¿Alguna vez se ha enfrentado a la frustración de que un producto se atasque en el molde? No estás solo.
Un desmoldeo irregular en el moldeo por inyección puede deberse a un diseño inadecuado del molde, una presión de inyección excesiva o una selección inadecuada del material. Para afrontar estos desafíos, optimizar el diseño del molde, ajustar los parámetros de inyección y elegir los materiales adecuados son pasos esenciales.
¡Pero no te quedes aquí! Hay una gran cantidad de ideas para explorar que pueden transformar su proceso de producción. Profundicemos en los matices y estrategias que pueden mejorar sus resultados.
Una presión de inyección excesiva provoca problemas de desmoldeo.Verdadero
La alta presión de inyección aumenta la fuerza de sujeción, lo que complica el desmolde.
- 1. ¿Cómo afecta el diseño del molde a la eficiencia del desmoldeo?
- 2. ¿Qué papel juega la presión de inyección en los desafíos de desmoldeo?
- 3. ¿Cómo puede afectar la selección de materiales al éxito del desmoldeo?
- 4. ¿Qué técnicas adicionales pueden mejorar los resultados del desmoldeo?
- 5. Conclusión
¿Cómo afecta el diseño del molde a la eficiencia del desmoldeo?
Las complejidades del diseño de moldes pueden influir drásticamente en la eficiencia del desmolde, lo que afecta la calidad del producto y la velocidad de producción.
El diseño del molde es crucial para la eficiencia del desmolde. Los aspectos clave incluyen la pendiente de desmoldeo, la rugosidad de la superficie y la complejidad estructural. La optimización de estos factores minimiza la resistencia durante el desmolde, garantizando procesos de producción más fluidos.
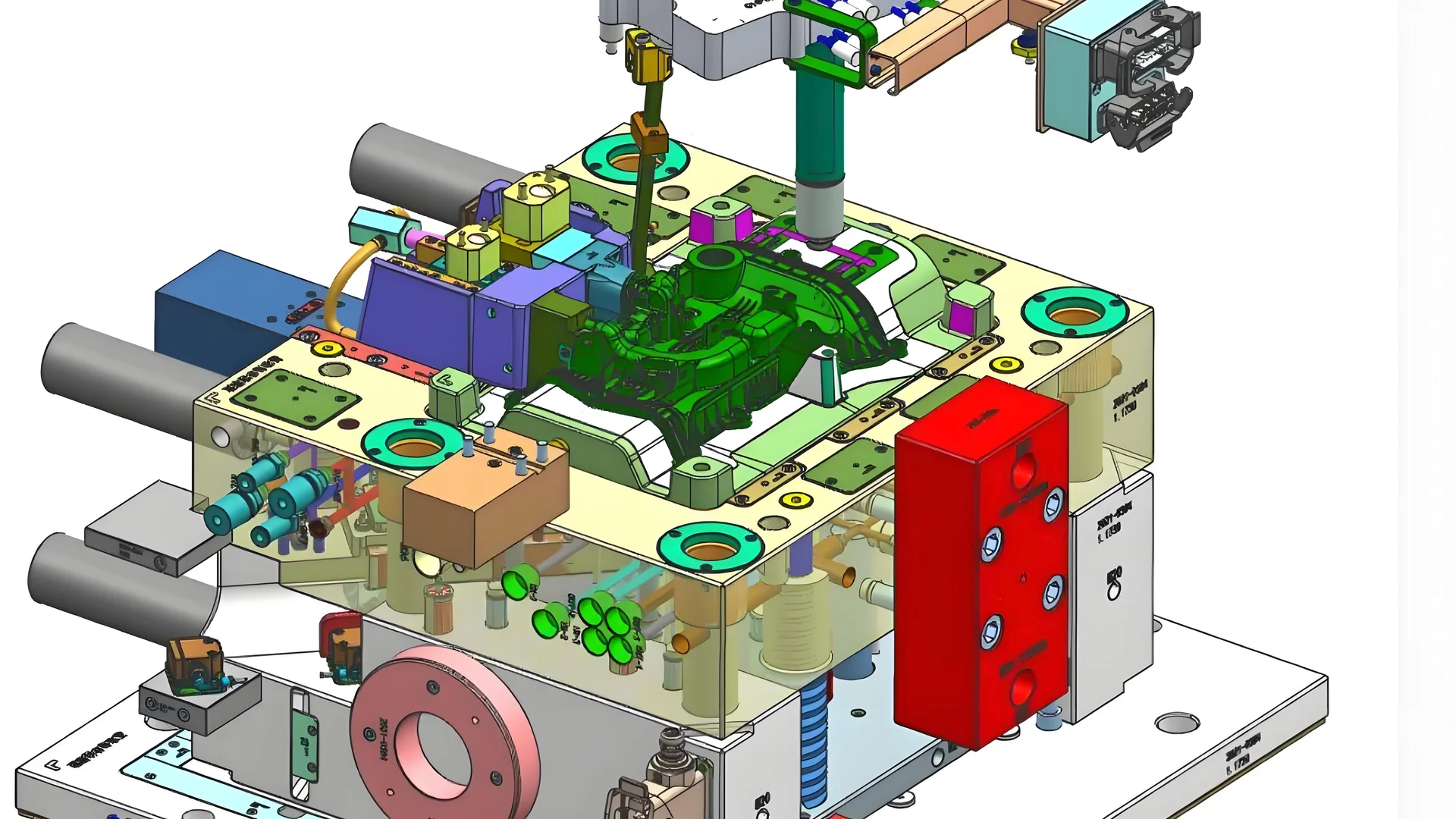
La importancia de desmoldar taludes
La pendiente de desmolde 1 es un aspecto fundamental que determina la facilidad con la que se puede desmoldar un producto. Una pendiente insuficiente puede provocar resistencias importantes, provocando un desencofrado irregular. Normalmente, se recomienda una pendiente de entre 1° y 3° para facilitar una expulsión suave.
Rugosidad superficial y sus implicaciones
La alta rugosidad de la superficie del molde aumenta la fricción entre el producto y el molde. Esta fricción puede dificultar el desmolde, provocando que el producto se pegue o se deforme. Pulir el molde puede reducir sustancialmente esta fricción, mejorando la eficiencia del proceso de desmoldeo.
Estructuras de moldes complejas
Los moldes con diseños complejos, como cavidades profundas y socavaduras, suponen un desafío en el desmoldeo. Estas características pueden hacer que las piezas queden atrapadas o dañadas durante la expulsión. El uso de mecanismos como controles deslizantes y eyectores inclinados puede ayudar a mitigar estos problemas al simplificar el proceso de eliminación.
Problema | Solución |
---|---|
Pendiente de desmoldeo insuficiente | Aumentar la pendiente a 1° – 3° |
Alta rugosidad superficial | Molde polaco para reducir la rugosidad. |
Estructuras de molde complejas | Utilice controles deslizantes/expulsores inclinados para facilitar el desmoldeo |
Considerando los factores materiales
Al centrarse en el diseño de moldes, es esencial no pasar por alto las propiedades del material. Los materiales con alta contracción o poca fluidez pueden exacerbar los problemas de desmoldeo, por lo que es vital seleccionar materiales apropiados que complementen el diseño del molde.
No se puede subestimar el papel del diseño de moldes en la eficiencia del desmolde. Al optimizar elementos clave como la pendiente de desmoldeo, el acabado de la superficie y la complejidad estructural, los fabricantes pueden mejorar significativamente sus procesos de producción y la calidad del producto.
Una pendiente de desmoldeo de 2° es óptima para una expulsión suave.Verdadero
Se recomienda una pendiente de entre 1° y 3° para un desmolde eficaz.
La alta rugosidad de la superficie mejora la eficiencia del desmoldeo.FALSO
La elevada rugosidad superficial aumenta la fricción, dificultando el desmolde.
¿Qué papel juega la presión de inyección en los desafíos de desmoldeo?
La presión de inyección es un factor crítico en el proceso de moldeo por inyección e influye directamente en los desafíos del desmolde.
Una presión de inyección excesiva puede provocar un aumento de la fuerza de sujeción, lo que dificulta el desmoldeo. Al optimizar la presión de inyección y los parámetros relacionados, los fabricantes pueden aliviar estos desafíos, garantizando un desmoldeo más suave y productos de mayor calidad.

Comprender la presión de inyección
La presión de inyección es la fuerza utilizada para inyectar plástico fundido en un molde. Debe controlarse cuidadosamente para garantizar que el material llene el molde de forma completa y uniforme. Sin embargo, demasiada presión puede provocar complicaciones, especialmente durante la etapa de desmoldeo.
Cómo la presión de inyección excesiva causa problemas
Cuando la presión de inyección es demasiado alta, puede exacerbar los siguientes problemas:
- Mayor fuerza de sujeción: la alta presión aumenta la fuerza que sujeta el producto dentro del molde, lo que genera más fricción y dificultad durante el desmolde.
- Potencial de daño a la pieza: la tensión adicional sobre el molde y la pieza puede causar defectos como deformaciones o grietas.
Equilibrio de la presión de inyección para un desmoldeo óptimo
Para afrontar estos desafíos, los fabricantes deberían considerar:
- Reducción de la presión de inyección: Disminuir la presión puede reducir la fuerza de sujeción, lo que facilita la extracción de piezas sin dañarlas.
- Ajuste del tiempo de retención: Al acortar el tiempo de retención, se puede garantizar que el proceso de enfriamiento no se prolongue innecesariamente, reduciendo así la contracción y facilitando el desmolde.
Aplicaciones y ajustes del mundo real
Una presión de inyección bien equilibrada es vital para producir componentes de alta calidad. Los fabricantes suelen realizar la optimización de procesos 2 ajustando varios parámetros, incluidos la presión, la temperatura y el tiempo del ciclo, para afinar sus operaciones.
Tabla: Efectos de los ajustes de presión de inyección
Estrategia de ajuste | Impacto en el desmoldeo |
---|---|
Reducir la presión de inyección | Disminuye la fuerza de sujeción; facilita el desmolde |
Acortar el tiempo de espera | Reduce la contracción por enfriamiento; eliminación del sida |
La incorporación de un enfoque sistemático para evaluar los parámetros de presión 3 puede ayudar a mantener un equilibrio entre una producción eficiente y el aseguramiento de la calidad. La implementación de sistemas de seguimiento y control periódicos garantiza que se utilicen de forma consistente los ajustes óptimos.
La alta presión de inyección aumenta la dificultad de desmoldeo.Verdadero
Una presión excesiva aumenta la fuerza de sujeción, lo que dificulta el desmoldeo.
Reducir la presión de inyección siempre daña las piezas.FALSO
Reducir la presión puede facilitar el desmoldeo sin dañar las piezas.
¿Cómo puede afectar la selección de materiales al éxito del desmoldeo?
Elegir el material adecuado es crucial para lograr un desmolde exitoso en los procesos de moldeo por inyección.
La selección del material influye en el éxito del desmoldeo al influir en las tasas de contracción y la fluidez. Optar por materiales con una contracción mínima y buenas características de flujo puede evitar problemas de desmoldeo y garantizar un proceso de producción más fluido.

Comprender la contracción del material
La contracción del material es un factor vital que afecta el éxito del desmoldeo. Durante el enfriamiento, los plásticos tienden a contraerse y una contracción excesiva puede hacer que la pieza moldeada se adhiera al molde, complicando el proceso de desmoldeo. La elección de materiales con tasas de contracción más bajas, como grados específicos de polipropileno o policarbonato, puede mitigar este problema.
Las tasas de contracción pueden variar significativamente entre los plásticos. Por ejemplo, el polipropileno 4 generalmente tiene una tasa de contracción de aproximadamente el 1-2%, mientras que el nailon puede encogerse hasta un 3-4%. La selección de materiales con contracción controlada ayuda a mantener la estabilidad dimensional y reduce las tensiones residuales en las piezas moldeadas.
Mejora de la fluidez del material
La fluidez del material determina qué tan bien fluye el plástico dentro del molde. Una fluidez deficiente puede provocar un llenado desigual y defectos, lo que dificulta el desmoldeo. Se puede mejorar la fluidez utilizando materiales que posean inherentemente mejores propiedades de flujo o incorporando aditivos como plastificantes.
Por ejemplo, el uso de ABS (acrilonitrilo butadieno estireno), conocido por sus excelentes características de flujo, puede mejorar los resultados del desmolde. Además, aditivos 5 como lubricantes para mejorar aún más el flujo, facilitando una extracción más fácil del molde.
Equilibrio entre rendimiento y desmoldeabilidad
Al seleccionar materiales, es fundamental equilibrar el rendimiento con la desmoldeabilidad. Algunos plásticos de alto rendimiento pueden ofrecer una resistencia excelente, pero plantean desafíos durante el desmolde debido a una alta contracción o características de flujo deficientes. Los ingenieros deben sopesar estos factores con las propiedades deseadas del producto final.
La incorporación de pruebas de materiales durante la fase de diseño puede proporcionar información valiosa sobre los posibles desafíos del desmolde. Este enfoque proactivo permite realizar ajustes en la selección de materiales, lo que garantiza que la producción se mantenga fluida sin comprometer la calidad del producto.
Al comprender estos aspectos de la selección de materiales, los fabricantes pueden optimizar sus procesos de moldeo por inyección, mejorando tanto la eficiencia como la calidad de la producción.
El polipropileno tiene una tasa de contracción del 1-2% en el moldeado.Verdadero
El polipropileno normalmente se encoge entre un 1% y un 2%, lo que ayuda a un desmoldeo predecible.
La tasa de contracción del nailon es menor que la del polipropileno en el moldeado.FALSO
El nailon se encoge entre un 3 y un 4%, más que el polipropileno, lo que afecta el desmoldeo.
¿Qué técnicas adicionales pueden mejorar los resultados del desmoldeo?
Dominar las técnicas de desmoldeo es esencial para mejorar la productividad en las operaciones de moldeo por inyección.
Las técnicas adicionales para mejorar los resultados del desmoldeo incluyen el uso de agentes desmoldantes, vibraciones ultrasónicas y tratamientos de superficie. La implementación de estos métodos puede reducir la fricción, mejorar el desmoldeo y prevenir defectos.
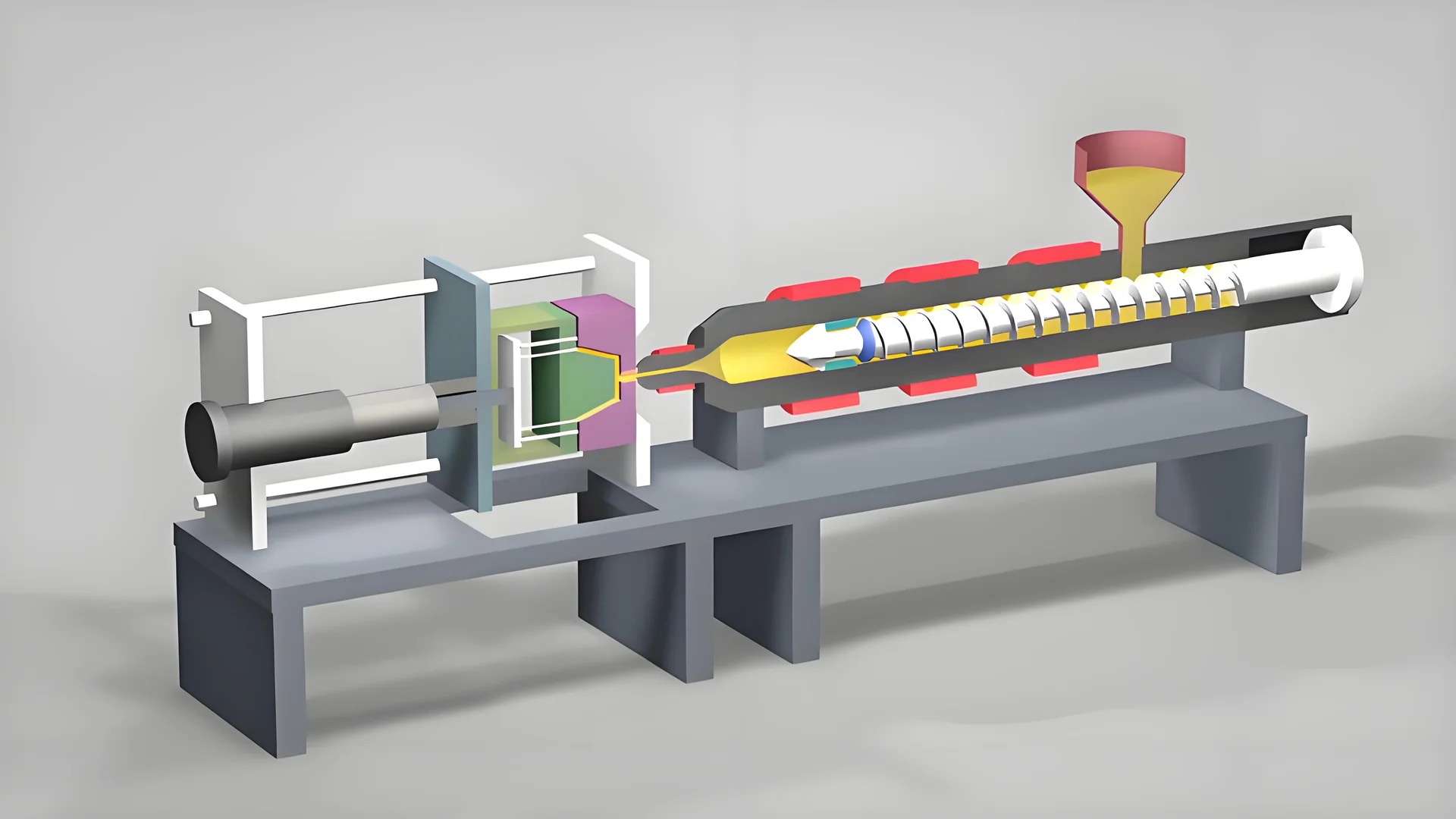
Uso de agentes de liberación
La aplicación de agentes desmoldantes es una técnica común para facilitar el desmolde reduciendo la fricción entre el producto y el molde. Estos agentes forman una fina película que impide la adhesión, facilitando la expulsión de la pieza moldeada sin dañarla. Sin embargo, un uso excesivo puede afectar el acabado superficial del producto, por lo que se debe controlar cuidadosamente.
Integración de vibraciones ultrasónicas
Las vibraciones ultrasónicas pueden mejorar significativamente la eficiencia del desmoldeo. Al colocar transductores ultrasónicos en el molde, se inducen vibraciones de alta frecuencia, lo que reduce la adherencia entre el molde y la pieza. Este método es especialmente beneficioso para geometrías complejas y puede reducir el tiempo del ciclo al facilitar el proceso de expulsión. Para obtener más información, explore los beneficios del desmolde ultrasónico 6 .
Tratamientos superficiales de moldes
Los tratamientos superficiales, como el recubrimiento con cromo duro o nitruro, pueden reducir la rugosidad de la superficie del molde, disminuyendo así la fricción durante el desmoldeo. Estos tratamientos no solo mejoran las propiedades de desmoldeo sino que también aumentan la durabilidad y la vida útil del molde. Un examen detallado de los tratamientos de la superficie del molde 7 puede ofrecer información adicional para seleccionar los métodos adecuados para sus necesidades específicas.
Optimización de sistemas de refrigeración
Los sistemas de refrigeración eficientes pueden conducir a mejores resultados de desmoldeo al garantizar una refrigeración uniforme y minimizar las tensiones residuales en la pieza moldeada. El enfriamiento uniforme ayuda a mantener la estabilidad dimensional y reduce las posibilidades de deformación o adherencia. Considere investigar tecnologías de refrigeración avanzadas 8 para comprender cómo se pueden integrar en los sistemas existentes.
Implementación de Soluciones de Automatización
La automatización en los procesos de desmoldeo puede agilizar las operaciones y mejorar la coherencia. Los sistemas robóticos equipados con sensores pueden controlar con precisión la fuerza y la velocidad de expulsión, minimizando los defectos asociados con la manipulación manual. Conozca las soluciones de desmoldeo automatizado 9 para ver cómo pueden revolucionar su línea de producción.
Los desmoldantes evitan la adherencia en el desmolde.Verdadero
Los desmoldantes forman una película que reduce la fricción, favoreciendo el desmoldeo.
Las vibraciones ultrasónicas aumentan la rugosidad de la superficie del molde.FALSO
Las vibraciones ultrasónicas reducen la adherencia, no aumentan la rugosidad de la superficie.
Conclusión
Al abordar los defectos de diseño del molde y optimizar los procesos, puede mitigar eficazmente los problemas de desmolde. ¡Mejoremos juntos la calidad del producto y la eficiencia operativa!
-
Descubra los ángulos ideales para una expulsión eficiente del producto: Para garantizar la posición óptima de un hueso, su ángulo de inclinación cero normalmente debe oscilar entre 0,25 y 1, con un tamaño superior mínimo absoluto... ↩
-
Explore técnicas para ajustar el moldeo por inyección para mejorar la calidad: Pasos para la optimización del proceso de MOLDEO POR INYECCIÓN · 1. Examen de la funcionalidad de la herramienta · 2. Pruebas de disparo corto · 3. Estudios de sello de puerta · 4. Evaluación/datos de piezas de muestra... ↩
-
Aprenda métodos para evaluar y ajustar la presión de inyección de manera efectiva: La presión de inyección generalmente se mide en libras por pulgada cuadrada (psi) o bares (1 bar = 14,5 psi). Es uno de los factores más importantes... ↩
-
Conozca las características de contracción del polipropileno para mejorar la eficiencia del desmoldeo: La tasa de contracción del plástico es una tasa de contracción del volumen de los polímeros desde el estado fundido y el estado enfriado que determinará la dimensión de las piezas de moldeo... ↩
-
Descubra aditivos que mejoran el flujo del plástico para un mejor desmoldeo. El carbono y el vidrio son aditivos de materiales comúnmente utilizados que añaden integridad estructural, dureza y rigidez a un termoplástico. Ellos son … ↩
-
Descubra cómo las vibraciones ultrasónicas mejoran la eficiencia del desmoldeo: En un ciclo de tiempo relativamente corto, el moldeo por ultrasonidos puede procesar una amplia variedad de materiales poliméricos sin ningún efecto térmico perceptible... ↩
-
Descubra varios tratamientos de superficie para mejorar el rendimiento del molde: En este episodio, Gordon Styles analiza 4 tipos de tratamientos de superficie para inyección de plástico... ↩
-
Explore sistemas de refrigeración innovadores para optimizar sus procesos. Descubra las ventajas de la tecnología de calor y frío para el moldeo por inyección de plástico. Mejore la eficiencia, reduzca los tiempos de ciclo y garantice una calidad superior con... ↩
-
Comprenda cómo la automatización mejora la eficiencia en el desmoldeo. Experiencia en automatización del moldeo por inyección en todos los niveles: desde la máquina de moldeo por inyección hasta el robot y los sistemas transportadores y los equipos periféricos. ↩