El moldeo por inyección es un proceso fascinante que requiere precisión y cuidado. He aprendido que incluso los ajustes más pequeños pueden generar mejoras notables en la calidad del producto.
Para reducir las tasas de defectos en el moldeo por inyección, ajuste parámetros clave como la temperatura, la presión, la velocidad y el tiempo. Cada parámetro afecta la calidad del producto final y debe ajustarse con precisión en función de las necesidades de fabricación específicas y las características del material.
Comprender la importancia de estos parámetros es sólo el comienzo. Profundicemos en cada ajuste, donde compartiré ideas que pueden ayudarle a abordar sus desafíos de fabricación específicos.
El ajuste de la temperatura del molde reduce los defectos del moldeo por inyección.Verdadero
La temperatura adecuada del molde mejora el flujo del material, reduce los defectos superficiales y mejora la calidad del producto.
- 1. ¿Cuáles son los ajustes de temperatura clave en el moldeo por inyección?
- 2. ¿Cómo afecta la presión a la calidad del moldeo por inyección?
- 3. ¿Por qué es vital el control de la velocidad en los procesos de moldeo por inyección?
- 4. ¿Qué papel juega el tiempo en la minimización de defectos en el moldeo por inyección?
- 5. Conclusión
¿Cuáles son los ajustes de temperatura clave en el moldeo por inyección?
El control de la temperatura es fundamental en el moldeo por inyección e influye en la calidad del producto y la eficiencia de la producción.
Los ajustes de temperatura clave en el moldeo por inyección implican regular las temperaturas del cilindro y del molde para optimizar el flujo de material y reducir los defectos. La configuración adecuada depende de los requisitos específicos del material y del producto, equilibrando el flujo de fusión y la eficiencia de enfriamiento.
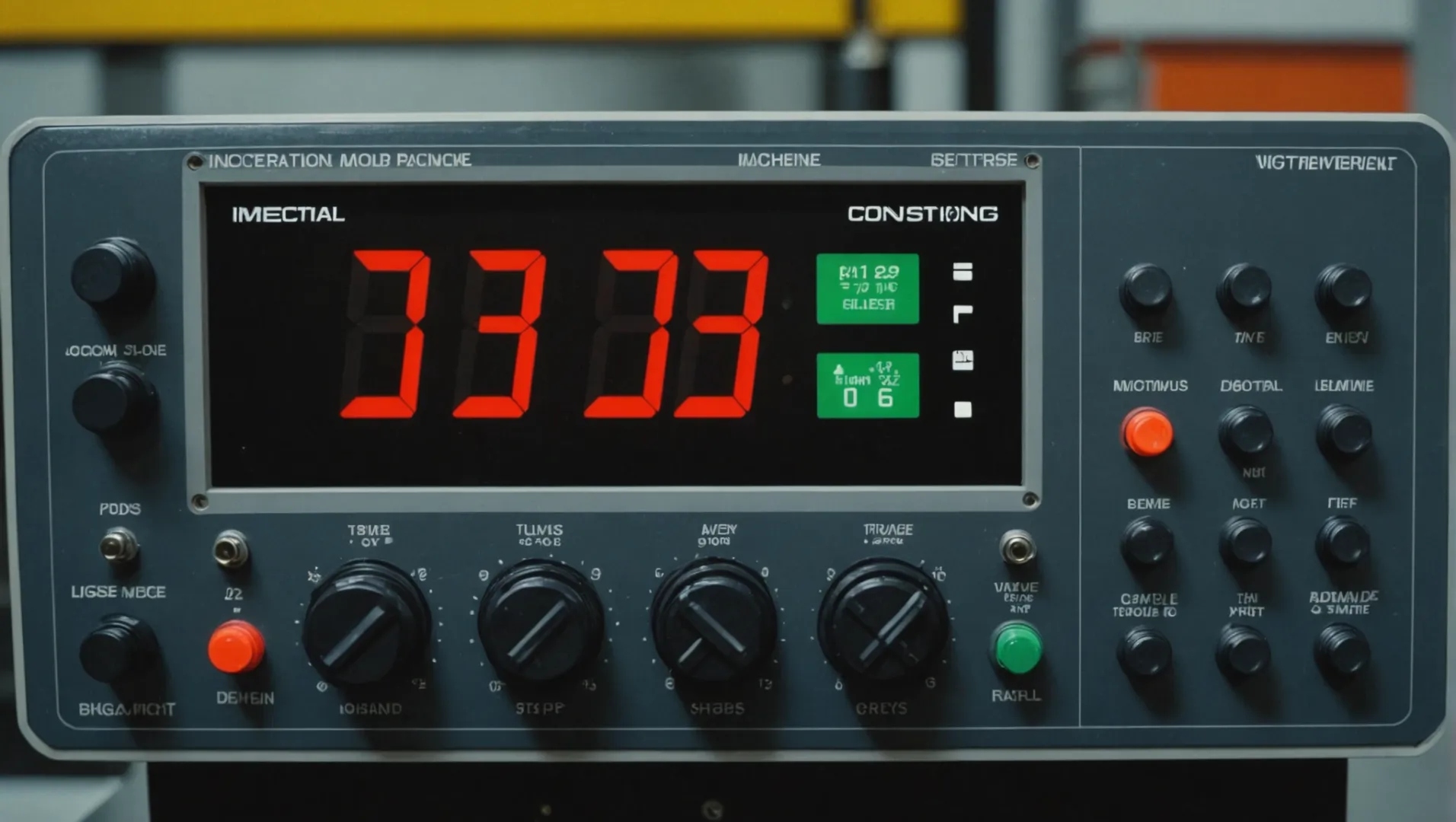
Ajuste de la temperatura del barril
La temperatura del barril influye significativamente en cómo el plástico se derrite y fluye hacia el molde.
-
Alta temperatura del barril: si los productos presentan problemas como rayas plateadas o burbujas, podría deberse a una temperatura excesiva del barril, lo que provoca la degradación del plástico. Por ejemplo, disminuir la temperatura de 230°C, 240°C y 250°C a 220°C, 230°C y 240°C puede mitigar estos defectos.
-
Baja temperatura del barril: Por el contrario, las bajas temperaturas del barril pueden provocar marcas de material frío o un llenado insuficiente. El aumento gradual de las temperaturas (por ejemplo, de 200 °C, 210 °C y 220 °C a 210 °C, 220 °C y 230 °C) puede mejorar el flujo y el llenado.
Optimización de la temperatura del molde
Los ajustes de temperatura del molde son cruciales para lograr la calidad superficial y la precisión dimensional deseadas.
-
Alta temperatura del molde: esto puede resultar beneficioso para productos que requieren un acabado superficial de alta calidad. El aumento de la temperatura del molde, por ejemplo de 50 °C a 60 °C, ayuda a lograr una mejor estética de la superficie al permitir que el plástico fluya más suavemente y llene la cavidad del molde por completo.
-
Baja temperatura del molde: Reducir las temperaturas del molde, por ejemplo de 80 °C a 70 °C, puede ayudar a un enfriamiento más rápido, reducir los tiempos de ciclo y aumentar potencialmente la eficiencia de la producción.
Ajustes de temperatura de equilibrio
Un enfoque sistemático es esencial al ajustar estos parámetros. Cambie únicamente un parámetro a la vez para evaluar su impacto con precisión. Documente cada cambio y su efecto en la calidad del producto. Esta práctica no solo ayuda a solucionar problemas sino también a identificar las condiciones óptimas para materiales y productos específicos.
Para obtener más información sobre las estrategias de control de temperatura 1 en el moldeo por inyección, comprender la interacción entre estas configuraciones puede guiarlo hacia un proceso de producción más eficiente.
La alta temperatura del barril provoca la degradación del plástico.Verdadero
El calor excesivo provoca problemas como rayas plateadas o burbujas.
La baja temperatura del molde mejora la calidad de la superficie.FALSO
Las temperaturas más altas del molde mejoran la estética de la superficie al suavizar el flujo.
¿Cómo afecta la presión a la calidad del moldeo por inyección?
En el moldeo por inyección, la presión desempeña un papel fundamental a la hora de determinar la calidad del producto y afecta todo, desde el llenado hasta el acabado.
La presión en el moldeo por inyección es fundamental ya que afecta la calidad del llenado, la densidad del producto y las tasas de defectos. El ajuste adecuado de las presiones de inyección y retención garantiza un llenado óptimo, minimiza defectos como deformación y contracción y mantiene la integridad estructural.
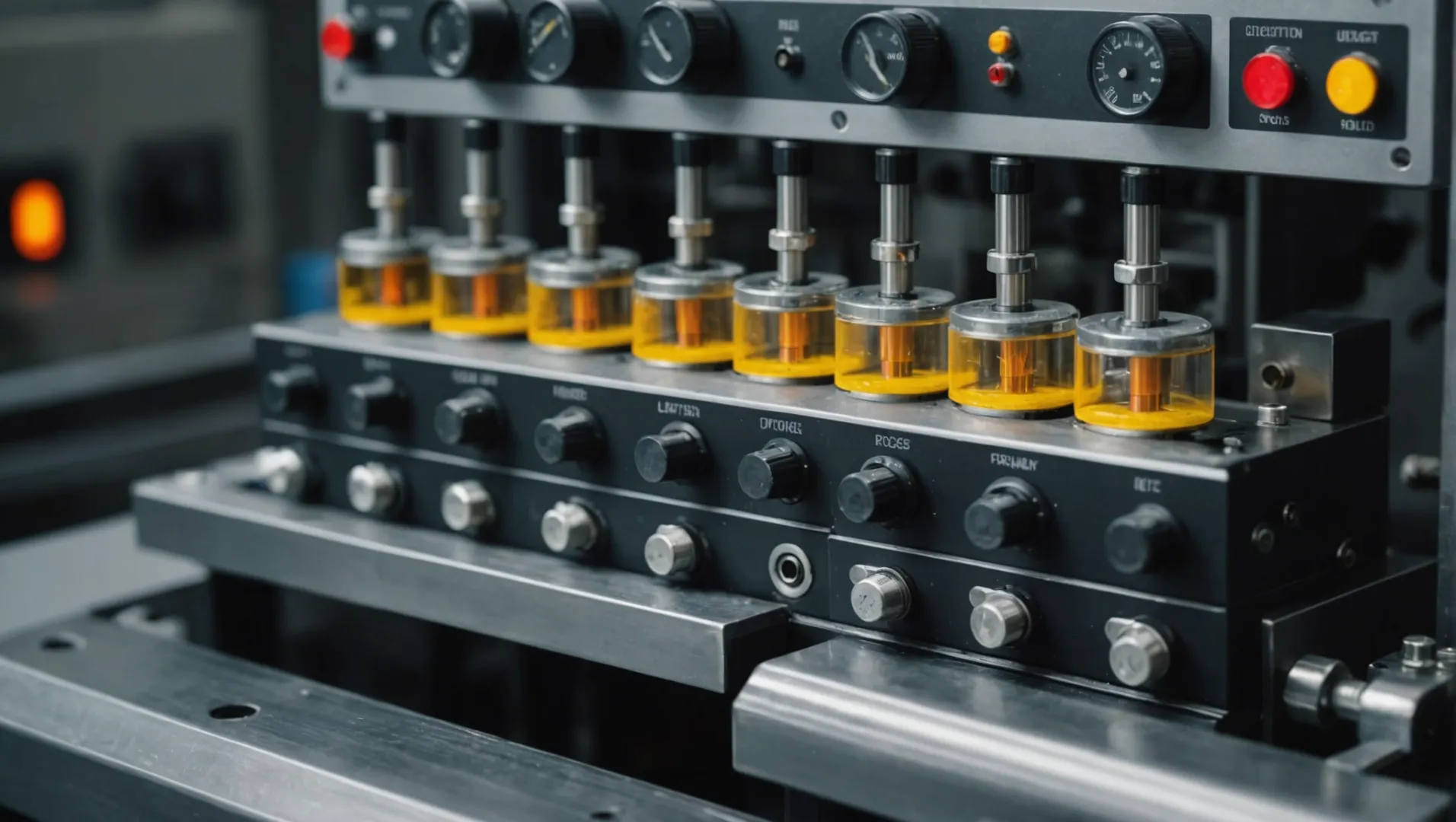
Comprender la presión de inyección
La presión de inyección es la fuerza utilizada para inyectar plástico fundido en la cavidad del molde. Este parámetro influye significativamente en el proceso de llenado y en la calidad del producto final. La alta presión de inyección garantiza que el plástico llegue a todas las áreas del molde, lo que reduce problemas como disparos cortos o un llenado incompleto.
Por ejemplo, si nota que sus productos tienen disparos cortos o un llenado insuficiente, considere aumentar ligeramente la presión de inyección. Por ejemplo, un aumento de 80 MPa a 90 MPa puede ayudar a lograr un mejor llenado. Sin embargo, una presión excesiva puede provocar problemas como rebabas o dificultad para desmoldar, por lo que el equilibrio es crucial.
El papel de mantener la presión
Una vez que se llena el molde, se aplica presión de retención para compensar la contracción del material a medida que se enfría y solidifica. Ajustar la presión de sujeción es esencial para gestionar defectos como marcas de contracción y deformaciones.
El aumento de la presión de sujeción puede mitigar la contracción y las abolladuras, pero debe hacerse con cuidado para evitar la concentración de tensiones. Lo ideal es que la presión de mantenimiento esté entre el 50 % y el 80 % de la presión de inyección, adaptada al tamaño y la forma del producto. Por ejemplo, con una presión de inyección de 100 MPa, un rango de presión de mantenimiento de 60 MPa a 80 MPa podría ser óptimo.
Equilibrio de presión con temperatura
Es esencial tener en cuenta la temperatura al ajustar la configuración de presión. Por ejemplo, una temperatura alta del molde podría requerir una presión de inyección más baja para evitar el sobrellenado. Por el contrario, una temperatura baja del molde podría requerir una presión de inyección más alta para garantizar un llenado completo sin defectos como marcas de material frío.
Estudio de caso: lograr ajustes de presión óptimos
Considere un escenario en el que un fabricante enfrenta problemas de deformación y contracción 2 en sus productos. Al ajustar sistemáticamente la presión de mantenimiento mientras se monitorean los resultados, pueden ajustar su proceso para reducir estos defectos significativamente. Este enfoque no sólo mejora la calidad del producto sino que también mejora la eficiencia de la producción al minimizar el desperdicio de material.
Esta interacción entre los ajustes de presión demuestra que comprender y controlar la inyección y mantener las presiones son vitales para lograr una calidad constante en el moldeo por inyección.
La alta presión de inyección reduce los disparos cortos.Verdadero
El aumento de la presión de inyección garantiza un llenado completo del molde, reduciendo los disparos cortos.
Una presión de sujeción excesiva provoca marcas de contracción.FALSO
La presión de sujeción correctamente ajustada minimiza las marcas de contracción, no las excesivas.
¿Por qué es vital el control de la velocidad en los procesos de moldeo por inyección?
El moldeo por inyección exige un control preciso sobre numerosos parámetros, siendo la velocidad un factor crucial que influye en la calidad del producto y la eficiencia de la producción.
El control de la velocidad en el moldeo por inyección es vital para garantizar la calidad del producto, prevenir defectos como rebabas y quemaduras y optimizar los tiempos de los ciclos. Los ajustes de velocidad adecuados permiten un mejor llenado de las cavidades del molde y mejoran la eficiencia general de fabricación.
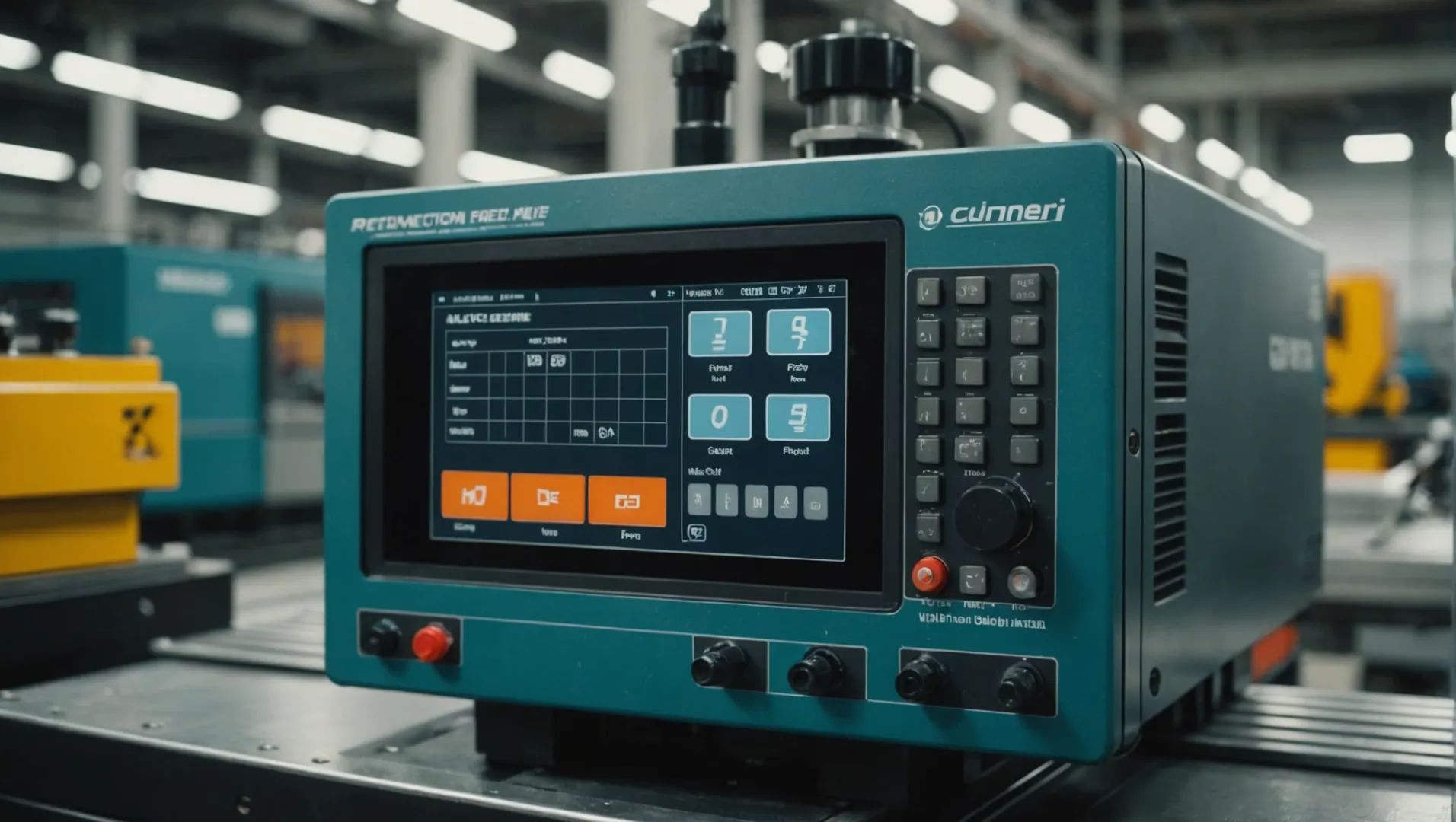
Importancia de la velocidad de inyección en el llenado de moldes
La velocidad de inyección afecta significativamente la forma en que el plástico fundido llena la cavidad del molde. Para productos de paredes delgadas o de formas complejas, podría ser necesaria una velocidad de inyección más alta para garantizar que el material llegue a todas las áreas del molde antes de que comience a solidificarse. Sin embargo, esto requiere un manejo cuidadoso para evitar defectos como fumigación o quema.
Por ejemplo, si un producto presenta marcas de flujo o llenado insuficiente, aumentar la velocidad de inyección de 50 mm/s a 60 mm/s puede ayudar a llenar el molde de manera más eficiente. Sin embargo, se necesita precaución para evitar posibles problemas como rebabas, que pueden ocurrir si la velocidad es demasiado alta.
Papel de la velocidad del tornillo en la plastificación
La velocidad del tornillo juega un papel fundamental en el proceso de plastificación. Si el tornillo gira demasiado rápido, puede provocar que el plástico se sobrecaliente y se descomponga, provocando defectos como puntos negros. Por el contrario, una velocidad de tornillo más lenta podría dar lugar a una plastificación deficiente, lo que afectaría tanto a la calidad del producto como a la eficiencia de la producción.
Ajustar la velocidad del tornillo de 100 r/min a 80 r/min puede ayudar a mitigar los problemas de sobrecalentamiento, mientras que un aumento de 60 r/min a 70 r/min puede mejorar la plastificación cuando se encuentran marcas de material frío.
Equilibrando la velocidad con la calidad del producto
Equilibrar los ajustes de velocidad es clave para mantener la calidad del producto. Una velocidad de inyección más rápida ayuda a llenar los moldes rápidamente, pero también puede introducir defectos si no se gestiona con cuidado. De manera similar, encontrar la velocidad correcta del tornillo garantiza que el material se funda y mezcle adecuadamente sin comprometer la calidad.
Considere utilizar un enfoque estructurado al ajustar las velocidades: cambie un parámetro a la vez, observe los efectos en el producto final y documente estos cambios meticulosamente para construir una base de conocimientos. Este proceso metódico puede evitar problemas que surjan de ajustes simultáneos.
Optimización de la velocidad para lograr eficiencia
Además de las consideraciones de calidad, el control de la velocidad también afecta la eficiencia de la producción. Tiempos de ciclo más rápidos pueden aumentar la producción, pero deben equilibrarse con el riesgo de problemas de calidad. Ajustar los parámetros de velocidad en función de las necesidades específicas de cada producto y tipo de material puede conducir a una mayor eficiencia sin sacrificar la calidad.
Implementar un enfoque sistemático para los ajustes de velocidad, como modificar gradualmente las velocidades y monitorear los resultados, es crucial para optimizar los procesos de moldeo por inyección. Al aprovechar técnicas precisas de control de velocidad 3 , los fabricantes pueden lograr productos de alta calidad y ciclos de producción eficientes.
Una mayor velocidad de inyección evita defectos en el llenado del molde.Verdadero
El aumento de la velocidad garantiza que el plástico fundido llegue a todas las áreas antes de solidificarse.
Una velocidad de tornillo más rápida siempre mejora la plastificación.FALSO
Una velocidad excesiva puede provocar sobrecalentamiento y descomposición, provocando defectos.
¿Qué papel juega el tiempo en la minimización de defectos en el moldeo por inyección?
Los ajustes de tiempo en el moldeo por inyección son fundamentales para mejorar la calidad del producto y minimizar los defectos. Cada segundo cuenta.
En el moldeo por inyección, el tiempo es crucial para garantizar la integridad del producto. Ajustar adecuadamente los tiempos de inyección y enfriamiento puede evitar problemas como llenado insuficiente, rebabas y deformaciones, lo que genera resultados de mayor calidad.
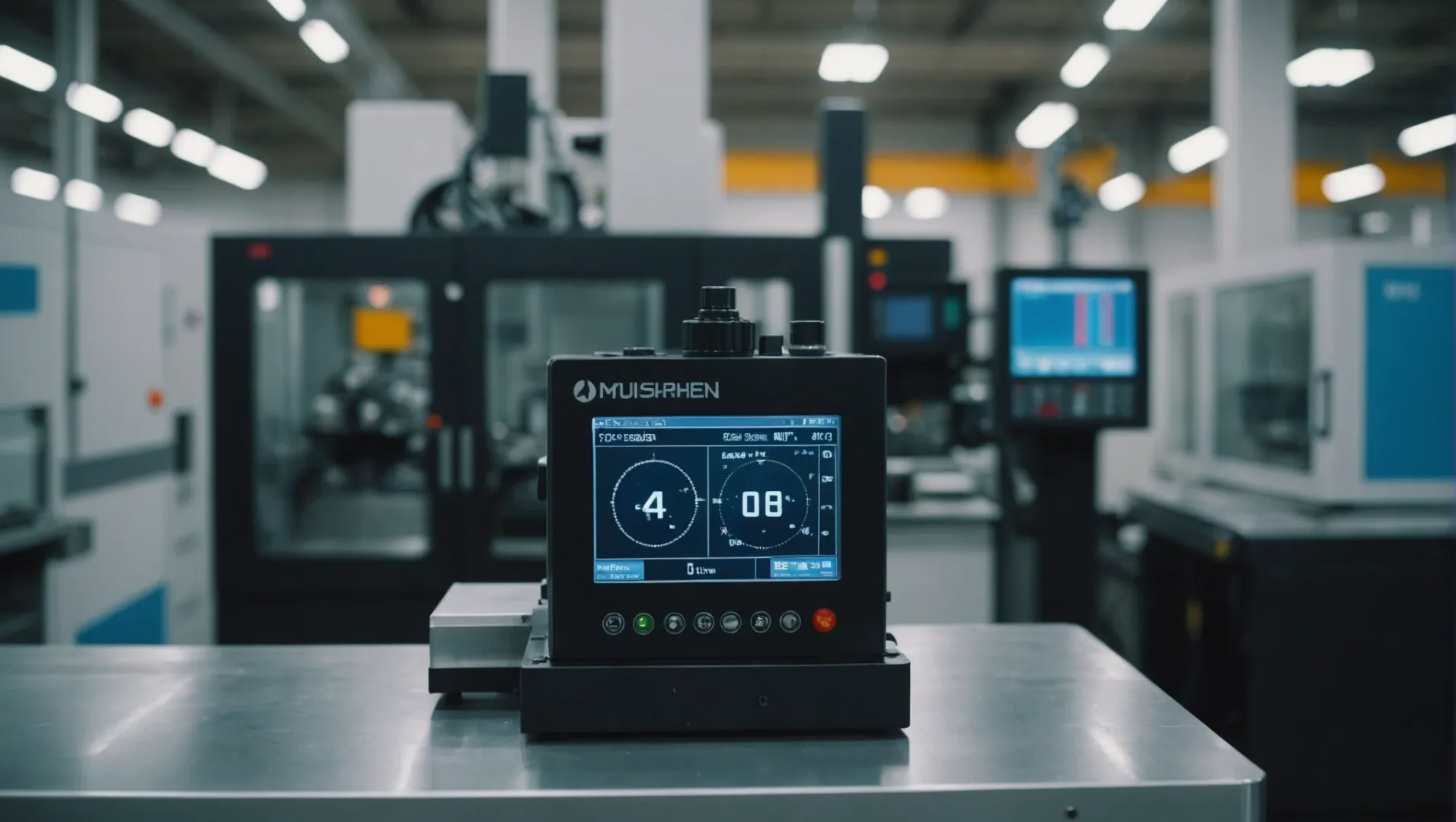
Comprensión del tiempo en el moldeo por inyección
Los parámetros de sincronización en el moldeo por inyección abarcan varios aspectos, como el tiempo de inyección, el tiempo de enfriamiento y el tiempo general del ciclo. Cada uno de estos puede tener un profundo impacto en la calidad del producto final.
Tiempo de inyección
El tiempo de inyección es el tiempo necesario para llenar la cavidad del molde con plástico fundido. Si el tiempo de inyección es demasiado corto, puede provocar un llenado insuficiente o inyecciones cortas. Por el contrario, un tiempo de inyección demasiado largo podría provocar problemas como llenado excesivo o rebabas.
Por ejemplo, un producto que experimenta disparos cortos puede requerir una extensión del tiempo de inyección de 2 a 3 segundos, mejorando el llenado del molde sin causar defectos.
Tiempo de enfriamiento
El tiempo de enfriamiento es fundamental para solidificar el plástico antes de desmoldar. Una refrigeración insuficiente puede provocar deformaciones o dimensiones inestables después del desmolde. Ajustar el tiempo de enfriamiento en función de las propiedades y el espesor del material garantiza la estabilidad dimensional y reduce los defectos.
Considere un escenario en el que el tiempo de enfriamiento original de 15 s de un producto de 3 mm de espesor es inadecuado, lo que provoca deformación. Aumentar este tiempo a 20 segundos podría estabilizar las dimensiones del producto.
Mejores prácticas para ajustes de sincronización
- Ajuste de un solo parámetro: modifique siempre un parámetro a la vez para medir con precisión su impacto en la calidad del producto.
- Documentación: mantenga registros detallados de todos los cambios y resultados para establecer una referencia para futuras ejecuciones de producción.
- Verificaciones periódicas del equipo: asegúrese de que la maquinaria funcione de manera óptima para evitar discrepancias en el tiempo que afecten la calidad del producto.
Ejemplo de tabla de tiempos
Parámetro | Configuración original | Configuración ajustada |
---|---|---|
Tiempo de inyección | 2s | 3s |
Tiempo de enfriamiento | 15 | 20 años |
Estos ajustes ilustran cómo la sincronización juega un papel crítico en la minimización de defectos durante los procesos de moldeo por inyección 4 . Al ajustar cuidadosamente estas configuraciones, los fabricantes pueden mejorar la eficiencia y la calidad del producto y, en última instancia, reducir las tasas de defectos.
El aumento del tiempo de enfriamiento reduce la deformación de los productos.Verdadero
Los tiempos de enfriamiento más prolongados permiten que el plástico se solidifique adecuadamente, lo que reduce la deformación.
Acortar el tiempo de inyección evita el sobrellenado y las rebabas.Verdadero
Reducir el tiempo de inyección ayuda a evitar el exceso de material, evitando sobrellenados y rebabas.
Conclusión
Al ajustar estratégicamente los parámetros de moldeo por inyección, puede mejorar significativamente la calidad del producto y al mismo tiempo reducir los defectos. Adopte el proceso de prueba y error para encontrar la configuración óptima para sus necesidades.
-
Obtenga conocimientos más profundos sobre la gestión eficaz de la temperatura en el moldeo por inyección: La temperatura del molde debe controlarse a 60 grados Celsius para evitar el agrietamiento por tensión en plásticos con buena fluidez como PE, PP, HIPS... ↩
-
Proporciona estrategias para abordar defectos comunes del moldeo por inyección, como la deformación.: Si el problema es una diferencia de contracción dimensional a lo largo de la pieza, reduzca la viscosidad del plástico. Esto reducirá las diferencias de presión en el... ↩
-
Descubra técnicas precisas para optimizar el control de la velocidad del moldeo por inyección: Estos son los 8 parámetros clave en el moldeo por inyección que debe alinear para producir piezas de plástico consistentes y de alta calidad. ↩
-
Descubra cómo los ajustes de sincronización precisos mejoran los resultados del moldeo por inyección: El tiempo del ciclo de moldeo por inyección o el tiempo de enfriamiento es uno de los factores principales para mejorar y mantener la eficiencia en el proceso de moldeo por inyección. ↩