क्या आप अपनी प्लास्टिक इंजेक्शन मोल्डिंग प्रक्रिया में सुधार करना चाहते हैं? मैं आपकी स्थिति में रहा हूँ. महत्वपूर्ण कारकों को जानने से वास्तव में सब कुछ बदल जाता है।
प्लास्टिक इंजेक्शन मोल्डिंग की अवधि इंजेक्शन चक्र, सामग्री विशेषताओं, भाग के आकार और आकार और मोल्ड डिजाइन से प्रभावित होती है। इन कारकों को समझने से उत्पादन क्षमता और गुणवत्ता में वृद्धि हो सकती है।
जब मैंने पहली बार प्लास्टिक इंजेक्शन मोल्डिंग की दुनिया में प्रवेश किया, तो मुझे विवरण से अभिभूत महसूस हुआ। लेकिन समय के साथ, मुझे कई प्रमुख कारकों के बारे में पता चला। ये कारक संभवतः प्रक्रिया की अवधि को बहुत अधिक प्रभावित करते हैं। इंजेक्शन चक्र की संरचना और मोल्ड डिजाइन की पेचीदगियां दोनों एक भूमिका निभाती हैं। प्रत्येक तत्व योगदान देता है। चक्र में इंजेक्शन का समय, ठंडा करने का समय और इजेक्शन का समय शामिल होता है। इस समय का सही होना बहुत महत्वपूर्ण है। दक्षता और गुणवत्ता इस पर निर्भर करती है। मैंने पाया कि मापदंडों को समायोजित करने से हमारे उत्पादन परिणामों में सुधार हुआ। पूरा अनुभव और भी अधिक फायदेमंद हो गया।
सामग्री की विशेषताएं इंजेक्शन मोल्डिंग अवधि को प्रभावित करती हैं।सत्य
इंजेक्शन मोल्डिंग में उपयोग की जाने वाली सामग्री का प्रकार चिपचिपाहट और शीतलन दर जैसे विभिन्न गुणों के कारण चक्र समय को प्रभावित करता है।
भाग के आकार का इंजेक्शन मोल्डिंग दक्षता पर कोई प्रभाव नहीं पड़ता है।असत्य
बड़े हिस्सों को आम तौर पर लंबे चक्र समय की आवश्यकता होती है, जिससे इंजेक्शन मोल्डिंग प्रक्रिया में समग्र दक्षता प्रभावित होती है।
इंजेक्शन मोल्डिंग चक्र क्या बनता है?
क्या आपने कभी सोचा है कि इंजेक्शन मोल्डिंग चक्र के दौरान क्या होता है? इस प्रक्रिया को समझने से न केवल विनिर्माण दक्षता बढ़ती है बल्कि उत्पाद की गुणवत्ता में भी सुधार होता है। आइए इसे एक साथ खोजें!
एक इंजेक्शन मोल्डिंग चक्र में इंजेक्शन, होल्डिंग, कूलिंग, मोल्ड खोलना और इजेक्शन चरण शामिल होते हैं, जो उत्पादन की गति को बढ़ाने और उच्च गुणवत्ता वाले भागों को सुनिश्चित करने के लिए महत्वपूर्ण हैं।
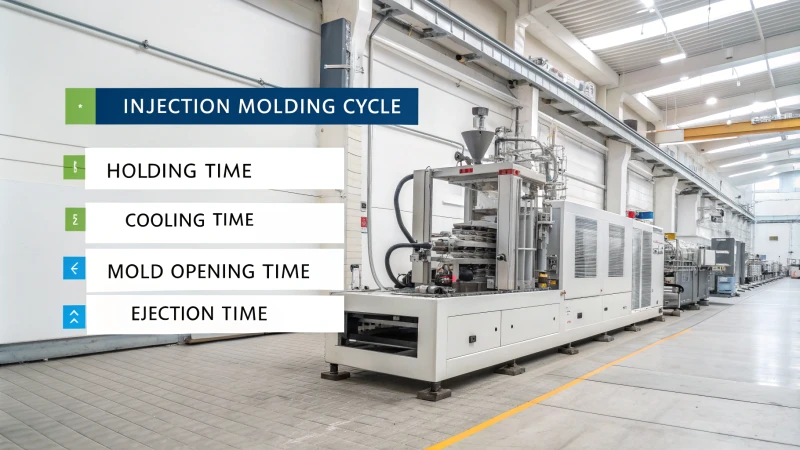
इंजेक्शन मोल्डिंग चक्र को समझना
एक डिजाइनर के रूप में, मैं अक्सर प्रशंसा करता हूं कि इंजेक्शन मोल्डिंग चक्र कितना जटिल है। यह एक सुव्यवस्थित नृत्य जैसा लगता है। सटीकता के साथ प्लास्टिक के हिस्से बनाने में प्रत्येक चरण की बहुत महत्वपूर्ण भूमिका होती है। चक्र में पांच मुख्य चरण शामिल हैं: इंजेक्शन समय, होल्डिंग समय, ठंडा करने का समय, मोल्ड खोलने का समय और इजेक्शन समय।
इंजेक्शन मोल्डिंग चक्र के चरण
- इंजेक्शन का समय: यहीं से प्रक्रिया शुरू होती है. पिघला हुआ प्लास्टिक मोल्ड गुहा में प्रवेश करता है, आमतौर पर छोटे भागों के लिए केवल 0.5 से 1 सेकंड में। इसे प्रभावित करने वाले कारकों में शामिल हैं:
- प्लास्टिक पिघलने की तरलता
- इंजेक्शन का दबाव
- इंजेक्शन की गति
- मोल्ड गुहा की जटिलता
कारक | विवरण |
---|---|
द्रवता | यह निर्धारित करता है कि प्लास्टिक कितनी आसानी से साँचे में प्रवाहित होता है |
इंजेक्शन का दबाव | उच्च दबाव प्रवाह दर को बढ़ा सकता है लेकिन भाग की गुणवत्ता को प्रभावित कर सकता है |
इंजेक्शन की गति | तेज़ गति से इंजेक्शन का समय कम हो जाता है लेकिन खराबी हो सकती है |
-
धारण समय : सांचा भर जाने के बाद, यह चरण शुरू होता है। प्लास्टिक के ठंडा और सिकुड़ने के दौरान दबाव बनाए रखने के लिए यह चरण बहुत महत्वपूर्ण है। यह आमतौर पर लगभग 5-10 सेकंड तक रहता है, यह इस पर निर्भर करता है:
- प्लास्टिक सामग्री के लक्षण
- भाग की दीवार की मोटाई
-
ठंडा करने का समय : ठंडा करने का समय अक्सर चक्र का सबसे लंबा हिस्सा होता है, जिससे ढले हुए हिस्से ठंडे हो जाते हैं और सांचे में जम जाते हैं। पतले भागों के लिए 10-20 सेकंड और मोटे भागों के लिए एक मिनट से अधिक का समय लग सकता है। शीतलन समय को प्रभावित करने वाले कारकों में शामिल हैं:
- सामग्री के थर्मल गुण
- दीवार की मोटाई और भाग का आकार
-
मोल्ड खुलने का समय : ठंडा होने के बाद, यह चरण तेजी से होता है और इसमें लगभग 1-3 सेकंड लगते हैं।
-
इजेक्शन टाइम : अंत में, इजेक्शन तब होता है जब मोल्ड किए गए हिस्से को लगभग 1-2 सेकंड में मोल्ड कैविटी से हटा दिया जाता है।
चक्र संरचना पर प्रभाव डालने वाले कारक
- प्लास्टिक सामग्री की विशेषताएँ : विभिन्न प्लास्टिक गर्मी और दबाव में अलग-अलग व्यवहार करते हैं। उदाहरण के लिए, उच्च तापीय चालकता वाले प्लास्टिक जल्दी ठंडे हो जाते हैं जबकि क्रिस्टलीय सामग्रियों को उचित क्रिस्टलीकरण सुनिश्चित करने के लिए अधिक समय की आवश्यकता होती है।
- भाग का आकार और आकार : बड़े या मोटे भागों को ठंडा होने में अधिक समय लगता है क्योंकि वे धीरे-धीरे गर्मी खो देते हैं; जटिल आकृतियों पर काम करते समय मैं अक्सर इन कारकों के आधार पर अपने डिज़ाइन बदलता हूँ।
- प्रक्रिया पैरामीटर : इंजेक्शन की गति, दबाव और धारण समय का मिश्रण महत्वपूर्ण है; उत्पाद मानकों को पूरा करते हुए दक्षता बनाए रखने के लिए गति और गुणवत्ता को संतुलित करना आवश्यक है।
- मोल्ड डिज़ाइन : मोल्ड डिज़ाइन में एक अच्छी शीतलन प्रणाली वास्तव में चक्र के समय को कम कर सकती है; कंफर्मल कूलिंग चैनल जैसे नवाचार मुझे प्रेरित करते हैं क्योंकि वे एक समान शीतलन की अनुमति देते हैं।
बेहतर उत्पादन के लिए इन चरणों को अनुकूलित करने के बारे में अधिक जानने के इच्छुक लोगों के लिए, इंजेक्शन मोल्डिंग प्रक्रिया अनुकूलन 1 की अनुशंसा की जाती है।
इंजेक्शन मोल्डिंग चक्र में शीतलन समय सबसे लंबा चरण है।सत्य
भाग की मोटाई के आधार पर ठंडा करने का समय काफी भिन्न होता है, जो इसे इंजेक्शन मोल्डिंग प्रक्रिया में सबसे विस्तारित चरण बनाता है।
इंजेक्शन मोल्डिंग में मोल्ड खोलने का समय इजेक्शन समय से अधिक समय लगता है।असत्य
मोल्ड का खुलना आम तौर पर 1-3 सेकंड तक चलता है, जबकि इजेक्शन में केवल 1-2 सेकंड लगते हैं, जिससे इजेक्शन तेज हो जाता है।
भौतिक गुण मोल्डिंग अवधि को कैसे प्रभावित करते हैं?
क्या आपने कभी सोचा है कि हम जो सामग्री चुनते हैं उसका मोल्डिंग प्रक्रिया पर क्या प्रभाव पड़ता है? सामग्री विशेषताओं और मोल्डिंग समय के बीच का संबंध शायद हमारे इंजेक्शन मोल्डिंग परियोजनाओं में वास्तव में मायने रखता है। इस ज्ञान से परियोजनाएँ बदल सकती हैं।
सामग्री के गुण मोल्डिंग अवधि को बहुत प्रभावित करते हैं, तापीय चालकता शीतलन की सुविधा प्रदान करती है और जटिल भाग डिजाइन इंजेक्शन की गति और गुणवत्ता आश्वासन के लिए आवश्यक होल्डिंग समय को प्रभावित करता है।
इंजेक्शन मोल्डिंग चक्र संरचना को समझना
कार्यशाला में, मैं इंजेक्शन मोल्डिंग की जटिल प्रक्रिया देखता हूं। प्रत्येक चक्र घटनाओं के एक समयबद्ध क्रम का अनुसरण करता है। भौतिक गुण हर चीज़ को प्रभावित करते हैं। यहां इंजेक्शन मोल्डिंग चक्र के चरणों पर एक त्वरित नज़र डाली गई है:
-
इंजेक्शन का समय : यह तब शुरू होता है जब प्लास्टिक पिघला हुआ मोल्ड गुहा में प्रवेश करता है। मैंने एक बहुत ही तरल प्लास्टिक के साथ काम किया जो केवल 0.5 सेकंड में इंजेक्ट हो गया! तरलता, दबाव और साँचे की जटिलता इस चरण को प्रभावित करती है।
-
धारण समय : भरने के बाद, ठंडा होने के दौरान सिकुड़न की अनुमति देने के लिए दबाव बना रहता है। सामग्री और मोटाई के आधार पर यह चरण 5 से 10 सेकंड तक रहता है। लंबे समय तक रखने से सटीकता सुनिश्चित होती है। यहाँ धैर्य फल देता है!
-
ठंडा करने का समय : ठंडा करने में सबसे अधिक समय लगता है। थर्मल गुण यहां सबसे ज्यादा मायने रखते हैं। पतली दीवार वाले हिस्से 10-20 सेकंड में ठंडे हो जाते हैं। मोटे भागों को एक मिनट से अधिक की आवश्यकता होती है। ऐसा लगता है कि यह बहुत लंबा समय है, लेकिन इससे मुझे बेहतर योजना बनाने में मदद मिलती है।
-
मोल्ड खुलने और बाहर निकलने में लगने वाला समय : ये चरण त्वरित हैं, खुलने में लगभग 1-3 सेकंड और बाहर निकलने में 1-2 सेकंड लगते हैं। जब भाग आसानी से सामने आता है तो सफलता बहुत अच्छी लगती है!
मोल्डिंग अवधि को प्रभावित करने वाली सामग्री की विशेषताएं
चुनी गई सामग्री चक्र समय पर बहुत अधिक प्रभाव डालती है। उच्च तापीय चालकता के कारण कुछ सामग्रियाँ तेजी से ठंडी होती हैं - यह एक वास्तविक गेम-चेंजर है!
भाग के आकार और आकार का प्रभाव
साइज़ और आकार भी महत्वपूर्ण हैं! भाग के आयाम और जटिलता चक्रों को प्रभावित करते हैं:
- बड़े हिस्से : ये धीमी गति से ठंडे होते हैं क्योंकि गर्मी धीरे-धीरे नष्ट होती है। एक बड़े घटक को मेरी अपेक्षा से अधिक समय लगा।
- जटिल आकार : जटिल डिज़ाइनों को अच्छी गुणवत्ता के लिए इंजेक्शन की गति और धारण समय में समायोजन की आवश्यकता होती है। यह ढलाई के समय को प्रभावित करता है, इसलिए मत भूलिए!
इंजेक्शन मोल्डिंग प्रक्रिया पैरामीटर्स की भूमिका
प्रक्रिया सेटिंग्स समान रूप से मायने रखती हैं:
- इंजेक्शन की गति और दबाव : तेज़ गति से समय कम हो जाता है लेकिन गुणवत्ता पर असर पड़ सकता है। सही संतुलन बहुत महत्वपूर्ण है.
- होल्डिंग दबाव : उचित होल्डिंग दबाव गुणवत्ता सुनिश्चित करता है लेकिन चक्र का समय भी बढ़ाता है। इन्हें संतुलित करना एक बड़ी चुनौती है!
प्रक्रिया अनुकूलन तकनीकें देखें ।
कूलिंग दक्षता में मोल्ड डिजाइन का महत्व
मोल्ड डिज़ाइन भी महत्वपूर्ण है! एक अच्छी शीतलन प्रणाली सब कुछ बदल सकती है:
- शीतलन प्रणाली डिज़ाइन : दबाव बनाए रखना: तेज़ शीतलन चैनल शीतलन समय को कम करते हैं। अनुरूप शीतलन डिज़ाइन एकरूपता और दक्षता में सुधार करते हैं - यह वास्तव में आश्चर्यजनक है!
अनुकूलित मोल्ड डिज़ाइन चक्र समय में बहुत सुधार करते हैं।
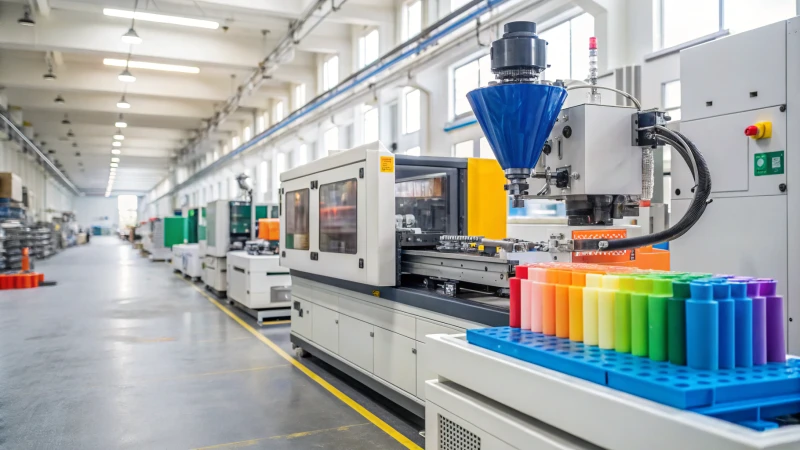
उत्पाद डिज़ाइन और सामग्री विशेषताओं को समझना
मैंने उत्पाद डिज़ाइन और मोल्ड को आकार देने में वर्षों बिताए। एक बात जो मैंने सीखी वह यह है कि भौतिक गुणों के छोटे-छोटे विवरण बहुत महत्वपूर्ण हैं। ये विवरण अक्सर हमारे कार्य चरणों को वास्तव में बेहतर बनाने की कुंजी होते हैं। तो, आइए एक साथ मिलकर इस विषय पर और गहराई से विचार करें!
उत्पाद डिज़ाइन में सामग्री विशेषताओं का महत्व
उत्पाद डिज़ाइन में उपयोग की जाने वाली सामग्रियों के विशिष्ट गुण प्रक्रिया की समग्र गुणवत्ता और दक्षता को नाटकीय रूप से प्रभावित कर सकते हैं। यहां कुछ प्रमुख कारक दिए गए हैं:
भौतिक गुण | उत्पाद की गुणवत्ता पर प्रभाव |
---|---|
सहनशीलता | उच्च स्थायित्व वाली सामग्री लंबे समय तक चलने वाले उत्पादों को सुनिश्चित करती है। |
FLEXIBILITY | लचीली सामग्री बिना टूटे अधिक जटिल डिज़ाइन बनाने की अनुमति देती है। |
सतही समापन | सतह की फिनिश उत्पाद के सौंदर्यशास्त्र और कार्यक्षमता दोनों को प्रभावित करती है। |
उदाहरण के लिए, इष्टतम स्थायित्व वाली सामग्री का चयन करने से न केवल उत्पाद का जीवनकाल बढ़ेगा बल्कि उपयोगकर्ता की संतुष्टि में भी सुधार होगा।
डिज़ाइन जटिलता और आकार का प्रभाव
डिज़ाइन किए जा रहे उत्पाद के आयाम और जटिलता महत्वपूर्ण विचार हैं:
- बड़े उत्पाद : इन्हें संरचनात्मक अखंडता बनाए रखने के लिए आम तौर पर अधिक मजबूत सामग्रियों की आवश्यकता होती है।
- जटिल डिज़ाइन : जटिल डिज़ाइन वाले उत्पादों को वांछित प्रदर्शन विशेषताओं को प्राप्त करने के लिए विशेष सामग्रियों की आवश्यकता हो सकती है।
सामग्री चयन में डिज़ाइन पैरामीटर्स की भूमिका
डिज़ाइन पैरामीटर भी सामग्री चयन के निर्धारण में महत्वपूर्ण भूमिका निभाते हैं:
- वजन पर विचार : हल्की सामग्री प्रयोज्यता बढ़ा सकती है लेकिन ताकत से समझौता कर सकती है, जिससे संतुलन की आवश्यकता होती है।
- लागत दक्षता : लागत प्रभावी सामग्री का चयन गुणवत्ता मानकों को बनाए रखते हुए परियोजना व्यवहार्यता सुनिश्चित करता है।
सामग्री चयन रणनीतियाँ 2 देखें ।
डिज़ाइन दक्षता में सामग्री गुणों के परीक्षण का महत्व
सामग्री गुणों का परीक्षण एक और महत्वपूर्ण पहलू है जो डिज़ाइन परिणामों को प्रभावित करता है:
- सामग्री परीक्षण विधियाँ : कुशल परीक्षण विधियाँ चयन प्रक्रियाओं में तेजी लाती हैं और इस प्रकार समग्र डिज़ाइन अवधि में सुधार करती हैं। उदाहरण के लिए, रैपिड प्रोटोटाइप सामग्री प्रदर्शन पर तत्काल प्रतिक्रिया प्रदान कर सकता है।
अनुकूलित परीक्षण प्रोटोकॉल का उपयोग करने से डिज़ाइन दक्षता में महत्वपूर्ण सुधार हो सकते हैं। उन्नत परीक्षण तकनीकों के बारे में और जानें
उच्च तापीय चालकता मोल्डिंग में शीतलन समय को कम कर देती है।सत्य
उच्च तापीय चालकता वाली सामग्री तेजी से ठंडी होती है, जिससे समग्र इंजेक्शन मोल्डिंग चक्र का समय कम हो जाता है।
जटिल भाग आकार हमेशा मोल्डिंग अवधि को बढ़ाते हैं।असत्य
जटिल डिज़ाइनों के लिए लंबे समय तक इंजेक्शन और होल्डिंग समय की आवश्यकता हो सकती है, जो किए गए समायोजन के आधार पर समग्र चक्र अवधि को सकारात्मक या नकारात्मक रूप से प्रभावित करता है।
मोल्ड डिज़ाइन साइकिल दक्षता को कैसे प्रभावित करता है?
क्या आपने कभी सोचा है कि मोल्ड डिज़ाइन इंजेक्शन मोल्डिंग में दक्षता को कैसे प्रभावित करता है? उत्पादन अनुकूलन को समझने का प्रयास करते समय मैंने इस चुनौती का अनुभव किया है। आइए जानें कि मोल्ड डिज़ाइन चक्र दक्षता को कैसे प्रभावित करता है!
मोल्ड डिज़ाइन इंजेक्शन मोल्डिंग में चक्र दक्षता में सुधार करने में महत्वपूर्ण भूमिका निभाता है। यह शीतलन प्रणालियों में सुधार, सामग्री विशेषताओं को समायोजित करने और प्रक्रिया सेटिंग्स को परिष्कृत करके ऐसा करता है। ये तत्व चक्र समय को छोटा करने में सहयोग करते हैं। वे उच्च गुणवत्ता वाले परिणाम की गारंटी भी देते हैं।
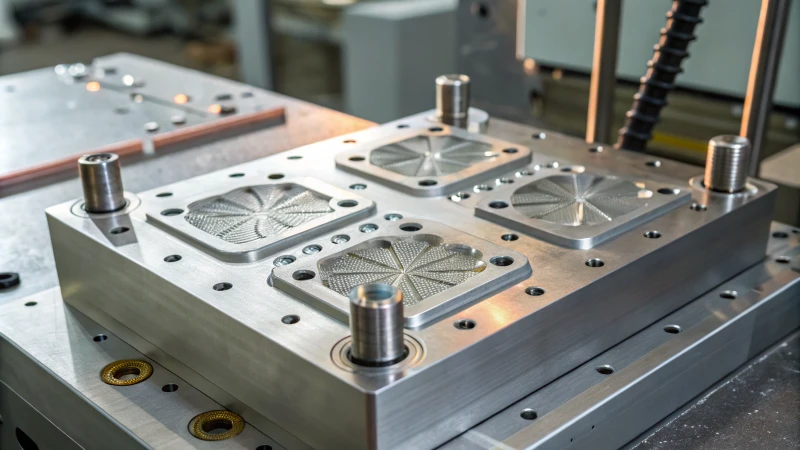
इंजेक्शन मोल्डिंग चक्र चरणों को समझना
इंजेक्शन मोल्डिंग चक्र एक ऑर्केस्ट्रा की तरह है, जिसमें प्रत्येक भाग एक आदर्श परिणाम के लिए मिलकर काम करता है। एक पूर्ण चक्र में कई महत्वपूर्ण चरण शामिल होते हैं:
-
इंजेक्शन का समय : यहां, प्रक्रिया शुरू होती है। पिघला हुआ प्लास्टिक सांचे में प्रवेश करता है। जब मैंने पहली बार इसे देखा तो मैं आश्चर्यचकित रह गया। यह किसी खजाने के संदूक में पिघले हुए सोने की लहर की तरह भर गया था! छोटे भागों के लिए, यह केवल 0.5 से 1 सेकंड में होता है। समय प्लास्टिक की तरलता और मोल्ड की जटिलता पर निर्भर करता है।
-
धारण समय : भरने के बाद, सिकुड़न से बचने के लिए 5-10 सेकंड तक दबाव बना रहता है। यह जीवन के विशेष क्षणों को पकड़कर रखने जैसा है - चीजों को ठीक से व्यवस्थित होने देने के लिए बस थोड़ा और समय चाहिए।
-
ठंडा करने का समय : इस चरण में सबसे लंबा समय लगता है। एक डिजाइनर के रूप में, मैं हिस्सों को अच्छे से देखता हूं। पतली दीवारें लगभग 10-20 सेकंड में ठंडी हो जाती हैं, जबकि मोटी दीवारें एक मिनट से अधिक समय लेती हैं। यह चरण धैर्य की परीक्षा लेता है, बहुत कुछ आटे के फूलने की प्रतीक्षा करने जैसा!
-
मोल्ड खुलने और बाहर निकलने में लगने वाला समय : ये त्वरित चरण खुलने में 1-3 सेकंड और बाहर निकलने में 1-2 सेकंड लगते हैं। यह चक्र का भव्य समापन है। तैयार हिस्से को उभरते हुए देखना वास्तव में फायदेमंद है।
कैसे मोल्ड डिज़ाइन दक्षता में सुधार करता है
अब, आइए देखें कि मोल्ड डिज़ाइन चक्र दक्षता को कैसे प्रभावित करता है:
- शीतलन प्रणाली डिज़ाइन : एक अच्छी शीतलन प्रणाली शीतलन समय को कम करती है और चक्र को गति देती है। मैंने अनुरूप शीतलन तकनीकें आज़माई हैं। नतीजों ने मुझे चकित कर दिया! यह सही पहेली टुकड़ा ढूंढने जैसा है जो प्रक्रिया को गति देता है।
ठंडा करने की विधि | दक्षता प्रभाव |
---|---|
अनुरूप शीतलन | उच्च |
मानक शीतलन | मध्यम |
-
सामग्री विशेषताएँ : प्लास्टिक के विकल्प चक्र समय को बहुत प्रभावित करते हैं। उच्च तापीय चालकता वाली सामग्री क्रिस्टलीय सामग्री की तुलना में तेजी से ठंडी होती है। यह आश्चर्यजनक है कि कैसे एक साधारण सामग्री का चुनाव दक्षता को प्रभावित करता है।
-
भाग की जटिलता : जटिल आकृतियाँ पेचीदा होती हैं! मुझे एक परियोजना याद है जहां जटिल डिजाइनों को गुणवत्ता बनाए रखने के लिए इंजेक्शन की गति और होल्डिंग समय में सावधानीपूर्वक बदलाव की आवश्यकता थी। इन मापदंडों को संतुलित करना रस्सी पर चलने जैसा है; सही काम करने पर सफलता मिलती है।
उदाहरण : एक बारीक विस्तृत भाग के बारे में सोचें। कभी-कभी हम इसका नाजुक आकार बनाए रखने के लिए इसे अधिक समय तक पकड़कर रखते हैं।
इंजेक्शन मोल्डिंग पैरामीटर्स में सुधार
यहां प्रमुख पैरामीटर हैं जो चक्र दक्षता में सुधार करते हैं:
- इंजेक्शन की गति : तेज़ गति से इंजेक्शन का समय कम हो जाता है, लेकिन गुणवत्ता उच्च बनी रहनी चाहिए। यह एक ऐसा संतुलन है जिसके लिए कौशल और अभ्यास की आवश्यकता है।
- होल्डिंग दबाव : सही दबाव दोषों को कम करता है लेकिन चक्र समय को बढ़ा सकता है। मैं अक्सर सेटिंग्स समायोजित करता हूं जब तक कि वे पूरी तरह से काम न करें।
मोल्ड डिज़ाइन और साइकिल दक्षता पर निष्कर्ष
संक्षेप में, अच्छा मोल्ड डिज़ाइन बेहतर शीतलन, सामग्री चयन और डिज़ाइन विवरण के माध्यम से इंजेक्शन मोल्डिंग चक्र दक्षता में सुधार करता है। इस ज्ञान ने मेरी विनिर्माण प्रथाओं और उत्पाद की गुणवत्ता में सुधार किया है। मोल्ड डिज़ाइन अनुकूलन 3 पर हमारा विस्तृत विश्लेषण देखें । साथ मिलकर, हम वास्तव में उत्कृष्ट परिणाम प्राप्त करते हैं!
कुशल शीतलन प्रणाली इंजेक्शन मोल्डिंग चक्र के समय को कम करती है।सत्य
शीतलन प्रणाली का डिज़ाइन शीतलन समय को कम करके, समग्र उत्पादन गति और गुणवत्ता को बढ़ाकर चक्र दक्षता पर सीधे प्रभाव डालता है।
जटिल भाग डिज़ाइन हमेशा इंजेक्शन मोल्डिंग चक्र की अवधि बढ़ाते हैं।असत्य
जबकि जटिल डिज़ाइनों को लंबे समय तक रखने की आवश्यकता हो सकती है, कुशल मोल्ड डिज़ाइन देरी को कम कर सकता है, जिससे यह दावा सार्वभौमिक रूप से सत्य नहीं हो जाता है।
मैं बेहतर परिणामों के लिए प्रक्रिया पैरामीटर्स को कैसे अनुकूलित कर सकता हूँ?
प्रक्रिया सेटिंग्स में सुधार करना विनिर्माण क्षेत्र में एक जटिल पहेली को सुलझाने जैसा लगता है। मेरी बात पर भरोसा करो. इन सेटिंग्स को समायोजित करने में केवल संख्याओं के अलावा और भी बहुत कुछ शामिल है। यह कुछ विशेष बनाने के बारे में है। हम यह कैसे हासिल करते हैं?
प्रक्रिया मापदंडों को अनुकूलित करने के लिए, सामग्री गुणों और भाग डिजाइन को समझने पर ध्यान केंद्रित करें। विनिर्माण दक्षता और उत्पाद की गुणवत्ता बढ़ाने, डेटा-संचालित निर्णयों के लिए डिज़ाइन ऑफ़ एक्सपेरिमेंट्स (डीओई) और तागुची पद्धति का उपयोग करें।
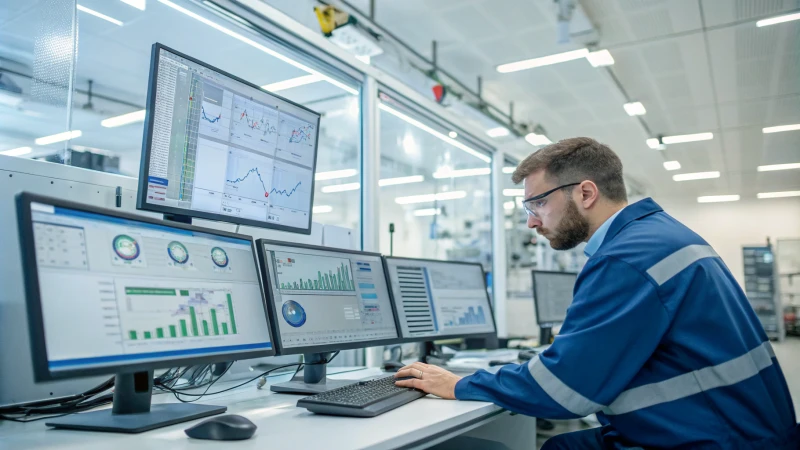
इंजेक्शन मोल्डिंग चक्र को समझना
इंजेक्शन मोल्डिंग चक्र की संरचना को समझना आवश्यक है । इस चक्र में कई चरण शामिल हैं:
- इंजेक्शन का समय: संदर्भित करता है कि पिघले हुए प्लास्टिक को मोल्ड कैविटी में डालने में कितना समय लगता है।
- विशिष्ट अवधि : आमतौर पर छोटे भागों के लिए 0.5-1 सेकंड के भीतर।
- धारण समय : सांचे को भरने के बाद सामान्यतः 5-10 सेकंड के बीच दबाव बनाए रखा जाता है।
- ठंड का समय: एक महत्वपूर्ण अवधि जहां प्लास्टिक जम जाता है, जो भौतिक गुणों के आधार पर काफी भिन्न होता है।
- पतली दीवार वाले हिस्सों के लिए, यह लगभग 10-20 सेकंड हो सकता है, जबकि बड़े हिस्सों के लिए 1 मिनट से अधिक हो सकता है।
- मोल्ड खुलने और बाहर निकलने का समय : ये अपेक्षाकृत कम होते हैं, आमतौर पर प्रत्येक में लगभग 1-3 सेकंड।
इनमें से प्रत्येक चरण को अनुकूलित करने से दक्षता और उत्पाद की गुणवत्ता में सुधार हो सकता है। इन चरणों के अधिक विस्तृत विवरण के लिए, इस व्यापक मार्गदर्शिका 4 ।
अनुकूलन पर प्रभाव डालने वाले कारक
कई प्रभावशाली कारक यह निर्धारित कर सकते हैं कि आप अपने प्रक्रिया मापदंडों को कितने प्रभावी ढंग से अनुकूलित कर सकते हैं:
कारक | विवरण | चक्र समय पर प्रभाव |
---|---|---|
प्लास्टिक सामग्री की विशेषताएँ | विभिन्न सामग्रियों में अलग-अलग थर्मल और रियोलॉजिकल गुण होते हैं। | उच्च तापीय चालकता शीतलन समय को कम कर देती है, जबकि क्रिस्टलीय प्लास्टिक को लंबे समय तक शीतलन की आवश्यकता होती है। |
भाग का आकार और आकार | बड़े या जटिल भागों को अधिक सावधानीपूर्वक पैरामीटर समायोजन की आवश्यकता होती है। | बढ़ा हुआ आकार गर्मी अपव्यय के कारण शीतलन समय को काफी लंबा कर सकता है। |
इंजेक्शन मोल्डिंग प्रक्रिया पैरामीटर | इंजेक्शन की गति और दबाव जैसे पैरामीटर चक्र समय और भाग की गुणवत्ता को प्रभावित करते हैं। | तेज़ इंजेक्शन गति समय को कम कर सकती है लेकिन अगर अच्छी तरह से प्रबंधित न किया जाए तो गुणवत्ता कम हो सकती है। |
साँचे का डिज़ाइन | अनुकूलित शीतलन चैनलों के साथ एक कुशल मोल्ड डिज़ाइन चक्र समय में काफी सुधार कर सकता है। | अनुरूप शीतलन डिज़ाइन शीतलन प्रक्रियाओं को तेज कर सकते हैं। |
इन कारकों को संबोधित करके, आप दक्षता और उत्पाद अखंडता के बीच बेहतर संतुलन प्राप्त कर सकते हैं। इस लेख 5 को देखें ।
अनुकूलन के लिए तरीके
प्रक्रिया मापदंडों को प्रभावी ढंग से अनुकूलित करने के लिए, डिज़ाइन ऑफ़ एक्सपेरिमेंट्स (डीओई) और तागुची पद्धति पर्याप्त लाभ मिल सकते हैं:
- प्रयोगों का डिज़ाइन (डीओई) : यह सांख्यिकीय पद्धति आपको परिणामों पर उनके प्रभाव की पहचान करने के लिए कई चर को व्यवस्थित रूप से बदलने की अनुमति देती है। नियंत्रित प्रयोगों का संचालन करके, आप इंजेक्शन की गति, दबाव और शीतलन समय के लिए इष्टतम सेटिंग्स पा सकते हैं।
- टैगुची विधि : मजबूत डिजाइन पर केंद्रित, इस दृष्टिकोण का उद्देश्य सावधानीपूर्वक पैरामीटर चयन के माध्यम से भिन्नता को कम करके गुणवत्ता में सुधार करना है। यह पहचानने में मदद करता है कि प्रदर्शन और निरंतरता के लिए कौन से पैरामीटर सबसे महत्वपूर्ण हैं।
इन पद्धतियों का उपयोग करने से कार्रवाई योग्य अंतर्दृष्टि मिलती है और डेटा-संचालित निर्णय मिलते हैं जो समग्र दक्षता को बढ़ाते हैं। विनिर्माण अनुकूलन से संबंधित अधिक विस्तृत कार्यप्रणाली के लिए, कृपया इस संसाधन 6 ।
छोटे भागों के लिए इंजेक्शन का समय आम तौर पर 0.5-1 सेकंड तक रहता है।सत्य
यह दावा इंजेक्शन मोल्डिंग चक्र में इंजेक्शन समय की मानक अवधि को दर्शाता है, जो दक्षता को अनुकूलित करने के लिए महत्वपूर्ण है।
डीओई का उपयोग इंजेक्शन मोल्डिंग प्रक्रिया दक्षता में सुधार कर सकता है।सत्य
प्रयोगों का डिज़ाइन (डीओई) व्यवस्थित रूप से चर का परीक्षण करता है, जिससे अनुकूलित सेटिंग्स और बेहतर विनिर्माण परिणाम प्राप्त होते हैं।
निष्कर्ष
प्लास्टिक इंजेक्शन मोल्डिंग अवधि को प्रभावित करने वाले प्रमुख कारकों में चक्र चरण, सामग्री विशेषताएँ, भाग आयाम, प्रक्रिया सेटिंग्स और मोल्ड डिज़ाइन शामिल हैं। इनमें महारत हासिल करने से उत्पादन क्षमता में सुधार हो सकता है।
-
बेहतर दक्षता और गुणवत्ता के लिए इंजेक्शन मोल्डिंग प्रक्रिया के प्रत्येक चरण को अनुकूलित करने के बारे में और जानें। ↩
-
पता लगाएं कि विभिन्न सामग्री गुण आपकी मोल्डिंग प्रक्रियाओं को कैसे अनुकूलित कर सकते हैं और उत्पाद की गुणवत्ता में सुधार कर सकते हैं। ↩
-
मोल्ड डिज़ाइन में उन्नत तकनीकों का पता लगाएं जो चक्र दक्षता में सुधार कर सकती हैं और उत्पादन समय को कम कर सकती हैं। ↩
-
प्रभावी अनुकूलन तकनीकों का पता लगाएं जो बेहतर परिणामों के लिए आपकी उत्पादन प्रक्रियाओं को बढ़ा सकती हैं। ↩
-
उन पद्धतियों के बारे में जानें जो आपकी विनिर्माण प्रक्रियाओं को सुव्यवस्थित करने में मदद कर सकती हैं। ↩
-
इंजेक्शन मोल्डिंग चक्रों पर विभिन्न सामग्री विशेषताओं के प्रभाव की खोज करें। ↩