Naviguer dans le monde du moulage multi-matériaux peut donner l’impression de s’attaquer à un puzzle complexe, chaque pièce exigeant précision et soin.
Les défis liés au moulage de composants multi-matériaux incluent la garantie de la compatibilité des matériaux, la conception de moules complexes et le maintien de processus de production efficaces, qui ont tous un impact sur la qualité et la rentabilité des produits.
En repensant à mes débuts dans la conception de moules, je me souviens très bien de l'excitation et de la frustration de mon premier projet multi-matériaux. C’était comme essayer d’assembler les pièces de différents puzzles. Pourtant, chaque défi surmonté était une leçon apprise. Dans cet article, je vais vous guider à travers ces obstacles courants et partager les stratégies que j'ai choisies en cours de route pour transformer ces obstacles en tremplins pour une conception innovante.
La compatibilité des matériaux est cruciale dans le moulage multi-matériaux.Vrai
S’assurer que les matériaux fonctionnent bien ensemble évite les défauts et garantit la qualité.
Concevoir des moules simples suffit pour des composants multi-matériaux.FAUX
Des moules complexes sont nécessaires pour s’adapter efficacement à différents matériaux.
- 1. Comment les problèmes de compatibilité des matériaux affectent-ils le moulage multi-matériaux ?
- 2. Quelles sont les considérations essentielles de conception pour les moules complexes ?
- 3. Comment optimiser l’efficacité de la production dans le moulage multi-matériaux ?
- 4. Quelles sont les dernières avancées en matière de fabrication additive pour les multi-matériaux ?
- 5. Comment puis-je améliorer le contrôle qualité dans le moulage multi-matériaux ?
- 6. Conclusion
Comment les problèmes de compatibilité des matériaux affectent-ils le moulage multi-matériaux ?
Avez-vous déjà essayé de jongler ? C'est à cela que ressemble le moulage multi-matériaux : équilibrer différents matériaux pour créer un produit homogène.
Les problèmes de compatibilité des matériaux dans le moulage multi-matériaux peuvent provoquer des défauts tels qu'un délaminage, une mauvaise adhérence et une déformation, affectant la qualité mécanique et visuelle du produit, nécessitant une sélection minutieuse des matériaux.
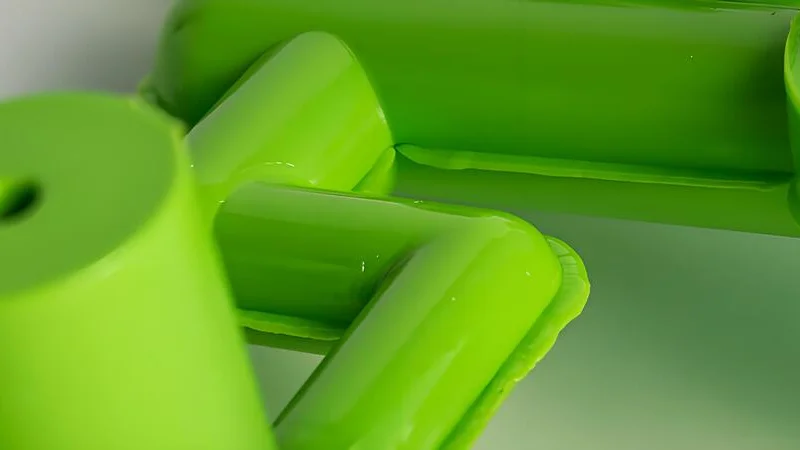
Comprendre la compatibilité des matériaux
Imaginez que vous essayiez de préparer un smoothie parfait avec des ingrédients qui ne se mélangent pas bien : certains pourraient s'agglutiner, d'autres pourraient se séparer. C'est un peu ce qui se passe dans le moulage multi-matériaux 1 , où différents polymères ou matériaux sont moulés ensemble. Le défi ? Assurez-vous que ces matériaux se mélangent le plus harmonieusement possible.
Facteurs clés influençant la compatibilité
Les angles de tirage standard sont de 1 à 2 degrés, variant avec la complexité.
Matériau A | Matériau B | Taux d'expansion |
---|---|---|
Polymère X | Polymère Y | Faible |
Polymère X | Polymère Z | Haut |
Un autre facteur est l'adhésion. Si les matériaux ne collent pas correctement entre eux, un délaminage peut se produire, ce qui compromet l'ensemble de la structure. Et ne me lancez même pas sur la réactivité chimique. Certains matériaux ne s'entendent tout simplement pas chimiquement, ce qui affecte la durabilité de la liaison.
Défauts courants dus à l'incompatibilité
- Délaminage : Comme la peinture qui s'écaille sur un mur, les couches se séparent, entraînant des défauts visibles.
- Déformation : Une dilatation thermique inégale peut provoquer la torsion ou la courbure des pièces. Imaginez un disque déformé qui ne fonctionnera pas.
- Imperfections de surface : Mauvaises finitions de surface qui affectent l'esthétique.
Pour éviter ces catastrophes, j'ai appris que les concepteurs doivent évaluer minutieusement les propriétés des matériaux et recourir à des tests de compatibilité 2 .
Stratégies pour une sélection efficace des matériaux
Voici ce qui fonctionne :
- Utilisation d'agents de couplage : Ceux-ci améliorent la liaison entre des matériaux différents.
- Outils de simulation : considérez-les comme une boule de cristal prédisant les problèmes potentiels avant qu'ils ne surviennent.
- Prototypage : testez la compatibilité dans des conditions réelles. Pensez-y comme à une répétition générale avant le grand spectacle.
Ces stratégies contribuent non seulement à réduire les défauts, mais améliorent également l’efficacité et la rentabilité de la production.
Explorer plus loin
Pour quiconque comme moi qui s'intéresse vraiment à ce genre de choses, l'exploration des techniques de moulage par injection multi-matériaux 3 peut fournir des informations plus approfondies sur la manière de surmonter les défis de compatibilité dans la fabrication.
Application dans l'industrie
Dans des secteurs comme l'automobile et l'électronique grand public, c'est comme marcher sur une corde raide : les composants multi-matériaux doivent répondre à des normes rigoureuses. Comprendre la compatibilité est essentiel pour garantir que les produits fonctionnent non seulement bien, mais aussi qu'ils soient beaux.
En résumé, gérer la compatibilité des matériaux dans le moulage multi-matériaux consiste à combiner le savoir-faire scientifique avec des tests pratiques. L’adoption d’outils et de stratégies avancés peut considérablement atténuer ces défis.
La dilatation thermique affecte les résultats du moulage multi-matériaux.Vrai
Différents matériaux se dilatent à des rythmes variables, provoquant des contraintes et des déformations.
La réactivité chimique n'a pas d'importance dans le moulage multi-matériaux.FAUX
Les interactions chimiques peuvent affecter la durabilité des zones collées.
Quelles sont les considérations essentielles de conception pour les moules complexes ?
Vous êtes-vous déjà demandé ce qu'impliquait la conception d'un moule complexe ? Il ne s'agit pas seulement de formes et de tailles : c'est un art qui nécessite d'équilibrer créativité et praticité.
La conception de moules complexes implique des considérations clés telles que la sélection des matériaux, la complexité géométrique, l'épaisseur des parois, les angles de dépouille et les contre-dépouilles. Ces facteurs sont essentiels pour garantir l’efficacité, les performances et la durabilité du moule lors d’une production à grande échelle.
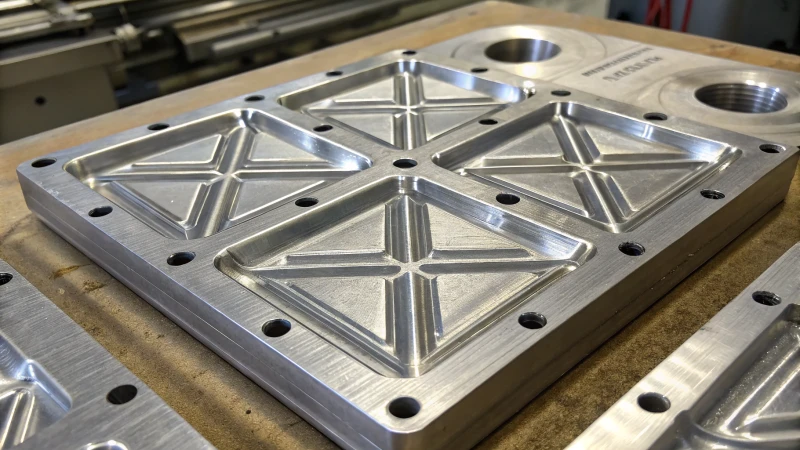
Lorsque j’ai commencé à me plonger dans le monde de la conception de moules, j’avais l’impression d’essayer de résoudre une énigme sans fin. Chaque pièce (choix des matériaux, géométrie, épaisseur) devait s'adapter parfaitement pour que tout fonctionne parfaitement. Permettez-moi de partager quelques idées de mon voyage.
Sélection des matériaux
Choisir le bon matériau, c’est comme choisir l’ingrédient parfait pour une recette. Il doit résister à des pressions et des températures élevées. J'ai découvert que les moules en aluminium 4 , les moules en acier 5 et les alliages de cuivre apportent chacun quelque chose d'unique à la table. Les moules en aluminium, par exemple, sont légers et ont une excellente conductivité thermique, ce qui peut réduire considérablement les temps de cycle, ce que je garde toujours à l'esprit lorsque les délais approchent. D’un autre côté, les moules en acier sont mon choix pour les productions à grand volume en raison de leur durabilité.
Complexité géométrique
Naviguer dans la complexité géométrique donne souvent l’impression de marcher sur une corde raide. Lorsque vous abordez des conceptions complexes avec des nervures et des finitions détaillées, des techniques telles que le refroidissement conforme 6 peuvent vous sauver la vie. Ils aident à gérer efficacement la répartition de la chaleur, assurant un refroidissement uniforme et réduisant le risque de déformation.
Épaisseur de paroi
J'ai appris très tôt qu'il était vital de maintenir une épaisseur de paroi constante. Trop fin, vous risquez des défauts comme des traces d'évier ; trop épais et vous gaspillez du matériel et de l'argent.
Matériel | Épaisseur de paroi recommandée (mm) |
---|---|
Plastique | 1-3 |
Métal | 2-4 |
Pour les moules en plastique, coller aux murs entre 1 et 3 mm est généralement ma règle de base.
Angles de dépouille
Les angles de dépouille peuvent sembler triviaux, mais ils jouent un rôle important dans le démoulage de la pièce sans accroc. Je vise généralement un angle d'au moins 1 à 2 degrés, même si les formes complexes peuvent en exiger plus.
Contre-dépouilles
Les contre-dépouilles peuvent être délicates : elles nécessitent souvent des outils supplémentaires comme des actions latérales ou des élévateurs. Il est essentiel d'y remédier dès le début de la phase de conception afin d'éviter des retouches coûteuses. L'utilisation d'outils de CAO avancés 7 s'est avérée inestimable pour identifier et concevoir autour de ces fonctionnalités.
En intégrant ces considérations dans chaque conception, j'ai réussi à créer des moules qui non seulement répondent aux attentes esthétiques, mais qui fonctionnent également efficacement sous les pressions de production.
Les moules en aluminium réduisent les temps de cycle grâce à la conductivité thermique.Vrai
L'excellente conductivité thermique de l'aluminium contribue à une dissipation thermique plus rapide.
Les angles de dépouille supérieurs à 5 degrés sont standard pour toutes les conceptions de moules.FAUX
Les angles de dépouille standard sont de 1 à 2 degrés, variant selon la complexité.
Comment optimiser l’efficacité de la production dans le moulage multi-matériaux ?
Avez-vous déjà eu l'impression que le moulage multi-matériaux est un puzzle avec des pièces manquantes ? Rassemblons le tout en optimisant votre efficacité de production grâce à ces stratégies éprouvées.
Optimisez l’efficacité du moulage multi-matériaux en sélectionnant les matériaux appropriés, la conception avancée des moules et l’automatisation des processus. Mettez en œuvre une surveillance en temps réel et une maintenance prédictive pour améliorer les performances tout en minimisant les temps d'arrêt.
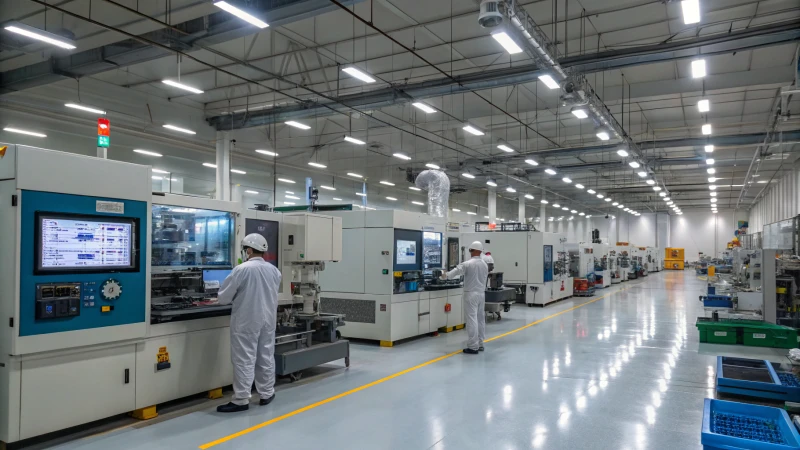
Comprendre la sélection des matériaux
Je me souviens de la première fois où j'ai dû choisir des matériaux pour un projet de moulage complexe. C'était comme essayer de trouver le mélange parfait de café – trop fort et ça accable ; trop faible, et cela ne satisfait pas. La sélection des bons matériaux dans le moulage multi-matériaux est tout aussi cruciale. Chaque matériau doit compléter l’autre, garantissant qualité et durabilité. Par exemple, j'ai combiné un polymère rigide avec un élastomère plus souple pour obtenir à la fois résistance et flexibilité.
J'ai également découvert que l'utilisation de polymères avancés présentant une stabilité thermique 8 ou une résistance aux UV améliorée peut réduire considérablement les défauts et améliorer la longévité du produit. Cette approche permet non seulement de gagner du temps, mais augmente également la satisfaction des clients.
Techniques avancées de conception de moules
Une fois, j'ai passé des heures à peaufiner la conception d'un moule, pour ensuite réaliser que la solution résidait dans l'utilisation de techniques de refroidissement conforme. Ces innovations peuvent réduire considérablement les temps de cycle et améliorer l'efficacité du refroidissement 9 . L’utilisation d’outils de CAO a été ma stratégie privilégiée pour simuler et optimiser le flux de matériaux, en garantissant que tout s’emboîte parfaitement et avec un minimum de déchets.
Un autre truc dans mon sac est la conception de moules modulaires. Ils offrent la flexibilité nécessaire pour effectuer des ajustements rapides sans provoquer de longs temps d'arrêt, ce qui change véritablement la donne lorsque les délais sont serrés.
Automatisation et intégration des processus
L’automatisation, c’était comme découvrir une arme secrète dans mon arsenal de fabrication. L'intégration de la robotique pour des tâches telles que la manutention des matériaux a minimisé les erreurs humaines et augmenté le débit. C'est comme avoir une paire de mains supplémentaire qui ne se fatigue jamais.
Investir dans un système d'exécution de fabrication (MES) 10 a également rationalisé les opérations pour moi. Avec des données en temps réel sur l’état de la production à portée de main, identifier et résoudre les goulots d’étranglement n’a jamais été aussi simple.
Surveillance en temps réel et maintenance prédictive
Imaginez ceci : des capteurs et des appareils IoT travaillant 24 heures sur 24 pour fournir des informations sur les performances des machines. Ces données m'ont permis d'effectuer une maintenance prédictive, réduisant considérablement les pannes inattendues.
Une machine bien entretenue est comme un vélo bien huilé : fluide, fiable et toujours prêt à partir. La mise en place d'un tableau de bord de surveillance aide mon équipe à détecter tout écart par rapport aux performances optimales avant qu'ils ne deviennent des problèmes coûteux.
Utiliser l'analyse des données pour une amélioration continue
L'analyse des données, c'est comme avoir une boule de cristal qui révèle les tendances et les modèles dans les processus de production. En analysant ces tendances, j'ai pu prendre des décisions éclairées qui améliorent encore l'efficacité.
La mise en place d'un cadre d' amélioration continue 11 implique d'examiner régulièrement les mesures de performance et de mettre en œuvre des changements basés sur des informations basées sur les données. Cette approche proactive garantit que ma ligne de production reste optimisée dans le temps.
Voici un aperçu rapide :
Stratégie | Avantages |
---|---|
Sélection précise des matériaux | Réduit les défauts, améliore la durabilité |
Conception avancée de moules | Améliore le débit, réduit les temps de cycle |
Automatisation des processus | Augmente le débit, réduit les erreurs |
Surveillance en temps réel | Minimise les temps d'arrêt, garantit la qualité |
Analyse des données | Permet une prise de décision éclairée |
La combinaison de polymères rigides et d'élastomères améliore la durabilité.Vrai
Les polymères rigides ajoutent de la résistance, tandis que les élastomères offrent de la flexibilité, améliorant ainsi la durabilité.
Le refroidissement conforme augmente les temps de cycle dans la conception des moules.FAUX
Le refroidissement conforme réduit les temps de cycle en améliorant l’efficacité du refroidissement dans les moules.
Quelles sont les dernières avancées en matière de fabrication additive pour les multi-matériaux ?
Plongeons dans le monde de pointe de la fabrication additive multi-matériaux, où les possibilités sont infinies et où l'innovation est le maître mot.
Les progrès récents dans la fabrication additive multi-matériaux, tels que l’impression voxel et les nouveaux mélanges de matériaux, permettent une personnalisation sans précédent, des performances améliorées et des conceptions innovantes dans tous les secteurs.
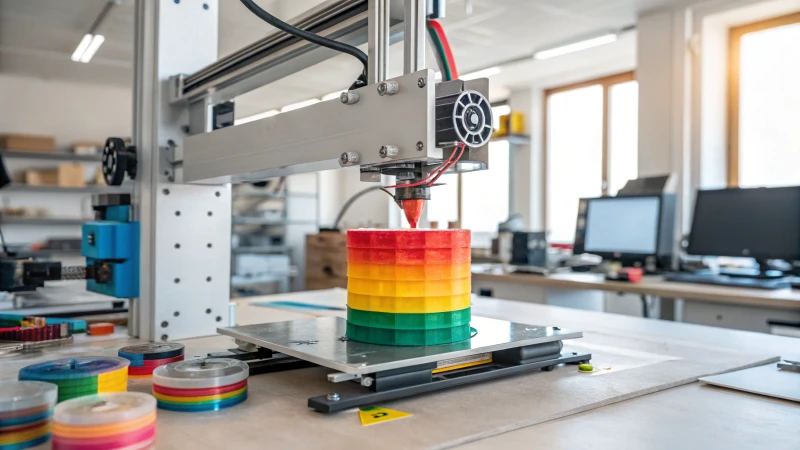
Révolutionner les combinaisons de matériaux
Imaginez pouvoir contrôler chaque petit détail des propriétés d'un matériau, comme concevoir un chef-d'œuvre Lego dans lequel chaque bloc a une fonction différente. C'est à cela que ressemble pour moi l'impression basée sur le voxel. Récemment, cette incroyable avancée dans la fabrication additive 12 a ouvert des possibilités dont je ne pouvais que rêver en tant que jeune designer. En contrôlant les matériaux à l'échelle microscopique, je suis capable d'intégrer différents matériaux aux propriétés mécaniques et thermiques variées, créant ainsi des structures qui semblaient impossibles il y a quelques années à peine.
Fonctionnalité | Avantages |
---|---|
Impression basée sur Voxel | Distribution de matériaux personnalisable, performances améliorées |
Nouveaux mélanges de matériaux | Résistance, flexibilité et polyvalence d'application améliorées |
Applications dans tous les secteurs
Je me souviens de ma première rencontre avec l’impression 3D multi-matériaux dans le secteur aérospatial. C'était comme assister à de la magie : des composants à la fois légers et suffisamment robustes pour améliorer le rendement énergétique tout en réduisant les émissions. Il ne s'agit pas seulement de l'aérospatiale; même dans le domaine médical 13 , j'ai vu comment ces technologies créent des implants personnalisés qui imitent les tissus humains plus fidèlement que jamais. Il ne s’agit pas seulement de technologie ; c'est une révolution.
Et parlons d'électronique grand public ! Chaque fois que je tiens un appareil intégrant de manière transparente des composants et des boîtiers électroniques, le tout fabriqué en une seule fois, je me souviens du chemin parcouru. Cette approche réduit les délais et les coûts de production, changeant ainsi la donne pour les designers comme moi.
Défis et orientations futures
Bien sûr, tout ne se passe pas sans heurts. Il reste encore des obstacles à surmonter, comme garantir une qualité constante entre les différents matériaux et augmenter la production pour les applications industrielles. Mais chaque défi est une nouvelle opportunité, n'est-ce pas ? Je suis avec impatience la recherche de nouveaux matériaux et de méthodes d'impression améliorées qui repoussent encore plus les limites.
L’avenir regorge de potentiels passionnants. Imaginez travailler avec des matériaux auto-réparateurs 14 ou des matériaux intelligents qui s'adaptent aux changements environnementaux : c'est comme si la science-fiction prenait vie ! Se tenir au courant de ces développements n'est pas seulement nécessaire ; c'est exaltant. Pour des professionnels comme Jacky, suivre ces progrès garantit que nous sommes prêts à relever les défis futurs et à saisir de nouvelles opportunités dans ce paysage concurrentiel.
L’impression voxel contrôle les propriétés des matériaux de manière microscopique.Vrai
L'impression basée sur Voxel permet un contrôle précis à un niveau microscopique.
Les matériaux auto-réparateurs sont actuellement utilisés dans l’impression 3D multi-matériaux.FAUX
Les matériaux auto-cicatrisants sont une innovation future, pas encore largement utilisée.
Comment puis-je améliorer le contrôle qualité dans le moulage multi-matériaux ?
Vous êtes-vous déjà retrouvé aux prises avec les complexités du moulage multi-matériaux ? Explorons quelques stratégies révolutionnaires qui garantissent un contrôle qualité de premier ordre dans ce processus complexe.
Améliorez le contrôle qualité dans le moulage multi-matériaux en mettant en œuvre une surveillance en temps réel, un contrôle précis des processus et une analyse avancée des matériaux, soutenus par une maintenance régulière des équipements et une formation approfondie du personnel pour une qualité de produit constante.
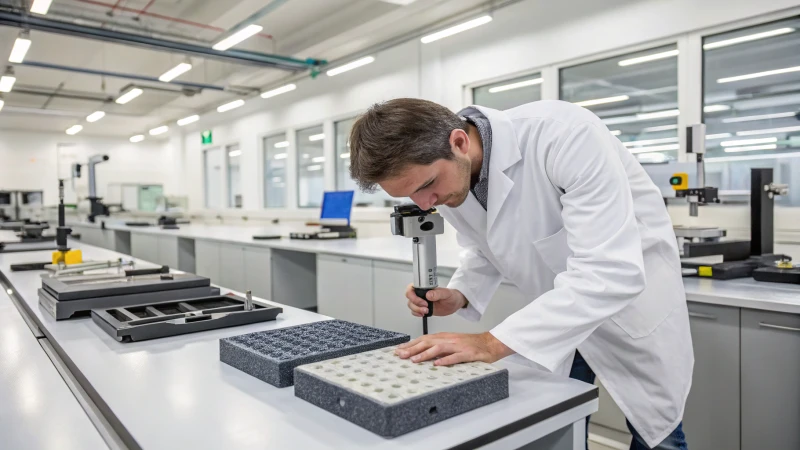
Systèmes de surveillance en temps réel
L'une des mesures les plus transformatrices que j'ai prises consiste à mettre en œuvre de surveillance en temps réel 15 . Imaginez avoir des capteurs et des logiciels qui vous alertent instantanément de tout problème de pression, de température ou de temps de remplissage. C'est comme avoir un ange gardien pour votre processus de fabrication, qui détecte les défauts avant qu'ils ne deviennent des problèmes coûteux.
- Avantages : Cette approche m'a permis de réduire considérablement les déchets et d'améliorer l'efficacité globale.
- Outils : J'ai découvert que l'intégration transparente de solutions logicielles avec des configurations existantes peut changer la donne.
Précision dans le contrôle des processus
La précision n'est pas qu'un mot à la mode ; c'est la pierre angulaire de la qualité. Des techniques telles que l'usinage de précision 16 et la CAO ont joué un rôle déterminant dans mon parcours pour obtenir des résultats impeccables.
Aspect | Importance |
---|---|
Précision dimensionnelle | Haut |
Temps de cycle | Modéré |
Cohérence des matériaux | Très élevé |
Analyse avancée des matériaux
Avant de me lancer dans la production, j’insiste toujours sur l’importance d’analyser la compatibilité et les performances des matériaux. L'utilisation de l'analyse spectroscopique 17 garantit que j'évite les réactions inattendues lors du moulage, ce qui m'aide à sélectionner les meilleurs matériaux, qu'il s'agisse de thermoplastiques ou d'élastomères, pour minimiser les défauts.
- Matériaux : Thermoplastiques, élastomères.
- Avantages : Une meilleure sélection des matériaux réduit les défauts.
Entretien et étalonnage des équipements
Je ne saurais trop insister sur l’importance cruciale de la maintenance et de l’étalonnage réguliers. Sauter ces étapes entraînait autrefois des variations imprévues dans la qualité des produits, une leçon que j'ai apprise à mes dépens. Désormais, je m'en tiens à un programme de maintenance rigoureux : mensuel pour les machines très utilisées et étalonnages trimestriels.
- Vérification de routine : mensuellement pour les équipements à forte utilisation.
- Calibrage : Trimestriel pour assurer la précision.
Programmes de formation du personnel
Enfin, la formation est essentielle. J'ai investi massivement dans des ateliers et des cours en ligne pour mon équipe, axés sur la sécurité, les nouvelles technologies et le dépannage. Investir dans la formation 18 a non seulement amélioré la qualité, mais a également stimulé le moral des employés et réduit les taux de roulement. Il s’agit de favoriser une culture d’apprentissage continu pour nous garder une longueur d’avance.
La surveillance en temps réel réduit les déchets lors du moulage.Vrai
La surveillance en temps réel détecte les défauts à un stade précoce, réduisant ainsi le gaspillage et améliorant l'efficacité.
Un étalonnage mensuel est recommandé pour tous les équipements.FAUX
L'étalonnage est recommandé tous les trimestres, et non mensuellement, pour une maintenance de précision.
Conclusion
Le moulage multi-matériaux présente des défis tels que la compatibilité des matériaux, la conception complexe des moules et l'efficacité de la production. Les stratégies comprennent une sélection minutieuse des matériaux, des techniques de conception avancées et une surveillance en temps réel pour le contrôle qualité.
-
Comprendre les bases du moulage multi-matériaux et ses applications dans diverses industries. ↩
-
Découvrez les méthodes permettant de tester la compatibilité des matériaux afin de prévenir les défauts de moulage. ↩
-
Découvrez des techniques de pointe en matière de moulage par injection multi-matériaux pour de meilleurs résultats de produits. ↩
-
Les moules en aluminium offrent une conductivité thermique supérieure, ce qui peut réduire considérablement les temps de cycle de production. ↩
-
Les moules en acier sont très durables, ce qui les rend idéaux pour les séries de production à grand volume où la longévité est cruciale. ↩
-
Le refroidissement conforme améliore la gestion de la chaleur dans les conceptions de moules complexes, conduisant à une meilleure qualité et à une réduction du gauchissement. ↩
-
Les outils de CAO avancés aident à identifier et à traiter les caractéristiques complexes telles que les contre-dépouilles dès le début du processus de conception. ↩
-
Explorez les polymères qui améliorent la stabilité thermique pour réduire les défauts et améliorer la longévité des produits. ↩
-
Découvrez comment les techniques de refroidissement conforme peuvent réduire les temps de cycle et améliorer l'efficacité du refroidissement des moules. ↩
-
Comprenez comment MES peut rationaliser les opérations en fournissant des données en temps réel sur l'état de la production. ↩
-
Découvrez des cadres d'amélioration continue qui aident à maintenir des lignes de production optimisées. ↩
-
Découvrez comment l'impression voxel permet de personnaliser les propriétés des matériaux à un niveau microscopique. ↩
-
Découvrez comment l'impression 3D multi-matériaux révolutionne les implants médicaux. ↩
-
Découvrez les matériaux auto-réparateurs innovants et leurs applications potentielles. ↩
-
Les systèmes de surveillance en temps réel fournissent un retour d'information immédiat, aidant à identifier les défauts plus tôt et à améliorer l'efficacité globale. ↩
-
L'usinage de précision garantit des moules de haute qualité, essentiels au maintien de la précision dimensionnelle et à la réduction des déchets. ↩
-
L'analyse spectroscopique permet d'identifier la compatibilité des matériaux, évitant ainsi les réactions indésirables pendant le processus de moulage. ↩
-
Investir dans la formation du personnel améliore les compétences, renforce les mesures de contrôle de la qualité et augmente la satisfaction des employés. ↩