¿Alguna vez ha pensado en cómo utilizar el acero correcto ayuda a que un molde de inyección dure más?
La dureza garantiza la resistencia al desgaste, mejorando la durabilidad del acero del molde, mientras que la dureza previene el agrietamiento bajo tensión. Juntos, extienden significativamente la longevidad de los moldes de inyección al equilibrar la resiliencia y la resistencia.
Comencé en la industria del molde con una sensación de asombro acerca de los cambios de materiales y sus efectos en la vida útil del molde. Un simple cambio de material realmente podría extender la vida útil de un molde. Es realmente fascinante cómo la dureza y la tenacidad funcionan bien juntas. Estas dos cualidades permiten que el molde pueda soportar duras demandas de producción.
La dureza es crucial para resistir daños y desgaste. Imagine la cavidad del molde como un dispositivo finamente ajustado, con la dureza actuando como escudo protector. Este escudo protege contra el roce constante del plástico derretido. Los moldes sin suficiente dureza se desgastaban rápidamente. Este desgaste conduce a cambios de forma y a costosos reemplazos. Por ejemplo, el uso de acero como el H13, tratado con una dureza entre HRC48-52, reduce significativamente el desgaste. Esto es especialmente cierto con los plásticos que tienen cargas abrasivas como la fibra de vidrio.
La dureza implica resiliencia. Es la capacidad del molde para recuperarse de los golpes sin romperse bajo presión. Recuerdo momentos en que los moldes enfrentaban impactos repentinos o condiciones inusuales durante su uso. En estas situaciones, la tenacidad absorbía los golpes sin dañar la estructura del molde.
Estas propiedades son esenciales a la hora de seleccionar el acero que se ajuste a sus necesidades. Garantizan durabilidad y precisión en la producción. La próxima vez que planifique su diseño, considere estos detalles detenidamente. Centrarse un poco en estos aspectos podría ayudar a evitar problemas futuros.
La dureza aumenta la resistencia al desgaste del acero para moldes.Verdadero
Una mayor dureza reduce el desgaste de la superficie y prolonga la vida útil del molde.
La dureza disminuye la resistencia al impacto del molde.FALSO
La dureza mejora la capacidad de un material para absorber el impacto.
- 1. ¿Por qué es importante la dureza para la resistencia al desgaste?
- 2. ¿Cómo afecta la tenacidad a la resistencia al impacto en los moldes?
- 3. ¿Por qué la resistencia a la deformación es fundamental para la longevidad del molde?
- 4. ¿Cómo puede la selección de acero optimizar la vida útil del molde?
- 5. Conclusión
¿Por qué es importante la dureza para la resistencia al desgaste?
La dureza puede aparecer como una característica más del material. Sin embargo, en ingeniería la situación cambia significativamente.
La dureza es muy importante para la resistencia al desgaste. Determina qué tan bien un material resiste la abrasión y la deformación de la superficie. A menudo, una mayor dureza mejora la resistencia al desgaste. Esto es esencial para prolongar la vida útil de componentes como los moldes. Los moldes se benefician significativamente de una alta dureza.
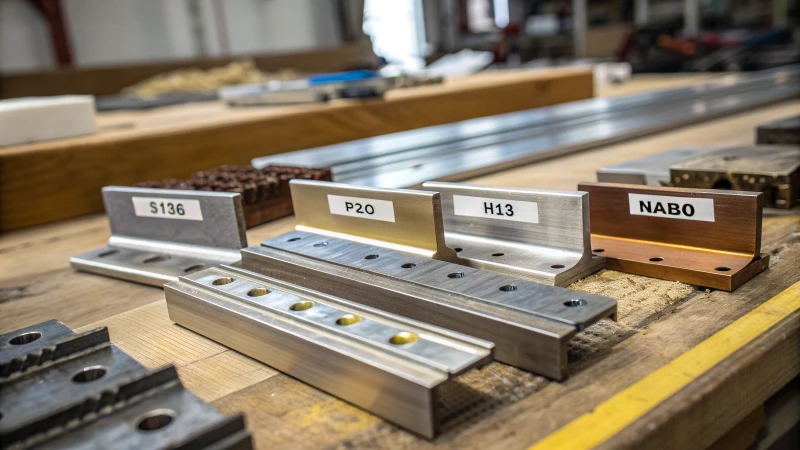
Dureza y desgaste superficial
Años de trabajo con moldes me enseñaron que la dureza del material es clave para resistir el desgaste. La dureza es la capacidad de un material para resistir rayones y abolladuras. Un material más duro resiste mejor la fricción y las fuerzas abrasivas, lo que lo hace muy resistente al desgaste.
Tomemos los moldes de inyección 1 . Recuerdo un proyecto en el que utilizamos moldes con altos niveles de dureza para manipular plástico fundido lleno de materiales abrasivos como fibras de vidrio. Con el tiempo, estos moldes mantuvieron fantásticamente su forma y dimensiones, lo que dio lugar a productos de alta calidad constante. Los moldes mostraron mucho menos desgaste en comparación con los de menor dureza.
Influencia en la vida útil
La dureza afecta directamente la duración de los componentes. Trabajé con aceros para moldes como el H13, que alcanzó niveles impresionantes de dureza de HRC48 – 52 después del tratamiento térmico. Estos aceros resistieron el desgaste significativamente más que los materiales más blandos y duraron mucho más.
La siguiente tabla ilustra la relación entre dureza y vida útil:
Tipo de acero del molde | Dureza ( HRC ) | Vida útil estimada (ciclos) |
---|---|---|
Acero estándar | 40 | 100,000 |
Acero endurecido | 50 | 250,000 |
Deformación y dureza
La dureza implica resistir la presión, no sólo resistir los rayones. Los materiales de alta dureza resisten bien la deformación elástica. Esto es importante durante procesos de alta presión como el moldeo por inyección. Mantener las cavidades del molde en forma significa menos defectos como variaciones de tamaño o rebabas.
La producción de artículos de plástico de gran tamaño implica una intensa presión de inyección. Los aceros para moldes 2 adecuados con suficiente dureza lo manejan sin doblarse ni deformarse, lo que prolonga su vida útil.
Equilibrando la dureza con la tenacidad
Sin embargo, la dureza debe equilibrarse con la dureza. Un material duro pero quebradizo puede desarrollar grietas bajo tensión. Busco un equilibrio donde la resistencia al desgaste y la durabilidad convivan maravillosamente. Los materiales que equilibran la dureza con la resistencia al impacto 3 pueden extender la vida útil de los componentes bajo cargas cíclicas o condiciones duras.
Elegir los materiales adecuados es crucial en industrias donde los componentes enfrentan diferentes desafíos mecánicos y térmicos. A menudo me baso en estándares y datos para tomar decisiones, considerando factores como la carga esperada, las condiciones ambientales y la vida útil deseada.
Una mayor dureza mejora la resistencia al desgaste de los materiales.Verdadero
La dureza aumenta la capacidad de un material para resistir la abrasión, mejorando la resistencia al desgaste.
La alta dureza siempre garantiza una mejor tenacidad de los materiales.FALSO
Si bien la dureza mejora la resistencia al desgaste, debe equilibrarse con la tenacidad para evitar grietas.
¿Cómo afecta la tenacidad a la resistencia al impacto en los moldes?
¿Alguna vez te has preguntado por qué algunos mohos sobreviven más que otros, incluso en condiciones difíciles? La dureza juega un papel crucial. Ayuda a absorber energía y detener daños. Esto es muy importante. Exploremos por qué.
La dureza de los moldes les ayuda a resistir el impacto absorbiendo los impactos. Esto evita que se formen grietas. La durabilidad del molde es muy importante durante procesos rápidos como el moldeo por inyección. Los moldes resistentes duran mucho tiempo. La integridad del molde permanece intacta. Esta cualidad realmente extiende la vida útil del molde.
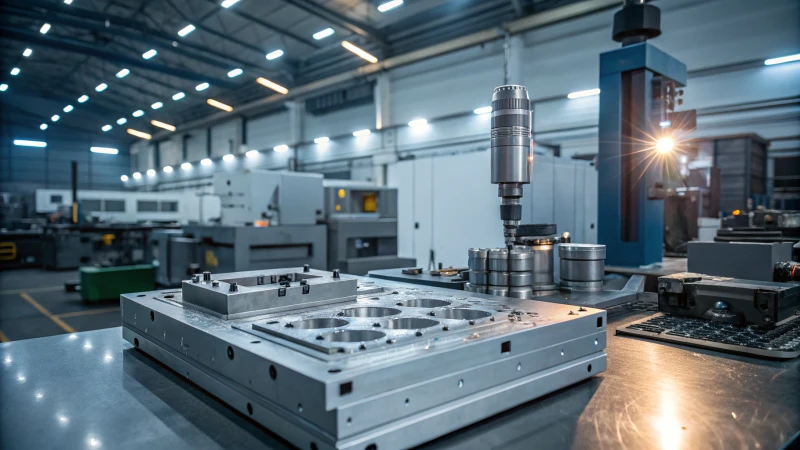
El papel de la tenacidad en el diseño de moldes
Recuerdo mi primer diseño de molde para un proceso de inyección rápido. Pensé que todo estaba perfecto hasta que noté que aparecían pequeñas grietas después de algunos ciclos. Esto me enseñó la importancia de la dureza. No se trata sólo de resistir los impactos; se trata de doblarse sin romperse.
Absorbiendo energía de impacto
Imagine el molde abriéndose y cerrándose cientos de veces al día. Los materiales resistentes absorben toda esa energía, como una esponja absorbe agua. Esto evita fracturas repentinas durante movimientos rápidos o golpes inesperados.
Tabla de ejemplo: Dureza versus resistencia al impacto | Tipo de material | Nivel de dureza | Resistencia al impacto |
---|---|---|---|
Acero estándar | Moderado | Medio | |
Acero endurecido | Alto | Alto | |
Materiales compuestos | muy alto | muy alto |
Prevención de daños por moho
Piense en un pequeño trozo de residuo que queda atrapado en su molde durante una ejecución crucial. Un material resistente resiste estos golpes repentinos, manteniendo el molde intacto y prolongando su vida.
Factores que influyen en la dureza
Con el tiempo, descubrí que varios factores afectan la dureza del material:
- Composición del material : Al igual que cocinar, diferentes ingredientes crean resultados diferentes. Agregar elementos como níquel y cromo al acero mejora su capacidad para soportar impactos.
- Tratamiento térmico : Es como un día de spa para los metales, fortaleciéndolos para soportar operaciones rápidas sin agrietarse.
- Microestructura : Los pequeños detalles dentro del material importan, como el tamaño del grano. Los granos finos distribuyen la energía del impacto de manera más efectiva.
Para comprender mejor estos elementos, es posible que desee explorar los estudios de ciencia de materiales 4 en ingeniería metalúrgica.
Aplicaciones prácticas en la industria
En mi experiencia, los materiales resistentes para moldes en máquinas de inyección de alta velocidad son como automóviles confiables. Pasa menos tiempo arreglando y más tiempo funcionando sin problemas. Mantienen la máxima calidad incluso con un uso constante, preservando la forma del molde.
Ejemplo de rebajas:
- Punto 1: el tratamiento térmico adecuado fortalece la tenacidad.
- Punto 2: La microestructura afecta en gran medida la resistencia al impacto.
Para obtener más información sobre cómo se comportan los diferentes materiales en cuanto a dureza, consulte los estudios de casos de la industria 5 . Estos conocimientos pueden ayudarle a elegir el material adecuado para sus necesidades específicas, equilibrando calidad con eficiencia.
La dureza previene fracturas del molde durante operaciones rápidas.Verdadero
La alta tenacidad absorbe la energía cinética, lo que reduce el riesgo de fractura en los moldes.
La microestructura no afecta la resistencia al impacto de los moldes.FALSO
La microestructura influye en la distribución de la energía, afectando la tenacidad y la resistencia.
¿Por qué la resistencia a la deformación es fundamental para la longevidad del molde?
¿Alguna vez has pensado por qué algunos mohos duran mucho tiempo mientras que otros desaparecen tan rápido?
La resistencia a la deformación es muy importante para la vida útil de un molde. Esto se debe a que mantiene fuerte la estructura del molde bajo alta presión. Realmente reduce el daño y ayuda a mantener la precisión durante mucho tiempo.
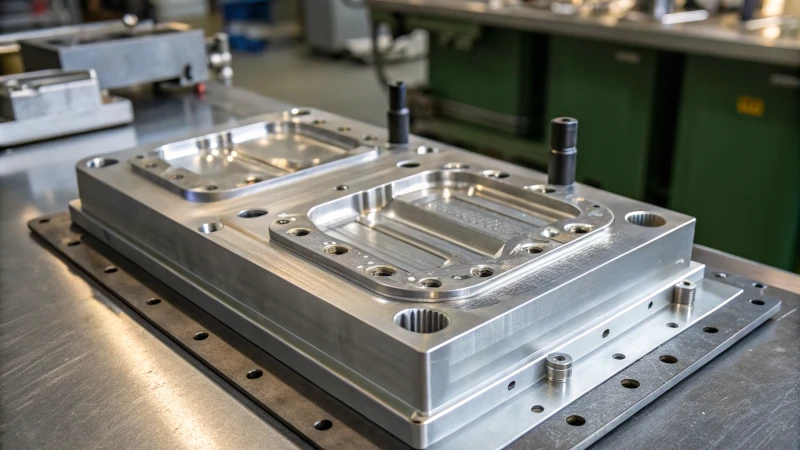
El papel de la dureza en la resistencia a la deformación
Recuerdo mis primeros días en la industria del molde. Me quedé asombrado ante las gigantescas máquinas que parecían dar vida a los productos de plástico. Una cosa quedó clara rápidamente: el acero para moldes más duro resiste mejor la deformación. Durante el moldeo por inyección, el molde se enfrenta a altas presiones, lo que podría provocar una deformación elástica no deseada si el acero es demasiado blando. Imagínese intentar moldear productos grandes y de paredes gruesas; una alta presión de inyección podría doblar permanentemente un molde de acero más blando, lo que provocaría errores e imprecisiones costosos.
Tabla 1: Impacto de la dureza en la deformación del molde
Tipo de acero | Dureza ( HRC ) | Tasa de deformación |
---|---|---|
H13 | 48-52 | Bajo |
Estándar | 35-40 | Medio |
Esto realmente muestra por qué el acero de alta dureza 6 , como el H13, es esencial para mantener estables las cavidades del molde bajo presión. El uso de acero de alta dureza es muy importante para la estabilidad.
Dureza y su contribución a la longevidad
Pero hay un problema: la dureza por sí sola no es suficiente. La dureza también juega un papel muy importante. Durante las rápidas aperturas y cierres del molde, el molde experimenta grandes impactos. Si el acero carece de dureza, corre el riesgo de agrietarse y eventualmente fallar el molde. Aprendí esta lección cuando los moldes se agrietaron bajo la presión de una máquina de alta velocidad: era costoso.
Tabla 2: Impacto de la tenacidad en la resistencia a la fatiga
Tipo de acero | Nivel de dureza | Resistencia a la fatiga |
---|---|---|
De primera calidad | Alto | Excelente |
Estándar | Medio | Justo |
Nunca se debe pasar por alto la tenacidad durante la apertura y cierre rápido del molde 7 . Quizás la dureza sea más importante de lo que pensamos.
Resistencia a la fatiga y ciclos térmicos
Otro desafío es la resistencia a la fatiga. Los moldes de inyección soportan innumerables ciclos térmicos. Sin una alta tenacidad, las grietas por fatiga aparecen fácilmente. He visto moldes de trabajo en caliente sufrir grietas por fatiga superficial porque el acero no podía soportar la tensión de los cambios repetidos de temperatura; esto sucede todo el tiempo.
Elegir aceros de alta tenacidad 8 es vital ya que mantiene la integridad del molde a lo largo de muchos ciclos y extiende su vida útil; realmente, marca una gran diferencia.
Conclusión
Equilibrar la dureza y la tenacidad en los aceros para moldes es crucial; no es sólo una necesidad técnica sino también una piedra angular para una mayor longevidad del molde 9 . Mejorar la resistencia a la deformación y al mismo tiempo reducir el desgaste y la fatiga garantiza una producción eficiente y ahorro de costos a lo largo del tiempo. Según mi experiencia, invertir en los materiales adecuados desde el principio ahorra innumerables dolores de cabeza más adelante; utilizar los materiales adecuados puede cambiarlo todo.
El acero de alta dureza resiste la deformación del molde.Verdadero
La alta dureza del acero, como el H13, reduce la deformación bajo presión.
La baja tenacidad aumenta el riesgo de agrietamiento del molde.Verdadero
La baja tenacidad conduce a la propagación de grietas durante las operaciones rápidas del molde.
¿Cómo puede la selección de acero optimizar la vida útil del molde?
Cuando comencé a aprender sobre diseño de moldes, elegir el acero adecuado parecía un rompecabezas muy difícil. Pero con el tiempo entendí que es la clave para que el molde dure más. Realmente, es fundamental para la durabilidad del molde.
Las opciones de acero para la vida útil del molde tienen que ver con el equilibrio entre dureza y tenacidad. Los materiales duros ayudan a resistir el desgaste. Los materiales resistentes detienen las grietas durante el uso del molde.
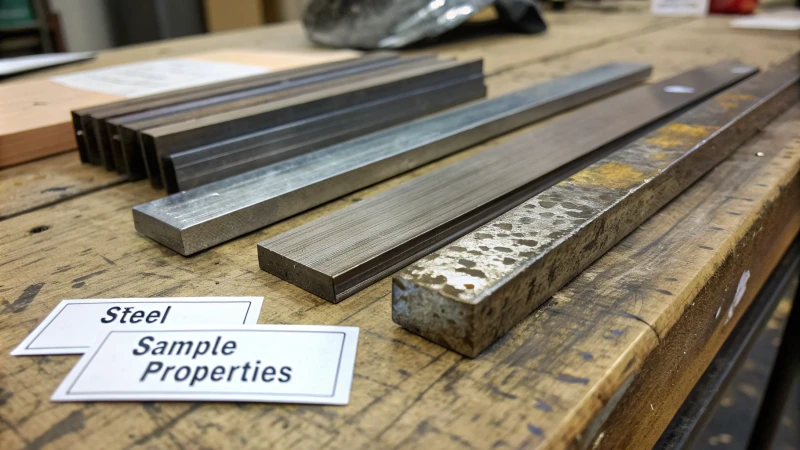
Comprender la dureza en el acero para moldes
Esa sensación de crear un molde perfecto es inigualable. El éxito depende a menudo de la dureza del acero. El acero duro tiene una alta resistencia al desgaste 10 . Esta característica es esencial para manipular plásticos fundidos abrasivos, especialmente aquellos con rellenos arenosos como fibras de vidrio. Piense en ello como un poderoso escudo que protege la cavidad del molde para que no cambie de forma.
Tipo de acero | Dureza típica ( HRC ) |
---|---|
H13 | 48-52 |
P20 | 28-32 |
Mi experiencia me enseñó que los aceros de mayor dureza, como el H13 posttratado térmicamente, lo cambian todo. Reducen el desgaste durante el desmolde y disminuyen los rayones en la superficie del molde, extendiendo la vida útil del molde.
El papel de la dureza en la longevidad del molde
He visto moldes sobrevivir a innumerables ciclos en máquinas rápidas. La tenacidad es muy importante ya que absorbe el impacto durante las operaciones rápidas del molde, evitando fallas importantes como fracturas.
Resistencia al impacto
Recuerdo cuando la alta presión casi arruina un proyecto. Afortunadamente, la elección de acero resistente salvó el proyecto al evitar grietas bajo tensión.
Guión | Respuesta de acero |
---|---|
Cierre rápido del molde | Absorbe el impacto sin agrietarse |
Aumento repentino de presión | Mantiene la integridad estructural |
Equilibrio de dureza y tenacidad
Equilibrar dureza y tenacidad es complicado. He pasado horas estudiando los entornos del molde para encontrar un punto en el que el acero sea lo suficientemente duro para resistir el desgaste y lo suficientemente resistente para los impactos. Este equilibrio ayuda a que los moldes duren más, reduce los costos de mantenimiento y mantiene las líneas de producción en movimiento sin problemas. Encontrar el equilibrio adecuado se adapta a las necesidades de moldeo específicas; No se trata sólo de elegir el acero más duro sino de lograr una eficiencia sostenida 11 en el tiempo.
El acero H13 es más duro que el acero P20.Verdadero
H13 tiene una dureza de 48-52 HRC, mientras que P20 tiene 28-32 HRC.
Una mayor dureza reduce el daño a la superficie del molde.Verdadero
La alta dureza resiste los abrasivos, manteniendo la precisión del molde.
Conclusión
La dureza y tenacidad del acero para moldes influyen significativamente en la longevidad del molde de inyección al mejorar la resistencia al desgaste, la absorción de impactos y la estabilidad de la deformación, lo que en última instancia garantiza una producción eficiente y costos de mantenimiento reducidos.
-
Descubra cómo una mayor dureza reduce el desgaste en los moldes de inyección al resistir la abrasión del plástico fundido. ↩
-
Comprenda por qué seleccionar aceros para moldes con una dureza óptima es fundamental para mantener la forma bajo presión. ↩
-
Descubra cómo el equilibrio de estas propiedades mejora el rendimiento del material en entornos exigentes. ↩
-
Conozca los estudios avanzados que exploran la relación entre dureza y resistencia al impacto. ↩
-
Descubra ejemplos del mundo real de selección de materiales basados en la dureza para diversas aplicaciones industriales. ↩
-
Al hacer clic en este enlace obtendrá información detallada sobre cómo la dureza afecta la resistencia a la deformación en el acero para moldes. ↩
-
Explore este enlace para comprender cómo la dureza contribuye a la durabilidad del molde y a la resistencia a los impactos. ↩
-
Descubra estrategias prácticas para mejorar la longevidad del molde mediante la mejora de las propiedades y el diseño de los materiales. ↩
-
Descubra estrategias prácticas para mejorar la longevidad del molde mediante la mejora de las propiedades y el diseño de los materiales. ↩
-
Explore cómo la dureza mejora la resistencia al desgaste y preserva la precisión del molde. ↩
-
Descubra cómo las propiedades equilibradas del acero garantizan una eficiencia a largo plazo. ↩