क्या आपने कभी सोचा है कि प्लास्टिक की कुछ वस्तुएँ आसानी से क्यों टूट जाती हैं? इसका कारण आमतौर पर मोल्ड एग्जॉस्ट का डिज़ाइन होता है।
इंजेक्शन मोल्डिंग में खराब मोल्ड एग्जॉस्ट डिज़ाइन से हवा के बुलबुले और प्रवाह रेखाओं जैसे दोष होते हैं, जो प्लास्टिक उत्पादों की उपस्थिति और ताकत से समझौता करते हैं। उच्च गुणवत्ता वाले आउटपुट के लिए उचित वेंटिंग आवश्यक है।
मुझे याद है कि पहली बार मुझे मोल्ड एग्ज़ॉस्ट डिज़ाइन के साथ समस्याओं का सामना करना पड़ा था। यह सचमुच आश्चर्यजनक था. पहले तो सब कुछ ठीक लग रहा था. फिर, हमने एयर पॉकेट और प्रवाह के निशान देखे। इन खामियों ने फिनिश को बर्बाद कर दिया। समस्याएँ अपेक्षा से अधिक गहरी हो गईं। उन्होंने उत्पाद की ताकत को प्रभावित किया और उत्पादन समय में वृद्धि की। इन चुनौतियों को ठीक करना बहुत महत्वपूर्ण हो गया। खराब मोल्ड निकास ने गुणवत्ता और दक्षता दोनों के लिए परेशानी पैदा की। हमने बेहतर वेंटिंग की अनुमति देने के लिए डिज़ाइन को समायोजित किया। इस बदलाव से हमारे उत्पादों के रूप, मजबूती और उत्पादन में सुधार हुआ।
खराब मोल्ड निकास के कारण प्लास्टिक में हवा जमा हो जाती है।सत्य
फंसी गैसों के कारण एयर पॉकेट बन जाते हैं, जिससे उत्पाद की गुणवत्ता प्रभावित होती है।
उच्च गुणवत्ता वाले प्लास्टिक उत्पादों के लिए प्रभावी वेंटिंग अनावश्यक है।असत्य
वेंटिंग प्रवाह के निशान और असमान घनत्व जैसे दोषों को रोकता है।
खराब वेंटिंग के कारण होने वाले सामान्य सतह दोष क्या हैं?
क्या आपने कभी महसूस किया है कि आपके सावधानीपूर्वक नियोजित उत्पाद में अप्रत्याशित समस्याएं थीं? खराब वेंटिंग इसका कारण हो सकता है। इन सतही खामियों के बारे में जानना वास्तव में आपकी मदद कर सकता है। यह आपका दिन बचा सकता है.
साँचे में अपर्याप्त वेंटिलेशन कष्टप्रद सतह दोषों का कारण बनता है। एयर पॉकेट, प्रवाह चिह्न और संलयन चिह्न दिखाई देते हैं। फंसी हुई हवा प्लास्टिक के प्रवाह को बाधित करती है। यह वास्तव में अंतिम उत्पाद की उपस्थिति और मजबूती दोनों को नुकसान पहुँचाता है। यह इसे बर्बाद कर देता है.
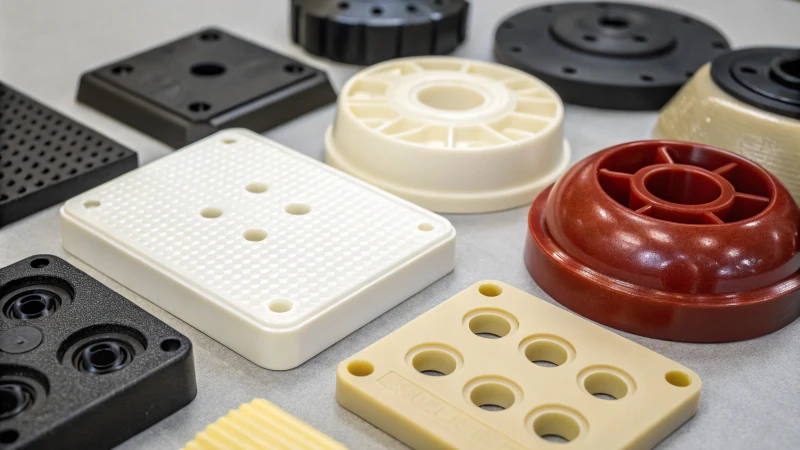
उपस्थिति गुणवत्ता के मुद्दे
एयर पॉकेट और बुलबुले
मुझे वह समय याद है जब किसी प्रोजेक्ट पर काम करने का मतलब एकदम सही होता था - वस्तुतः। जब भद्दे गड्ढे और पॉकमार्क दिखाई दिए तो हमने ऑप्टिकल लेंस बनाए। अपर्याप्त वेंटिंग के कारण हवा की जेबें बनने लगीं। फंसी हवा ने सतह को बर्बाद कर दिया, विशेष रूप से लेंस जैसे स्पष्ट उत्पादों के साथ, जिससे गुणवत्ता 1 और स्पष्टता कम हो गई। यहां एक सुनियोजित वेंट सिस्टम आवश्यक है।
फ्लो मार्क्स और फ्यूज़न मार्क्स का बढ़ना
किसी चिकने उत्पाद को केवल तभी डिज़ाइन करने पर विचार करें ताकि वह अपूर्ण साँचे से बाहर आ जाए। हवा प्लास्टिक के पिघले प्रवाह को अवरुद्ध कर सकती है, जिससे असमान पैटर्न बन सकते हैं जिन्हें प्रवाह चिह्न के रूप में जाना जाता है। जब पिघल विभाजित हो जाता है और फिर से मिलता है, तो खराब वेंटिंग से संलयन के निशान खराब हो जाते हैं, जो आपके उत्पाद की समग्र उपस्थिति गुणवत्ता को कम कर देता है।
दोष प्रकार | कारण | प्रभाव |
---|---|---|
हवाई गर्त | फंसी हुई हवा | गड्ढे/पॉकमार्क |
प्रवाह चिह्न | असमान प्रवाह | पैटर्न विरूपण |
आंतरिक गुणवत्ता संबंधी मुद्दे
असमान घनत्व
एक प्रारंभिक परियोजना में, फंसी हवा के असमान घनत्व के कारण हमारे प्लास्टिक कंटेनरों में स्थायित्व की कमी थी, जिससे उत्पाद के भीतर खालीपन आ गया था। इस असंगतता ने उन्हें कमजोर कर दिया, जिससे उनके टूटने का खतरा हो गया - कमजोर बिंदु बहुत खतरनाक होते हैं।
अवशिष्ट तनाव में वृद्धि
उत्पादों में विकृति या अप्रत्याशित दरारें अवशिष्ट तनाव का संकेत देती हैं। फंसी हुई हवा से प्रतिक्रिया बल शीतलन के दौरान दबाव बनाते हैं, जो अवशिष्ट तनाव में परिवर्तित हो जाते हैं जो दबाव में विरूपण या दरार का कारण बनते हैं।
मोल्डिंग दक्षता में कमी
भरने में कठिनाइयाँ
कल्पना कीजिए कि आप एक सांचे को भरने की कोशिश कर रहे हैं लेकिन हवा नहीं चल रही; हर चीज़ और अधिक जटिल हो जाती है। भरने के दौरान बढ़ते प्रतिरोध के कारण अधिक दबाव और समय की आवश्यकता होती है, जिसके लिए अधिक दबाव और अधिक समय की आवश्यकता होती है। अपूर्ण फिल या शॉर्ट शॉट उत्पादकता 2 ।
डिमोल्डिंग कठिनाइयाँ
और डिमोल्डिंग? अतिरिक्त आंतरिक गैस डिमोल्डिंग के दौरान घर्षण को बढ़ाती है - बिना किसी क्षति के उत्पाद को छोड़ना एक दुःस्वप्न है।
ये दोष उत्पाद की अखंडता और सौंदर्य अपील को बनाए रखने के लिए सांचों में प्रभावी वेंटिंग सिस्टम के महत्व को दर्शाते हैं। इन समस्याओं 3 से से संभवतः मोल्ड डिजाइन और दक्षता में सुधार हो सकता है।
एयर पॉकेट के कारण पारदर्शी सतहों पर गड्ढे हो जाते हैं।सत्य
अपर्याप्त वेंटिंग से हवा जेब में चली जाती है, जिससे सतहों पर निशान पड़ जाते हैं।
खराब वेंटिंग से मोल्डिंग दक्षता कम हो जाती है।सत्य
फंसी हुई हवा प्रतिरोध बढ़ाती है, जिससे भरने और डिमोल्डिंग प्रक्रिया जटिल हो जाती है।
अकुशल मोल्ड निकास गुणवत्ता संबंधी समस्याओं का कारण क्यों बनता है?
प्रत्येक व्यक्ति ने ऐसे समय का अनुभव किया है जब एक छोटी सी गलती बड़ी समस्या बन जाती है। खराब मोल्ड निकास विनिर्माण क्षेत्र में एक छिपा हुआ दुश्मन है जो अचानक परेशानी ला सकता है।
खराब मोल्ड निकास हवा की जेब का कारण बनता है। ये पॉकेट असमान घनत्व बनाते हैं। उत्पादों में तनाव बढ़ जाता है, जिससे उनकी उपस्थिति कम हो जाती है। परिणामस्वरूप संरचनात्मक अखंडता प्रभावित होती है। गुणवत्ता के मुद्दे अधिक आम हो गए हैं।
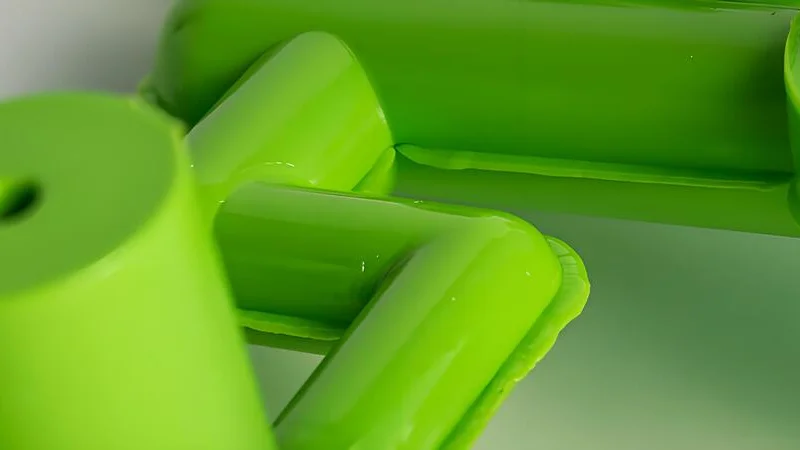
उपस्थिति गुणवत्ता पर प्रभाव
खराब मोल्ड वेंटिंग के कारण हवा फंस जाती है। इससे हवा के छिद्र और बुलबुले बनते हैं, जो भद्दे गड्ढे या निशान छोड़ जाते हैं। ऑप्टिकल लेंस जैसी पारदर्शी चीज़ों को सबसे ज़्यादा नुकसान होता है। बुलबुले उनकी पारदर्शिता को बहुत कम कर देते हैं। जब मैं नया था, मैंने पारदर्शी प्लास्टिक के गोले पर काम किया। बुलबुले के कारण काम के घंटे बर्बाद होते देखना वास्तव में निराशाजनक था। इसके अतिरिक्त, प्रवाह चिह्न और संलयन चिह्न बदतर हो जाते हैं, जिससे उत्पाद की उपस्थिति गुणवत्ता को नुकसान पहुंचता है।
आंतरिक गुणवत्ता से समझौता
खराब निकास के परिणामस्वरूप असमान घनत्व होता है, जिससे उत्पादों में कमजोर धब्बे पैदा होते हैं। मैंने एक बार प्लास्टिक के कंटेनर डिज़ाइन किए थे जो असमान घनत्व के कारण दबाव में फट जाते थे। यह मुझे याद दिलाता है कि घनत्व भी उपस्थिति जितना ही महत्वपूर्ण है। इसके अलावा, फंसी हुई हवा अवशिष्ट तनाव को । यह तनाव समय के साथ उत्पादों को विकृत या तोड़ सकता है, जिससे वे नाजुक और अविश्वसनीय हो सकते हैं।
मोल्डिंग दक्षता में कमी
अकुशल निकास मोल्डिंग दक्षता को भी कम कर देता है। भरने का प्रतिरोध बढ़ जाता है, उच्च दबाव और लंबे चक्र की आवश्यकता होती है, जिससे अक्सर छोटे शॉट । मुझे याद है कि इस समस्या के कारण एक उत्पादन लाइन रुक गई थी—कोई भी नहीं चाहता कि ऐसा दोबारा हो। यह चक्र के समय को बढ़ाता है और अपूर्ण भराव का कारण बनता है, जिससे मूल्यवान सामग्री और समय बर्बाद होता है। फंसी हुई गैस भी डिमोल्डिंग को जटिल बनाती है, जिससे उत्पाद और मोल्ड दोनों को नुकसान होने का खतरा होता है।
विषय वर्ग | कारण | प्रभाव |
---|---|---|
उपस्थिति की समस्याएँ | हवाई गर्त | गड्ढे/पॉकमार्क |
आंतरिक गुणवत्ता संबंधी मुद्दे | असमान घनत्व | कमजोरी/टूटना |
मोल्डिंग दक्षता | भरने का प्रतिरोध | छोटे शॉट/लंबे चक्र |
ये मुद्दे दिखाते हैं कि उत्पादन में उच्च गुणवत्ता मानकों को बनाए रखने के लिए अच्छे मोल्ड निकास सिस्टम क्यों महत्वपूर्ण हैं।
प्रत्येक नई डिज़ाइन चुनौती मुझे इन पिछले पाठों की याद दिलाती है। जो लोग आगे समाधान तलाशने के इच्छुक हैं, उनके लिए ये उन्नत तकनीकें 4 उपयोगी हो सकती हैं।
फंसी हुई हवा के कारण उत्पाद की सतह पर गड्ढे हो जाते हैं।सत्य
ख़राब मोल्ड वेंटिंग हवा को फँसा लेती है, जिससे सतह पर गड्ढे या पॉकमार्क बन जाते हैं।
अकुशल निकास मोल्डिंग चक्र के समय को कम कर देता है।असत्य
यह वास्तव में उच्च दबाव और लंबे समय तक भरने के कारण चक्र का समय बढ़ाता है।
ख़राब एग्ज़ॉस्ट डिज़ाइन मोल्डिंग दक्षता को कैसे प्रभावित करता है?
क्या आपने कभी सोचा है कि एग्ज़ॉस्ट डिज़ाइन जैसी कोई चीज़ मोल्डिंग को पूरी तरह से कैसे बदल सकती है? मैंने भी इसके बारे में सोचा, जब तक मैंने नहीं देखा कि यह वास्तव में कितना महत्वपूर्ण है।
ख़राब निकास डिज़ाइन वास्तव में मोल्डिंग दक्षता को नुकसान पहुँचाता है। वायु जेब, असमान घनत्व और लंबे चक्र समय जैसी समस्याएं उत्पन्न होती हैं। ये मुद्दे उत्पादकता को बर्बाद कर देते हैं। वे उत्पाद की गुणवत्ता को भी नुकसान पहुंचाते हैं। इसलिए, अच्छी मोल्डिंग प्रक्रियाओं के लिए निकास प्रणालियों का अनुकूलन महत्वपूर्ण है।
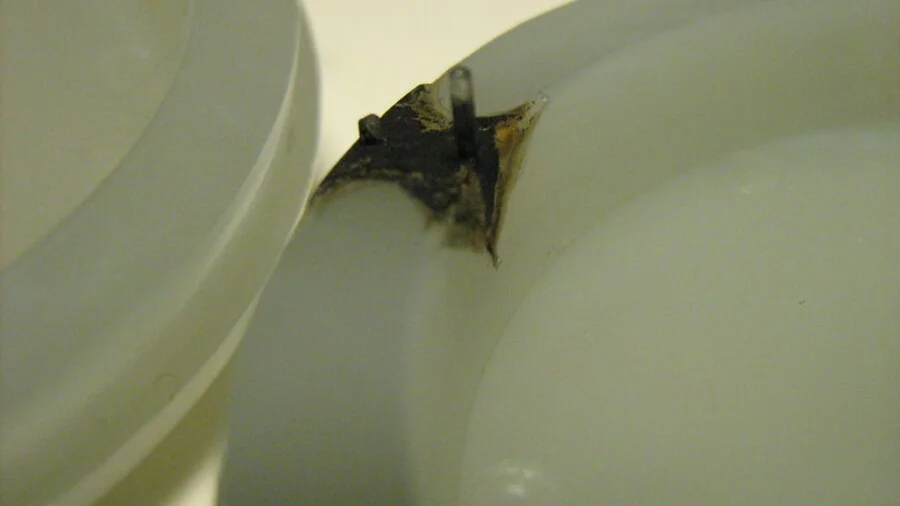
उपस्थिति गुणवत्ता की समस्याएँ
मुझे पहली बार बदसूरत बुलबुले और पॉकमार्क वाले ऑप्टिकल लेंस देखना याद है। यह जानकर बहुत निराशा हुई कि ये खामियाँ पूरी तरह से टाली जा सकती थीं। समस्या ख़राब एग्ज़ॉस्ट डिज़ाइन की थी, जिससे हवा मोल्ड के अंदर फंसी रहती थी। यह बिल्कुल सोडा डालने के समान है, लेकिन फंसी हुई हवा के कारण यह ओवरफ्लो हो जाता है। ये एयर पॉकेट वास्तव में स्पष्टता और चमक को नुकसान पहुंचाते हैं। ऑप्टिकल लेंस 5 या स्पष्ट प्लास्टिक शेल जैसे उत्पादों के लिए उपस्थिति ही सब कुछ है
प्रवाह चिह्न और संलयन चिह्न अधिक समस्याएँ पैदा करते हैं। ये ठंडे टोस्ट पर मक्खन फैलाने जैसा है। हवा पिघले प्रवाह में बाधा डालती है, असमान रूप से चलती है और ध्यान देने योग्य निशान छोड़ती है। यह विशेष रूप से समस्याग्रस्त होता है जब एक चिकनी, निर्बाध समाप्ति महत्वपूर्ण होती है।
आंतरिक गुणवत्ता की समस्याएँ
आंतरिक समस्याएँ भी उतनी ही गंभीर हैं। मैंने असमान घनत्व के कारण दबाव को संभालने वाले कंटेनरों को तेजी से फटते देखा है। यह ऊबड़-खाबड़ ज़मीन पर घर बनाने जैसा है; अंततः, कुछ टूट जाता है। फंसी हुई हवा रिक्त स्थान बनाती है जो संरचना को कमजोर करती है, जिससे तनाव के कारण इसके विफल होने की संभावना होती है।
अवशिष्ट तनाव एक और छिपा हुआ खतरा है। ऐसे जूते पहनने की कल्पना करें जो थोड़े बहुत तंग हों - असुविधाजनक और समय के साथ हानिकारक। यह तनाव शीतलन के दौरान असमान दबाव से बनता है, जिससे अप्रत्याशित रूप से विकृत या टूट जाता है।
मोल्डिंग दक्षता में कमी
ढलाई में अक्षमताएँ स्पष्ट हैं। चक्र का समय कभी-कभी हमेशा के लिए बढ़ जाता है क्योंकि हमने फंसी हवा को बाहर निकालने के लिए इंजेक्शन का दबाव बढ़ा दिया है। यह लगभग खाली ट्यूब से टूथपेस्ट का आखिरी टुकड़ा निचोड़ने की कोशिश करने जैसा है - जो निराशाजनक रूप से अक्षम है। इससे भी बुरी बात यह है कि कभी-कभी हमारे पास अपूर्ण भराव होता था, जो सीधे उत्पाद स्क्रैप 6 ।
डिमोल्डिंग, एक प्रक्रिया जो सरल होनी चाहिए, उत्पाद के अंदर अवशिष्ट गैस के विस्तार के कारण एक संघर्ष में बदल जाती है। उस स्टिकर को छीलने का प्रयास करने के बारे में सोचें जो बिना फटे निकलने से इनकार करता है। इससे उत्पादन में देरी होती है और मोल्ड और उत्पाद दोनों को नुकसान पहुंचने का जोखिम होता है।
सारांश तालिका: मोल्डिंग पर ख़राब निकास डिज़ाइन का प्रभाव
मुद्दा | विवरण |
---|---|
हवाई गर्त | सतह की खामियां जैसे गड्ढे और खरोंच के निशान |
असमान घनत्व | शक्ति और कठोरता में कमज़ोरियाँ |
प्रवाह चिह्न | असमान पिघल प्रवाह दृश्य दोषों का कारण बनता है |
अवशिष्ट तनाव | विकृत होने और टूटने का खतरा बढ़ जाता है |
भरने में कठिनाई | उच्च चक्र समय और स्क्रैप की ओर ले जाता है |
ध्वस्तीकरण चुनौतियाँ | क्षति पहुंचाता है और कार्यकुशलता कम कर देता है |
एग्जॉस्ट डिज़ाइन को अनुकूलित करना उबाऊ लग सकता है, लेकिन यह वास्तव में मोल्डिंग प्रक्रियाओं में दक्षता और गुणवत्ता में सुधार के लिए सब कुछ बदल देता है।
ख़राब निकास डिज़ाइन के कारण ढले हुए उत्पादों में हवा की कमी हो जाती है।सत्य
खराब वेंटिंग के कारण फंसी हुई हवा एयर पॉकेट बनाती है, जिससे उपस्थिति प्रभावित होती है।
असमान घनत्व प्लास्टिक उत्पादों की ताकत में सुधार करता है।असत्य
रिक्त स्थान बनने पर असमान घनत्व ताकत को कमजोर कर देता है, जिससे उत्पाद की अखंडता कम हो जाती है।
हम उत्पाद की गुणवत्ता में सुधार के लिए मोल्ड वेंटिंग को कैसे बढ़ा सकते हैं?
मोल्ड वेंटिंग में सुधार करना जटिल लग सकता है, लेकिन यह सब उत्पाद की गुणवत्ता और विश्वसनीयता के बारे में है। हम शायद बेहतर उत्पाद चाहते हैं। हम वास्तव में ऐसा करते हैं। आइए कुछ व्यावहारिक तरीकों का पता लगाएं। ये तरीके महत्वपूर्ण सुधार ला सकते हैं।
उत्पाद की बेहतर गुणवत्ता के लिए, वेंट को सही स्थानों पर लगाने पर ध्यान दें। जहां संभव हो वहां बड़े वेंट का प्रयोग करें। वैक्यूम वेंटिंग जैसे नए तरीके आज़माएं। ये तरीके एयर पॉकेट से छुटकारा पाने में मदद करते हैं। वे उत्पादों में बचे हुए तनाव को कम करते हैं। परिणामस्वरूप लगातार उत्पाद की गुणवत्ता उभर कर सामने आती है।
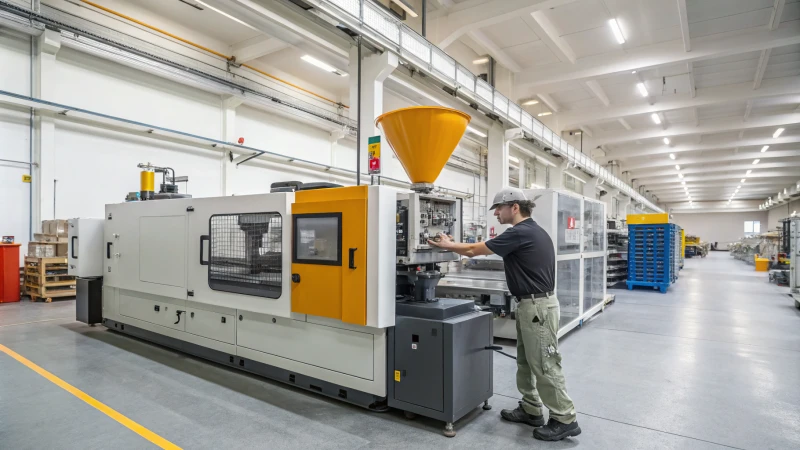
वेंट्स के लिए सर्वोत्तम स्थान खोजें
मुझे याद है कि मैं पहली बार मोल्ड डिज़ाइन से जुड़ा था। मैंने तुरंत देखा कि वेंट लगाना एक पहेली को सुलझाने जैसा लगा। सही स्थानों पर मौजूद वेंट, उत्पाद की सतह पर हवा के छिद्रों और बुलबुले को रोकते हैं। इससे इसकी चमक और स्पष्टता बरकरार रहती है। सीएडी उपकरण का उपयोग करके, डिजाइनर अनुकरण कर सकते हैं कि प्लास्टिक कैसे बहता है और पहचान सकता है कि हवा कहां फंस सकती है, अक्सर प्रवाह के अंत के पास या मुश्किल आकार में। यह लगभग एक जासूस होने जैसा है, जो यह पता लगाता है कि वे गुप्त हवाई जाल कहाँ छिपे हैं।
वेंट्स को बड़ा करें
एक प्रोजेक्ट में, बड़े वेंट ने सब कुछ बदल दिया। बड़े वेंट हवा को अधिक कुशलता से बाहर निकलने की अनुमति देते हैं, जिससे प्रवाह के निशान और संलयन के निशान कम हो जाते हैं। हालाँकि, मोल्ड की संरचनात्मक अखंडता को बनाए रखने के साथ वेंट आकार को संतुलित करना महत्वपूर्ण है।
विभिन्न प्रकार के प्लास्टिक के लिए अनुशंसित वेंट आकार को दर्शाने के लिए एक तालिका का उपयोग किया जा सकता है:
प्लास्टिक प्रकार | अनुशंसित वेंट आकार (मिमी) |
---|---|
polypropylene | 0.02 – 0.05 |
पॉलीकार्बोनेट | 0.03 – 0.06 |
पेट | 0.04 – 0.07 |
वैक्यूम वेंटिंग का प्रयोग करें
जब मोल्ड कैविटी से हवा को बाहर निकालने के लिए वैक्यूम लगाने के नियमित तरीके विफल हो जाते हैं तो वैक्यूम वेंटिंग एक मजबूत उपाय की तरह काम करता है। यह असमान घनत्व को रोककर आंतरिक गुणवत्ता में सुधार करता है और अवशिष्ट तनाव को कम करता है।
यह समझना महत्वपूर्ण है कि विभिन्न सामग्रियां वैक्यूम वेंटिंग पर कैसे प्रतिक्रिया करती हैं, विशेष रूप से उच्च दबाव वाले प्लास्टिक कंटेनरों को डिजाइन करते समय जिन्हें लगातार घनत्व की आवश्यकता होती है।
मोल्डिंग दक्षता समस्याओं का समाधान करें
सांचों में वेंटिंग में सुधार करने से भरने की कठिनाइयों और डिमोल्डिंग चुनौतियों को कम करके सीधे मोल्डिंग दक्षता बढ़ जाती है। इसमें कम इंजेक्शन दबाव की आवश्यकता होती है, जिससे चक्र का समय और छोटे शॉट कम हो जाते हैं।
डिमोल्डिंग विश्लेषण 7 शामिल करने से डिजाइनरों को डिमोल्डिंग के दौरान गैस विस्तार की समस्याओं की भविष्यवाणी करने में मदद मिल सकती है, जिससे उत्पादकता में और वृद्धि होगी।
सामग्री और शर्तों के साथ वेंट डिज़ाइन का मिलान करें
अंत में, सामग्री और स्थितियों के साथ वेंट डिज़ाइन का मिलान महत्वपूर्ण है क्योंकि कुछ सामग्रियों को उच्च तापमान या दबाव की आवश्यकता होती है, जो वेंट दक्षता को प्रभावित करती है।
सामग्री-विशिष्ट वेंटिंग 8 पर शोध प्रत्येक सामग्री के अद्वितीय गुणों को समझकर बेहतर उत्पादों के लिए अंतर्दृष्टि प्रदान करता है।
वेंट प्लेसमेंट को अनुकूलित करने से हवा की जेब कम हो जाती है।सत्य
रणनीतिक रूप से लगाए गए वेंट हवा को फंसने से रोकते हैं, दोषों को कम करते हैं।
बड़े वेंट मोल्ड की संरचनात्मक अखंडता से समझौता करते हैं।असत्य
उचित आकार के बड़े वेंट बिना किसी क्षति के हवा के निकास में सुधार कर सकते हैं।
निष्कर्ष
ख़राब मोल्ड एग्ज़ॉस्ट डिज़ाइन के कारण प्लास्टिक उत्पादों में हवा की कमी, असमान घनत्व और अवशिष्ट तनाव बढ़ जाता है, जिससे उपस्थिति गुणवत्ता और मोल्डिंग दक्षता से समझौता होता है।
-
यह पता लगाता है कि कैसे एयर पॉकेट ऑप्टिकल लेंस में पारदर्शिता से समझौता करते हैं, जो गुणवत्ता नियंत्रण के लिए महत्वपूर्ण है। ↩
-
चर्चा करता है कि अपर्याप्त वेंटिंग इंजेक्शन मोल्डिंग प्रक्रियाओं की दक्षता को कैसे प्रभावित करती है। ↩
-
सामान्य मोल्ड वेंटिंग मुद्दों को संबोधित करने, उत्पाद की गुणवत्ता बढ़ाने के लिए रणनीतियाँ प्रदान करता है। ↩
-
उन तकनीकों के बारे में जानें जो मोल्ड निकास दक्षता में सुधार करती हैं, उत्पाद की गुणवत्ता बढ़ाती हैं। ↩
-
लेंस में ऑप्टिकल स्पष्टता पर एयर पॉकेट के प्रभाव के बारे में जानें। ↩
-
पता लगाएं कि अधूरा भरने से उत्पाद स्क्रैप में वृद्धि क्यों होती है। ↩
-
घर्षण को कम करने और उत्पादकता में सुधार के लिए डिमोल्डिंग चुनौतियों और समाधानों का विश्लेषण करने के बारे में जानें। ↩
-
पता लगाएं कि इष्टतम मोल्डिंग परिणामों के लिए विभिन्न सामग्रियों को अद्वितीय वेंटिंग रणनीतियों की आवश्यकता कैसे होती है। ↩