- 1. I. grundlegend kognitive Ebene: Konzepterrahmen festlegen
- 2. Ii. Anwendungsanalysestufe: Lösen von Problemen mit Benutzerentscheidungsproblemen
- 3. III. Technische Deep -Tauchstufe: Erfüllung des professionellen Leserbedarfs
- 4. Iv. Praktische Tools Level: Verbesserung der Betriebsfähigkeit von Inhalten
- 5. V. Erweiterungsstufe: Erstellen eines Wissensnetzwerks
- 6. Schlussfolgerung: Mastering der Kühlzeit mit Zetarmold
I. grundlegend kognitive Ebene: Konzepterrahmen festlegen
Bevor wir optimieren, müssen wir verstehen.
Klare Definitionen
- Injektionsformkühlzeit:
- Voller technischer Name: Kühlphasendauer im Injektionsformzyklus.
- Häufige Aliase: Kühlzeit 1 , Verfestigungszeit 2 , Heilzeit (seltener für Thermoplastik, mehr für Thermosets/Silikon).
- Kernprinzip: Die Kühlzeit ist die Periode innerhalb des Injektionsformzyklus, beginnend nach der Form des Formhohlraums gefüllt und mit geschmolzenem Kunststoff gepackt, in dem das Kunststoffmaterial bis zu einem Punkt verfestigt wird, an dem es starr genug ist, um ohne Verformung oder Beschädigung aus der Form ausgestoßen zu werden. Dies erfolgt durch Wärmeübertragung vom geschmolzenen Kunststoff auf die kühlere Form.
- Signifikanz: Es ist typischerweise den größten Teil (häufig 50-80%) der gesamten Injektionsformzykluszeit.
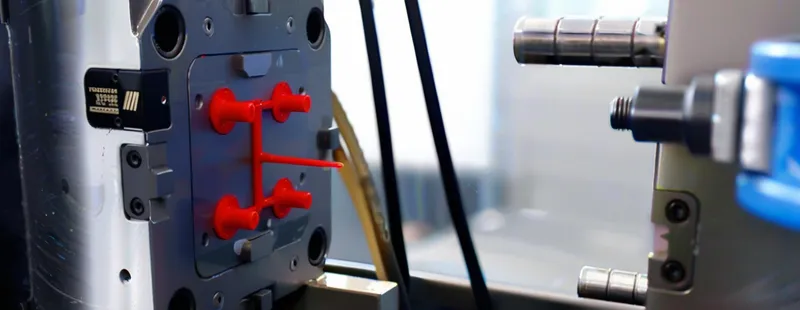
- Injektionsformzyklus3: Die vollständige Folge von Ereignissen zur Herstellung eines Teils (oder Teilesatzes) umfasst:
- Formenschließen
- Injektion (Füllung)
- Verpackung (Holding)
- Kühlung
- Formenöffnung
- Auswurf
Klassifizierung (Faktoren, die die Kühlzeit beeinflussen)
Kühlzeit ist kein fester Wert. Es wird von einem Zusammenfluss von Faktoren beeinflusst, die weitgehend klassifiziert werden können:
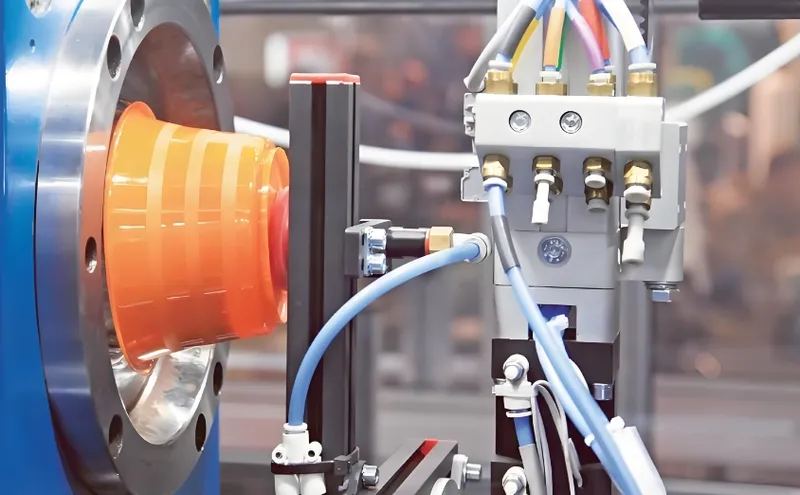
-
Materiell zentriert:
- Art des Polymers 4 : amorph (z. B. PC, PS) gegen halbkristalline (z. B. PP, PA, POM). Halbkristalline Materialien erfordern aufgrund der latenten Schrumpfung der Fusion und Kristallisation häufig eine genauere Kühlung.
- Wärme Eigenschaften: Wärmeleitfähigkeit, spezifische Wärmekapazität, thermische Diffusivität und Glasübergangstemperatur (TG) oder Schmelztemperatur (TM) des Polymers.
- Ausstoßtemperatur: Die maximale Temperatur, bei der das Teil ohne Probleme wie Verzerrungen oder Kleben ausgeworfen werden kann.
-
Teildesign-zentriert:
- Wandstärke: Der dominanteste Faktor. Die Kühlzeit ist ungefähr proportional zum Quadrat des dicksten Wandabschnitts.
- Teilgeometrie: Komplexe Geometrien, Rippen, Bosse und ungleichmäßige Wandstärken können heiße Flecken und differentielle Kühlung erzeugen.
-
Schimmeldesign-zentriert:
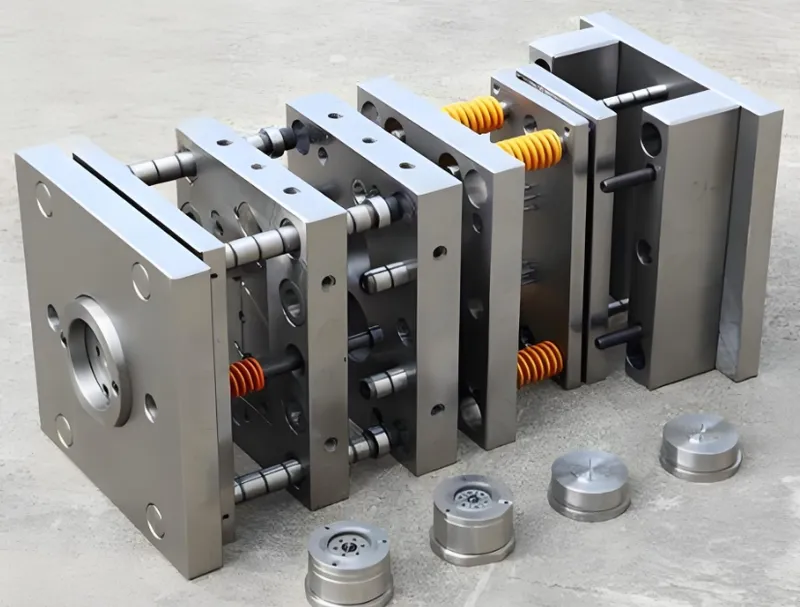
- Kühlkanal Design 5 : Layout, Durchmesser, Nähe zum Hohlraum und Typ (z. B. herkömmliche Bohrleitungen, konforme Kühlkanäle).
- Schimmelpilzmaterial: höhere Wärmeleitfähigkeitsformmaterialien (z. B. Beryllium Kupfereinsätze gegen P20 -Stahl) können die Kühlzeit verkürzen.
- Entlüftung: Die ordnungsgemäße Entlüftung ermöglicht die Entweichen der gefangenen Luft und verhindert Isolierungseffekte, die die Kühlung verlängern können.
- Prozessparameter-zentriert:
- Schmelztemperatur 6 : höhere Schmelztemperatur bedeutet mehr Wärme zum Entfernen.
- Schimmelpilztemperatur: Niedrigere Schimmelpilztemperatur bedeutet im Allgemeinen eine schnellere Kühlung, kann jedoch die Oberflächenbeschaffung, Spannungen und Füllen beeinflussen.
- Kühlmitteltemperatur und Durchflussrate: Kälter Kühlmittel und höhere Durchflussraten erhöhen die Wärmeentfernungseffizienz.
Ii. Anwendungsanalysestufe: Lösen von Problemen mit Benutzerentscheidungsproblemen
Das Verständnis der Kühlzeit hilft dabei, fundierte Entscheidungen für verschiedene Anwendungen zu treffen.
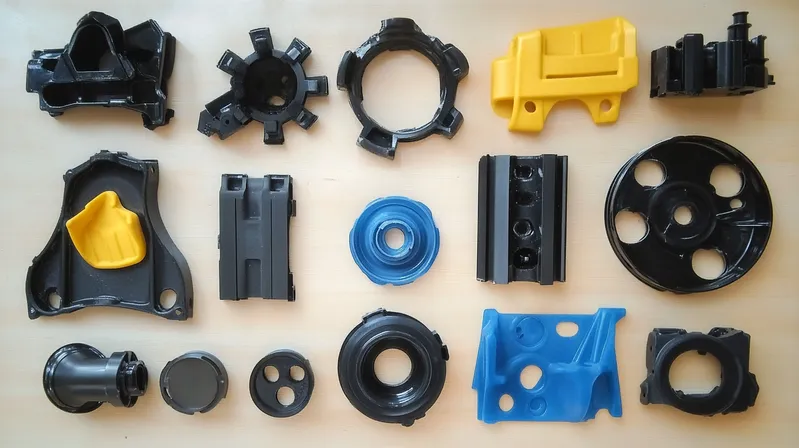
Typische Anwendungsszenarien
- Hochvolumige, dünnwandige Verpackung (z. B. Lebensmittelbehälter, Kappen-oft PP, PE):
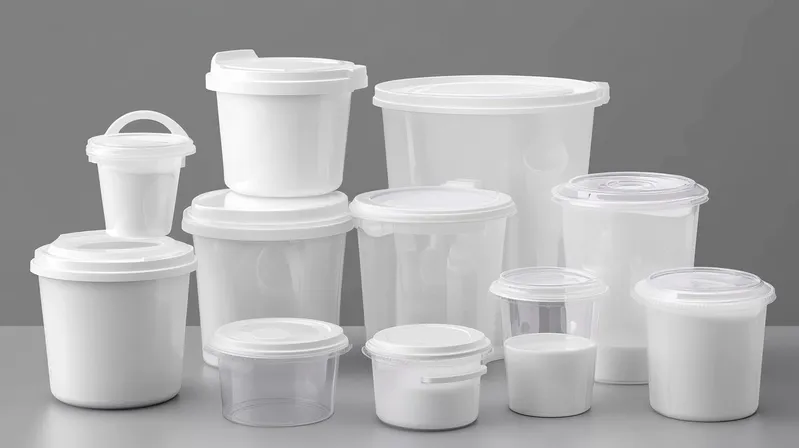
- Vorschlag: Die Kühlzeit ist für die Zykluszeit von größter Bedeutung. Optimieren Sie für die schnelle Kühlung mit hochleitenden Schimmelpilzmaterialien, effizientem Kühlkanal -Design und möglicherweise niedrigeren (aber kontrollierten) Schimmelpilztemperaturen. Die Materialauswahl begünstigt schnelles Zykliernoten.
- Medizinprodukte (z. B. Spritzen, diagnostische Komponenten - häufig PC, Peek, CoC):
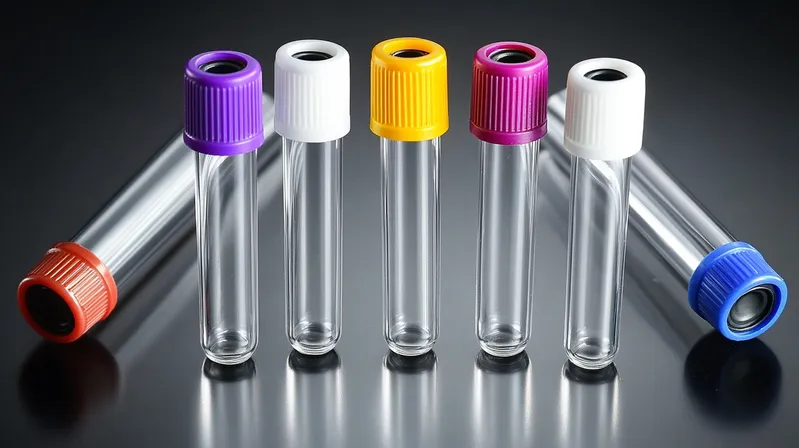
- Vorschlag: Präzision und materielle Integrität sind der Schlüssel. Die Kühlung muss gleichmäßig sein, um die inneren Belastungen zu minimieren und eine dimensionale Genauigkeit zu gewährleisten. Eine längere, kontrollierte Kühlung kann akzeptabel sein, um kritische Toleranzen zu erreichen.
- Unterhaltungselektronikgehäuse (z. B. Telefonkoffer, Fernbedienungen - häufig ABS, PC):
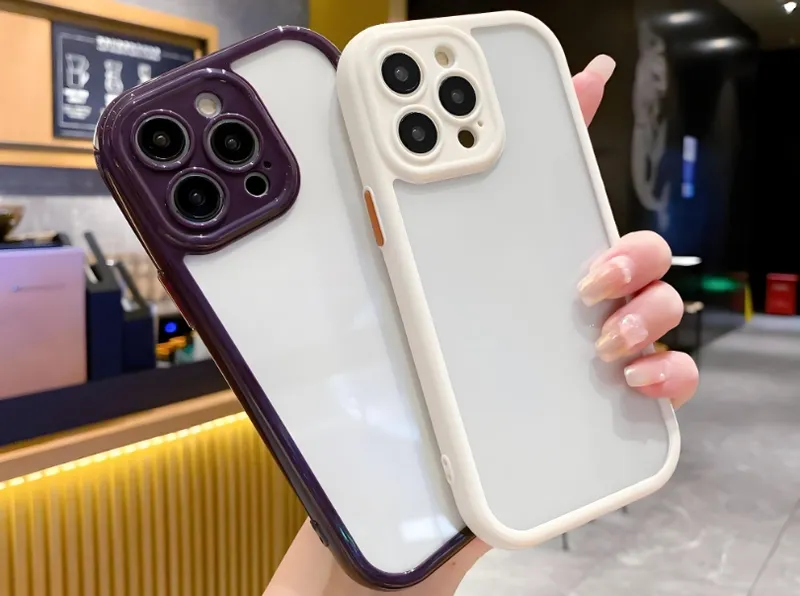
- Vorschlag: Ästhetik (Oberflächenbeschaffung) und strukturelle Integrität sind wichtig. Kühlung muss gelungen werden, um Spülenspuren zu vermeiden und eine gute Passform und das Gefühl zu gewährleisten. Das optimierte Kühlkanal -Design ist entscheidend.
- Silikongummiprodukte (LSR -Formteil):
- Vorschlag: Während Zetarmold auch Silikon behandelt, ist seine "Kühlung" tatsächlich "Härte" durch Hitze. Die Form ist heiß und das "Kühlung" -äquivalent ist die Zeit, die für die Vernetzung der Vernetzung benötigt wird. Die Prinzipien der Wärmeübertragung und der Gleichmäßigkeit gelten weiterhin, aber das Ziel ist es, Wärme für das Heiltieren aufrechtzuerhalten, anstatt ihn zur Erstarrung zu entfernen.
Vor- und Nachteilevergleich (Auswirkungen der Kühlzeitdauer)
Besonderheit | Kürzere Kühlzeit | Längere Kühlzeit |
---|---|---|
Vorteile | - verkürzte Zykluszeit | - bessere dimensionale Stabilität |
- Erhöhte Produktivität | - Verbesserte Teilqualität (weniger Waschbeckenmarken, weniger Verwerfungen) | |
-niedrigere Kosten pro Teil | - Reduzierte innere Belastungen | |
Nachteile | - Risiko für Mängel (Vererdigung, Waschbecken, kurze Schüsse) | - Erhöhte Zykluszeit |
- Potential für Teile, die beim Auswurf kleben oder verformten | - niedrigere Produktivität | |
- höhere innere Spannungen, wenn sie zu schnell/ungleichmäßig abgekühlt sind | -höhere Kosten pro Teil | |
- Möglicherweise erfordern ein robusteres Auswurfsystem | -Mögliche Überpackungsprobleme, wenn der Druck des Haltens zu lange bis zur Abkühlung aufrechterhalten wird |
III. Technische Deep -Tauchstufe: Erfüllung des professionellen Leserbedarfs
Lassen Sie uns in das Nitty-Greaty einsteigen.
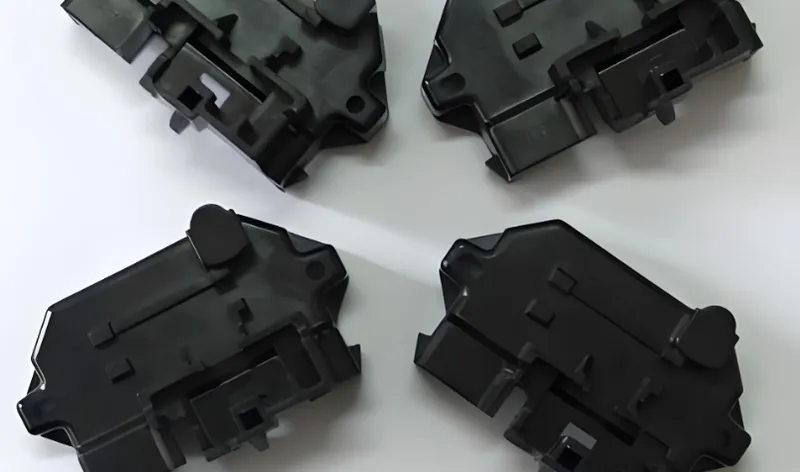
Verarbeiten Sie den vollständigen Workflow -Zusammenbruch (Fokus auf das Abkühlen)
-
Schimmelpass und Klemme: Die beiden Hälften der Form sind sicher geschlossen und geklemmt.
-
Injektion: geschmolzene Kunststoff wird unter hohem Druck in die Formhöhle injiziert.
-
Verpackung/Halten: Nachdem der Hohlraum größtenteils gefüllt ist, wird zusätzliches Material unter Druck gepackt, um das Schrumpfung zu kompensieren, wenn das Material in der Nähe der Formwände abkühlt und verfestigt.
- Schlüsselparameter: Packdruck, Packungszeit.
-
Kühlphase:
- Wärmeübertragung: Dies ist der Kern der Kühlung. Die Wärme aus dem geschmolzenen Kunststoff (bei Schmelztemperatur) wird hauptsächlich durch Leitung auf den Kühlerschimmelstahl übertragen und dann vom Kühlmittel (normalerweise Wasser) weggetragen, der durch die Kühlkanäle der Form zirkuliert.
- Verfestigung von Front: Die Verfestigung beginnt an den Schimmelpilzwänden und führt nach innen in Richtung der Mitte des Teils.
- Schrumpfung Kompensation 7 : Anfänglich wird vom Packdruck fortgesetzt, dann tritt eine volumetrische Schrumpfung auf, wenn sich das Massenmaterial weiter abkühlt.
- Dauer Determinanten: Ausschläge des Materialiens, thermische Eigenschaften, dickster Abschnitt des Teils, Schimmelpilztemperatur und Effizienz des Kühlsystems.
- Schlüsselparameter: Schimmelpilztemperatur, Kühlmitteltemperatur, Kühlmittelflussrate, gewünschte Teilwiederungstemperatur.
-
Schimmelpilzöffnung: Sobald die Kühlzeit abgelaufen ist und der Teil ausreichend starr ist, öffnet die Klemme die Form.
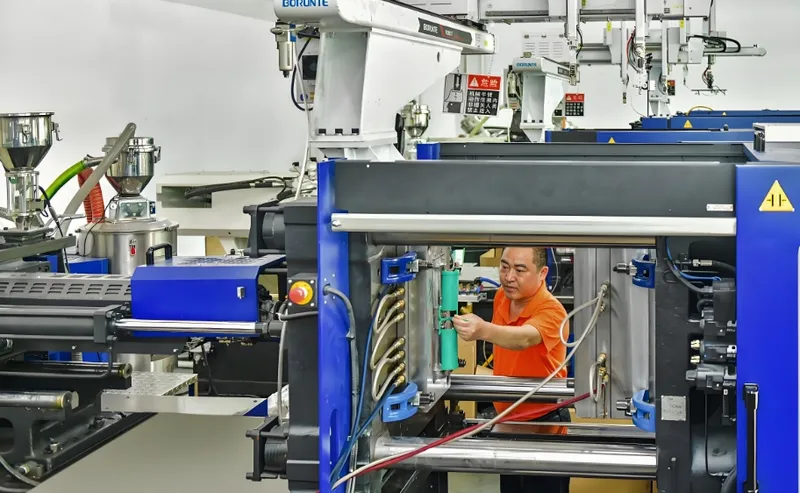
- Ausstoß: Der verfestigte Teil wird durch ein Ejektorsystem (Stifte, Ärmel, Platten) aus der Formhöhle gedrückt.
Schlüsselkühlungsparameter zur Überwachung und Steuerung:
-
Formoberflächentemperatur 8 : Kritisch für die Steuerung der Wärmeextraktion und zur Beeinflussung der Oberflächenfinish und -kristallisation (für halbkristalline Polymere).
-
Kühlmitteleinlass-/Auslasstemperaturdifferenz (Delta T): Zeigt die Entfernung der Wärme an. Ein sehr kleines Delta -T könnte einen unzureichenden Fluss oder einen schlechten thermischen Kontakt hindeuten.
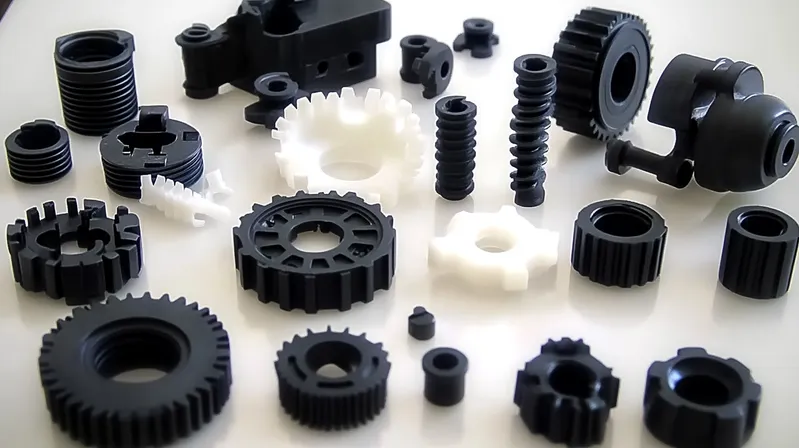
-
Kühlmittelflussrate 9 : Der turbulente Strömung wird im Allgemeinen für eine effiziente Wärmeübertragung bevorzugt.
-
Schmelztemperatur: Legt die anfängliche Wärmebelastung fest.
Materialkompatibilität Erklärung
Die thermischen Eigenschaften des Kunststoffmaterials sind für sein Kühlverhalten von grundlegender Bedeutung:
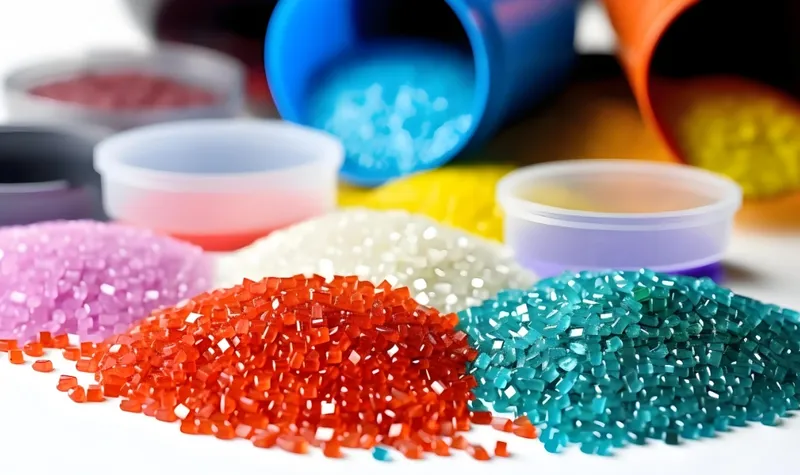
-
Amorphe Polymere (z. B. Polystyrol (PS), Polycarbonat (PC), ABS):
- Kein scharfer Schmelzpunkt; Sie erweichen über einen Temperaturbereich.
- Im Allgemeinen niedrigere Schrumpfung als halbkristalline.
- Bei Kühlung geht es darum, das Material unter seine Glasübergangstemperatur (TG) zu bringen, um Starrheit zu erreichen.
- Kann anfälliger für interne Belastungen sein, wenn es zu schnell abgekühlt ist.
-
Halbkristalline Polymere (EG, Polypropylen (PP), Polyethylen (PE), Nylon (PA), PET, PBT):
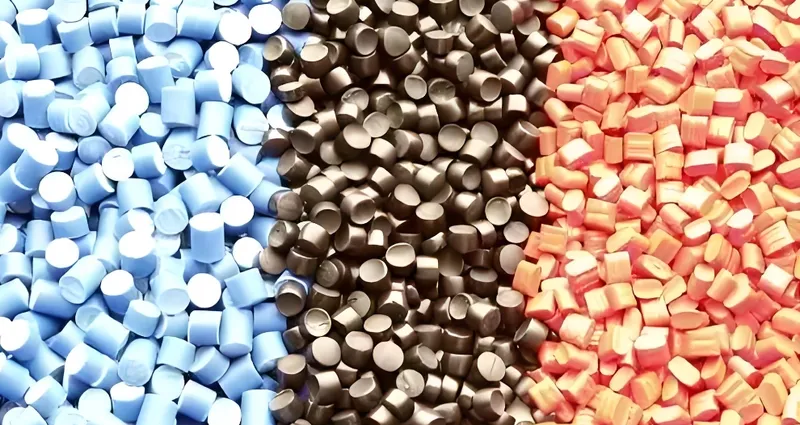
- Scharfer Schmelzpunkt (TM).
- Höhere Schrumpfung aufgrund der Bildung geordneter kristalliner Strukturen; Dieser Vorgang setzt auch latente Fusionswärme frei, die entfernt werden muss.
- Die Kühlrate kann den Grad der Kristallinität beeinflussen und die mechanischen Eigenschaften beeinflussen. Schnelle Kühlung kann zu kleineren Sphäeliten und manchmal verbesserten Zähigkeit, aber möglicherweise mehr Verzerrungen führen.
- Erfordern Sie eine sorgfältige Kühlkontrolle für die Verwaltung von Verwerfungen und dimensionalen Stabilität.
- Flüssiges Silikonkautschuk (LSR - zum Vergleich):
- Thermosets. Die Form ist erhitzt (typischerweise 170-210 ° C).
- "Kühlzeit" ist tatsächlich "Aushärtzeit", wo das Material zusammenbricht. Der Teil wird heiß ausgeworfen. Die Wärmeübertragung ist immer noch der Schlüssel, aber für die gleichmäßige Aufrechterhaltung der Aushärttemperatur.
Iv. Praktische Tools Level: Verbesserung der Betriebsfähigkeit von Inhalten
Umsetzbare Erkenntnisse für Ihre Projekte.
Design -Checkliste (Erinnerungen an Prozessbeschränkungen für das Abkühlen)
Betrachten Sie beim Entwerfen von Teilen für die Injektionsformung diese, um die Kühlung zu optimieren:
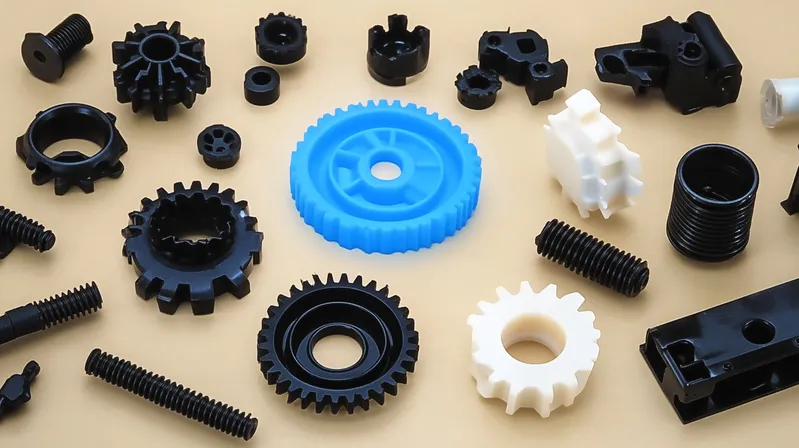
-
Gleichmäßige Wandstärke: Ziel auf eine konsistente Wandstärke während des gesamten Teils. Dies ist die #1 -Regel für die überschaubare Kühlung.
-
Vermeiden Sie dicke Abschnitte: Wenn Sie unvermeidlich sind, zahlen Sie sie aus oder verwenden Sie Funktionen wie Gasassistent.
-
Großzügige Radien: Verwenden Sie Radien anstelle von Radien anstelle von scharfen Kanten, um Spannungskonzentrationen zu verhindern und den Durchfluss/die Abkühlung zu verbessern.
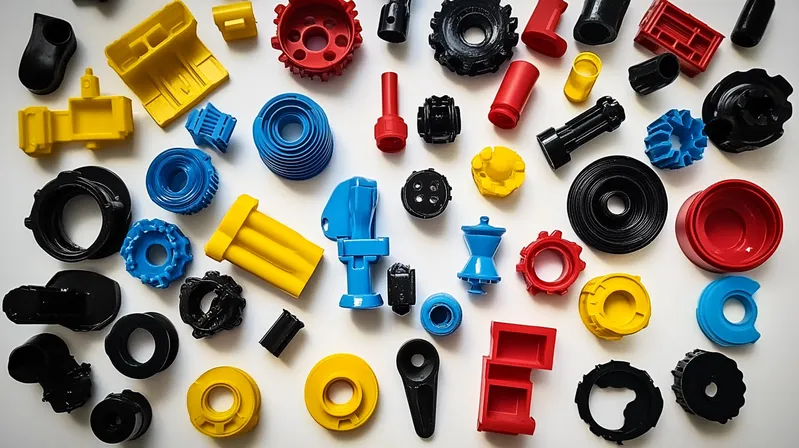
-
Allmähliche Übergänge: Wenn Änderungen der Dicke erforderlich sind, machen Sie sie allmählich.
-
Rippen/Bosse Design: Die Rippendicke sollte ~ 50-70% der Nominalwand sein, um Spülenspuren zu verhindern. Chefs sollten koriert werden.
-
Materialauswahl: Betrachten Sie Materialien mit einer besseren thermischen Leitfähigkeit oder niedrigeren Verarbeitungstemperaturen, wenn die Zykluszeit kritisch ist.
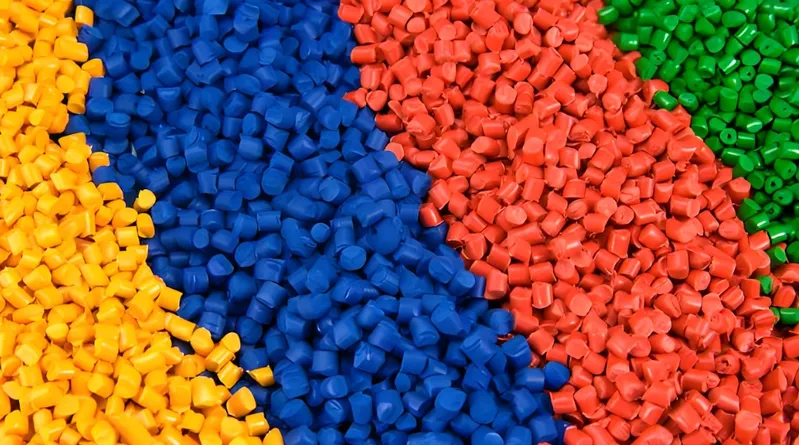
-
GATE -Standort: Platzieren Sie Tore, um zuerst dicke Abschnitte zu füllen oder die Temperaturschwankungen zu minimieren.
-
Betrachten Sie die Machbarkeit der Formkühlung: Ist das Teil -Design so komplex, dass effektive Kühlkanäle nicht konventionell umgesetzt werden können? (Dies könnte zur konformen Kühlung drängen).
Entscheidungsfindung der Prozessauswahl (Optimierung der Kühlzeit)
Hier ist ein grundlegender Gedankenprozess zur Optimierung der Kühlzeit:
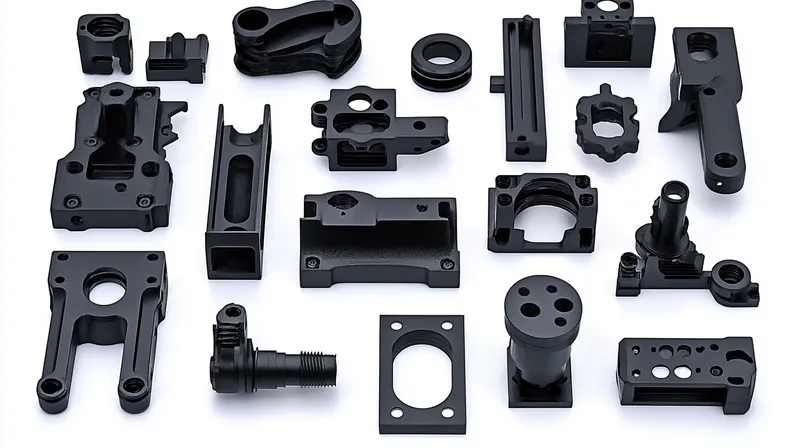
-
Ist die aktuelle Kühlzeit übermäßig und führt zu hohen Kosten oder einer niedrigen Leistung?
- Ja: Gehen Sie mit der Analyse fort.
- NEIN: Ist die Teilqualität (Verzögerungen, Waschbecken, Abmessungen) ein Problem?
- Ja: Das Abkühlen kann zu kurz oder ungleichmäßig sein. Fortfahren, um zu analysieren.
- Nein: Die Stromkühlung ist wahrscheinlich angemessen. Regelmäßig überwachen.
-
Teilentwurf analysieren:
- Ist die Wandstärke ungleichmäßig? Aktion: Beraten Sie den Kunden auf DFM für einheitliche Wände.
- Gibt es vermeidbare dicke Abschnitte? Aktion: Raten Sie das Coring.
-
Material analysieren:
- Ist das Material für das Zykluszeitziel geeignet? Aktion: Erforschen Sie alternative Noten oder Materialien, falls möglich.
- Beachten Sie die empfohlene Ausschläge des Materials und die thermischen Eigenschaften des Materials.
-
Analysieren Sie das Schimmeldesign und -zustand:
- Sind Kühlkanäle angemessen (Größe, Anzahl, Platzierung)? Aktion: Verwenden Sie die Formflusssimulation. Betrachten Sie die konforme Kühlung für komplexe Teile oder kritische Anwendungen.
- Sind Kanäle klar und frei von Skalen? Aktion: Implementieren Sie regelmäßige Schimmelpilzwartung.
- Ist das Formmaterial für Wärmeübertragungsanforderungen geeignet? Aktion: Betrachten Sie Einsätze mit höherem Leitfähigkeitsmaterial in Hotspot -Bereichen.
-
Prozessparameter analysieren:
- Ist die Schmelztemperatur höher als nötig? Aktion: Allmählich reduzieren, Überwachungsfüllung.
- Ist die Schimmelpilztemperatur optimal eingestellt? (Zu niedrig kann andere Probleme verursachen). Aktion: Experimentieren Sie im empfohlenen Bereich des materiellen Lieferanten.
- Ist Kühlmittelflussrate und Temperatur optimiert? Aktion: Turbulenten Fluss sicherstellen; Verwenden Sie gegebenenfalls gekühltes Wasser und kostengünstig.
Entscheidungsbaumabschnitt:
-
Wenn ein Teil dicke Abschnitte aufweist und die Kühlung lang ist, sollten Sie Gasassistenten korrigieren oder verwenden.
-
Wenn ein Teil das Versehen und die Kühlung kurz sind, erhöhen Sie die Kühlzeit oder verbessern Sie die Kühlungsgleichheit (z. B. konforme Kühlung).
-
Wenn die Zykluszeit kritisch ist und die Teilqualität die Optionen ermöglicht, um die Kühlung (optimierte Form, Parameter) vorsichtig zu reduzieren.
V. Erweiterungsstufe: Erstellen eines Wissensnetzwerks
Kühlzeit existiert nicht im Vakuum.
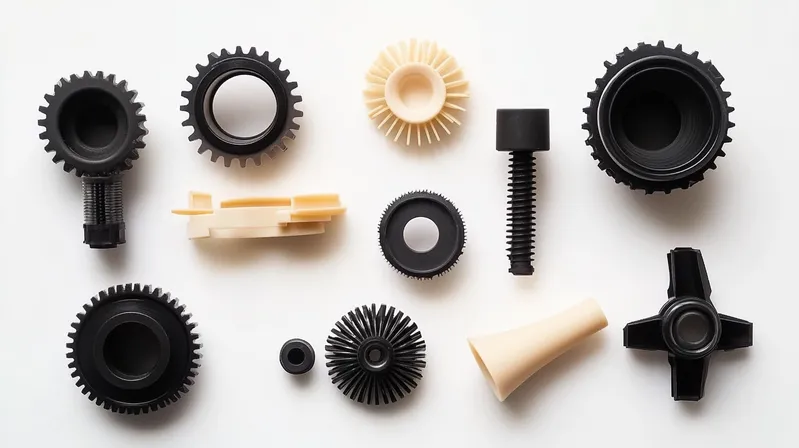
Verwandte Technologienavigation
- Upstream -Technologien:
- Teildesign (DFM - Design für die Herstellbarkeit): Die hier getroffenen Entscheidungen beeinflussen stark die Kühlung.
- Materialauswahl: Wärmeeigenschaften sind für Kühlberechnungen intrinsisch.
- Formströmungsanalyse (Simulation): Software wie Formfleisch, Solidworks -Kunststoffe usw. kann die Kühlzeit vorhersagen, Hot Spots identifizieren und das Kühlkanal -Design optimieren, bevor der Stahl geschnitten wird. Das ist von unschätzbarem Wert.
- Schimmelpilzdesign: Einbeziehen effizienter Kühlkanallayouts unter Verwendung geeigneter Schimmelpilzmaterialien.
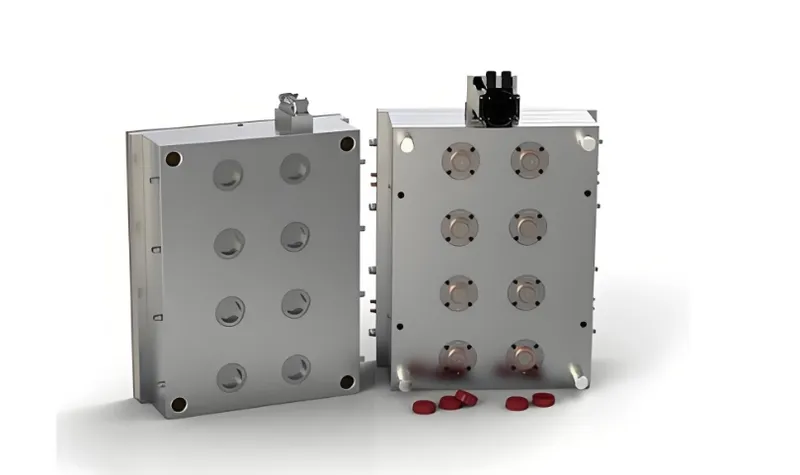
-
Nachgelagerte Technologien/Überlegungen:
- Nach dem Ermoldungsvorgang kann für Teile mit hoher interner Spannung Tempel erforderlich sein, die manchmal durch schnelle oder ungleiche Kühlung verschärft werden.
- Qualitätskontrolle (QC): Dimensionalprüfungen, Verzerrungsanalysen und Stresstests werden vom Kühlprozess beeinflusst.
-
Parallel/Verbesserungstechnologien:
- Konforme Kühlung: Kühlkanäle, die der Kontur der Formhöhle folgen und viel gleichmäßigere und effizientere Kühlung bieten. Oft mit additiver Herstellung (3D -Druck von Metall) gebaut.
- Pulsierte Kühlung/Variotherme (Wärme- und Kühlform): schnell die Formoberfläche während der Injektion für eine bessere Oberflächenfinish und -abfluss und dann schnell abkühlen. Komplex, kann aber bestimmte Probleme lösen.
- Hot Runner -Systeme: Obwohl sie nicht direkt abkühlen, halten sie den Läufer geschmolzen, wodurch die Kühlzeit und der Materialabfall der Läufer beseitigt werden, wodurch sich die Gesamteffizienz beeinflusst.
- Schimmelpilzsteuerung (TCUS): Essentiell für die Aufrechterhaltung einer präzisen Kühlmitteltemperatur und -abfluss.
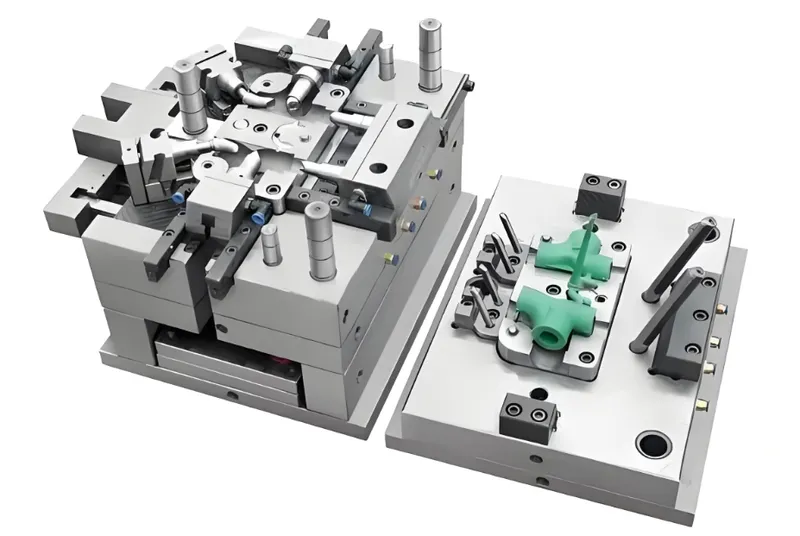
Schlussfolgerung: Mastering der Kühlzeit mit Zetarmold
In Zetarmold erkennen wir, dass die Mastering-Injektionsformkühlzeit eine Mischung aus Wissenschaft, Erfahrung und modernen Technologie ist. Es ist ein kritischer Faktor, den wir unseren internationalen Kunden akribisch schaffen, um qualitativ hochwertige, kostengünstige Injektionsgummiprodukte zu liefern.
Durch das Verständnis der Grundlagen, die Analyse von Anwendungen, das Tauchen in die technischen Details und die Verwendung praktischer Tools können wir gemeinsam Kühlprozesse für überlegene Ergebnisse optimieren.
-
Das Verständnis der Kühlzeit ist entscheidend für die Optimierung des Injektionsformprozesses und zur Verbesserung der Produktqualität. ↩
-
Das Erlernen der Verfestigungszeit kann zu einer besseren Kontrolle über den Formprozess führen und hochwertige Produkte sicherstellen. ↩
-
Die Erforschung des Injektionsformzyklus hilft dabei, den gesamten Herstellungsprozess zu erfassen und die Effizienz und die Leistung zu verbessern. ↩
-
Das Verständnis der Polymertypen ist entscheidend für die Optimierung der Kühlzeiten bei Herstellungsprozessen. Erforschen Sie diesen Link für detaillierte Erkenntnisse. ↩
-
Das Kühlkanal -Design wirkt sich erheblich auf die Kühlungseffizienz aus. Entdecken Sie Best Practices und Innovationen in diesem Bereich. ↩
-
Die Schmelztemperatur spielt eine wichtige Rolle bei der Kühlungseffizienz. Erfahren Sie mehr über seine Auswirkungen auf Produktionsprozesse. ↩
-
Das Erlernen der Schrumpfungskompensation ist wichtig, um die Genauigkeit und Qualität der Dimension in geformten Teilen zu gewährleisten und Defekte während des Abkühlens zu verhindern. ↩
-
Das Verständnis der Formtemperatur der Schimmelpilz ist entscheidend für die Optimierung der Wärmeextraktion und zur Erreichung hochwertiger Oberflächenoberflächen in geformten Teilen. ↩
-
Durch die Erforschung der Auswirkungen der Kühlmittelflussrate kann die Effizienz des Wärmeübertragung und die allgemeine Produktionsqualität bei Injektionsformprozessen verbessert werden. ↩