Je me souviens de la première fois que j'ai mis un casque - je me suis sentie dans un monde de sécurité et d'aventure. Vous êtes-vous déjà demandé comment ces outils de sécurité cruciaux sont fabriqués?
Les machines de moulage par injection créent des casques en sélectionnant des matériaux précis, en concevant des moules détaillés et en effectuant des contrôles de qualité stricts pour assurer la sécurité et l'efficacité.
Lorsque je me suis plongé pour la première fois dans le monde de la production de casques, la complexité du choix des matériaux comme le polycarbonate ou les abs m'ont étonné. Ces matériaux offrent non seulement la ténacité et la clarté nécessaires, mais assurent également la rentabilité. Le voyage de conception d'un moule qui correspond aux courbes complexes de la tête était tout aussi fascinante. C'est comme sculpter un chef-d'œuvre qui promet une protection. Et puis, en regardant le plastique fondu se refroidir sous une forme solide - chacun de casque émergeant de son moule en tant que gardien pour la tête du porteur - mettant en évidence la magie derrière le moulage par injection. Ce processus méticuleux ne fait pas seulement des casques; Il façonne la sécurité.
Le moulage par injection est utilisé pour fabriquer des coquilles de casque.Vrai
Le moulage par injection crée efficacement des coquilles de casque précises et durables.
Les casques sont fabriqués en utilisant un seul type de plastique.FAUX
Différents plastiques sont sélectionnés pour leurs propriétés et leurs pièces de casque.
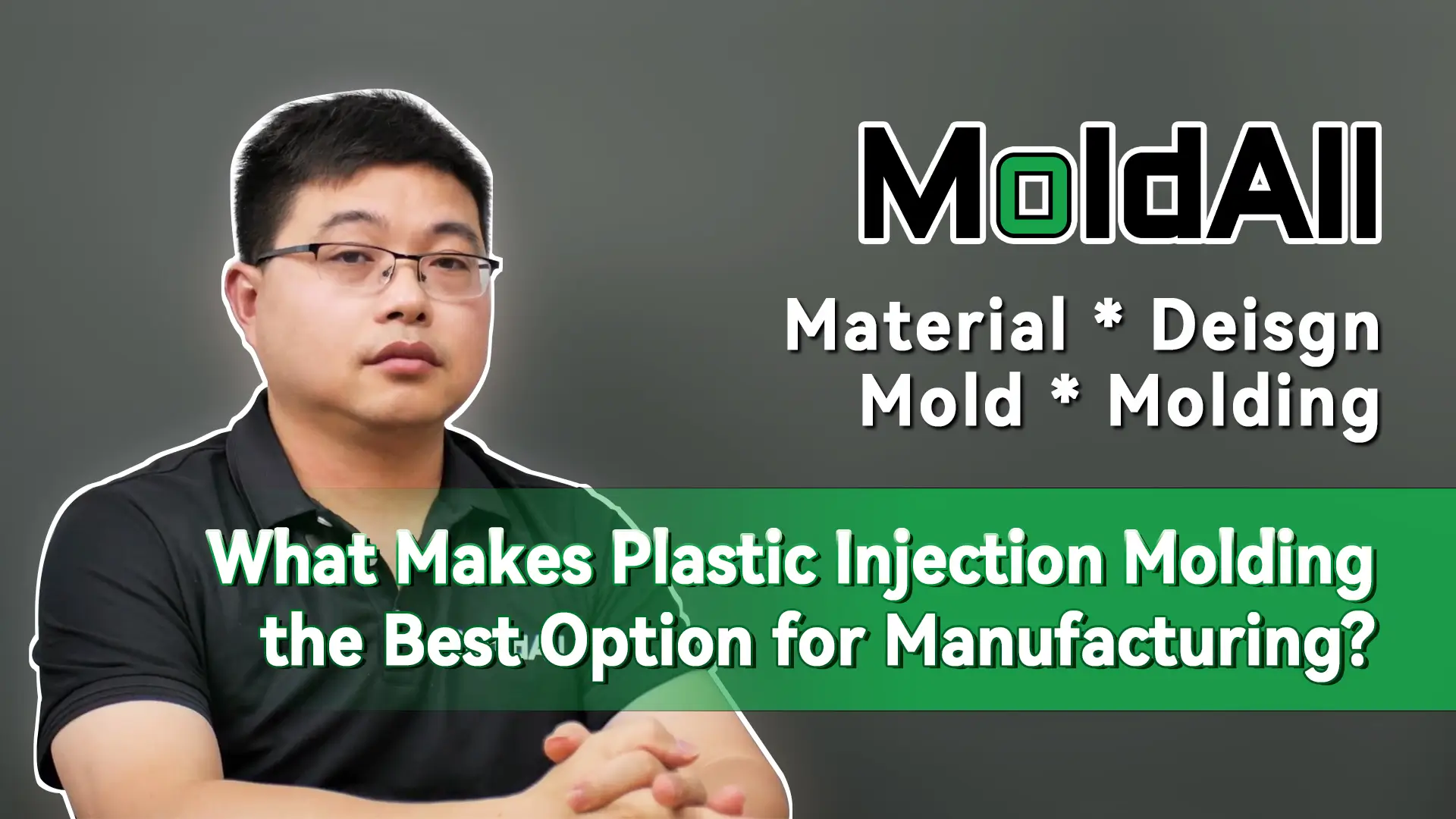
- 1. Quels matériaux sont les meilleurs pour le moulage par injection de casque?
- 2. Comment la conception des moisissures influence-t-elle la qualité du casque?
- 3. Comment les casques sont-ils fabriqués à l'aide de moulage par injection?
- 4. Pourquoi le contrôle de la qualité est-il crucial dans la fabrication des casques?
- 5. Comment les normes de sécurité ont-elles un impact sur la production de casques?
- 6. Conclusion
Quels matériaux sont les meilleurs pour le moulage par injection de casque?
Je me souviens de la première fois que j'ai démonté un casque pour voir ce qui le rendait si fort et sûr. Il est incroyable de voir comment les bons matériaux peuvent transformer un simple moule en une pièce d'équipement sauvage.
Le polycarbonate et l'acrylonitrile-butadiène-styrène ( ABS ) sont idéaux pour le moulage par injection de casque, offrant une excellente résistance à l'impact, la durabilité et la rentabilité, améliorant la résistance et l'efficacité du casque.
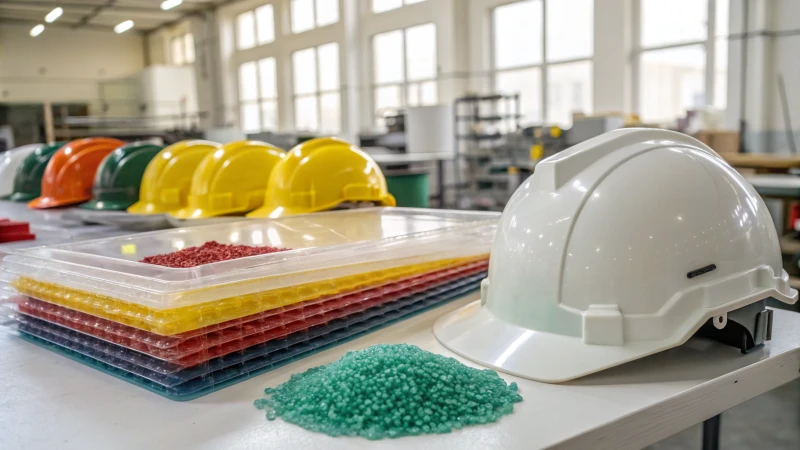
Quand j'ai commencé à bricoler des dessins de moisissures, j'ai été captivé par l'art de choisir les bons matériaux. C'est comme trouver l'équilibre parfait dans une recette pour s'assurer que le produit final est non seulement durable mais aussi sûr.
Pourquoi choisir le polycarbonate?
Le polycarbonate ( PC ) est rapidement devenu un favori dans ma boîte à outils. Sa résistance à fort impact et sa clarté optique le rendent indispensable pour la fabrication du casque 1 . Pensez-y comme porter des lunettes; Vous devez voir clairement sans sacrifier la sécurité. La résilience de PC
- Résistance à l'impact: le PC est comme un bouclier invisible, absorbant les coups sans se fissurer.
- Clarité optique: essentiel pour les casques avec les visières; C'est comme si vous regardiez à travers une fenêtre cristalline.
- Résistance mécanique: construite pour durer, il maintient le casque intact dans le temps et l'utilisation.
Les avantages de l'ABS
Ensuite, il y a de l'acrylonitrile-butadiène-styrène ( ABS ), que j'aime considérer comme l'épine dorsale robuste de la production de casque. C'est abordable mais difficile, offrant une base solide qui résiste à l'usure quotidienne.
- Ténacité et rigidité: imaginez la résilience d'une maison bien construite - elle est conçue pour résister aux éléments.
- Corplication: Considérez les abdos comme en vous donnant plus pour votre argent, en particulier dans la production à grande échelle.
- Facilité de traitement: un matériau de rêve pour des cycles de production efficaces, ce qui rend la fabrication moins de maux de tête.
Matériel | Résistance aux chocs | Coût | Processabilité |
---|---|---|---|
Polycarbonate | Haut | Modéré | Bien |
ABS | Modéré | Faible | Excellent |
Combiner PC et ABS
En mélangeant le polycarbonate et l'ABS 2 , c'est comme combiner du beurre d'arachide et de la gelée - tout apporte quelque chose de spécial à la table. Ce mélange améliore la ténacité, rend les formes complexes plus faciles à mouler et équilibre les coûts à merveille.
Facteurs influençant la sélection des matériaux
Chaque fois que je suis profondément dans la phase de conception, plusieurs facteurs guident mon choix de matériaux:
- Normes de sécurité: respecter les réglementations de sécurité n'est pas négociable; Ces casques doivent protéger à tout prix. Explorez plus sur les normes de sécurité 3 et comment ces matériaux respectent les réglementations strictes pour fournir une protection optimale.
- Conception du casque: Des conceptions complexes nécessitent souvent des capacités flexibles des mélanges PC / ABS
- Volume de production: pour la production de masse, des matériaux rentables comme l'ABS occupent le devant de la scène.
La compréhension de ces éléments aide à fabriquer des casques qui répondent non seulement aux attentes de performance, mais assurent également la sécurité et le confort des utilisateurs. Tout comme la création d'un chef-d'œuvre, chaque détail compte.
Le polycarbonate offre une clarté optique élevée pour les visières de casque.Vrai
Le polycarbonate est connu pour sa clarté optique, ce qui le rend idéal pour les visières claires.
L'ABS est plus cher que le polycarbonate pour la production de casque.FAUX
L'ABS est généralement plus rentable que le polycarbonate, ce qui le rend populaire pour la production de masse.
Comment la conception des moisissures influence-t-elle la qualité du casque?
Vous êtes-vous déjà demandé ce qui se passe vraiment pour faire un casque de haute qualité? Plongeons-nous dans le rôle critique que la conception du moule joue pour façonner l'excellence du casque.
La conception des moisissures est vitale dans la production de casques, affectant l'intégrité structurelle, l'ajustement et la sécurité du casque. La précision dans le moule améliore le confort du casque, l'esthétique et les caractéristiques de protection, garantissant une sortie de haute qualité.
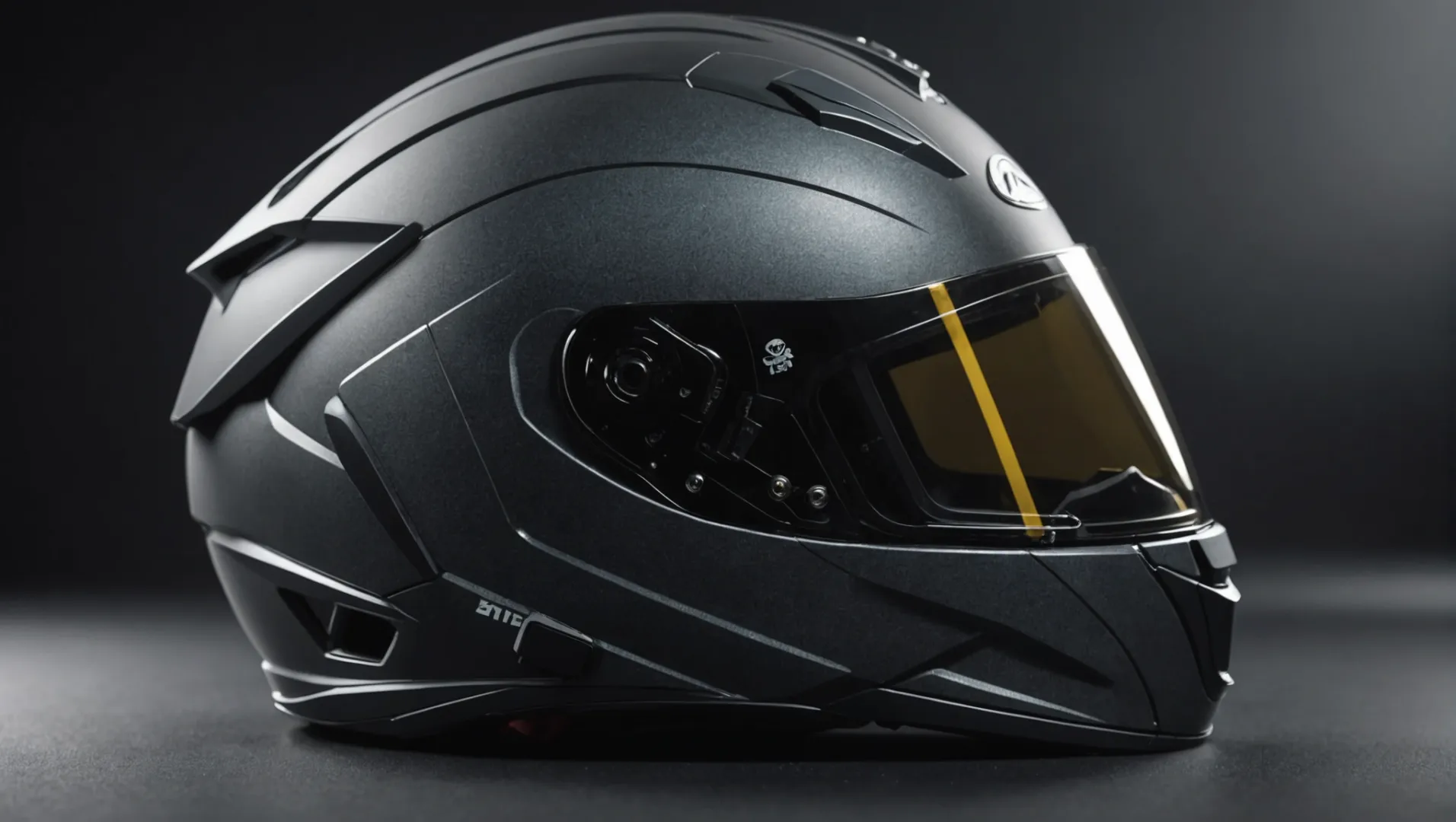
Sélection des matériaux et son impact
Lorsque j'ai commencé à travailler avec la production de casques, j'ai rapidement appris que le choix des bons matériaux, c'est comme trouver les ingrédients parfaits pour une recette - il peut faire ou casser le produit final. Nous utilisons généralement du polycarbonate ( PC ) et de l'acrylonitrile-butadiène-styrène ( ABS ) car ils offrent un grand équilibre de résistance à l'impact et de facilité de traitement. PC est notre incontournable pour sa ténacité, tandis que l'ABS nous aide à contrôler les coûts sans compromettre la qualité.
Un tableau illustrant les propriétés du matériau:
Matériel | Résistance aux chocs | Processabilité | Rentabilité |
---|---|---|---|
PC | Haut | Modéré | Haut |
ABS | Modéré | Haut | Modéré |
Subtilités de la conception de moisissures
L'étape de conception de moisissure ressemble à de la création d'un puzzle complexe. Chaque pièce, de la courbure du casque 4 à sa forme aérodynamique, doit s'adapter parfaitement. Je me souviens de la première fois que j'ai vu des évents intégrés dans un moule - cela changeait la donne pour le confort et les fonctionnalités, permettant un meilleur flux d'air.
Composants de moule clés:
- Moule de carrosserie du casque: il est essentiel pour la protection et les looks.
- Moule de doublure intérieure: pensez-y comme un coussin confortable qui s'enroule autour de votre tête.
- Système d'éjection: les épingles d'éjection correctement placées s'assurent que le casque apparaît en douceur sans dommage.
Le processus de moulage par injection
Le moulage par injection est l'endroit où la magie se produit. Je suis toujours excité en regardant les granulés en plastique se transformer en casques solides. Par exemple, nous faisons fondre PC à 280-320 ° C. Il est fascinant de voir comment l'ajustement de la pression d'injection 5 et de la vitesse peut affecter le produit final.
Étapes du processus :
- Mélange et injection: les granulés sont chauffés jusqu'à ce qu'ils coulent comme du sirop.
- Refroidissement: le casque prend forme à mesure qu'il refroidisse - le timing est tout ici.
- Éjection: Out est un nouveau casque brillant, prêt pour l'inspection.
Considérations de qualité dans la conception de moisissures
La satisfaction des normes de sécurité n'est pas négociable dans notre ligne de travail. J'ai vu de première main comment une finition lisse peut empêcher l'irritation cutanée, ce qui rend la précision dans la conception des moisissures cruciale pour le confort et la sécurité.
Voici notre liste de contrôle pour assurer la qualité du casque de premier ordre:
- Résistance à l'impact: doit passer des tests de sécurité rigoureux.
- Finition de surface 6 : lisse en soie pour un confort maximal.
- Précision d'adaptation: garantit que le casque se trouve juste sur votre tête.
En fin de compte, la conception des moisissures n'est pas seulement une question d'efficacité - il s'agit de cassants auxquels les gens peuvent faire confiance avec leur sécurité et leur confort.
Le polycarbonate offre une résistance à fort impact dans les casques.Vrai
Le polycarbonate est connu pour sa forte résistance à l'impact, ce qui le rend idéal pour les casques.
L'ABS offre une meilleure résistance à l'impact que le polycarbonate.FAUX
L'ABS offre une résistance à l'impact modéré, tandis que le polycarbonate offre une résistance élevée.
Comment les casques sont-ils fabriqués à l'aide de moulage par injection?
Vous êtes-vous déjà demandé comment ces casques robustes auxquels nous avons confiance ont tant pris vie?
Le moulage par injection pour les casques implique la sélection des matériaux, la conception de moules, la fusion et l'injection de plastique, le refroidissement, l'éjection du casque et les vérifications de qualité approfondies pour assurer la durabilité et la sécurité.
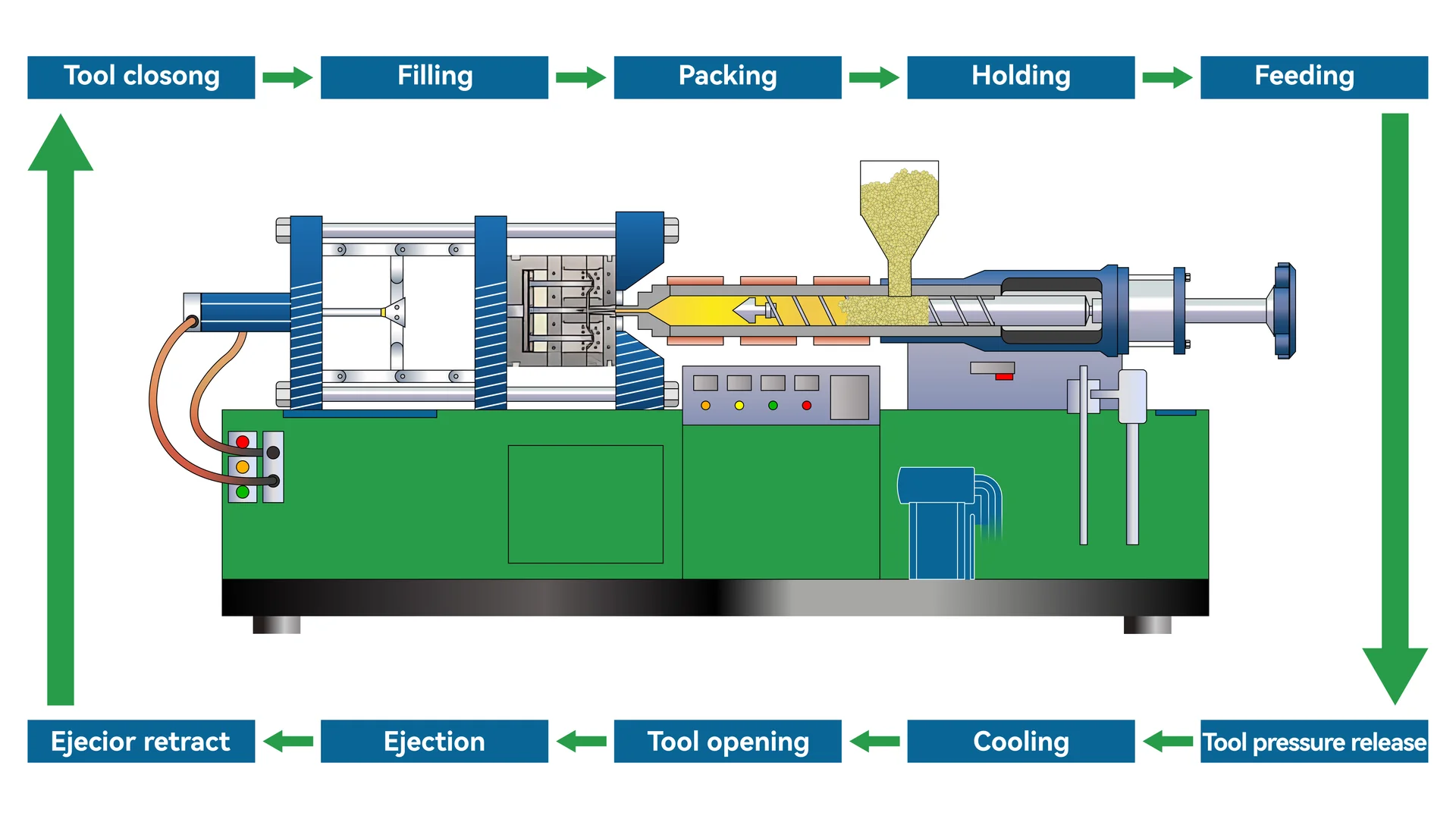
Sélection des matériaux
Je me souviens de la première fois que je suis entré dans une usine de moisissure; C'était un monde propre. La clé pour faire un excellent casque commence par la sélection des bons matériaux. Pensez-y comme choisir les meilleurs ingrédients pour votre plat préféré. Pour les casques, je regarde souvent le polycarbonate ( PC ) pour sa résistance et sa clarté à impact de premier ordre, ou son acrylonitrile-butadiène ( ABS ) car il est difficile et rentable. Mélanger ces deux peut être comme tirer le meilleur parti des deux mondes.
Matériel | Propriétés |
---|---|
PC | Haute résistance aux chocs, clarté |
ABS | Ténacité, rentable |
Conception de moules
Moule de carrosserie du casque:
La conception du moule, c'est comme rédiger les plans pour une nouvelle maison. Il doit parfaitement refléter la forme complexe du casque, en tenant compte de l'aérodynamique et de la sécurité. Lors de la conception de fonctionnalités telles que les évents, il est crucial, ils sont intégrés de manière transparente dans le moule pour assurer le bon flux d'air.
Moule de doublure intérieure:
Pour les casques qui nécessitent une doublure intérieure confortable, j'utilise un moule séparé pour fabriquer cette partie avec des matériaux plus doux.
Système d'éjection:
Et n'oublions pas le système d'éjection - ces minuscules épingles d'éjecteurs doivent être placées juste à juste titre pour sortir le casque hors du moule sans accroc. Le placement est basé sur la forme du casque pour distribuer uniformément la force d'éjection.
Processus de moulage par injection
Mélange et injection:
Maintenant, sur l'événement principal! Il s'agit de chauffer ces pastilles en plastique jusqu'à ce qu'ils fondent - l'imagine faisant une fondue au chocolat lisse et les injectant ensuite dans le moule sous haute pression. Pour le polycarbonate, cela signifie que les températures planent jusqu'à 320 ° C!
Matériel | Point de fusion (°C) |
---|---|
Polycarbonate | 280-320 |
ABS | 200-260 |
Refroidissement et éjection:
Une fois refroidi et solidifié, il est incroyable de regarder chaque casque émerger du moule, prêt à l'action.
Ce cycle se répète pour la production de masse.
Considérations relatives à la qualité
Enfin, les contrôles de qualité ne sont pas négociables. Chaque casque doit répondre à des normes de sécurité 7 ; Après tout, nous parlons de protéger des vies ici. La surface doit être lisse pour éviter toute irritation lorsqu'elle est portée. Et croyez-moi, la précision dans le moulage n'est pas une question de look - il s'agit de s'assurer que chaque casque est un fidèle compagnon en cas de besoin le plus.
En réfléchissant à mon voyage dans ce domaine, je me souviens comment chaque étape contribue à faire des casques fiables sur lesquels les personnes dans le monde dépendent pour la sécurité.
Le polycarbonate fond à 280-320 ° C dans le moulage par injection.Vrai
Le point de fusion du polycarbonate se situe en effet dans cette plage, adaptée à la moulure.
L'ABS est utilisé pour sa clarté optique dans les casques.FAUX
L'ABS est choisi pour la ténacité et la rentabilité, et non la clarté optique.
Pourquoi le contrôle de la qualité est-il crucial dans la fabrication des casques?
Vous êtes-vous déjà demandé ce qui se passe vraiment pour faire un casque?
Le contrôle de la qualité dans la fabrication des casques garantit la sécurité, la durabilité et la conformité aux normes grâce à des tests rigoureux, garantissant une protection efficace des utilisateurs.
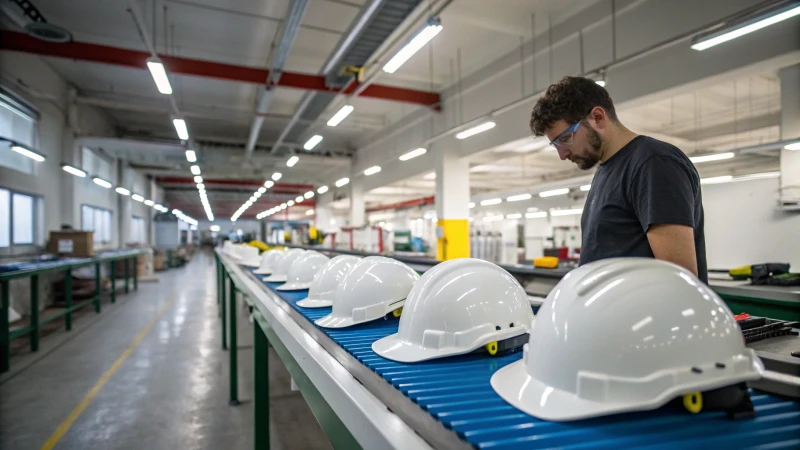
Sélection et importance des matériaux
Je me souviens de la première fois que j'ai vu un casque être mis à l'épreuve dans un laboratoire de contrôle de la qualité. Cela m'a frappé à quel point la réflexion se déroule dans la sélection des bons matériaux, comme le polycarbonate ( PC ) et l'acrylonitrile-butadiène-styrène ( ABS ). PC offre une résistance à l'impact incroyable, tandis que l'ABS offre la rigidité et la rentabilité nécessaires pour un usage quotidien. Lorsqu'ils sont combinés, ils créent un bouclier super fort, qui est essentiel pour améliorer la qualité du casque 8 .
Signification de conception de moisissure
De retour à mes débuts, j'ai appris que la conception de moisissures est tout. Les moules doivent accueillir chaque courbe et évent du casque pour s'assurer qu'elle est aérodynamique et offre une protection à impact de premier ordre.
Caractéristiques de conception de moisissure | Avantages |
---|---|
Moule du corps du casque | Forme et protection aérodynamique |
Moule de doublure intérieure | Confort et absorption des chocs |
Système d'éjection | Élimination du casque sans dommages |
Imaginez concevoir un moule à doublure intérieure si bien que cela ressemble à un coussin contre votre tête - c'est ce que nous visons avec différents matériaux pour l'absorption de choc 9 .
Processus de moulage par injection
Permettez-moi de vous guider à travers la magie du processus de moulage par injection. Imaginez ceci: minuscules granules en plastique transformées sous la chaleur en forme d'un casque. Il s'agit de précision - le polycarbonate fond à 280-320 ° C tandis que l'ABS a besoin de 200-260 ° C. Une fois moulés, ces casques se refroidissent avant qu'ils ne sortent, prêts pour la production de casque 10 .
Assurer les normes de sécurité
Répondre aux normes de sécurité n'est pas seulement une exigence; C'est une responsabilité que nous prenons au sérieux. Les casques sont soumis à une batterie de tests de résistance à l'impact et de stabilité pour s'assurer qu'ils sont à la hauteur. Même la finition de surface est importante - aucun ne veut un casque de démangeaisons et inconfortables! L'attention aux détails pendant le processus d'assurance qualité 11 garantit que chaque casque a non seulement l'air bien, mais se sent bien aussi.
Les casques PC offrent une meilleure résistance à l'impact que les casques ABS.Vrai
Le polycarbonate (PC) a une résistance à l'impact plus élevée par rapport à l'acrylonitrile-butadiène-styrène (ABS).
L'ABS est plus cher que le PC dans la production de casque.FAUX
L'ABS est généralement plus rentable que le polycarbonate (PC) dans la fabrication.
Comment les normes de sécurité ont-elles un impact sur la production de casques?
Vous êtes-vous déjà demandé comment les normes de sécurité façonnent la façon dont les casques sont fabriqués? C'est plus complexe que vous ne le pensez, ce qui impactait tout, du choix des matériaux aux plus petits détails de conception.
Les normes de sécurité influencent la production de casques en fixant des critères stricts pour les matériaux, la conception et les tests pour assurer un impact optimal et une résistance à la pénétration.
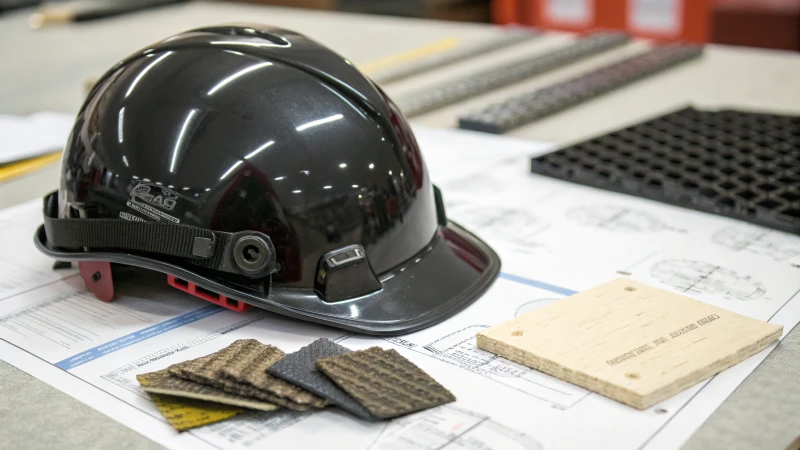
Normes de sélection et de sécurité des matériaux
Je me souviens de la première fois que j'ai tenu un casque en polycarbonate ( PC ) et acrylonitrile-butadiène-styrène ( ABS ). Ces matériaux sont fascinants car ils mélangent la ténacité avec la capacité d'absorber les chocs pendant les collisions - comme un duo de super-héros!
- Polycarbonate ( PC ): Celui-ci est comme le héros méconnu, offrant une résistance à fort impact 12 et une clarté optique.
- Acrylonitrile-butadiène-styrène ( ABS ): il apporte de la ténacité et est favorable à un budget.
- Combinaison: l'utilisation des deux nous donne un casque qui peut gérer des impacts difficiles tout en faisant baisser les coûts.
Conception de moisissure influencée par les normes
La conception d'un moule de casque, c'est comme créer un gant personnalisé. Le moule doit embrasser chaque courbe de la tête pour assurer à la fois le confort et la sécurité. Une fois, j'ai regardé un designer des évents méticuleusement placés pour permettre le flux d'air sans compromettre la sécurité. Ce sont ces petits détails qui font une si grande différence!
- Zone ajustée: assure le confort et la sécurité.
- Forme aérodynamique: réduit la traînée tout en maintenant la protection.
- Placement de ventilation: permet un flux d'air sans compromettre la sécurité.
Le moule à doublure intérieure utilise des matériaux plus doux pour le confort et une absorption de choc supplémentaire.
Processus de moulage par injection et conformité
Assister au processus de moulage par injection, c'est comme regarder la magie se dérouler. La machine fait fondre les granulés en plastique et les injecte dans des moules avec précision. Les normes dictent la pression d'injection 13 et la vitesse, assurant que les casques répondent à ces exigences de résistance à l'impact critique.
Scène | Description |
---|---|
Fusion et injection | Les pastilles en plastique sont fondues et injectées dans des moules. |
Refroidissement et éjection | Les casques refroidissent avant d'être éjectés de moules. |
Contrôle de la qualité en fonction des normes
Chaque casque est rigoureusement testé pour s'assurer qu'il répond aux normes de sécurité. Je les ai vus passer par des tests de résistance à l'impact qui imitent les collisions réelles - c'est intense mais nécessaire.
- Résistance à l'impact: testé pour la protection lors des accidents.
- Résistance à la pénétration: Assure qu'aucun objet net ne peut percer le casque.
- Finition de surface: les finitions lisses empêchent l'irritation cutanée.
L'ajustement, influencé par un moulage précis, est essentiel pour la sécurité et le confort des utilisateurs.
Le rôle des normes de sécurité dans l'innovation
Les normes de sécurité ne sont pas seulement une question de conformité; Il s'agit également de l'innovation. Ils poussent les fabricants à explorer de nouveaux matériaux 14 et des processus qui améliorent la protection tout en adhérant à des réglementations strictes. Cette quête d'innovation conduit à des casques qui sont plus sûrs et plus confortables - un gagnant-gagnant pour toutes les personnes impliquées.
En réfléchissant à ces aspects, je vois comment les normes de sécurité guident les fabricants dans la création de casques qui protègent des vies. Au fur et à mesure que la technologie progresse, ces normes évolueront, continuant de défier et de nous inspirer à fabriquer des casques toujours à son assurer.
Le polycarbonate est choisi pour sa clarté optique dans les casques.Vrai
Le polycarbonate est connu pour sa forte résistance à l'impact et sa clarté optique.
L'ABS est plus cher que le polycarbonate dans la production de casques.FAUX
ABS offre une ténacité et une efficacité, ce qui le rend moins cher.
Conclusion
Les machines de moulage par injection créent des casques en sélectionnant des matériaux comme le polycarbonate et l'ABS , la conception de moules, l'injection de plastique fondu, le refroidissement du produit et la qualité de la qualité grâce à des normes de sécurité rigoureuses.
-
Découvrez pourquoi le polycarbonate est favorisé dans la production de casques pour sa résistance à l'impact et sa clarté. ↩
-
Comprendre comment le mélange PC et ABS améliore la force du casque et l'efficacité du processus. ↩
-
Découvrez comment les différents matériaux répondent aux normes de sécurité essentielles pour la fabrication des casques. ↩
-
L'exploration de ce lien fournira des informations sur la façon dont les formes de moisissures affectent les performances et la sécurité du casque. ↩
-
Découvrir plus sur la pression d'injection aidera à comprendre son rôle dans la réalisation de la qualité cohérente du casque. ↩
-
Cliquer sur ce lien révélera pourquoi la finition de surface est cruciale pour la sécurité du casque et le confort de l'utilisateur. ↩
-
Plongez dans les normes de sécurité nécessaires pour assurer la fiabilité du casque pendant les impacts. ↩
-
Découvrez comment la combinaison du PC et de l'ABS améliore la durabilité et la sécurité du casque. ↩
-
Découvrez pourquoi les moules bien conçus sont essentiels pour l'intégrité du casque. ↩
-
Explorez les étapes impliquées dans la moulure précise d'injection des casques. ↩
-
Comprendre les casques de test rigoureux subissent pour répondre aux normes de sécurité. ↩
-
Découvrez comment les matériaux en polycarbonate et ABS améliorent la sécurité des casques grâce à une résistance à l'impact supérieur. ↩
-
Découvrez les paramètres optimaux de pression d'injection cruciaux pour produire des casques qui répondent aux normes de sécurité. ↩
-
Explorez les matériaux de pointe stimulant l'innovation dans la production de casques tout en garantissant le respect des normes de sécurité. ↩