क्या कभी इंजेक्शन मोल्डेड उत्पादों पर फ़्यूज़न के निशानों से निराशा महसूस हुई है? मेरा विश्वास करो, मैंने भी इसका सामना किया है। कड़ी मेहनत अक्सर खामियों के कारण बर्बाद होती महसूस होती है। सचमुच निराशाजनक.
इंजेक्शन मोल्डेड उत्पादों पर फ़्यूज़न निशान को रोकने के लिए, मोल्ड डिज़ाइन को अनुकूलित करें, मोल्डिंग सेटिंग्स को समायोजित करें, उपयुक्त सामग्री का चयन करें और गेटों को सही ढंग से रखें। इष्टतम इंजेक्शन गति की पहचान करना और द्रव सामग्री का उपयोग करने से भी उत्पाद की गुणवत्ता में वृद्धि होती है।
इंजेक्शन मोल्डिंग में मेरी यात्रा ने मुझे दिखाया है कि फ्यूजन मार्क्स को संभालने के लिए मोल्ड डिजाइन को समझना महत्वपूर्ण है। प्रक्रिया समायोजन और सामग्री विकल्प भी महत्वपूर्ण हैं। ये तत्व उस संपूर्ण परिणाम तक पहुंचने में मायने रखते हैं। प्रत्येक भाग बहुत महत्वपूर्ण है. यह अच्छे परिणाम प्राप्त करने में मदद करता है।
इन विवरणों की खोज करना वास्तव में आवश्यक है। अंतर्दृष्टि साझा करने से संभवतः आपके उत्पादन की गुणवत्ता में सुधार होगा।
इंजेक्शन मोल्डिंग में फ्यूजन मार्क्स को पूरी तरह से खत्म किया जा सकता है।असत्य
जबकि तकनीकें संलयन के निशान को कम कर सकती हैं, लेकिन मोल्डिंग प्रक्रिया में विभिन्न कारकों के कारण पूर्ण उन्मूलन अक्सर अवास्तविक होता है।
सामग्री का चयन संलयन चिह्नों को रोकने में महत्वपूर्ण भूमिका निभाता है।सत्य
सही सामग्री चुनना महत्वपूर्ण है क्योंकि यह प्रवाह और शीतलन दर को प्रभावित करता है, इस प्रकार संलयन चिह्न निर्माण को प्रभावित करता है।
मोल्ड डिज़ाइन फ़्यूज़न मार्क्स को रोकने में कैसे मदद कर सकता है?
क्या आपने कभी सोचा है कि मोल्ड डिज़ाइन के छोटे-छोटे विवरण उत्पाद की गुणवत्ता को कैसे प्रभावित करते हैं? आइए इंजेक्शन मोल्डिंग की दिलचस्प दुनिया का अन्वेषण करें। उन कष्टप्रद संलयन चिह्नों को रोकने के रहस्यों को उजागर करें।
मोल्ड डिज़ाइन इष्टतम गेट स्थिति का चयन करके, रनर सिस्टम को समायोजित करके, उपयुक्त सामग्रियों का उपयोग करके और प्रक्रिया मापदंडों को ठीक करके संलयन के निशान को रोकने में मदद करता है, जो पिघले हुए प्लास्टिक के प्रवाह और पिघलने को बढ़ाता है।
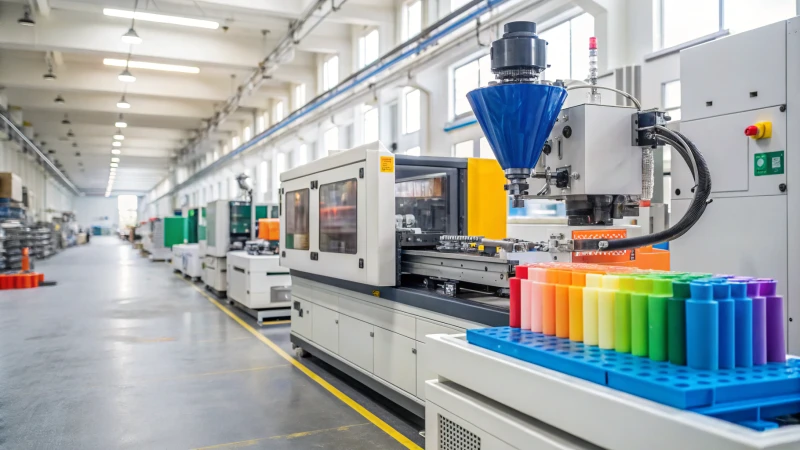
इंजेक्शन मोल्डिंग में मोल्ड डिजाइन का महत्व
इंजेक्शन मोल्डिंग प्रक्रिया में मोल्ड डिजाइन महत्वपूर्ण है, खासकर जब फ्यूजन मार्क्स जैसे दोषों को कम करने की बात आती है। फ़्यूज़न निशान तब होते हैं जब पिघले हुए प्लास्टिक की दो धाराएँ मिलती हैं लेकिन ठीक से मिश्रित नहीं हो पाती हैं, जिससे उत्पाद की सतह पर रेखाएँ या खामियाँ दिखाई देने लगती हैं।
गेट की स्थिति और नंबर को अनुकूलित करना
मोल्ड डिज़ाइन में सबसे पहले विचारों में से एक गेट की स्थिति । एक अच्छी तरह से रखा गया गेट प्लास्टिक पिघल के प्रवाह पथ को बेहतर बनाने में मदद करता है, जिससे वेल्ड निशान काफी कम हो जाते हैं। उदाहरण के लिए, मल्टी-पॉइंट गेट डिज़ाइन का कई पतली दीवारों वाले जटिल आकार के लिए फायदेमंद हो सकता है।
एक प्लास्टिक शेल उत्पाद की कल्पना करें जिसे विभिन्न स्थानों पर रणनीतिक रूप से स्थित तीन द्वारों के साथ डिज़ाइन किया गया है; यह सेटअप पिघल को विभिन्न दिशाओं से एक साथ गुहा भरने की अनुमति देता है, जिससे वेल्ड निशान की संभावना कम हो जाती है।
गेट का प्रकार | विवरण | फ़ायदे |
---|---|---|
साइड गेट्स | अधिक सीधे प्रवाह की अनुमति देते हुए, इसे मोल्ड के किनारे पर स्थित किया गया है। | साधारण आकृतियों के लिए अच्छा है. |
पिन-पॉइंट गेट्स | फैलाव को बढ़ाते हुए, जेट जैसी आकृति में पिघलने का परिचय देता है। | वेल्ड निशान को प्रभावी ढंग से कम करता है। |
गुप्त द्वार | छिपे हुए द्वार जो इंजेक्शन के दौरान खुलते हैं, सौंदर्यशास्त्र और कार्यक्षमता में सुधार करते हैं। | दृश्यमान गेटिंग निशान कम कर देता है। |
रनर सिस्टम में सुधार
रनर प्रणाली भी संलयन चिह्नों को रोकने में महत्वपूर्ण भूमिका निभाती है। एक संतुलित धावक प्रणाली प्लास्टिक पिघलने का एक समान प्रवाह सुनिश्चित करती है, जबकि आकार और सतह खुरदरापन जैसे कारक प्रवाह की गतिशीलता को प्रभावित कर सकते हैं। उदाहरण के लिए, गोलाकार धावकों का प्रवाह प्रतिरोध कम हो जाता है, जिससे गुहा में आसानी से पिघले प्रवाह की अनुमति मिलती है।
इसके अलावा, रनर के भीतर डायवर्टर या बफ़र्स को यह कदम महत्वपूर्ण है क्योंकि अशांति के कारण अधूरा पिघलन हो सकता है और संलयन चिह्न की संभावना बढ़ सकती है।
इंजेक्शन मोल्डिंग प्रक्रिया पैरामीटर्स को समायोजित करना
मोल्ड डिज़ाइन के अलावा, फ़्यूज़न निशान को रोकने के लिए प्रक्रिया मापदंडों को समायोजित करना आवश्यक है। मुख्य समायोजनों में शामिल हैं:
- इंजेक्शन की गति: इंजेक्शन की गति बढ़ाने से पिघली हुई तरलता बढ़ सकती है, जिससे धाराओं के अभिसरण होने पर बेहतर संलयन को बढ़ावा मिलता है। हालाँकि, अत्यधिक गति से बचने के लिए सावधानी आवश्यक है जिससे इजेक्शन की समस्या हो सकती है।
- इंजेक्शन दबाव: पर्याप्त दबाव फ्लैश जैसी समस्याओं को रोकते हुए प्रत्येक कैविटी कोने को पूरी तरह से भरना सुनिश्चित करता है। गुणवत्ता बनाए रखने के लिए एक इष्टतम रेंज ढूँढना महत्वपूर्ण है।
- होल्डिंग पैरामीटर्स: होल्डिंग समय बढ़ाने और ठंडा करने के दौरान दबाव बढ़ाने से यह सुनिश्चित करने में मदद मिलती है कि मोटी दीवार वाले क्षेत्रों को पर्याप्त पिघल पुनःपूर्ति प्राप्त होती है, जिससे वेल्ड निशान कम हो जाते हैं।
इष्टतम प्रवाह के लिए सामग्री का चयन करना
सामग्री का चयन एक अन्य महत्वपूर्ण कारक है। अच्छी तरलता वाले प्लास्टिक का चयन करने से वेल्ड निशानों को काफी कम किया जा सकता है। उदाहरण के लिए:
- पीपी (पॉलीप्रोपाइलीन) जैसी उच्च पिघल प्रवाह दर वाली सामग्री गुहाओं में बेहतर मिश्रण की अनुमति देती है।
- स्नेहक जोड़ने से सामग्री की तरलता भी बढ़ सकती है, जिससे पिघलने के लिए सही ढंग से फ़्यूज़ करना आसान हो जाता है।
उपयोग से पहले यह सुनिश्चित करना भी उतना ही महत्वपूर्ण है कि सामग्री ठीक से सूख गई नायलॉन (पीए) जैसी हाइग्रोस्कोपिक सामग्री के लिए , उन दोषों को रोकने के लिए एक कठोर सुखाने प्रोटोकॉल (4-6 घंटे के लिए 80-90 डिग्री सेल्सियस) आवश्यक है जो वेल्ड निशान में योगदान कर सकते हैं।
मोल्ड डिजाइन और इंजेक्शन मोल्डिंग मापदंडों के इन पहलुओं पर ध्यान केंद्रित करके, निर्माता उत्पाद की गुणवत्ता में काफी सुधार कर सकते हैं और फ्यूजन मार्क्स जैसे दोषों को कम कर सकते हैं।
गेट की स्थिति को अनुकूलित करने से मोल्डिंग में संलयन के निशान कम हो जाते हैं।सत्य
रणनीतिक रूप से गेट लगाने से पिघले प्रवाह में सुधार होता है, जिससे ढले हुए उत्पादों पर संलयन के निशान दिखाई देने की संभावना कम हो जाती है।
भौतिक तरलता का संलयन चिह्न निवारण पर कोई प्रभाव नहीं पड़ता है।असत्य
उच्च तरलता वाली सामग्रियों का चयन करना आवश्यक है क्योंकि वे बेहतर मिश्रण करते हैं, जिससे संलयन चिह्नों की घटना काफी कम हो जाती है।
मैं इंजेक्शन मोल्डिंग प्रक्रिया पैरामीटर्स को कैसे अनुकूलित कर सकता हूं?
क्या आप अपने इंजेक्शन मोल्डिंग कौशल में सुधार करना चाहते हैं? बेहतर दक्षता और उच्च गुणवत्ता वाले उत्पादों के लिए अपनी प्रक्रिया को कैसे समायोजित करें, यह जानने के लिए मेरे साथ एक यात्रा शुरू करें। आइए मोल्ड डिज़ाइन, सेटिंग परिवर्तन और सही सामग्री चुनने के विवरण एक साथ देखें!
मोल्ड डिज़ाइन, गेट स्थिति, रनर सिस्टम, इंजेक्शन गति, दबाव और मोल्ड तापमान को समायोजित करके इंजेक्शन मोल्डिंग को अनुकूलित करें। उत्पाद की गुणवत्ता बढ़ाने और वेल्ड मार्क्स जैसे दोषों को कम करने के लिए अच्छी तरलता वाली सामग्रियों का उपयोग करें।
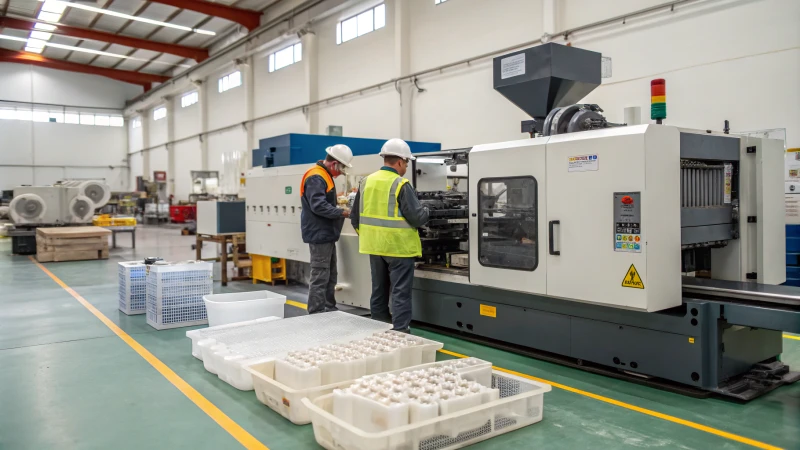
मोल्ड डिज़ाइन को समझना
इंजेक्शन मोल्डिंग प्रक्रिया का अनुकूलन प्रभावी मोल्ड डिजाइन । प्रमुख तत्वों में शामिल हैं:
- गेट की स्थिति और संख्या : गेटों का स्थान प्लास्टिक पिघलने के प्रवाह को प्रभावित करता है। जटिल आकृतियों के लिए, मेल्ट फिलिंग को बेहतर बनाने के लिए मल्टी-पॉइंट गेट डिज़ाइन पर विचार करें।
उदाहरण के लिए, एक प्लास्टिक के खोल में, तीन गेटों का उपयोग करने से पिघल को समान रूप से वितरित करने में मदद मिल सकती है, जिससे वेल्ड के निशान कम हो सकते हैं।
- धावक प्रणाली : एक संतुलित धावक प्रणाली समान प्रवाह सुनिश्चित करती है। कम प्रवाह प्रतिरोध के कारण अक्सर गोलाकार धावक को प्राथमिकता दी जाती है। रनर की सतह को चमकाने से घर्षण कम हो जाता है, जिससे पिघलने का प्रवाह सुचारू हो जाता है।
इंजेक्शन मोल्डिंग पैरामीटर्स को समायोजित करना
इंजेक्शन मोल्डिंग प्रक्रिया मापदंडों को समायोजित करने पर ध्यान दें । इन समायोजनों पर विचार करें:
- इंजेक्शन की गति और दबाव : इंजेक्शन की गति बढ़ाने से उच्च पिघल तापमान बनाए रखा जाता है, जो संलयन को बढ़ाता है और वेल्ड के निशान को कम करता है। हालाँकि, अत्यधिक गति से इजेक्शन जैसे दोष हो सकते हैं।
पैरामीटर | प्रक्रिया पर प्रभाव |
---|---|
इंजेक्शन की गति में वृद्धि | उच्चतर पिघली हुई तरलता |
इष्टतम इंजेक्शन दबाव | पूर्ण गुहा भरना |
- होल्डिंग पैरामीटर्स : होल्डिंग समय बढ़ाने और दबाव बढ़ाने से कूलिंग के दौरान बेहतर पिघलने में मदद मिलती है। असमान दीवार मोटाई वाले उत्पादों के लिए, होल्डिंग समय को तदनुसार समायोजित करें।
सामग्री का चयन और प्रसंस्करण
सही सामग्री का चयन परिणामों को महत्वपूर्ण रूप से प्रभावित करता है। मुख्य विचारों में शामिल हैं:
-
सामग्रियों की तरलता : गुहा भरने को बढ़ाने और वेल्ड निशान को कम करने के लिए उच्च पिघल प्रवाह दर वाली सामग्रियों का चयन करें। उदाहरण के लिए, उच्च एमएफआर वाला पीपी (पॉलीप्रोपाइलीन) प्रदर्शन में सुधार कर सकता है।
-
सामग्री को सुखाना : सुनिश्चित करें कि इंजेक्शन के दौरान दोषों को रोकने के लिए सामग्री पर्याप्त रूप से सूख गई है। नायलॉन (पीए) जैसी नमी-संवेदनशील सामग्री के लिए, गुणवत्ता संबंधी समस्याओं से बचने के लिए 4-6 घंटे के लिए 80-90℃ पर सुखाना आवश्यक है।
मोल्ड तापमान का नियंत्रण
अंत में, मोल्ड तापमान को प्रभावी ढंग से नियंत्रित करें।
- उपयुक्त साँचे का तापमान बनाए रखने से पिघली हुई तरलता बढ़ती है और जमने की संभावना कम हो जाती है जिससे वेल्ड पर निशान पड़ सकते हैं। पीसी (पॉलीकार्बोनेट) जैसी उच्च-चिपचिपापन सामग्री के लिए, उच्च मोल्ड तापमान पिघल के बेहतर मिश्रण की सुविधा प्रदान करता है।
निष्कर्ष में, इंजेक्शन मोल्डिंग के अनुकूलन में मोल्ड डिजाइन, प्रक्रिया मापदंडों, सामग्री चयन और तापमान नियंत्रण पर ध्यान केंद्रित करने वाला एक बहुआयामी दृष्टिकोण शामिल है। प्रत्येक पहलू की गहन जांच करके, निर्माता उत्पाद की गुणवत्ता और दक्षता बढ़ा सकते हैं।
मल्टी-पॉइंट गेट डिज़ाइन इंजेक्शन मोल्डिंग में पिघली हुई फिलिंग में सुधार करते हैं।सत्य
मोल्ड डिज़ाइन में कई गेटों का उपयोग प्लास्टिक पिघल के वितरण को बढ़ाता है, वेल्ड निशान को कम करता है और जटिल आकृतियों को बेहतर ढंग से भरने को सुनिश्चित करता है।
उच्च मोल्ड तापमान इंजेक्शन मोल्डेड उत्पादों में वेल्ड निशान को कम करता है।सत्य
उचित मोल्ड तापमान बनाए रखने से पिघली हुई तरलता बढ़ जाती है, जिससे जमने का जोखिम कम हो जाता है जिससे इंजेक्शन प्रक्रिया के दौरान वेल्ड निशान जैसे दोष हो सकते हैं।
फ़्यूज़न मार्क्स को कम करने के लिए आपको कौन सी सामग्री चुननी चाहिए?
लेजर कटिंग या उत्कीर्णन में सामग्री का चुनाव महत्वपूर्ण है। विभिन्न सामग्रियां अंतिम उत्पाद को महत्वपूर्ण रूप से प्रभावित करती हैं। मैंने इसे कई परियोजनाओं में खोजा। प्रत्येक ने मुझे सही सामग्री चुनने के बारे में सिखाया। यह निर्णय वास्तव में परिणाम को प्रभावित करता है। आइए इसे एक साथ खोजें!
लेजर मशीनिंग में संलयन के निशान को कम करने के लिए, उच्च तरलता वाली सामग्री चुनें, उन्हें अच्छी तरह से सुखाएं, और क्लीनर फिनिश और समग्र गुणवत्ता में सुधार के लिए प्रवाह गुणों को बढ़ाने के लिए एडिटिव्स का उपयोग करें।
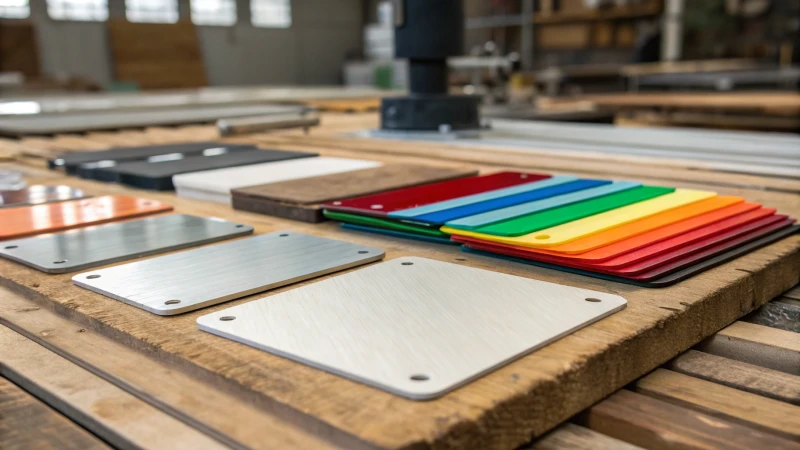
फ़्यूज़न मार्क्स को समझना
फ़्यूज़न निशान लेजर कटिंग या उत्कीर्णन से छोटी खामियां हैं। वे अक्सर किसी सामग्री के गुणों और लेज़र सेटिंग्स के बीच परस्पर क्रिया से उत्पन्न होते हैं। इन निशानों को कम करने के लिए सही सामग्रियों का चयन करना मेरी गुप्त तकनीक है, जिससे एक साफ-सुथरी फिनिश मिलती है।
फ्यूज़न मार्क्स को प्रभावित करने वाले भौतिक गुण
- सामग्री की तरलता
अच्छी तरलता वाली सामग्री प्रसंस्करण के दौरान एक चिकनी पिघल बनाती है।
यहां कुछ सामान्य सामग्रियों और उनकी प्रवाह विशेषताओं को दर्शाने वाली एक तालिका दी गई है:
सामग्री | पिघल प्रवाह दर (एमएफआर) | टिप्पणियाँ |
---|---|---|
पॉलीप्रोपाइलीन (पीपी) | उच्च | जटिल डिज़ाइन के लिए उत्कृष्ट |
पॉलीकार्बोनेट (पीसी) | मध्यम | अच्छा प्रभाव प्रतिरोध |
नायलॉन (पीए) | कम | पूरी तरह सुखाने की आवश्यकता है |
उदाहरण के लिए, मैंने एक बार एक विस्तृत परियोजना के लिए उच्च तरलता ग्रेड पीपी का उपयोग किया था, जिसने अपने बेहतर प्रवाह गुणों के कारण वेल्ड निशान को काफी कम कर दिया था।
-
नमी सामग्री
नमी वास्तव में नायलॉन जैसी सामग्री को बर्बाद कर सकती है, जिससे अवांछित बुलबुले और खामियां पैदा हो सकती हैं।
उपयोग से पहले पूरी तरह सुखाना सुनिश्चित करें:- सुखाने का तापमान: 80-90°C
- अवधि: 4-6 घंटे
सामग्री की अखंडता को बनाए रखने और संलयन के निशान को कम करने के लिए यह कदम आवश्यक है।
-
तरलता में सुधार करने वाले योजक
मैं कभी-कभी स्नेहक या योजक के साथ परीक्षण करता हूं जो प्रवाह में सुधार करते हैं।
ये बहुत प्रभावी हो सकते हैं, विशेष रूप से जटिल डिज़ाइनों के लिए या ऐसी सामग्रियों का उपयोग करते समय जिन्हें संभालना कठिन हो।
अपने प्रोजेक्ट के लिए सही सामग्री का चयन करना
सामग्री का चयन करते समय, महत्वपूर्ण कारकों पर विचार करें:
- आवेदन आवश्यकताएँ : यदि उपस्थिति मायने रखती है, तो मैं उच्च एमएफआर वाली सामग्री चुनता हूँ।
- पर्यावरणीय कारक : तापमान और आर्द्रता प्रदर्शन को प्रभावित करते हैं; मैं हमेशा उन्हें ध्यान में रखता हूं.
सामग्री चयन पर निष्कर्ष
अंत में, मैंने सीखा है कि सही सामग्री चुनने और उन्हें समझने से संलयन के निशान कम हो जाते हैं। तरलता, नमी की मात्रा और एडिटिव्स के आधार पर विकल्पों को अनुकूलित करना लेजर कटिंग और उत्कीर्णन में बेहतर परिणाम प्राप्त करने की कुंजी है।
उच्च तरलता वाली सामग्री लेजर कटिंग में संलयन के निशान को कम करती है।सत्य
उच्च तरलता वाली पॉलीप्रोपाइलीन जैसी सामग्री बेहतर पिघल संलयन की अनुमति देती है, लेजर प्रसंस्करण के दौरान खामियों को कम करती है।
नायलॉन में नमी के कारण फ्यूज़न मार्क्स का खतरा बढ़ जाता है।सत्य
नायलॉन में अत्यधिक नमी से बुलबुले और खामियां हो सकती हैं, जिससे लेजर कटिंग या उत्कीर्णन के दौरान संलयन के निशान खराब हो सकते हैं।
इंजेक्शन मोल्डिंग में फ्यूजन मार्क्स के सामान्य कारण क्या हैं?
क्या आपने कभी अपने इंजेक्शन-मोल्ड उत्पादों पर उन कष्टप्रद संलयन चिह्नों को देखा है? मेरा भी है। यह समझना कि वे क्यों घटित होते हैं, वास्तव में हमें सुधार करने में मदद करता है। आइए इन दोषों के मुख्य कारणों का पता लगाएं!
इंजेक्शन मोल्डिंग में फ़्यूज़न निशान आमतौर पर खराब मोल्ड डिज़ाइन, अनुचित प्रक्रिया सेटिंग्स, या अनुपयुक्त सामग्री विकल्पों के कारण होते हैं, जिनमें गेट की स्थिति, इंजेक्शन की गति और सामग्री की नमी सहित प्रमुख कारक होते हैं। इन कारकों को समझने से उत्पाद की गुणवत्ता में वृद्धि होती है।
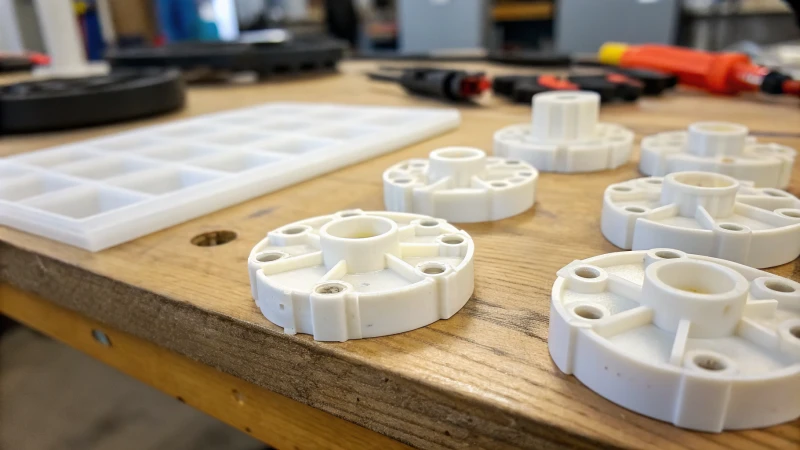
साँचे का डिज़ाइन
इंजेक्शन मोल्डिंग के दौरान संलयन के निशान को रोकने के लिए मोल्ड डिज़ाइन एक महत्वपूर्ण कारक है। गेट की स्थिति और संख्या का अनुकूलन प्लास्टिक पिघल के प्रवाह पथ को महत्वपूर्ण रूप से प्रभावित कर सकता है, जिससे वेल्ड निशान कम हो सकते हैं।
उदाहरण के लिए, जटिल उत्पादों में मल्टी-पॉइंट गेट डिज़ाइन का उपयोग करके मोल्ड कैविटी को अधिक समान रूप से भरना सुनिश्चित किया जा सकता है। प्लास्टिक शेल उत्पाद में, अलग-अलग स्थानों पर तीन गेट स्थापित करने से पिघल को विभिन्न दिशाओं से एकत्रित होने की अनुमति मिलती है, जिससे वेल्ड निशान की संभावना प्रभावी रूप से कम हो जाती है।
इसके अलावा, गेट का प्रकार एक महत्वपूर्ण भूमिका निभाता है। उदाहरण के लिए, पिन-पॉइंट गेट पिघल को जेट की तरह गुहा में प्रवेश करने में सक्षम बनाते हैं, जिससे पिघल के बेहतर फैलाव और संलयन को बढ़ावा मिलता है, जो उच्च सौंदर्य संबंधी मांग वाले उत्पादों के लिए महत्वपूर्ण है। मेरी टीम को उस बदलाव के बाद गुणवत्ता में सुधार वास्तव में पसंद आया।
इंजेक्शन मोल्डिंग प्रक्रिया पैरामीटर समायोजन
संलयन के निशान को कम करने के लिए इंजेक्शन की गति और दबाव जैसे प्रक्रिया मापदंडों को समायोजित करना महत्वपूर्ण है। इंजेक्शन की गति बढ़ने से गुहा के भीतर पिघले हुए तापमान और तरलता में वृद्धि होती है, जो इसके अभिसरण और संलयन में सहायता करती है। हालाँकि, सावधानी बरतनी चाहिए कि इजेक्शन जैसी गुणवत्ता संबंधी समस्याओं से बचने के लिए गति बहुत अधिक न रखें - एक सबक जो मैंने अच्छी तरह से सीखा है।
इस समायोजन का एक उदाहरण रिब्ड प्लास्टिक उत्पादों को इंजेक्ट करते समय देखा जा सकता है; संगम क्षेत्र में बढ़ती गति से पिघलों का तेजी से विलय संभव हो पाता है। इसके अतिरिक्त, होल्डिंग समय को बढ़ाकर और होल्डिंग दबाव को बढ़ाकर होल्डिंग मापदंडों को अनुकूलित करने से शीतलन के दौरान बेहतर पिघलने को सुनिश्चित करके वेल्ड निशान को काफी कम किया जा सकता है।
सामग्री का चयन और प्रसंस्करण
संलयन के निशानों को रोकने के लिए सही सामग्री का चयन करना आवश्यक है। उच्च पिघल प्रवाह दर (एमएफआर) वाले प्लास्टिक का चयन करना, जैसे उच्च तरलता ग्रेड पॉलीप्रोपाइलीन (पीपी), गुहा के भीतर पिघल की तरलता और मिश्रण को बढ़ाता है, जिससे वेल्ड निशान कम हो जाते हैं।
इसके अलावा, यह सुनिश्चित करना महत्वपूर्ण है कि इंजेक्शन मोल्डिंग से पहले सामग्री ठीक से सूख जाए। सामग्रियों में नमी प्रसंस्करण के दौरान दोष पैदा कर सकती है और पिघले हुए संलयन पर प्रतिकूल प्रभाव डाल सकती है; नायलॉन (पीए) जैसी नमी-संवेदनशील सामग्रियों के लिए पूरी तरह से सुखाने की प्रक्रिया से गुजरना महत्वपूर्ण हो गया है।
कारक | विवरण | उदाहरण |
---|---|---|
साँचे का डिज़ाइन | प्रवाह पथ को बेहतर बनाने के लिए गेट की स्थिति और प्रकार को अनुकूलित करें | जटिल आकृतियों पर बहु-बिंदु द्वार |
इंजेक्शन पैरामीटर | इष्टतम पिघल प्रवाह के लिए गति और दबाव को समायोजित करें | पसली संगम के लिए बढ़ी हुई गति |
सामग्री चयन | अच्छी तरलता वाली सामग्रियों का उपयोग करें और उचित सुखाने को सुनिश्चित करें | उच्च एमएफआर पीपी; नायलॉन को 80-90°C पर सुखाना |
इनमें से प्रत्येक पहलू इंजेक्शन मोल्डेड उत्पादों में फ़्यूज़न निशान को कम करने, समग्र गुणवत्ता और उपस्थिति में योगदान देने में महत्वपूर्ण भूमिका निभाता है।
गेट डिज़ाइन को अनुकूलित करने से साँचे में संलयन के निशान कम हो जाते हैं।सत्य
उचित गेट स्थिति और डिज़ाइन इंजेक्शन मोल्डिंग के दौरान वेल्ड निशान को कम करते हुए, पिघले प्रवाह को बढ़ाता है।
सामग्रियों में उच्च नमी की मात्रा संलयन निशान का कारण बनती है।सत्य
अत्यधिक नमी से पिघलने में दोष हो सकता है, जिससे संलयन प्रभावित हो सकता है और परिणामस्वरूप उत्पाद पर निशान दिखाई दे सकते हैं।
निष्कर्ष
अनुकूलित मोल्ड डिज़ाइन, सटीक प्रक्रिया मापदंडों और सावधानीपूर्वक सामग्री चयन के माध्यम से इंजेक्शन मोल्डेड उत्पादों में फ़्यूज़न निशान को कम करने का तरीका जानें।
-
अपनी परियोजनाओं के लिए फ़्यूज़न चिह्नों को कम करने के लिए सामग्री चुनने पर विस्तृत मार्गदर्शन प्राप्त करें। ↩