Crear la superficie de separación perfecta en el moldeo por inyección puede cambiar las reglas del juego para la calidad del producto. ¿Pero cómo lo logras cada vez?
Las técnicas de diseño óptimas para las superficies de separación de moldes de inyección enfatizan la forma, la apariencia y la facilidad de procesamiento del producto, lo que garantiza un desmolde suave, defectos mínimos y una fabricación eficiente.
Sabes, cuando comencé a trabajar con moldes de inyección, me sentí abrumado por todos los detalles que necesitaban atención. Fue como armar un rompecabezas complejo donde cada pieza tenía que encajar perfectamente para crear algo realmente extraordinario. Con el tiempo, me di cuenta de que dominar el diseño de superficies de separación es como encontrar la última pieza de un rompecabezas: es crucial para lograr un acabado impecable.
Profundicemos en algunas estrategias que me han ayudado a perfeccionar mi enfoque. Para formas simples, como una copa cilíndrica, colocar la superficie de separación a lo largo del contorno máximo simplifica la estructura del molde. Pero cuando se trata de formas complejas, garantizar un desmolde suave se convierte en la clave. He aprendido que utilizar mecanismos de extracción de núcleos laterales para socavados o superficies de separación escalonadas para diferentes características puede marcar la diferencia.
La apariencia también juega un papel muy importante, especialmente en superficies de alta calidad como los interiores de los automóviles. Evitar las líneas de separación puede evitar rebabas y marcas de soldadura antiestéticas. Y no se olvide de la comodidad de procesamiento. Elegir superficies planas en lugar de curvas facilita el fresado y el rectificado, lecciones que aprendí de la manera más difícil durante las noches en el taller.
La incorporación de estas técnicas no sólo mejora la calidad del producto moldeado sino que también agiliza el proceso de fabricación. Créame, una vez que haya logrado estos diseños, sus proyectos pasarán de buenos a excelentes en poco tiempo.
Las superficies de separación influyen en la calidad de la apariencia del producto.Verdadero
El diseño adecuado de las superficies de separación minimiza los defectos visibles y mejora la apariencia.
Ignorar la forma en el diseño conduce a un desmolde eficiente.FALSO
Tener en cuenta la forma es fundamental para un desmolde suave y evitar defectos.
- 1. ¿Cómo influye la forma del producto en el diseño de la superficie de separación?
- 2. ¿Por qué los requisitos de apariencia son cruciales para las superficies de separación?
- 3. ¿Cuáles son las consideraciones de procesamiento y ensamblaje para superficies de partición?
- 4. ¿Cómo afecta el proceso de moldeo por inyección al diseño de la superficie de partición?
- 5. ¿Cuáles son los desafíos y soluciones comunes en el diseño de superficies de partición?
- 6. Conclusión
¿Cómo influye la forma del producto en el diseño de la superficie de separación?
¿Alguna vez se preguntó cómo la forma de un producto puede dictar todo el diseño de su molde? Permítame explicarle este fascinante aspecto de la fabricación.
La forma del producto afecta el diseño de la superficie de separación al determinar la complejidad del molde y la facilidad de desmoldeo. Las formas simples permiten líneas de separación sencillas, mientras que las formas intrincadas requieren diseños complejos para gestionar características como los cortes.

Los fundamentos del diseño de superficies de partición
Todavía recuerdo mi primera experiencia práctica con el moldeo por inyección. Recién estaba comenzando y la idea de crear una superficie de separación parecía desalentadora. Imagínese esto: la superficie de separación 1 es donde se unen las dos mitades del molde, lo cual es crucial para permitir que el producto se retire fácilmente. Es sorprendente cuánto influye la forma de un producto en esta configuración.
Formas simples versus complejas
Cuando traté por primera vez con formas simples (piense en cilindros o cuboides), el proceso fue más sencillo. A menudo es posible alinear la línea de separación a lo largo del contorno más grande, lo que simplifica la construcción del molde y reduce los costos. Recuerdo un proyecto de copa cilíndrica en el que alinear la línea de separación con el eje central hacía que todo encajara en su lugar. Es casi como encontrar la pieza perfecta del rompecabezas.
Tipo de forma | Consideraciones |
---|---|
Simple | Alinear con el contorno máximo |
Complejo | Garantizar un desmoldeo suave |
Pero cuando se trata de formas complejas , como aquellas con recortes o características direccionales múltiples, la cosa se vuelve más complicada. Una vez abordé un proyecto con características complejas que requerían mecanismos de extracción de núcleos laterales; imagínelos como pequeños ninjas del molde trabajando detrás de escena para manejar puntos difíciles.
Impacto en la apariencia y la funcionalidad
Para productos que necesitan una alta calidad estética, como la electrónica de consumo, es fundamental ocultar o minimizar las líneas de separación. Aprendí esto de la manera más difícil cuando incluso la más mínima marca de soldadura se destacaba en la elegante carcasa de un dispositivo. Para materiales transparentes, es aún más complicado; Los defectos en la superficie de separación pueden ser notoriamente obvios y afectar tanto a la transparencia como a las propiedades ópticas.
Desafíos de procesamiento y ensamblaje
Tener en cuenta tanto la conveniencia del procesamiento como los requisitos de ensamblaje es vital en el diseño de la superficie de separación 2 . A menudo utilizo pasadores o llaves de localización para mantener la alineación durante el montaje. Es un poco como montar bloques de Lego: quieres que todo encaje perfectamente para un funcionamiento perfecto.
Consideraciones sobre el proceso de moldeo por inyección
Finalmente, la superficie de separación debe soportar un flujo y ventilación de plástico eficiente durante el moldeo por inyección. He visto de primera mano cómo las compuertas y los canales de ventilación colocados correctamente pueden evitar problemas como disparos cortos o gases atrapados, que pueden degradar la calidad del producto.
Equilibrar todos estos factores no se trata sólo de conocimientos técnicos; se trata de comprender cómo cada elección afecta tanto a la eficiencia de la producción como a la calidad del producto. Es un rompecabezas donde cada pieza importa.
Las formas simples permiten una fácil colocación de la línea de separación.Verdadero
Las formas simples, como los cilindros, permiten una alineación sencilla de la línea de separación.
Las formas complejas nunca requieren mecanismos centrales laterales.FALSO
Las formas complejas a menudo necesitan núcleos laterales para desmoldar elementos intrincados.
¿Por qué los requisitos de apariencia son cruciales para las superficies de separación?
¿Alguna vez te has preguntado por qué el aspecto de las superficies de separación es tan importante? Profundicemos en cómo la apariencia afecta tanto a la calidad como a la estética de los productos moldeados.
Los requisitos de apariencia para las superficies de separación son cruciales para mejorar el atractivo visual y la funcionalidad de los productos plásticos al prevenir defectos como rebabas y marcas de soldadura, lo que da como resultado un producto más atractivo.

Comprensión de las superficies de separación y su función
Cuando profundicé por primera vez en el mundo del moldeo por inyección 3 , rápidamente aprendí que las superficies de separación (donde se unen las dos mitades de un molde) son fundamentales. La forma en que se diseñan estas superficies puede hacer o deshacer el proceso de fabricación, lo que afecta el aspecto del producto final. Si el diseño no es correcto, podría terminar con rebabas (exceso de material que se filtra) o líneas de soldadura visibles, las cuales pueden arruinar la estética de un producto.
Equilibrio entre funcionalidad y estética
Recuerdo haber trabajado en un proyecto para un elegante dispositivo electrónico. Había mucho en juego porque cualquier defecto podría desanimar a los compradores potenciales. Para productos tan importantes, especialmente aquellos con materiales transparentes, es fundamental garantizar líneas de separación impecables. Incluso una pequeña imperfección puede llamar la atención y estropear todo el look. Esto significa colocar el molde y la puerta correctamente para evitar estas imperfecciones.
Factores que influyen en el diseño de la superficie de separación
Consideración | Descripción |
---|---|
Forma del producto | Las formas simples permiten un diseño más sencillo; Las formas complejas pueden necesitar técnicas avanzadas como la extracción lateral del núcleo. |
Tipo de material | Los materiales transparentes exigen una cuidadosa consideración para evitar defectos que afecten a la claridad. |
Procesamiento de moldes | La precisión es clave; Las superficies curvas pueden requerir equipos especiales como máquinas de electroerosión. |
Consejos prácticos para diseñadores
Según mi experiencia, elegir planos para las superficies de separación simplifica tanto el procesamiento como el montaje. Tomemos como ejemplo las formas cúbicas; La colocación de las superficies de separación a lo largo de su contorno máximo hace que el molde sea sencillo y la producción más fluida.
Cuando entran en juego las nervaduras de refuerzo, alinear las líneas de separación paralelas a ellas es clave para no alterar su estructura. Siguiendo estas estrategias, me ha resultado mucho más fácil producir diseños que sean funcionales y agradables a la vista.
Un mal diseño de la superficie de separación provoca defectos de rebaba.Verdadero
Los defectos de rebaba ocurren cuando el exceso de material se filtra debido a un cierre inadecuado del molde.
Todos los materiales tienen los mismos requisitos de superficie de separación.FALSO
Los diferentes materiales, especialmente los transparentes, requieren consideraciones específicas para evitar defectos.
¿Cuáles son las consideraciones de procesamiento y ensamblaje para superficies de partición?
¿Alguna vez se ha preguntado por qué las superficies de separación en el diseño de moldes son tan importantes?
Elija las superficies de separación con cuidado para optimizar el procesamiento del molde, facilitar el montaje y mantener la calidad del producto, teniendo en cuenta la forma, la estética, la simplicidad del procesamiento y las necesidades de ventilación.
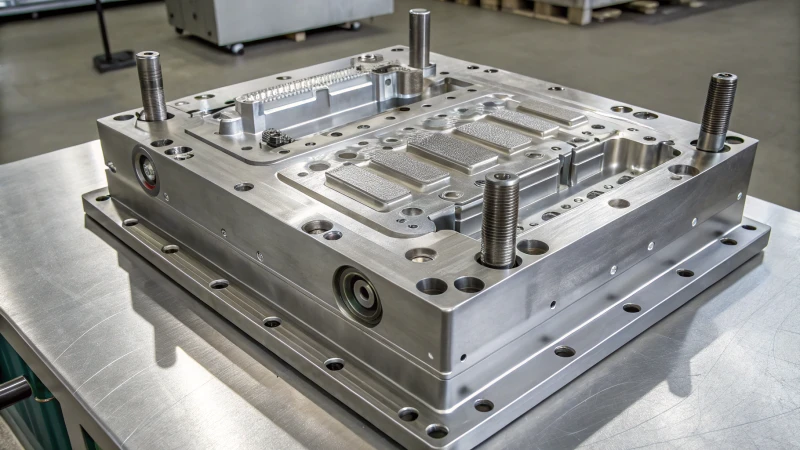
Consideraciones sobre la forma del producto
Recuerdo mi primer proyecto con un producto cilíndrico simple. Alinear la superficie de separación con el contorno máximo 4 fue un punto de inflexión. No sólo simplificó el diseño del molde sino que también facilitó el procesamiento. Para formas más complejas, como aquellas con socavaduras, aprendí por las malas que una superficie de separación escalonada podría hacer maravillas, permitiendo que se moldeen diferentes características a diferentes profundidades.
Requisitos de apariencia
Hubo un momento en el que trabajé en una pieza interior de automóvil de alta calidad. La ubicación de la superficie de separación fue fundamental para evitar marcas de soldadura antiestéticas o rebabas, que podrían arruinar el aspecto del producto. Descubrí que para artículos transparentes, colocar las puertas latentes 5 con cuidado puede mejorar drásticamente la transparencia al estabilizar el flujo de fusión.
Facilidad de procesamiento y montaje
Siempre he buscado superficies de separación planas siempre que sea posible porque simplifican el procesamiento con técnicas de fresado convencionales. Sin embargo, cuando el trabajo requería superficies curvas, tenía que depender de equipos especializados como la electroerosión. El montaje se volvió mucho más fácil cuando se trataba de ubicar los pasadores, asegurando que todo estuviera perfectamente alineado.
Proceso de moldeo por inyección
Siempre me ha fascinado el flujo de plástico fundido dentro de una cavidad de molde 6 Una vez tuve problemas con tomas cortas hasta que me di cuenta de la importancia de la posición estratégica de la puerta para guiar la masa fundida de manera uniforme a través de la cavidad. La ventilación adecuada también es crucial: un proyecto me enseñó que los canales de ventilación bien diseñados pueden evitar defectos causados por el aire atrapado, especialmente en el moldeo por inyección de alta velocidad.
Aspecto | Consideración |
---|---|
Forma | Simple versus complejo |
Apariencia | Alta calidad versus transparente |
Tratamiento | Superficies planas versus curvas |
Asamblea | Alineación y facilidad de apertura |
Moldeo por inyección | Requisitos de flujo y ventilación |
Estos conocimientos han sido invaluables para perfeccionar mi enfoque en el diseño de moldes, garantizando que tanto la funcionalidad como la estética cumplan con los estándares de la industria, especialmente en campos exigentes como la electrónica de consumo y la fabricación de automóviles.
Las formas simples requieren superficies de separación complejas.FALSO
Las formas simples, como los cilindros, se alinean con el contorno máximo, simplificando el molde.
Las superficies de separación afectan el flujo del moldeo por inyección.Verdadero
El diseño afecta el flujo de fusión del plástico, evitando disparos cortos o áreas estancadas.
¿Cómo afecta el proceso de moldeo por inyección al diseño de la superficie de partición?
¿Alguna vez se preguntó cómo algo tan simple como una superficie de separación puede afectar todo el proceso de moldeo por inyección?
El moldeo por inyección afecta el diseño de la superficie de separación al influir en el desmolde, el flujo del plástico y la apariencia. La colocación correcta de la línea de partición mejora el rendimiento del molde y la calidad del producto.
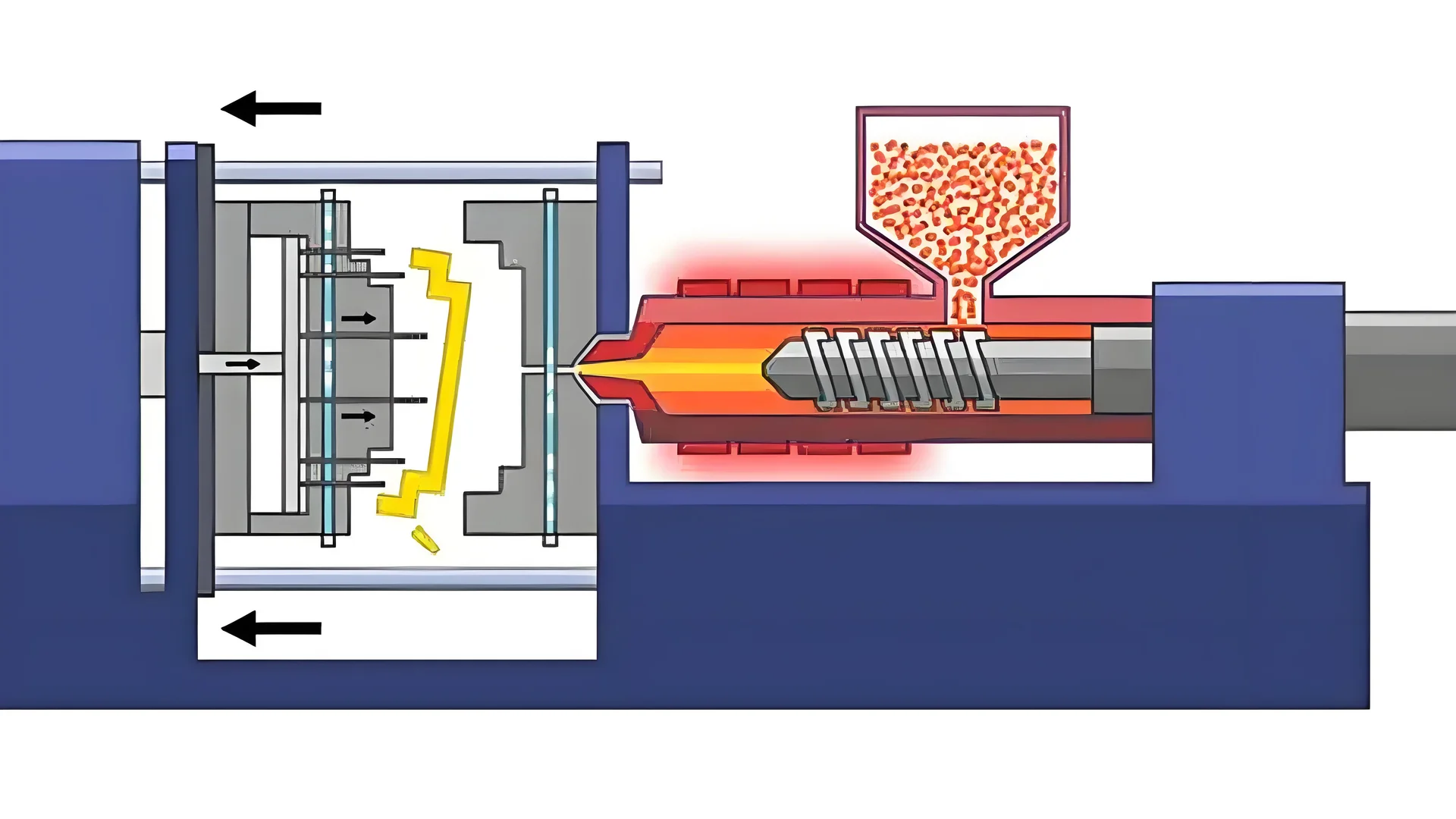
Cuando comencé a diseñar moldes, nunca imaginé lo complejo que sería el proceso, en particular el diseño de la superficie de separación. Al principio parecía sencillo, pero a medida que profundicé, me di cuenta de que es una forma de arte que exige atención al detalle y una buena comprensión de los requisitos del producto.
Consideraciones clave en el diseño de superficies de partición
El diseño de una superficie de separación requiere equilibrar múltiples factores para garantizar un funcionamiento eficaz del molde y productos de alta calidad. Exploremos algunas consideraciones esenciales:
1. Forma y complejidad del producto
La forma del producto plástico influye en gran medida en el diseño de la superficie de separación. Para productos con formas simples 7 como una copa cilíndrica, colocar la línea de separación en el contorno máximo simplifica enormemente la vida. Es como encontrar la costura perfecta en un trozo de tela: todo encaja en su lugar.
Pero luego hay formas complejas, llenas de socavados y características que me recuerdan a resolver un rompecabezas en 3D. Estos requieren mecanismos especiales, como tirar del núcleo lateral, para garantizar que todo se desmolde sin problemas. Si es factible, el desmolde forzado puede ser una opción, siempre que la elasticidad del material lo soporte.
2. Requisitos de apariencia
Los requisitos estéticos afectan significativamente las decisiones sobre la superficie de separación, especialmente para productos de alta visibilidad como interiores de automóviles o carcasas electrónicas. Se presionó para ocultar las líneas de separación para evitar que las marcas de soldadura y rebabas arruinaran esa apariencia impecable.
En el caso de los productos transparentes, cada pequeño defecto se magnifica, casi como una huella digital sobre el vidrio. El uso de puertas latentes se vuelve crucial para estabilizar el flujo y mantener invisibles esas líneas de separación.
3. Procesamiento y Montaje
La facilidad de procesamiento y montaje es otro aspecto crítico. Al procesar piezas con superficies planas, un simple fresado o rectificado es suficiente.
Por el contrario, cuando trabajas con curvas, es como entrar en un mundo completamente nuevo donde las máquinas de electroerosión y CNC se convierten en tus mejores amigas. Durante el montaje, alinear todo con pasadores de localización garantiza que todas las piezas del rompecabezas encajen perfectamente sin interferencias.
4. Dinámica del moldeo por inyección
La dinámica del flujo de plástico durante el moldeo por inyección es fundamental en el diseño de la superficie de separación. Una superficie bien planificada debe promover un llenado uniforme de la cavidad para evitar disparos cortos o áreas estancadas.
Se trata de guiar el flujo de plástico de manera eficiente a través de la cavidad con posiciones de entrada bien planificadas en relación con la línea de separación.
Consideraciones de ventilación
La ventilación eficaz durante el moldeo por inyección es vital para evitar defectos causados por el aire atrapado o la descomposición del gas. Una superficie de separación bien diseñada también funciona como canal de ventilación; por lo tanto, diseñar ranuras de ventilación o aprovechar los espacios naturales entre las superficies puede mejorar el rendimiento del molde.
Con estos conocimientos, diseñar una superficie de separación se convierte en algo más que una simple tarea técnica; se trata de crear una obra de arte que cumpla con los objetivos estéticos y de fabricación. Si tiene curiosidad por saber más sobre estas consideraciones, consulte recursos adicionales 8 .
El diseño de la superficie de separación afecta la complejidad del molde.Verdadero
Una superficie de separación bien diseñada simplifica la estructura del molde y reduce la complejidad.
Las superficies de partición curvas son más fáciles de procesar que las planas.FALSO
Las superficies curvas requieren procesos especializados como la electroerosión, a diferencia de las planas.
¿Cuáles son los desafíos y soluciones comunes en el diseño de superficies de partición?
Al navegar por el intrincado mundo del diseño de moldes, me he enfrentado a una buena cantidad de desafíos, especialmente cuando se trata de crear la superficie de separación perfecta.
Los desafíos del diseño de superficies de partición incluyen formas complejas y estándares estrictos. Las soluciones implican la selección estratégica de superficies, la optimización de las compuertas y técnicas de ventilación efectivas para garantizar una producción de moldes de calidad.

Comprender la forma de los productos plásticos
En mi viaje a través del laberinto de superficies de separación de moldes de inyección 9 , aprendí rápidamente que la forma de un producto plástico dicta gran parte de la estrategia de diseño.
-
Formas simples : para formas regulares como cuboides o cilindros, colocar la superficie de separación en el contorno máximo hace la vida mucho más fácil. Simplifica la estructura del molde y reduce los dolores de cabeza del procesamiento.
-
Formas complejas : los desafíos incluyen socavaduras que requieren mecanismos centrales laterales. Recuerdo que una vez abordé un proyecto en el que era necesario un desmolde forzado. Fue estresante asegurarse de que el material no se agrietara bajo presión, pero con una planificación cuidadosa, todo salió bien.
Requisitos de apariencia
No olvidemos la presión para cumplir con altos estándares estéticos, especialmente para interiores de automóviles o carcasas electrónicas.
-
Superficies de alta calidad : Cada detalle tenía que ser perfecto, minimizando las superficies de separación para evitar esos molestos defectos como rebabas o marcas de soldadura. Optimice la ubicación de las puertas para reducir estos problemas.
-
Productos transparentes : con los productos transparentes, era aún más complicado: cada imperfección resaltaba como un pulgar dolorido. Seleccione las superficies de separación con cuidado ya que los defectos son más visibles. Utilice puertas latentes para un flujo de fusión estable, mejorando la transparencia.
Procesamiento y ensamblaje de moldes
Cuando se trata de procesamiento y montaje, la comodidad es la clave.
-
Procesamiento : Diseñar superficies de separación planas para fresado de precisión me ahorró muchos dolores de cabeza. Las superficies curvas requirieron equipos CNC más avanzados, lo que desafió mis habilidades pero gratificó la precisión.
-
Montaje : Montar moldes es como armar un rompecabezas complejo. El diseño para un fácil montaje con pasadores de ubicación garantiza que todo se alinee perfectamente; es absolutamente imprescindible para evitar interferencias, especialmente cuando se trata de mecanismos deslizantes.
Proceso de moldeo por inyección
Una superficie de separación bien pensada puede mejorar o deshacer la eficiencia de los procesos de moldeo.
-
Rendimiento del flujo : Garantizar un flujo plástico fluido es crucial; Lo aprendí de primera mano con productos de paredes delgadas donde los pasos en falso conducían a tiros cortos. Coloque las superficies de separación para garantizar un flujo plástico suave y evite disparos cortos considerando las longitudes de las rutas de flujo.
-
Ventilación : La ventilación es otro aspecto crítico; El uso de superficies de separación como canales de ventilación puede mejorar enormemente la calidad del producto al expulsar el aire y los gases atrapados durante el moldeo. Implemente ranuras de ventilación para productos más grandes o procesos de alta velocidad para mejorar la calidad del producto.
Tabla: Desafíos comunes versus soluciones
Desafío | Solución |
---|---|
Formas complejas | Mecanismos de núcleo lateral o desmolde forzado |
Alta demanda de apariencia | Minimiza las superficies de separación, optimiza la ubicación de la puerta |
Dificultades de procesamiento | Superficies planas, mecanizado avanzado para curvas |
Problemas de ventilación | Canales de ventilación de la superficie de separación |
Al abordar estos desafíos de frente con soluciones estratégicas, los diseñadores pueden aumentar significativamente la calidad y la eficiencia 10 de los productos moldeados. Mis experiencias me han enseñado que con cada proyecto, siempre hay algo nuevo que aprender e innovar.
Las formas simples requieren superficies de separación complejas.FALSO
Las formas simples se benefician de superficies de separación sencillas, lo que simplifica el molde.
Los canales de ventilación mejoran la calidad del producto en el moldeado.Verdadero
Los canales de ventilación ayudan a expulsar el aire y los gases, evitando defectos.
Conclusión
Las técnicas de diseño eficaces para las superficies de separación de moldes de inyección mejoran la calidad del producto al considerar la forma, la apariencia, la conveniencia del procesamiento y la dinámica del moldeo por inyección para garantizar un desmolde suave y minimizar los defectos.
-
Este enlace explora por qué posicionar correctamente las líneas de separación es esencial para la eficacia del molde y la eficiencia de la producción. ↩
-
Descubra los estándares de la industria y las mejores prácticas que guían el diseño eficaz de superficies de separación para diversos productos. ↩
-
Descubra cómo el moldeo por inyección afecta la eficiencia de fabricación y la calidad del producto. ↩
-
Descubra cómo la alineación con el contorno máximo simplifica la estructura del molde para una fabricación eficiente. ↩
-
Descubra cómo las puertas latentes mejoran la transparencia al estabilizar el flujo de plástico en los procesos de moldeo. ↩
-
Comprenda cómo la ubicación de la compuerta afecta la eficiencia del flujo de plástico en las cavidades del molde. ↩
-
Aprenda a manejar formas simples en moldeo por inyección para facilitar el procesamiento y el ensamblaje. ↩
-
Descubra estrategias de ventilación efectivas para mejorar el rendimiento del molde y la calidad del producto. ↩
-
Explore métodos para seleccionar superficies de separación efectivas que simplifiquen el diseño de moldes y mejoren la calidad de la producción. ↩
-
Descubra cómo las superficies de separación optimizadas contribuyen a una mejor calidad del producto y una mayor eficiencia de fabricación. ↩