Los problemas de desmoldeo pueden parecer una montaña insuperable, pero te aseguro que ¡hay una manera de superarla!
Para resolver los problemas de desmolde en el moldeo por inyección complejo, los fabricantes deben optimizar el diseño del molde, ajustar los procesos de inyección, mejorar la calidad de la superficie del molde y utilizar mecanismos de desmolde adecuados.
Si bien esta breve descripción general proporciona un punto de partida, los conocimientos detallados y las estrategias de expertos que se analizan a continuación ofrecen un enfoque integral para superar estos desafíos de manera efectiva.
La optimización del diseño del molde facilita el desmolde en estructuras complejas.Verdadero
El diseño eficaz del molde reduce la fricción y evita daños al producto durante el desmolde.
- 1. ¿Cómo afecta el diseño de moldes al desmolde en estructuras complejas?
- 2. ¿Qué papel juega el proceso de moldeo por inyección en el éxito del desmoldeo?
- 3. ¿Por qué es crucial la calidad de la superficie del molde para un desmolde sin problemas?
- 4. ¿Qué mecanismos de desmoldeo son mejores para productos moldeados complejos?
- 5. Conclusión
¿Cómo afecta el diseño de moldes al desmolde en estructuras complejas?
El diseño del molde influye profundamente en la facilidad de desmolde en estructuras complejas, lo que afecta la integridad del producto y la eficiencia de la producción. Profundicemos en los matices.
El diseño eficaz de moldes en estructuras complejas garantiza un desmolde más fácil al optimizar las pendientes, evitar estructuras difíciles y tener en cuenta la contracción del material.
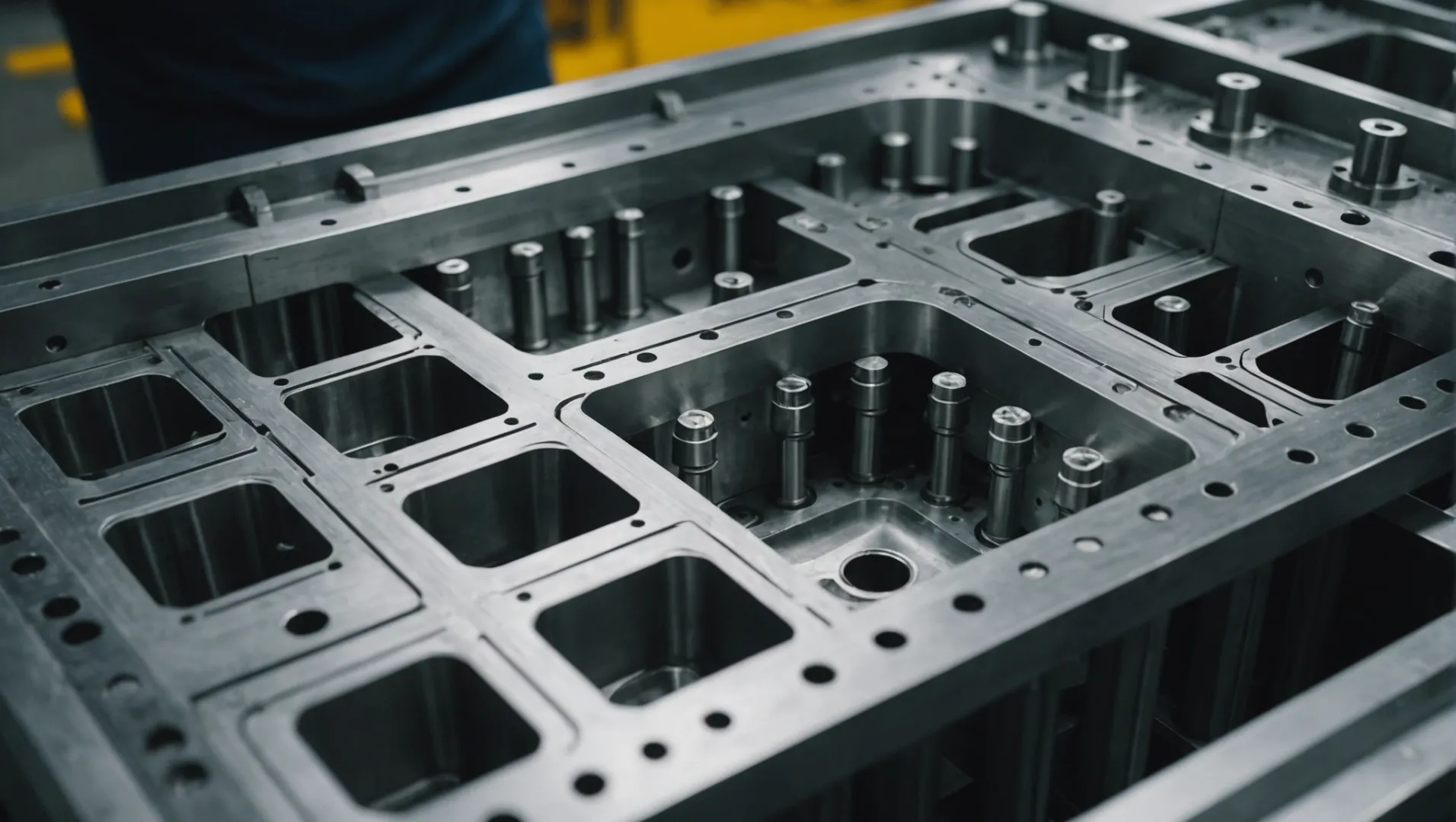
Comprender los desafíos del diseño de moldes
El diseño de un molde influye directamente en cómo se desmoldará un producto durante la fase de desmolde. En estructuras complejas, esto se vuelve aún más crítico. Algunos diseños se ajustan demasiado al producto, lo que aumenta la fricción y dificulta el desmolde.
- Cavidades profundas y socavaduras : estas características pueden atrapar el producto dentro del molde, lo que requiere una fuerza significativa para liberarlo, lo que puede dañar tanto el molde como el producto.
- Contracción del material : A medida que el producto se enfría, se encoge, a menudo envolviéndose firmemente alrededor de los núcleos del molde.
Optimización del diseño de moldes para un mejor desmolde
Para abordar estos problemas, se pueden implementar varias estrategias:
-
Optimización de pendientes de desmolde
- Aumentar la pendiente de desmolde generalmente facilita el desmolde. Para diseños complejos, la pendiente debe adaptarse a las complejidades específicas del producto.
-
Evitar estructuras difíciles
- Mientras diseña, evite cavidades profundas y socavaciones siempre que sea posible. Si es inevitable, implemente mecanismos como controles deslizantes o tapas inclinadas para facilitar la liberación.
-
Contabilización de la contracción
- Durante la fase de diseño, considere la tasa de contracción de los materiales. Asigne márgenes adecuados para evitar que el producto se adhiera demasiado después del enfriamiento.
Característica | Desafío | Solución |
---|---|---|
Cavidades Profundas | Producto trampas | Utilice controles deslizantes o tapas inclinadas. |
Contracción | Post-enfriamiento ajustado | Márgenes de contracción de reservas |
Equilibrando la innovación con la practicidad
Si bien los diseños innovadores son esenciales para una ventaja competitiva, deben equilibrarse con consideraciones prácticas para la eficiencia de fabricación. Por ejemplo, los diseños de moldes innovadores 1 siempre deben incorporar un análisis de viabilidad para los procesos de desmoldeo.
Al comprender y aplicar a fondo estos principios de diseño, los fabricantes pueden reducir significativamente los problemas comunes del desmolde, como la deformación, los rayones y la adhesión.
El aumento de la pendiente de desmolde facilita la liberación del producto.Verdadero
Una mayor pendiente reduce la fricción y facilita la liberación del producto.
Las cavidades profundas siempre mejoran la eficiencia del molde.FALSO
Las cavidades profundas pueden atrapar productos, lo que hace que el desmolde sea difícil e ineficiente.
¿Qué papel juega el proceso de moldeo por inyección en el éxito del desmoldeo?
El proceso de moldeo por inyección tiene un impacto complejo en el éxito del desmolde, lo que influye en la integridad del producto y la eficiencia de la producción. Descubra cómo los ajustes estratégicos pueden mejorar los resultados.
El éxito del desmolde en el moldeo por inyección depende de un control preciso de los parámetros del proceso como la presión, la velocidad y el tiempo de enfriamiento, lo que garantiza la integridad estructural y minimiza los defectos.
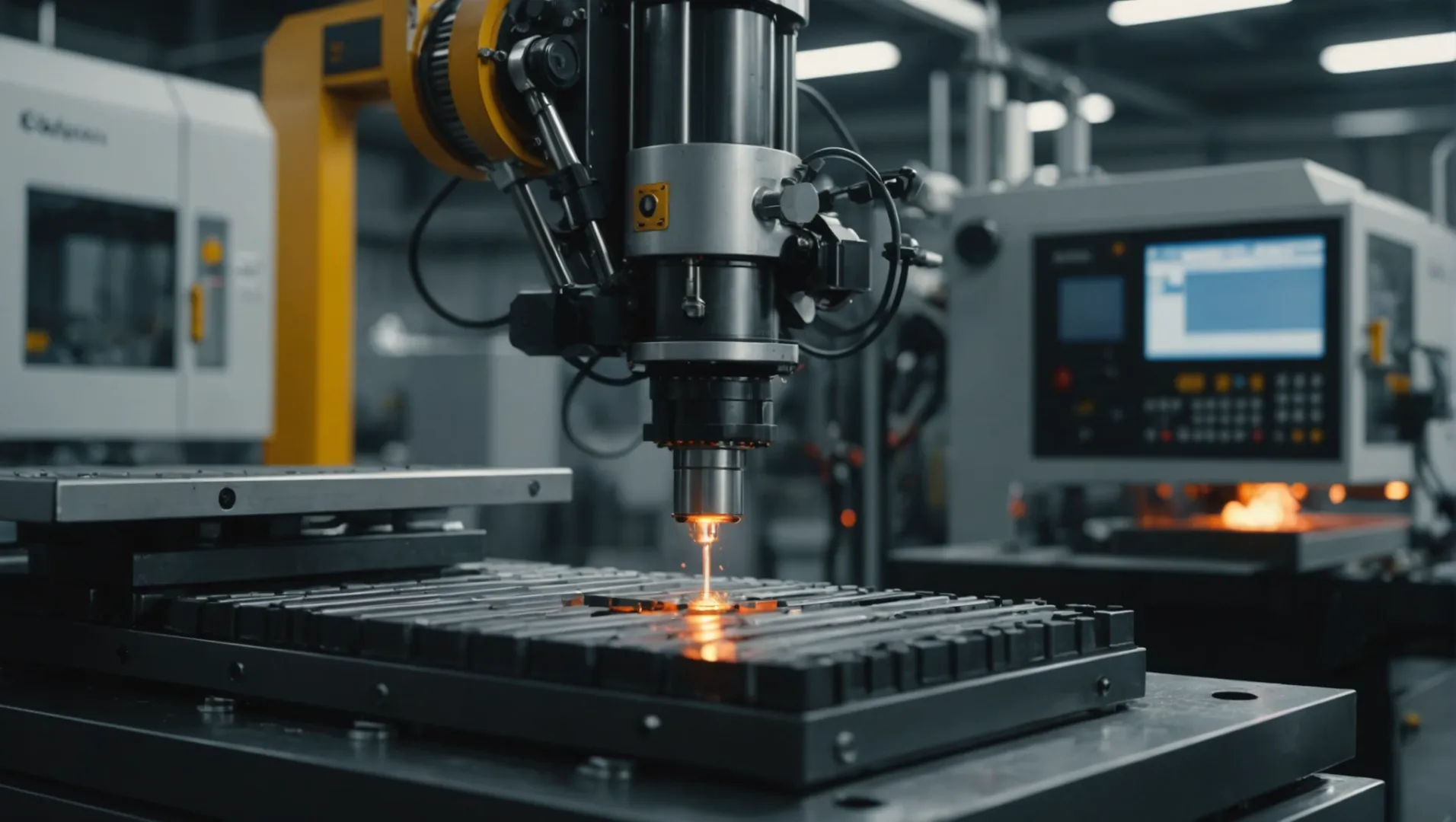
Comprender el proceso de moldeo por inyección
El proceso de moldeo por inyección implica inyectar material fundido en la cavidad de un molde, donde se enfría y se solidifica hasta obtener la forma del producto final. Este proceso es fundamental para determinar la facilidad y el éxito del desmolde, especialmente para estructuras complejas. Las complejidades de este proceso incluyen parámetros como la presión de inyección, la velocidad y el tiempo de enfriamiento, todos los cuales requieren un control meticuloso para lograr resultados óptimos.
Factores clave en el proceso de moldeo por inyección
Presión y velocidad de inyección
La presión y la velocidad de inyección son variables críticas que influyen directamente en la distribución de tensiones dentro del producto moldeado. La alta presión puede provocar una tensión excesiva, aumentando el riesgo de deformación durante el desmolde. Por el contrario, reducir la presión y la velocidad ayuda a aliviar las tensiones internas, minimizando así posibles problemas de deformación.
Por ejemplo, cuando se trabaja con materiales que presentan altas tasas de contracción, ajustar estos parámetros puede ayudar a evitar que el producto quede apretado alrededor del núcleo del molde. Este ajuste reduce la fricción y la fuerza requerida durante el desmolde, lo cual es vital para mantener la integridad del producto.
Optimización del tiempo de enfriamiento
El tiempo de enfriamiento es otro factor importante que afecta el éxito del desmolde. Permitir un tiempo de enfriamiento adecuado garantiza que el producto se solidifique por completo, lo que reduce la probabilidad de deformación o daño durante el desmolde. Además, un enfriamiento adecuado ayuda a controlar las tasas de contracción, lo que contribuye aún más a un desmolde sin problemas.
Al extender adecuadamente el período de enfriamiento, los fabricantes pueden garantizar que es menos probable que los productos se adhieran a los moldes o sufran rayones y deformaciones al retirarlos.
Selección de materiales y optimización de fórmulas
La selección de materiales apropiados con bajas tasas de contracción y buena fluidez puede mejorar en gran medida los resultados del desmolde. Al optimizar la fórmula del material, los fabricantes pueden mejorar las características de flujo del material fundido, asegurando un llenado uniforme del molde y reduciendo las concentraciones de tensión.
Por ejemplo, el uso de materiales con propiedades lubricantes inherentes puede disminuir la fricción entre el molde y el producto, lo que facilita el desmolde.
Conclusión: un enfoque integrado para el éxito del desmolde
En resumen, el proceso de moldeo por inyección desempeña un papel fundamental en el éxito del desmolde al gestionar variables como la presión, la velocidad, el tiempo de enfriamiento y la selección de materiales. Los fabricantes pueden mejorar significativamente los resultados del desmolde integrando ajustes estratégicos en estos parámetros. Para aquellos que buscan profundizar en técnicas específicas para optimizar estas variables, explorar la optimización de la presión del moldeo por inyección 2 ofrece información valiosa para lograr resultados de desmolde exitosos.
La alta presión de inyección aumenta la tensión de desmoldeo.Verdadero
La alta presión provoca una tensión excesiva, con riesgo de deformación durante el desmolde.
El tiempo de enfriamiento no tiene ningún impacto en el éxito del desmolde.FALSO
Un enfriamiento adecuado asegura la solidificación, reduciendo el riesgo de deformación durante el desmolde.
¿Por qué es crucial la calidad de la superficie del molde para un desmolde sin problemas?
La calidad de la superficie del molde juega un papel fundamental en el éxito de los procesos de desmoldeo en el moldeo por inyección. Una superficie del molde bien mantenida garantiza un desmolde más suave, minimizando los defectos y mejorando la calidad del producto.
La calidad de la superficie del molde es crucial ya que afecta directamente la fricción, la adhesión y la integridad del producto durante el desmolde. Las superficies pulidas y sin defectos reducen la fricción, evitan rayones y facilitan una liberación más suave y sin daños del producto.
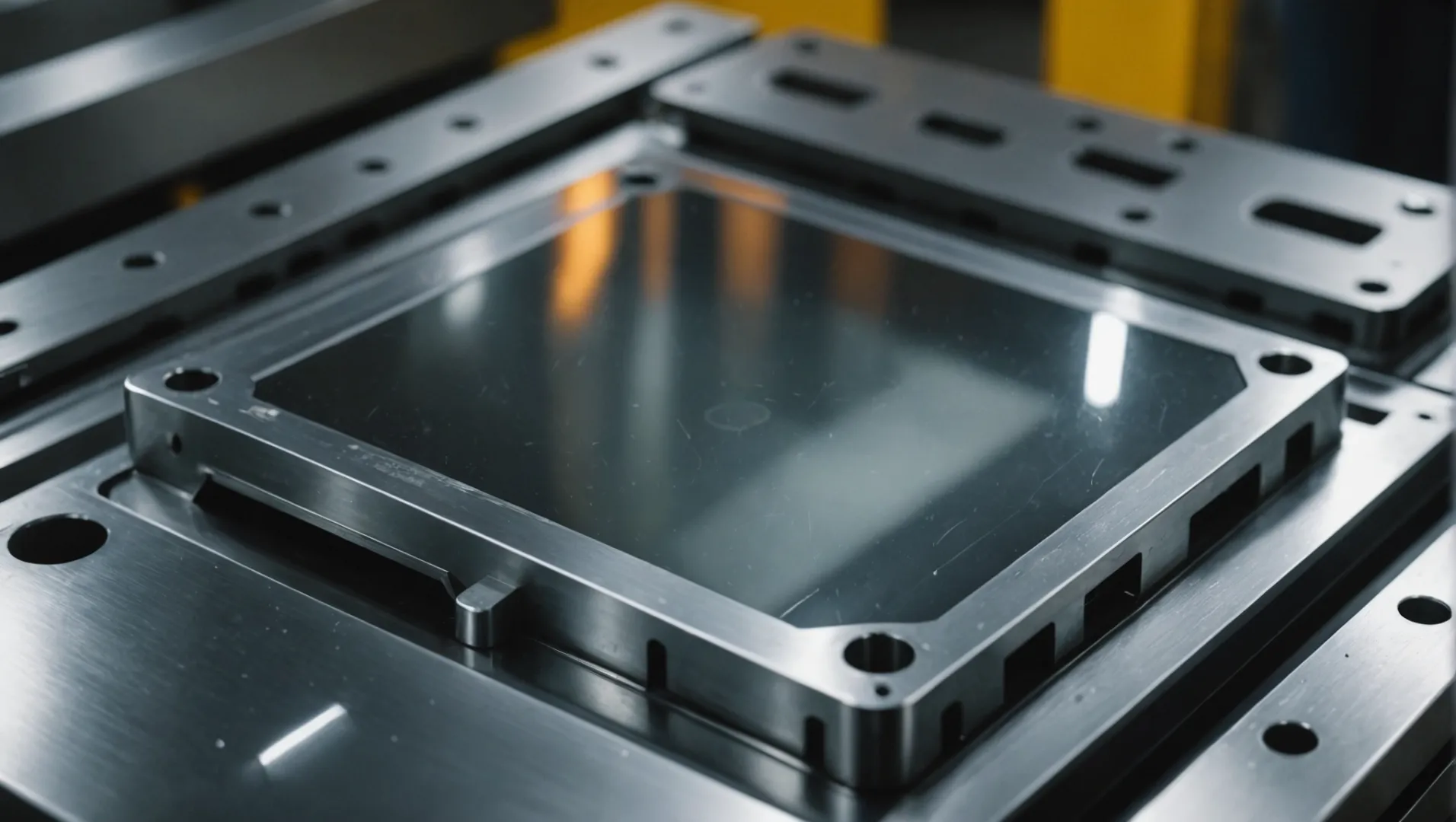
Comprender el impacto de la calidad de la superficie del molde
La calidad de la superficie del molde a menudo se subestima, pero afecta profundamente el proceso de desmoldeo. Una superficie pulida del molde reduce la fricción entre el molde y el producto. Esto es especialmente importante para estructuras complejas, donde la fricción puede provocar daños o deformaciones importantes del producto.
Reducción de fricción
- Una superficie lisa del molde disminuye la fuerza necesaria para retirar el producto, protegiendo así las piezas delicadas contra roturas.
- Las superficies pulidas también ayudan a reducir la tensión sobre los moldes y productos durante el proceso de desmoldeo.
Prevención de adherencias
- Los materiales con alta afinidad con los materiales del molde pueden pegarse o adherirse, provocando defectos como rayones. Una superficie del molde en buen estado puede mitigar este problema al reducir la adherencia.
- El mantenimiento regular y el uso de agentes desmoldantes pueden mantener los moldes en óptimas condiciones.
Estrategias para mejorar la calidad de la superficie del molde
Técnicas de pulido
Pulir el molde es una de las formas más efectivas de mejorar la calidad de su superficie. Implica:
- Utilizar herramientas y compuestos especializados para lograr un acabado similar a un espejo.
- Inspecciones periódicas para identificar y abordar el desgaste antes de que afecten la producción.
Uso de agentes de liberación
La aplicación de agentes desmoldantes es otra estrategia para mejorar la calidad de la superficie del molde:
- Estos agentes forman una barrera entre el molde y el producto, impidiendo la adhesión.
- Es crucial seleccionar agentes apropiados compatibles tanto con el material del molde como con el material del producto.
Mantenimiento y reparación de rutina
El mantenimiento preventivo es clave:
- Los controles periódicos para detectar rayones, óxido y otros defectos garantizan que los moldes permanezcan en las mejores condiciones.
- Abordar problemas menores con prontitud puede evitar problemas más importantes que podrían interrumpir la producción.
Ejemplos del mundo real de optimización de la superficie del molde
Considere un ejemplo de la industria automotriz donde la producción de gran volumen requiere un mantenimiento impecable del molde. Las empresas pulen rutinariamente los moldes y aplican agentes desmoldantes adecuados para mantener un alto rendimiento sin comprometer la calidad.
Estas prácticas no se limitan sólo a la automoción; también prevalecen en la fabricación de productos electrónicos y de bienes de consumo, donde la precisión y el acabado son primordiales.
Al centrarse en mejorar la calidad de la superficie del molde 3 , los fabricantes pueden garantizar procesos de desmolde más fluidos, reducir los residuos y mejorar la integridad del producto. Esta meticulosa atención al detalle se traduce directamente en una mejor calidad del producto y una mayor satisfacción del cliente.
Las superficies pulidas del molde reducen la fricción de desmoldeo.Verdadero
Una superficie pulida del molde disminuye la fricción, lo que ayuda a un desmolde más suave.
La adherencia no se ve afectada por la calidad de la superficie del molde.FALSO
La calidad de la superficie del molde reduce la adhesión, evitando defectos como rayones.
¿Qué mecanismos de desmoldeo son mejores para productos moldeados complejos?
Seleccionar los mecanismos de desmoldeo adecuados es crucial para mantener la integridad de productos moldeados complejos. Se pueden emplear varias técnicas para garantizar un desmolde suave y sin daños.
Para productos moldeados complejos, el empleo de mecanismos como eyectores, deslizadores y eyectores inclinados garantiza un desmolde eficiente sin dañar estructuras intrincadas.
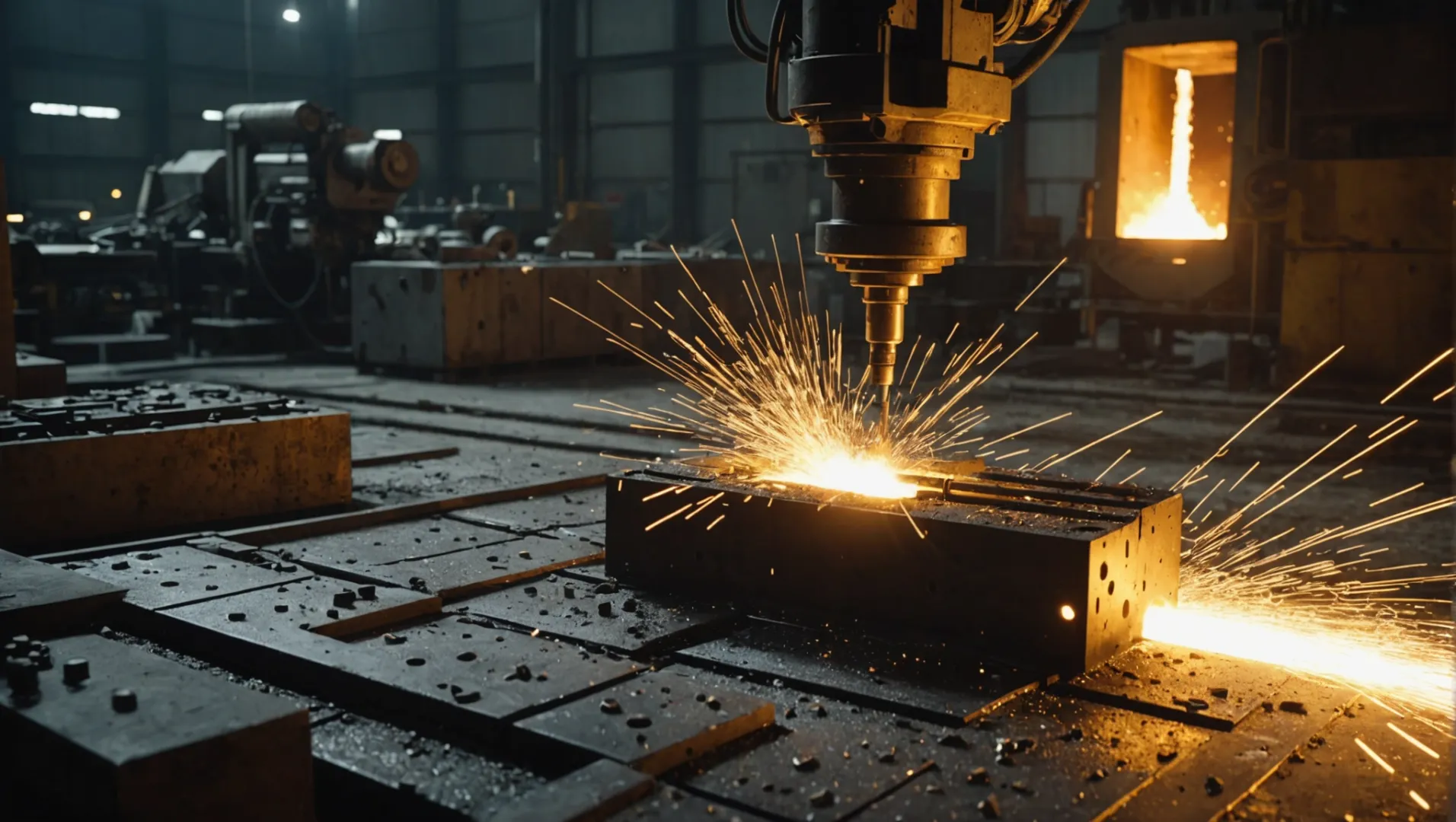
Comprender los desafíos del desmoldeo
El desmolde de productos moldeados complejos plantea desafíos importantes debido a estructuras intrincadas, socavaciones y cavidades profundas. Estas complejidades requieren mecanismos de desmolde cuidadosamente seleccionados para evitar daños y garantizar la eficiencia de la producción.
Tipos de mecanismos de desmoldeo
-
Pasadores eyectores
- Función : Los pasadores eyectores empujan la pieza moldeada fuera del molde.
- Aplicación : Adecuado para productos con geometrías simples.
- Limitación : Puede causar deformación si no se distribuye uniformemente.
-
Deslizadores
- Función : Permitir que las partes del molde se muevan hacia los lados, liberando las áreas socavadas.
- Aplicación : Ideal para productos con socavados complejos.
- Beneficio : Reduce la necesidad de posprocesamiento.
-
Eyectores inclinados
- Función : Expulsa piezas en ángulo para acomodar formas complejas.
- Aplicación : Se utiliza para productos que requieren desmoldeo en ángulo.
- Ventaja : Minimiza los defectos superficiales y la tensión.
-
Placas de empuje
- Función : Utilice placas planas para empujar toda la pieza de manera uniforme.
- Aplicación : Beneficioso para productos grandes y planos.
- Fuerza : Garantiza una distribución uniforme de la fuerza.
Seleccionar el mecanismo adecuado
La elección del mejor mecanismo depende del diseño del producto y de las propiedades del material. Por ejemplo, seleccionar un mecanismo de desmoldeo 4 que se alinee con las características estructurales del producto moldeado es fundamental para mantener la calidad y la eficiencia.
Técnicas de desmoldeo multipunto
Para productos particularmente grandes o complejos, el uso de desmolde multipunto puede mejorar la estabilidad y confiabilidad. Este enfoque distribuye las fuerzas de manera uniforme en todo el producto, lo que reduce las concentraciones de tensiones y las posibles deformaciones.
Conclusión
La incorporación de mecanismos de desmolde adecuados requiere un conocimiento profundo del diseño del producto y del comportamiento del material. Al adaptar el mecanismo para que se ajuste a estos parámetros, los fabricantes pueden lograr un desmolde eficiente y al mismo tiempo preservar la integridad de productos moldeados complejos.
Los pasadores eyectores son ideales para productos moldeados complejos.FALSO
Los pasadores eyectores son más adecuados para geometrías simples, no para moldes complejos.
Los controles deslizantes reducen la necesidad de posprocesamiento en productos moldeados.Verdadero
Los controles deslizantes permiten liberar áreas socavadas, minimizando el posprocesamiento.
Conclusión
Al implementar estas soluciones, los fabricantes pueden mejorar la calidad del producto y la eficiencia de la producción. Recuerde, ¡superar los desafíos del desmoldeo está a su alcance!
-
Explore diseños de moldes de vanguardia que simplifican el desmoldeo complejo. Nos especializamos en inyección de plástico, inyección termoestable, compresión termoestable y moldes de fundición a presión, junto con mecanizado personalizado, diseño por contrato y trabajo de electroerosión. ↩
-
Explore estrategias para optimizar la presión para obtener mejores resultados de desmoldeo: Pasos para la optimización del proceso de MOLDEO POR INYECCIÓN · 1. Examen de la funcionalidad de la herramienta · 2. Pruebas de disparo corto · 3. Estudios del sello de la compuerta · 4. Evaluación/datos de piezas de muestra... ↩
-
Explore métodos prácticos para mejorar las superficies de los moldes y mejorar la calidad de la producción: 1. Pulido y texturizado. El acabado de superficies es otro paso fundamental para mejorar la calidad del molde de inyección. Pulir la superficie del molde ayuda... ↩
-
Explore cómo los diferentes mecanismos se adaptan a varios diseños complejos: explore técnicas efectivas de desmoldeo en moldeo por inyección para mejorar la calidad del producto, reducir el tiempo del ciclo y minimizar los defectos en los productos terminados. ↩