Únase a un viaje a través de las complejidades del moldeo por inyección. El proceso brilla con la presión de inyección adecuada. La magia realmente ocurre aquí.
La mejor presión para el moldeo por inyección depende de las características del material, la estructura del producto y el diseño del molde. La presión suele oscilar entre 30 y 150 MPa. Factores como la viscosidad y la fluidez afectan esta presión. Las pruebas y ajustes durante las pruebas de molde ayudan a encontrar la presión adecuada. Las pruebas prácticas realmente importan.
Cuando comencé a aprender sobre moldeo por inyección, me sentí muy asombrado. Un pequeño cambio de presión realmente podría mejorar o arruinar el producto final. No se trata sólo de números. Implica tanto el arte como la ciencia. La gente necesita comprender los pequeños detalles, como el grosor del material o el diseño complejo del producto. Recuerdo un proyecto con policarbonato (PC). Este material tenía un espesor elevado y necesitaba mucha presión, entre 80 y 130 MPa, para llenar correctamente cada parte del molde.
El diseño del molde importa mucho. El tamaño y la posición de la compuerta realmente afectan la presión necesaria. Me enfrenté a un problema difícil con un producto que tenía una parte interna compleja. Tuve que cambiar el diseño de la puerta para llenar el producto perfectamente y sin errores. Estas experiencias me demostraron que encontrar la presión de inyección perfecta no es igual para todos los proyectos. Necesita un enfoque especial. A menudo implica pruebas repetidas y cambios muy precisos.
La presión de inyección óptima es siempre de 100 MPa.FALSO
La presión óptima varía según el material y el diseño del molde, no fijada en 100 MPa.
Las pruebas empíricas ayudan a determinar la presión de inyección.Verdadero
Las pruebas durante las pruebas de moldes ayudan a optimizar la presión de inyección.
- 1. ¿Cómo afecta la viscosidad del material a la presión de inyección?
- 2. ¿Cómo influye la estructura del producto en la presión de inyección?
- 3. ¿Por qué es crucial el diseño de moldes en los ajustes de presión de inyección?
- 4. ¿Cómo optimizo la presión en las pruebas de moldes?
- 5. ¿Cuáles son los errores comunes al configurar la presión de inyección?
- 6. Conclusión
¿Cómo afecta la viscosidad del material a la presión de inyección?
¿Alguna vez has pensado por qué algunos materiales requieren más presión en el moldeo por inyección? ¡Explore el interesante mundo de la viscosidad y la presión de inyección!
El espesor del material es muy importante a la hora de elegir la presión de inyección para el moldeo. Los materiales gruesos necesitan más presión para llenar los moldes que los materiales delgados. La alta presión garantiza que los moldes se llenen correctamente y se obtengan buenos productos.
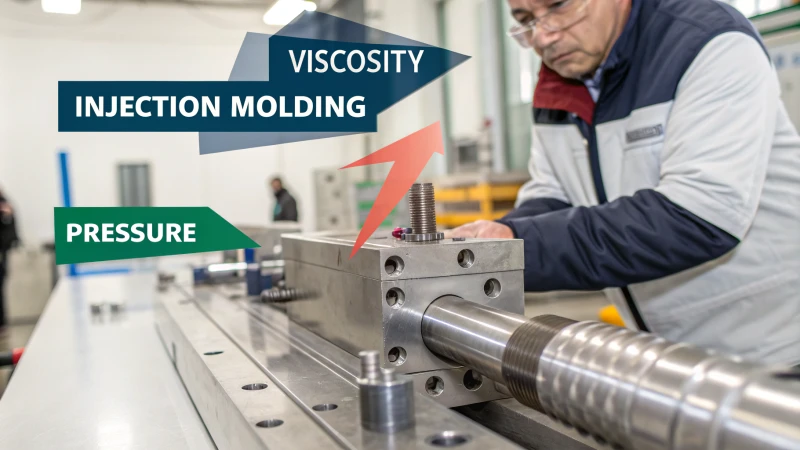
Comprender la viscosidad del material
La viscosidad juega un papel silencioso pero crucial en el moldeo por inyección. Recuerdo mi primera experiencia con el policarbonato. Este material tiene alta viscosidad. Es como pasar miel por una pajita. Es necesario utilizar alta presión para llenar cada parte del molde. Por el contrario, los materiales de baja viscosidad como el polietileno actúan como agua. Se deslizan con poco esfuerzo.
El papel de la fluidez
La fluidez ofrece una perspectiva interesante. Imagínese una fiesta con dos líneas de buffet. La cola lenta hace que la gente tarde mucho en elegir la comida. Esto se asemeja a materiales con poca fluidez y que necesitan más presión para moverse. Mientras tanto, el poliestireno fluye suavemente como una línea que se mueve rápidamente, incluso con menos presión.
Material | Viscosidad | Presión de inyección (MPa) |
---|---|---|
policarbonato | Alto | 80-130 |
Polietileno | Bajo | 30-80 |
Poliestireno | Moderado | 40-90 |
Análisis de la estructura del producto
El diseño de un producto se puede comparar con la planificación de un viaje. Diseñar elementos de paredes gruesas es como conducir por una carretera ancha, moviéndose de manera constante con una presión adicional mínima. Los productos de paredes delgadas se asemejan a caminos de montaña sinuosos y requieren más fuerza (o presión) para mantenerse suaves.
Consideraciones de diseño de moldes
El diseño del molde implica el tamaño y la posición de la puerta. Una puerta grande se asemeja a las puertas abiertas de un concierto, lo que permite una entrada fácil con menos presión. Las puertas más pequeñas actúan como pocas puertas abiertas y necesitan más fuerza para evitar cuellos de botella.
Un buen sistema de guías 1 funciona como un camino suave, disminuyendo la resistencia y reduciendo la presión necesaria. Una vez, cambiar a un sistema de canal caliente ayudó a reducir la presión en 20 MPa, como descubrir un atajo para facilitar el procesamiento.
Prueba y optimización de moldes
Ajustar la presión correctamente es realmente un arte. Empiezo con conjeturas fundamentadas y las refine en función de los resultados de las pruebas. Me recuerda a la cocina, donde los ajustes de calor logran la cocción a fuego lento perfecta. Los elementos de ajuste fino, como la velocidad de inyección y la presión de retención, generan productos ideales sin sorpresas.
Comprender el efecto de la viscosidad sobre la presión de inyección 2 transformó mi enfoque. Es como una receta secreta para elaborar eficientemente productos de la mejor calidad. De hecho, este conocimiento beneficia a todos los diseñadores, especialmente a Jacky.
Los materiales de alta viscosidad requieren presiones de inyección más altas.Verdadero
Materiales como el policarbonato necesitan más presión debido a su resistencia al flujo.
Los productos de paredes más gruesas requieren presiones de inyección más altas.FALSO
Las paredes más gruesas enfrentan menos resistencia, lo que permite una menor presión para el moldeado.
¿Cómo influye la estructura del producto en la presión de inyección?
¿Alguna vez has pensado por qué algunos productos necesitan varias presiones durante su fabricación? Los productos a menudo necesitan esto para lograr la forma correcta. Durante la producción, diversas presiones ayudan a crear diseños detallados. Algunos materiales responden mejor a la alta presión, mientras que otros necesitan menos fuerza. Los fabricantes utilizan estas técnicas con frecuencia. Este método mejora la calidad del producto final.
La estructura del producto es muy importante para establecer la presión de inyección necesaria en la fabricación. El espesor de la pared, la complejidad y el diseño de la puerta afectan la forma en que se mueve el material. Este movimiento influye en la eficiencia. También afecta la calidad del producto final.
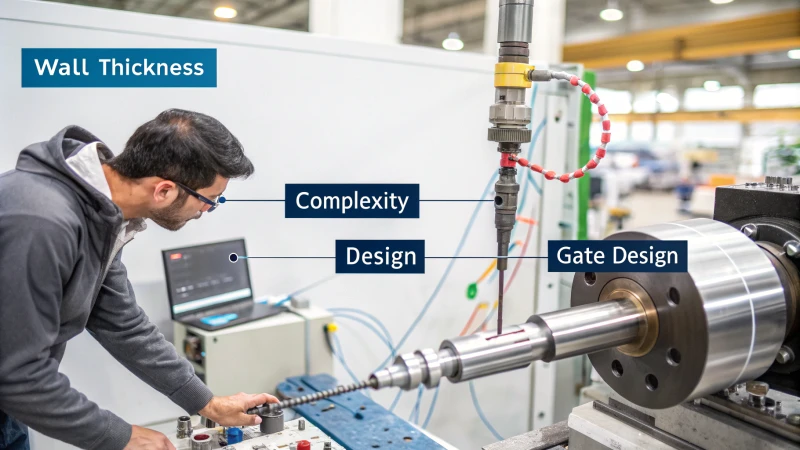
Explorando las propiedades de los materiales
Viscosidad y fluidez
Al comienzo de mi trabajo con muchos materiales, la viscosidad y la fluidez se convirtieron en algo más que una teoría. Los materiales de alta viscosidad como el policarbonato 3 , con su naturaleza espesa, a menudo requerían una fuerza considerable (alrededor de 80-130 MPa) para llenar los moldes. Por el contrario, los materiales de baja viscosidad como el polietileno se comportaron de manera diferente, moviéndose fácilmente con presiones mucho más bajas (entre 30 y 80 MPa).
Una vez usamos poliestireno porque fluía sin esfuerzo en los moldes a 40-90 MPa. Pero los plásticos reforzados eran duros. Recuerdo una vez que aumentamos la presión hasta 150 MPa solo para un buen llenado.
Comprender la estructura del producto
Espesor de la pared
El grosor de las paredes a menudo me sorprende. El espesor de las paredes del producto afecta directamente a los requisitos de presión:
Espesor de la pared | Rango de presión |
---|---|
Paredes más gruesas | Se necesita menos presión |
Paredes más delgadas | Se requiere más fuerza |
Las paredes más gruesas son indulgentes y utilizan menos presión. Los más finos necesitan más fuerza para llenarse por completo.
Complejidad
Los diseños complejos en carcasas electrónicas a menudo me desafían. Suelen necesitar hasta 150MPa para evitar las molestas marcas de soldadura.
Habilidades de diseño de moldes
Tamaño y posición de la puerta
El tamaño y la posición de la puerta desempeñan papeles cruciales en el diseño de moldes:
- Las compuertas más grandes permiten un flujo más fácil con menor presión.
- Las puertas más pequeñas requieren una presión más alta.
- La ubicación de la puerta también es fundamental; Las malas posiciones arruinan el proceso.
El sistema de correderas influye mucho en las necesidades de presión. Experimenté con diferentes diseños y vi cómo un diseño inteligente realmente puede reducir la presión en comparación con los sistemas fríos.
Mejorar mediante pruebas
Cada proyecto comienza estableciendo presiones iniciales utilizando datos. Es un proceso de ida y vuelta de ajuste y observación, a menudo en pasos de 5 a 10 MPa, hasta que todo se alinea perfectamente y sin fallas.
Cada cambio revela nuevos trucos para optimizar la presión, simplificando proyectos futuros. Cada ajuste exitoso es un hito en mi búsqueda del dominio del diseño y la fabricación.
Los materiales de alta viscosidad necesitan presiones de inyección más altas.Verdadero
Materiales como el policarbonato requieren entre 80 y 130 MPa para llenar los moldes.
Las paredes más delgadas requieren presiones de inyección más bajas.FALSO
Las paredes delgadas se enfrían rápidamente y necesitan entre 80 y 140 MPa para llenar completamente la cavidad.
¿Por qué es crucial el diseño de moldes en los ajustes de presión de inyección?
¿Alguna vez ha pensado en cómo el diseño de moldes podría realmente ayudar o destruir su trabajo de moldeo por inyección?
El diseño del molde juega un papel vital a la hora de decidir los ajustes de presión de inyección. Afecta la forma en que el material se mueve y llena un molde. Conocer el diseño permite establecer la presión adecuada. El llenado completo de una cavidad necesita la presión correcta. Esto evita defectos y mejora tanto la eficiencia como la calidad.
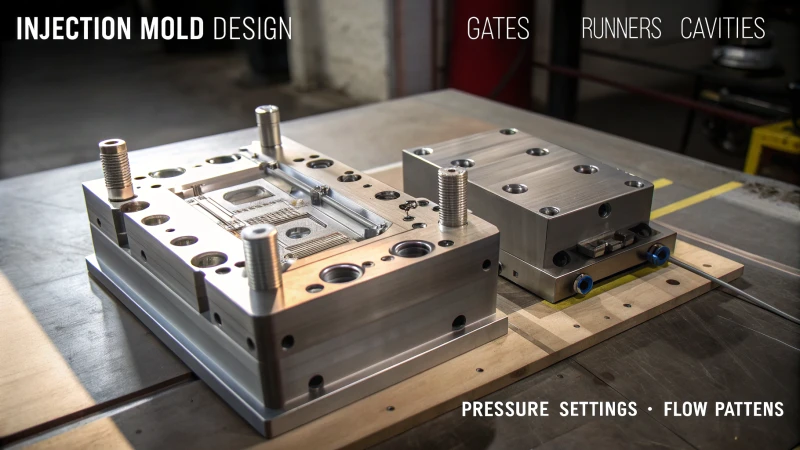
El papel de las propiedades materiales
Recuerdo la primera vez que utilicé policarbonato: ¡era como luchar contra un animal testarudo! Este material tiene una alta resistencia al flujo, por lo que es necesario aumentar la presión, a veces hasta 130 MPa, solo para llenar el molde. Por el contrario, era fácil trabajar con polietileno y necesitaba mucha menos presión, alrededor de 30 a 80 MPa, porque fluye más fácilmente.
El diseño del molde debe considerar propiedades del material como la viscosidad 4 y la fluidez para garantizar un moldeo por inyección eficiente. Los materiales con mayor viscosidad requieren mayor presión para llenar la cavidad del molde, mientras que aquellos con menor viscosidad necesitan menos presión.
Tipo de material | Viscosidad | Rango de presión (MPa) |
---|---|---|
Policarbonato (PC) | Alto | 80-130 |
Polietileno (PE) | Bajo | 30-80 |
Análisis de la estructura del producto
Estudiar la estructura del producto es algo que nunca me salto. Una vez trabajé en una vivienda con una pared de sólo 2 mm de espesor. Estas delgadas paredes se enfriaron tan rápidamente que necesité una presión cercana a los 140 MPa para llenar el formulario correctamente. En otro proyecto con paredes de 8 mm de espesor, sólo fueron suficientes unos 70 MPa de presión.
Los diseñadores deben analizar la estructura del producto para establecer presiones de inyección adecuadas. El espesor de la pared juega un papel crucial: las paredes más gruesas reducen la resistencia y requieren menos presión, mientras que las paredes más delgadas exigen una presión más alta debido al enfriamiento rápido y la mayor resistencia al flujo.
Factores de diseño de moldes
El tamaño y la posición de la puerta lo cambian todo. Una vez subestimé el efecto de una compuerta pequeña en un diseño complejo, lo que me enseñó una lección importante sobre las presiones de inyección. Ahora presto mucha atención porque incluso una puerta bien colocada ahorra mucho esfuerzo al dar un relleno uniforme.
¡Nunca ignores el sistema de corredores! La primera vez que utilicé un sistema de canal rugoso, fue como pasar almíbar a través de una pajita. Me demostró que los corredores cortos y suaves reducen la resistencia y mantienen la presión baja.
El tamaño y la posición de la compuerta son fundamentales para gestionar la presión de inyección. Las compuertas más grandes reducen la resistencia a la fusión, lo que reduce la presión necesaria, mientras que las compuertas más pequeñas requieren una presión más alta. Además, una compuerta bien ubicada garantiza un llenado uniforme de la cavidad.
El diseño del sistema de canales (su longitud, diámetro y rugosidad de la superficie) también afecta la resistencia al flujo del material fundido.
Prueba y optimización de moldes
Al principio me puse nervioso durante las pruebas con el molde. Rápidamente vi que usar fórmulas básicas y ajustar de 5 a 10 MPa a la vez me ayudaba a encontrar la configuración perfecta. El ajuste no sólo mejoró realmente la calidad, sino que también proporcionó datos útiles para tareas futuras.
Los ajustes iniciales de presión de inyección se pueden estimar mediante fórmulas empíricas y ajustarse durante las pruebas del molde. Los ajustes graduales (incrementos de 5 a 10 MPa) ayudan a lograr ajustes óptimos donde la cavidad se llena completamente sin defectos.
El policarbonato requiere una presión de inyección mayor que el polietileno.Verdadero
El policarbonato tiene una alta viscosidad y necesita entre 80 y 130 MPa, mientras que el polietileno necesita entre 30 y 80 MPa.
Las paredes más gruesas de los moldes requieren presiones de inyección más altas.FALSO
Las paredes más gruesas reducen la resistencia y requieren menos presión en comparación con las paredes más delgadas.
¿Cómo optimizo la presión en las pruebas de moldes?
Ajustar la presión en las pruebas de moldes eleva la calidad del producto de buena a excelente. Este proceso es crítico. Así es como lo manejo.
Para realizar bien las pruebas de molde para los ajustes de presión, estudio cómo se comportan los materiales, observo la forma del producto y compruebo la disposición del molde. Cambio lentamente la configuración y observo los resultados. Esto me ayuda a ajustar la presión para obtener una mejor calidad del producto. Sí, mejor calidad.
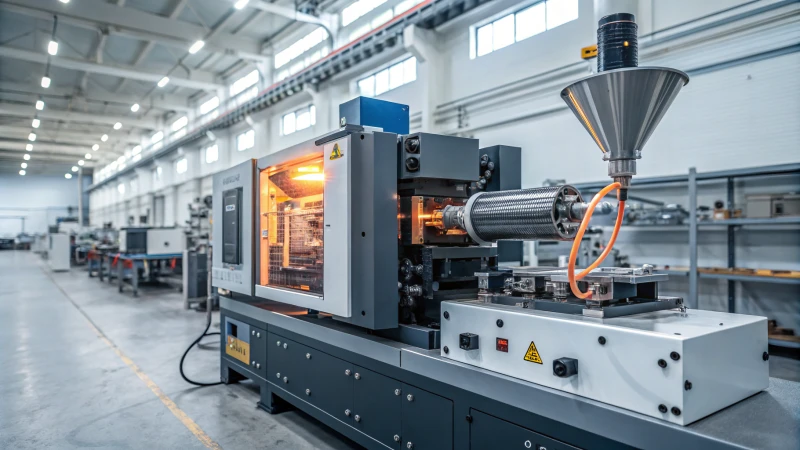
Comprender las propiedades de los materiales
Al estudiar las pruebas de moldes, he aprendido lo importantes que son las cualidades de los materiales, como el grosor y su extensión. Por ejemplo, los materiales gruesos como el policarbonato 5 necesitan presiones de inyección más altas, tal vez de 80 a 130 MPa. Los materiales de fácil flujo como el polietileno necesitan sólo de 30 a 80 MPa. Los materiales que se esparcen bien llenan los espacios con menor presión. Otros suelen necesitar más presión para un buen llenado.
Análisis de la estructura del producto
El diseño del producto realmente cambia las necesidades de presión. El espesor de la pared juega un papel crucial. Las paredes más gruesas ofrecen menos resistencia, necesitando sólo de 50 a 90 MPa para paredes de entre 5 y 10 mm. Las paredes delgadas de menos de 3 mm requieren más esfuerzo. Presiones más altas, de 80 a 140 MPa, combaten la resistencia y previenen problemas como no llenar lo suficiente.
Evaluación de factores de diseño de moldes
El diseño del molde es crucial. El tamaño y la posición de la puerta y el sistema de guías son muy importantes. Las puertas grandes reducen la resistencia, mientras que las puertas pequeñas necesitan más presión. Un 6 bien planificado puede reducir significativamente la resistencia, especialmente en sistemas de canales calientes. Estas reducen las necesidades de presión entre 10 y 30 MPa en comparación con los sistemas fríos.
Factor | Impacto en la presión |
---|---|
Tamaño de la puerta | Las puertas más grandes reducen la presión |
Sistema de corredor | Los canales calientes reducen las necesidades de presión |
Realización de la prueba del molde
Comenzar con una presión inicial basada en fórmulas probadas es mi enfoque habitual. Ajusto gradualmente entre 5 y 10 MPa mientras observo de cerca la calidad del llenado del producto. ¿El objetivo? Cavidades perfectamente rellenas sin defectos como marcas de flujo o burbujas. Mientras ajusto la velocidad y otras configuraciones, registro el mejor rango de presión para cada molde y tipo de producto para agilizar la producción futura.
Esto ayuda a mantener una calidad constante y mejorar la eficiencia en los procesos de moldeo por inyección 7 .
Los materiales de alta viscosidad requieren presiones de inyección más altas.Verdadero
Materiales como el policarbonato necesitan entre 80 y 130 MPa debido a su alta viscosidad.
Las paredes delgadas requieren presiones de inyección más bajas que las paredes gruesas.FALSO
Las paredes delgadas necesitan presiones más altas (80-140 MPa) debido a una mayor resistencia.
¿Cuáles son los errores comunes al configurar la presión de inyección?
¿Alguna vez un error le ha detenido en el taller mientras miraba un molde defectuoso y reflexionaba sobre el error? Los errores comunes al ajustar la presión de inyección a menudo causan este tipo de problemas. Comprender estos errores le ayudará a evitarlos.
Los errores comunes al establecer la presión de inyección implican ignorar las características del material, pasar por alto los detalles del diseño del producto, olvidar los factores de diseño del molde y saltarse las pruebas del molde. Corregir estos errores realmente conduce a mejores resultados de moldeo por inyección.
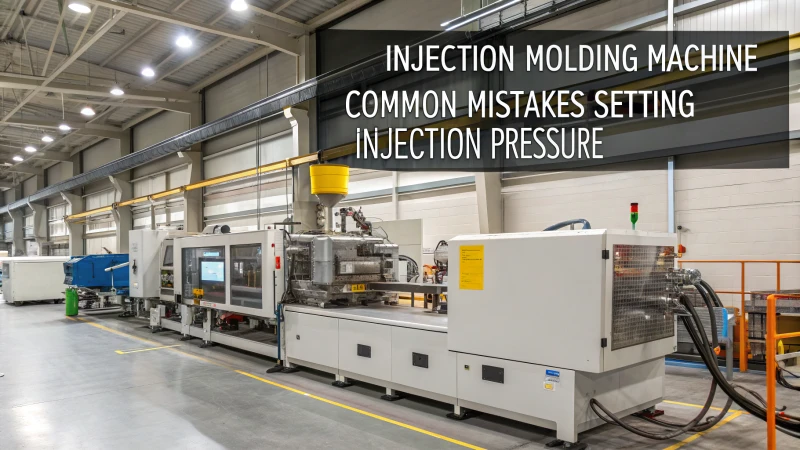
Sin considerar las propiedades del material
Imagínate hacer galletas sin pensar en la masa. Los materiales en moldeo por inyección son similares. Cada uno tiene rasgos únicos. El policarbonato, por ejemplo, se parece a una masa espesa. Necesita más presión, entre 80 y 130 MPa, para fluir bien. Por el contrario, el polietileno fluye como mantequilla derretida y necesita mucha menos presión.
Comprender estas propiedades puede evitar problemas de llenado debido a variaciones en la viscosidad 8 y la fluidez.
Olvidar la estructura del producto
Armar un rompecabezas sin todas las piezas resulta frustrante. Esto sucede si ignoro los detalles de la estructura del producto en el moldeado. Es posible que los productos más gruesos no necesiten tanta presión porque se produce menos resistencia. El desafío está en los diseños finos o complejos. Las paredes delgadas o las esquinas difíciles, como en las carcasas de dispositivos electrónicos, necesitan una presión precisa. Sin él, aparecen defectos como marcas de soldadura o rellenos incompletos.
Espesor de la pared | Rango de presión recomendado (MPa) |
---|---|
>5mm | 50-90 |
<3mm | 80-140 |
Pasar por alto los factores de diseño del molde
El tamaño de la puerta y los sistemas de correderas desempeñan funciones vitales. Un tamaño de puerta grande permite que el material fluya libremente, como abrir compuertas. Las compuertas más pequeñas exigen más presión para un flujo fluido.
De manera similar, un sistema de canal caliente eficiente puede disminuir la presión entre 10 y 30 MPa en comparación con un sistema frío.
Ignorar las pruebas y la optimización del molde
Producir sin pruebas de moldes es como empezar un viaje sin un mapa: es arriesgado. Utilizo datos y realizo pruebas, ajustando la configuración lentamente. Encontrar el punto óptimo es fundamental para conseguir rellenos perfectos, evitando burbujas y marcas de flujo.
La configuración inicial debe basarse en datos empíricos, pero es fundamental realizar ajustes durante las pruebas de molde.
Consideraciones adicionales
Documentar los parámetros exitosos es clave para la coherencia; es como guardar recetas de buenos platos: ayuda a replicar el éxito de manera consistente.
Al evitar estos errores comunes, garantiza una mejor calidad del producto y eficiencia del proceso.
Para leer más, piense en estos consejos de diseño de moldes 9 que probablemente mejoren su proceso.
Los materiales de alta viscosidad necesitan una presión de inyección más baja.FALSO
Los materiales de alta viscosidad como el policarbonato requieren presiones de inyección más altas.
Las paredes más gruesas requieren una presión de inyección más baja.Verdadero
Las paredes de producto más gruesas generalmente necesitan presiones de inyección más bajas para llenarse adecuadamente.
Conclusión
La presión de inyección óptima en el moldeo varía según la viscosidad del material, la estructura del producto y el diseño del molde, y generalmente oscila entre 30 y 150 MPa, lo que requiere pruebas empíricas para realizar ajustes precisos.
-
Descubra cómo los diferentes sistemas de rodetes pueden influir en la presión de inyección y la eficiencia general del molde. ↩
-
Explore cómo las diferentes viscosidades afectan los requisitos de presión de inyección para diversos materiales. ↩
-
Conozca las propiedades del policarbonato para comprender por qué requiere presiones de inyección más altas. ↩
-
Comprender la viscosidad del material es crucial para establecer las presiones de inyección correctas y evitar defectos. ↩
-
Comprender la viscosidad ayuda a determinar las presiones de inyección adecuadas para diferentes materiales. ↩
-
Un sistema de guías bien diseñado puede reducir la resistencia y optimizar los ajustes de presión. ↩
-
Explorar las mejores prácticas puede conducir a una mayor eficiencia y calidad del producto. ↩
-
Descubra por qué comprender la viscosidad es esencial para establecer presiones de inyección correctas y mejorar la calidad del llenado. ↩
-
Explore estrategias prácticas de diseño de moldes que optimicen los ajustes de presión de inyección y prevengan defectos comunes. ↩