¿Está listo para aprovechar todo el potencial del polipropileno en sus proyectos de moldeo por inyección? ¡Profundicemos juntos en algunas estrategias transformadoras!
Mejorar la resistencia del polipropileno en el moldeo por inyección implica seleccionar materiales de alta cristalinidad, utilizar rellenos de refuerzo como fibra de vidrio o carbono, optimizar el proceso de moldeo y aplicar técnicas de posprocesamiento como el recocido.
Si bien estos pasos iniciales sientan una base sólida para componentes de polipropileno más resistentes, profundizar en cada estrategia revela enfoques matizados que pueden generar mejoras aún mayores. Exploremos estos aspectos en detalle para garantizar que su producción cumpla con los más altos estándares de resistencia.
La fibra de vidrio mejora la resistencia a la tracción del polipropileno.Verdadero
La fibra de vidrio se entrelaza con la matriz polimérica, distribuyendo las fuerzas de manera uniforme.
- 1. ¿Qué papel juegan los rellenos de refuerzo en la resistencia del polipropileno?
- 2. ¿Cómo puede la optimización del proceso de moldeo por inyección mejorar el polipropileno?
- 3. ¿Cuáles son los métodos eficaces de posprocesamiento del polipropileno?
- 4. ¿Cómo influye el diseño del molde en la resistencia de las piezas moldeadas por inyección?
- 5. Conclusión
¿Qué papel juegan los rellenos de refuerzo en la resistencia del polipropileno?
Los rellenos de refuerzo son cruciales para mejorar la resistencia del polipropileno, lo que lo convierte en una opción versátil en el moldeo por inyección.
Los rellenos de refuerzo, como las fibras de vidrio y de carbono, aumentan significativamente la resistencia del polipropileno al mejorar sus propiedades mecánicas, lo que permite aplicaciones más duraderas y robustas.
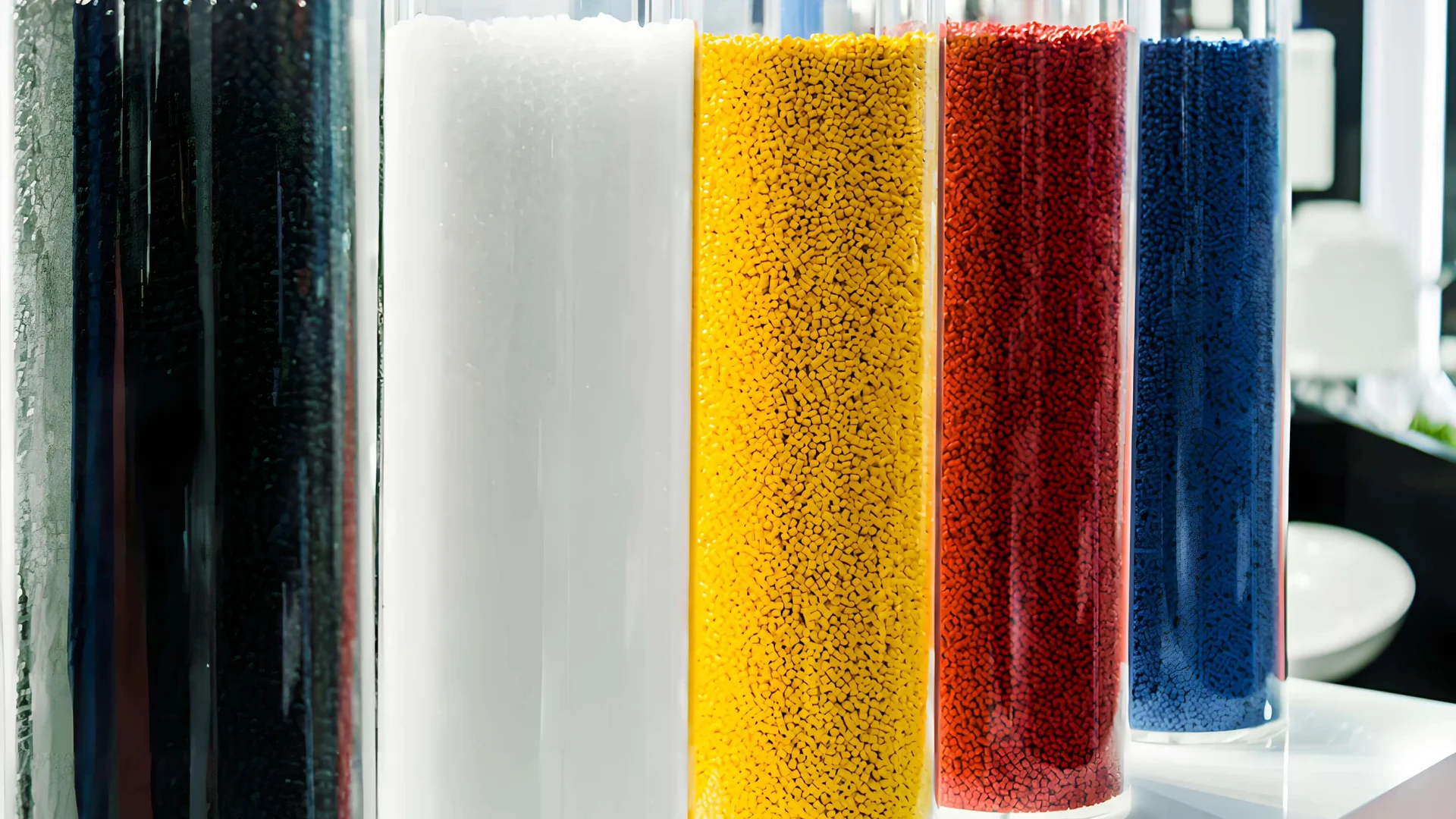
Tipos de rellenos de refuerzo
Cuando se trata de rellenos de refuerzo, los dos tipos más eficaces de polipropileno son la fibra de vidrio y la fibra de carbono.
Fibra de vidrio
La fibra de vidrio es un relleno muy utilizado debido a su capacidad para aumentar sustancialmente la resistencia a la tracción del polipropileno. Lo hace entrelazándose con la matriz polimérica, que distribuye las fuerzas aplicadas de manera más uniforme por todo el material. Normalmente, el contenido de fibra de vidrio en el polipropileno puede oscilar entre el 10% y el 40%, dependiendo de la resistencia deseada. Un porcentaje más alto puede conducir a una resistencia mejorada pero puede complicar el procesamiento.
Fibra de carbono
Aunque es más costosa que la fibra de vidrio, la fibra de carbono ofrece una resistencia y rigidez excepcionales. A menudo se utiliza en aplicaciones donde el peso es un factor crítico y la resistencia no puede verse comprometida. La adición de incluso una pequeña cantidad de fibra de carbono puede mejorar drásticamente las propiedades mecánicas del polipropileno.
Efectos sobre las propiedades mecánicas
La adición de rellenos de refuerzo afecta directamente varias propiedades mecánicas del polipropileno:
- Resistencia a la tracción : Tanto las fibras de vidrio como las de carbono mejoran la resistencia a la tracción al proporcionar soporte adicional a la estructura del polímero.
- Resistencia al impacto : Si bien mejoran la rigidez, estos rellenos también ayudan a mantener o incluso mejorar la resistencia al impacto del polipropileno.
- Estabilidad dimensional : El polipropileno reforzado exhibe menos contracción y deformación durante la fase de enfriamiento, lo que resulta en piezas más estables dimensionalmente.
Consideraciones de uso
A la hora de incorporar rellenos de refuerzo es fundamental tener en cuenta:
- Condiciones de procesamiento : Es posible que sean necesarios ajustes en las condiciones de procesamiento, como la temperatura y la presión, para adaptarse a las características de flujo alteradas del polipropileno relleno.
- Análisis costo-beneficio : si bien los rellenos como la fibra de carbono ofrecen un refuerzo superior, tienen un costo mayor. Evaluar los requisitos específicos de su aplicación puede ayudar a determinar la solución más rentable.
- Impacto ambiental : Algunos rellenos pueden afectar la reciclabilidad del polipropileno. Por lo tanto, considerar opciones sustentables es vital para prácticas de producción amigables con el medio ambiente.
En resumen, los rellenos de refuerzo desempeñan un papel fundamental en la mejora de la resistencia y usabilidad del polipropileno en diversas aplicaciones. Al seleccionar y gestionar cuidadosamente estos rellenos, los fabricantes pueden mejorar significativamente el rendimiento del producto y cumplir con los requisitos de aplicaciones específicas.
La fibra de vidrio puede aumentar la resistencia a la tracción del polipropileno en un 40%.Verdadero
El contenido de fibra de vidrio en el polipropileno oscila entre el 10% y el 40%, lo que mejora la resistencia.
La fibra de carbono es más barata que la fibra de vidrio para reforzar el polipropileno.FALSO
La fibra de carbono es más costosa que la fibra de vidrio pero ofrece una resistencia superior.
¿Cómo puede la optimización del proceso de moldeo por inyección mejorar el polipropileno?
La optimización del proceso de moldeo por inyección es crucial para mejorar la resistencia de los componentes de polipropileno. Descubra las técnicas clave involucradas.
La optimización del proceso de moldeo por inyección mejora la resistencia del polipropileno ajustando la temperatura, la presión, el tiempo de retención y el diseño del molde.
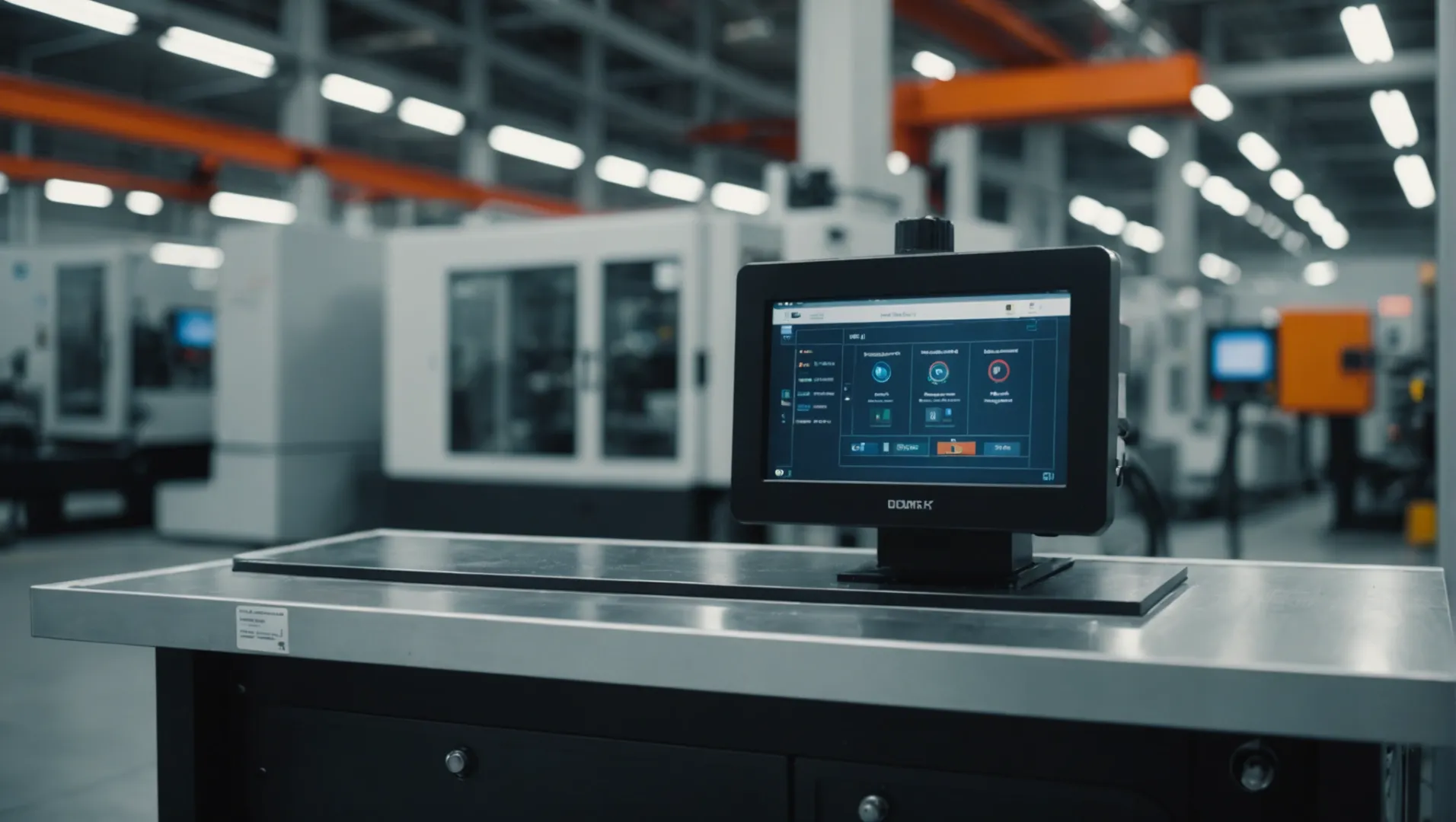
Aumento de la temperatura de moldeo por inyección
El aumento de la temperatura de moldeo por inyección puede mejorar significativamente la alineación molecular en el polipropileno, lo que da lugar a componentes más fuertes. Es esencial mantener la temperatura dentro de un rango específico (generalmente entre 200 ℃ y 250 ℃) para evitar la degradación y al mismo tiempo garantizar un flujo óptimo. Los ajustes graduales de temperatura pueden ayudar a encontrar el equilibrio perfecto, ofreciendo una marcada mejora en la fuerza.
Aumento de la presión de inyección
Una presión de inyección más alta garantiza que el polipropileno llene el molde herméticamente, lo que reduce los huecos y defectos internos. Sin embargo, es clave equilibrar esto con la longevidad del molde, ya que una presión excesiva podría provocar un mayor desgaste. El rango recomendado es de 50MPa a 150MPa. Monitorear de cerca las condiciones del molde durante los ajustes puede evitar daños innecesarios, garantizando tanto la calidad del producto como la seguridad del equipo.
Ajuste del tiempo de retención y la presión
Extender el tiempo de retención y ajustar la presión de retención permite que el polipropileno se enfríe y solidifique completamente, minimizando la contracción y la deformación. Normalmente, el tiempo de retención oscila entre 5 y 30 segundos, mientras que la presión debe ser del 50 % al 80 % de la presión de inyección inicial. Consideraciones como el tamaño, la forma y el espesor de la pared del producto son fundamentales para determinar los parámetros correctos para reducir la tensión interna sin comprometer la integridad de la pieza.
Optimización del diseño de moldes
El diseño innovador de moldes puede mejorar sustancialmente la resistencia del polipropileno. La ubicación y el tamaño estratégicos de la compuerta garantizan un llenado uniforme, lo que reduce el estrés y los defectos. Mejorar el sistema de enfriamiento promueve una cristalización rápida y uniforme, aumentando la fuerza. Una temperatura uniforme del molde evita el sobrecalentamiento o enfriamiento localizado, proporcionando una calidad constante en todas las piezas. Comprender estos principios de diseño de moldes 1 es crucial para optimizar el proceso de moldeo por inyección.
El aumento de la temperatura mejora la resistencia del polipropileno.Verdadero
El aumento de la temperatura mejora la alineación molecular, aumentando la fuerza.
El tiempo de espera siempre debe ser inferior a 5 segundos.FALSO
El tiempo de retención oscila entre 5 y 30 segundos para un enfriamiento y solidificación óptimos.
¿Cuáles son los métodos eficaces de posprocesamiento del polipropileno?
Para garantizar piezas robustas de polipropileno, es esencial dominar técnicas eficaces de posprocesamiento.
Los métodos eficaces de posprocesamiento para el polipropileno incluyen el recocido para aliviar la tensión y mejorar la cristalinidad, así como tratamientos de superficie como pulverización y galvanoplastia para mejorar la durabilidad y la apariencia.
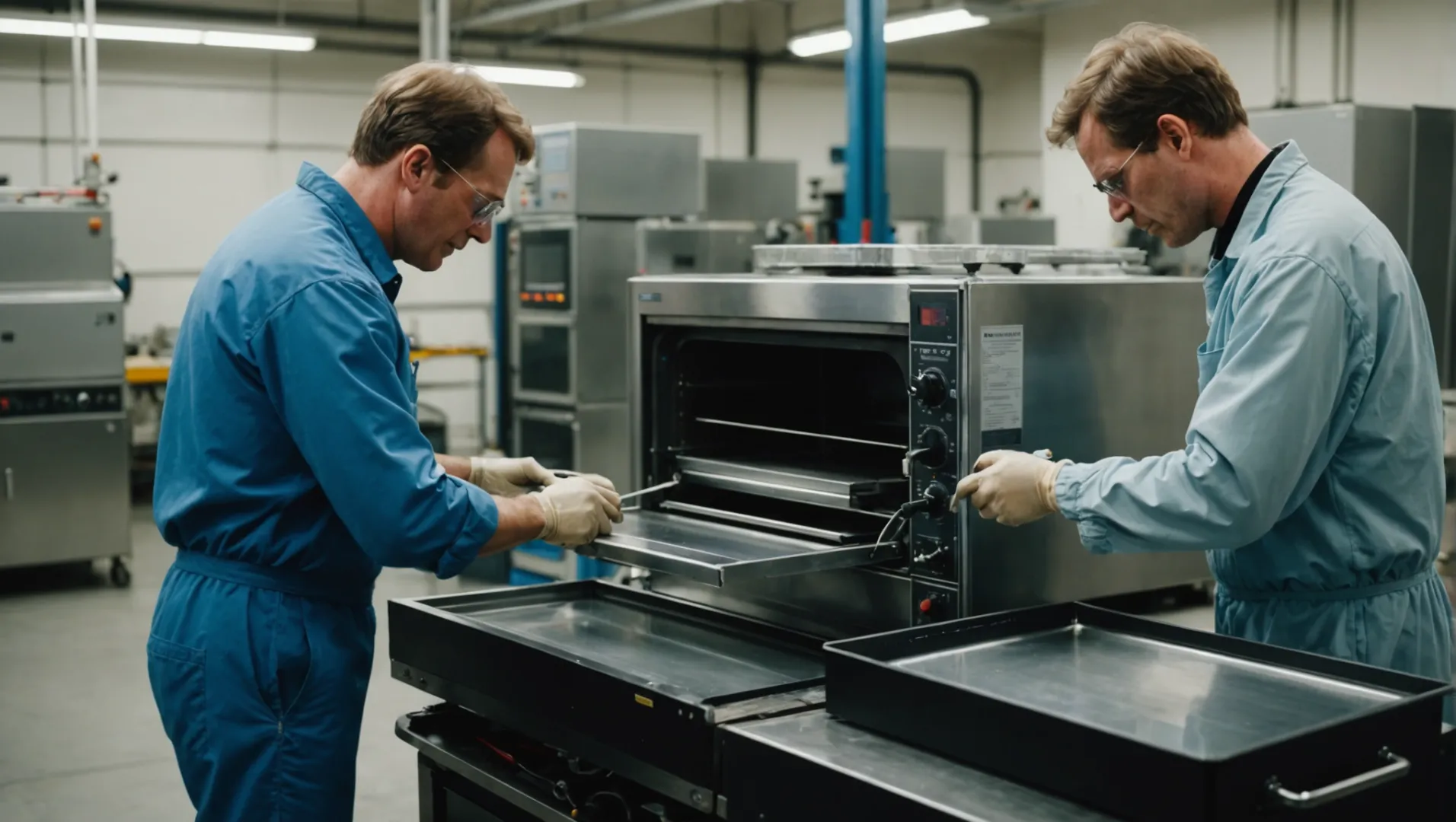
Tratamiento de recocido: mejora de la resistencia y la estabilidad
El recocido es un proceso de tratamiento térmico que puede mejorar significativamente las propiedades del polipropileno. Al calentar el material por debajo de su temperatura de transición vítrea, se alivian las tensiones internas, lo que mejora la cristalinidad. Este proceso puede mejorar la resistencia y estabilidad generales de las piezas moldeadas.
Normalmente, la temperatura de recocido se establece justo por debajo de la temperatura de transición vítrea del polipropileno, y la duración puede variar según el tamaño y el espesor de la pieza, desde varias horas hasta decenas de horas. Es fundamental controlar tanto la temperatura como el tiempo para evitar la degradación del rendimiento debido al recocido excesivo.
Técnicas de tratamiento de superficies
Los tratamientos superficiales no sólo pueden mejorar las propiedades mecánicas del polipropileno sino también sus cualidades estéticas. Opciones como la pulverización y la galvanoplastia pueden aumentar la dureza de la superficie y la resistencia al desgaste, aumentando así indirectamente la resistencia general de la pieza. Además, estos tratamientos añaden valor al mejorar el atractivo visual del producto terminado.
Al seleccionar un método de tratamiento de superficies, es esencial equilibrar los requisitos de uso del producto con las consideraciones de costos. Cada método ofrece diferentes beneficios:
Método | Beneficios |
---|---|
Pulverización | Aumenta la dureza de la superficie, mejora la estética. |
galvanoplastia | Proporciona resistencia al desgaste, mejora la conductividad eléctrica. |
Combinación de técnicas para obtener resultados óptimos
Al integrar el recocido con tratamientos superficiales adecuados, los fabricantes pueden lograr un doble beneficio: mejores propiedades internas y mayor durabilidad externa. Por ejemplo, combinar el recocido con la galvanoplastia puede producir piezas de polipropileno que sean estructuralmente robustas y resistentes al desgaste.
Comprender estas técnicas de posprocesamiento 2 es vital para los fabricantes que buscan producir componentes de polipropileno de alta resistencia de manera eficiente. Adaptar estos métodos a aplicaciones específicas garantiza que cada pieza no sólo cumpla sino que supere los estándares de la industria.
El recocido mejora la cristalinidad del polipropileno.Verdadero
El recocido alivia las tensiones internas, mejorando la cristalinidad.
La galvanoplastia reduce la resistencia al desgaste del polipropileno.FALSO
La galvanoplastia aumenta la resistencia al desgaste al endurecer la superficie.
¿Cómo influye el diseño del molde en la resistencia de las piezas moldeadas por inyección?
El diseño de moldes juega un papel crucial a la hora de determinar la resistencia y la calidad de las piezas moldeadas por inyección. Pero ¿cómo influye exactamente en estas características?
El diseño del molde influye en la resistencia de las piezas moldeadas por inyección al garantizar un flujo de material adecuado, reducir las concentraciones de tensión y mejorar la eficiencia de enfriamiento. La ubicación óptima de la compuerta, los sistemas de enfriamiento y la geometría de las piezas son elementos clave que impactan las propiedades mecánicas y la durabilidad del producto final.
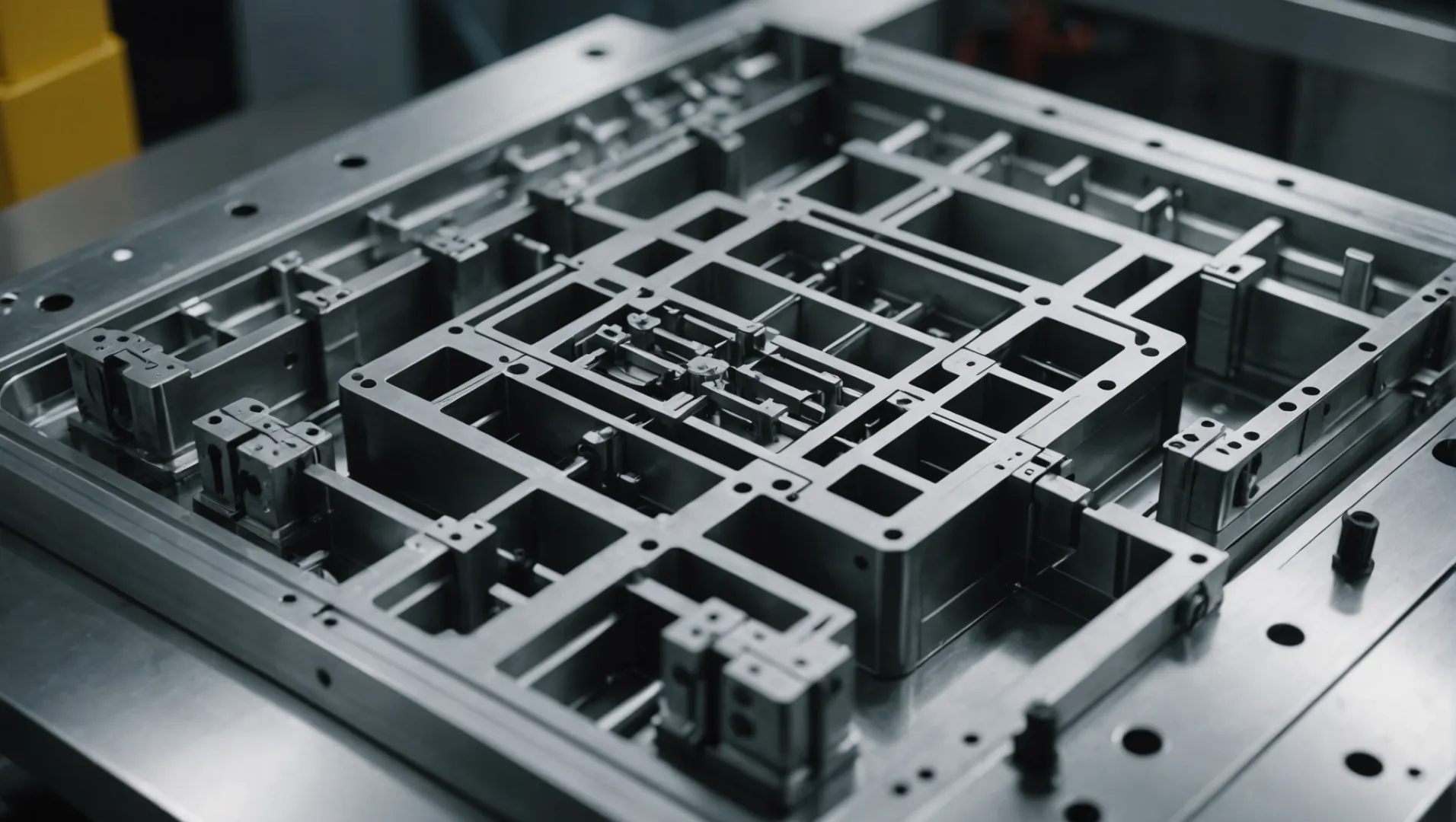
La importancia del diseño de la puerta
Un aspecto fundamental del diseño de moldes es la posición y el tamaño de la puerta, que sirve como punto de entrada para el plástico fundido. Una compuerta bien diseñada garantiza un llenado uniforme, minimizando posibles concentraciones de tensiones que podrían debilitar la pieza. La ubicación óptima de la compuerta reduce las rutas de flujo y las caídas de presión, lo que lleva a una distribución más uniforme del material.
- Tipos de compuertas : se pueden utilizar diferentes tipos de compuertas, como de borde, de abanico o submarinas, según la complejidad y los requisitos de la pieza. Por ejemplo, podría preferirse una compuerta de ventilador para piezas anchas, ya que proporciona una entrada amplia y reduce las marcas de flujo.
Eficiencia del sistema de enfriamiento
El sistema de enfriamiento del molde es fundamental para controlar el proceso de solidificación, afectando directamente la cristalinidad y las propiedades mecánicas. Los sistemas de enfriamiento mejorados ayudan a lograr un enfriamiento uniforme en toda la pieza, lo cual es vital para mantener una resistencia constante y evitar deformaciones o imprecisiones dimensionales.
- Canales de enfriamiento : la incorporación de canales de enfriamiento conformes que coincidan con la geometría de la pieza puede mejorar significativamente la eficiencia de enfriamiento. Este enfoque ayuda a mantener una temperatura uniforme, reduciendo los tiempos de ciclo y mejorando la resistencia de las piezas.
Consideraciones sobre la geometría de la pieza
La geometría de las cavidades del molde influye profundamente en cómo se distribuye la tensión en la pieza. Diseñar con un espesor de pared uniforme ayuda a reducir las concentraciones de tensión y los posibles puntos débiles.
- Diseño de nervadura : Un diseño de nervadura adecuado puede agregar soporte estructural sin comprometer el peso. Las nervaduras deben estar ubicadas estratégicamente y ser lo suficientemente gruesas para equilibrar la resistencia adicional y las posibles marcas de hundimiento.
Gestión del flujo de materiales
Garantizar un flujo fluido de material por todo el molde es esencial para evitar defectos como trampas de aire o líneas de soldadura que pueden debilitar las piezas. Es necesaria una ventilación adecuada para permitir que escape el aire atrapado, asegurando el llenado completo de la cavidad del molde.
- Simulación de flujo : el uso de herramientas de ingeniería asistidas por computadora para la simulación de flujo puede ayudar a predecir problemas potenciales en el flujo de materiales y permitir a los diseñadores realizar ajustes informados antes de la fabricación.
En resumen, el diseño de moldes es un proceso multifacético que implica una cuidadosa consideración de múltiples factores. Optimizar la ubicación de las compuertas 3 , perfeccionar los sistemas de refrigeración y garantizar un flujo de material adecuado son esenciales para producir piezas moldeadas por inyección resistentes y fiables. Cada decisión afecta la resistencia del producto final, lo que resalta la importancia de la precisión en el diseño del molde.
La ubicación óptima de la puerta reduce las concentraciones de tensión.Verdadero
La colocación adecuada de la compuerta garantiza un flujo uniforme del material, minimizando el estrés.
Los sistemas de refrigeración no tienen ningún impacto en la resistencia de las piezas.FALSO
Los sistemas de enfriamiento eficientes garantizan una solidificación uniforme, mejorando la resistencia.
Conclusión
Al seleccionar materiales estratégicamente, optimizar procesos y aplicar métodos de posprocesamiento efectivos, puede mejorar significativamente la resistencia del polipropileno en el moldeo por inyección. Implemente estos conocimientos para elevar la eficiencia de fabricación y la calidad del producto.
-
Descubra los principios esenciales para mejorar la resistencia del polipropileno a través del diseño innovador de moldes. El moldeo por inyección de plástico es donde los materiales plásticos (en este caso, polipropileno) se funden y luego se inyectan a alta presión en moldes. ↩
-
Explore diversos métodos de posprocesamiento para piezas de polipropileno más resistentes: este artículo describe un nuevo método eficiente para el procesamiento de desechos de polipropileno posconsumo (y otras poliolefinas) en ceras polares que tienen... ↩
-
Explore cómo la colocación precisa de la puerta mejora la resistencia de la pieza: en moldes de inyección con núcleos largos y delgados, la puerta debe ubicarse lejos del núcleo para evitar la deformación causada por el flujo de material. Tú … ↩