ता बनाए रखने के लिए एक संतुलित रनर लेआउट महत्वपूर्ण है। यह गुहाओं को एक समान भरने को सुनिश्चित करता है, कम भरने या अधिक भरने जैसे दोषों को रोकता है, और ढाले हुए हिस्सों की गुणवत्ता को स्थिर करता है। रनर लेआउट को अनुकूलित करके, निर्माता उच्च दक्षता और बेहतर उत्पाद स्थिरता प्राप्त कर सकते हैं।
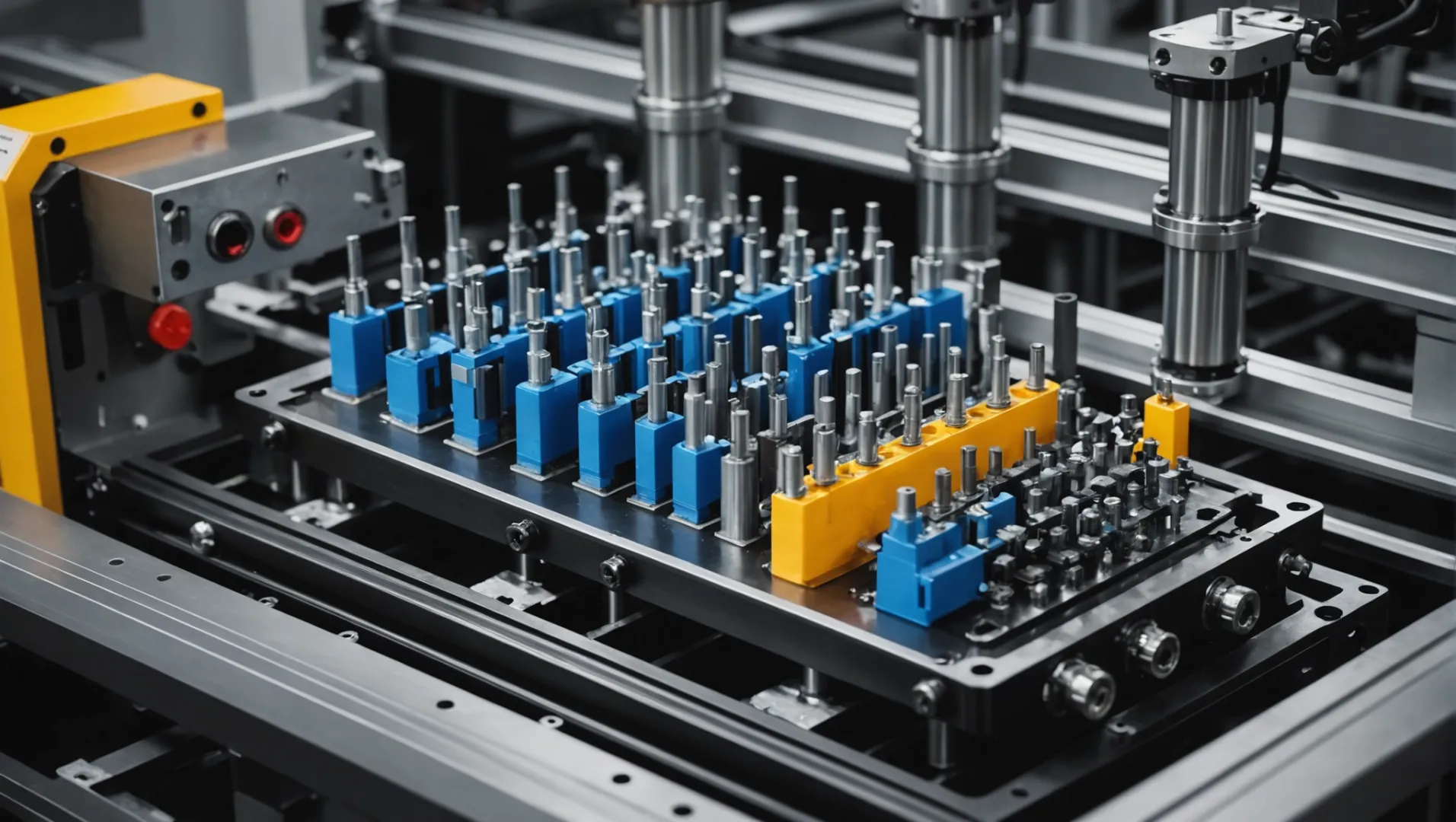
रनर लेआउट की भूमिका को समझना
एक संतुलित धावक लेआउट 4 महत्वपूर्ण है क्योंकि यह सुनिश्चित करता है कि पिघला हुआ प्लास्टिक इंजेक्शन प्रक्रिया के दौरान प्रत्येक गुहा को समान रूप से भरता है। शॉर्ट शॉट्स, फ्लैश या वॉरपिंग जैसे दोषों से बचने के लिए यह समान भरना आवश्यक है, जो तब हो सकता है जब कुछ गुहाएं कम या अधिक भरी होती हैं। एक सुसंगत धावक लेआउट सभी गुहाओं में स्थिर दबाव और तापमान वितरण की अनुमति देता है, यह सुनिश्चित करता है कि प्रत्येक ढाला हुआ भाग आवश्यक गुणवत्ता मानकों को पूरा करता है।
संतुलन प्राप्त करने की तकनीकें
-
धावक संतुलन सॉफ्टवेयर
सॉफ़्टवेयर टूल का उपयोग एक संतुलित धावक प्रणाली को डिज़ाइन करने में सहायता कर सकता है। ये प्रोग्राम रनर सिस्टम के माध्यम से प्लास्टिक के प्रवाह का अनुकरण करते हैं, जिससे डिजाइनरों को समान भरने के समय और दबाव प्राप्त करने के लिए आकार और लेआउट को समायोजित करने में मदद मिलती है।
-
अनुभवजन्य सूत्र
अनुभवी डिजाइनर अक्सर इष्टतम धावक आयामों की गणना के लिए अनुभवजन्य सूत्रों पर भरोसा करते हैं। ये गणनाएँ गुहाओं की संख्या, प्लास्टिक चिपचिपाहट और वांछित चक्र समय जैसे कारकों को ध्यान में रखती हैं।
-
शाखा कोणों और लंबाई को समायोजित करना
मल्टी-कैविटी सांचों में, शाखा के कोण और लंबाई को समायोजित करने से प्लास्टिक को समान रूप से वितरित करने में मदद मिल सकती है। इसमें धावकों की ज्यामिति को बदलना शामिल है ताकि प्रत्येक गुहा को समकालिक तरीके से समान मात्रा में सामग्री प्राप्त हो।
चुनौतियाँ और समाधान
चुनौती: असंतुलित धावकों के कारण गुहा भरने में भिन्नता से असंगत भाग की गुणवत्ता हो सकती है।
समाधान: सुव्यवस्थित प्रवाह चैनल 5 उपयोग करके संतुलित धावक लेआउट को लागू करने से दबाव हानि कम हो जाती है और चक्र समय कम हो जाता है।
केस स्टडी: संतुलित धावकों के साथ दक्षता में सुधार
ऑटोमोटिव घटकों के लिए जटिल मल्टी-कैविटी मोल्ड बनाने वाले निर्माता पर विचार करें। प्रारंभ में, उन्हें असंतुलित रनर लेआउट के कारण अलग-अलग उत्पाद गुणवत्ता के साथ समस्याओं का सामना करना पड़ा। सॉफ्टवेयर सिमुलेशन और अनुभवजन्य समायोजन सहित एक संतुलित डिजाइन दृष्टिकोण अपनाकर, उन्होंने एक समान गुहा भरने को प्राप्त किया। इसके परिणामस्वरूप चक्र समय में 15% की कमी आई और आंशिक स्थिरता में महत्वपूर्ण सुधार हुआ।
संक्षेप में, एक संतुलित रनर लेआउट न केवल इंजेक्शन मोल्डिंग प्रक्रिया की दक्षता को बढ़ाता है बल्कि यह भी सुनिश्चित करता है कि प्रत्येक उत्पाद कड़े गुणवत्ता मानकों को पूरा करता है।
संतुलित रनर लेआउट इंजेक्शन मोल्डिंग दोषों को रोकता है।सत्य
एक संतुलित लेआउट एक समान भराव सुनिश्चित करता है, जिससे विकृति जैसे दोषों को रोका जा सकता है।
असंतुलित धावक मोल्डिंग प्रक्रियाओं में चक्र का समय कम कर देते हैं।असत्य
असंतुलित धावक असमान भराव का कारण बनते हैं, संभावित रूप से चक्र का समय बढ़ाते हैं।
भौतिक गुण धावक डिज़ाइन निर्णयों को कैसे प्रभावित करते हैं?
सामग्री गुण सीधे धावक डिजाइन को प्रभावित करते हैं, इष्टतम दक्षता के लिए प्रवाह चैनल आकार और लेआउट समायोजन को निर्देशित करते हैं।
प्लास्टिक की तरलता और सिकुड़न जैसे भौतिक गुण धावक डिजाइन निर्णयों को महत्वपूर्ण रूप से प्रभावित करते हैं। रनर आकार और लेआउट में समायोजन इन गुणों को पूरा करता है, सुचारू प्रवाह सुनिश्चित करता है, अपशिष्ट को कम करता है और उत्पाद की गुणवत्ता बनाए रखता है। इंजेक्शन मोल्डिंग दक्षता बढ़ाने के लिए इन भौतिक विशेषताओं को समझना आवश्यक है।
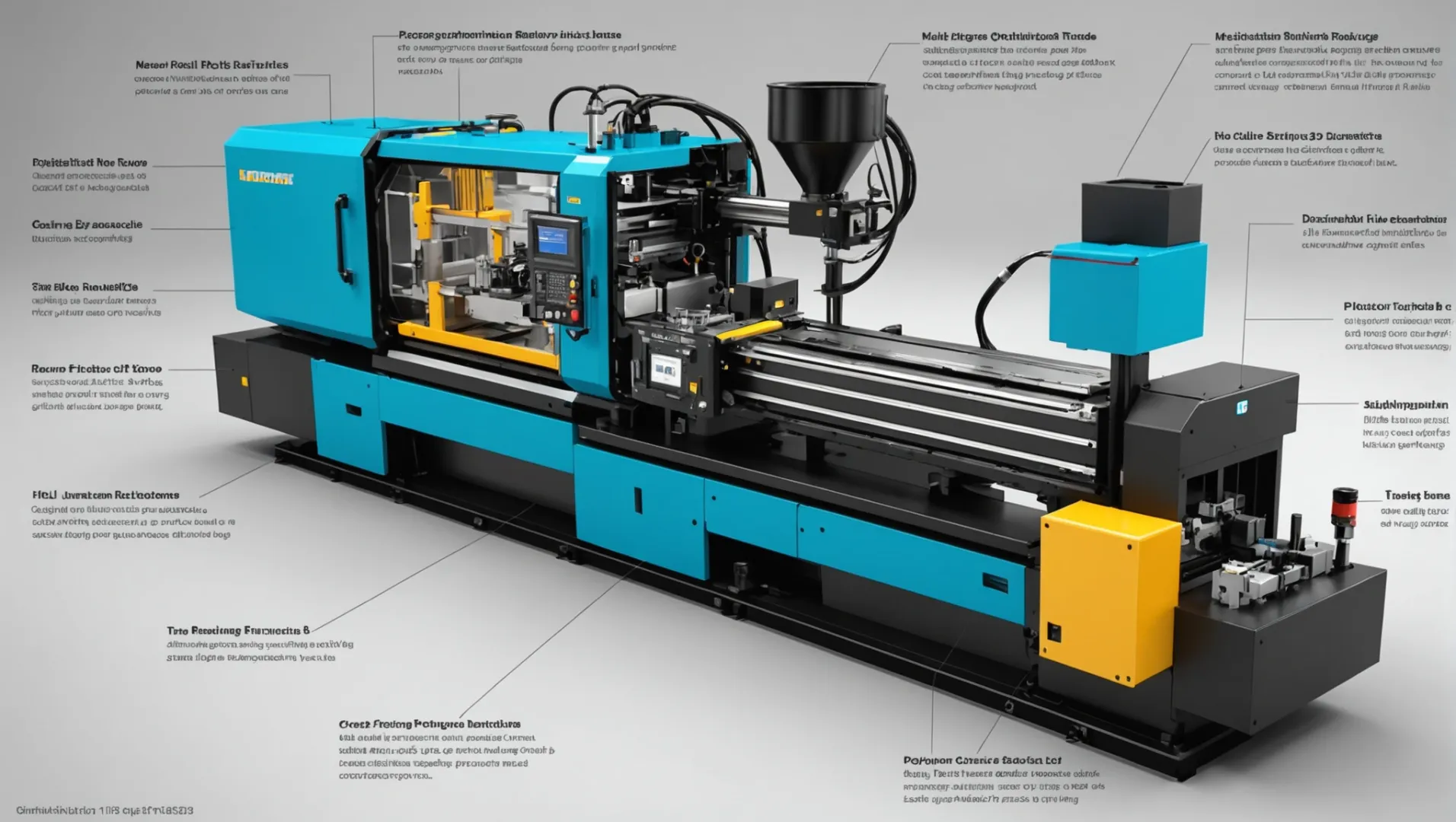
प्लास्टिक तरलता को समझना
प्लास्टिक सामग्री की तरलता यह निर्धारित करती है कि इंजेक्शन मोल्डिंग प्रक्रिया के दौरान यह रनर सिस्टम के माध्यम से कितनी आसानी से प्रवाहित हो सकती है। उदाहरण के लिए, पॉलीइथाइलीन और पॉलीप्रोपाइलीन जैसी सामग्रियां उच्च तरलता प्रदर्शित करती हैं, जिससे छोटे धावक आकारों के उपयोग की अनुमति मिलती है। इन सामग्रियों को धावक के माध्यम से चलने के लिए कम बल की आवश्यकता होती है, जिससे चक्र का समय और ऊर्जा की खपत कम हो जाती है।
इसके विपरीत, कम तरलता वाले प्लास्टिक, जैसे पॉली कार्बोनेट और पॉलीफेनिलीन ईथर, को उचित प्रवाह की सुविधा के लिए बड़े रनर आकार की आवश्यकता होती है। यह समायोजन दोषों को रोकने और यह सुनिश्चित करने के लिए महत्वपूर्ण है कि पिघला हुआ प्लास्टिक मोल्ड के सभी हिस्सों तक कुशलतापूर्वक पहुंचे।
इसके अलावा, धावक की लंबाई भी मायने रखती है। दबाव हानि को कम करने और समय से पहले ठंडा होने से रोकने के लिए उच्च तरलता वाले प्लास्टिक के लिए छोटे धावकों को प्राथमिकता दी जाती है। कम तरलता वाली सामग्रियों के लिए, लंबे धावकों की आवश्यकता हो सकती है, लेकिन पूरे प्रवाह के दौरान पर्याप्त गर्मी और दबाव बनाए रखने के लिए उन्हें सावधानीपूर्वक डिजाइन किया जाना चाहिए।
सामग्री संकोचन संबंधी विचार
सिकुड़न एक अन्य महत्वपूर्ण कारक है जो धावक डिजाइन को प्रभावित करता है। उच्च संकोचन दर वाली सामग्री, जैसे एबीएस प्लास्टिक, को धावक आयामों पर सावधानीपूर्वक विचार करने की आवश्यकता होती है। ठंडा होने पर सामग्री के सिकुड़ने की प्रवृत्ति की भरपाई के लिए एक बड़ा व्यास आवश्यक हो सकता है। इसके अतिरिक्त, डिज़ाइन में सिकुड़न मार्जिन छोड़ने से अंतिम उत्पाद में आयामी अशुद्धियों को रोका जा सकता है।
रनर सिस्टम के लेआउट को भी सिकुड़न विशेषताओं के आधार पर समायोजित किया जाना चाहिए। एक अच्छी तरह से डिज़ाइन किया गया लेआउट यह सुनिश्चित कर सकता है कि सामग्री सिकुड़न की प्रवृत्ति के बावजूद समान रूप से मोल्ड को भरती है, जिससे उत्पाद की स्थिरता और गुणवत्ता बनी रहती है।
स्पष्ट करने के लिए, आइए भौतिक गुणों और उनके संबंधित धावक डिज़ाइन निहितार्थों की तुलना की जाँच करें:
सामग्री | द्रवता | सिकुड़न दर | धावक आकार सुझाव |
---|---|---|---|
polyethylene | उच्च | कम | छोटा |
पॉलीकार्बोनेट | कम | उच्च | बड़ा |
polypropylene | उच्च | मध्यम | छोटा |
पेट | मध्यम | उच्च | बड़ा |
सामग्री गुणों के अनुरूप रनर डिज़ाइन तैयार करना
धावक डिजाइन में विभिन्न सामग्रियों के अद्वितीय गुणों को शामिल करने के लिए एक सूक्ष्म दृष्टिकोण की आवश्यकता होती है। तरलता और सिकुड़न के अलावा, तापीय चालकता और रासायनिक प्रतिरोध जैसे कारक भी इष्टतम डिज़ाइन सुविधाओं को निर्धारित करने में भूमिका निभाते हैं।
उदाहरण के लिए, कुछ सामग्रियों को हॉट रनर सिस्टम 6 , जिससे समय से पहले जमने का खतरा कम हो जाता है। कोल्ड रनर सिस्टम 7 से लाभान्वित हो सकते हैं जो उच्च मात्रा में उत्पादन में लागत-प्रभावशीलता के लिए अनुकूलित हैं।
अंततः, भौतिक गुणों को समझने और उनका लाभ उठाने से निर्माताओं को अपनी इंजेक्शन मोल्डिंग प्रक्रियाओं को अनुकूलित करने, अपशिष्ट को कम करने, चक्र समय में सुधार करने और उच्च गुणवत्ता वाले आउटपुट सुनिश्चित करने की अनुमति मिलती है।
उच्च तरलता वाले प्लास्टिक में छोटे धावकों का उपयोग किया जाता है।सत्य
उच्च तरलता वाली सामग्रियों को प्रवाहित होने के लिए कम बल की आवश्यकता होती है, जिससे छोटे धावकों को अनुमति मिलती है।
एबीएस प्लास्टिक में सिकुड़न दर कम होती है।असत्य
एबीएस प्लास्टिक उच्च संकोचन प्रदर्शित करता है, जिसके लिए बड़े रनर डिज़ाइन की आवश्यकता होती है।
निष्कर्ष
इंजेक्शन मोल्डिंग दक्षता को बढ़ाने में रनर डिज़ाइन को अनुकूलित करना महत्वपूर्ण है। इन जानकारियों को लागू करके, निर्माता तेज़ चक्र, कम अपशिष्ट और बेहतर उत्पाद गुणवत्ता प्राप्त कर सकते हैं।
-
हॉट और कोल्ड रनर सिस्टम के बीच चयन करने के बारे में गहराई से जानकारी प्राप्त करें: हॉट रनर सिस्टम में आमतौर पर कोल्ड रनर सिस्टम की तुलना में काफी तेज चक्र समय होता है। धावकों के हटने से इनकी संख्या बहुत कम हो जाती है... ↩
-
पता लगाता है कि रनर व्यास मोल्डिंग दक्षता और गुणवत्ता को कैसे प्रभावित करता है।: रनर व्यास एक महत्वपूर्ण भूमिका निभाता है: यदि यह बहुत छोटा है, तो यह बहुत जल्दी जम सकता है, जिससे पैक करने के लिए प्रभावी प्रवाह चैनल बहुत छोटा हो जाता है ... ↩
-
जानें कि सॉफ्टवेयर रनर लेआउट को कुशलतापूर्वक अनुकूलित करने में कैसे सहायता करता है: मोल्डेक्स3डी फ्लो की शक्ति के साथ, आप स्पष्ट रूप से पिघल प्रवाह व्यवहार का निरीक्षण कर सकते हैं, संभावित वेल्डलाइन का सटीक पता लगा सकते हैं और शॉर्ट शॉट, एयर ट्रैप समस्याओं आदि का पता लगा सकते हैं। ↩
-
जानें कि दोष-मुक्त मोल्डिंग के लिए समान भरना क्यों महत्वपूर्ण है: डिज़ाइन यह सुनिश्चित करने के लिए है कि प्रत्येक गुहा में संतुलित सामग्री प्रवाह हो और एक ही समय में भरा जाए। उदाहरण के लिए, रेडियेट रनर, लीनियर रनर, वाई-आकार... ↩
-
जानें कि दबाव हानि को कम करने से चक्र समय में कैसे सुधार होता है।: यह ब्लॉग पोस्ट 6 ठोस, दोहराए जाने योग्य चरण प्रदान करता है जो कस्टम इंजेक्शन मोल्डिंग का उपयोग करके प्लास्टिक भाग परियोजना को सुव्यवस्थित करने के लिए सबसे अच्छा दृष्टिकोण बनाते हैं। ↩
-
जानें कि कैसे हॉट रनर तापमान स्थिरता में सुधार करते हैं और अपशिष्ट को कम करते हैं।: इसके अलावा, हॉट रनर सिस्टम के साथ, आमतौर पर कम इंजेक्शन दबाव का उपयोग किया जा सकता है, जो मोल्ड और प्लेटन विक्षेपण को कम करेगा और फ्लैश बनाए रखेगा ... ↩
-
उच्च मात्रा में उत्पादन के लिए लागत प्रभावी लाभों के बारे में जानें: कोल्ड रनर मोल्ड भी बहुत कम महंगे हैं, और निर्माताओं के लिए डिजाइन और उत्पादन करना बहुत आसान है। इससे टूलींग लागत और लीड समय को कम करने में मदद मिलती है… ↩