El moldeo por inyección no se trata sólo de llenar un molde; se trata de crear la perfección en medio de desafíos invisibles.
Las tensiones internas en los productos moldeados por inyección resultan del flujo desigual, el enfriamiento y la contracción durante el proceso de moldeo. Estas tensiones pueden provocar cambios dimensionales, fallas mecánicas y defectos estéticos, afectando la calidad y el rendimiento del producto.
Si bien comprender los conceptos básicos de las tensiones internas es crucial, profundizar en sus causas y efectos puede ofrecer información valiosa para mitigar problemas potenciales. Exploremos estos aspectos más a fondo para mejorar la confiabilidad del producto y la eficiencia de fabricación.
El desequilibrio del flujo provoca tensión interna en el moldeo por inyección.Verdadero
El desequilibrio del flujo conduce a una velocidad y presión desiguales, lo que provoca estrés.
- 1. ¿Cuáles son las causas principales de la tensión interna en el moldeo por inyección?
- 2. ¿Cómo afectan las tensiones internas a las propiedades mecánicas de los productos?
- 3. ¿Qué defectos de apariencia pueden resultar del estrés interno?
- 4. ¿Cómo se puede minimizar la tensión interna durante el moldeo por inyección?
- 5. Conclusión
¿Cuáles son las causas principales de la tensión interna en el moldeo por inyección?
La tensión interna en el moldeo por inyección surge de factores como el desequilibrio del flujo, el enfriamiento desigual y la orientación molecular.
Las causas principales de la tensión interna en el moldeo por inyección incluyen el desequilibrio del flujo, el enfriamiento desigual y la orientación molecular, que ocurren debido a inconsistencias en el proceso y el diseño. Estas tensiones pueden comprometer la integridad estructural y la apariencia de los productos moldeados.
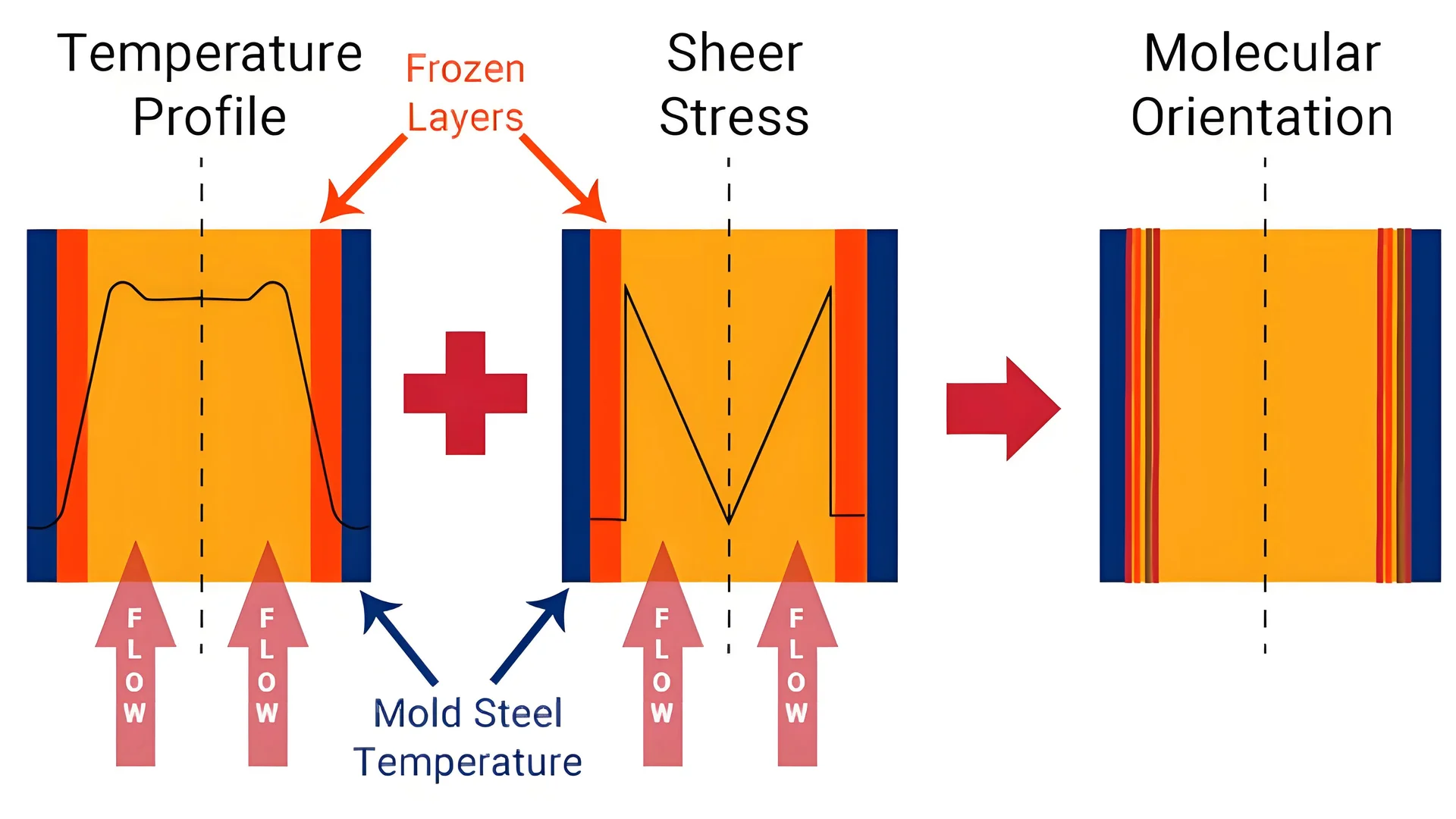
Desequilibrio de flujo
Durante el proceso de moldeo por inyección, el plástico fundido no siempre fluye uniformemente dentro de la cavidad del molde. Esta discrepancia se debe principalmente a variaciones en la velocidad del flujo y la distribución de presión. Por ejemplo, cerca de la puerta por donde entra el plástico, la masa fundida fluye más rápido en comparación con áreas más alejadas. Este desequilibrio genera tensión de corte dentro del producto.
Los diseños de moldes poco razonables, como puertas mal colocadas o guías de tamaño inadecuado, exacerban este desequilibrio. Al perfeccionar estos elementos de diseño, se puede reducir significativamente la tensión inducida por las discrepancias de flujo.
Enfriamiento desigual
La fase de enfriamiento es crucial para definir las propiedades finales de un producto moldeado por inyección. Si ciertas áreas se enfrían más rápido que otras, se introduce estrés térmico. A ello contribuyen factores como la temperatura inconsistente del molde y los canales de refrigeración mal diseñados.
El espesor desigual de las paredes también influye. Las secciones más gruesas se enfrían más lentamente que las más delgadas, lo que genera tensión interna. Un enfoque de diseño estratégico, centrado en un espesor de pared uniforme, puede mitigar este problema.
Orientación molecular
A medida que el plástico fundido fluye a través del molde, sus moléculas se alinean en la dirección del flujo. Esta alineación puede provocar tensiones de orientación, que se encuentran predominantemente a lo largo de la dirección del flujo y menos perpendicularmente a ella.
Los parámetros del proceso, como la velocidad de inyección y la presión de mantenimiento, impactan directamente en la orientación molecular. Por ejemplo, una velocidad de inyección o una presión de mantenimiento excesivamente altas pueden amplificar la tensión de orientación. Ajustar estos parámetros ayuda a gestionar el grado de orientación molecular de forma eficaz.
Análisis comparativo: causas del estrés interno
Causa | Descripción | Estrategia de mitigación |
---|---|---|
Desequilibrio de flujo | Distribución desigual de velocidad y presión dentro de la cavidad del molde. | Optimice la posición de la puerta y el tamaño del corredor. |
Enfriamiento desigual | Velocidades de enfriamiento diferenciales que conducen a estrés térmico. | Temperatura uniforme del molde; Mejor diseño de canales. |
Orientación molecular | Alineación de moléculas que causan tensión en la dirección del flujo. | Controle la velocidad de inyección y la presión de mantenimiento. |
Comprender estas causas fundamentales es fundamental para cualquier persona involucrada en la optimización del moldeo por inyección 1 . Al identificar y abordar estos factores, los fabricantes pueden mejorar la calidad del producto y extender su ciclo de vida.
El desequilibrio del flujo provoca tensión cortante en los productos moldeados.Verdadero
El desequilibrio del flujo crea una presión desigual, lo que genera tensión cortante.
El espesor uniforme de la pared aumenta la tensión interna en la moldura.FALSO
El espesor uniforme de la pared reduce el estrés térmico, no lo aumenta.
¿Cómo afectan las tensiones internas a las propiedades mecánicas de los productos?
Las tensiones internas en los productos pueden comprometer gravemente sus propiedades mecánicas, influyendo en su resistencia y durabilidad.
Las tensiones internas pueden degradar las propiedades mecánicas de los productos al provocar cambios dimensionales, reducir la resistencia y promover fallas bajo tensión.
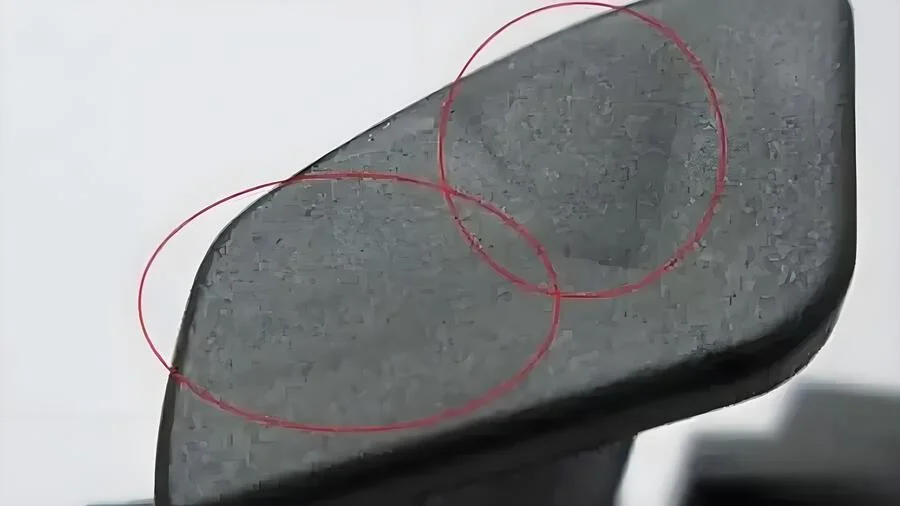
Comprender el papel de las tensiones internas
Las tensiones internas en los productos moldeados por inyección se generan debido a desequilibrios de flujo, enfriamiento desigual y orientación molecular durante el proceso de fabricación. Estas tensiones pueden manifestarse de diversas formas, incluidas tensiones cortantes, tensiones térmicas y tensiones de orientación. Cada tipo contribuye de forma única a alterar las características mecánicas de un producto.
Desafíos de estabilidad dimensional
Las tensiones internas a menudo provocan cambios dimensionales posteriores a la fabricación. A medida que estas tensiones se relajan con el tiempo, los productos pueden experimentar deformaciones o encogimientos, lo que afecta no solo la apariencia sino también la funcionalidad. Por ejemplo, un ajuste incorrecto 2 en operaciones de montaje puede resultar de incluso ligeras desviaciones dimensionales.
Factor | Impacto en las dimensiones |
---|---|
Desequilibrio de flujo | Contracción desigual, deformación |
Enfriamiento desigual | Expansión o contracción localizada |
Orientación molecular | Contracción diferencial en la dirección del flujo. |
Degradación de propiedades mecánicas
Las tensiones internas afectan directamente las propiedades mecánicas como la resistencia, la tenacidad y la resistencia a la fatiga. Cuando estas tensiones se concentran en áreas específicas, pueden convertirse en puntos de debilidad. En consecuencia, los productos pueden fallar prematuramente bajo cargas mecánicas, particularmente si se someten a fuerzas repetitivas o dinámicas.
Por ejemplo, los componentes automotrices fabricados mediante moldeo por inyección deben soportar una tensión significativa a lo largo del tiempo. Las concentraciones de tensiones internas pueden provocar grietas 3 o fracturas bajo carga, comprometiendo la seguridad y el rendimiento.
Factores que influyen en las propiedades mecánicas
- Características del material : Los diferentes plásticos exhiben distintos grados de susceptibilidad al estrés interno. Por ejemplo, los plásticos amorfos pueden reaccionar de manera diferente a los cristalinos cuando se exponen a tensiones internas.
- Parámetros de fabricación : la elección de la velocidad de inyección, los ajustes de presión y las velocidades de enfriamiento influyen significativamente en el grado de formación de tensiones internas. La optimización de estos parámetros puede ayudar a mitigar los efectos adversos.
Estrategias de mitigación
Para preservar las propiedades mecánicas de los productos moldeados por inyección, los fabricantes pueden:
- Optimice el diseño del molde : esto incluye la ubicación estratégica de compuertas y canales de enfriamiento para promover un flujo y enfriamiento uniformes.
- Ajustes de proceso : el ajuste fino de la velocidad y la presión de inyección ayuda a reducir el estrés de orientación molecular. La implementación de una inyección de múltiples etapas también puede aliviar las tensiones inducidas por el flujo.
- Técnicas de posprocesamiento : técnicas como el recocido pueden relajar las tensiones internas, mejorando la estabilidad mecánica con el tiempo.
Comprender estas estrategias es crucial para mejorar la longevidad y confiabilidad del producto y al mismo tiempo minimizar posibles fallas debido a tensiones internas.
Las tensiones internas provocan que el producto se deforme con el tiempo.Verdadero
Las tensiones internas se relajan, lo que provoca cambios dimensionales como deformaciones.
Todos los plásticos se ven igualmente afectados por las tensiones internas.FALSO
Los diferentes plásticos tienen diferentes susceptibilidades al estrés interno.
¿Qué defectos de apariencia pueden resultar del estrés interno?
La tensión interna en los productos moldeados por inyección puede provocar defectos antiestéticos que comprometan tanto la estética como la funcionalidad.
La tensión interna puede provocar diversos defectos de apariencia en los productos moldeados por inyección, como grietas, vetas plateadas y burbujas. Estos problemas no sólo perjudican el atractivo visual del producto sino que también pueden afectar su integridad estructural.
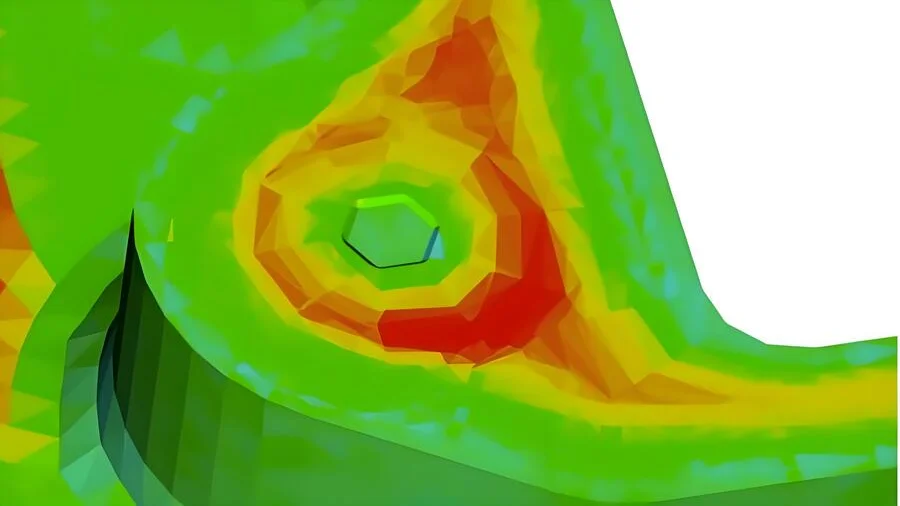
Comprender el estrés interno
La tensión interna surge durante el proceso de moldeo por inyección cuando el plástico fundido experimenta un flujo desigual, enfriamiento y contracción. Este estrés se manifiesta en defectos que afectan la calidad visual del producto.
Defectos de apariencia comunes
-
Grietas:
- Las grietas suelen aparecer debido a una elevada tensión interna que se concentra en zonas específicas. Pueden ocurrir durante o después del desmolde.
- Factores como el diseño inadecuado del molde o las rápidas velocidades de enfriamiento exacerban la formación de grietas.
-
Rayas plateadas:
- Estas son líneas onduladas y plateadas que se ven en la superficie, causadas por la humedad o el aire atrapado dentro del material durante el moldeo.
- Las vetas plateadas son particularmente notables en productos transparentes y afectan la claridad y el atractivo estético.
-
Burbujas:
- Ocurre cuando se forman bolsas de gas o aire dentro del producto, generalmente debido al enfriamiento rápido o al alto contenido de humedad en el plástico.
- Las burbujas comprometen tanto la apariencia como potencialmente las propiedades mecánicas del producto.
Factores que contribuyen a los defectos de apariencia
Diseño de moldes y parámetros de proceso
- Desequilibrio del flujo: la distribución desigual del flujo de plástico fundido puede provocar defectos como grietas y burbujas 4 .
- Velocidad de enfriamiento: el enfriamiento inconsistente causa estrés térmico, lo que contribuye a defectos como deformaciones y rayas plateadas.
- Orientación molecular: los niveles altos de orientación durante velocidades de inyección rápidas aumentan la probabilidad de que se formen vetas plateadas.
Soluciones para mitigar los defectos de apariencia
- Optimice los diseños de moldes ajustando las posiciones de las compuertas y garantizando un flujo equilibrado.
- Utilice procesos de inyección de varias etapas para gestionar la orientación molecular y reducir el estrés.
- Implemente diseños de canales de enfriamiento adecuados para garantizar un enfriamiento uniforme en todo el producto.
Al abordar estos factores, los fabricantes pueden reducir significativamente los defectos de apariencia en los productos moldeados por inyección, mejorando tanto la calidad estética como el rendimiento.
Las grietas en los productos resultan del enfriamiento rápido.Verdadero
El enfriamiento rápido provoca una distribución desigual de la tensión, lo que provoca grietas.
Las rayas plateadas son causadas por un calor excesivo.FALSO
Las rayas plateadas son el resultado de la humedad o el aire atrapados, no del calor.
¿Cómo se puede minimizar la tensión interna durante el moldeo por inyección?
Minimizar la tensión interna en el moldeo por inyección es crucial para garantizar la durabilidad y el atractivo estético del producto. Las estrategias efectivas implican optimizar el diseño del molde, ajustar los parámetros del proceso e implementar técnicas de posprocesamiento.
Para minimizar la tensión interna en el moldeo por inyección, optimice el diseño del molde, ajuste los parámetros de procesamiento como la velocidad y la presión de inyección y utilice métodos de posprocesamiento como el recocido. Estos pasos ayudan a equilibrar el flujo, el enfriamiento y la orientación molecular, reduciendo posibles defectos y mejorando la calidad del producto.
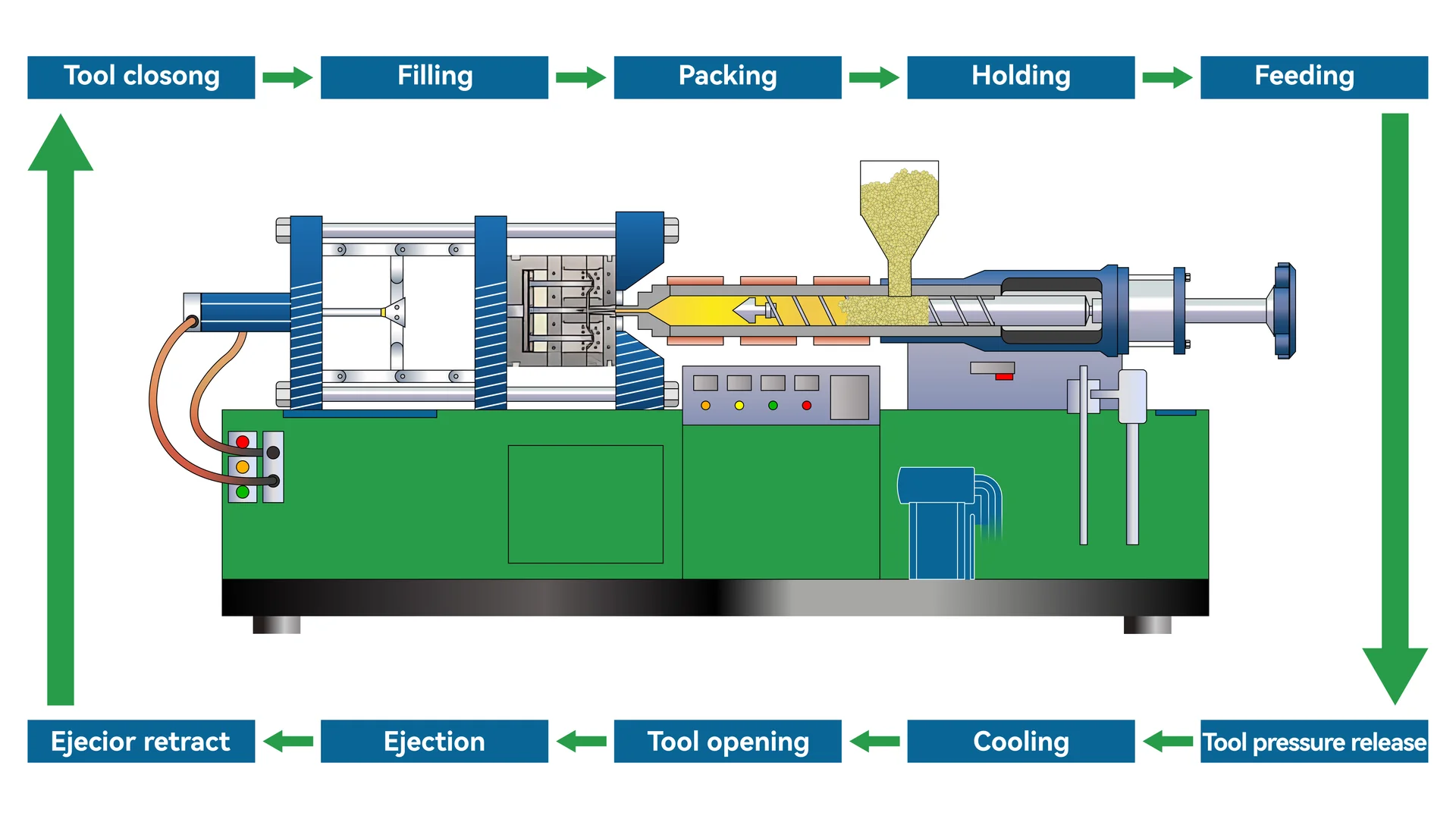
Optimizar el diseño del molde
Una de las principales formas de reducir la tensión interna es mediante un diseño cuidadoso del molde. Al colocar compuertas estratégicamente y utilizar múltiples sistemas de compuertas, los fabricantes pueden lograr un flujo más equilibrado del plástico fundido, lo que evita la acumulación de tensiones cortantes. Un diseño bien pensado también incluye la optimización de los tamaños y formas de los canales para minimizar la resistencia y garantizar un flujo uniforme a través del molde.
Además, es vital disponer canales de enfriamiento para facilitar un enfriamiento uniforme. Por ejemplo, un producto con espesor de pared variable puede beneficiarse de un diseño de espesor de pared gradual 5 , que ayuda a mantener velocidades de enfriamiento constantes y minimiza el estrés térmico.
Ajustar los parámetros del proceso de moldeo por inyección
Los parámetros del proceso tienen un impacto significativo en los niveles de tensión interna dentro de un producto moldeado por inyección. Reducir la velocidad de inyección y mantener la presión puede disminuir el grado de orientación molecular, lo que genera menos tensión interna. Ampliar el tiempo de retención permite reducir las tasas de contracción, disminuyendo así el estrés.
Controlar las temperaturas (tanto del molde como del material fundido) también es crucial. Las altas temperaturas de fusión pueden aumentar la orientación molecular, por lo que es esencial seleccionar temperaturas apropiadas según el tipo de material. La implementación de un proceso de inyección de múltiples etapas puede ayudar aún más a controlar el estrés al ajustar gradualmente la velocidad y la presión a lo largo del ciclo de moldeo.
Parámetro | Ajuste sugerido |
---|---|
Velocidad de inyección | Baje para reducir el estrés de orientación. |
Mantener la presión | Baje para minimizar la contracción |
Temperatura del molde | Optimice para un enfriamiento uniforme |
Temperatura de fusión | Ajustar según las necesidades materiales. |
Técnicas de posprocesamiento
Las técnicas de posprocesamiento, como el recocido, pueden aliviar significativamente las tensiones internas en los productos moldeados por inyección. El recocido implica calentar el producto a una temperatura específica, mantenerlo durante un período determinado y luego enfriarlo lentamente. Este proceso relaja la estructura molecular, reduciendo efectivamente el estrés.
Para productos que requieren alta precisión dimensional, se puede aplicar acondicionamiento de humedad. Al colocar el producto en un ambiente de humedad controlada, absorbe la humedad, lo que ayuda a ajustar la contracción y aliviar el estrés.
Estas técnicas en conjunto garantizan que el producto final cumpla con los estándares de calidad y funcione de manera confiable en la aplicación prevista. La implementación de tales medidas no sólo mejora la durabilidad sino que también extiende la vida útil del producto.
La optimización del diseño del molde reduce la tensión interna.Verdadero
La ubicación estratégica de la compuerta y el diseño del canal de enfriamiento equilibran el flujo y el enfriamiento.
Una mayor velocidad de inyección disminuye la tensión interna.FALSO
Una mayor velocidad aumenta la orientación molecular, lo que aumenta la tensión interna.
Conclusión
Al abordar las tensiones internas mediante el diseño estratégico de moldes y ajustes de procesos, los fabricantes pueden mejorar significativamente la calidad del producto. Adopte estas estrategias para minimizar los defectos y optimizar el rendimiento.
-
Explore estrategias para mejorar la calidad del producto a través de la optimización de procesos: Mejores prácticas para optimizar su proceso de moldeo por inyección · 1. Monitoreo y ajuste periódico de los parámetros · 2. Uso de sistemas de control avanzados · 3. Minucioso… ↩
-
Descubra cómo los cambios menores inducidos por la tensión afectan la precisión del ensamblaje: un cambio local de la deformación durante el conformado en frío podría causar un estado de tensión y una rigidez diferentes en el producto. Esto puede mejorar o disminuir... ↩
-
Descubra por qué las tensiones internas causan grietas bajo carga: (1) La existencia de tensiones internas en el producto afectará gravemente las propiedades mecánicas y el rendimiento del producto; debido a la… ↩
-
Aprenda técnicas para evitar defectos comunes en productos moldeados: cuando los métodos de ventilación convencionales fallan, la ventilación por vacío puede resolver eficazmente los problemas relacionados con la desgasificación y el atrapamiento de aire en los moldes de inyección. ↩
-
Descubra cómo el diseño de espesor de pared gradual mejora la uniformidad del enfriamiento. Calidad de la pieza: el diseño de piezas moldeadas por inyección con problemas de espesor de pared puede provocar defectos como sumideros, deformaciones y disparos cortos. Estos problemas… ↩