la consistencia de color perfecta 1 en las piezas moldeadas por inyección es un aspecto crítico de la fabricación que garantiza que cada parte producida tenga el mismo color, sin variaciones notables. Esta uniformidad es esencial para mantener la calidad del producto, la identidad de la marca y el cumplimiento de los estándares de la industria. Ya sea en piezas automotrices, bienes de consumo o dispositivos médicos, la consistencia del color puede afectar la estética, la funcionalidad y la adherencia regulatoria.
La consistencia de color perfecta en las partes moldeadas por inyección 2 garantiza un color uniforme en todos los productos, mejorando la estética, la identidad de la marca y el cumplimiento de los estándares de la industria.
Comprender los factores que influyen en la consistencia del color es clave para optimizar su proceso de fabricación. Profundizar para explorar cómo la selección de materiales 3 , el control del proceso y las medidas de calidad afectan el color del producto final.
La consistencia del color solo es importante por razones estéticas.FALSO
En industrias como dispositivos médicos, el color puede indicar funcionalidad o cumplimiento de las regulaciones, lo que lo hace crucial más allá de la estética.
El uso de Masterbatches siempre garantiza una consistencia de color perfecta.FALSO
Si bien los maestros proporcionan un color consistente, factores como los parámetros del proceso y la calidad del material también juegan un papel importante.
- 1. ¿Cuáles son los materiales comunes utilizados en el moldeo por inyección para la consistencia del color?
- 2. ¿Cuáles son los pasos clave para lograr la consistencia del color en el moldeo por inyección?
- 3. ¿Cuáles son los tres factores principales que influyen en la consistencia del color en el moldeo por inyección?
- 4. ¿Cuáles son las aplicaciones donde la consistencia del color es crítica?
- 5. ¿Cuáles son las diferencias entre MasterBatch y el compuesto para la consistencia del color?
- 6. Conclusión
¿Cuáles son los materiales comunes utilizados en el moldeo por inyección para la consistencia del color?
La selección de materiales es fundamental para lograr la consistencia del color, ya que diferentes plásticos y colorantes interactúan de manera única durante el proceso de moldeo.
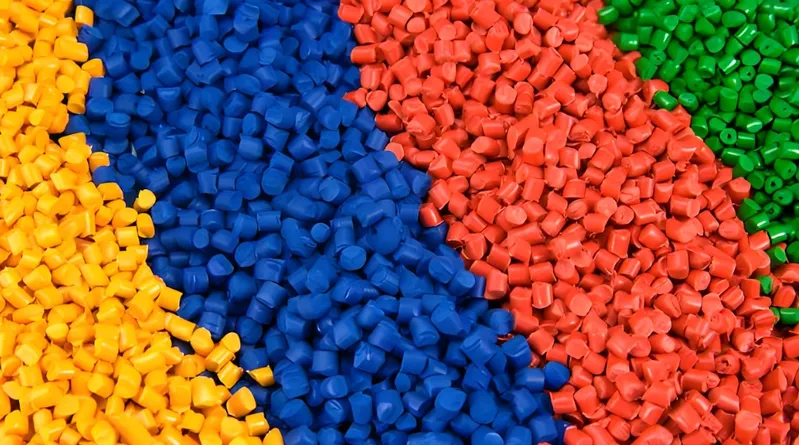
Los materiales comunes incluyen ABS, policarbonato, polipropileno y colorantes como pigmentos, colorantes y masterbatches, cada uno que afecta la estabilidad del color y la uniformidad.
Tipo de material | Estabilidad del color | Notas |
---|---|---|
ABS | Moderado | Propenso a la decoloración del estrés |
Policarbonato (PC) | Alto | UV-sensible, requiere estabilizadores |
Polipropileno (PP) | Bajo | Desafiante con algunos pigmentos |
Masterbatches | Alto | Color consistente, requiere una mezcla precisa |
ABS (Acrilonitrilo Butadieno Estireno)
El ABS se usa ampliamente para su fuerza y versatilidad, pero puede experimentar la decoloración del estrés 4 , lo que afecta la consistencia del color. El control de temperatura adecuado durante el moldeo minimiza las variaciones.
Policarbonato (PC)
El policarbonato ofrece una excelente estabilidad térmica, pero es sensible a la exposición a los rayos UV, lo que puede alterar el color con el tiempo. El uso de estabilizadores UV 5 o resinas precoloradas ayuda a mantener la consistencia.
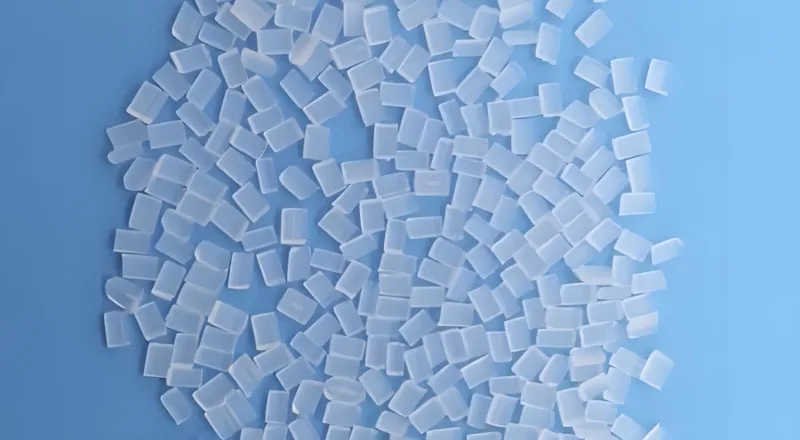
Polipropileno (PP)
La estructura cristalina de PP 6 complica la dispersión del pigmento, lo que puede conducir a un color desigual. Los colorantes compatibles y el control preciso del proceso son críticos para la uniformidad.
Colorantes: pigmentos, tintes y masterbatches
Se agregan colorantes como pigmentos, tintes y masterbatches a las resinas para lograr los colores deseados. Los pigmentos y los tintes permiten tonos personalizados, mientras que los pigmentos maestros, pigmentos concentrados en una resina portadora, proporcionan resultados consistentes para grandes ejecuciones de producción.
Todos los plásticos se comportan de la misma manera cuando están coloreados.FALSO
Diferentes plásticos tienen propiedades únicas que afectan la forma en que interactúan con los colorantes, lo que requiere enfoques a medida para cada material.
Los maestros son el método más confiable para lograr la consistencia del color.Verdadero
Masterbatches ofrece una dispersión de color consistente y son ideales para grandes volúmenes de producción.
¿Cuáles son los pasos clave para lograr la consistencia del color en el moldeo por inyección?
Lograr la consistencia del color requiere una atención meticulosa a la preparación del material, el control del proceso y las medidas de calidad durante todo el flujo de trabajo de moldeo por inyección.
Los pasos clave incluyen seleccionar materiales compatibles, mezcla de colorantes precisos, parámetros de proceso de control e implementar un riguroso control de calidad.
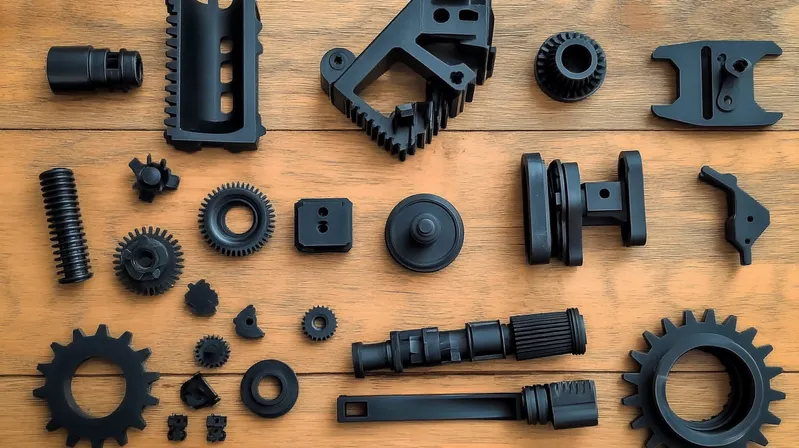
Preparación de materiales
-
Selección de resina y colorante : elija resinas y colorantes de alta calidad para evitar inconsistencias.
-
Inspección y secado : Inspeccione las materias primas para la contaminación y las resinas secas para controlar la humedad, lo que puede afectar la dispersión del color.
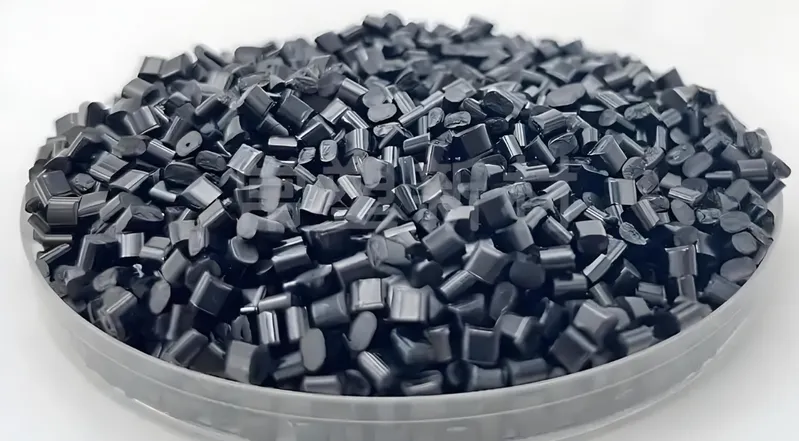
Mezcla de colorantes
-
Equipo de medición : use equipos precisos como mezclas gravimétricas para relaciones precisas de resina a color.
-
Métodos de mezcla:
- Masterbatching : ideal para grandes volúmenes, típicamente mezclados con una relación 1:24.
- Compuesto : resinas precoloradas para volúmenes medianos a altos.
- Mezcla de pigmento seco : adecuado para lotes pequeños pero propenso a la inconsistencia.
Proceso de moldeo por inyección
- Control de temperatura : Mantenga las temperaturas consistentes de barril y moho para evitar cambios de color.
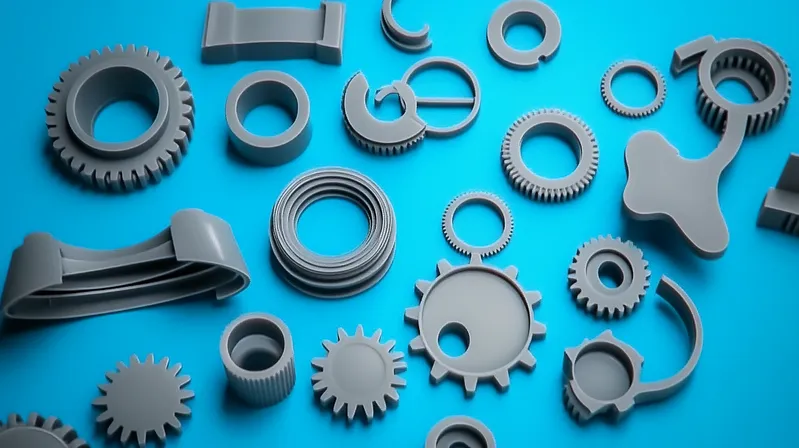
-
Velocidad y presión de inyección : use la inyección de varias etapas para minimizar el calentamiento por cizallamiento y garantizar un color uniforme.
-
Enfriamiento : asegure un enfriamiento uniforme para evitar variaciones en la cristalinidad que afectan el color.
Control de calidad
-
Medición del color : use sistemas estandarizados como Pantone o RAL y herramientas como colorímetros para verificar la consistencia.
-
Monitoreo del proceso : ajuste regularmente los parámetros para mantener la uniformidad.
Se puede lograr una consistencia de color perfecta sin medidas de control de calidad.FALSO
El control de calidad es esencial para detectar y corregir variaciones en el color durante la producción.
El control preciso de los parámetros del proceso es crucial para la uniformidad del color.Verdadero
Factores como la temperatura y la presión afectan directamente cómo los colorantes se dispersan y se estabilizan en la parte moldeada.
¿Cuáles son los tres factores principales que influyen en la consistencia del color en el moldeo por inyección?
Tres factores críticos: compatibilidad material, control de procesos y garantía de calidad, determinan el éxito de lograr la consistencia del color en las piezas moldeadas por inyección.
La compatibilidad del material, el control del proceso y la garantía de calidad son los tres factores principales que influyen en la consistencia del color, cada uno que afecta cómo los colorantes se integran y se estabilizan en el producto final.
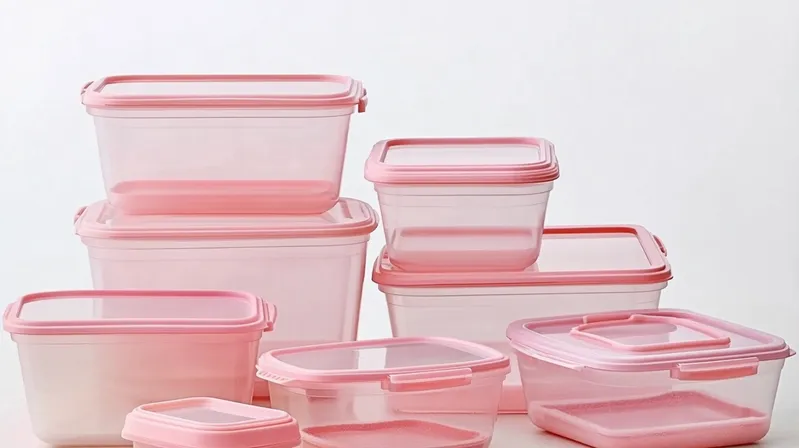
Compatibilidad de materiales
La interacción entre resina y colorante es fundamental. Los materiales incompatibles pueden conducir a una dispersión deficiente, causando rayas o un color desigual. Por ejemplo, el polipropileno requiere pigmentos específicos para resultados uniformes debido a su estructura cristalina.
Control de procesos
El control preciso de los parámetros de moldeo es vital:
-
Temperatura : afecta la viscosidad de la resina y la dispersión de los colorantes.
-
Presión : la alta presión puede causar calentamiento de corte, lo que lleva a inconsistencias.
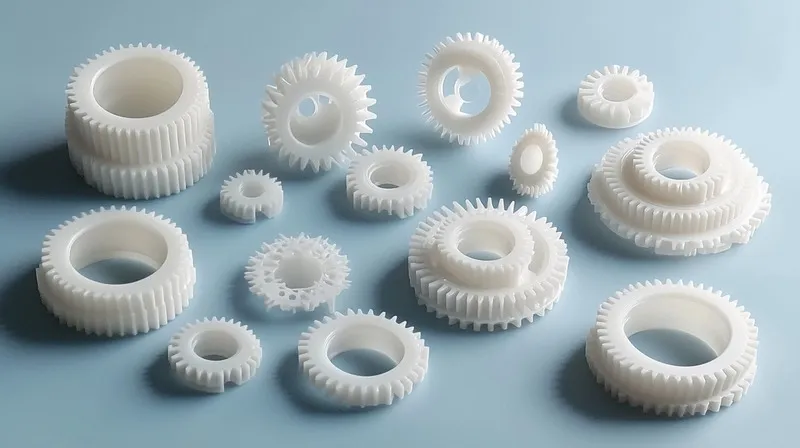
- Velocidad de enfriamiento : el enfriamiento desigual puede causar variaciones de color debido a las diferencias de cristalinidad.
Seguro de calidad
Los controles de calidad rigurosos aseguran la consistencia:
- Medición del color : use colorímetros o espectrofotómetros para cuantificar las diferencias.
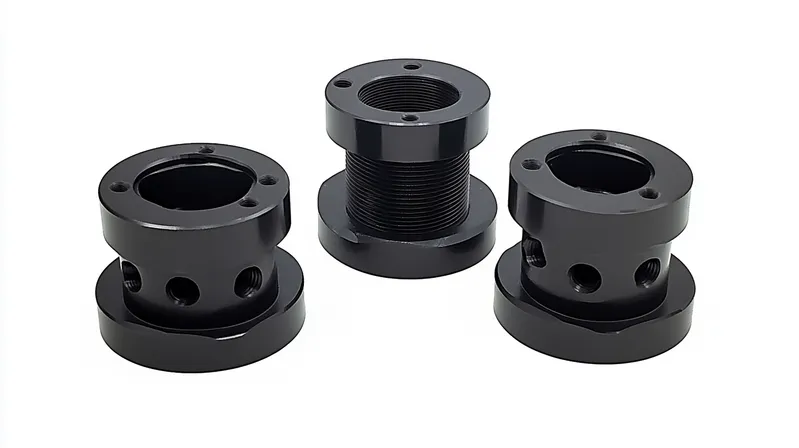
-
Estandarización : adopte estándares de color como Pantone o RAL.
-
Prueba de lotes : muestreo regular para detectar y corregir desviaciones.
La compatibilidad del material es el único factor que afecta la consistencia del color.FALSO
Si bien es importante, el control de procesos y la garantía de calidad son igualmente críticos para lograr un color uniforme.
Los sistemas de color estandarizados como Pantone aseguran una combinación de color perfecta en diferentes lotes.Verdadero
Estos sistemas proporcionan una referencia universal, reduciendo el riesgo de variaciones de color.
¿Cuáles son las aplicaciones donde la consistencia del color es crítica?
La consistencia del color es crucial en las industrias donde la estética, la marca y la funcionalidad dependen del color uniforme entre los productos.
Las industrias como el automóvil, los bienes de consumo, los dispositivos médicos y el embalaje dependen de la consistencia del color para la marca, la funcionalidad y el cumplimiento.
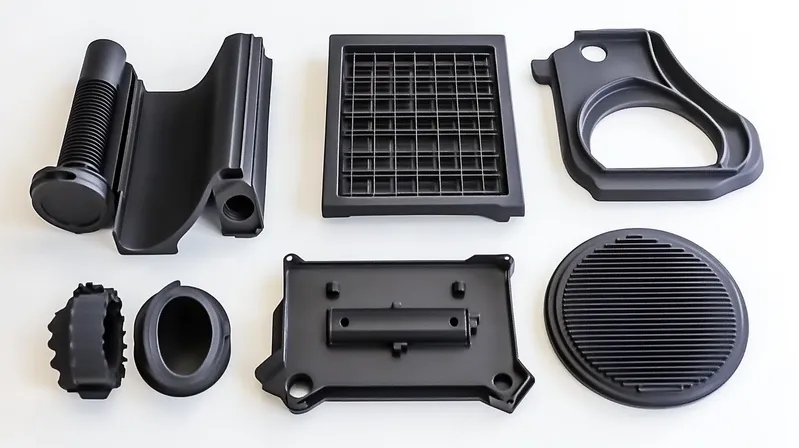
Industria automotriz
En la fabricación de automóviles 7 , la consistencia del color es vital para piezas interiores y exteriores. Los paneles, paneles o molduras no coincidentes pueden restar valor a la apariencia y la calidad percibida.
Bienes de consumo
Para la electrónica, los juguetes y los electrodomésticos, el color consistente garantiza el reconocimiento de marca y la satisfacción del cliente. Las empresas como Apple o LEGO confían en la coincidencia de color precisa.
Dispositivos médicos
En aplicaciones médicas, el color puede indicar la funcionalidad (por ejemplo, los tamaños) o el cumplimiento de los estándares. Los materiales que cumplen con la FDA 8 a menudo requieren un color constante para la seguridad e identificación.
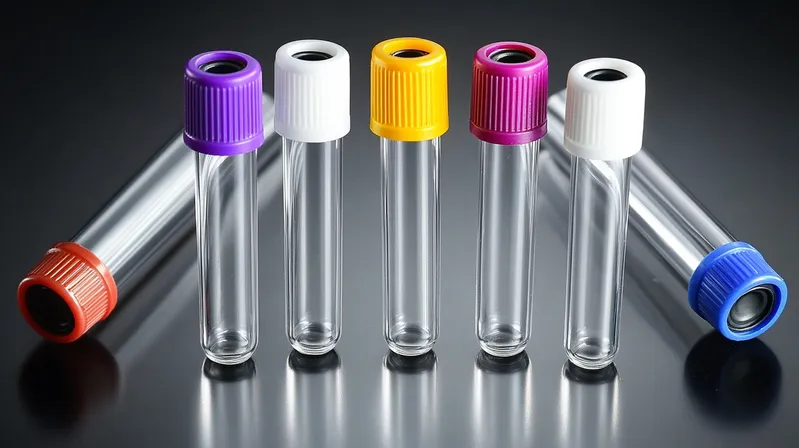
Embalaje
En el embalaje, especialmente para alimentos y bebidas, el color consistente es clave para el reconocimiento de la marca. El icónico rojo de Coca-Cola debe ser uniforme en todos los empaques.
La consistencia del color solo es crítica en los productos de consumo de alta gama.FALSO
Es igualmente importante en industrias como dispositivos médicos y envases, donde la funcionalidad y el cumplimiento están en juego.
El color inconsistente puede conducir a retiros de productos en industrias reguladas.Verdadero
En sectores como dispositivos médicos, las variaciones de color pueden dar lugar al incumplimiento de los estándares de seguridad.
¿Cuáles son las diferencias entre MasterBatch y el compuesto para la consistencia del color?
Masterbatch y compuestos son dos métodos comunes para agregar color a piezas moldeadas por inyección, cada una con ventajas y limitaciones distintas.
Masterbatch 9 implica mezclar colorantes 10 con resina durante el moldeo, mientras que el compuesto utiliza resinas precoloradas, cada una adecuada para diferentes escalas de producción y necesidades de color.
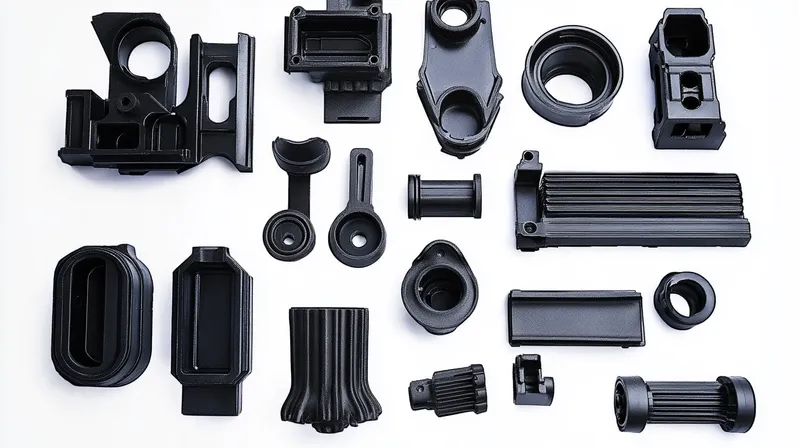
lote maestro
-
Proceso : los colorantes se concentran en una resina portadora y se mezclan con la resina base durante el moldeo.
-
Ventajas : color consistente, rentable para grandes volúmenes, colores fáciles de cambiar.
-
Desventajas : requiere una mezcla precisa, grandes cantidades de pedido mínimo (por ejemplo, 2 toneladas).
Compuesto
- Proceso : las resinas son preculadas por proveedores antes de moldear.
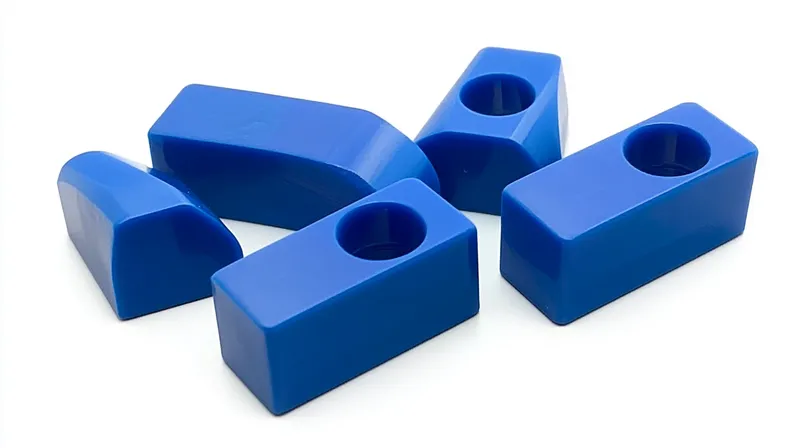
-
Ventajas : colores personalizados, adecuados para volúmenes medianos a altos, resultados consistentes.
-
Desventajas : mayores costos para lotes pequeños, menos flexibilidad en los cambios de color.
Método | Mejor para | Limitaciones |
---|---|---|
lote maestro | Grandes tiradas de producción | Altos pedidos mínimos |
Compuesto11 | Colores personalizados | Caro para lotes pequeños |
Masterbatch es siempre la mejor opción para la consistencia del color.FALSO
Si bien es efectivo para grandes volúmenes, el compuesto puede ser mejor para colores personalizados o lotes más pequeños.
El compuesto ofrece más flexibilidad en la selección de color.Verdadero
Permite una personalización precisa de los colores, lo que es beneficioso para las necesidades de marca únicas.
Conclusión
Lograr la consistencia de color perfecta en las piezas moldeadas por inyección requiere un enfoque integral que integre la selección de materiales, el control preciso del proceso y el riguroso garantía de calidad. Al comprender la interacción entre resinas, colorantes y parámetros de moldeo, los fabricantes pueden producir piezas que cumplan con los más altos estándares de uniformidad y calidad. La atención al detalle en cada etapa, desde la preparación del material hasta la inspección final, es esencial para el éxito.
-
Explore este recurso para aprender estrategias efectivas para garantizar la consistencia del color en sus productos moldeados por inyección, mejorando la calidad y la identidad de la marca. ↩
-
Este enlace proporcionará información sobre el proceso de fabricación de piezas moldeadas por inyección, crucial para comprender el control de calidad y la consistencia. ↩
-
Descubra por qué la selección de materiales es vital en el moldeo por inyección, impactando la consistencia del color y la calidad general del producto. ↩
-
Comprender las causas de la decoloración del estrés puede ayudar a seleccionar los materiales y procesos adecuados para evitarlo. ↩
-
Aprender sobre los estabilizadores UV puede mejorar su conocimiento de mantener la consistencia del color en los materiales de policarbonato. ↩
-
Explorar los efectos de la estructura cristalina en el color puede mejorar su comprensión del procesamiento de polipropileno y la selección de colorantes. ↩
-
Explore cómo la consistencia del color afecta la industria automotriz, afectando tanto la estética como la calidad percibida de los vehículos. ↩
-
Conozca los estándares críticos para la consistencia del color en dispositivos médicos para garantizar la seguridad y el cumplimiento de las regulaciones. ↩
-
Explore este enlace para comprender el proceso MasterBatch y sus beneficios en el moldeo por inyección, mejorando su conocimiento de la aplicación de color. ↩
-
Conozca los diferentes tipos de colorantes utilizados en el moldeo por inyección, lo que puede mejorar su comprensión de las técnicas de aplicación de color. ↩
-
Descubra el método de compuesto y sus ventajas para los colores personalizados en el moldeo por inyección, lo que puede ayudarlo a tomar decisiones de producción informadas. ↩