La conception des canaux de moulage par injection change la donne dans le domaine de la fabrication.
Les erreurs courantes dans la conception des canaux de moulage par injection incluent une taille et une forme inappropriées, un positionnement incorrect des portes et des systèmes de canaux déséquilibrés. En résolvant ces problèmes grâce à une conception minutieuse et à une analyse du flux de moule, vous pouvez améliorer la qualité des produits et réduire les coûts.
Comprendre les erreurs n’est que le début ; Explorons comment nous pouvons résoudre ces problèmes efficacement !
Une taille inappropriée des canaux entraîne une augmentation des défauts.Vrai
La taille des canaux affecte l'écoulement de la matière fondue et le refroidissement, ce qui a un impact sur la qualité.
- 1. Comment la taille des coureurs affecte-t-elle la qualité du produit ?
- 2. Quelles sont les meilleures pratiques pour concevoir des formes de canaux d’écoulement ?
- 3. Pourquoi la position de la porte est-elle critique dans la conception des coureurs ?
- 4. Comment atteindre l’équilibre des canaux dans les moules multi-empreintes ?
- 5. Conclusion
Comment la taille des coureurs affecte-t-elle la qualité du produit ?
La taille des canaux dans les moules à injection est cruciale pour garantir des produits de haute qualité. Un dimensionnement incorrect peut entraîner des défauts et des inefficacités.
La taille des canaux affecte la qualité du produit en influençant l'écoulement de la matière fondue, les vitesses de refroidissement et la répartition des contraintes. Un dimensionnement optimal garantit un remplissage efficace, réduit le gaspillage de matériaux et minimise les défauts tels que la déformation ou la fissuration.
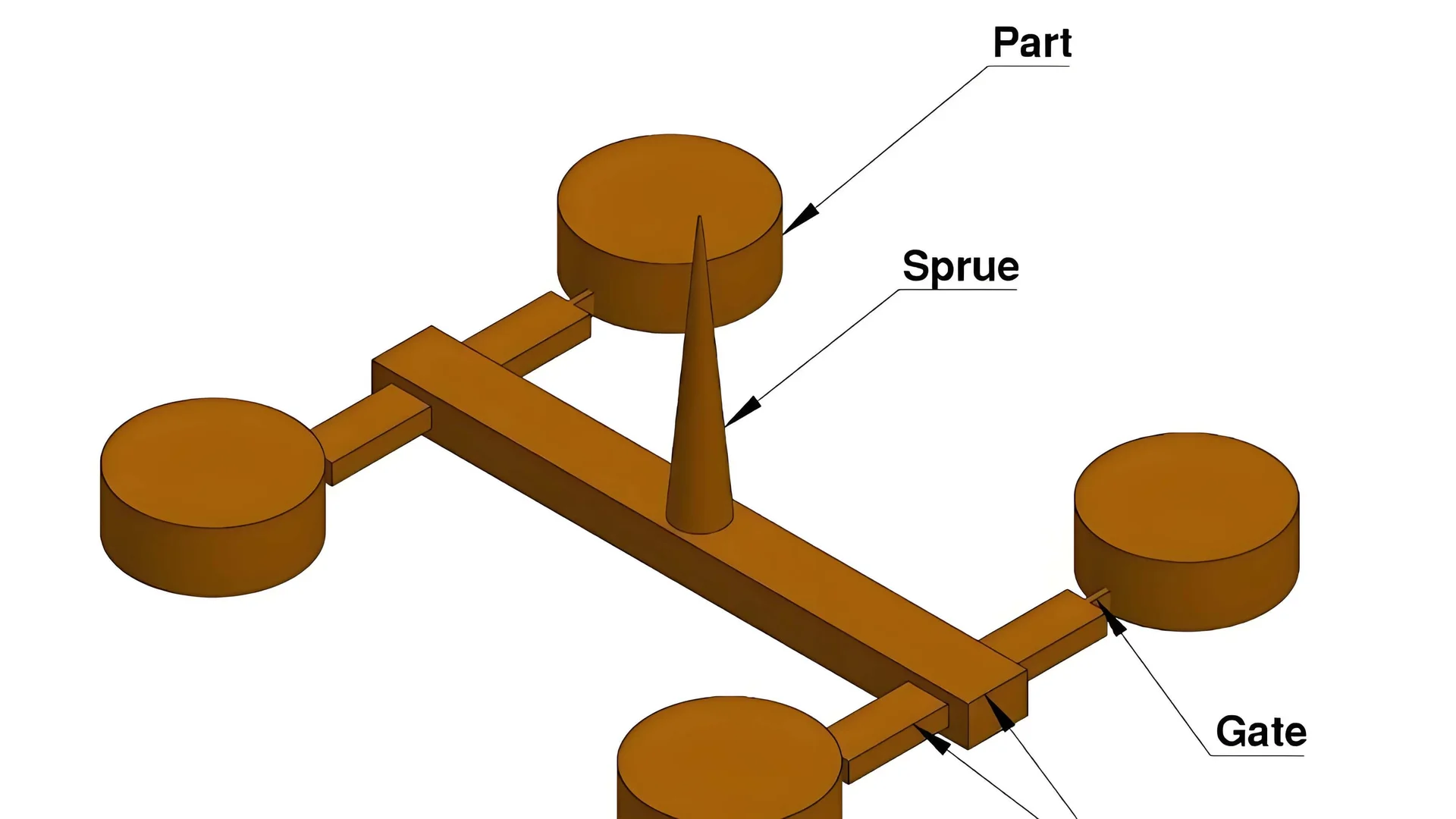
Comprendre le rôle de la taille des coureurs
Le système de canaux dans le moulage par injection sert de chemin permettant au plastique fondu de se déplacer de l'unité d'injection à la cavité du moule. La taille du canal affecte directement l’efficacité et l’uniformité du plastique dans le remplissage du moule. Un canal 1 peut entraîner plusieurs problèmes qui ont un impact sur la qualité du produit.
-
Coulisses trop épaisses : Si une coulisse est trop épaisse, le plastique fondu restera plus longtemps dans la coulisse. Ce temps de séjour prolongé peut conduire à un refroidissement excessif, voire à une dégradation thermique du matériau avant qu'il n'atteigne la cavité. Par exemple, lors de la fabrication de petits articles à parois minces, un canal trop épais peut provoquer un remplissage incomplet, entraînant des pénuries de matériaux et des défauts.
-
Couloirs trop fins : À l'inverse, des couloirs trop fins augmentent la résistance à l'écoulement de la matière fondue. Cela nécessite une pression d’injection plus élevée, ce qui entraîne une consommation d’énergie accrue et une usure potentielle des machines. De plus, les glissières fines peuvent provoquer des contraintes internes, entraînant des défauts tels que des déformations ou des fissures. Un exemple est lorsque des canaux minces provoquent un cisaillement excessif, entraînant une surchauffe, une décomposition et des défauts tels que des bulles ou des stries argentées dans le produit.
Stratégies pour un dimensionnement optimal des coureurs
Pour optimiser la taille des glissières, il est essentiel de prendre en compte des facteurs tels que les dimensions du produit, sa forme et l'épaisseur de la paroi. Généralement, le diamètre du canal doit être compris entre 1,5 et 2 fois l'épaisseur de la paroi du produit. Pour les produits plus grands ou plus épais, un canal plus grand peut être nécessaire, tandis que les produits plus petits ou plus fins bénéficient d'une taille de canal réduite.
L'utilisation d'un logiciel d'analyse de flux de moule peut aider à simuler différents scénarios de tailles de canaux afin de déterminer la conception optimale. Cette approche améliore non seulement la qualité du produit, mais réduit également le gaspillage de matériaux et les coûts de production.
Étude de cas : Ajustement de la taille des coureurs
Imaginons un scénario dans lequel une entreprise est confrontée à des problèmes de déformation de ses pièces moulées par injection. En analysant leur système de glissières, ils ont découvert que celles-ci étaient trop fines, ce qui entraînait un remplissage et une répartition inégale des contraintes. En ajustant la taille des canaux selon les recommandations des experts 2 , ils ont obtenu un remplissage plus cohérent, réduit le stress et amélioré la qualité globale du produit.
Grâce à une conception et une analyse réfléchies des canaux, les fabricants peuvent améliorer considérablement les performances et la fiabilité de leurs produits. S'assurer que la taille des canaux correspond aux exigences spécifiques du produit est une étape essentielle vers l'obtention de résultats de fabrication optimaux.
Les patins épais réduisent le risque de dégradation du matériau.FAUX
Les canaux épais peuvent provoquer un refroidissement excessif, entraînant une dégradation.
Les canaux fins augmentent les besoins en pression d'injection.Vrai
Les canaux minces augmentent la résistance à l'écoulement, nécessitant une pression plus élevée.
Quelles sont les meilleures pratiques pour concevoir des formes de canaux d’écoulement ?
La conception de la forme des canaux d'écoulement est cruciale dans le moulage, affectant à la fois l'efficacité et la qualité du produit final.
Les meilleures pratiques pour concevoir des formes de canaux d'écoulement incluent l'utilisation de transitions en arc dans les coins et la garantie de formes de section transversale régulières pour faciliter un écoulement de matière fondu doux et uniforme.
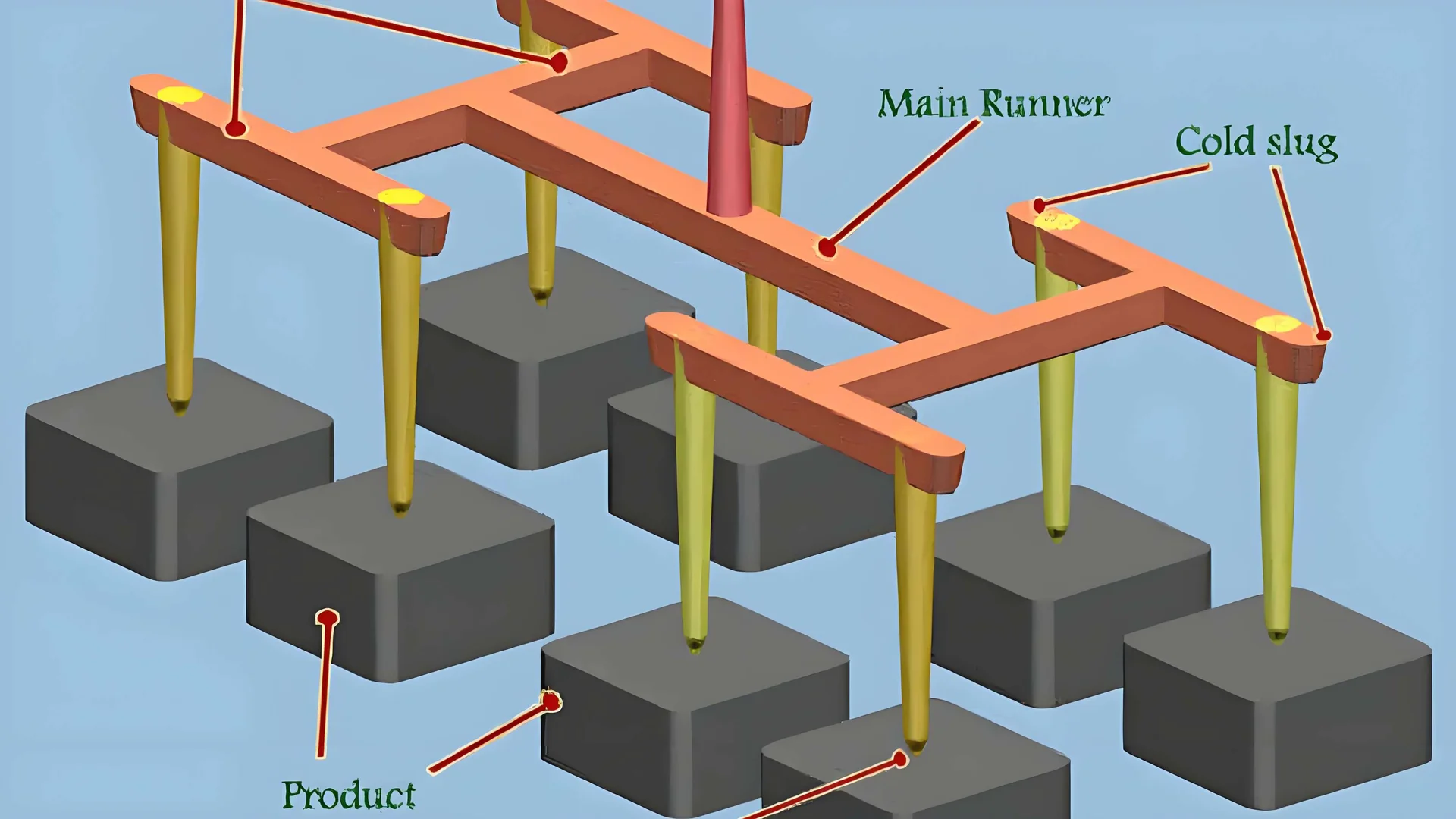
Importance de la forme du canal d'écoulement
La conception de la forme d'un canal d'écoulement peut grandement influencer l'efficacité du processus de moulage par injection. Les formes des canaux d'écoulement affectent la façon dont le plastique fondu se déplace à travers le moule, influençant des facteurs tels que la pression, la température et l'uniformité de l'écoulement. Un canal d'écoulement bien conçu minimise les défauts tels que la déformation, les bulles d'air et les lignes de soudure.
Erreurs courantes et solutions
Les angles vifs et leur impact
Les angles vifs des canaux d'écoulement peuvent entraîner une augmentation des contraintes de cisaillement sur le matériau en fusion. Cela peut entraîner des températures plus élevées, provoquant la décomposition du plastique et créant des défauts indésirables comme des bulles ou des stries argentées.
- Solution : Implémenter les transitions d'arc 3 pour réduire les contraintes de cisaillement. Le rayon de ces arcs doit généralement être compris entre 0,25 et 0,5 fois le diamètre du canal.
Formes transversales irrégulières
Une section transversale irrégulière peut provoquer des vitesses d'écoulement inégales, entraînant des défauts tels que des variations locales d'épaisseur et des marques de soudure.
- Solution : Visez des sections transversales circulaires ou trapézoïdales pour favoriser un débit uniforme dans tout le système de canaux. Cette consistance aide à maintenir une transition en douceur de la masse fondue.
Analyse du flux de moule
L'utilisation d'un logiciel d'analyse de flux de moule permet aux concepteurs de simuler différentes configurations de canaux d'écoulement. En ajustant des paramètres tels que la forme, la taille et le rayon de l'arc, il est possible d'identifier la configuration optimale qui minimise le gaspillage de matériaux tout en préservant l'intégrité du produit.
- Exemple : Dans les productions à grande échelle, les simulations peuvent révéler à quel point de petits ajustements dans la forme des canaux peuvent avoir un impact significatif sur l'efficacité et la qualité globales de la production.
Considération des matériaux
Les propriétés du matériau plastique utilisé sont également un facteur critique pour déterminer la meilleure forme de canal d'écoulement. Différents matériaux peuvent nécessiter des conceptions de canaux uniques pour optimiser leurs caractéristiques d'écoulement sans compromettre la qualité du produit.
- Considération : Certains plastiques peuvent nécessiter des transitions plus douces en raison de leur viscosité et de leur sensibilité thermique.
Conclusion
En intégrant ces meilleures pratiques, telles que l'utilisation de transitions en arc et le maintien de formes transversales régulières, les fabricants peuvent améliorer les performances de leurs moules à injection. De plus, l’analyse du flux de moule permet une personnalisation précise adaptée aux besoins de production spécifiques. Cela améliore non seulement la qualité du produit, mais réduit également les coûts en minimisant les défauts et le gaspillage de matériaux.
Les transitions d'arc réduisent les contraintes de cisaillement dans les canaux d'écoulement.Vrai
Les transitions d'arc lissent les angles vifs, réduisant ainsi les contraintes et les défauts.
Les sections transversales irrégulières favorisent un écoulement uniforme de la matière fondue.FAUX
Les formes irrégulières provoquent un écoulement irrégulier, entraînant des défauts tels que des marques de soudure.
Pourquoi la position de la porte est-elle critique dans la conception des coureurs ?
La position de la porte dans la conception du canal est essentielle, car elle influence le débit, la qualité et l'efficacité des processus de moulage par injection.
Le caractère critique de la position de la porte dans la conception des canaux découle de son impact direct sur le modèle de remplissage, la qualité du produit et l'efficacité de la production. Un positionnement correct de la porte garantit un remplissage uniforme de la cavité, minimise la concentration des contraintes et réduit les défauts, conduisant à des produits de meilleure qualité et à une fabrication optimisée.
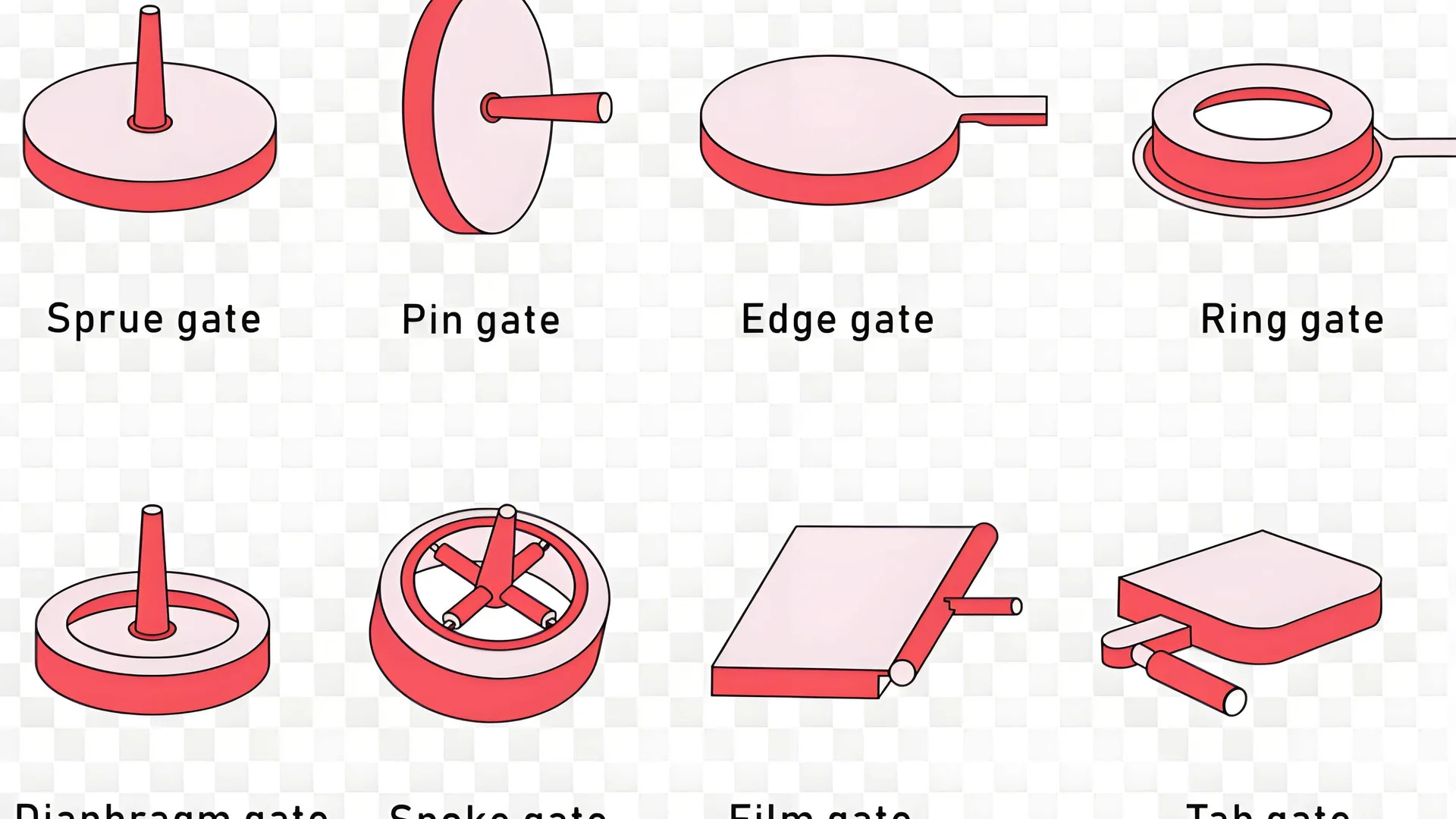
Impact sur le modèle de remplissage
L'emplacement de la porte détermine la manière dont le matériau fondu remplit la cavité. Une porte stratégiquement placée garantit un modèle de remplissage uniforme, ce qui est essentiel pour maintenir une qualité constante du produit. En plaçant la porte sur une section plus épaisse du produit ou à un emplacement central, les fabricants peuvent obtenir une répartition plus uniforme du matériau. Cette approche permet de minimiser les défauts tels que les lignes de soudure et les pièges à air.
Par exemple, si la porte est positionnée sur une section plus fine du moule, il existe un risque de remplissage incomplet ou de répartition inégale de la pression. Cela peut entraîner des concentrations de contraintes susceptibles de provoquer des déformations ou des fissures sous charge.
Influence sur la qualité du produit
Le positionnement de la porte joue un rôle crucial dans la définition des propriétés mécaniques et de l'état de surface du produit moulé. Une porte mal positionnée peut entraîner une contrainte de cisaillement excessive sur le matériau, entraînant une dégradation et des défauts comme une décoloration ou une fragilité.
À l'aide d'un logiciel d'analyse de flux de moule 4 , les concepteurs peuvent simuler différentes positions de portes pour évaluer leur impact sur le produit final. Cet outil aide à prédire les problèmes potentiels tels que les pénuries de matériaux ou le suremballage, permettant ainsi des ajustements avant le début de la production réelle.
Considérations sur l’efficacité de la production
L'efficacité du processus de moulage par injection est considérablement influencée par l'emplacement des portes. Le positionnement optimal de la porte réduit le temps de cycle en garantissant un remplissage plus rapide et plus efficace, économisant ainsi de l'énergie et des ressources. De plus, il minimise les exigences de post-traitement en réduisant le flash et autres artefacts indésirables.
Par exemple, une porte située au centre peut conduire à un remplissage équilibré de moules multi-empreintes, évitant ainsi les écarts de poids et de dimensions des produits. Cela facilite également l’éjection des pièces, améliorant ainsi le débit global de production.
En résumé, l'évaluation de la position de la porte grâce à une analyse 5 ne consiste pas seulement à améliorer la qualité du produit, mais également à optimiser l'ensemble du processus de fabrication. Des considérations de conception appropriées garantissent que chaque élément du système de canaux fonctionne harmonieusement pour une production efficace.
La position de la porte affecte la qualité du moulage par injection.Vrai
La position de la porte influence les modèles de remplissage, la répartition des contraintes et les défauts.
Les portes situées au centre entraînent un remplissage inégal.FAUX
Les portes situées au centre assurent un remplissage équilibré et réduisent les défauts.
Comment atteindre l’équilibre des canaux dans les moules multi-empreintes ?
L’équilibrage des canaux dans les moules multi-empreintes est crucial pour garantir une qualité de produit uniforme et des processus de fabrication efficaces.
Pour parvenir à l’équilibre des canaux dans les moules multi-empreintes, il faut concevoir des longueurs, des formes et des tailles de canaux cohérentes dans toutes les cavités. L'ajustement des débits de matière fondue à l'aide de vannes d'étranglement ou la modification de la taille des vannes peuvent également contribuer à garantir une distribution uniforme.
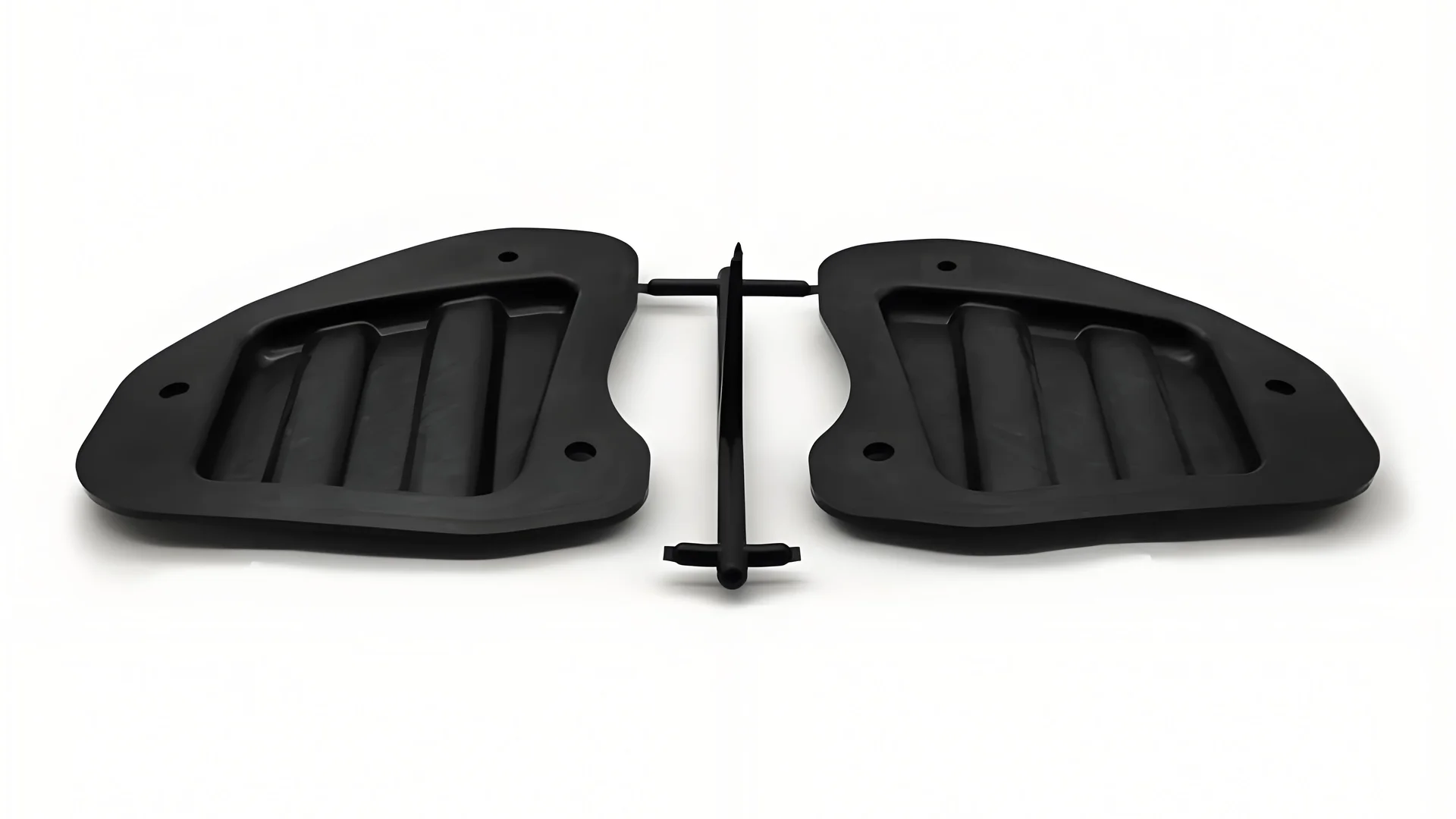
Importance de l’équilibre du coureur
Dans les moules multi-empreintes, l’équilibre des canaux est fondamental pour maintenir une qualité de produit constante dans toutes les empreintes. Un système de canaux déséquilibré peut entraîner des variations dans les dimensions, le poids et les performances du produit, affectant finalement l'efficacité de la production et augmentant les coûts.
Lorsque le canal d'une cavité est plus long ou plus fin que les autres, la résistance à l'écoulement de la matière fondue augmente, ce qui ralentit la vitesse de remplissage et peut provoquer des défauts tels qu'un manque de matériau. Pendant ce temps, les produits présents dans d’autres cavités peuvent se remplir correctement, entraînant une disparité de qualité.
Considérations de conception pour les coureurs équilibrés
Pour garantir des coureurs équilibrés, il est essentiel de maintenir une cohérence dans la longueur, la forme transversale et la taille 6 pour chaque cavité. L’objectif est de permettre à la matière fondue de se répartir uniformément dans toutes les cavités.
Longueur et forme des coureurs
En gardant les longueurs de canal uniformes, vous minimisez les écarts de résistance à l'écoulement. Si des différences inévitables existent en raison de la forme du produit ou de la structure du moule, envisagez d'utiliser une disposition symétrique lorsque cela est possible. De plus, les sections transversales rondes ou trapézoïdales sont préférées pour un écoulement de matière fondue plus fluide et plus uniforme.
Aspect conception | Meilleure pratique |
---|---|
Longueur du coureur | Cohérent dans toutes les cavités |
Forme en coupe transversale | Circulaire ou trapézoïdal pour un débit uniforme |
Ajustements | Utiliser des papillons ou modifier la taille des vannes |
Utilisation des papillons des gaz et des modifications des portes
Lorsqu'un équilibre parfait ne peut être atteint uniquement par la conception, incorporez des papillons d'étranglement dans les glissières. Ces dispositifs aident à affiner le débit de fusion en fournissant une résistance réglable, garantissant que chaque cavité se remplit à une vitesse optimale.
Une autre stratégie efficace consiste à ajuster la taille des portes. En modifiant les dimensions de la porte, vous pouvez contrôler le flux de matière fondue dans chaque cavité, équilibrant la vitesse de remplissage et assurant une distribution uniforme.
Simulation de conceptions de coureurs
L'utilisation d'un logiciel d'analyse de flux de moule est inestimable pour simuler diverses conceptions et configurations de canaux. Cet outil permet aux concepteurs de visualiser les déséquilibres potentiels et de tester les ajustements avant le début de la production réelle.
Les simulations peuvent également fournir des informations sur la manière dont des modifications telles que des changements de vannes d'étranglement ou de taille de porte auront un impact sur l'équilibre et l'efficacité globale du système de moule. En tirant parti de ces technologies, vous pouvez améliorer la précision et l'efficacité de vos conceptions de canaux, en optimisant à la fois la qualité des produits et l'efficacité de la fabrication.
Des longueurs de glissière constantes garantissent une qualité de produit uniforme.Vrai
Les longueurs uniformes des canaux minimisent la résistance à l'écoulement, garantissant un remplissage uniforme.
Les vannes d'étranglement augmentent la résistance à l'écoulement de la matière fondue dans les canaux.FAUX
Les papillons des gaz ajustent les débits mais n’augmentent pas intrinsèquement la résistance.
Conclusion
En mettant en œuvre ces stratégies, vous pouvez améliorer considérablement votre processus de moulage par injection, garantissant ainsi des produits de meilleure qualité et des opérations efficaces.
-
Découvrez l'impact de la taille des canaux sur l'efficacité du moulage par injection. De plus, un canal de petit diamètre augmentera la pression de remplissage. Dimensionnez le canal trop grand et le moule reste là, attendant que le canal gèle… ↩
-
Découvrez comment l'analyse du flux de moule contribue à l'optimisation de la conception des canaux. : L'analyse du flux de moule est une simulation logicielle qui prédit comment une résine plastique s'écoulera dans et remplira un moule d'injection. ↩
-
Découvrez comment les transitions en arc réduisent les contraintes de cisaillement et améliorent l'efficacité de l'écoulement. : Il y a une transition en arc à la racine du raidisseur. La concentration de contraintes à la racine et à l'entrée peut être évitée lorsque les forces externes sont… ↩
-
Apprenez à simuler les positions des portes pour une conception optimale des canaux. : L'analyse du flux de moule est un logiciel de simulation qui peut montrer comment la résine remplira le moule pendant le processus de moulage par injection. En comprenant le remplissage des matériaux,… ↩
-
Découvrez comment le placement des portes affecte l'efficacité de la fabrication. : Les portes sont essentielles au système de moulage par injection et leurs types et tailles affectent directement la qualité des produits et les coûts. ↩
-
Explorez les techniques de conception de systèmes de canaux uniformes et efficaces. : Utilisez une analyse de l'équilibre des canaux pour optimiser la disposition des canaux et garantir une répartition uniforme du plastique dans les cavités du moule. Cette analyse permet d’identifier… ↩