Avez-vous déjà regardé un produit moulé par injection et constaté un défaut qui gâche sa perfection ? Sérieusement, cela arrive à tout le monde, même aux plus expérimentés d’entre nous.
Je cherche à améliorer la conception des moules pour réduire les défauts des articles moulés par injection. L'ajustement des paramètres du processus est également important. Des matières premières de haute qualité sont d’une grande aide. Ces étapes sont vraiment essentielles. Ils sont essentiels pour réduire les bavures, le retrait, les marques de soudure, les marques d’écoulement et les stries argentées.
Je me souviens de la première fois où j'ai découvert un gros problème de défauts. Cela a été une véritable révélation. La conception des moules nécessite beaucoup de soin. Chaque petit détail compte. L'espace entre les pièces du moule doit être très précis. Le réglage des paramètres d’injection, c’est comme régler un instrument de musique. Il faut de la patience et du soin pour bien faire les choses.
La sélection des matériaux vient ensuite. Choisir de bons matériaux, c’est comme choisir des ingrédients pour cuisiner. Des matériaux de qualité conduisent à un résultat parfait. Ce mélange de compétence et de concentration transforme quelque chose d’ordinaire en quelque chose de spécial.
L'optimisation de la conception des moules réduit les marques de soudure.Vrai
Une conception appropriée du moule garantit un flux de matériau uniforme, minimisant ainsi les marques de soudure.
Les matières premières de haute qualité augmentent le retrait.FAUX
Les matériaux de haute qualité réduisent les défauts comme le retrait, mais ne les augmentent pas.
- 1. Comment la conception de moules peut-elle aider à minimiser le flash ?
- 2. Comment l’optimisation des processus aide-t-elle à réduire la démarque inconnue ?
- 3. Pourquoi la position du portail est-elle importante pour éliminer les marques de soudure ?
- 4. Comment la conception des canaux affecte-t-elle les marques d'écoulement ?
- 5. Comment puis-je éviter les traces d’argent lors du moulage par injection ?
- 6. Conclusion
Comment la conception de moules peut-elle aider à minimiser le flash ?
Le design Flash in Mold est ennuyeux comme découvrir des poils de chien dans votre café du matin. Ne t'inquiète pas! Nous explorons les moyens de résoudre ce problème embêtant et de produire des produits plus propres et plus efficaces.
Une bonne conception du moule réduit les bavures en gardant les surfaces de joint précises. Des espaces uniformes dans les inserts sont d’une grande aide. Définir les bons paramètres de moulage par injection est également essentiel. Ces étapes améliorent réellement la qualité du produit. Ils ont également réduit les déchets. Moins de déchets est important.
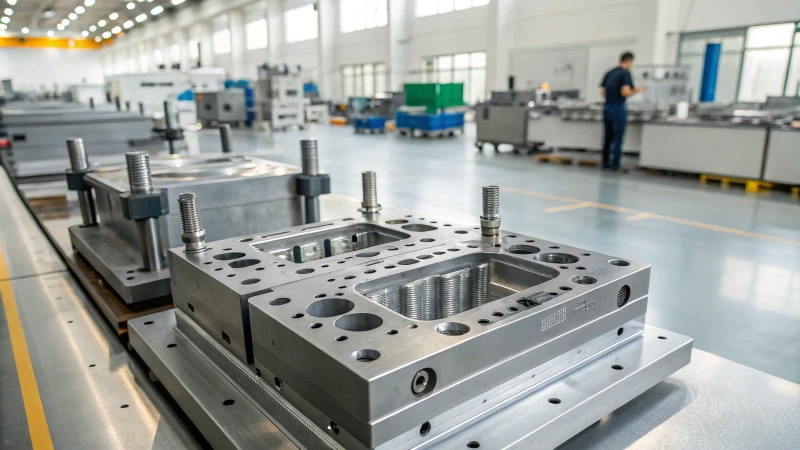
L'importance de surfaces de séparation précises
Lorsque j'ai commencé à travailler dans la conception de moules 1 , j'ai rapidement compris l'importance de surfaces de joint précises. Imaginez un puzzle qui ne s'ajuste pas bien. C'est ce que l'on ressent lorsque les surfaces de joint du moule ne sont pas correctes. Le maintien d'une rugosité de surface inférieure à Ra0,8 μm empêche les matériaux indésirables – appelés flash – de s'échapper et de ruiner le produit final.
Rugosité de la surface | Norme pour la réduction du flash |
---|---|
En dessous de Ra0,8 μm | Fortement recommandé |
Flash est ennuyeux. Cela ruine le produit final.
Espaces uniformes dans les inserts de moule
Une autre première leçon concernait les espaces uniformes dans les inserts de moule. C'est comme préparer des biscuits de la même taille. La cohérence compte. Pour les thermoplastiques, un écart compris entre 0,03 et 0,05 mm permet de maintenir l'étanchéité.
Type de matériau | Plage d'écart optimale |
---|---|
Thermoplastiques | 0,03-0,05 mm |
Cette précision réduit les risques de flash.
Ajustement des paramètres de moulage par injection
Ajuster les paramètres de moulage par injection me fascinait. C'est comme accorder parfaitement une guitare.
Commencer avec une pression d’injection élevée et l’abaisser lentement de 5 à 10 MPa permet de trouver le bon équilibre.
Paramètre | Réglage initial | Guide de réglage |
---|---|---|
Pression d'injection | Haut | Réduire de 5 à 10 MPa |
Il remplit bien le produit sans morceaux supplémentaires, ce qui en fait un exercice d'équilibre.
Utilisation des outils de CAO pour l'optimisation de la conception
Les outils CAO 2 ont tout changé pour moi. Ils nous permettent de simuler et d'affiner les conceptions de moules avant la production réelle, un peu comme une répétition générale où vous pouvez repérer des problèmes potentiels tels que des espaces inégaux ou des surfaces de joint mal alignées et les résoudre avant le spectacle final.
Étude de cas : réussite grâce à une conception de moule optimisée
Permettez-moi de partager l'histoire d'une entreprise de taille moyenne fabriquant des pièces en plastique pour l'électronique. Ils ont optimisé la conception de leurs moules, obtenant des surfaces de joint précises et des espaces uniformes, ce qui a considérablement réduit les bavures et amélioré leur efficacité de production.
Leur succès a montré à quel point ces optimisations sont cruciales.
l'intégration de ces pratiques signifie que les concepteurs de moules réduisent réellement les bavures, ce qui se traduit par une meilleure qualité de produit et moins de déchets – une approche qui s'aligne sur les objectifs de fabrication durable, ce qui me passionne profondément.
La rugosité de la surface inférieure à Ra0,8 μm empêche le flash.Vrai
Une surface plus lisse minimise les infiltrations excessives de matériau, empêchant ainsi les éclairs.
Les outils de CAO ne peuvent pas identifier les écarts inégaux dans la conception des moules.FAUX
Les outils de CAO simulent les conceptions pour détecter les problèmes tels que les écarts inégaux avant la production.
Comment l’optimisation des processus aide-t-elle à réduire la démarque inconnue ?
Avez-vous déjà pensé à changer vos méthodes pour économiser de l’argent et améliorer la qualité ?
L'optimisation des processus est cruciale pour réduire la démarque inconnue. Cela implique d’ajuster la conception des moules, de modifier les paramètres d’injection et d’améliorer les structures des produits. Ces changements conduisent à une utilisation efficace des matériaux. Les défauts tels que les marques de flash et d’évier deviennent moins fréquents. La qualité globale de la production s’améliore vraiment.

Améliorer la conception des moules
Une leçon clé m'a appris l'importance de corriger la conception des moules. En obtenant la bonne surface de joint du moule, nous avons considérablement réduit les bavures et les débordements 3 , qui gaspillaient auparavant de la matière. Cela signifiait garder les surfaces planes et contrôler la rugosité en dessous de Ra0,8 μm. Les inserts de moule avec des espaces réguliers – généralement de 0,03 à 0,05 mm pour les thermoplastiques – ont contribué à améliorer la précision du produit.
Ajustement des paramètres de moulage par injection
Le réglage fin des paramètres de moulage par injection a été une véritable découverte. En modifiant soigneusement la pression d'injection et la force de serrage, nous avons pu éviter les traces d'enfoncement. Je me souviens d'un cas où une pression de 100 MPa a provoqué un éclair ; nous avons fait de petits ajustements jusqu'à ce que nous y parvenions. Cette méthode d’essais et d’erreurs a parfaitement rempli le produit.
Améliorer la conception des produits
La conception des produits était un autre objectif pour réduire le retrait. Il était important de conserver une épaisseur de paroi uniforme, en particulier là où des changements étaient nécessaires, comme près des nervures. Nous avons utilisé une transition progressive sur 3 à 5 mm, ce qui a vraiment stoppé les traces d'évier 4 et amélioré la qualité du produit.
Utilisations réelles
Ces stratégies sont utiles, pas seulement des idées. Leur utilisation nous a aidé à réduire le retrait, ce qui a entraîné moins de défauts et une meilleure utilisation des matériaux. Il est très satisfaisant de voir ces améliorations augmenter les bénéfices et la durabilité pendant la production.
Aspect | Stratégie d'optimisation | Exemple de paramètre |
---|---|---|
Conception de moules | Rugosité de surface de contrôle inférieure à Ra0,8 μm | Écart thermoplastique : 0,03 mm |
Pression d'injection | Réduire de 5 à 10 MPa en cas de clignotement | Initiale : 100 MPa |
Épaisseur de paroi du produit | Concevoir une transition progressive pour les côtes | Longueur de transition : 3-5 mm |
En mettant en œuvre ces stratégies, les entreprises peuvent réduire efficacement le retrait 5 , ce qui entraîne moins de défauts et une meilleure efficacité des matériaux, augmentant ainsi la rentabilité et la durabilité des processus de production.
L'écart uniforme du moule améliore la précision du produit.Vrai
Des espaces de moule uniformes, de 0,03 à 0,05 mm pour les thermoplastiques, améliorent la précision.
La réduction de la pression d’injection évite les traces d’évier.FAUX
La réduction de la pression peut empêcher les éclairs, et non les traces d'évier, qui nécessitent des modifications de conception.
Pourquoi la position du portail est-elle importante pour éliminer les marques de soudure ?
Certaines pièces moulées semblent parfaites, tandis que d’autres présentent des lignes irritantes. La position de la porte compte !
La position de la porte revêt une grande importance dans le moulage par injection. Il garantit un flux constant de matière plastique fondue. Ce flux constant réduit les marques de soudure. Des conditions matérielles très lisses sont essentielles. Ces conditions conduisent à des pièces sans défauts.
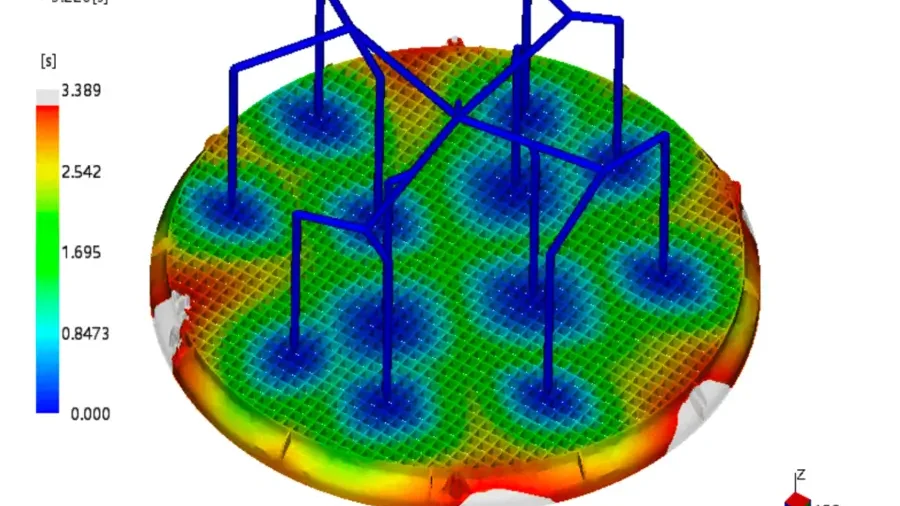
Comprendre les marques de soudure dans le moulage par injection
Les marques de soudure, également appelées lignes de soudure ou lignes de tricot, se produisent lorsque deux ou plusieurs fronts d'écoulement se rencontrent et se solidifient avant de fusionner complètement. Cela peut provoquer des points faibles et des lignes visibles sur la pièce moulée. La position de la porte est cruciale car elle dicte le chemin d’écoulement et la vitesse du plastique fondu.
Stratégies de positionnement des portes
-
Positionnement centralisé des portes : le placement des portes au centre permet au matériau de s'écouler uniformément, réduisant ainsi la distance parcourue par chaque front d'écoulement avant de se rencontrer. Par exemple, dans un produit en forme de boîte, une porte centrale assure un flux symétrique.
-
Plusieurs portes : L'utilisation de plusieurs portes peut aider à répartir le flux plus uniformément, bien que cette approche nécessite un équilibrage minutieux pour éviter de créer de nouvelles lignes de soudure.
-
Optimisation de la conception du moule : La conception du de moule et de porte 6 doit viser à minimiser les marques de soudure en permettant au matériau de se réunir dans des conditions optimales : température et vitesse élevées.
Caractéristique du moule | Impact sur les marques de soudure |
---|---|
Porte centrale | Réduit les lignes de soudure |
Puits froid | Recueille la fonte plus froide |
Paramètres de moulage par injection
L'ajustement de paramètres tels que la température de fusion et la vitesse d'injection peut affecter considérablement les marques de soudure :
- Augmentation de la température de fusion : améliore la fluidité, permettant aux chaînes moléculaires de mieux fusionner.
- Vitesse d'injection accrue : Assure un remplissage plus rapide et réduit le temps de refroidissement avant convergence.
Par exemple, augmenter la température de fusion des matériaux en polypropylène ( PP ) de 190 à 220 °C à 200 à 230 °C peut réduire les marques de soudure.
Exemples de mise en œuvre pratique
En termes pratiques, supposons que vous conceviez un boîtier d'appareils électroniques grand public 7 , placer les portes dans des zones d'épaisseur de paroi uniforme peut aider à maintenir la résistance et la qualité esthétique. De même, l'ajout de puits froids aux convergences d'écoulement peut piéger un matériau plus froid et moins fluide, l'empêchant ainsi d'affecter la qualité de surface du produit final.
En ajustant ces facteurs, les designers comme Jacky au Canada peuvent réaliser des produits de haute qualité qui répondent aux besoins fonctionnels et esthétiques sans compromettre l'efficacité de la production ou la rentabilité.
Le positionnement centralisé du portail réduit les marques de soudure.Vrai
Le placement central permet un flux de matériau uniforme, minimisant les lignes de soudure.
Plusieurs portes éliminent toujours les marques de soudure.FAUX
Plusieurs portes peuvent créer de nouvelles lignes de soudure si elles ne sont pas correctement équilibrées.
Comment la conception des canaux affecte-t-elle les marques d'écoulement ?
Avez-vous déjà réfléchi à la raison pour laquelle ces marques d'écoulement gênantes apparaissent sur vos pièces moulées par injection ? La clé est la conception du coureur. Une conception correcte des coureurs change probablement tout.
La conception des canaux affecte les repères d'écoulement en contrôlant la fluidité du mouvement de la matière fondue à travers le moule. Un système de glissières soigneusement planifié favorise un flux fluide. Cela réduit l’apparence des traces d’écoulement sur les produits finaux.
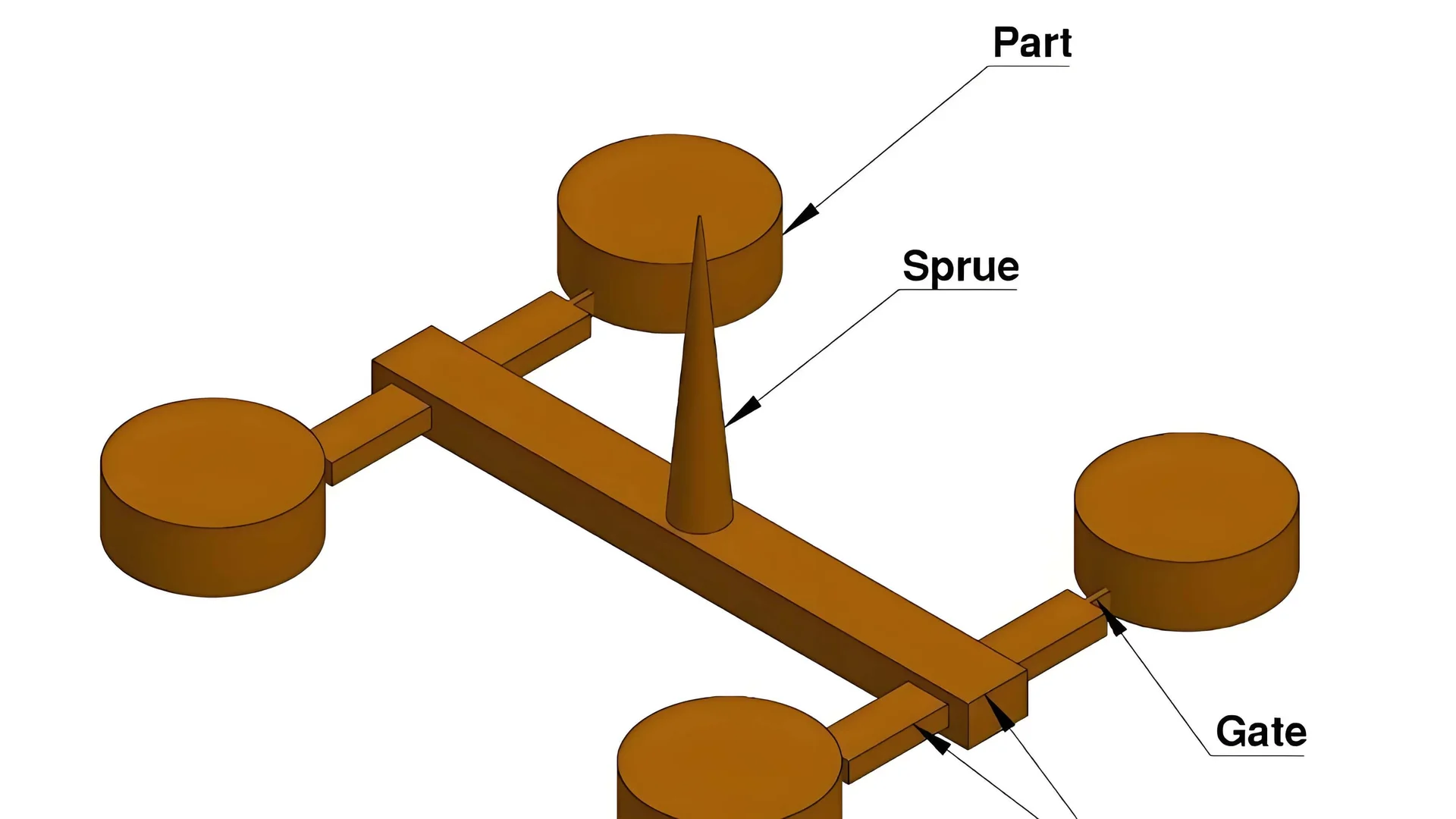
Le rôle de la qualité de la surface des coureurs
Les coureurs sont comme des autoroutes pour les matériaux chauds. S'ils sont rugueux et cahoteux, le trajet devient difficile, entraînant de vilaines traces d'écoulement. Une surface de roulement lisse signifie moins de résistance. Il permet au matériau de se déplacer facilement, comme si on conduisait sur une nouvelle route. C'est doux.
Tableau : Rugosité de la surface des glissières par rapport aux marques d'écoulement | Rugosité de la surface | Gravité du repère de flux |
---|---|---|
Ra0,8 μm | Haut | |
Ra0,4 μm | Faible |
Optimisation des dimensions des coureurs
Une fois, j'ai porté des chaussures de mauvaise taille pour un marathon. Cela m'a appris à quel point la taille et l'ajustement sont essentiels. Les coureurs doivent aussi être parfaits. S'il est trop petit, des problèmes de pression surviennent ; s'il est trop grand, vous gaspillez des ressources.
Des canaux plus grands et de taille plus appropriée facilitent une pression et un écoulement de fusion constants, réduisant ainsi les défauts de surface 8 .
Position et conception de la porte
Choisir la bonne position du portail, c’est comme planter dans le jardin parfait. Il faut qu'il soit parfait pour bien pousser. Une porte bien placée permet un écoulement fluide et moins de turbulences.
L'utilisation d'une porte ponctuelle 9 avec des dimensions optimales peut renforcer cet effet.
Effet de la vitesse et de la température d'injection
Changer la vitesse d’injection et la température, c’est comme cuisiner. Trop vite ou trop lentement pourrait gâcher le plat. Trouver l’équilibre parfait permet à la fonte de s’écouler en douceur.
Par exemple, l'ajustement ABS de 30-50 mm/s à 40-60 mm/s peut améliorer les résultats en améliorant la fluidité et en réduisant les marques d'écoulement potentielles sur la surface.
Stratégies d'optimisation des coureurs
Rassembler ces idées permet de minimiser les marques de flux. J'ai passé de nombreuses heures avec un logiciel de CAO, créant différents designs : c'est comme si un artiste perfectionnait son travail.
Lorsque tout s’enchaîne parfaitement, c’est vraiment satisfaisant, comme voir une pièce de puzzle s’adapter.
Pour obtenir des résultats optimaux, envisagez de mettre en œuvre une stratégie globale impliquant des améliorations de la conception des canaux ainsi que des ajustements des paramètres de processus à l'aide d'outils tels qu'un logiciel de CAO pour visualiser et tester différentes conceptions afin de minimiser les marques d'écoulement 10 .
Des coureurs plus lisses réduisent les marques d’écoulement.Vrai
Une surface de canal plus lisse diminue la résistance, permettant un écoulement uniforme de la matière fondue.
Les canaux plus grands augmentent les défauts de surface.FAUX
Les patins plus grands facilitent une pression constante, réduisant ainsi les défauts de surface.
Comment puis-je éviter les traces d’argent lors du moulage par injection ?
Je me souviens encore de l'irritation liée à la manipulation de traces argentées sur des objets en plastique. Ces marques gâchent la qualité et diminuent la confiance des clients. Personne ne les aime. Mais ne vous inquiétez pas, il y a de l'espoir !
Le séchage des matières plastiques aide vraiment à prévenir les traces d'argent lors du moulage par injection. Les conceptions de moules nécessitent des ajustements pour obtenir les meilleurs résultats. Un ajustement minutieux des paramètres d’injection est essentiel pour arrêter l’accumulation de gaz et la surchauffe.

Le rôle de la préparation des matières premières
Lorsque je suis entré dans le domaine du moulage par injection, j’ai rapidement découvert que le séchage des matières plastiques était très important. Un moment inoubliable grâce à l'utilisation du PA (polyamide). J'ai passé des heures à modifier les paramètres, pour découvrir que ne pas sécher suffisamment provoquait des traces argentées gênantes. Désormais, le PA sèche toujours à 80-100°C pendant 4 à 8 heures. L'humidité doit être inférieure à 0,1%. Cette étape simple m’a évité de nombreux problèmes.
Matériel | Température de séchage (°C) | Temps de séchage (heures) |
---|---|---|
Pennsylvanie | 80-100 | 4-8 |
Ajustement des paramètres de moulage par injection
Changer les paramètres d’injection a été une autre leçon difficile. Une fois, j'ai eu du mal avec trop de chaleur à l'arrière du canon. Cela provoquait des gaz indésirables. De nos jours, je contrôle la vitesse des vis pour arrêter les coupes excessives de plastique. Habituellement, il reste entre 30 et 60 tr/min. La bonne vitesse est essentielle, comme le rythme d’une chanson.
Conseils importants pour la conception de moules
La conception de moules a parfaitement changé mon approche de la réduction des défauts. Le traitement soigneux de la surface de séparation est pour moi une priorité. Il doit avoir une rugosité inférieure à Ra0,8μm. Ce soin garantit que les espaces s’alignent bien avec les caractéristiques du matériau.
Aspect conception | Norme recommandée |
---|---|
Rugosité de la surface | En dessous de Ra0,8 μm |
L’inclusion de ces étapes dans le travail quotidien a réellement amélioré la qualité et l’apparence des produits. Si vous rencontrez des problèmes similaires, envisagez de rechercher plus d'informations sur le perfectionnement de la conception du moule 11 et la modification des paramètres de moulage 12 pour améliorer vos compétences. Que vous soyez expérimenté ou que vous débutiez comme moi, il est toujours possible de grandir et d'en apprendre davantage.
Le PA doit être séché à 80-100°C pendant 4 à 8 heures.Vrai
Le séchage du PA à cette plage réduit l'humidité, évitant ainsi les stries argentées.
Les vitesses de vis doivent dépasser 60 tr/min pour éviter les défauts.FAUX
Une vitesse de vis excessive peut augmenter le cisaillement, provoquant des défauts.
Conclusion
Cet article traite des stratégies efficaces pour minimiser les défauts des produits moulés par injection, en se concentrant sur la conception des moules, la sélection des matériaux et l'optimisation des processus afin d'améliorer la qualité des produits et de réduire les déchets.
-
Découvrez pourquoi l'obtention d'une surface de joint précise est cruciale pour éviter les bavures lors du moulage par injection. ↩
-
Découvrez les meilleures options logicielles de CAO qui aident à optimiser les conceptions de moules pour éviter les bavures et améliorer la qualité des produits. ↩
-
Découvrez comment une conception précise des moules évite les débordements de matériaux et améliore la qualité de la production. ↩
-
Découvrez des stratégies pour garantir l’uniformité de l’épaisseur des murs et prévenir les traces d’évier. ↩
-
Explorez des méthodes complètes pour minimiser le gaspillage de matériaux et augmenter l’efficacité. ↩
-
L'exploration des principes de conception des portes permet d'optimiser l'efficacité du moule et de réduire les défauts tels que les marques de soudure. ↩
-
L'apprentissage du positionnement des portes pour l'électronique améliore la qualité et la durabilité des produits. ↩
-
La découverte des dimensions idéales des canaux aide à obtenir une pression de fusion uniforme, réduisant ainsi les défauts de surface. ↩
-
Les portes ponctuelles assurent une répartition uniforme de la matière fondue, minimisant les turbulences et les traces d'écoulement. ↩
-
L'exploration de stratégies d'optimisation des canaux peut réduire considérablement les marques d'écoulement dans les produits moulés. ↩
-
Apprenez des stratégies avancées pour améliorer la conception des moules, essentielles pour réduire les défauts tels que les stries argentées. ↩
-
Découvrez des directives détaillées sur l’optimisation des paramètres de moulage afin d’améliorer la qualité des produits. ↩