Choisir le bon système d'éjection pour votre moule, c'est comme choisir l'outil parfait dans une boîte à outils bondée : c'est intimidant mais crucial.
Choisissez le système d'éjection adapté à votre moule en tenant compte de la complexité de la conception des pièces, du type de matériau et des méthodes d'éjection appropriées afin d'améliorer l'efficacité et de minimiser les défauts.
En réfléchissant à mon propre parcours, je me souviens de la première fois où j'ai été confronté à ce défi. J'avais pour mission de concevoir un moule pour un composant électronique particulièrement complexe. La complexité de la pièce m'a fait remettre en question chacun de mes mouvements, mais plonger profondément dans les nuances des systèmes d'éjection a été ma percée.
Comprendre ces facteurs clés dans la sélection du système d’éjection est essentiel pour une conception et une fabrication réussies des moules. Dans les sections suivantes, je partagerai des idées que j'aurais aimé connaître à l'époque, en vous fournissant un guide complet pour prendre des décisions éclairées.
Le système d'éjection affecte l'efficacité de la production du moule.Vrai
Choisir le bon système d’éjection optimise la vitesse et la qualité de la production.
Le type de matériau n'a pas d'importance pour le choix du système d'éjection.FAUX
Le type de matériau influence la méthode d'éjection appropriée pour les moules.
- 1. Quels sont les différents types de systèmes d’éjection ?
- 2. Comment la conception des pièces influence-t-elle le choix du système d’éjection ?
- 3. Pourquoi le type de matériau est-il important lors du choix d'un système d'éjection ?
- 4. Quels sont les défis courants dans la mise en œuvre du système d’éjection ?
- 5. Comment les systèmes d’éjection peuvent-ils affecter la qualité des produits ?
- 6. Quelles innovations émergent dans la technologie d’éjection de moules ?
- 7. Conclusion
Quels sont les différents types de systèmes d’éjection ?
Vous êtes-vous déjà demandé ce qui se passait réellement dans la fabrication de ce gadget en plastique parfait que nous utilisons tous les jours ? Tout dépend de la magie des systèmes d'éjection dans le moulage par injection.
Différents systèmes d'éjection dans le moulage par injection (goupille, manchon, lame et plaque de dévêtissage) améliorent chacun l'efficacité du retrait des pièces, influençant la qualité des pièces moulées et la vitesse de production.
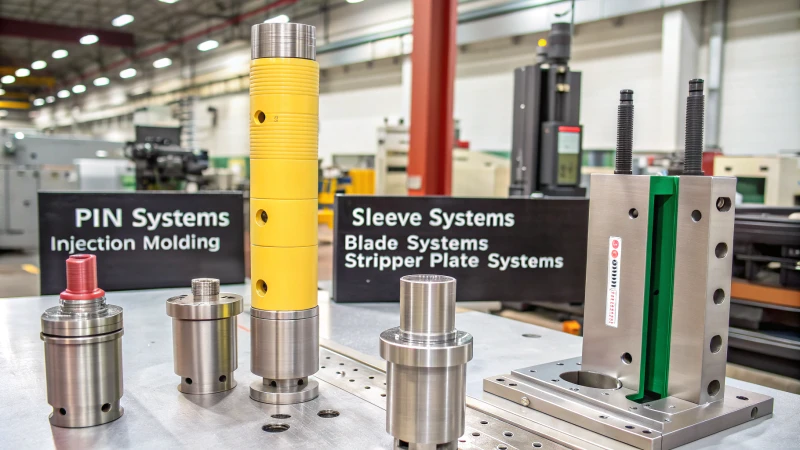
Système d'éjection de broches
Permettez-moi de partager une petite histoire. Je me souviens de la première fois que j'ai rencontré un système d'éjection de broches au cours de mes débuts sur le terrain. Imaginez ceci : de minuscules broches poussant une pièce moulée avec précision, presque comme par magie. Ce système est le cheval de bataille de l'industrie : rentable et polyvalent, même s'il laisse parfois des marques révélatrices sur vos produits. C'est comme utiliser un vieil outil fiable ; fiable mais pas toujours parfait.
Ce système 1 est économique et adapté à de nombreuses applications mais peut laisser des traces visibles sur le produit.
Système d'éjection des manchons
Imaginez que vous travaillez sur un projet dans lequel vous devez mouler quelque chose de cylindrique, comme un élégant boîtier de stylo. Le système d’éjection des manches devient ici votre meilleur ami. Il utilise des manchons cylindriques pour faire ressortir les pièces de manière uniforme, ce qui est idéal pour éviter toute marque ou déformation disgracieuse. C'est un peu plus cher que les systèmes à broches, mais lorsque vous visez la perfection, cela vaut chaque centime.
Fonctionnalité | Éjection de broche | Éjection du manchon |
---|---|---|
Coût | Faible | Moyen |
Marques sur le produit | Oui | Non |
Idéal pour les formes | Divers | Cylindrique |
Système d'éjection de lame
Ensuite, il y a ces pièces délicates, peut-être un composant électronique fin et complexe. C'est là que les systèmes d'éjection de lame brillent. Avec des lames aussi fines qu'un murmure, ils repoussent doucement les pièces sans les endommager. C'est comme enfiler une aiguille : cela nécessite de la précision mais offre de la finesse.
Les systèmes de lames 2 nécessitent un alignement précis pour éviter d'endommager le moule ou le produit.
Système de plaque de décapage
Pour les projets plus importants, comme la fabrication du corps d'un téléviseur à écran plat, le système de plaques à dénuder est votre choix. Il est robuste et fiable, dénudant les pièces sans effort, sans broches ni lames. Il gère les pièces lourdes avec grâce, réduisant ainsi les temps de cycle malgré la nécessité de moules complexes.
Fonctionnalité | Éjection de lame | Plaque de décapage |
---|---|---|
Contrainte sur la pièce | Faible | Très faible |
Complexité des moisissures | Modéré | Haut |
Impact sur le temps de cycle | Neutre | Réduit |
Comprendre ces différents systèmes, c'est comme choisir le bon outil pour le travail : chacun a son objectif et ses atouts. Le bon choix peut améliorer considérablement l’efficacité et la qualité des processus de fabrication.
Curieux d’en savoir plus sur ces techniques d’éjection fascinantes ? Plongez dans les techniques d'éjection 3 adaptées à vos besoins.
Les systèmes d'éjection de broches conviennent aux pièces creuses.FAUX
Les systèmes à broches peuvent laisser des traces et sont moins idéaux pour les pièces creuses.
Les systèmes d’éjection de lame nécessitent un alignement précis.Vrai
Un alignement précis évite d'endommager le moule ou le produit.
Comment la conception des pièces influence-t-elle le choix du système d’éjection ?
Vous êtes-vous déjà demandé pourquoi la conception d'une pièce est si cruciale dans le choix du bon système d'éjection pour la conception d'un moule ? Permettez-moi de partager quelques idées qui pourraient bien sauver votre prochain projet.
La conception des pièces a un impact sur le choix du système d'éjection en affectant la force d'éjection, les états de surface et la complexité de la forme, éléments cruciaux pour le bon déroulement des opérations de moulage et la haute qualité des produits.
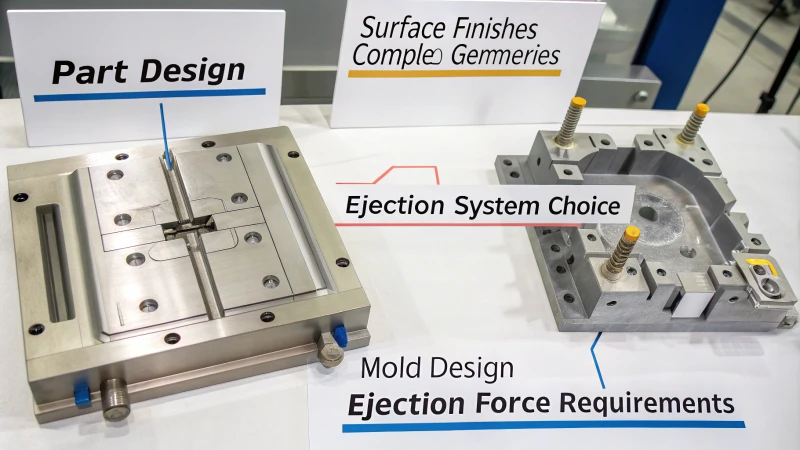
Le rôle des caractéristiques géométriques
Lorsque j’ai débuté dans le monde de la conception de moules, j’ai été submergé par la façon dont chaque petite courbe et chaque bord d’une pièce pouvait dicter la méthode d’éjection dont nous avions besoin. Si vous avez déjà travaillé sur des conceptions complexes, vous savez que ces détails délicats nécessitent parfois un toucher doux, comme un jet d'air ou un système hydraulique, pour éviter d'endommager la pièce. C'est comme manipuler un chaton nouveau-né ; trop de pression peut être désastreuse.
D'un autre côté, si vous avez affaire à des conceptions plus simples, comme des blocs ou des cylindres, les éjections de broches standard sont souvent suffisantes. Je me souviens d'un projet particulier avec un composant à parois fines ; il s'agissait d'un exercice d'équilibre constant entre assurer un flux de matière fluide et obtenir un démoulage propre. La différence d'approche par rapport aux pièces plus épaisses était une véritable courbe d'apprentissage.
Considérations sur la finition de surface
Il y a quelque chose de profondément satisfaisant à voir un produit sortir exactement comme prévu, surtout lorsqu'il présente une finition parfaite. Pour ces produits très brillants, il est crucial de minimiser le contact lors de l’éjection pour éviter les marques ou rayures disgracieuses. Je me souviens d'une époque où nous travaillions sur un composant électronique grand public élégant : nous utilisions un jet d'air pour garantir que la surface immaculée, semblable à un miroir, restait intacte.
Voici une référence rapide que j'utilise souvent :
Finition de surface | Méthode d'éjection recommandée |
---|---|
Haute brillance | Souffle d'air |
Mat | Broches standards |
Texturé | Éjecteurs de manchons |
Force d'éjection et intégrité des pièces
J'ai appris à mes dépens qu'il est primordial de comprendre la bonne force à appliquer lors de l'éjection. Trop de force et vous risquez de déformer la pièce ; trop peu, et il pourrait ne pas s'éjecter correctement du tout. Le calcul de cette force idéale implique d'évaluer les propriétés du matériau 4 et l'épaisseur de la paroi.
Pour ces conceptions complexes, vous avez parfois l’impression de résoudre un puzzle complexe. Des techniques telles que les noyaux pliables ou les éjections en plusieurs étapes ont sauvé la vie pour maintenir l’intégrité des pièces. L'intégration de ces considérations dès le début de la phase de conception m'a évité d'innombrables maux de tête, conduisant à des cycles de production plus fluides et à des résultats de meilleure qualité.
Naviguer dans ces éléments peut sembler intimidant au début, mais une fois qu'ils deviennent une seconde nature, ils améliorent considérablement à la fois l'efficacité et l'excellence des produits.
Les géométries complexes nécessitent des systèmes d'éjection hydrauliques.Vrai
Les systèmes hydrauliques évitent d’endommager les formes complexes lors de l’éjection.
Les éjections de broches standard conviennent mieux aux finitions très brillantes.FAUX
Les finitions très brillantes nécessitent un contact minimal, privilégiant les méthodes de soufflage d'air.
Pourquoi le type de matériau est-il important lors du choix d'un système d'éjection ?
Vous êtes-vous déjà demandé pourquoi le type de matériau que vous choisissez pour un système d’éjection peut tout changer ?
Le choix du bon matériau pour un système d'éjection est crucial pour la durabilité, l'efficacité et la rentabilité, réduisant l'usure et la friction, garantissant la compatibilité avec les produits moulés et améliorant les opérations et la qualité du moulage par injection.
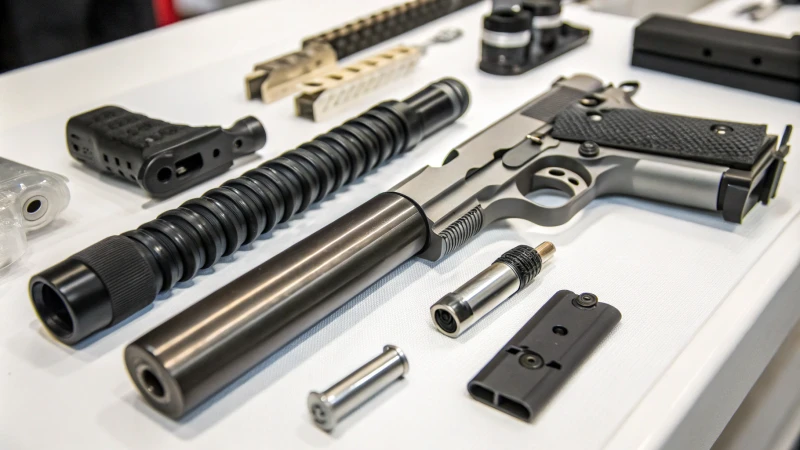
Comprendre les propriétés des matériaux
Lorsque j’ai commencé à travailler dans le monde du moulage par injection, j’ai rapidement appris que choisir le bon matériau pour un système d’éjection, c’était comme trouver la paire de chaussures parfaite. Tout comme pour les chaussures, tout est question d'ajustement et de fonctionnalité. J'ai dû prendre en compte des facteurs tels que la dureté, la conductivité thermique 5 et le coefficient de frottement. Par exemple, l’acier est la solution idéale pour la durabilité, tandis que l’aluminium est un excellent choix lorsque vous avez besoin de quelque chose de plus léger.
Matériel | Dureté | Conductivité thermique | Friction |
---|---|---|---|
Acier | Haut | Modéré | Faible |
Aluminium | Moyen | Haut | Moyen |
Laiton | Faible | Haut | Haut |
Compatibilité avec les matériaux moulés
Je me souviens d'un projet dans lequel nous utilisions un matériau de système d'éjection plus souple pour traiter les plastiques fragiles. Il était crucial d’éviter de rayer ou d’endommager le produit. Cela ressemblait à une partie d’échecs, élaborant une stratégie pour chaque mouvement pour s’assurer que tout s’emboîte parfaitement. De plus, j'ai dû comprendre les interactions chimiques 6 entre l'éjection et les matériaux moulés pour éviter la corrosion.
Rentabilité et efficacité
D’après mon expérience, équilibrer les coûts et les performances, c’est comme marcher sur une corde raide. J'ai souvent vu des entreprises opter pour des matériaux hautes performances malgré leurs coûts initiaux plus élevés, car ils entraînent moins de temps d'arrêt et de maintenance à long terme. Il s'agit toujours de considérer les coûts du cycle de vie 7 , et pas seulement le prix affiché.
Impact sur la qualité des produits
Le matériau d’un système d’éjection peut faire une énorme différence dans la qualité du produit. Je me souviens avoir testé différents matériaux pendant le prototypage pour trouver le point idéal qui minimisait la friction et l'usure, ce qui entraînait moins de défauts. C'est toujours satisfaisant d'atteindre cet objectif et de voir un produit impeccable sortir à la fin. Pour plus d'informations, je me réfère souvent aux études sur l'impact des matériaux sur les défauts 8 .
L'acier est le meilleur matériau pour tous les systèmes d'éjection.FAUX
Bien que l’acier soit durable, d’autres matériaux peuvent être plus adaptés à des besoins spécifiques.
Le choix des matériaux affecte la rentabilité des systèmes d'éjection.Vrai
Équilibrer les coûts et les performances peut améliorer l’efficacité de la production.
Quels sont les défis courants dans la mise en œuvre du système d’éjection ?
Naviguer dans le monde des systèmes d’éjection dans le moulage par injection peut donner l’impression de s’attaquer à un casse-tête complexe. Qu'il s'agisse d'obtenir la force d'éjection idéale ou de gérer le collage de matériaux tenaces, j'ai tout affronté.
Les défis liés à la mise en œuvre du système d'éjection comprennent le calcul de la force d'éjection, la garantie de l'alignement, l'intégration des systèmes de refroidissement et la gestion du collage des matériaux, crucial pour l'efficacité et la minimisation des défauts des produits moulés.
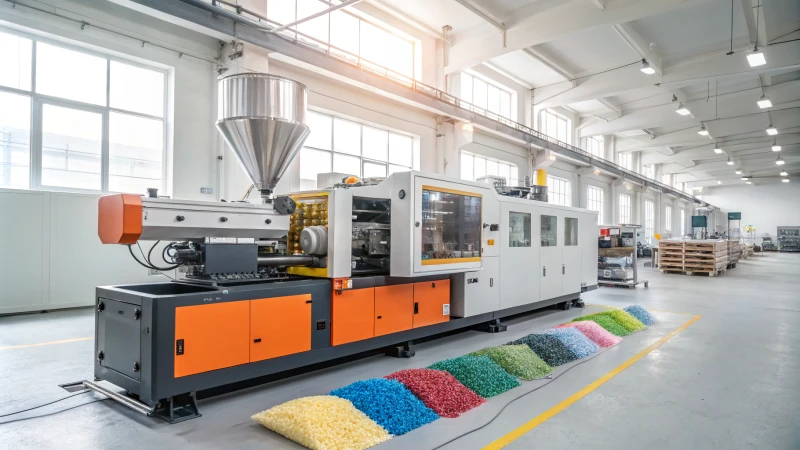
Calcul incorrect de la force d'éjection
Je me souviens encore du moment où j'ai mal calculé la force d'éjection sur un projet. Ce fut un désastre : des pièces étaient soit déformées, soit fissurées. Ce que j'ai appris, c'est qu'il est crucial de bien faire les choses pour éviter d'endommager les pièces ou les moules. C'est comme marcher sur une corde raide entre trop peu et trop de force. Par exemple, une force insuffisante peut déformer la pièce, tandis qu’une force excessive peut la fissurer. Cet équilibre nécessite une compréhension approfondie des propriétés des matériaux et de la géométrie des pièces.
Exemple de tableau : propriétés des matériaux et force d'éjection
Matériel | Force d'éjection (N) |
---|---|
ABS | 100 – 200 |
PP | 150 – 250 |
PC | 200 – 300 |
Ce tableau offre un point de départ pour les forces d'éjection avec des matériaux courants. Les normes 9 -conseil sont souvent nécessaires à la précision.
Mauvais alignement
Le désalignement était un autre problème auquel j’ai été confronté dès le début. C'est comme essayer d'insérer une cheville carrée dans un trou rond : les pièces sont endommagées ou coincées. Des contrôles d'entretien réguliers sont devenus mon mantra après cette expérience. de techniques d'alignement avancées 10 sont essentielles au maintien de la cohérence et de la précision.
Mauvaise intégration du système de refroidissement
Ensuite, il y a le système de refroidissement, que j’apprécie désormais comme le héros méconnu du processus d’éjection. Sans un refroidissement adéquat, les pièces peuvent se déformer ou coller au moule, ce qui me rappelle mes débuts, lorsqu'un refroidissement inégal entraînait des produits déformés. Il est crucial de concevoir un système garantissant une répartition uniforme de la température dans le moule. L'exploration de différentes méthodologies de refroidissement 11 m'a donné un aperçu de l'optimisation de cet aspect crucial.
Collage du matériau
Ah, le matériau qui colle, mon vieil ennemi ! Cela se résume souvent à des angles de dépouille insuffisants ou à des surfaces de moule rugueuses. J'ai découvert que l'utilisation d'agents de démoulage ou la modification de la finition de la surface peuvent considérablement atténuer ce problème. C'est comme trouver la poêle antiadhésive parfaite pour votre omelette du matin. Essayer différents agents de démoulage 12 peut parfois offrir des solutions pratiques.
Techniques de dépannage
Enfin, disposer d’un protocole de dépannage robuste a été mon filet de sécurité en cas de problèmes inattendus. C'est comme être prêt à tout lors d'un voyage de camping : des outils de diagnostic et des journaux détaillés des paramètres du processus d'éjection sont essentiels. Les enseignements tirés d' études de cas 13 portant sur des mises en œuvre similaires ont révélé des stratégies de dépannage efficaces.
En comprenant ces défis et en employant des stratégies ciblées, les ingénieurs comme moi peuvent améliorer la fiabilité et l'efficacité de leurs systèmes d'éjection, garantissant ainsi des résultats de production de haute qualité sans interruptions fréquentes. Il s'agit d'apprendre de chaque expérience et de s'améliorer continuellement.
Une force d'éjection incorrecte peut provoquer une déformation de la pièce.Vrai
Une force d'éjection inadéquate peut entraîner une déformation de la pièce en raison d'un déclenchement incorrect.
Des contrôles d'entretien réguliers sont inutiles pour l'alignement.FAUX
Un entretien régulier est crucial pour garantir un bon alignement et éviter les dommages.
Comment les systèmes d’éjection peuvent-ils affecter la qualité des produits ?
Vous êtes-vous déjà demandé comment les petits détails de la fabrication peuvent faire ou défaire la qualité d'un produit ?
Les systèmes d'éjection dans le moulage par injection sont essentiels au maintien de la qualité du produit, en évitant les défauts tels que les déformations et les marques de contrainte en garantissant un retrait rapide et uniforme des pièces, préservant ainsi l'intégrité du produit.
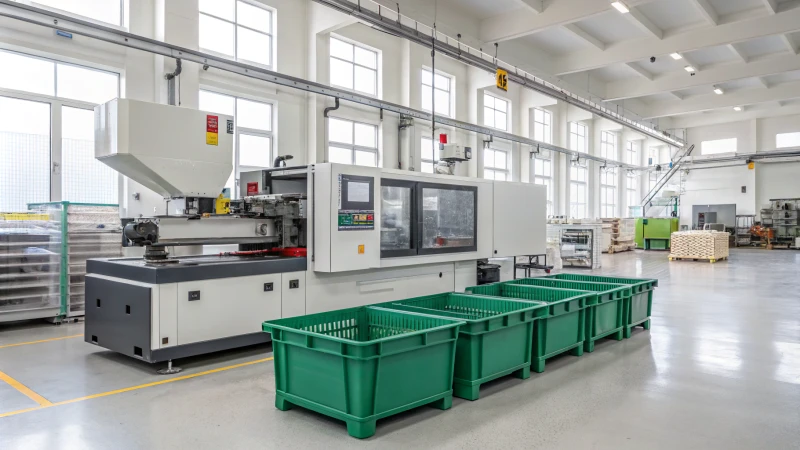
Le rôle des systèmes d'éjection dans le moulage par injection
J'ai toujours trouvé fascinant comment quelque chose d'aussi mineur qu'un système d'éjection puisse avoir un impact aussi important sur la qualité des produits en plastique. À mes débuts à l’usine de moules, je me souviens d’un lot de pièces qui sortaient toutes déformées et inégales. Il s’est avéré que le système d’éjection était mal aligné, provoquant toutes sortes de problèmes. Cette expérience m'a appris que dans le moulage par injection, il est essentiel de bien maîtriser ce système pour retirer les pièces moulées sans causer de dommages. Un système efficace ne permet pas seulement de gagner du temps ; cela réduit les coûts et garantit que chaque pièce est exactement comme elle devrait l'être.
Conceptions courantes de systèmes d’éjection
Au fil des années, j'ai rencontré différentes conceptions de systèmes d'éjection, chacune avec ses avantages et ses inconvénients :
- Éjection de broches : simple et économique, mais laisse parfois ces satanées marques d'épingles sur les produits.
- Éjection de lame : Excellent pour les pièces à paroi mince car il minimise le stress mais peut être un peu coûteux à mettre en place.
- Éjection d'air : Mon choix pour les pièces délicates car elle utilise de l'air comprimé pour éviter tout contact physique et tout dommage potentiel.
Voici une comparaison rapide de ces modèles :
Type d'éjection | Avantages | Limites |
---|---|---|
Épingle | Simple et économique | Peut laisser des marques visibles |
Lame | Contrainte minimale, idéal pour les pièces fines | Coût d'installation plus élevé |
Air | Sans contact, idéal pour les pièces délicates | Nécessite un contrôle précis |
Optimisation de la conception du système d'éjection
Pour tirer le meilleur parti d’un système d’éjection, j’ai appris que l’attention aux détails est primordiale. Tenez compte du choix des matériaux : différents matériaux réagissent différemment aux forces d'éjection. J'ai déjà eu un projet dans lequel le changement de matériaux faisait toute la différence dans la réduction des défauts. Un bon étalonnage de la force est également crucial ; il évite les dommages lors de l'éjection et maintient la précision dimensionnelle. L’ajustement du temps de refroidissement est un autre problème important ; s'assurer que la pièce est suffisamment solidifiée avant son éjection peut réduire considérablement les risques de déformation.
À tous ceux qui souhaitent approfondir l’amélioration de la qualité des produits, je recommanderais d’explorer des sujets tels que la sélection des matériaux 14 et les techniques de refroidissement 15 . Ces informations ont changé la donne pour moi en améliorant l'intégrité des produits 16 et en augmentant l'efficacité de la fabrication.
Une éjection incorrecte provoque une déformation des pièces moulées.Vrai
Une éjection incorrecte peut entraîner un refroidissement irrégulier, provoquant une déformation.
L'éjection de lame est rentable pour tous les types de pièces.FAUX
L'éjection de la lame est coûteuse et convient mieux aux pièces à paroi mince, pas à tous les types.
Quelles innovations émergent dans la technologie d’éjection de moules ?
Vous êtes-vous déjà demandé comment la tâche apparemment simple consistant à éjecter une pièce moulée évolue avec les technologies de pointe ? Plongeons dans le monde fascinant des innovations en matière d'éjection de moules.
Les innovations émergentes dans la technologie d'éjection de moules, notamment les systèmes d'éjection avancés, les moules intégrés aux capteurs et l'automatisation, améliorent l'efficacité, la précision et la qualité de la fabrication.
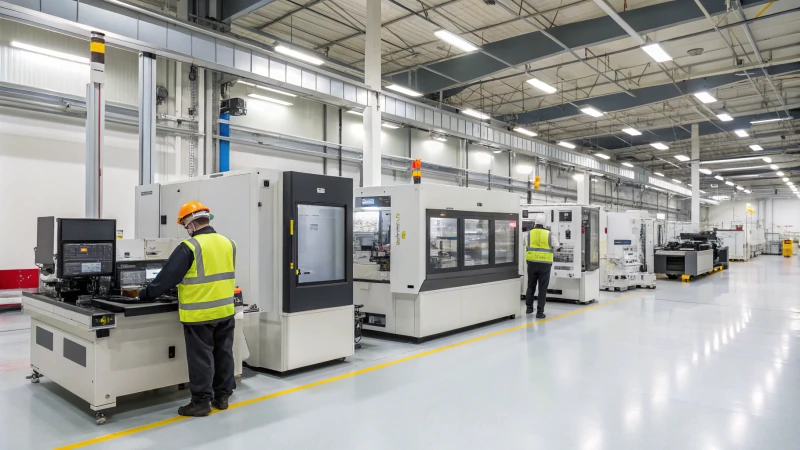
Systèmes d'éjection avancés
Imaginez le plaisir de travailler avec des matériaux qui semblent presque vivants, s'adaptant aux changements de température comme s'ils savaient exactement ce qui est nécessaire. C'est la magie qui se cache aujourd'hui derrière les systèmes d'éjection avancés. Ils utilisent des matériaux intelligents 17 qui s'ajustent parfaitement, réduisant ainsi l'usure comme dans un rêve. Vous vous souvenez de l’époque où nous devions constamment surveiller et ajuster les différentes températures de moisissure ? Ces systèmes le font tout seuls, promettant une durée de vie plus longue et une meilleure fiabilité. C'est comme avoir une paire de mains supplémentaire pour garantir que chaque pièce soit libérée en douceur, à chaque fois.
Moules avec capteurs intégrés
Avez-vous déjà souhaité pouvoir voir à l'intérieur de votre moule, pour comprendre exactement ce qui se passe ? Avec les moules à capteurs intégrés, ce souhait est désormais une réalité. Ils collectent des données en temps réel : température, pression, forces d'éjection, etc. Je me souviens de la première fois que j'ai vu un 18 à capteur intégré en action ; c'était comme entrer dans le futur. Nous pouvons désormais effectuer des ajustements précis à la volée, réduisant ainsi les défauts et améliorant l’efficacité au-delà de tout ce que nous avions imaginé.
Fonctionnalité | Avantage |
---|---|
Surveillance en temps réel | Retour immédiat pour les ajustements |
Analyse des données | Optimise le temps de cycle |
Maintenance prédictive | Réduit les temps d'arrêt |
Automatisation de l'éjection de moules
Ah, l'automatisation : le rêve de tout concepteur cherchant à réduire les ajustements manuels et les erreurs. Les systèmes automatisés ont changé la donne, s’attaquant à des formes complexes et à des tâches multiples sans transpirer. Je me souviens de mes débuts en matière de manipulation manuelle de conceptions complexes ; c'était comme un puzzle sans fin. Désormais, les systèmes d'éjection automatisés 19 améliorent sans effort la productivité et la précision. Moins de place à l’erreur humaine signifie des produits de meilleure qualité, et c’est quelque chose que nous pouvons tous célébrer.
Alors que je continue d’explorer ces avancées, je me souviens constamment de l’importance de rester informé. Pour quelqu'un comme moi qui est profondément impliqué dans la conception et la fabrication de moules, ces technologies émergentes ne sont pas seulement des outils : elles sont des partenaires dans la création efficace et efficiente de produits de premier ordre. Il est passionnant de réfléchir à la manière dont ces innovations façonneront notre travail et nos succès futurs.
Les matériaux intelligents réduisent l’usure des systèmes d’éjection de moules.Vrai
Les matériaux intelligents s'adaptent aux changements de température, minimisant ainsi l'usure.
L'automatisation de l'éjection des moules augmente les erreurs humaines.FAUX
L'automatisation réduit l'intervention humaine, diminuant ainsi les erreurs.
Conclusion
Le choix du bon système d'éjection pour les moules est crucial pour l'efficacité et la qualité de la production, influencé par la conception des pièces, le type de matériau et la méthode d'éjection.
-
Découvrez le fonctionnement de l'éjection des broches et ses applications dans diverses industries. ↩
-
Découvrez la mécanique et les avantages des systèmes d'éjection de lame pour les conceptions complexes. ↩
-
Explorez des techniques innovantes pour optimiser vos processus de moulage. ↩
-
Ce lien explique comment différentes caractéristiques géométriques influencent le choix des systèmes d'éjection, fournissant ainsi des informations sur l'optimisation de la conception des moules. ↩
-
Comprendre la conductivité thermique est crucial pour sélectionner des matériaux qui gèrent efficacement la chaleur, garantissant ainsi des cycles de refroidissement efficaces. ↩
-
Découvrez comment les interactions chimiques peuvent affecter les performances et la longévité du système d'éjection. ↩
-
Découvrez pourquoi la prise en compte des coûts du cycle de vie aide à sélectionner le matériau le plus rentable au fil du temps. ↩
-
Explorez la recherche sur la manière dont le choix des matériaux influence les taux de défauts et la qualité globale des produits. ↩
-
Explorez des normes d'ingénierie complètes pour calculer avec précision la force d'éjection requise, garantissant ainsi l'intégrité du moule et la qualité des pièces. ↩
-
Découvrez des techniques d'alignement innovantes qui améliorent la précision des systèmes d'éjection, minimisant ainsi le risque d'endommagement des pièces. ↩
-
Découvrez les différentes méthodes de refroidissement pour optimiser le contrôle de la température des moules, réduisant ainsi les défauts tels que le gauchissement et le collage. ↩
-
Recherchez des agents de démoulage efficaces pour empêcher le matériau de coller et améliorer l’efficacité de l’éjection. ↩
-
Obtenez des informations à partir d'études de cas réelles pour améliorer vos compétences en dépannage lors de la mise en œuvre de systèmes d'éjection. ↩
-
Le choix des bons matériaux améliore la durabilité et les performances des systèmes d'éjection, réduisant ainsi les défauts. ↩
-
Des techniques de refroidissement appropriées empêchent la déformation et le retrait, préservant ainsi la qualité des produits moulés. ↩
-
Le maintien de l’intégrité garantit que vos produits répondent à des normes élevées sans compromettre l’esthétique ou la fonctionnalité. ↩
-
Découvrez comment les matériaux intelligents peuvent s'adapter aux conditions changeantes des systèmes d'éjection de moules, améliorant ainsi les performances et la longévité. ↩
-
Découvrez comment l'intégration de capteurs peut fournir des données précieuses pour optimiser les processus de fabrication de moules. ↩
-
Découvrez comment l'automatisation transforme les processus d'éjection de moules en améliorant la vitesse, la précision et en réduisant les erreurs. ↩