- 1. I. Niveau cognitif de base: établir un cadre conceptuel
- 2. Ii Niveau d'analyse des applications: résoudre des problèmes de prise de décision des utilisateurs
- 3. Iii. Niveau de plongée profonde technique: répondre aux besoins professionnels des lecteurs
- 4. Iv. Niveau d'outils pratiques: améliorer l'opérabilité du contenu
- 5. V. Niveau d'extension: construire un réseau de connaissances
- 6. Conclusion: maîtrise le temps de refroidissement avec Zetarmold
I. Niveau cognitif de base: établir un cadre conceptuel
Avant d'optimiser, nous devons comprendre.
Définitions claires
- Temps de refroidissement du moulage par injection:
- Nom technique complet: Durée de phase de refroidissement dans le cycle de moulage par injection.
- Alias communs: temps de refroidissement 1 , temps de solidification 2 , temps de guérison (moins courant pour les thermoplastiques, plus pour les thermodosets / silicone).
- Principe central: le temps de refroidissement est la période dans le cycle de moulage par injection, commençant après que la cavité du moule est remplie et remplie de plastique fondu, au cours de laquelle le matériau plastique se solidifie à un point où il est suffisamment rigide pour être éjecté du moule sans déformation ni dommage. Cela se produit par le transfert de chaleur du plastique fondu vers le moule plus frais.
- Signification: elle constitue généralement la plus grande partie (souvent 50 à 80%) du temps global du cycle de moulage par injection.
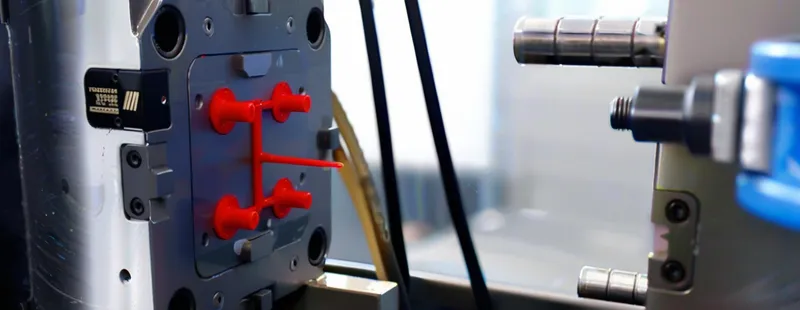
- Cycle de moulage par injection3: La séquence complète des événements pour produire une pièce (ou un ensemble de pièces), comprenant:
- Fermeture du moule
- Injection (remplissage)
- Emballage (maintien)
- Refroidissement
- Ouverture du moule
- Éjection
Classification (facteurs influençant le temps de refroidissement)
Le temps de refroidissement n'est pas une valeur fixe; Il est influencé par une confluence de facteurs qui peuvent être largement classés:
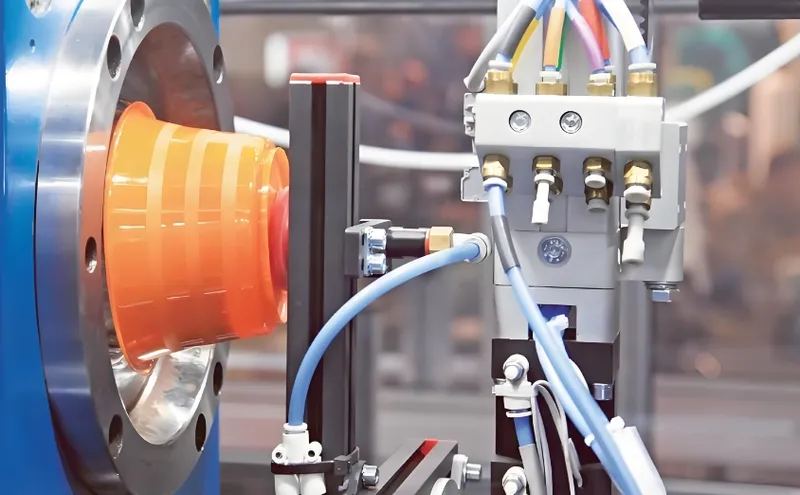
-
Centré sur le matériau:
- Type de polymère 4 : Amorphe (par exemple, PC, PS) vs semi-cristalline (par exemple, PP, PA, POM). Les matériaux semi-cristallins nécessitent souvent un contrôle de refroidissement plus précis en raison de la chaleur latente de la fusion et du rétrécissement de la cristallisation.
- Propriétés thermiques: conductivité thermique, capacité thermique spécifique, diffusivité thermique et température de transition du verre (TG) ou température de fusion (TM) du polymère.
- Température d'éjection: la température maximale à laquelle la pièce peut être éjectée sans problèmes tels que le warpage ou le collage.
-
Conception des pièces centrée sur les pièces:
- Épaisseur de paroi: le facteur le plus dominant. Le temps de refroidissement est approximativement proportionnel au carré de la section murale la plus épaisse.
- Géométrie en partie: les géométries complexes, les côtes, les boss et les épaisseurs de paroi non uniformes peuvent créer des points chauds et un refroidissement différentiel.
-
CONCEPTION DE MELLES CENTRIQUE:
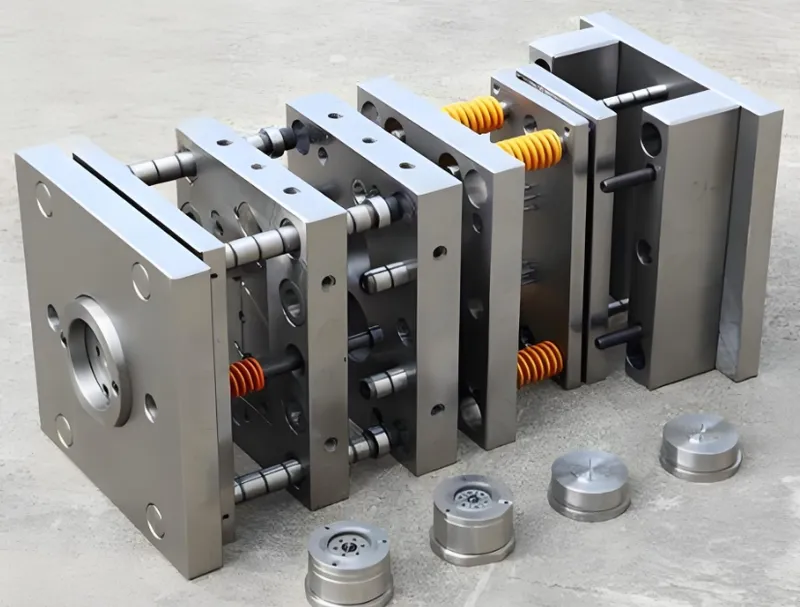
- Conception du canal de refroidissement 5 : Disposition, diamètre, proximité de la cavité et type (par exemple, lignes folles conventionnelles, canaux de refroidissement conformes).
- Matériau de moule: Matériaux de moisissure à conductivité thermique plus élevée (par exemple, inserts en cuivre de béryllium contre l'acier P20) peut réduire le temps de refroidissement.
- Ventilation: la ventilation appropriée permet à l'air piégé de s'échapper, empêchant les effets d'isolation qui peuvent prolonger le refroidissement.
- Processus centré sur le paramètre:
- Température de fusion 6 : Une température de fusion plus élevée signifie plus de chaleur à éliminer.
- Température du moule: La température de la moisissure plus basse signifie généralement un refroidissement plus rapide, mais peut affecter la finition de surface, les contraintes et la garniture.
- Température et débit du liquide de refroidissement: le liquide de refroidissement plus froid et les débits plus élevés améliorent l'efficacité d'élimination de la chaleur.
Ii Niveau d'analyse des applications: résoudre des problèmes de prise de décision des utilisateurs
Comprendre le temps de refroidissement aide à prendre des décisions éclairées pour diverses applications.
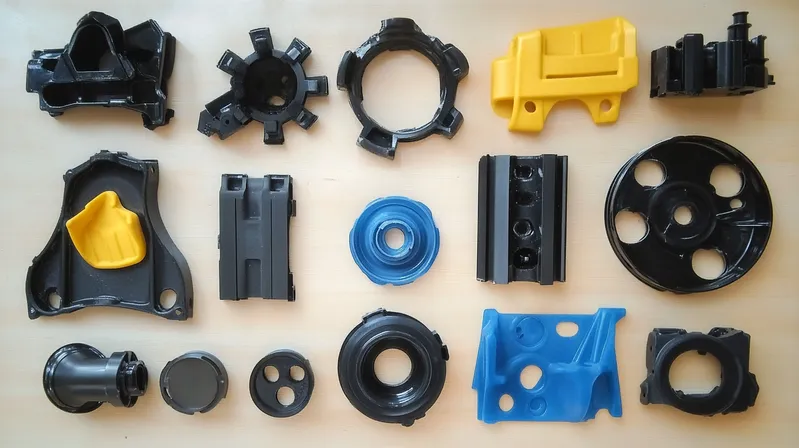
Scénarios d'application typiques
- Emballage à paroi mince à volume élevé (par exemple, contenants alimentaires, casquettes - souvent PP, PE):
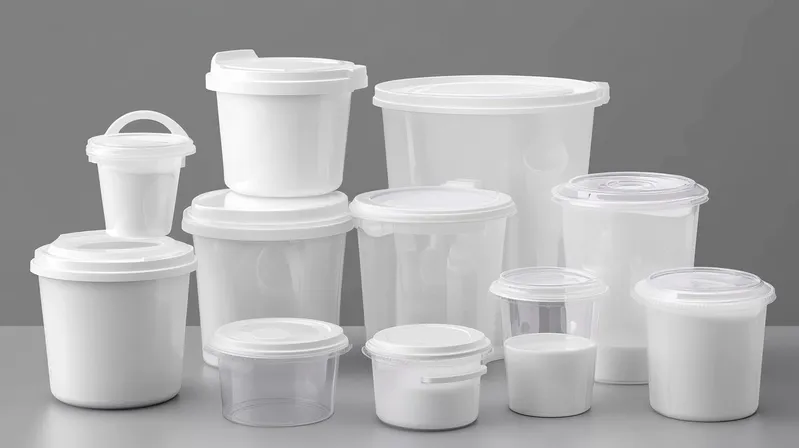
- Suggestion: le temps de refroidissement est primordial pour le temps de cycle. Optimiser le refroidissement rapide à l'aide de matériaux de moisissure hautement conductrices, une conception de canal de refroidissement efficace et des températures de moisissure potentiellement plus basses (mais contrôlées). Le choix du matériau favorise les notes de cyclisme rapide.
- Dispositifs médicaux (par exemple, seringues, composants diagnostiques - souvent PC, aperçu, CoC):
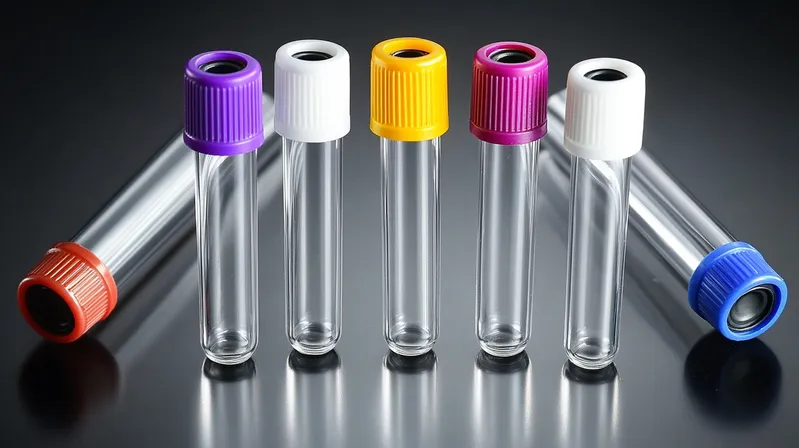
- Suggestion: la précision et l'intégrité des matériaux sont essentielles. Le refroidissement doit être uniforme pour minimiser les contraintes internes et assurer une précision dimensionnelle. Un refroidissement plus long, plus contrôlé peut être acceptable pour obtenir des tolérances critiques.
- Boîtiers électroniques grand public (par exemple, caisses de téléphone, télécommandes - souvent ABS, PC):
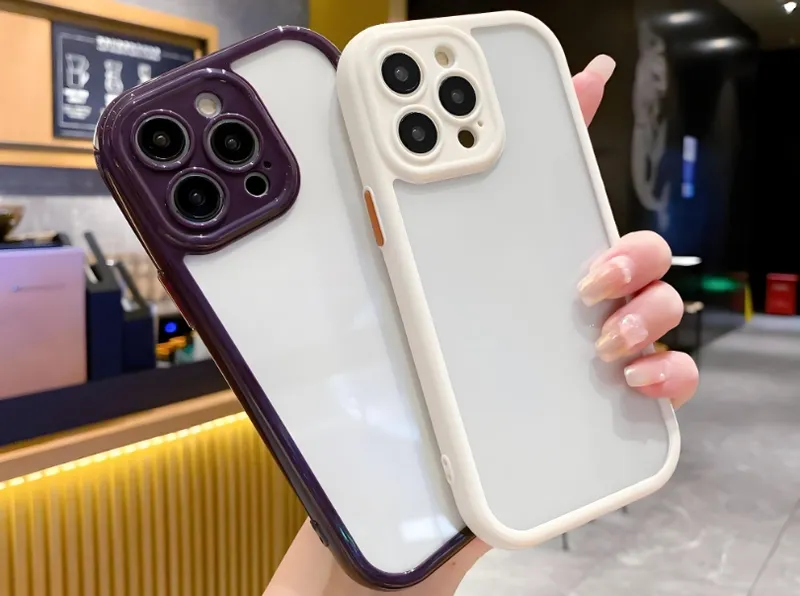
- Suggestion: l'esthétique (finition de surface) et l'intégrité structurelle sont importantes. Le refroidissement doit être géré pour éviter les marques d'évier et assurer une bonne ajustement et une bonne sensation. La conception optimisée du canal de refroidissement est cruciale.
- Produits en caoutchouc en silicone (moulage LSR):
- Suggestion: Alors que Zetarmold gère également le silicone, son "refroidissement" est en fait "durcissant" via la chaleur. Le moule est chaud et l'équivalent "refroidissement" est le temps pris pour que la réaction de réticulation soit terminée. Les principes du transfert de chaleur et de l'uniformité s'appliquent toujours, mais l'objectif est de maintenir la chaleur pour le durcissement plutôt que de le retirer pour la solidification.
Comparaison des avantages et des inconvénients (impact de la durée du temps de refroidissement)
Fonctionnalité | Temps de refroidissement plus court | Temps de refroidissement plus |
---|---|---|
Avantages | - Temps de cycle réduit | - une meilleure stabilité dimensionnelle |
- une productivité accrue | - Amélioration de la qualité des pièces (moins de marques d'évier, moins de warpage) | |
- Coût par partie inférieur | - Réduction des contraintes internes | |
Inconvénients | - Risque de défauts (warpage, marques de puits, coups courts) | - Augmentation du temps de cycle |
- Potentiel de pièces qui collaient ou se déformant sur l'éjection | - Productivité plus faible | |
- Stress internes plus élevés s'ils sont refroidis trop rapidement / de manière inégale | - Coût par partie plus élevé | |
- peut nécessiter un système d'éjection plus robuste | - Problèmes de sur-emballage possibles si la pression de maintien est maintenue trop longtemps dans le refroidissement |
Iii. Niveau de plongée profonde technique: répondre aux besoins professionnels des lecteurs
Passons dans la nity-gritty.
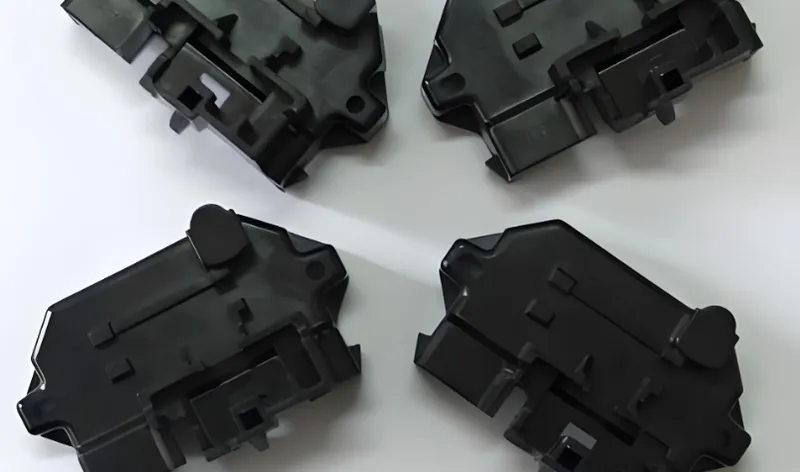
Traiter la répartition complète du flux de travail (concentrez-vous sur le refroidissement)
-
Fermeture et serrage des moisissures: les deux moitiés du moule sont solidement fermées et serrées.
-
Injection: Le plastique fondu est injecté dans la cavité du moule sous haute pression.
-
Emballage / tenue: Une fois la cavité principalement remplie, un matériau supplémentaire est emballé sous pression pour compenser le retrait alors que le matériau commence à refroidir et à se solidifier près des parois de la moisissure.
- Paramètre clé: pression d'emballage, temps d'emballage.
-
Phase de refroidissement:
- Transfert de chaleur: c'est le cœur du refroidissement. La chaleur du plastique fondu (à température de fusion) est transférée principalement par la conduction à l'acier de moule plus refroidie, puis emportée par le liquide de refroidissement (généralement l'eau) circulant à travers les canaux de refroidissement du moule.
- Front de solidification: La solidification commence aux parois des moisissures et progresse vers l'intérieur vers le centre de la pièce.
- Compensation de rétrécissement 7 : continue initialement à partir de la pression d'emballage, puis le rétrécissement volumétrique se produit à mesure que le matériau en vrac se refroidit davantage.
- Durée Déterminants: température d'éjection du matériau, propriétés thermiques, section la plus épaisse de la partie, température du moule et efficacité du système de refroidissement.
- Paramètres clés: température du moule, température du liquide de refroidissement, débit de liquide de refroidissement, température d'éjection de pièce souhaitée.
-
Ouverture du moule: Une fois que le temps de refroidissement de l'ensemble s'est écoulé et que la pièce est suffisamment rigide, la pince ouvre le moule.
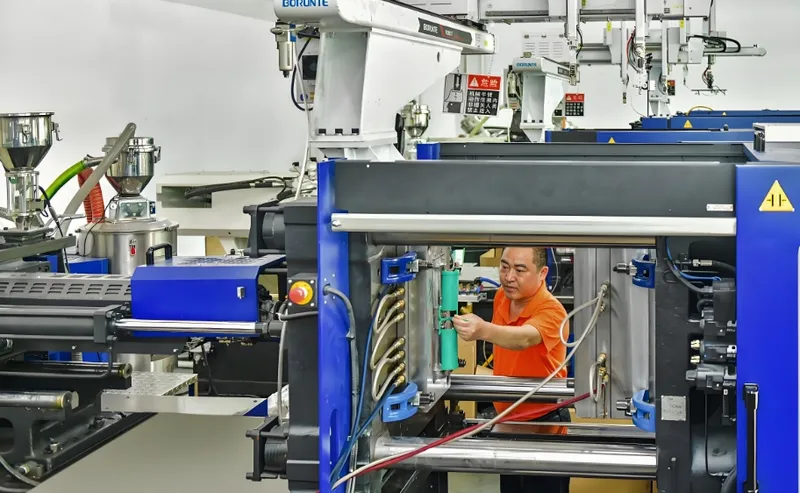
- Éjection: La partie solidifiée est poussée hors de la cavité de la moisissure par un système d'éjecteur (broches, manches, plaques).
Paramètres de refroidissement clés à surveiller et à contrôler:
-
Température de surface du moule 8 : critique pour contrôler le taux d'extraction de chaleur et d'influencer la finition de la surface et la cristallisation (pour les polymères semi-cristallins).
-
Différence de température de l'entrée / sortie du liquide de refroidissement (Delta T): indique la quantité de chaleur enlevée. Un très petit delta t pourrait suggérer un débit insuffisant ou un mauvais contact thermique.
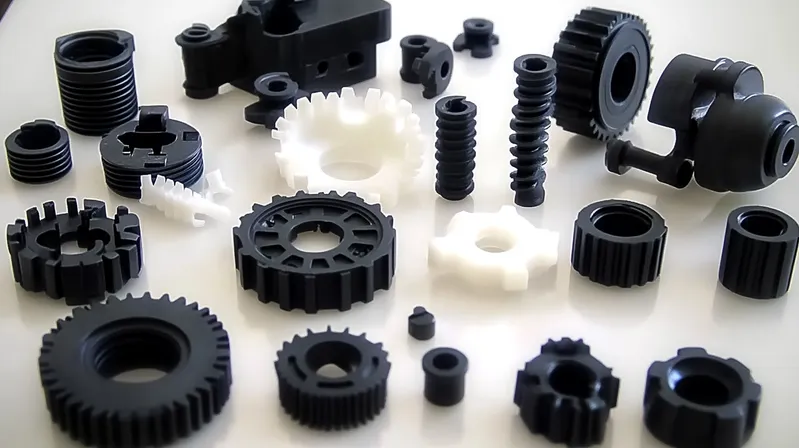
-
Débit de liquide de refroidissement 9 : L'écoulement turbulent est généralement préféré pour un transfert de chaleur efficace.
-
Température de fusion: Définit la charge de chaleur initiale.
Explication de compatibilité des matériaux
Les propriétés thermiques du matériau plastique sont fondamentales pour son comportement de refroidissement:
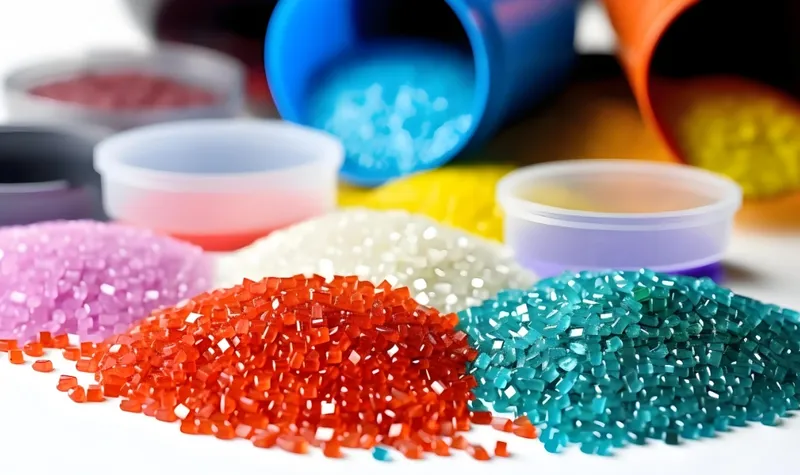
-
Polymères amorphes (par exemple, polystyrène (PS), polycarbonate (PC), ABS):
- Pas de point de fusion pointu; Ils adoucissent sur une plage de température.
- Généralement un retrait plus faible que semi-cristallin.
- Le refroidissement consiste à apporter le matériau en dessous de sa température de transition vitreuse (TG) pour atteindre la rigidité.
- Peut être plus sujet aux contraintes internes si elle est refroidie trop rapidement.
-
Polymères semi-cristallins (par exemple, polypropylène (PP), polyéthylène (PE), nylon (PA), PET, PBT):
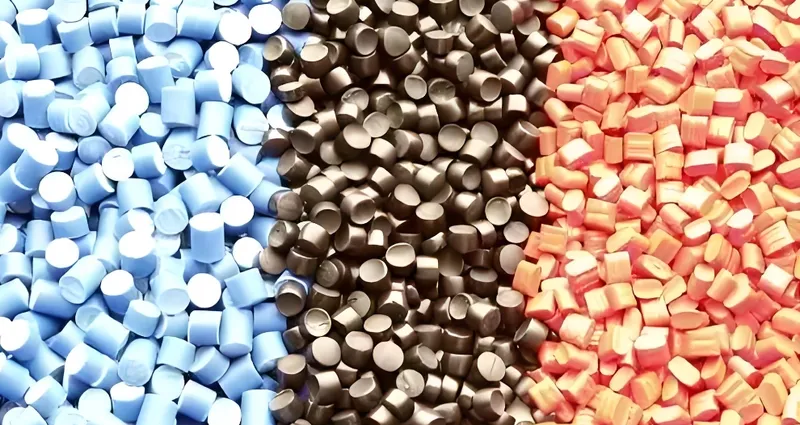
- Point de fusion tranchant (TM).
- Rétrécissement plus élevé en raison de la formation de structures cristallines ordonnées; Ce processus libère également la chaleur de fusion latente, qui doit être supprimée.
- Le taux de refroidissement peut affecter le degré de cristallinité, influençant les propriétés mécaniques. Le refroidissement rapide peut entraîner des sphérulites plus petites et parfois une ténacité améliorée mais potentiellement plus de warpage.
- Nécessitent un contrôle de refroidissement soigneux pour gérer le warpage et la stabilité dimensionnelle.
- Caoutchouc de silicone liquide (LSR - à titre de comparaison):
- Matériau thermodurcisse. Le moule est chauffé (généralement 170-210 ° C).
- Le "temps de refroidissement" est en fait "Temps de durcissement" où le matériau se réticule. La pièce est éjectée chaude. Le transfert de chaleur est toujours essentiel, mais pour maintenir uniformément la température de durcissement.
Iv. Niveau d'outils pratiques: améliorer l'opérabilité du contenu
Informations exploitables pour vos projets.
Liste de contrôle de conception (rappels des limitations du processus pour le refroidissement)
Lorsque vous concevez des pièces pour le moulage par injection, considérez-les pour optimiser le refroidissement:
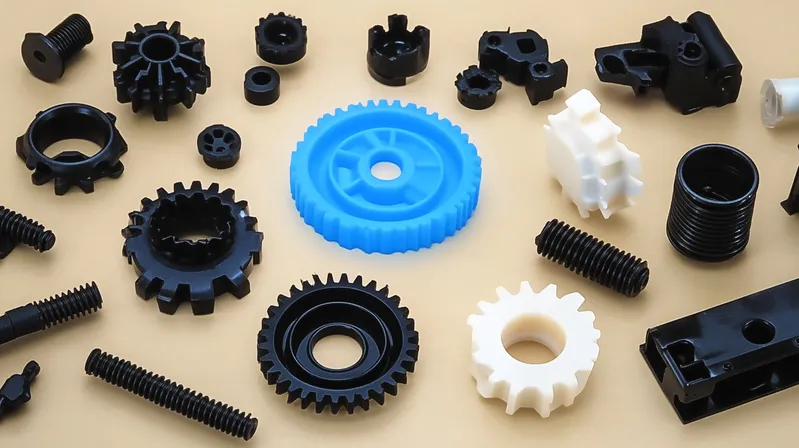
-
Épaisseur de paroi uniforme: visez une épaisseur de paroi constante dans toute la pièce. Il s'agit de la règle n ° 1 pour le refroidissement gérable.
-
Évitez les sections épaisses: si inévitable, noyez-les ou utilisez des fonctionnalités comme l'assistance au gaz.
-
Rayons généreux: utilisez des rayons dans les coins intérieurs et extérieurs au lieu de bords tranchants pour prévenir les concentrations de contraintes et améliorer l'écoulement / refroidissement.
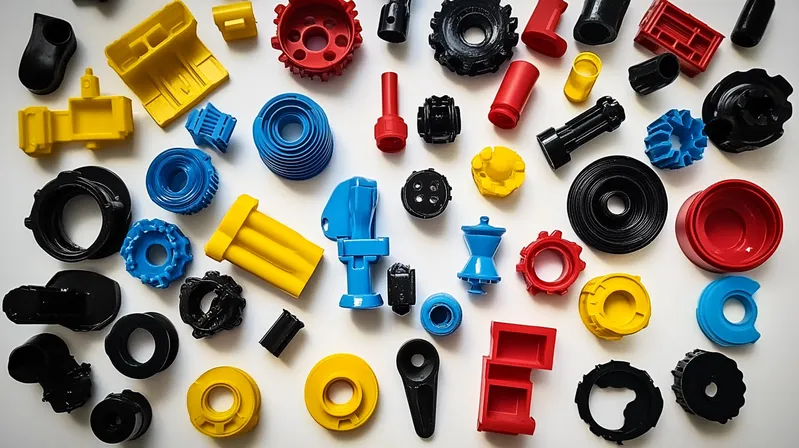
-
Transitions progressives: Si des changements d'épaisseur sont nécessaires, faites-les progressives.
-
Conception des côtes / boss: L'épaisseur des côtes doit être d'environ 50 à 70% de la paroi nominale pour empêcher les marques d'évier. Les boss doivent être dûs.
-
Sélection des matériaux: considérer les matériaux avec une meilleure conductivité thermique ou des températures de traitement plus basses si le temps de cycle est critique.
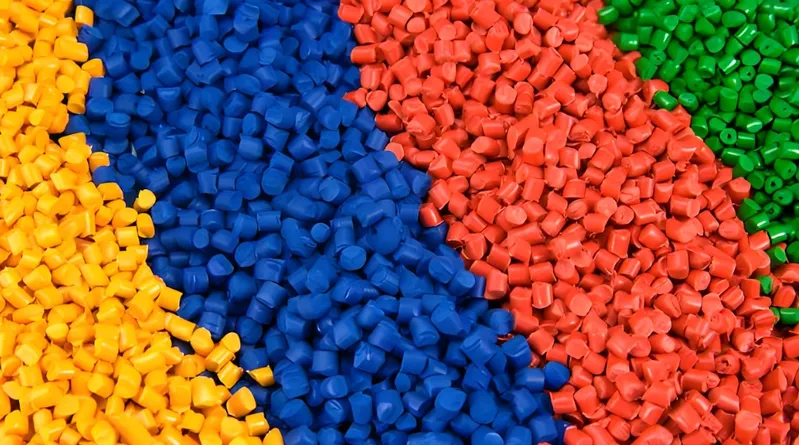
-
Emplacement de la porte: Placer les portes pour remplir d'abord des sections épaisses ou pour minimiser les variations de température.
-
Considérez la faisabilité de refroidissement des moisissures: la conception des pièces est-elle si complexe que les canaux de refroidissement efficaces sont-ils impossibles à mettre en œuvre conventionnellement? (Cela pourrait pousser vers le refroidissement conforme).
Prise de décision de sélection de processus (optimisation du temps de refroidissement)
Voici un processus de réflexion de base pour optimiser le temps de refroidissement:
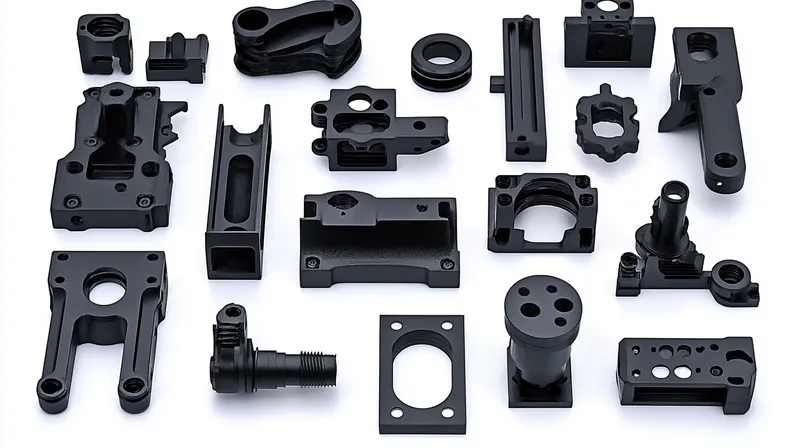
-
Le temps de refroidissement actuel est-il excessif, entraînant des coûts élevés ou une faible production?
- Oui: procédez à analyser.
- NON: La qualité des parties (Warpage, puits, dimensions) est-elle un problème?
- Oui: le refroidissement peut être trop court ou inégal. Procéder à l'analyse.
- Non: Le refroidissement actuel est probablement adéquat. Surveiller périodiquement.
-
Analyser la conception des pièces:
- L'épaisseur de paroi n'est-elle pas uniforme? Action: conseiller le client sur DFM pour les murs uniformes.
- Y a-t-il des sections épaisses évitables? Action: Conseiller le carotage.
-
Analyser le matériel:
- Le matériel est-il approprié pour l'objectif de temps de cycle? Action: Explorez des notes ou des matériaux alternatifs s'ils sont possibles.
- Notez la température d'éjection recommandée du matériau et les propriétés thermiques.
-
Analyser la conception et l'état des moisissures:
- Les canaux de refroidissement sont-ils adéquats (taille, nombre, placement)? Action: Utilisez la simulation de flux de moisissure. Considérez le refroidissement conforme pour les pièces complexes ou les applications critiques.
- Les canaux sont-ils clairs et exempts d'échelle? Action: Mettez en œuvre une maintenance régulière des moisissures.
- Le matériau du moule est-il adapté aux besoins de transfert de chaleur? Action: Considérons les inserts de matériaux de conductivité plus élevés dans les zones à chaud.
-
Analyser les paramètres du processus:
- La température de fusion est-elle plus élevée que nécessaire? Action: Réduisez progressivement, surveillant le remplissage.
- La température du moule est-elle définie de manière optimale? (Trop faible peut causer d'autres problèmes). Action: Expérimentez dans la gamme recommandée par le fournisseur de matériaux.
- Le débit et la température du liquide de refroidissement sont-ils optimisés? Action: assurer un flux turbulent; Utilisez de l'eau réfrigérée si appropriée et rentable.
Snippet d'arbre de décision:
-
Si la partie a des sections épaisses et que le refroidissement est long, envisagez de régler ou d'utiliser un assisté de gaz.
-
Si la partie montre le warpage et le refroidissement est court, augmentez le temps de refroidissement ou améliorez l'uniformité de refroidissement (par exemple, refroidissement conforme).
-
Si le temps de cycle est critique et que la qualité des pièces permet, explorez avec prudence les options pour réduire le refroidissement (moisissure optimisée, paramètres).
V. Niveau d'extension: construire un réseau de connaissances
Le temps de refroidissement n'existe pas dans le vide.
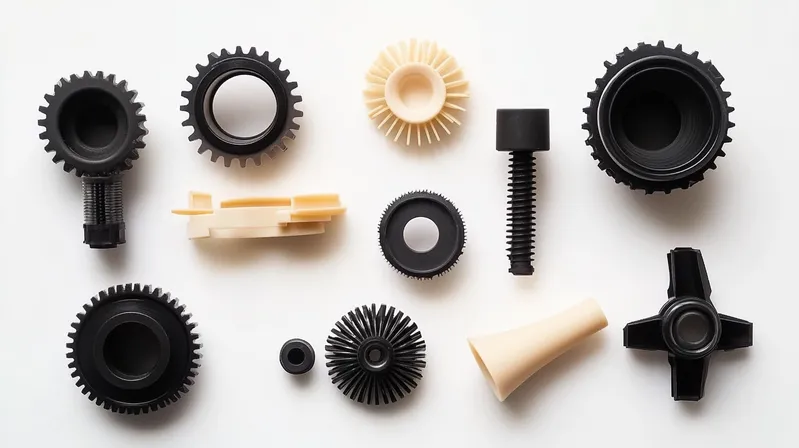
Navigation technologique associée
- Technologies en amont:
- Conception de pièces (DFM - Conception pour la fabrication): les décisions prises ici influencent fortement le refroidissement.
- Sélection du matériau: les propriétés thermiques sont intrinsèques aux calculs de refroidissement.
- Analyse du flux de moisissure (simulation): des logiciels comme Moldflow, SolidWorks Plastics, etc., peuvent prédire le temps de refroidissement, identifier les points chauds et aider à optimiser la conception du canal de refroidissement avant que l'acier ne soit coupé. C'est inestimable.
- Conception de moisissure: incorporer des dispositions de canaux de refroidissement efficaces, en utilisant des matériaux de moule appropriés.
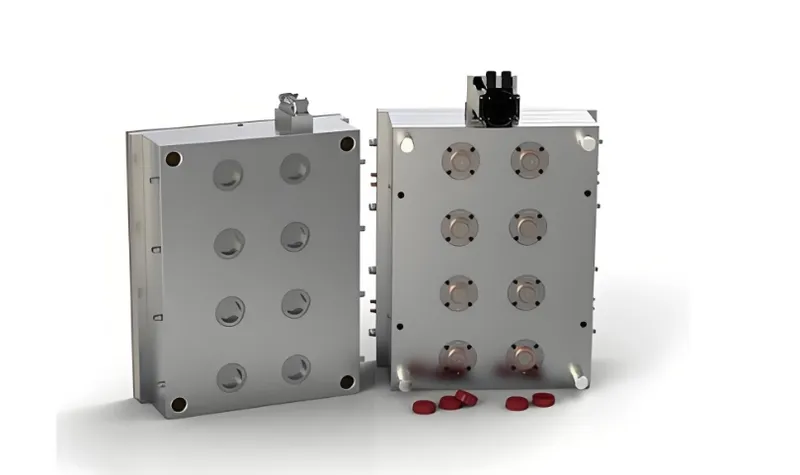
-
Technologies / considérations en aval:
- Opérations post-moulage: un recuit peut être nécessaire pour des pièces à stress interne élevé, parfois exacerbée par un refroidissement rapide ou inégal.
- Contrôle de la qualité (QC): les contrôles dimensionnels, l'analyse de la warpage et les tests de contrainte sont influencés par le processus de refroidissement.
-
Technologies parallèles / d'amélioration:
- Coldage conforme: canaux de refroidissement qui suivent le contour de la cavité du moule, offrant un refroidissement beaucoup plus uniforme et efficace. Souvent construit à l'aide de la fabrication additive (impression 3D du métal).
- Refroidissement / variotherm pulsé (moulure chauffante et refroidie): chauffer rapidement la surface du moule pendant l'injection pour une meilleure finition et coulé de surface, puis le refroidir rapidement. Complexe mais peut résoudre des problèmes spécifiques.
- Systèmes de coureurs chauds: Bien que ne pas refroidir directement, ils gardent le coureur fondu, éliminant le temps de refroidissement du coureur et les déchets de matériaux, ce qui a un impact sur l'efficacité globale.
- Contrôleurs de température de moisissure (TCUS): essentiel pour maintenir une température et un débit précis.
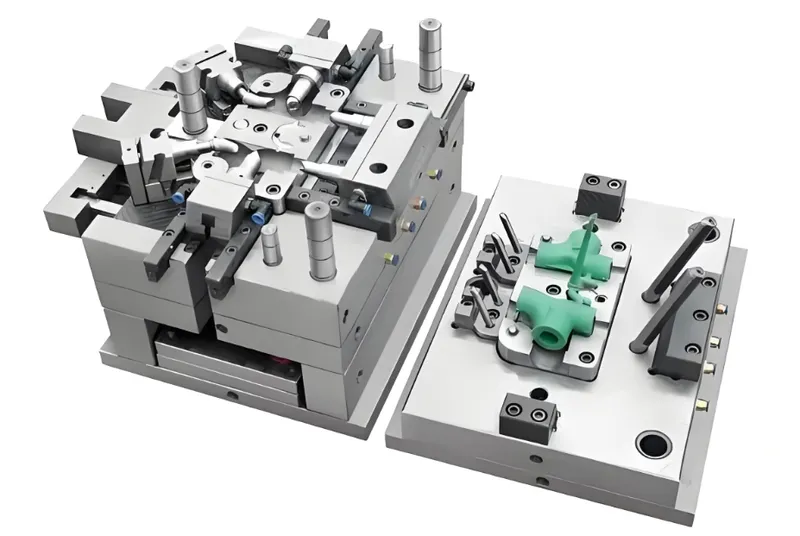
Conclusion: maîtrise le temps de refroidissement avec Zetarmold
Chez Zetarmold, nous reconnaissons que la maîtrise du temps de refroidissement du moulage par injection est un mélange de science, d'expérience et de technologie de pointe. C'est un facteur critique que nous parvenons méticuleusement à fournir des produits en caoutchouc moulés et en silicone à injection de haute qualité à nos clients internationaux.
En comprenant les fondamentaux, en analysant les applications, en plongeant dans les détails techniques et en utilisant des outils pratiques, nous pouvons collectivement optimiser les processus de refroidissement pour des résultats supérieurs.
-
Comprendre le temps de refroidissement est crucial pour optimiser le processus de moulage par injection et améliorer la qualité des produits. ↩
-
Apprendre le temps de solidification peut conduire à un meilleur contrôle sur le processus de moulage, en garantissant des produits de haute qualité. ↩
-
L'exploration du cycle de moulage par injection aide à saisir l'ensemble du processus de fabrication, à améliorer l'efficacité et la production. ↩
-
Comprendre les types de polymères est crucial pour optimiser les temps de refroidissement dans les processus de fabrication. Explorez ce lien pour des informations détaillées. ↩
-
La conception du canal de refroidissement a un impact significatif sur l'efficacité du refroidissement. Découvrez les meilleures pratiques et innovations dans ce domaine. ↩
-
La température de fonte joue un rôle vital dans l'efficacité du refroidissement. En savoir plus sur ses effets sur les processus de production. ↩
-
Apprendre la compensation de rétrécissement est essentiel pour assurer la précision dimensionnelle et la qualité dans les pièces moulées, empêchant les défauts pendant le refroidissement. ↩
-
La compréhension de la température de surface du moule est cruciale pour optimiser l'extraction de chaleur et réaliser des finitions de surface de haute qualité dans les pièces moulées. ↩
-
L'exploration de l'impact du débit de liquide de refroidissement peut aider à améliorer l'efficacité du transfert de chaleur et la qualité globale de la production dans les processus de moulage par injection. ↩