La création d’une surface de joint parfaite dans le moulage par injection peut changer la donne en matière de qualité des produits. Mais comment réussir à chaque fois ?
Les techniques de conception optimales pour les surfaces de séparation des moules à injection mettent l'accent sur la forme, l'apparence et la facilité de traitement du produit, garantissant un démoulage en douceur, des défauts minimes et une fabrication efficace.
Vous savez, lorsque j’ai commencé à travailler avec des moules à injection, j’étais submergé par tous les détails qui nécessitaient une attention particulière. C’était comme assembler un puzzle complexe où chaque pièce devait s’emboîter parfaitement pour créer quelque chose de vraiment remarquable. Au fil du temps, j'ai réalisé que maîtriser la conception des surfaces de joint, c'était comme trouver la dernière pièce d'un puzzle : c'est crucial pour obtenir une finition impeccable.
Examinons quelques stratégies qui m'ont aidé à affiner mon approche. Pour les formes simples, comme une coupelle cylindrique, le positionnement de la surface de joint le long du contour maximum simplifie la structure du moule. Mais lorsqu’il s’agit de formes complexes, garantir un démoulage en douceur devient essentiel. J'ai appris que l'utilisation de mécanismes de traction latéraux pour les contre-dépouilles ou les surfaces de joint étagées pour différentes caractéristiques peut faire toute la différence.
L'apparence joue également un rôle important, en particulier avec des surfaces de haute qualité comme les intérieurs d'automobiles. Éviter les lignes de séparation peut éviter les bavures et les marques de soudure disgracieuses. Et n'oubliez pas la commodité du traitement. Choisir des surfaces planes plutôt que des courbes facilite le fraisage et le meulage – des leçons que j'ai apprises à mes dépens pendant les nuits tardives en atelier.
L'intégration de ces techniques améliore non seulement la qualité du produit moulé, mais rationalise également le processus de fabrication. Croyez-moi, une fois que vous aurez réussi ces conceptions, vos projets passeront de bons à excellents en un rien de temps.
Les surfaces de joint influencent la qualité de l’apparence du produit.Vrai
Une conception appropriée des surfaces de joint minimise les défauts visibles, améliorant ainsi l'apparence.
Ignorer la forme dans la conception conduit à un démoulage efficace.FAUX
La prise en compte de la forme est cruciale pour un démoulage en douceur et éviter les défauts.
- 1. Comment la forme du produit influence-t-elle la conception des surfaces de joint ?
- 2. Pourquoi les exigences d’apparence sont-elles cruciales pour les surfaces de joint ?
- 3. Quelles sont les considérations relatives au traitement et à l'assemblage des surfaces de joint ?
- 4. Comment le processus de moulage par injection affecte-t-il la conception des surfaces de joint ?
- 5. Quels sont les défis et solutions courants dans la conception des surfaces de joint ?
- 6. Conclusion
Comment la forme du produit influence-t-elle la conception des surfaces de joint ?
Vous êtes-vous déjà demandé comment la forme d'un produit peut dicter la conception complète de son moule ? Laissez-moi vous expliquer cet aspect fascinant de la fabrication.
La forme du produit a un impact sur la conception des surfaces de joint en déterminant la complexité du moule et la facilité de démoulage. Les formes simples permettent des lignes de séparation simples, tandis que les formes complexes nécessitent des conceptions complexes pour gérer des caractéristiques telles que les contre-dépouilles.

Les bases de la conception des surfaces de joint
Je me souviens encore de ma première expérience pratique avec le moulage par injection. Je débutais tout juste et l’idée de créer une surface de séparation me paraissait intimidante. Imaginez ceci : la surface de séparation 1 est l'endroit où les deux moitiés du moule se rejoignent, ce qui est crucial pour permettre au produit d'être facilement retiré. Il est étonnant de constater à quel point la forme d'un produit influence cette configuration.
Formes simples ou complexes
Lorsque j’ai traité pour la première fois de formes simples – pensez aux cylindres ou aux cuboïdes – le processus était plus simple. Vous pouvez souvent aligner la ligne de joint le long du contour le plus grand, ce qui simplifie la construction du moule et réduit les coûts. Je me souviens d'un projet de coupelle cylindrique où l'alignement de la ligne de séparation avec l'axe central faisait que tout se mettait en place. C'est presque comme trouver la pièce de puzzle parfaite.
Type de forme | Considérations |
---|---|
Simple | Aligner avec le contour maximum |
Complexe | Assurer un démoulage en douceur |
Mais lorsqu'il s'agit de formes complexes , comme celles comportant des contre-dépouilles ou des caractéristiques directionnelles multiples, cela devient plus délicat. Un jour, j'ai abordé un projet comportant des fonctionnalités complexes qui nécessitaient des mécanismes d'extraction de noyau latéraux. Imaginez-les comme de petits ninjas du moule travaillant dans les coulisses pour gérer les points délicats.
Impact sur l'apparence et la fonctionnalité
Pour les produits nécessitant une haute qualité esthétique, tels que l’électronique grand public, il est crucial de masquer ou de minimiser les lignes de séparation. J'ai appris cela à mes dépens, lorsque la moindre marque de soudure ressortait sur un boîtier de gadget élégant. Pour les matériaux transparents, c'est encore plus délicat ; les défauts au niveau de la surface de joint peuvent être flagrants, affectant à la fois la transparence et les propriétés optiques.
Défis de traitement et d’assemblage
Il est essentiel de prendre en compte à la fois la commodité du traitement et les exigences d'assemblage lors de la conception des surfaces de joint 2 . J'utilise souvent des broches ou des clés de positionnement pour maintenir l'alignement pendant l'assemblage. C'est un peu comme installer des blocs Lego : vous voulez que tout s'emboîte parfaitement pour un fonctionnement fluide.
Considérations sur le processus de moulage par injection
Enfin, la surface de joint doit permettre un écoulement et une ventilation efficaces du plastique pendant le moulage par injection. J'ai pu constater par moi-même comment des portes et des canaux de ventilation correctement positionnés peuvent éviter des problèmes tels que des tirs courts ou des gaz piégés, qui peuvent dégrader la qualité du produit.
Équilibrer tous ces facteurs n’est pas seulement une question de savoir-faire technique ; il s'agit de comprendre l'impact de chaque choix sur l'efficacité de la production et la qualité des produits. C'est un puzzle où chaque pièce compte.
Les formes simples permettent un placement facile des lignes de séparation.Vrai
Des formes simples comme des cylindres permettent un alignement simple des lignes de joint.
Les formes complexes ne nécessitent jamais de mécanismes latéraux.FAUX
Les formes complexes nécessitent souvent des noyaux latéraux pour démouler des éléments complexes.
Pourquoi les exigences d’apparence sont-elles cruciales pour les surfaces de joint ?
Vous êtes-vous déjà demandé pourquoi l'apparence de vos surfaces de joint est si importante ? Voyons comment l'apparence affecte à la fois la qualité et l'esthétique des produits moulés.
Les exigences en matière d'apparence des surfaces de joint sont cruciales pour améliorer l'attrait visuel et la fonctionnalité des produits en plastique en évitant les défauts tels que les bavures et les marques de soudure, ce qui donne lieu à un produit plus attrayant.

Comprendre les surfaces de séparation et leur rôle
Lorsque j'ai découvert le monde du moulage par injection 3 , j'ai rapidement appris que les surfaces de joint, où se rencontrent deux moitiés d'un moule, sont essentielles. La façon dont ces surfaces sont conçues peut faire ou défaire le processus de fabrication, ayant un impact sur l'apparence du produit final. Si la conception est erronée, vous risquez de vous retrouver avec des éclairs (un excès de matériau qui s'échappe) ou des lignes de soudure visibles, qui peuvent tous deux ruiner l'esthétique d'un produit.
Équilibrer fonctionnalité et esthétique
Je me souviens avoir travaillé sur un projet de gadget électronique élégant. Les enjeux étaient élevés, car toute imperfection pouvait décourager les acheteurs potentiels. Pour des produits à enjeux aussi élevés, en particulier ceux comportant des matériaux transparents, il est crucial de garantir des lignes de séparation impeccables. Même une petite imperfection peut attirer le regard et gâcher l’ensemble du look. Cela signifie que le placement du moule et de la porte est parfait pour éviter ces imperfections.
Facteurs influençant la conception des surfaces de joint
Considération | Description |
---|---|
Forme du produit | Les formes simples permettent une conception plus facile ; les formes complexes peuvent nécessiter des techniques avancées telles que le tirage latéral. |
Type de matériau | Les matériaux transparents nécessitent un examen attentif pour éviter les défauts affectant la clarté. |
Traitement des moules | La précision est la clé ; les surfaces courbes peuvent nécessiter un équipement spécial comme des machines EDM. |
Conseils pratiques pour les designers
D'après mon expérience, le choix de plans plats pour les surfaces de joint simplifie à la fois le traitement et l'assemblage. Prenons par exemple les formes cubiques ; le positionnement des surfaces de joint le long de leur contour maximum rend le moule simple et la production plus fluide.
Lorsque des nervures de renforcement entrent en jeu, il est essentiel d’aligner les lignes de joint parallèlement à elles pour ne pas perturber leur structure. En m'en tenant à ces stratégies, j'ai trouvé beaucoup plus facile de produire des designs à la fois fonctionnels et agréables à l'œil.
Une mauvaise conception de la surface de joint provoque des défauts de bavure.Vrai
Des défauts instantanés se produisent lorsqu'un excès de matériau s'échappe en raison d'une mauvaise fermeture du moule.
Tous les matériaux ont les mêmes exigences en matière de surface de joint.FAUX
Différents matériaux, notamment les transparents, nécessitent des considérations spécifiques pour éviter les défauts.
Quelles sont les considérations relatives au traitement et à l'assemblage des surfaces de joint ?
Vous êtes-vous déjà demandé pourquoi les surfaces de joint dans la conception de moules sont si importantes ?
Choisissez soigneusement les surfaces de joint pour optimiser le traitement des moules, faciliter l'assemblage et maintenir la qualité du produit, en tenant compte de la forme, de l'esthétique, de la simplicité du traitement et des besoins de ventilation.
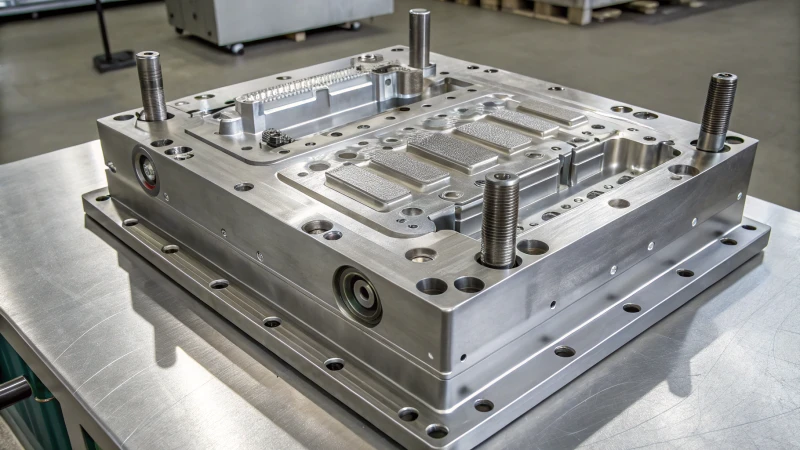
Considérations sur la forme du produit
Je me souviens de mon premier projet impliquant un simple produit cylindrique. L’alignement de la surface de joint avec le contour maximum 4 a changé la donne. Cela a non seulement simplifié la conception du moule, mais a également facilité le traitement. Pour les formes plus complexes, comme celles avec des contre-dépouilles, j'ai appris à mes dépens qu'une surface de joint étagée pouvait faire des merveilles, permettant à différentes caractéristiques de se mouler à différentes profondeurs.
Exigences d'apparence
Il fut un temps où je travaillais sur une pièce intérieure automobile de haute qualité. Le placement de la surface de joint était essentiel pour éviter les marques de soudure ou les bavures disgracieuses, qui pourraient gâcher l'apparence du produit. J'ai découvert que pour les articles transparents, le positionnement soigneux des portes latentes 5 peut améliorer considérablement la transparence en stabilisant l'écoulement de la matière fondue.
Facilité de traitement et d’assemblage
J'ai toujours cherché à obtenir des surfaces de joint planes autant que possible, car elles simplifient le traitement avec les techniques de fraisage conventionnelles. Cependant, lorsque le travail nécessitait des surfaces courbes, je devais recourir à des équipements spécialisés comme l'électroérosion. L'assemblage est devenu beaucoup plus facile lorsqu'il s'agissait de localiser les broches, garantissant que tout était parfaitement aligné.
Processus de moulage par injection
L'écoulement du plastique fondu dans une cavité de moule 6 m'a toujours fasciné. Une fois, j'ai eu du mal avec des plans courts jusqu'à ce que je réalise l'importance du positionnement stratégique de la porte pour guider la matière fondue uniformément à travers la cavité. Une ventilation adéquate est également cruciale : un projet m'a appris que des canaux de ventilation bien conçus peuvent empêcher les défauts dus à l'air emprisonné, en particulier dans le moulage par injection à grande vitesse.
Aspect | Considération |
---|---|
Forme | Simple ou complexe |
Apparence | Haute qualité ou transparent |
Traitement | Surfaces planes ou courbes |
Assemblée | Alignement et facilité d'ouverture |
Moulage par injection | Exigences en matière de débit et de ventilation |
Ces informations ont été inestimables pour affiner mon approche de la conception de moules, garantissant que la fonctionnalité et l'esthétique répondent aux normes de l'industrie, en particulier dans des domaines exigeants comme l'électronique grand public et la fabrication automobile.
Les formes simples nécessitent des surfaces de séparation complexes.FAUX
Les formes simples comme les cylindres s'alignent avec un contour maximal, simplifiant ainsi le moule.
Les surfaces de joint affectent le flux de moulage par injection.Vrai
La conception a un impact sur l'écoulement du plastique fondu, évitant ainsi les tirs courts ou les zones stagnantes.
Comment le processus de moulage par injection affecte-t-il la conception des surfaces de joint ?
Vous êtes-vous déjà demandé comment quelque chose d'aussi simple qu'une surface de joint peut avoir un impact sur l'ensemble du processus de moulage par injection ?
Le moulage par injection affecte la conception des surfaces de joint en influençant le démoulage, l'écoulement du plastique et l'apparence. Le placement correct de la ligne de joint améliore les performances du moule et la qualité du produit.
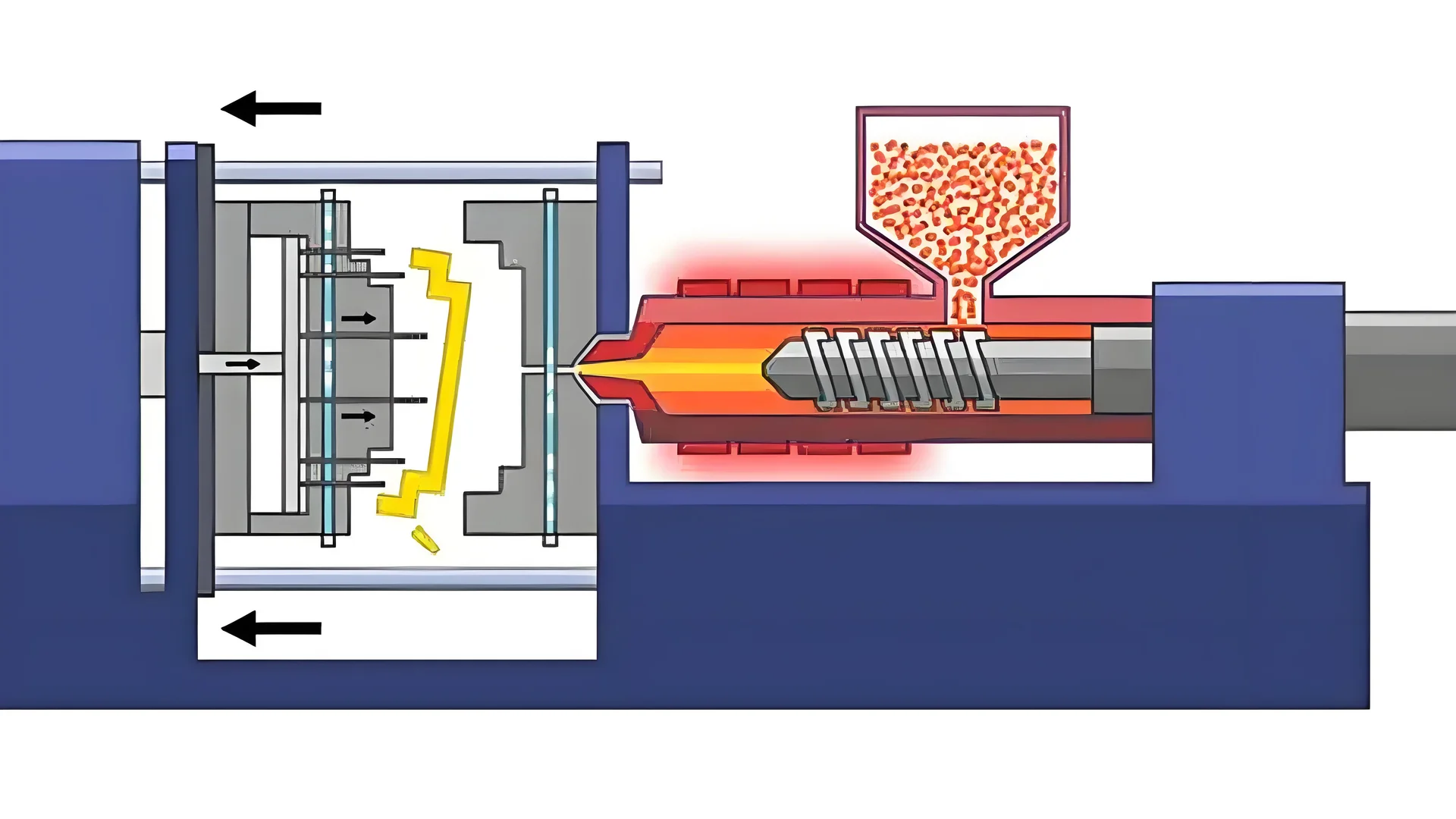
Lorsque je me suis lancé dans la conception de moules, je n'aurais jamais imaginé à quel point le processus serait complexe, en particulier la conception de la surface de joint. Cela semblait simple au début, mais en approfondissant, j'ai réalisé que c'était une forme d'art qui exigeait une attention aux détails et une bonne compréhension des exigences du produit.
Considérations clés dans la conception des surfaces de joint
La conception d'une surface de joint nécessite d'équilibrer plusieurs facteurs pour garantir un fonctionnement efficace du moule et des produits de haute qualité. Explorons quelques considérations essentielles :
1. Forme et complexité du produit
La forme du produit en plastique influence fortement la conception de la surface de joint. Pour les produits aux formes simples 7 comme une coupelle cylindrique, le positionnement du plan de joint au contour maximum simplifie énormément la vie. C'est comme trouver la couture parfaite sur un morceau de tissu : tout se met en place.
Mais il y a aussi des formes complexes, pleines de contre-dépouilles et de caractéristiques qui me rappellent la résolution d’un puzzle en 3D. Ceux-ci nécessitent des mécanismes spéciaux, comme le tirage latéral du noyau, pour garantir que tout se démoule en douceur. Si cela est réalisable, le démoulage forcé peut être une option, à condition que l'élasticité du matériau le supporte.
2. Exigences d'apparence
Les exigences esthétiques ont un impact significatif sur les décisions concernant les surfaces de joint, en particulier pour les produits à haute visibilité tels que les intérieurs automobiles ou les boîtiers électroniques. La pression était forte pour masquer les lignes de séparation afin d'éviter que les bavures et les marques de soudure ne gâchent cet aspect impeccable.
Pour les produits transparents, chaque petit défaut est amplifié, presque comme une empreinte digitale sur du verre. L’utilisation de portes latentes devient cruciale pour stabiliser l’écoulement et garder ces lignes de séparation invisibles.
3. Traitement et assemblage
La facilité de traitement et d’assemblage est un autre aspect critique. Lors du traitement de pièces à surfaces planes, un simple fraisage ou meulage suffit.
À l'inverse, lorsque vous travaillez avec des courbes, c'est comme entrer dans un tout nouveau monde où les machines EDM et CNC deviennent vos meilleures amies. Lors de l'assemblage, l'alignement du tout avec des broches de positionnement garantit que toutes les pièces du puzzle s'adaptent parfaitement sans interférence.
4. Dynamique du moulage par injection
La dynamique de l'écoulement du plastique lors du moulage par injection est essentielle dans la conception des surfaces de joint. Une surface bien planifiée doit favoriser un remplissage uniforme des cavités pour éviter les tirs courts ou les zones stagnantes.
Il s'agit de guider efficacement le flux de plastique à travers la cavité avec des positions de porte bien planifiées par rapport à la ligne de joint.
Considérations sur la ventilation
Une ventilation efficace pendant le moulage par injection est essentielle pour éviter les défauts causés par l'air emprisonné ou la décomposition des gaz. Une surface de séparation bien conçue sert également de canal de ventilation ; par conséquent, la conception de rainures d'aération ou l'exploitation des espaces naturels entre les surfaces peuvent améliorer les performances du moule.
Grâce à ces connaissances, la conception d’une surface de joint devient plus qu’une simple tâche technique ; il s'agit de créer une œuvre d'art qui répond à la fois à des objectifs de fabrication et à des objectifs esthétiques. Si vous souhaitez en savoir plus sur ces considérations, consultez des ressources supplémentaires 8 .
La conception des surfaces de joint affecte la complexité du moule.Vrai
Une surface de joint bien conçue simplifie la structure du moule, réduisant ainsi la complexité.
Les surfaces de joint courbes sont plus faciles à traiter que les surfaces planes.FAUX
Les surfaces courbes nécessitent des processus spécialisés comme l'EDM, contrairement aux surfaces planaires.
Quels sont les défis et solutions courants dans la conception des surfaces de joint ?
En naviguant dans le monde complexe de la conception de moules, j'ai fait face à de nombreux défis, notamment lorsqu'il s'agit de créer la surface de joint parfaite.
Les défis de conception des surfaces de joint incluent des formes complexes et des normes strictes. Les solutions impliquent une sélection stratégique des surfaces, l’optimisation des portes et des techniques de ventilation efficaces pour garantir une production de moules de qualité.

Comprendre la forme des produits en plastique
Au cours de mon voyage à travers le labyrinthe des surfaces de joint des moules à injection 9 , j'ai rapidement appris que la forme d'un produit en plastique dicte une grande partie de la stratégie de conception.
-
Formes simples : Pour les formes régulières comme les cuboïdes ou les cylindres, placer la surface de joint au contour maximum rend la vie beaucoup plus facile. Il simplifie la structure du moule et réduit les problèmes de traitement.
-
Formes complexes : les défis incluent des contre-dépouilles qui nécessitent des mécanismes latéraux. Je me souviens avoir abordé un jour un projet où un démoulage forcé était nécessaire. C'était angoissant de s'assurer que le matériau ne se fissurerait pas sous la pression, mais avec une planification minutieuse, tout s'est bien passé.
Exigences d'apparence
N'oublions pas la pression de répondre à des normes esthétiques élevées, notamment pour les intérieurs automobiles ou les boîtiers électroniques.
-
Surfaces de haute qualité : chaque détail devait être parfait, minimisant les surfaces de joint pour éviter les défauts embêtants comme les éclairs ou les marques de soudure. Optimisez les emplacements des portes pour réduire ces problèmes.
-
Produits transparents : Avec les produits transparents, c'était encore plus délicat : chaque imperfection ressortait comme un pouce endolori. Sélectionnez soigneusement les surfaces de joint car les défauts sont plus visibles. Utilisez des portes latentes pour un écoulement de fusion stable, améliorant ainsi la transparence.
Traitement et assemblage de moules
Lorsqu'il s'agit de traitement et d'assemblage, la commodité est reine.
-
Usinage : La conception de surfaces de joint planes pour le fraisage de précision m'a évité bien des maux de tête. Les surfaces courbes nécessitaient un équipement CNC plus avancé, mettant mes compétences au défi mais gratifiant en précision.
-
Assemblage : Assembler des moules, c'est comme reconstituer un puzzle complexe. La conception pour un assemblage facile avec des broches de positionnement garantit que tout s'aligne parfaitement : c'est un must absolu pour éviter les interférences, en particulier lorsqu'il s'agit de mécanismes coulissants.
Processus de moulage par injection
Une surface de joint bien pensée peut améliorer ou défaire l’efficacité des processus de moulage.
-
Performance d'écoulement : Il est crucial d'assurer un écoulement fluide du plastique ; J'ai appris cela de première main avec des produits à parois minces où des faux pas conduisaient à des tirs courts. Positionnez les surfaces de séparation pour garantir un écoulement fluide du plastique et éviter les projections courtes en tenant compte de la longueur du trajet d'écoulement.
-
Ventilation : La ventilation est un autre aspect critique ; l'utilisation de surfaces de séparation comme canaux de ventilation peut améliorer considérablement la qualité du produit en expulsant l'air et les gaz emprisonnés pendant le moulage. Implémentez des rainures d'aération pour les produits plus gros ou les processus à grande vitesse afin d'améliorer la qualité du produit.
Tableau : Défis courants et solutions
Défi | Solution |
---|---|
Formes complexes | Mécanismes à noyau latéral ou démoulage forcé |
Forte demande d’apparence | Minimisez les surfaces de séparation, optimisez le placement des portes |
Difficultés de traitement | Surfaces planes, usinage avancé pour les courbes |
Problèmes de ventilation | Canaux de ventilation des surfaces de séparation |
En abordant ces défis de front avec des solutions stratégiques, les concepteurs peuvent améliorer considérablement la qualité et l'efficacité 10 des produits moulés. Mes expériences m'ont appris qu'à chaque projet, il y a toujours quelque chose de nouveau à apprendre et à innover.
Les formes simples nécessitent des surfaces de séparation complexes.FAUX
Les formes simples bénéficient de surfaces de séparation simples, simplifiant ainsi le moule.
Les canaux de ventilation améliorent la qualité du produit lors du moulage.Vrai
Les canaux de ventilation aident à évacuer l'air et les gaz, évitant ainsi les défauts.
Conclusion
Des techniques de conception efficaces pour les surfaces de séparation des moules à injection améliorent la qualité du produit en prenant en compte la forme, l'apparence, la commodité de traitement et la dynamique du moulage par injection pour garantir un démoulage en douceur et minimiser les défauts.
-
Ce lien explique pourquoi le positionnement correct des lignes de joint est essentiel pour l'efficacité du moule et l'efficience de la production. ↩
-
Découvrez les normes de l'industrie et les meilleures pratiques qui guident la conception efficace des surfaces de joint pour divers produits. ↩
-
Découvrez l'impact du moulage par injection sur l'efficacité de la fabrication et la qualité des produits. ↩
-
Découvrez comment l'alignement avec un contour maximal simplifie la structure du moule pour une fabrication efficace. ↩
-
Découvrez comment les portes latentes améliorent la transparence en stabilisant le flux de plastique dans les processus de moulage. ↩
-
Comprenez comment le placement des portes affecte l'efficacité de l'écoulement du plastique dans les cavités des moules. ↩
-
Apprenez à manipuler des formes simples dans le moulage par injection pour faciliter le traitement et l'assemblage. ↩
-
Découvrez des stratégies de ventilation efficaces pour améliorer les performances des moules et la qualité des produits. ↩
-
Explorez les méthodes permettant de sélectionner des surfaces de joint efficaces qui simplifient la conception des moules et améliorent la qualité de la production. ↩
-
Découvrez comment les surfaces de joint optimisées contribuent à une meilleure qualité des produits et à une efficacité de fabrication accrue. ↩