El diseño de canales de moldeo por inyección cambia las reglas del juego en la fabricación.
Los errores comunes en el diseño de canales de moldes de inyección incluyen tamaño y forma inadecuados de los canales, posicionamiento incorrecto de la puerta y sistemas de canales desequilibrados. Al abordar estos problemas mediante un diseño cuidadoso y un análisis del flujo del molde, puede mejorar la calidad del producto y reducir los costos.
Comprender los errores es sólo el comienzo; ¡Exploremos cómo podemos rectificar estos problemas de manera efectiva!
Un tamaño inadecuado de los canales conduce a un aumento de los defectos.Verdadero
El tamaño del canal afecta el flujo de fusión y el enfriamiento, lo que afecta la calidad.
- 1. ¿Cómo afecta el tamaño del corredor a la calidad del producto?
- 2. ¿Cuáles son las mejores prácticas para diseñar formas de canales de flujo?
- 3. ¿Por qué la posición de la puerta es fundamental en el diseño de corredores?
- 4. ¿Cómo se puede lograr el equilibrio del canal en moldes de cavidades múltiples?
- 5. Conclusión
¿Cómo afecta el tamaño del corredor a la calidad del producto?
El tamaño del canal en los moldes de inyección es crucial para garantizar productos de alta calidad. Un dimensionamiento incorrecto puede provocar defectos e ineficiencias.
El tamaño del canal afecta la calidad del producto al influir en el flujo de fusión, las velocidades de enfriamiento y la distribución de tensiones. El tamaño óptimo garantiza un llenado eficiente, reduce el desperdicio de material y minimiza defectos como deformaciones o grietas.
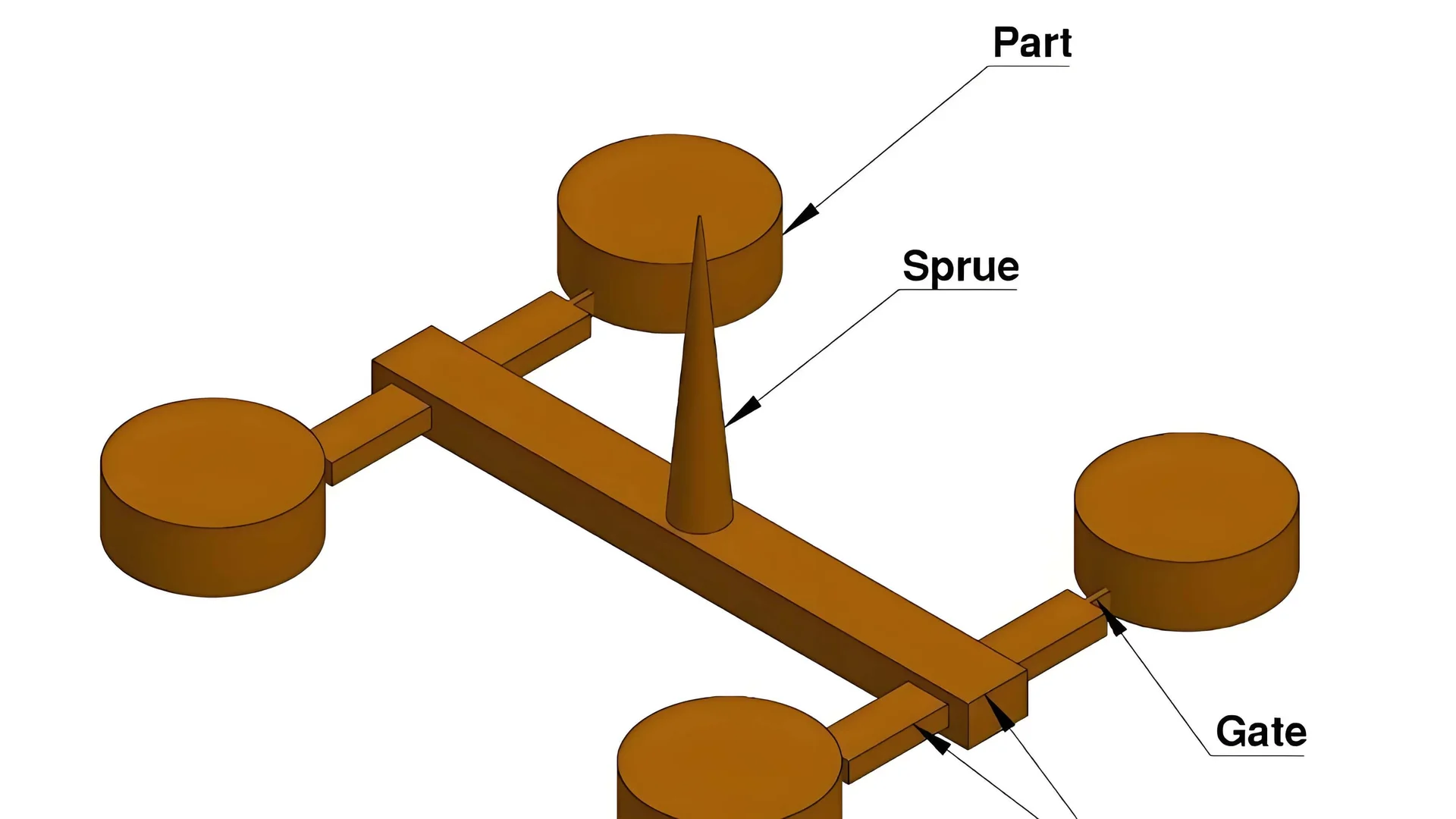
Comprender el papel del tamaño del corredor
El sistema de canales en el moldeo por inyección actúa como vía para que el plástico fundido viaje desde la unidad de inyección hasta la cavidad del molde. El tamaño del canal afecta directamente la eficiencia y uniformidad con que el plástico llena el molde. Un corredor 1 puede provocar varios problemas que afectan la calidad del producto.
-
Corredores demasiado gruesos : si un corredor es excesivamente grueso, el plástico derretido permanecerá más tiempo en el corredor. Este tiempo de residencia prolongado puede provocar un enfriamiento excesivo o incluso una degradación térmica del material antes de que llegue a la cavidad. Por ejemplo, cuando se fabrican artículos pequeños de paredes delgadas, un canal demasiado grueso puede causar un llenado incompleto, lo que resulta en escasez de material y defectos.
-
Canales demasiado delgados : por el contrario, los canales que son demasiado delgados aumentan la resistencia al flujo de la masa fundida. Esto requiere una mayor presión de inyección, lo que genera un mayor consumo de energía y un posible desgaste de la maquinaria. Además, los canales delgados pueden causar tensión interna, lo que provoca defectos como deformaciones o grietas. Un ejemplo es cuando los canales delgados causan un corte excesivo, lo que provoca sobrecalentamiento, descomposición y defectos como burbujas o rayas plateadas en el producto.
Estrategias para el tamaño óptimo del corredor
Para optimizar el tamaño del canal, es esencial considerar factores como las dimensiones del producto, la forma y el espesor de la pared. Generalmente, el diámetro del canal debe ser entre 1,5 y 2 veces el espesor de la pared del producto. Para productos más grandes o más gruesos, puede ser necesario un corredor más grande, mientras que los productos más pequeños o más delgados se benefician de un tamaño de corredor reducido.
El empleo de software de análisis de flujo de molde puede ayudar a simular escenarios de diferentes tamaños de canales para determinar el diseño óptimo. Este enfoque no sólo mejora la calidad del producto sino que también reduce el desperdicio de material y los costos de producción.
Estudio de caso: Ajuste del tamaño del corredor
Considere un escenario en el que una empresa enfrentaba problemas de deformación en sus piezas moldeadas por inyección. Al analizar su sistema de corredores, descubrieron que los corredores eran demasiado delgados, lo que provocaba un llenado desigual y una distribución de la tensión. Al ajustar el tamaño del canal según las recomendaciones de los expertos 2 , lograron un llenado más consistente, redujeron el estrés y mejoraron la calidad general del producto.
Mediante un cuidadoso diseño y análisis de rodetes, los fabricantes pueden mejorar significativamente el rendimiento y la confiabilidad de sus productos. Garantizar que el tamaño del canal se alinee con los requisitos específicos del producto es un paso vital para lograr resultados de fabricación óptimos.
Los corredores gruesos reducen el riesgo de degradación del material.FALSO
Los corredores gruesos pueden causar un enfriamiento excesivo, lo que lleva a la degradación.
Los canales delgados aumentan las necesidades de presión de inyección.Verdadero
Los canales delgados aumentan la resistencia al flujo y necesitan una presión más alta.
¿Cuáles son las mejores prácticas para diseñar formas de canales de flujo?
El diseño de la forma del canal de flujo es crucial en el moldeo y afecta tanto la eficiencia como la calidad del producto final.
Las mejores prácticas para diseñar formas de canales de flujo incluyen el uso de transiciones de arco en las esquinas y garantizar formas transversales regulares para facilitar un flujo de fusión suave y uniforme.
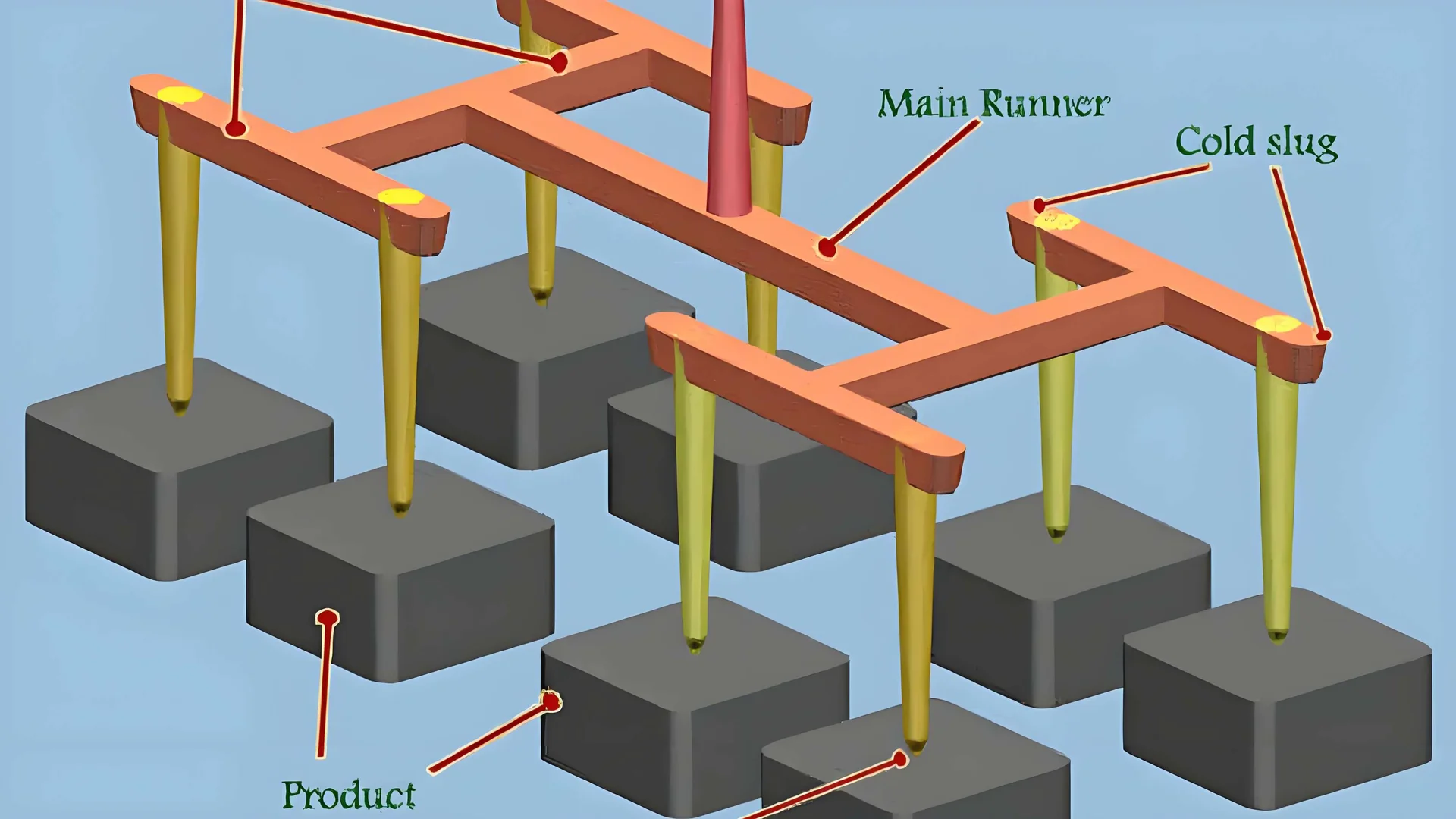
Importancia de la forma del canal de flujo
Diseñar la forma de un canal de flujo puede influir en gran medida en la eficiencia del proceso de moldeo por inyección. Las formas de los canales de flujo afectan la forma en que el plástico fundido viaja a través del molde, influyendo en factores como la presión, la temperatura y la uniformidad del flujo. Un canal de flujo bien diseñado minimiza defectos como deformaciones, burbujas de aire y líneas de soldadura.
Errores comunes y soluciones
Esquinas afiladas y su impacto
Las esquinas afiladas dentro de los canales de flujo pueden provocar un aumento del esfuerzo cortante en el material fundido. Esto puede provocar temperaturas más altas, lo que hace que el plástico se descomponga y cree defectos no deseados como burbujas o rayas plateadas.
- Solución : Implemente transiciones de arco 3 para reducir el esfuerzo cortante. El radio de estos arcos normalmente debe estar entre 0,25 y 0,5 veces el diámetro del canal.
Formas transversales irregulares
Una sección transversal irregular puede provocar velocidades de flujo desiguales, lo que provoca defectos como variaciones locales de espesor y marcas de soldadura.
- Solución : Apunte a secciones transversales circulares o trapezoidales para promover un caudal uniforme en todo el sistema de canales. Esta consistencia ayuda a mantener una transición suave de la masa fundida.
Análisis de flujo de molde
El uso de software de análisis de flujo de moldes permite a los diseñadores simular diferentes configuraciones de canales de flujo. Al ajustar parámetros como la forma, el tamaño y el radio del arco, es posible identificar la configuración óptima que minimice el desperdicio de material y al mismo tiempo mantenga la integridad del producto.
- Ejemplo : en producciones a gran escala, las simulaciones pueden revelar cómo pequeños ajustes en la forma del canal pueden afectar significativamente la eficiencia y la calidad generales de la producción.
Consideración de materiales
Las propiedades del material plástico que se utiliza también son un factor crítico para determinar la mejor forma del canal de flujo. Diferentes materiales pueden requerir diseños de canales únicos para optimizar sus características de flujo sin comprometer la calidad del producto.
- Consideración : algunos plásticos pueden necesitar transiciones más suaves debido a su viscosidad y sensibilidad térmica.
Conclusión
Al incorporar estas mejores prácticas, como utilizar transiciones de arco y mantener formas transversales regulares, los fabricantes pueden mejorar el rendimiento de sus moldes de inyección. Además, aprovechar el análisis del flujo del molde permite una personalización precisa adaptada a las necesidades de producción específicas. Esto no sólo mejora la calidad del producto sino que también reduce los costos al minimizar los defectos y el desperdicio de material.
Las transiciones de arco reducen la tensión cortante en los canales de flujo.Verdadero
Las transiciones de arco suavizan las esquinas afiladas, reduciendo el estrés y los defectos.
Las secciones transversales irregulares promueven un flujo de fusión uniforme.FALSO
Las formas irregulares provocan un flujo desigual, lo que provoca defectos como marcas de soldadura.
¿Por qué la posición de la puerta es fundamental en el diseño de corredores?
La posición de la compuerta en el diseño de canales es vital e influye en el flujo, la calidad y la eficiencia de los procesos de moldeo por inyección.
La importancia de la posición de la compuerta en el diseño de canales surge de su impacto directo en el patrón de llenado, la calidad del producto y la eficiencia de la producción. La colocación adecuada de la compuerta garantiza un llenado uniforme de la cavidad, minimiza la concentración de tensiones y reduce los defectos, lo que genera productos de mayor calidad y una fabricación optimizada.
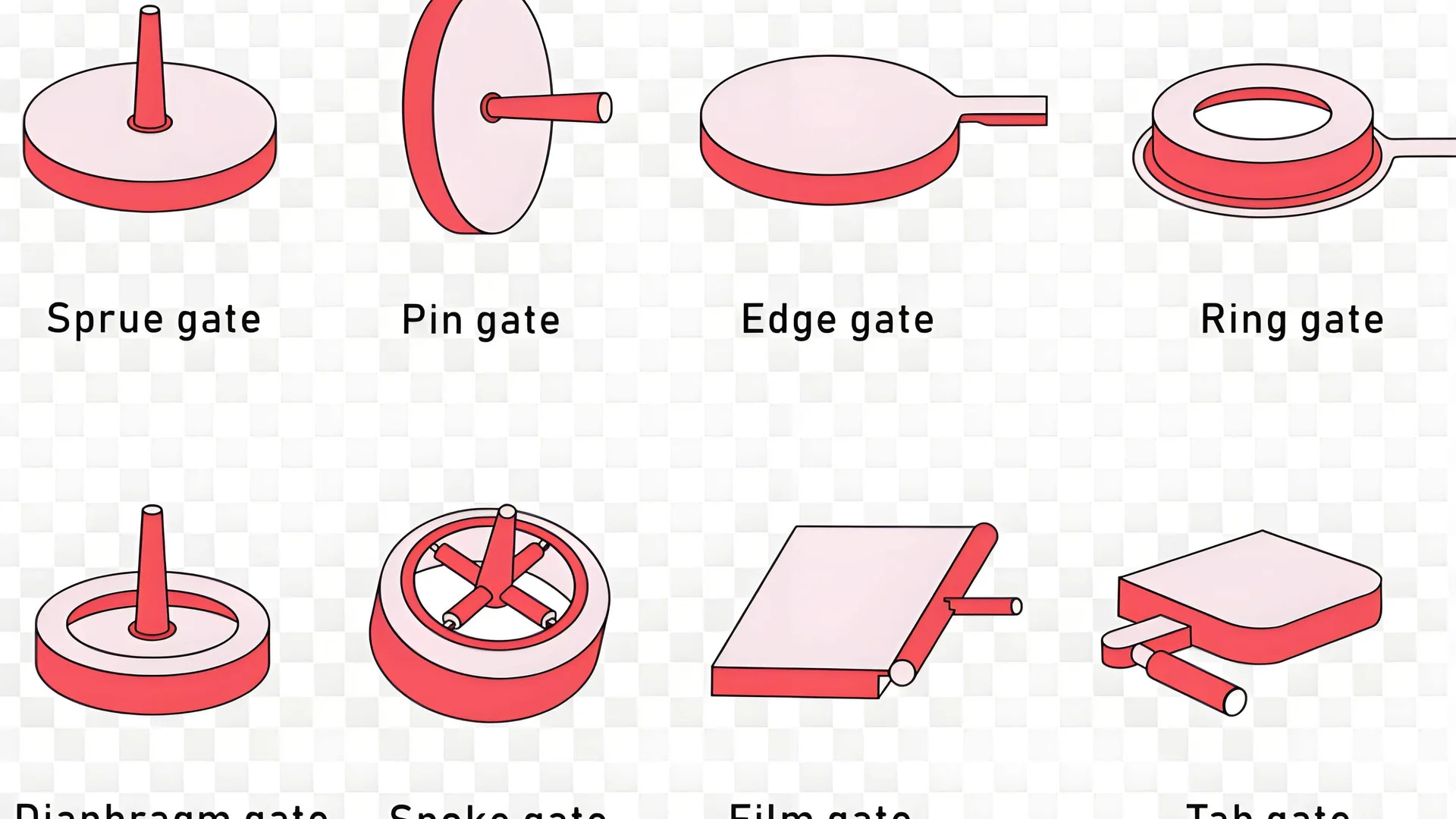
Impacto en el patrón de llenado
La ubicación de la compuerta determina cómo el material fundido llena la cavidad. Una puerta estratégicamente ubicada garantiza un patrón de llenado uniforme, lo cual es esencial para mantener una calidad constante del producto. Al colocar la puerta en una sección más gruesa del producto o en una ubicación central, los fabricantes pueden lograr una distribución más uniforme del material. Este enfoque ayuda a minimizar defectos como líneas de soldadura y trampas de aire.
Por ejemplo, si la compuerta se coloca en una sección más delgada del molde, existe el riesgo de un llenado incompleto o una distribución desigual de la presión. Esto puede provocar concentraciones de tensión, que podrían provocar deformaciones o grietas bajo carga.
Influencia en la calidad del producto
El posicionamiento de la puerta juega un papel crucial en la definición de las propiedades mecánicas y el acabado superficial del producto moldeado. Una compuerta mal colocada puede provocar una tensión de corte excesiva en el material, lo que provoca degradación y defectos como decoloración o fragilidad.
Utilizando software de análisis de flujo de molde 4 , los diseñadores pueden simular diferentes posiciones de la puerta para evaluar su impacto en el producto final. Esta herramienta ayuda a predecir problemas potenciales como escasez de material o embalaje excesivo, lo que permite realizar ajustes antes de que comience la producción real.
Consideraciones de eficiencia de producción
La eficiencia del proceso de moldeo por inyección está significativamente influenciada por la ubicación de la puerta. La colocación óptima de la compuerta reduce el tiempo del ciclo al garantizar un llenado más rápido y eficiente, ahorrando así energía y recursos. Además, minimiza los requisitos de posprocesamiento al reducir el flash y otros artefactos no deseados.
Por ejemplo, una compuerta ubicada en el centro puede permitir un llenado equilibrado de moldes de múltiples cavidades, evitando discrepancias en el peso y las dimensiones del producto. También facilita la expulsión de piezas, mejorando el rendimiento general de la producción.
En resumen, evaluar la posición de la puerta mediante un análisis 5 no se trata sólo de mejorar la calidad del producto sino también de optimizar todo el proceso de fabricación. Las consideraciones de diseño adecuadas garantizan que cada elemento del sistema de canales funcione armoniosamente hacia una producción eficiente.
La posición de la puerta afecta la calidad del moldeo por inyección.Verdadero
La posición de la puerta influye en los patrones de llenado, la distribución de tensiones y los defectos.
Las puertas situadas en el centro provocan un llenado desigual.FALSO
Las puertas ubicadas centralmente garantizan un llenado equilibrado y reducen los defectos.
¿Cómo se puede lograr el equilibrio del canal en moldes de cavidades múltiples?
Equilibrar los canales en moldes de múltiples cavidades es crucial para garantizar una calidad uniforme del producto y procesos de fabricación eficientes.
Lograr el equilibrio de los canales en moldes de múltiples cavidades implica diseñar longitudes, formas y tamaños de canales consistentes en todas las cavidades. Ajustar los caudales de fusión con válvulas de mariposa o modificar el tamaño de las compuertas también puede ayudar a garantizar una distribución uniforme.
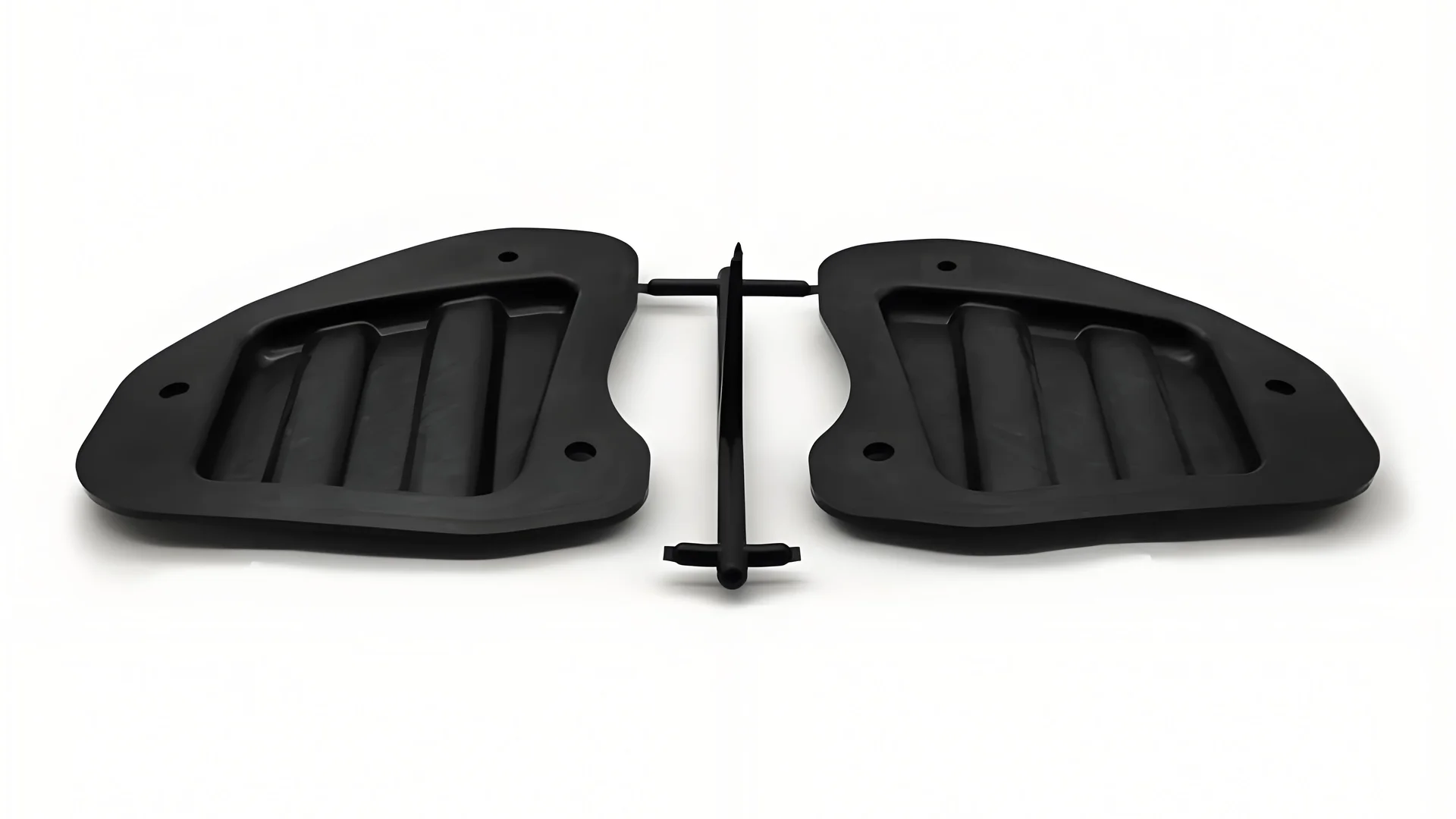
Importancia del equilibrio del corredor
En moldes de múltiples cavidades, lograr el equilibrio de los canales es fundamental para mantener una calidad constante del producto en todas las cavidades. Un sistema de canales desequilibrado puede provocar variaciones en las dimensiones, el peso y el rendimiento del producto, lo que en última instancia afecta la eficiencia de la producción y aumenta los costos.
Cuando el corredor de una cavidad es más largo o más delgado que otros, la resistencia al flujo de fusión aumenta, lo que ralentiza la velocidad de llenado y potencialmente causa defectos como escasez de material. Mientras tanto, los productos en otras cavidades pueden llenarse correctamente, lo que genera una disparidad en la calidad.
Consideraciones de diseño para corredores equilibrados
Para garantizar corredores equilibrados, es esencial mantener la consistencia en la longitud del corredor, la forma de la sección transversal y el tamaño 6 para cada cavidad. El objetivo es permitir que la masa fundida se distribuya uniformemente por todas las cavidades.
Longitud y forma del corredor
Mantener uniforme la longitud de los canales minimiza las discrepancias en la resistencia al flujo. Si existen diferencias inevitables debido a la forma del producto o la estructura del molde, considere utilizar un diseño simétrico siempre que sea posible. Además, se prefieren secciones transversales redondas o trapezoidales para un flujo de fusión más suave y uniforme.
Aspecto de diseño | Mejores prácticas |
---|---|
Longitud del corredor | Consistente en todas las cavidades |
Forma transversal | Circular o trapezoidal para un flujo uniforme |
Ajustes | Utilice válvulas de mariposa o modifique el tamaño de las compuertas. |
Utilización de válvulas de mariposa y modificaciones de compuerta
Cuando no se pueda lograr el equilibrio perfecto únicamente mediante el diseño, incorpore válvulas de mariposa en los patines. Estos dispositivos ayudan a ajustar el caudal de fusión al proporcionar una resistencia ajustable, lo que garantiza que cada cavidad se llene a una velocidad óptima.
Otra estrategia eficaz es ajustar el tamaño de las puertas. Al cambiar las dimensiones de la compuerta, puede controlar el flujo de masa fundida en cada cavidad, equilibrando la velocidad de llenado y garantizando una distribución uniforme.
Simulación de diseños de corredores
El uso de software de análisis de flujo de moldes es invaluable para simular varios diseños y configuraciones de canales. Esta herramienta permite a los diseñadores visualizar posibles desequilibrios y probar ajustes antes de que comience la producción real.
Las simulaciones también pueden proporcionar información sobre cómo modificaciones como las válvulas de mariposa o los cambios en el tamaño de la compuerta afectarán el equilibrio general y la eficiencia del sistema de molde. Al aprovechar estas tecnologías, puede mejorar la precisión y efectividad de sus diseños de guías, optimizando tanto la calidad del producto como la eficiencia de fabricación.
Las longitudes constantes de los canales garantizan una calidad uniforme del producto.Verdadero
Las longitudes uniformes de los canales minimizan la resistencia al flujo, lo que garantiza un llenado uniforme.
Las válvulas de mariposa aumentan la resistencia al flujo de fusión en los canales.FALSO
Las válvulas de mariposa ajustan los caudales pero no aumentan inherentemente la resistencia.
Conclusión
Al implementar estas estrategias, puede mejorar significativamente su proceso de moldeo por inyección, garantizando productos de mayor calidad y operaciones eficientes.
-
Descubra cómo el tamaño del canal afecta la eficiencia del moldeo por inyección. Además, un canal de diámetro pequeño aumentará la presión de llenado. Si se dimensiona el corredor demasiado grande, el molde simplemente se queda ahí, esperando a que el corredor se congele... ↩
-
Descubra cómo el análisis de flujo de molde ayuda a optimizar el diseño de canales: El análisis de flujo de molde es una simulación basada en software que predice cómo una resina plástica fluirá y llenará un molde de inyección. ↩
-
Aprenda cómo las transiciones de arco reducen el esfuerzo cortante y mejoran la eficiencia del flujo: Hay una transición de arco en la raíz del refuerzo. La concentración de esfuerzos en la raíz y la entrada se puede evitar cuando se aplican fuerzas externas... ↩
-
Aprenda a simular posiciones de compuerta para un diseño óptimo del canal: El análisis de flujo del molde es una simulación de software que puede mostrar cómo la resina llenará el molde durante el proceso de moldeo por inyección. Al comprender el relleno material,... ↩
-
Descubra cómo la ubicación de las puertas afecta la eficiencia de fabricación: Las puertas son esenciales para el sistema de moldeo por inyección y los tipos y tamaños afectan directamente la calidad de los productos y los costos. ↩
-
Explore técnicas para diseñar sistemas de canales uniformes y eficientes. Utilice un análisis de equilibrio de canales para optimizar el diseño de los canales y garantizar una distribución uniforme del plástico en las cavidades del molde. Este análisis ayuda a identificar... ↩