El moldeo por inyección es más que un simple proceso de fabricación; es una danza intrincada de ciencia y arte. Gestionar la tensión dentro de los moldes es crucial para evitar los temidos defectos que pueden arruinar un producto perfectamente elaborado.
Reducir la tensión de moldeo en el moldeo por inyección implica optimizar los parámetros del proceso, mejorar el diseño del molde, seleccionar materiales adecuados y emplear técnicas de posprocesamiento. Estas estrategias ayudan a minimizar defectos como marcas de tensión y deformaciones, garantizando resultados de alta calidad.
Comprender los conceptos básicos es sólo el comienzo. Profundicemos en cada estrategia para descubrir enfoques matizados que realmente pueden transformar su proceso de fabricación.
Reducir la temperatura de inyección disminuye la tensión de moldeo entre un 10% y un 20%.Verdadero
La reducción de la temperatura de inyección reduce la orientación molecular, minimizando el estrés.
- 1. ¿Cómo pueden los parámetros de inyección influir en la tensión de moldeo?
- 2. ¿Qué papel juega el diseño de moldes en la reducción del estrés?
- 3. ¿Por qué es crucial la selección de materiales para minimizar la tensión del moldeo?
- 4. ¿Cómo afectan las técnicas de posprocesamiento a la calidad del producto?
- 5. Conclusión
¿Cómo pueden los parámetros de inyección influir en la tensión de moldeo?
Los parámetros de inyección desempeñan un papel fundamental en la configuración de los niveles de tensión dentro de los productos moldeados. Al ajustar estas configuraciones, los fabricantes pueden controlar la orientación molecular y las fuerzas de corte, lo que afecta directamente la calidad y el rendimiento del producto final.
Los parámetros de inyección influyen en la tensión de moldeo al afectar la orientación molecular y las fuerzas de corte. Ajustar la temperatura, la presión, la velocidad y los tiempos de enfriamiento puede reducir significativamente los niveles de estrés, minimizando los defectos y mejorando la calidad del producto.

El impacto de la temperatura de inyección
La temperatura de inyección es un parámetro crítico que influye en la fluidez del plástico fundido. Una temperatura más alta aumenta la fluidez, lo que puede mejorar el llenado de geometrías de moldes complejas. Sin embargo, también aumenta la orientación de las cadenas moleculares, aumentando así la tensión dentro de la pieza moldeada.
Optimización de la temperatura : seleccionar un rango de temperatura óptimo según las propiedades del material y las especificaciones del producto puede reducir significativamente el estrés. Por ejemplo, una reducción de la temperatura de inyección puede disminuir la orientación molecular hasta en un 20 %, lo que da lugar a una estructura del producto más estable.
Dinámica de presión y velocidad
La presión y velocidad de inyección excesivas son los principales contribuyentes al aumento de las fuerzas de corte en el molde. Estas fuerzas aumentan la orientación de la cadena molecular, aumentando la tensión de moldeo. Al ajustar estos parámetros, los fabricantes pueden lograr un delicado equilibrio entre un llenado adecuado del molde y niveles de tensión minimizados.
- Reducción de la presión y la velocidad : los ajustes en la configuración de la máquina de moldeo por inyección pueden reducir la tensión entre un 15% y un 30%. Este enfoque garantiza que las fuerzas de corte permanezcan dentro de límites tolerables, preservando la integridad del producto.
El papel del tiempo de retención y enfriamiento
La duración de los tiempos de mantenimiento y enfriamiento es crucial en el manejo del estrés. Un tiempo de retención insuficiente da como resultado una mayor tensión de contracción después del desmolde, mientras que un enfriamiento inadecuado no permite la solidificación completa del producto.
- Plazos de ampliación : al ampliar estos períodos de forma adecuada, según el tamaño y la complejidad del producto, los fabricantes pueden reducir el estrés por contracción entre un 20% y un 35%, lo que garantiza una mejor estabilidad dimensional y menos defectos.
Combinación de parámetros para obtener resultados óptimos
Un enfoque holístico que combine todos estos ajustes de parámetros puede conducir a mejoras significativas en la calidad del producto. Al comprender cómo interactúa cada parámetro con los demás, los fabricantes pueden desarrollar estrategias sólidas para minimizar el estrés de manera efectiva. Por ejemplo, combinar una presión de inyección reducida con un tiempo de enfriamiento optimizado puede generar beneficios compuestos más allá de los ajustes individuales.
Estas combinaciones estratégicas no sólo mejoran la calidad del producto sino que también promueven una mayor vida útil del molde y menores costos de producción. Para explorar cómo se interrelacionan estos factores, profundice en recursos como las Técnicas de optimización de parámetros de moldeo por inyección 1 que brindan información integral sobre estrategias de moldeo avanzadas.
Una temperatura de inyección más alta aumenta la tensión de moldeo.Verdadero
Una temperatura más alta eleva la orientación molecular, aumentando el estrés.
Reducir el tiempo de enfriamiento disminuye el estrés del moldeo.FALSO
Un enfriamiento insuficiente aumenta la tensión debido a una solidificación incompleta.
¿Qué papel juega el diseño de moldes en la reducción del estrés?
El diseño del molde es fundamental en el proceso de moldeo por inyección y afecta significativamente la distribución de tensiones y la calidad del producto. Al optimizar las características del molde, los fabricantes pueden reducir los defectos y mejorar la durabilidad.
El diseño eficaz del molde reduce el estrés al optimizar la ubicación de la compuerta, los sistemas de enfriamiento y las pendientes de desmolde, lo que garantiza un flujo equilibrado y un enfriamiento uniforme. Estos ajustes mitigan las concentraciones de tensión, mejorando la calidad general de los productos moldeados.

Comprender el impacto del diseño de moldes sobre el estrés
El diseño de un molde influye directamente en cómo se distribuye la tensión por todo el producto moldeado. Un molde diseñado eficazmente garantiza que el plástico fundido fluya uniformemente, se enfríe uniformemente y se suelte sin fricción o fuerza indebida. Cada uno de estos elementos juega un papel crucial a la hora de minimizar la tensión y evitar defectos como deformaciones o grietas.
Diseño de puerta
La ubicación y el número de puertas en un molde son vitales para mantener un flujo equilibrado del plástico fundido. La posición incorrecta de la compuerta puede provocar un flujo desigual, lo que provoca concentraciones de tensión que provocan defectos. Al emplear múltiples compuertas 2 o diseños de compuertas equilibradas, los fabricantes pueden garantizar una distribución uniforme del material, reduciendo así la tensión hasta en un 25%.
Optimización del sistema de refrigeración
Un sistema de enfriamiento bien diseñado es esencial para lograr una distribución uniforme de la temperatura en todo el producto. El enfriamiento desigual genera gradientes de temperatura que pueden aumentar la tensión del moldeo. Técnicas como el enfriamiento rápido y los sistemas de enfriamiento uniforme ayudan a minimizar estos gradientes, reduciendo el estrés entre un 20% y un 30%. Esto no sólo previene defectos sino que también mejora las propiedades mecánicas del producto final.
Consideraciones de pendiente de desmoldeo
La pendiente de las superficies del molde afecta la facilidad con la que se puede retirar el producto del molde. Una pendiente insuficiente aumenta la fricción durante el desmolde, lo que genera mayores niveles de tensión. Al aumentar la pendiente de desmolde, los fabricantes pueden facilitar una liberación más suave y una menor acumulación de tensión. Este ajuste puede disminuir la tensión de moldeo hasta en un 20%.
Ideas prácticas para implementar un diseño de molde eficaz
La implementación de estas mejoras de diseño requiere una comprensión profunda tanto de las propiedades del material como de los requisitos del producto. Por ejemplo, diferentes plásticos tienen diferentes tasas de expansión térmica, lo que debe tenerse en cuenta al diseñar sistemas de refrigeración y ubicación de puertas.
Característica de diseño | Enfoque recomendado | Potencial de reducción del estrés |
---|---|---|
Colocación de la puerta | Puertas múltiples/equilibradas | 15% – 25% |
Sistemas de refrigeración | Enfriamiento uniforme/rápido | 20% – 30% |
Pendiente de desmoldeo | Aumentar el ángulo de pendiente | 10% – 20% |
Al centrarse en estas áreas clave, los fabricantes pueden mejorar significativamente la integridad y el rendimiento del producto, lo que lleva a resultados de fabricación más consistentes y a una reducción del desperdicio de productos defectuosos. Conozca más sobre estas técnicas 3 para optimizar completamente sus procesos de moldeo por inyección.
El diseño equilibrado de la puerta reduce el estrés en un 25%.Verdadero
Los diseños de puertas equilibradas garantizan una distribución uniforme del material, lo que reduce el estrés.
El enfriamiento desigual aumenta el estrés en un 30%.Verdadero
El enfriamiento desigual provoca gradientes de temperatura, lo que aumenta la tensión del moldeo.
¿Por qué es crucial la selección de materiales para minimizar la tensión del moldeo?
Elegir el material adecuado es fundamental para minimizar el estrés del moldeo, lo que puede prevenir defectos y garantizar la longevidad de los productos moldeados.
La selección de materiales juega un papel fundamental a la hora de minimizar el estrés del moldeo al elegir plásticos de bajo estrés, agregar aditivos reductores del estrés y considerar factores ambientales. Estas decisiones ayudan a lograr un rendimiento y una longevidad óptimos del producto.

La importancia de elegir materiales de bajo estrés
La selección del material es crucial porque los diferentes plásticos tienen características de tensión inherentemente distintas. Los plásticos cristalinos, por ejemplo, tienden a tener una mayor tensión de moldeo en comparación con sus homólogos no cristalinos. Optar por materiales con menor estrés intrínseco puede afectar significativamente la durabilidad del producto final.
Para productos con requisitos de rendimiento estrictos, se prefieren materiales como el policarbonato (PC) o el éter de polifenileno (PPO) debido a sus menores niveles de tensión. Esta elección es particularmente esencial cuando se fabrican componentes que sufrirán tensión mecánica durante el uso, como piezas de automóviles o productos electrónicos de consumo.
Papel de los aditivos en la selección de materiales
La incorporación de aditivos a la resina plástica puede mejorar las propiedades del material y reducir la tensión del moldeo. Los plastificantes, por ejemplo, hacen que los plásticos sean más flexibles, disminuyendo así la fragilidad y la tensión general. De manera similar, los modificadores de impacto mejoran la resistencia de un material al agrietamiento bajo presión.
La selección de los aditivos adecuados depende tanto del plástico base como de la aplicación prevista del producto. Este enfoque personalizado puede reducir el estrés del moldeo hasta en un 25 %, lo que lo convierte en una estrategia rentable para los fabricantes que buscan optimizar sus procesos de producción.
Consideraciones ambientales en la selección de materiales
Otro aspecto de la selección de materiales implica considerar el entorno donde se utilizará el producto. Factores como la exposición a la luz ultravioleta, las fluctuaciones de temperatura y la humedad pueden influir en el rendimiento y la longevidad de los productos plásticos. Los materiales elegidos deben soportar estas condiciones sin comprometer la integridad estructural.
Por ejemplo, seleccionar un material resistente a los rayos UV para aplicaciones en exteriores evitará la degradación con el tiempo, manteniendo así la funcionalidad y el atractivo estético del producto.
Aplicaciones prácticas y ejemplos
A modo de ejemplo, consideremos un fabricante de automóviles que selecciona materiales para componentes interiores. Al elegir una mezcla de plásticos de baja tensión y aditivos adecuados, pueden garantizar que los componentes sean duraderos, menos propensos a deformarse y estéticamente agradables con el tiempo.
Los fabricantes también deberían realizar pruebas de estrés de materiales 4 para validar sus elecciones de materiales en condiciones del mundo real. Este paso es vital para mantener altos estándares de control de calidad y garantizar la satisfacción del cliente.
Los plásticos cristalinos tienen una menor tensión de moldeo.FALSO
Los plásticos cristalinos generalmente presentan mayores tensiones de moldeo que los no cristalinos.
Los aditivos pueden reducir el estrés del moldeo hasta en un 25%.Verdadero
La incorporación de aditivos específicos a los plásticos puede reducir significativamente la tensión de moldeo.
¿Cómo afectan las técnicas de posprocesamiento a la calidad del producto?
Las técnicas de posprocesamiento son fundamentales para refinar la calidad del producto al reducir la tensión del moldeo, mejorar la durabilidad y mejorar el rendimiento.
Las técnicas de posprocesamiento, como el recocido y el acondicionamiento de la humedad, afectan significativamente la calidad del producto al reducir la tensión del moldeo, mejorar las propiedades del material y mejorar la estabilidad dimensional. Estos métodos garantizan que los productos cumplan con estrictos estándares de rendimiento y durabilidad.
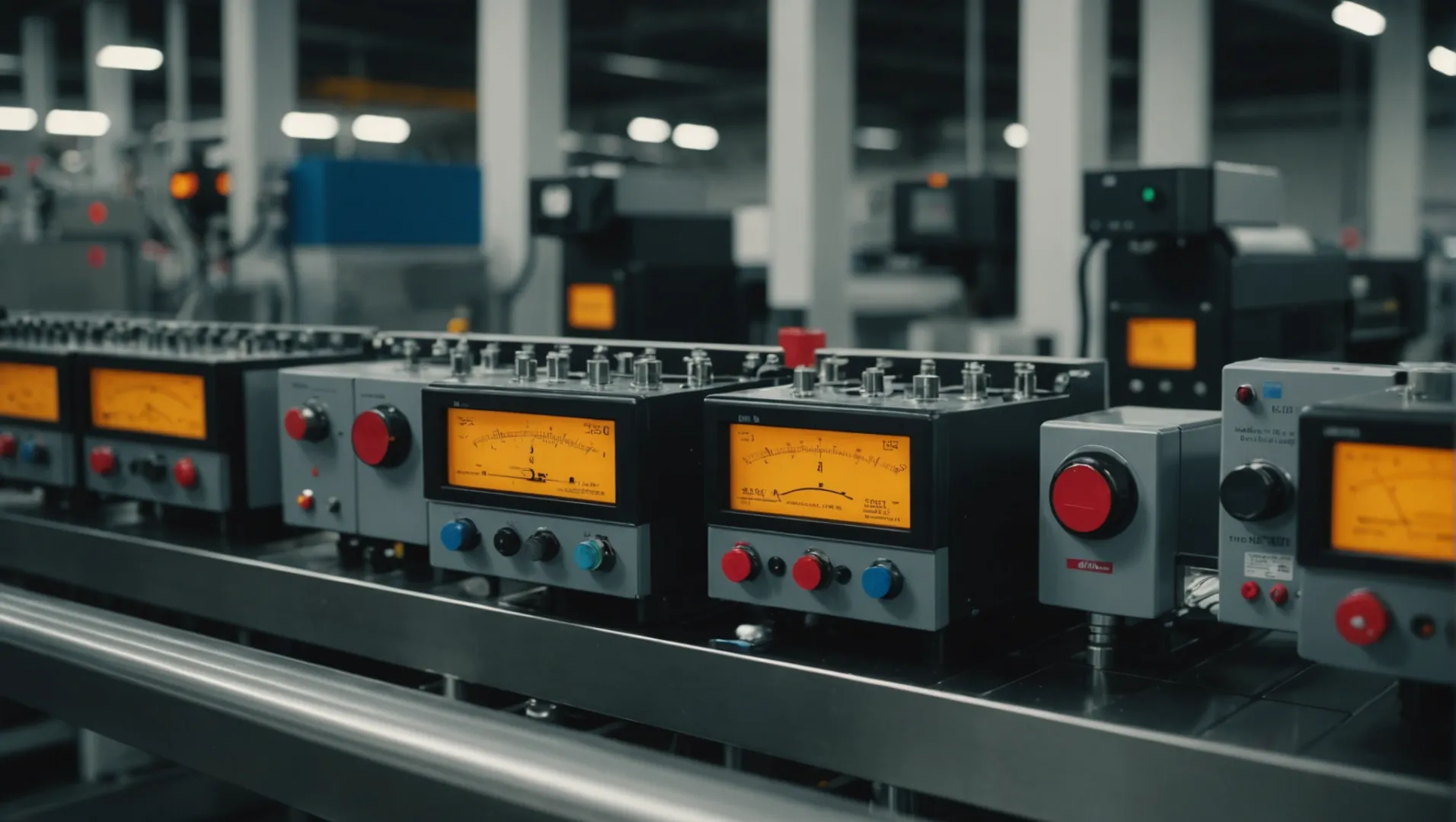
El impacto del recocido en la calidad del producto
El recocido es una técnica de posprocesamiento fundamental que implica calentar el producto moldeado a una temperatura específica, mantenerlo durante un período determinado y luego enfriarlo gradualmente. Este proceso permite que las cadenas moleculares dentro del plástico se relajen, lo que reduce significativamente la tensión residual y posibles defectos como deformaciones o grietas.
Por ejemplo, los productos fabricados con materiales como el policarbonato se benefician enormemente del recocido, ya que mejora su resistencia al impacto y su claridad. Según los estándares de la industria, el recocido puede reducir la tensión del moldeo hasta en un 50%, mejorando así la 5 del producto .
El papel del acondicionamiento de la humedad en la reducción del estrés
El acondicionamiento de la humedad es particularmente beneficioso para materiales higroscópicos como el nailon. Al exponer el producto a niveles de humedad controlados, absorbe la humedad, lo que alivia las tensiones internas. Este método es eficaz para reducir la contracción y la distorsión, que son problemas comunes en los productos moldeados por inyección.
Por ejemplo, ajustar los parámetros de acondicionamiento de la humedad puede conducir a una reducción de la tensión de moldeo entre un 20% y un 40%. Este proceso también mejora la estabilidad dimensional del producto, asegurando que mantenga su forma y tamaño previstos en diversas condiciones ambientales.
Comparación del recocido y el acondicionamiento de la humedad
Método | Materiales adecuados | Reducción del estrés | Beneficios adicionales |
---|---|---|---|
Recocido | Policarbonato, ABS | 30% – 50% | Aumenta la claridad y la resistencia al impacto. |
Acondicionamiento de humedad | nailon, mascota | 20% – 40% | Mejora la estabilidad dimensional |
Selección estratégica de técnicas de posprocesamiento
La selección de la técnica de posprocesamiento adecuada depende del material utilizado y de las propiedades deseadas del producto final. Por ejemplo, un fabricante que busca una alta resistencia al impacto podría favorecer el recocido, mientras que uno que se centra en la precisión dimensional puede optar por el acondicionamiento de la humedad.
Al comprender los matices de cada método, los fabricantes pueden adaptar sus procesos para mejorar la calidad general del producto 6 . Este enfoque estratégico no sólo mejora el rendimiento sino que también reduce el desperdicio y el retrabajo, lo que conduce a ciclos de producción más eficientes.
El recocido reduce la tensión de moldeo en un 50%.Verdadero
El recocido puede reducir significativamente la tensión residual, mejorando la durabilidad del producto.
El acondicionamiento de la humedad aumenta la contracción de los productos de nailon.FALSO
El acondicionamiento de la humedad reduce la contracción al aliviar las tensiones internas en materiales higroscópicos.
Conclusión
La aplicación de estas estrategias puede mejorar significativamente la calidad del producto en el moldeo por inyección. Reflexiona sobre qué técnicas se adaptan mejor a tus operaciones para reducir defectos y optimizar la producción.
-
Explore técnicas para ajustes de parámetros estratégicos en moldeo.: 1. Control de temperatura: · 2. Velocidad de inyección: · 3. Tiempo de enfriamiento: · 4. Selección de material plástico: · 5. Velocidad del tornillo y contrapresión: · 6. Inyección… ↩
-
Descubra cómo las compuertas múltiples mejoran el flujo de material y reducen la tensión: esto ayuda a evitar que el plástico fundido se endurezca de manera prematura y desigual. También evita que las piezas de plástico se deformen como tensión... ↩
-
Explore técnicas avanzadas para optimizar el diseño de moldes y reducir el estrés: cree piezas más atractivas y eficientes, además de reducir los costos de producción con estos consejos de diseño de moldeo por inyección, que incluyen bisagras vivas, salientes, texto y más... ↩
-
Aprenda cómo evaluar materiales de manera efectiva en condiciones del mundo real: Las pruebas de tensión del molde, también conocidas como pruebas de distorsión y alivio de tensión del molde, se realizan en productos que tienen una carcasa de plástico. ↩
-
Descubra cómo el recocido mejora la durabilidad y reduce los defectos: el recocido es un método de tratamiento térmico que se utiliza para eliminar cualquier tensión inaceptable que pueda resultar del proceso de fabricación y mejorar la estabilidad dimensional. ↩
-
Descubra cómo estas técnicas elevan los estándares de los productos: de hecho, las técnicas de posprocesamiento pueden mejorar en gran medida la microestructura y, en consecuencia, el comportamiento mecánico del uso final funcional... ↩