इंजेक्शन मोल्डिंग एक आकर्षक प्रक्रिया है, आधुनिक विनिर्माण का एक सच्चा चमत्कार है। हालाँकि, यह चुनौतियों का उचित हिस्सा लेकर आता है। मेरे द्वारा सामना किए गए सबसे निराशाजनक मुद्दों में से एक ढले हुए उत्पादों में किनारे का फ्रैक्चर है - कुछ ऐसा जो वास्तव में गुणवत्ता से समझौता कर सकता है।
इंजेक्शन मोल्डिंग में उत्पाद किनारे के फ्रैक्चर को रोकने के लिए, इंजेक्शन मापदंडों को समायोजित करें, मोल्ड डिजाइन को अनुकूलित करें, उपयुक्त सामग्री चुनें और उपकरण बनाए रखें। मुख्य रणनीतियों में इंजेक्शन की गति कम करना, मोल्ड तापमान बढ़ाना और सामग्री की गुणवत्ता सुनिश्चित करना शामिल है।
लेकिन हमें यहीं नहीं रुकना चाहिए! प्रत्येक रणनीति की बारीकियों की खोज वास्तव में आपकी उत्पादन प्रक्रिया को बदल सकती है। मेरे साथ जुड़ें क्योंकि हम उन प्रभावी प्रथाओं पर चर्चा कर रहे हैं जो आपको सामान्य नुकसान से बचने में मदद कर सकती हैं।
इंजेक्शन की गति कम करने से किनारे के फ्रैक्चर को रोका जा सकता है।सत्य
इंजेक्शन की गति कम करने से किनारों पर प्रभाव बल कम हो जाता है, तनाव कम हो जाता है।
इंजेक्शन मोल्डिंग में किनारे के फ्रैक्चर के सामान्य कारण क्या हैं?
इंजेक्शन मोल्डिंग में किनारे का फ्रैक्चर एक लगातार समस्या हो सकती है, जो उत्पादों की अखंडता और कार्यक्षमता को प्रभावित कर सकती है। उनके कारणों को समझना रोकथाम की कुंजी है।
इंजेक्शन मोल्डिंग में किनारे के फ्रैक्चर अक्सर अनुचित प्रक्रिया मापदंडों, उप-इष्टतम मोल्ड डिजाइन, सामग्री अपर्याप्तता और खराब रखरखाव के परिणामस्वरूप होते हैं। गुणवत्ता सुधार के लिए इन क्षेत्रों पर ध्यान देना महत्वपूर्ण है।
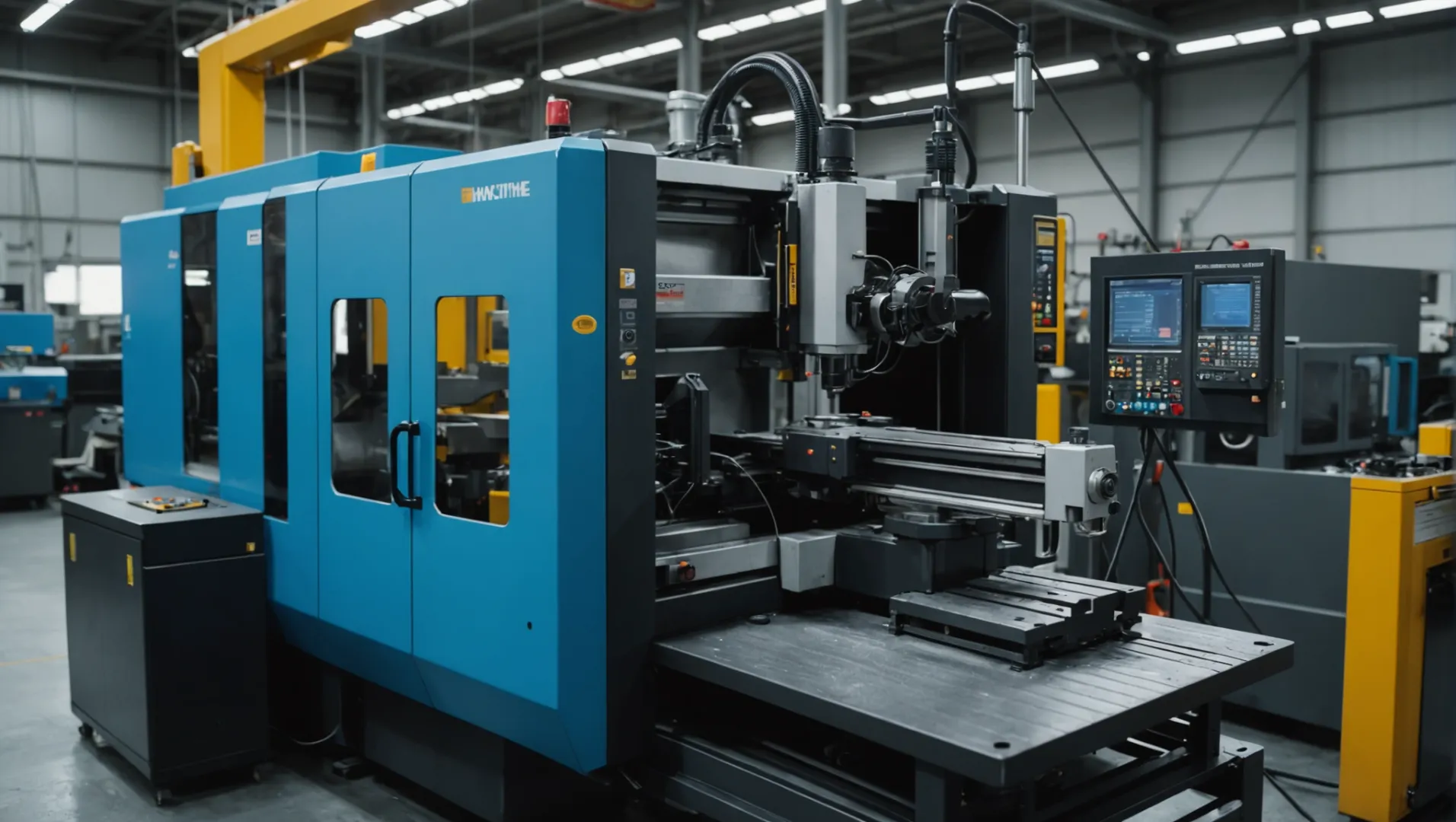
प्रक्रिया पैरामीटर
इंजेक्शन मोल्डिंग में, प्रक्रिया मापदंडों का नियंत्रण महत्वपूर्ण है। इंजेक्शन की गति और धारण दबाव दो महत्वपूर्ण कारक हैं:
-
इंजेक्शन की गति : अत्यधिक गति के कारण किनारों पर उच्च प्रभाव बल पड़ सकता है, जिससे फ्रैक्चर हो सकता है। इंजेक्शन की गति 1 पिघल को मोल्ड में अधिक आसानी से भरने की अनुमति मिलती है, जिससे तनाव कम हो जाता है।
-
होल्डिंग दबाव : होल्डिंग चरण के दौरान अत्यधिक दबाव से किनारे के फ्रैक्चर का खतरा बढ़ सकता है। इसे उचित रूप से कम करने से शीतलन के दौरान अधिक बाहर निकालना बंद हो जाता है।
इसके अतिरिक्त, शीतलन समय मोल्ड के भीतर उत्पाद का पूर्ण स्थिरीकरण सुनिश्चित होता है, जिससे विरूपण जोखिम कम हो जाता है।
साँचे का डिज़ाइन
मोल्ड का डिज़ाइन किनारे के फ्रैक्चर को रोकने में महत्वपूर्ण भूमिका निभाता है:
-
गेट का स्थान और संख्या : मोटे हिस्सों में गेट लगाने या बड़े उत्पादों के लिए उनकी संख्या बढ़ाने से पिघल को समान रूप से वितरित करने में मदद मिलती है और स्थानीय तनाव कम हो जाता है।
-
मोल्ड संरचना : किनारों और कोनों पर बड़े फ़िलेट रेडी को शामिल करने से तनाव एकाग्रता कम हो जाती है। एक अनुकूलित डिमोल्डिंग तंत्र उत्पाद हटाने के दौरान क्षति को रोकता है।
सामग्री चयन
स्थायित्व के लिए सही सामग्री का चयन आवश्यक है:
-
सामग्री की कठोरता : उच्च कठोरता और ताकत वाली सामग्री का चयन करना, जैसे कि फाइबर के साथ प्रबलित सामग्री, किनारे के फ्रैक्चर की घटनाओं को काफी कम कर सकती है।
-
सामग्री की गुणवत्ता : यह सुनिश्चित करना कि सामग्री सूखी और अशुद्धियों से मुक्त है, मोल्डिंग प्रक्रिया के दौरान तनाव और दोषों को रोकती है।
उपकरण रखरखाव
मशीनरी और मोल्ड दोनों का नियमित रखरखाव महत्वपूर्ण है:
-
इंजेक्शन मोल्डिंग मशीन : स्क्रू, बैरल और नोजल जैसे घटकों की नियमित जांच और रखरखाव लगातार प्रदर्शन सुनिश्चित करता है।
-
मोल्ड रखरखाव : नियमित सफाई और घिसाव की जांच से उपकरण की विफलता से उत्पन्न होने वाली खराबी को रोका जा सकता है।
कर्मचारी प्रशिक्षण 2 यह सुनिश्चित करता है कि ऑपरेटर मापदंडों को समायोजित करने और सामान्य मुद्दों को संबोधित करने में कुशल हैं, जिससे किनारे के फ्रैक्चर को रोका जा सके।
अत्यधिक इंजेक्शन गति के कारण किनारे में फ्रैक्चर हो जाता है।सत्य
उच्च इंजेक्शन गति से प्रभाव बल बढ़ जाता है, जिससे फ्रैक्चर हो जाता है।
मोल्ड के रख-रखाव को नजरअंदाज करने से किनारे के फ्रैक्चर पर कोई प्रभाव नहीं पड़ता है।असत्य
रखरखाव की उपेक्षा करने से खराबी हो सकती है, जिससे फ्रैक्चर का खतरा बढ़ सकता है।
मोल्ड डिज़ाइन एज फ्रैक्चर रोकथाम को कैसे प्रभावित करता है?
इंजेक्शन मोल्डिंग में मोल्ड का डिज़ाइन किनारे के फ्रैक्चर को रोकने में महत्वपूर्ण है, एक लगातार दोष जो उत्पाद की अखंडता को कमजोर करता है।
मोल्ड डिज़ाइन गेट स्थान को अनुकूलित करके, फ़िलेट रेडी को बढ़ाकर और एक समान मोल्ड तापमान सुनिश्चित करके किनारे फ्रैक्चर की रोकथाम को महत्वपूर्ण रूप से प्रभावित करता है। ये समायोजन तनाव एकाग्रता को कम करते हैं और उत्पाद स्थायित्व को बढ़ाते हैं।
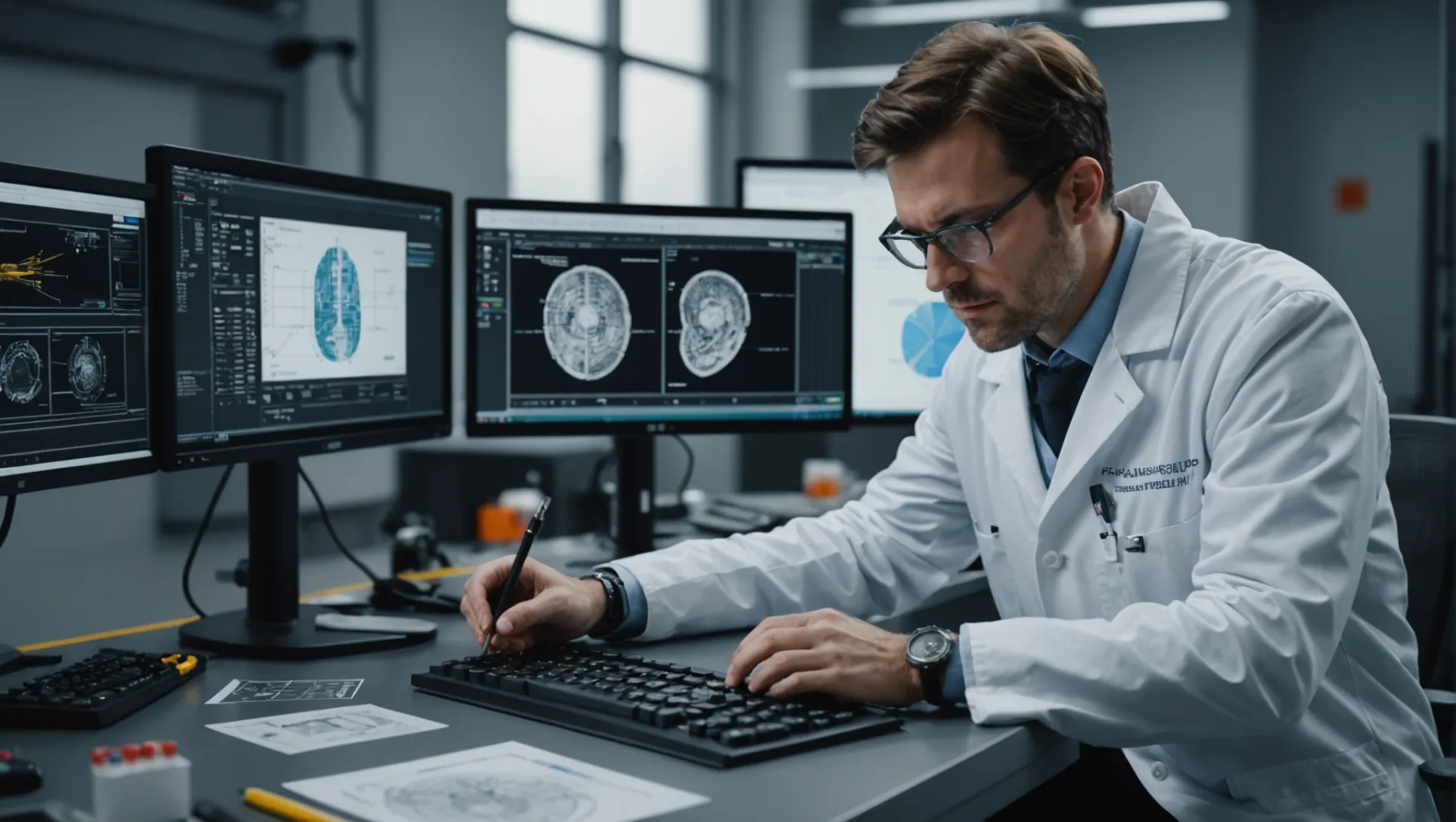
गेट स्थानों और संख्याओं को अनुकूलित करना
पिघली हुई सामग्री को साँचे में समान रूप से वितरित करने के लिए रणनीतिक स्थान और द्वारों की संख्या महत्वपूर्ण है। मोटे उत्पाद खंडों में या कमजोर किनारों से दूर गेट स्थापित करने से, भरने के दौरान इन किनारों पर प्रभाव बल कम हो जाता है। गेटों की संख्या बढ़ाने से स्थानीय तनाव को कम करते हुए अधिक समान भराव सुनिश्चित किया जा सकता है। उदाहरण के लिए, बड़े या जटिल डिज़ाइनों में, एकाधिक द्वार प्रवाह को संतुलित करने और फ्रैक्चर को रोकने में मदद कर सकते हैं।
मोल्ड संरचना को बढ़ाना
किनारों और कोनों पर तनाव सांद्रता को कम करने का एक प्रभावी तरीका फ़िलेट त्रिज्या को बढ़ाना है। नुकीले कोने तनाव सांद्रक होते हैं और उनमें फ्रैक्चर होने का खतरा हो सकता है। एक बड़ा फ़िललेट त्रिज्या तनाव को अधिक समान रूप से वितरित करता है, जिससे समग्र उत्पाद शक्ति बढ़ती है। इसके अलावा, एक अनुकूलित डिमोल्डिंग तंत्र 3 आवश्यक है। उचित रूप से डिज़ाइन किए गए डिमोल्डिंग ढलान और तरीके रिलीज के दौरान क्षति को रोकते हैं, किनारे की अखंडता को बनाए रखते हैं।
एक समान मोल्ड तापमान सुनिश्चित करना
सभी क्षेत्रों में एक समान मोल्ड तापमान बनाए रखने से असमान सिकुड़न से बचने में मदद मिलती है, जो तनाव एकाग्रता का एक सामान्य कारण है जो किनारे के फ्रैक्चर का कारण बनता है। समान तापमान वितरण सुनिश्चित करने के लिए मोल्ड शीतलन प्रणाली को परिष्कृत करके इसे प्राप्त किया जा सकता है। उन सामग्रियों के लिए जो विशेष रूप से कठोर या भंगुर हैं, मोल्ड तापमान में मामूली वृद्धि से पिघली हुई तरलता में सुधार हो सकता है, जिससे तनाव कम हो सकता है।
केस स्टडी: मोल्ड डिजाइन रणनीतियों को लागू करना
एक निर्माता पर विचार करें जो अपने प्लास्टिक आवासों में बार-बार होने वाले किनारे के फ्रैक्चर का सामना कर रहा है। अपने साँचे के डिज़ाइन का पुनर्मूल्यांकन करके, उन्होंने गेट को पतले वर्गों से दूर कर दिया और महत्वपूर्ण क्षेत्रों में एक बड़ा फ़िलेट त्रिज्या शामिल किया। इसके अतिरिक्त, उन्होंने समान मोल्ड तापमान बनाए रखने के लिए शीतलन चैनलों को समायोजित किया। परिणाम स्वरूप दोषों में उल्लेखनीय कमी आई, जिससे पता चला कि कैसे लक्षित मोल्ड डिज़ाइन 4 रणनीतियाँ किनारे के फ्रैक्चर को प्रभावी ढंग से रोक सकती हैं।
गेट स्थान को अनुकूलित करने से किनारे के फ्रैक्चर कम हो जाते हैं।सत्य
रणनीतिक रूप से रखे गए गेट पिघली हुई सामग्री को समान रूप से वितरित करते हैं, जिससे तनाव कम होता है।
फ़िलेट त्रिज्या बढ़ने से तनाव एकाग्रता बढ़ती है।असत्य
बड़ी पट्टिका त्रिज्या तनाव को अधिक समान रूप से वितरित करती है, जिससे एकाग्रता कम हो जाती है।
किनारे के फ्रैक्चर को कम करने में सामग्री चयन की क्या भूमिका है?
इंजेक्शन मोल्डिंग के दौरान किनारे के फ्रैक्चर को कम करने के लिए सामग्री का चयन महत्वपूर्ण है, जिससे उत्पाद की गुणवत्ता पर महत्वपूर्ण प्रभाव पड़ता है।
उच्च कठोरता और उचित तरलता वाली सामग्रियों का चयन तनाव को कम करता है और इंजेक्शन मोल्डिंग में किनारे के फ्रैक्चर को रोकता है। भौतिक गुणों को बढ़ाने के लिए संशोधित प्लास्टिक और सुदृढ़ीकरण फाइबर पर विचार करें।
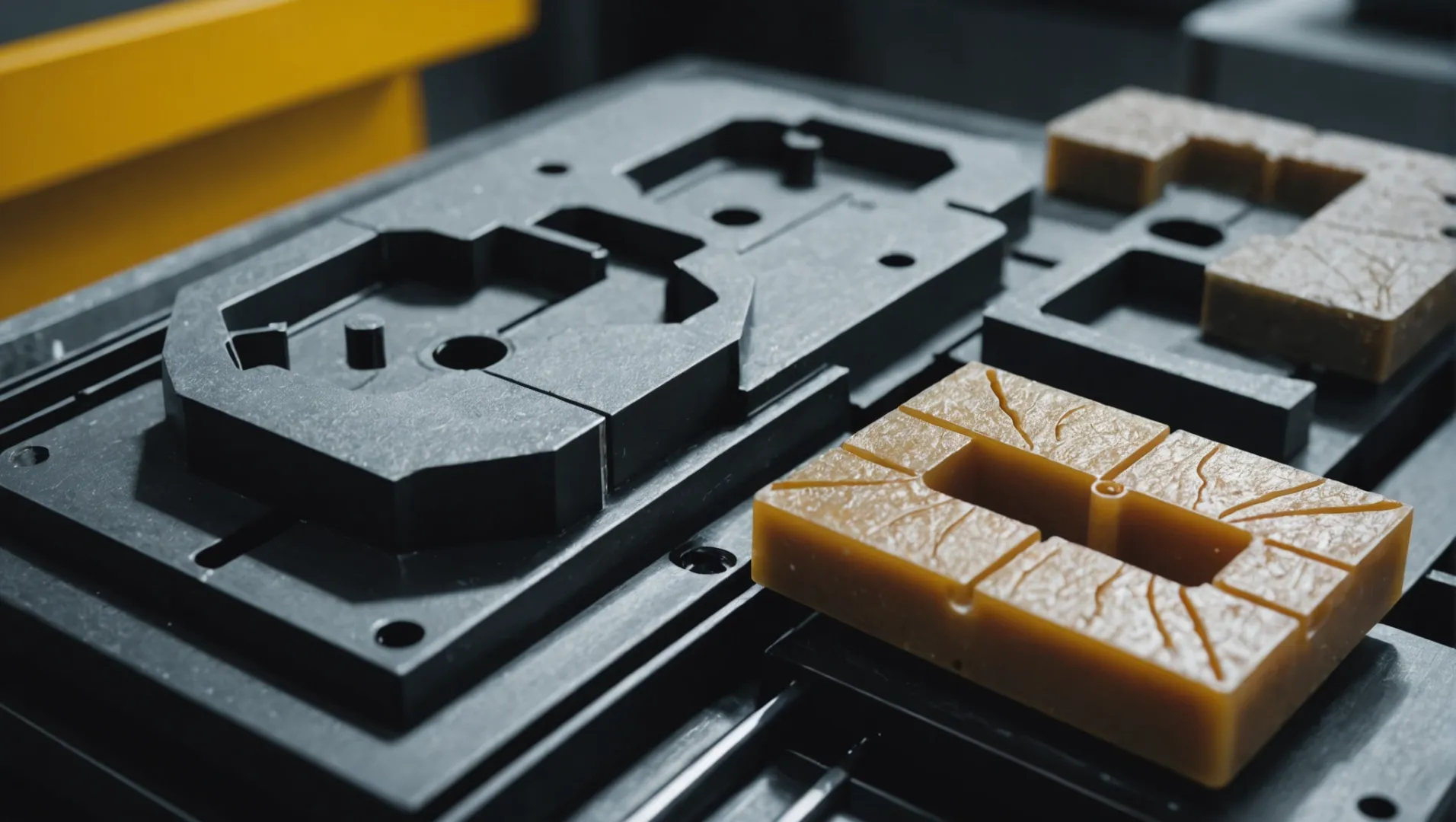
सामग्री की कठोरता का महत्व
इंजेक्शन मोल्डिंग के लिए सामग्री का चयन करते समय, प्राथमिक विचारों में से एक उनकी कठोरता होनी चाहिए। उच्च कठोरता वाली सामग्री प्रभाव को बेहतर ढंग से अवशोषित कर सकती है और तनाव के तहत टूटने की संभावना कम होती है। उदाहरण के लिए, संशोधित प्लास्टिक 5 या अतिरिक्त मजबूत फाइबर वाले प्लास्टिक का उपयोग पूरे उत्पाद में तनाव को अधिक समान रूप से वितरित करके किनारे के फ्रैक्चर की घटनाओं को नाटकीय रूप से कम कर सकता है।
पॉलीकार्बोनेट या पॉलीप्रोपाइलीन के कुछ ग्रेड जैसी सामग्रियों को अक्सर उन अनुप्रयोगों के लिए पसंद किया जाता है जिनके लिए उच्च प्रभाव प्रतिरोध की आवश्यकता होती है। ये सामग्रियां इंजेक्शन मोल्डिंग प्रक्रिया के दौरान लगने वाले यांत्रिक तनाव का सामना कर सकती हैं, जिससे वे किनारे के फ्रैक्चर वाले उत्पादों के लिए आदर्श बन जाती हैं।
भौतिक तरलता की भूमिका
सामग्री चयन में तरलता एक अन्य महत्वपूर्ण कारक है। अच्छी तरलता वाली सामग्री साँचे को अधिक समान रूप से भर सकती है, जिससे तनाव सांद्रता की संभावना कम हो जाती है जिससे फ्रैक्चर होता है। सांचे के भीतर पर्याप्त सामग्री प्रवाह सुनिश्चित करने से तेज किनारों और पतले खंडों को कम किया जाता है जिनके टूटने का खतरा होता है।
तरलता में सुधार के लिए, निर्माता उन सामग्रियों का चयन कर सकते हैं जिन्हें प्लास्टिसाइज़र या अन्य एडिटिव्स के साथ संशोधित किया गया है। यह पिघल को जटिल सांचों को आसानी से भरने की अनुमति देता है, जिससे दोषों का खतरा कम हो जाता है।
सामग्री की गुणवत्ता को नियंत्रित करना
सही सामग्री चुनने के अलावा उसकी गुणवत्ता को नियंत्रित करना भी उतना ही महत्वपूर्ण है। नमी की मात्रा और अशुद्धियाँ इंजेक्शन मोल्डिंग के दौरान सामग्रियों के प्रदर्शन को महत्वपूर्ण रूप से प्रभावित कर सकती हैं। नमी के कारण पिघले हुए हिस्से में बुलबुले बन सकते हैं, जिससे आंतरिक तनाव और फ्रैक्चर का खतरा बढ़ सकता है। इस प्रकार, यह सुनिश्चित करना महत्वपूर्ण है कि उपयोग से पहले सामग्री पूरी तरह से सूख जाए।
इसके अतिरिक्त, अशुद्धियों की जांच से उन दोषों को रोकने में मदद मिलती है जो उत्पाद संरचना को कमजोर कर सकते हैं। सख्त गुणवत्ता नियंत्रण उपायों का पालन करने वाले प्रतिष्ठित आपूर्तिकर्ताओं की सामग्रियों का उपयोग करना उत्पाद की निरंतर गुणवत्ता बनाए रखने के लिए एक सक्रिय दृष्टिकोण है।
व्यावहारिक अनुप्रयोग: एक केस स्टडी
इंजेक्शन मोल्डिंग का उपयोग करके ऑटोमोटिव घटकों का उत्पादन करने वाले निर्माता पर विचार करें। प्रारंभ में, भंगुर पॉलिमर के उपयोग के कारण उन्हें बार-बार किनारे के फ्रैक्चर का सामना करना पड़ा। ग्लास फाइबर के साथ प्रबलित उच्च-क्रूरता वाली सामग्री पर स्विच करके, उन्होंने दोषों में उल्लेखनीय कमी देखी। इंजेक्शन पैरामीटर 6 के साथ मिलकर इस परिवर्तन से उत्पाद स्थायित्व में सुधार हुआ और अपशिष्ट में कमी आई।
सामग्रियों के रणनीतिक चयन पर ध्यान केंद्रित करके, निर्माता न केवल किनारे के फ्रैक्चर को कम कर सकते हैं, बल्कि समग्र उत्पादन दक्षता और उत्पाद की दीर्घायु को भी बढ़ा सकते हैं।
उच्च-क्रूरता वाली सामग्री किनारे के फ्रैक्चर को रोकती है।सत्य
उच्च कठोरता वाली सामग्री प्रभाव को बेहतर ढंग से अवशोषित करती है, जिससे फ्रैक्चर का जोखिम कम हो जाता है।
इंजेक्शन मोल्डिंग में तरलता अप्रासंगिक है।असत्य
अच्छी तरलता एक समान मोल्ड भरने को सुनिश्चित करती है, तनाव और फ्रैक्चर को कम करती है।
नियमित रखरखाव इंजेक्शन मोल्डिंग में किनारे के फ्रैक्चर को कैसे रोक सकता है?
किनारे के फ्रैक्चर को रोकने और लगातार उत्पाद की गुणवत्ता सुनिश्चित करने के लिए इंजेक्शन मोल्डिंग उपकरण का नियमित रखरखाव महत्वपूर्ण है। जानें कि कैसे नियमित जांच और रखरखाव दोषों को कम कर सकता है।
नियमित रखरखाव तनाव और दोषों से बचते हुए, उपकरण के सुचारू संचालन को सुनिश्चित करके किनारे के फ्रैक्चर को रोकता है। मुख्य कार्यों में सफाई, स्नेहन और भाग निरीक्षण शामिल हैं।

उपकरण रखरखाव का महत्व
यह सुनिश्चित करना कि इंजेक्शन मोल्डिंग मशीन इष्टतम स्थिति में है, किनारे के फ्रैक्चर को रोकने के लिए मौलिक है। नियमित रखरखाव से टूट-फूट जैसे मुद्दों की पहचान करने में मदद मिलती है जो खराबी का कारण बन सकते हैं। उदाहरण के लिए, घिसे हुए स्क्रू या नोजल से मोल्डिंग के दौरान असमान दबाव हो सकता है, जिससे उत्पाद के किनारों पर फ्रैक्चर का खतरा बढ़ जाता है।
नियमित रखरखाव चेकलिस्ट
- सफाई: सांचों और मशीन के हिस्सों की नियमित सफाई अवशेषों को जमा होने से रोकती है जो सामग्री के प्रवाह को प्रभावित कर सकते हैं, जिससे उत्पाद के किनारों पर तनाव जमा हो सकता है।
- स्नेहन: गतिशील भागों का उचित स्नेहन घर्षण और घिसाव को कम करता है, सुचारू संचालन सुनिश्चित करता है और विफलता के संभावित बिंदुओं को रोकता है।
- टूट-फूट का निरीक्षण: लगातार निरीक्षण से घिसे-पिटे घटकों की समय पर पहचान संभव हो पाती है। परिचालन संबंधी अक्षमताओं या दोषों का कारण बनने से पहले इन हिस्सों को बदल दें।
रखरखाव गतिविधि | आवृत्ति | फ़ायदे |
---|---|---|
सफाई | साप्ताहिक | अवशेष निर्माण को कम करता है |
स्नेहन | द्वि-साप्ताहिक | घर्षण और घिसाव को कम करता है |
निरीक्षण | महीने के | विफलता से पहले घिसाव की पहचान करता है |
साँचे का रखरखाव
उचित साँचे की देखभाल भी उतनी ही आवश्यक है। साँचे को नियमित रूप से साफ किया जाना चाहिए और पहनने के लिए जाँच की जानी चाहिए। एक क्षतिग्रस्त मोल्ड इंजेक्शन प्रक्रिया के दौरान असमान दबाव वितरण पैदा कर सकता है, जिससे किनारों पर स्थानीय तनाव पैदा हो सकता है।
- मोल्ड की सफाई: अवशेषों से बचने के लिए नियमित रूप से मोल्डों को साफ करें जो मोल्ड किए गए उत्पाद की गुणवत्ता और अखंडता को प्रभावित कर सकते हैं।
- घिसाव का निरीक्षण: घिसाव या क्षति के संकेतों के लिए मोल्ड सतहों का निरीक्षण करें जिससे असमान दबाव अनुप्रयोग हो सकता है।
- स्नेहन: मोल्डिंग प्रक्रिया के दौरान अनावश्यक घर्षण और क्षति से बचने के लिए सुनिश्चित करें कि मोल्ड भागों को ठीक से चिकनाई दी गई है।
प्रशिक्षण एवं जागरूकता
उपकरणों के रखरखाव में प्रशिक्षित कर्मियों की भूमिका भी उतनी ही महत्वपूर्ण है। संभावित मुद्दों को पहले से ही संबोधित करने के लिए ऑपरेटरों को उपकरण प्रबंधन और रखरखाव प्रक्रियाओं में अच्छी तरह से पारंगत होना चाहिए। प्रशिक्षण कार्यक्रमों पर ध्यान केंद्रित करना चाहिए:
- उत्पाद की गुणवत्ता पर उपकरण स्थितियों के प्रभाव को समझना।
- नियमित जांच के दौरान पहचानी गई किसी भी छोटी विसंगति की भरपाई के लिए मापदंडों को समायोजित करना सीखना।
एक व्यापक रखरखाव रणनीति को लागू करके, आप न केवल अपने उपकरण का जीवनकाल बढ़ाते हैं बल्कि न्यूनतम दोषों के साथ लगातार उच्च गुणवत्ता वाले उत्पाद भी तैयार करते हैं। ऐसे सक्रिय उपाय ऐसे उद्योग में महत्वपूर्ण हैं जहां सटीकता और विश्वसनीयता सर्वोपरि है।
नियमित सफाई से इंजेक्शन मोल्डिंग में किनारे के फ्रैक्चर कम हो जाते हैं।सत्य
सफाई अवशेषों को जमा होने से रोकती है, उत्पाद के किनारों पर तनाव को कम करती है।
स्नेहन छोड़ने से इंजेक्शन मोल्डिंग गुणवत्ता पर कोई प्रभाव नहीं पड़ता है।असत्य
स्नेहन की कमी से घर्षण बढ़ता है, जिससे घिसाव और संभावित दोष उत्पन्न होते हैं।
निष्कर्ष
इन रणनीतियों को अपनाकर, मैं अपनी इंजेक्शन मोल्डिंग प्रक्रिया में किनारे के फ्रैक्चर को काफी हद तक कम कर सकता हूं, जिससे उत्पाद की गुणवत्ता और दक्षता बेहतर हो सकती है।
-
किनारे के फ्रैक्चर को कम करने के लिए इंजेक्शन की गति को ठीक करना सीखें। पहला कदम: V1, V2 और V3 को एक ही गति पर सेट करके शुरू करें, फिर धीरे-धीरे इंजेक्शन की गति को लगभग 5% से 5% तक बढ़ाएं, ... ↩
-
समझें कि कुशल ऑपरेटर गुणवत्ता नियंत्रण के लिए महत्वपूर्ण क्यों हैं: निरंतर प्रशिक्षण मोल्ड निर्माताओं को टूलींग निर्णय लेने में मदद करता है और उच्च गुणवत्ता वाले मोल्डों को कुशलतापूर्वक मशीन करने के लिए नवीनतम कटिंग टूल का उचित उपयोग करता है। ↩
-
उत्पाद किनारों की रक्षा करने वाली विभिन्न डिमोल्डिंग तकनीकों का अन्वेषण करें: इंजेक्शन मोल्डिंग में कुशल डिमोल्डिंग तंत्र के लिए मोल्ड डिजाइन में प्रमुख कारकों का पता लगाएं, जिसमें भाग ज्यामिति, सामग्री गुण और उत्पादन शामिल हैं ... ↩
-
पता लगाएं कि कैसे विशिष्ट डिज़ाइन परिवर्तन तनाव जोखिमों को कम कर सकते हैं: फ़िललेट्स कोनों या अनुभागों के परिवर्तनों पर तनाव एकाग्रता को कम करते हैं क्योंकि वे लागू तनाव को बड़े सतह क्षेत्रों में संचारित करते हैं। ↩
-
देखें कि कैसे संशोधित प्लास्टिक कठोरता को बढ़ाता है और फ्रैक्चर के जोखिम को कम करता है: इंजेक्शन मोल्डिंग अत्यधिक जटिल भागों को संभाल सकता है, एकरूपता प्रदान करता है, और लाखों लगभग समान भागों को बनाने की क्षमता प्रदान करता है। ↩
-
फ्रैक्चर को रोकने के लिए इंजेक्शन मापदंडों को परिष्कृत करने की तकनीक सीखें।: 1. तापमान नियंत्रण: · 2. इंजेक्शन की गति: · 3. ठंडा करने का समय: · 4. प्लास्टिक सामग्री का चयन: · 5. पेंच की गति और पिछला दबाव: · 6. इंजेक्शन ... ↩