Injection -Formteile sind ein weit verbreitetes Herstellungsprozess zur Herstellung präziser plastischer Teile, von kleinen Konsumgütern bis hin zu großen industriellen Komponenten. Ein kritischer Faktor bei der Gestaltung dieser Teile ist die Wandstärke 1 , die die Stärke, Funktionalität und die Effizienz des Formprozesses selbst beeinflusst. Die Wandstärke beeinflusst die Zykluszeiten, die Materialkosten und das Risiko von Defekten wie Spülenspuren oder Verzerrungen. Aber was ist die maximale Wandstärke 2 für Injektionsform 3 ? Die Antwort ist nicht festgelegt - sie variiert je nach Material, Design und Anwendung, die normalerweise zwischen 3 mm und 25 mm reichen, mit einer allgemeinen Richtlinie von rund 5 mm, um Probleme zu minimieren.
Die maximale Wandstärke für die Injektionsformung hängt von den Materialeigenschaften und dem Teildesign ab, der typischerweise zwischen 3 mm und 25 mm liegt. Die meisten Richtlinien empfehlen jedoch, unter 5 mm zu bleiben, um Mängel zu vermeiden.
In diesem Artikel werden diese Grenzen, materiellen Empfehlungen und praktische Überlegungen für dickwandige Teile untersucht.
Die maximale Wandstärke für Injektionsformungen beträgt immer 5 mm.FALSCH
Während 5 mm eine häufige Richtlinie ist, können Materialien wie Polycarbonat bis zu 9,35 mm und langfaserverstärkte Kunststoffe 25,4 mm erreichen.
Dickwandige Teile sind ohne Mängel unmöglich zu formen.FALSCH
Mit der richtigen Konstruktions- und Prozesskontrolle können dickwandige Teile erfolgreich geformt werden, obwohl sie sorgfältig aufmerksam werden müssen.
- 1. Warum ist die Wandstärke bei Injektionsformungen von Bedeutung?
- 2. Was sind die allgemeinen Richtlinien für die maximale Wandstärke?
- 3. Wie wirkt sich die Materialauswahl auf die maximale Wandstärke aus?
- 4. Welche Herausforderungen sind mit dickwandigen Teilen ausgestattet?
- 5. Wann werden dickwandige Teile benötigt?
- 6. Wie entwerfe ich dickwandige Injektionsgeformteile?
- 7. Gibt es Alternativen zu dickwandigem Injektionsformen?
- 8. Abschluss
Warum ist die Wandstärke bei Injektionsformungen von Bedeutung?
Die Wandstärke ist aus mehreren Gründen ein Eckpfeiler des Injektionsformgestalts:
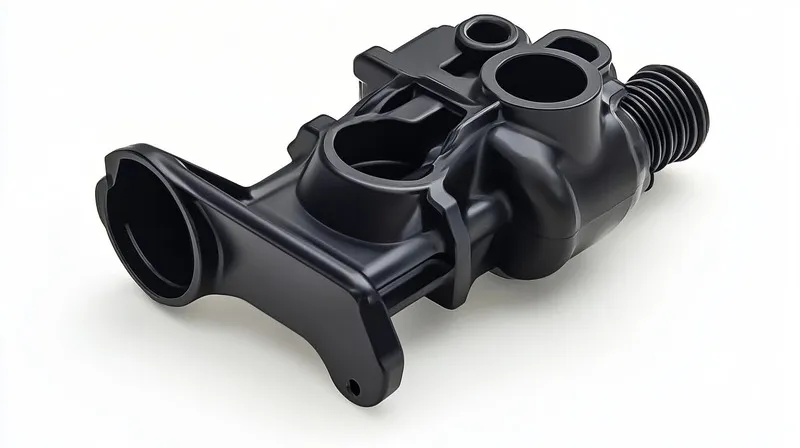
-
Kühlungseffizienz 4 : Dickere Wände dauern länger, um die Produktion zu kühlen, die Produktion zu verlangsamen und die Kosten zu erhöhen.
-
Defektrisiko 5 : Dicke oder ungleiche Wände können aufgrund der ungleichmäßigen Kühlung zu Speeksnoten, Verziehen oder Hohlräumen führen.
-
Materialverbrauch : Dickere Wände verbrauchen mehr Material, zunehmend Gewicht und Kosten.
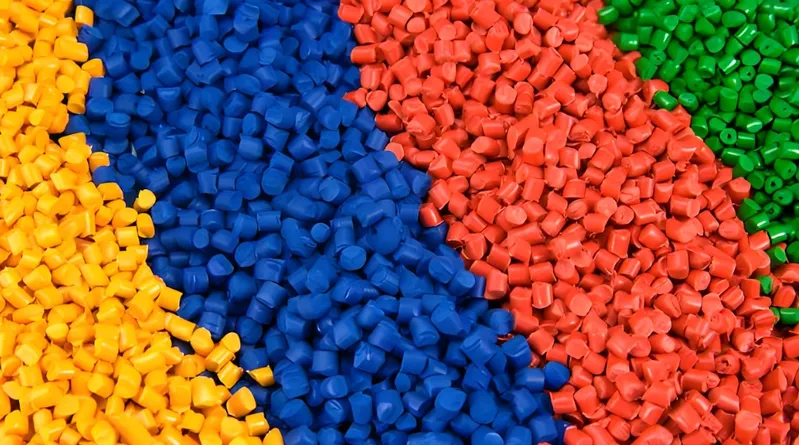
- Teilleistung 6 : Während dickere Wände die Festigkeit verbessern können, kann das Übertreiben von IT -Ressourcen oder Schwachstellen erzeugen, wenn sie nicht gut gestaltet sind.
Designer streben in der Regel die dünnsten Wände an, die den funktionalen Anforderungen entsprechen, aber einige Anwendungen - wie strukturelle oder isolierte Teile - erhöhen dickere Wände, und drücken die Grenzen dessen, was das Injektionsleisten erreichen kann.
Was sind die allgemeinen Richtlinien für die maximale Wandstärke?
Es gibt keine universelle maximale Wanddicke für die Injektionsformung - es variiert basierend auf Materialien, Teilgeometrie und Formbedingungen. Branchenstandards bieten jedoch einen Ausgangspunkt:

-
Typischer Bereich : 3 mm bis 5 mm für die meisten Thermoplastik 7 , um effiziente Form- und fehlerfreie Teile zu gewährleisten.
-
Obergrenzen : Bis zu 25,4 mm für spezielle Materialien wie langfaserverstärkte Kunststoffe, obwohl dies fortschrittliche Techniken erfordert.
5 mm zu halten, um häufige Fallstricke wie Verzerrungen oder anhaltende Zykluszeiten zu vermeiden. Über 6 mm stellt häufig Herausforderungen ein, die eine sorgfältige Prozessoptimierung erfordern.
Wie wirkt sich die Materialauswahl auf die maximale Wandstärke aus?
Das Material, das Sie wählen, beeinflusst wesentlich, wie dick Ihre Wände sein können. Hier ist der Grund:

-
Wärmeeigenschaften 8 : Materialien, die Wärme gut abkühlen lassen und dickere Wände stützen.
-
Schrumpfung : Niedrige Materialien reduzieren das Defektrisiko in dicken Abschnitten.
-
Fließfähigkeit 9 : Hochwassermaterial füllen dicke Abschnitte besser und vermeiden unvollständige Formteile.
Hier ist eine Tabelle mit maximalen Wandstärken für gemeinsame Injektionsformmaterialien, die auf allgemeinen Richtlinien basieren:
Materialname | Maximale Wandstärke (mm) |
---|---|
ABS | 3.18 – 3.56 |
Polypropylen (PP) | 4.53 |
Polycarbonat (PC) | 3.81 – 9.35 |
Nylon (PA) | 3.18 |
Polystyrol (PS) | 6.35 |
Polyethylen (HDPE/LDPE) | 5.08 – 6.35 |
Langfaser verstärkte Kunststoffe10 | 25.4 |
Hinweis : Dies sind ungefähre Bereiche. Spezifische Designs oder Prozessveränderungen können diese Grenzen höher oder niedriger erhöhen.
Zum Beispiel Polycarbonat dank seiner Festigkeits- und Durchflusseigenschaften bis zu 9,35 mm verarbeiten, während langfaserverstärkte Kunststoffe aufgrund ihrer verbesserten Stabilität 25,4 mm erreichen können-ideal für schwere Anwendungen.
Alle Materialien haben die gleiche maximale Wandstärke.FALSCH
Materialeigenschaften wie Schrumpfung und Fließfähigkeit führen zu einer maximalen Wandstärke, die sich über Kunststoffe stark variieren.
Welche Herausforderungen sind mit dickwandigen Teilen ausgestattet?
Dicke Wände bringen einzigartige Herausforderungen für die Injektionsformung: Formen:
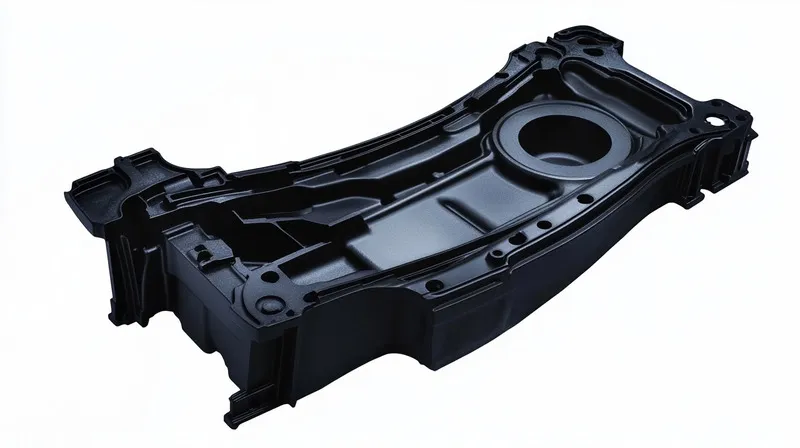
-
Verlängerte Kühlzeiten 11 : Dickere Abschnitte halten länger Wärme und verlangsamen die Produktion.
-
Defektrisiken 12 : Unebenes Abkühlen kann zu Waschbecken, Verzerrungen oder inneren Hohlräumen führen.
-
Höhere Kosten : Mehr Material und längere Zyklen erhöhen die Kosten.
-
Füllungsprobleme : Dicke Abschnitte dürfen ohne Druck oder Material nicht vollständig gefüllt werden.
Trotz dieser Hürden gibt es Lösungen:
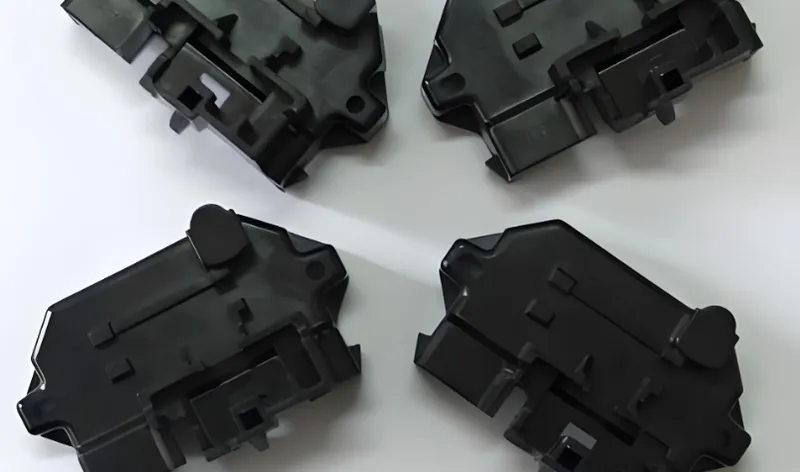
-
Gleichmäßige Dicke : Kühlung bleibt konsistent.
-
Rippen oder Zwickel : Steigert die Festigkeit, ohne Masse hinzuzufügen.
-
Erweiterte Kühlung 13 : Optimierte Formkanäle reduzieren die Zykluszeiten.
Dickwandige Teile erhöhen immer die Produktionskosten.WAHR
Mehr materielle und längere Kühlzeiten erhöhen zwangsläufig die Kosten, obwohl intelligentes Design dies mildern kann.
Wann werden dickwandige Teile benötigt?
Dicke Wände sind in bestimmten Szenarien gerechtfertigt:
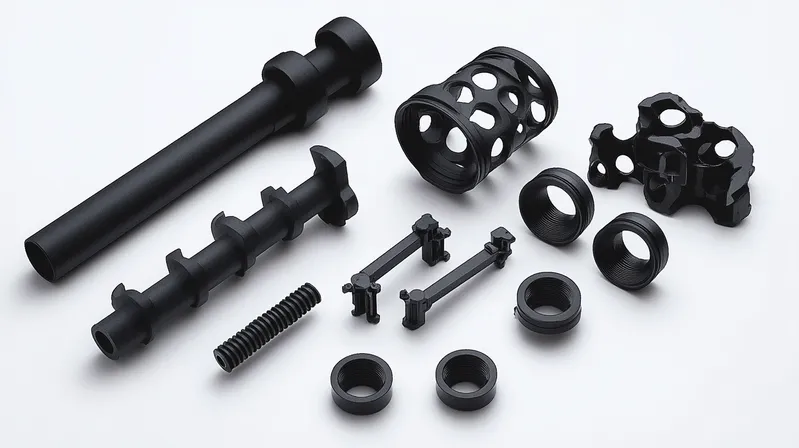
-
Strukturfestigkeit : Automobilteile wie Dashboards oder Türplatten benötigen Starrheit.
-
Isolierung : Dicke Wände verbessern die thermische oder akustische Isolierung wie in den Konstruktionskomponenten.
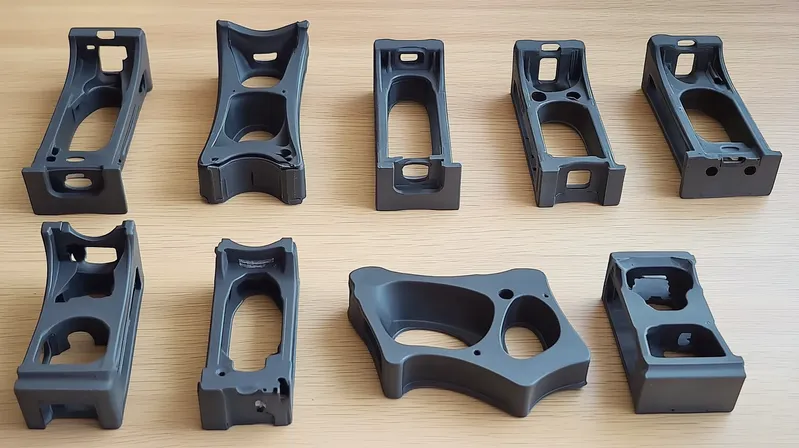
- Haltbarkeit : Schutzhülsen oder Hochleistungsteile profitieren von einer zusätzlichen Dicke.
In der Automobilindustrie ersetzen dickwandige Teile beispielsweise Metallkomponenten, wobei das Gewicht abschneidet und gleichzeitig die Festigkeit aufrechterhält. In der Konstruktion werden sie für Schallschutz oder Isolierung verwendet.
Wie entwerfe ich dickwandige Injektionsgeformteile?
Wenn dicke Wände erforderlich sind, folgen Sie folgenden Tipps:
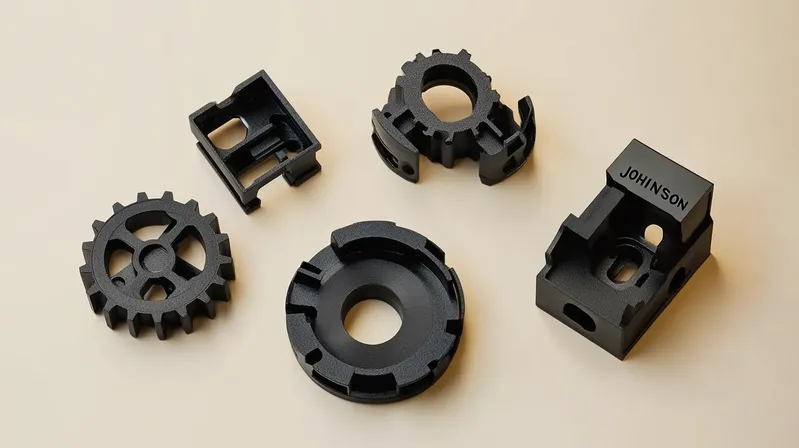
-
Wählen Sie mit Bedacht : Entscheiden Sie sich für Materialien wie Polycarbonat oder verstärkte Kunststoffe, die für dickere Abschnitte geeignet sind.
-
Glätte Übergänge : Vermeiden Sie Änderungen der starken Dicke, um Spannung oder Kühlprobleme zu vermeiden.
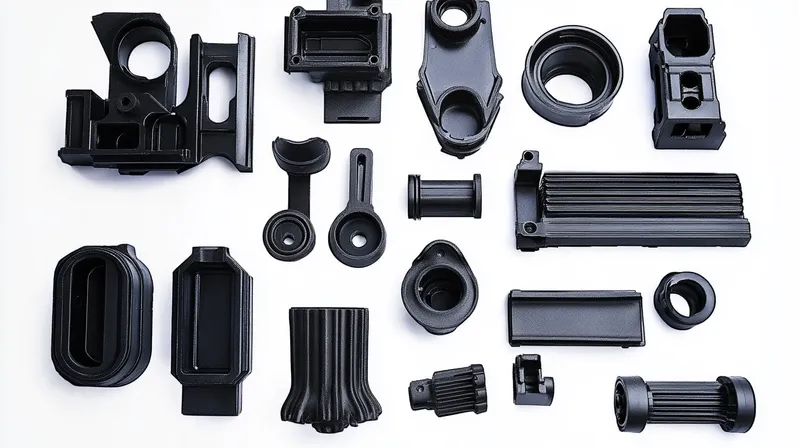
-
Verbesserung von Formen : Verwenden Sie effiziente Kühlkanäle oder konforme Kühlung für eine gleichmäßige Wärmeableitung.
-
Simulieren Sie zuerst : Formflussanalyse kann Probleme vor der Produktion erkennen.
-
Zusammenarbeit : Arbeiten Sie mit erfahrenen Summs zusammen, um Parameter mit Feinabstimmung zu erhalten.
Teile dickwandige Teile erfordern keine speziellen Konstruktionsüberlegungen.FALSCH
Sie fordern bestimmte materielle Auswahlmöglichkeiten, Schimmelpilzdesigns und Prozessanpassungen, um erfolgreich zu sein.
Gibt es Alternativen zu dickwandigem Injektionsformen?
Manchmal passen andere Prozesse dicke Teile besser:
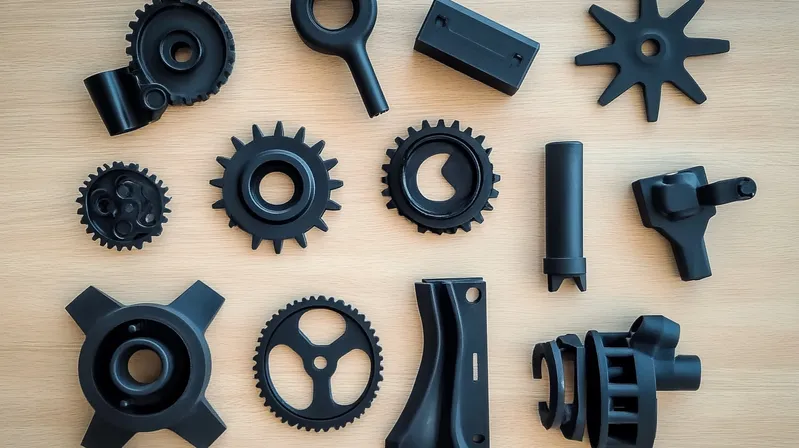
-
Rotationsformung : Ideal für große, hohle, dickwandige Gegenstände wie Tanks.
-
Kompressionsformen : eignet sich gut für Thermosets mit dicken Abschnitten.
-
Casting : Bietet Flexibilität für dicke Wände, aber es fehlen die Präzision von Injection Moulding.
Dennoch zeichnet sich in Injektionsformungen dank seiner Geschwindigkeit und Vielseitigkeit aus, auch mit dickeren Wänden mit hohem Volumen, komplexe Teile, selbst bei dickeren Wänden.
Abschluss
Die maximale Wandstärke für die Injektionsformung ist keine einzige Zahl - sie reicht je nach Material und Konstruktion zwischen 3 mm und 25 mm. Während 5 mm eine praktische Richtlinie für die meisten Anwendungen darstellt, können fortschrittliche Materialien und Techniken diese Grenze höher vorantreiben. Designer müssen die Vorteile dickerer Wände (wie Kraft oder Isolierung) gegen Herausforderungen wie Defekte und Kosten abwägen. Durch die Auswahl des richtigen Materials, die Optimierung von Designs und die Partnerschaft mit qualifizierten Molzen können dickwandige Teile effektiv erzeugt werden.
-
Das Verständnis der Wanddicke ist entscheidend für die Optimierung des Injektionsformprozesses und der Gewährleistung der Produktqualität. Entdecken Sie diesen Link für eingehende Einblicke. ↩
-
Entdecken Sie die Faktoren, die die maximale Wandstärke bei Injektionsformungen beeinflussen, um Ihre Design- und Herstellungsprozesse zu verbessern. ↩
-
Erfahren Sie mehr über die kritischen Faktoren bei der Injektionsformung, um die Effizienz und die Produktqualität zu verbessern. Diese Ressource liefert wertvolle Informationen. ↩
-
Das Verständnis der Kühlungseffizienz ist von entscheidender Bedeutung, um die Produktionsgeschwindigkeit zu optimieren und die Kosten bei Injektionsformprozessen zu senken. ↩
-
Durch die Erforschung von Möglichkeiten zur Minimierung des Mangelrisikos kann zu Produkten von höherer Qualität und zu verringernden Abfällen in der Herstellung führen. ↩
-
Das Erlernen von Faktoren, die die Teilleistung beeinflussen, kann dazu beitragen, stärkere und effizientere geformte Teile zu entwerfen. ↩
-
Das Erlernen von Thermoplastik kann Einblicke in die Materialauswahl geben und Ihre Produktqualität verbessern. ↩
-
Das Verständnis der thermischen Eigenschaften ist entscheidend für die Optimierung der Wandstärke beim Injektionsform, wodurch eine bessere Leistung und Effizienz gewährleistet ist. ↩
-
Durch die Erforschung der Fließfähigkeit können Sie erfassen, wie sich das Materialverhalten auf die Form der Form von Form und Wanddicke auswirkt, was zu überlegenen Designs führt. ↩
-
Entdecken Sie die Vorteile von langfaserverstärkten Kunststoffen, insbesondere ihre Fähigkeit, dickere Wände für robuste Anwendungen zu unterstützen. ↩
-
Das Verständnis erweiterter Kühlzeiten kann dazu beitragen, die Produktionseffizienz zu optimieren und die Kosten bei Injektionsformprozessen zu senken. ↩
-
Das Erforschen von Defektrisiken kann Einblicke in die Verbesserung der Produktqualität und zur Reduzierung von Abfällen in der Herstellung liefern. ↩
-
Das Erlernen von fortschrittlichen Kühltechniken kann Ihr Wissen über effiziente Injektionsformpraktiken verbessern und die Zykluszeiten reduzieren. ↩