ढले हुए उत्पादों में छोटी-छोटी खामियाँ अक्सर सब कुछ बर्बाद कर देती हैं। एक केक पकाने की कल्पना करें। बस एक गलती सब कुछ बर्बाद कर देती है.
इंजेक्शन मोल्डिंग में फ्लैश, सिकुड़न, वेल्ड निशान, प्रवाह निशान और चांदी की धारियाँ अक्सर होती हैं। ये खामियां अक्सर सामने आती रहती हैं. समस्याएँ बहुत अधिक दबाव, विभिन्न मोटाई वाली दीवारों, ख़राब जुड़ाव या मोल्ड प्रक्रिया के दौरान फँसी गैसों से आती हैं। इनसे उत्पाद की गुणवत्ता और प्रदर्शन में कमी आती है। गुणवत्ता प्रभावित होती है। प्रदर्शन गिरता है.
जब मैंने मोल्ड उद्योग में अपनी यात्रा शुरू की, तो हमारी इंजेक्शन-मोल्ड वस्तुओं में खामियां एक अंतहीन पहेली की तरह लग रही थीं। प्रत्येक दोष से मोल्डिंग प्रक्रिया के दौरान आवश्यक सावधानीपूर्वक संतुलन के बारे में कुछ नया पता चला। फ्लैश तब होता है जब बहुत अधिक दबाव या गैप के कारण प्लास्टिक मोल्ड पर फैल जाता है। यह केक पर बहुत अधिक आइसिंग निचोड़ने जैसा है। सिकुड़न वाले डेंट मुझे याद दिलाते हैं कि कैसे कभी-कभी कुकीज़ असमान रूप से ठंडी हो जाती हैं, जिससे उभार आ जाते हैं। दोनों असमान वितरण से आते हैं।
वेल्ड के निशान वहां दिखाई देते हैं जहां गर्म प्लास्टिक की विभिन्न धाराएं मिलती हैं लेकिन अच्छी तरह से मिश्रित नहीं होती हैं, जैसे कि दो रंगों के पेंट को मिलाने और धारियाँ बनने पर। इसी तरह, प्रवाह के निशान तब होते हैं जब प्लास्टिक मोल्ड के माध्यम से आसानी से नहीं चलता है, जिससे एक लहरदार पैटर्न बनता है।
चांदी की धारियाँ एक और चुनौती हैं। ये कष्टप्रद गैस लाइनें तब दिखाई देती हैं जब नमी या धुआं अंदर घुस जाता है। वे आपके प्रयासों का मज़ाक उड़ाते हैं। तापमान, दबाव या सामग्री की तैयारी में एक पैनी नजर और सावधानीपूर्वक बदलाव इन खामियों को उत्पाद के रूप और कार्य को नुकसान पहुंचाने से रोकते हैं। व्यक्ति को वास्तव में इन दोषों की भविष्यवाणी करना और उन्हें ठीक करना सीखना चाहिए। उन्हें संभालना सीखना उतना ही महत्वपूर्ण है जितना उन्हें जानना, इसलिए प्रत्येक उत्पाद उन उच्च मानकों को पूरा करता है जो हमने संभवतः अपने लिए निर्धारित किए हैं।
मोल्डिंग में अत्यधिक दबाव के कारण फ्लैश होता है।सत्य
फ़्लैश अतिरिक्त सामग्री के साँचे से बाहर निकलने के कारण होता है।
दीवार की मोटाई में भिन्नता से सिकुड़न अप्रभावित रहती है।असत्य
सिकुड़न असमान दीवार की मोटाई से प्रभावित हो सकती है, जिससे शीतलन प्रभावित हो सकता है।
फ्लैश इंजेक्शन मोल्डेड उत्पादों को कैसे प्रभावित करता है?
प्लास्टिक उत्पादों में कभी-कभी कष्टप्रद टुकड़े चिपक जाते हैं। फैक्ट्रियाँ प्लास्टिक की वस्तुओं को आकार देने के लिए सांचों का उपयोग करती हैं। लेकिन, जब सांचा पूरी तरह से फिट नहीं होता है, तो अतिरिक्त टुकड़े बन जाते हैं। इन्हें "फ्लैश" कहा जाता है। फ्लैश बहुत होता है. मशीनें अधिकांश फ़्लैश काट देती हैं, लेकिन छोटे टुकड़े रह सकते हैं। फ़ैक्टरियाँ कभी-कभी जल्दी करती हैं। फिर, और टुकड़े चिपक जाते हैं। त्रुटिपूर्ण या घिसे-पिटे साँचे भी इस समस्या का कारण बनते हैं। गुणवत्ता जांच से बचा हुआ खाना कम हो जाता है, लेकिन सभी नोटिस से बच नहीं पाते।
इंजेक्शन मोल्डेड उत्पादों पर फ्लैश अतिरिक्त प्लास्टिक है जो लुक को खराब करता है। श्रमिकों को इसे दूर करना होगा, जिससे उत्पादन लागत में वृद्धि होगी। अत्यधिक इंजेक्शन का दबाव इसका कारण बनता है। खराब मोल्ड संरेखण से भी फ्लैश होता है। इसका असर असेंबली पर पड़ता है. उत्पाद की गुणवत्ता प्रभावित होती है।

उपस्थिति पर फ़्लैश का प्रभाव
फ्लैश प्लास्टिक का एक अतिप्रवाह है जो इंजेक्शन प्रक्रिया के दौरान मोल्ड से निकल जाता है। मोल्ड पार्टिंग सतह 1 के कारण होता है । जब सांचा दबाव को नियंत्रित नहीं कर पाता, तो प्लास्टिक दरारों से बाहर निकल जाता है, ठीक उसी तरह जैसे टूटे हुए बांध से पानी निकल रहा हो।
कारण | विवरण |
---|---|
अत्यधिक दबाव | उच्च दबाव प्लास्टिक को अंतराल के माध्यम से पिघला देता है। |
अपर्याप्त क्लैम्पिंग | कमजोर क्लैम्पिंग प्लास्टिक रिसाव की अनुमति देती है। |
असमान साँचे की सतह | गलत संरेखित सतहें फ़्लैश निर्माण के लिए अंतराल बनाती हैं। |
आर्थिक और कार्यात्मक प्रभाव
फ्लैश की उपस्थिति न केवल उत्पाद की उपस्थिति को खराब करती है बल्कि अतिरिक्त ट्रिमिंग प्रक्रिया की भी आवश्यकता होती है, जिससे उत्पादन लागत बढ़ जाती है। यह दोष उत्पादों के असेंबली प्रदर्शन में भी बाधा उत्पन्न कर सकता है, विशेष रूप से उपभोक्ता इलेक्ट्रॉनिक्स जैसे सटीक फिट की आवश्यकता वाले उत्पादों में। उदाहरण के लिए, जैकी 2 , एक उत्पाद डिजाइनर, को निर्बाध असेंबली सुनिश्चित करने के लिए मोल्ड डिजाइन करते समय संभावित फ्लैश को ध्यान में रखना चाहिए।
प्रभाव | विवरण |
---|---|
बढ़ी हुई लागत | अतिरिक्त ट्रिमिंग से उत्पादन खर्च बढ़ जाता है। |
विधानसभा मुद्दे | अतिरिक्त सामग्री के कारण असेंबली के दौरान मिसफिट। |
रोकथाम और कमी के तरीके
फ्लैश को रोकना मैराथन के लिए तैयार होने जैसा है - आपको अच्छी योजनाओं और रखरखाव की आवश्यकता है। मशीनों का नियमित अंशांकन वास्तव में सहायक है; यात्रा से पहले अपने उपकरण को पूरी तरह से समायोजित करने के बारे में सोचें—यह बिल्कुल सांचों को समायोजित करने जैसा है। उचित संरेखण और दबाव नियंत्रण उन कष्टप्रद अतिप्रवाहों को कम करता है।
फ्लैश होने से रोकने के लिए, निर्माताओं को इष्टतम इंजेक्शन दबाव बनाए रखने और मोल्ड भागों के उचित संरेखण को सुनिश्चित करने पर ध्यान केंद्रित करना चाहिए। दोषों को कम करने के लिए उपकरणों का नियमित रखरखाव और अंशांकन महत्वपूर्ण है।
रणनीति | फ़ायदा |
---|---|
नियमित अंशांकन | सुनिश्चित करता है कि उपकरण आदर्श सेटिंग्स पर संचालित हो। |
समुचित संरेखण | उन अंतरालों को कम करता है जो फ़्लैश निर्माण का कारण बनते हैं। |
दबाव नियंत्रण | सामग्री के निरंतर प्रवाह को बनाए रखता है, अतिप्रवाह को रोकता है। |
इन तरीकों को समझने से जैकी 3 और मेरे जैसे डिजाइनरों को डिज़ाइन को स्मार्ट तरीके से समायोजित करने की अनुमति मिलती है, जिससे यह सुनिश्चित होता है कि हमारे उत्पाद अच्छे दिखते हैं और अवांछित अतिरिक्त चीजों के बिना ठीक से काम करते हैं।
फ्लैश से मोल्डिंग में उत्पादन लागत बढ़ जाती है।सत्य
फ़्लैश को अतिरिक्त ट्रिमिंग की आवश्यकता होती है, जिससे उत्पादन व्यय बढ़ता है।
असमान मोल्ड सतहें फ्लैश गठन को रोकती हैं।असत्य
गलत संरेखित सतहें अंतराल पैदा करती हैं, जिससे फ्लैश का निर्माण होता है।
इंजेक्शन मोल्डिंग में सिकुड़न एक चिंता का विषय क्यों है?
क्या आपने कभी इस बारे में सोचा है कि आपके इंजेक्शन-मोल्ड वाले हिस्से कभी-कभी डिज़ाइन विनिर्देशों से भिन्न क्यों होते हैं? सिकुड़न अक्सर इस गुप्त समस्या का कारण बनती है। इससे गुणवत्ता प्रभावित हो सकती है. गुणवत्ता वास्तव में मायने रखती है.
इंजेक्शन मोल्डिंग में सिकुड़न असमान शीतलन और सामग्री संकुचन के कारण होती है। ये कारक आकार की सटीकता और उपस्थिति को प्रभावित करते हैं। डेंट जैसी खामियाँ हो सकती हैं। मोल्ड डिज़ाइन अनुकूलन और सही सामग्री का चयन इन समस्याओं को काफी हद तक कम कर देता है। सिकुड़न से समस्याएँ आम हैं।
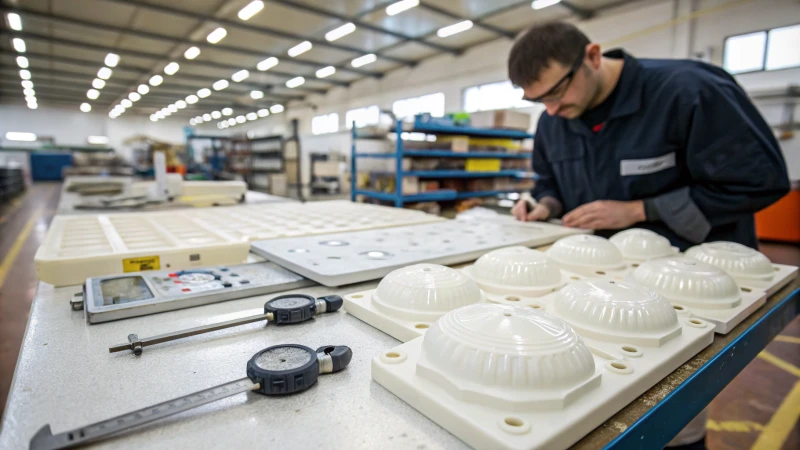
इंजेक्शन मोल्डिंग में सिकुड़न को समझना
इसे चित्रित करें: आप एक आदर्श भाग को डिज़ाइन करने में बहुत समय व्यतीत करते हैं, लेकिन जब यह साँचे से बाहर आता है, तो यह थोड़ा अलग दिखता है। यह सिकुड़न 4 । यह तब होता है जब प्लास्टिक, पहले गर्म और तरल, एक सांचे में चला जाता है और फिर ठंडा होकर सख्त हो जाता है। जैसे-जैसे यह ठंडा होता है, यह छोटा होता जाता है। ऐसा कई कारणों से हो सकता है, जैसे उपयोग की जाने वाली सामग्री का प्रकार, सांचे का डिज़ाइन और सामग्री कितनी तेजी से ठंडी होती है।
सिकुड़न के कारण
सिकुड़न का मुख्य कारण तापीय संकुचन है। पॉलिमर ठंडा होने पर छोटे हो जाते हैं। एक केक पकाने के बारे में सोचो. अलग-अलग मोटाई वाला केक असमान रूप से पकता है। यहां, मोटे हिस्से धीमी गति से ठंडे होते हैं और अधिक छोटे हो जाते हैं। इससे डेंट बन सकते हैं. सामग्री का प्रकार भी मायने रखता है; क्रिस्टलीय प्लास्टिक अनाकार प्लास्टिक की तुलना में अधिक सिकुड़ते हैं।
सामग्री प्रकार | विशिष्ट संकोचन दर |
---|---|
अनाकार प्लास्टिक | 0.5% – 1% |
क्रिस्टलीय प्लास्टिक | 1.5% – 2% |
उत्पाद की गुणवत्ता पर प्रभाव
सिकुड़न सिर्फ दिखावे से ज्यादा प्रभावित करती है। एक चमकदार कार के इंटीरियर की कल्पना करें जहां हर सतह सही दिखनी चाहिए। यहां तक कि एक छोटा सा डेंट भी लुक को खराब कर सकता है और संभवतः पार्ट असेंबली को प्रभावित कर सकता है। इस प्रकार की खराबी के कारण महंगा सुधार हो सकता है और उत्पादन धीमा हो सकता है।
सिकुड़न कम करना
अच्छी खबर मौजूद है! स्मार्ट डिज़ाइन और सही सामग्री से सिकुड़न कम हो जाती है। समान दीवार की मोटाई का उपयोग करने या शीतलन गति को बदलने से बहुत मदद मिलती है। मोल्ड तापमान नियंत्रण प्रणाली जैसी आधुनिक प्रौद्योगिकियाँ शीतलन नियंत्रण में सुधार करती हैं।
अधिक विस्तृत रणनीतियों के लिए, एक मोल्ड डिज़ाइन विशेषज्ञ से परामर्श करने से विशिष्ट उत्पादन चुनौतियों के अनुरूप समाधान प्रदान किया जा सकता है। याद रखें कि प्रत्येक कारक - मोल्ड डिज़ाइन से लेकर सामग्री की पसंद तक - सिकुड़न को अलग तरह से प्रभावित करेगा, जिससे सफल इंजेक्शन मोल्डिंग 5 ।
क्रिस्टलीय प्लास्टिक अनाकार प्लास्टिक की तुलना में अधिक सिकुड़ते हैं।सत्य
अनाकार प्लास्टिक की तुलना में क्रिस्टलीय प्लास्टिक में सिकुड़न दर 1.5% -2% अधिक होती है।
समान दीवार की मोटाई इंजेक्शन मोल्डिंग में सिकुड़न को कम करती है।सत्य
लगातार दीवार की मोटाई समान शीतलन सुनिश्चित करती है, अंतर संकोचन को कम करती है।
वेल्ड निशान कैसे बनते हैं और उन्हें रोकने के लिए क्या किया जा सकता है?
क्या आपने कभी किसी प्लास्टिक की वस्तु को घूरकर देखा है और उसकी शक्ल खराब करने वाली अजीब रेखाओं पर सवाल उठाया है?
वेल्ड के निशान तब दिखाई देते हैं जब गर्म प्लास्टिक अलग-अलग रास्तों में चलता है और फिर सांचे में एक साथ आता है। यह कमजोरियों का कारण बनता है। मोल्ड डिज़ाइन को समायोजित करने से इन्हें बनने से रोकने में मदद मिलती है। प्रोसेसिंग सेटिंग्स बदलने से भी उनमें कमी आती है। लगातार सामग्री की गुणवत्ता वास्तव में महत्वपूर्ण है। बहुत ज़रूरी।
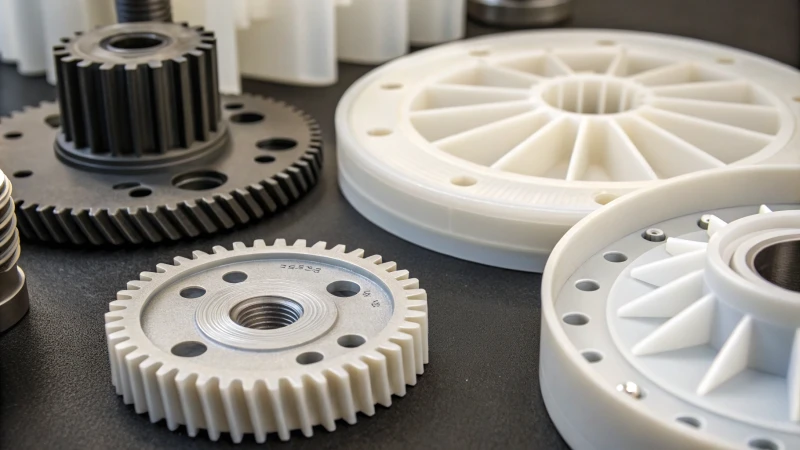
वेल्ड मार्क्स के निर्माण को समझना
इस परिदृश्य की कल्पना करें: एक परियोजना सटीकता की मांग करती है और सही दिखती है। अचानक, सतह पर एक रेखा दिखाई देती है - एक वेल्ड का निशान। यह एक दीवार को पेंट करने और उस रेखा को देखने के समान है जहां रोलर छूट गया था। वेल्ड के निशान तब दिखाई देते हैं जब एक सांचे में पिघला हुआ प्लास्टिक बाधाओं के चारों ओर घूमता है और धाराओं में विभाजित हो जाता है, फिर अपूर्ण रूप से एक साथ आता है। यह अक्सर जटिल आकृतियों या छेद वाले डिज़ाइनों में होता है।
यहां कारणों :
कारण | विवरण |
---|---|
साँचे का डिज़ाइन | जटिल ज्यामिति या पतली दीवारें पिघल को विभाजित करने और अनुचित तरीके से फिर से जुड़ने का कारण बन सकती हैं। |
सामग्री प्रवाह दर | असमान प्रवाह दर के कारण प्लास्टिक धाराओं का असंगत विलय होता है। |
पिघलने का तापमान | कम तापमान के परिणामस्वरूप जंक्शन पर आणविक श्रृंखलाओं का खराब संलयन होता है। |
वेल्ड मार्क्स को रोकने के तरीके
मैंने इस मुद्दे का सामना किया है, देर रात तक डिज़ाइन बदलना, छोटे बदलावों को समझना वास्तव में परिणामों को प्रभावित करता है। ये तकनीकें मेरे लिए काम आईं:
-
मोल्ड डिज़ाइन में सुधार करें
- प्रवाह विभाजन को कम करने के लिए आकृतियों को सरल बनाएं।
- समान प्रवाह के लिए संतुलित रनर और गेट का उपयोग करें।
- फंसी हवा को बाहर निकालने के लिए वेंटिंग सिस्टम जोड़ें।
-
प्रोसेसिंग सेटिंग्स बदलें
- प्रवाह रुकने को कम करने के लिए इंजेक्शन की गति बढ़ाएं।
- सर्वोत्तम संलयन के लिए उचित पिघला हुआ तापमान सुनिश्चित करें।
- स्थिर प्रवाह के लिए इंजेक्शन दबाव 6 को देखें
-
सामग्री की गुणवत्ता रखें
- समान गुणों वाले उच्च गुणवत्ता वाले प्लास्टिक का उपयोग करें।
- असमान गलनांक वाली पुनर्चक्रित सामग्रियों से बचें।
- गैस के छींटों को रोकने के लिए प्लास्टिक को सूखा रखें, जिससे वेल्ड के निशान खराब हो जाते हैं।
इन समस्याओं को ठीक करके, मैंने देखा कि कैसे वेल्ड के निशान वास्तव में कम हो जाते हैं, जिससे उत्पाद दिखने में और लंबे समय तक चलने में बेहतर होते हैं। अधिक उन्नत युक्तियों के लिए, मेरा सुझाव है कि मोल्ड डिज़ाइन सिद्धांत 7 और प्रसंस्करण तकनीकी समायोजन की जाँच करें। ये विचार संभवतः आपकी उत्पादन विधियों को बढ़ाएंगे और आपके काम की गुणवत्ता बढ़ाएंगे।
कम पिघला हुआ तापमान वेल्ड निशानों में खराब संलयन का कारण बनता है।सत्य
कम तापमान के कारण जंक्शनों पर अपूर्ण आणविक संलयन होता है।
उच्च गुणवत्ता वाला प्लास्टिक वेल्ड मार्क की घटना को बढ़ाता है।असत्य
समान गुणों वाला उच्च गुणवत्ता वाला प्लास्टिक वेल्ड निशान को कम करता है।
चाँदी की धारियाँ उत्पाद की पारदर्शिता को कैसे प्रभावित करती हैं?
क्या आपने कभी स्पष्ट प्लास्टिक वस्तुओं पर उन कष्टप्रद चांदी की रेखाओं को देखा है? वे न केवल बदसूरत हैं बल्कि पारदर्शिता को भी बर्बाद करते हैं।
ढले हुए प्लास्टिक में चांदी की रेखाएं अंदर नमी या गैसों से आती हैं। ये रेखाएँ प्लास्टिक को कम स्पष्ट बनाती हैं। इन मुद्दों को हल करने के लिए बेहतर सुखाने और मोल्डिंग तरीकों को बदलने की आवश्यकता है। बेहतर प्रक्रियाओं से साफ़ प्लास्टिक बनता है।
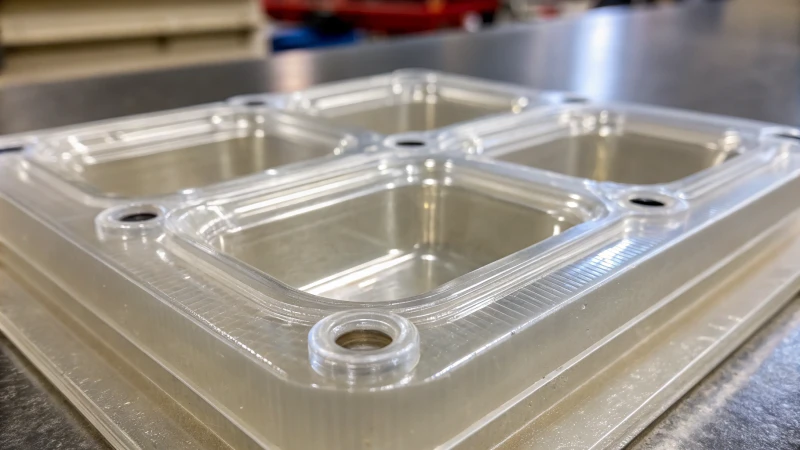
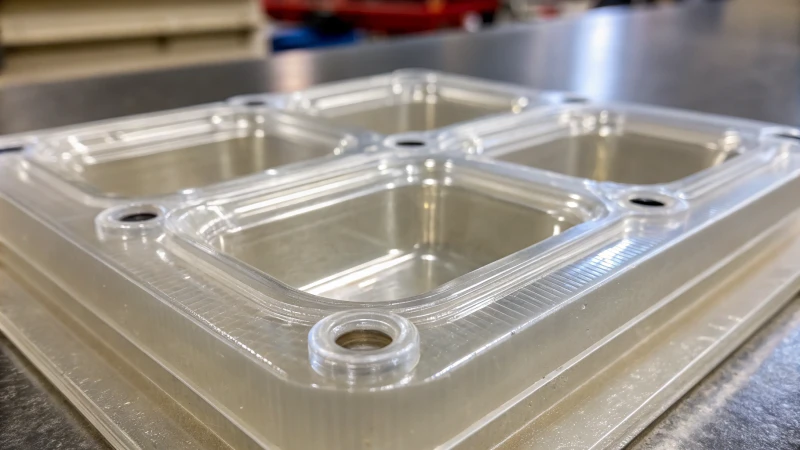
सिल्वर स्ट्रीक्स को समझना
चांदी की धारियाँ कष्टप्रद रेखाएँ हैं जो स्पष्ट प्लास्टिक को बर्बाद कर देती हैं। वर्कशॉप में वे सभी को निराश करते हैं। ये धारियाँ प्लास्टिक में नमी और गैसों से आती हैं। जैसे ही प्लास्टिक गर्म होता है, ये तत्व वाष्प में बदल जाते हैं और पिघले हुए प्लास्टिक के साथ चले जाते हैं। फिर, वे सतह पर पहुंचते हैं और धारियाँ बनाते हैं, जो विशेष रूप से स्पष्ट वस्तुओं पर दिखाई देती हैं।
चाँदी की धारियाँ के कारण
कच्चे माल में नमी मुख्य समस्या है। कल्पना करें कि आपके स्नीकर्स गीले और फफूंदयुक्त हैं क्योंकि आप उन्हें सुखाना भूल गए हैं। प्लास्टिक के साथ भी ऐसा ही होता है. यदि प्लास्टिक छर्रों को उपयोग से पहले अच्छी तरह से नहीं सुखाया जाता है, तो समस्याएँ उत्पन्न होती हैं। तेज़ गर्मी के कारण कुछ प्लास्टिक टूट जाते हैं और गैसें निकलती हैं जो धारियाँ बनाती हैं।
-
मोल्ड डिजाइन और तापमान:
खराब मोल्ड डिजाइन इस समस्या को और खराब कर देता है। यदि सांचा बहुत ठंडा है, तो यह असमान प्रवाह का कारण बनता है, जैसे एक पतली भूसे के माध्यम से एक मोटी स्मूथी डालने की कोशिश करना।कारक विवरण सामग्री की नमी अपर्याप्त सुखाने से पिघलने के दौरान गैस बनने लगती है। उच्च तापमान अत्यधिक गर्मी प्लास्टिक को विघटित करती है, जिससे गैसें उत्पन्न होती हैं। साँचे का डिज़ाइन अपर्याप्त शीतलन चैनल गैसों को फँसा सकते हैं।
पारदर्शिता पर प्रभाव
स्पष्टता महत्वपूर्ण है. चांदी की धारियां लुक और कार्यप्रणाली को खराब कर देती हैं। लेंस या क्लियर बॉक्स जैसे उत्पाद उत्तम होने चाहिए। छोटी-छोटी खामियाँ बड़ी समस्याएँ पैदा कर सकती हैं।
-
उपभोक्ता धारणा:
किसी को भी नई वस्तुओं में खामियां ढूंढना पसंद नहीं है। धारियाँ उत्पादों को सस्ता दिखाती हैं। यह दृश्य ब्रांड प्रतिष्ठा और ग्राहक संतुष्टि को नुकसान पहुँचाता है। -
कार्यात्मक अखंडता:
चिकित्सा उपकरण या कार पार्ट्स जैसे स्पष्ट भागों की मांग वाले क्षेत्रों में, धारियाँ गंभीर समस्याएं पैदा करती हैं। वे किसी उत्पाद के काम करने के तरीके को नुकसान पहुंचा सकते हैं।
चाँदी की धारियाँ कम करना
दागों से बचने के लिए, निर्माताओं को सामग्री को पूरी तरह सुखाना चाहिए। इसे ऐसे समझें जैसे कपड़ों को मोड़ने से पहले अच्छी तरह सुखाना - यह महत्वपूर्ण है लेकिन अक्सर इसे नजरअंदाज कर दिया जाता है। सामग्री को ठीक से सुखाने से नमी दूर हो जाती है; मोल्डिंग तापमान और डिज़ाइन को समायोजित करने से गैसों को बनने से रोका जा सकता है।
दोषों को ठीक करने के और तरीकों के लिए, इंजेक्शन मोल्डिंग अनुकूलन 8 ।
-
कच्चे माल को पहले से सुखाना:
एबीएस या पॉलीकार्बोनेट जैसी सामग्रियों को सुखाना महत्वपूर्ण है। -
मोल्डिंग पैरामीटर्स को समायोजित करना:
तापमान बदलना और अच्छा मोल्ड डिज़ाइन सुनिश्चित करना गैस फंसने से रोकने में मदद करता है।
इन चुनौतियों का सामना करके, निर्माता उत्पाद की स्पष्टता और गुणवत्ता में उल्लेखनीय सुधार करते हैं - यह सब विज्ञान को कला के साथ मिलाने के बारे में है।
चांदी की धारियाँ कच्चे माल में नमी के कारण बनती हैं।सत्य
प्लास्टिक सामग्री में नमी ढलाई के दौरान गैस बनाती है, जिससे धारियाँ बन जाती हैं।
उच्च मोल्ड तापमान चांदी की धारियाँ बनने से रोकता है।असत्य
अत्यधिक गर्मी प्लास्टिक को विघटित करती है, जिससे गैसें उत्पन्न होती हैं जो धारियाँ पैदा करती हैं।
निष्कर्ष
इंजेक्शन मोल्डेड उत्पादों में सामान्य दोषों में फ्लैश, सिकुड़न, वेल्ड निशान, प्रवाह निशान और चांदी की धारियाँ शामिल हैं, जो अनुचित मोल्डिंग स्थितियों के कारण उपस्थिति और प्रदर्शन को प्रभावित करती हैं।
-
यह लिंक असमान मोल्ड बिदाई सतहों के कारणों की पड़ताल करता है, जो फ्लैश गठन का एक प्राथमिक कारण है। ↩
-
यह समझने से कि फ़्लैश असेंबली प्रदर्शन को कैसे प्रभावित करता है, संबंधित समस्याओं को कम करने में मदद करता है। ↩
-
ऐसी डिज़ाइन रणनीतियों की खोज करें जो फ़्लैश दोषों को कम करती हैं और उत्पाद की गुणवत्ता बढ़ाती हैं। ↩
-
ढले हुए भागों में दोषों को कैसे रोका जाए, इसे बेहतर ढंग से समझने के लिए सिकुड़न को प्रभावित करने वाले कारकों का अन्वेषण करें। ↩
-
इंजेक्शन मोल्डिंग प्रक्रियाओं में सिकुड़न को कम करने के लिए डिज़ाइन की गई उन्नत तकनीकों और तकनीकों की खोज करें। ↩
-
इंजेक्शन दबाव नियंत्रण के बारे में सीखने से प्रवाह की स्थिति को अनुकूलित करने और दोषों को कम करने में मदद मिल सकती है। ↩
-
उन्नत मोल्ड डिज़ाइन सिद्धांतों की खोज से वेल्ड निशान को कम करके बेहतर उत्पाद गुणवत्ता प्राप्त की जा सकती है। ↩
-
मोल्डिंग प्रक्रियाओं को परिष्कृत करने, चांदी की धारियों जैसे दोषों को कम करने और उत्पाद की स्पष्टता में सुधार करने की तकनीकों की खोज करें। ↩