Hatten Sie schon einmal mit den lästigen Einfallstellen beim Spritzgießen zu kämpfen? Andere stehen wahrscheinlich auch vor dem gleichen Problem!
Um Einfallstellendefekte beim Spritzgießen zu beheben, die Einspritzgeschwindigkeit zu erhöhen, die Abkühlzeit zu optimieren, einen höheren Einspritzdruck zu verwenden, die Teiledicke anzupassen und das Formendesign zu verbessern. Diese Methoden verbessern den Materialfluss und die Kühlung, reduzieren die Schrumpfung und sorgen für eine glattere Oberflächenbeschaffenheit.
Als ich zum ersten Mal an der Lösung von Einfallstellen arbeitete, fühlte es sich an wie ein endloses Spiel, bei dem ich Problemen hinterherjage. Jedes Mal, wenn ein Problem behoben schien, tauchte ein anderes auf. Mit der Zeit wurde es sehr wichtig, die wahren Gründe zu verstehen. Diese Reise führte dazu, dass ich mich auf wichtige Bereiche wie Produktdesign und die Auswahl der richtigen Materialien konzentrierte.
Gleichmäßige Wandstärken und gute Kühlsysteme führten zu weniger Defekten. Auch das Ändern von Einstellungen wie Nachdruck und Einspritzgeschwindigkeit hat sehr geholfen. Diese Anpassungen haben die Produktqualität deutlich verbessert und den Prozess effizienter gemacht. Wenn Sie mit ähnlichen Problemen konfrontiert sind, könnten diese Ansätze die Lösung sein, die Sie benötigen.
Eine gleichmäßige Wandstärke reduziert Einfallstellen.WAHR
Die Sicherstellung einer gleichmäßigen Wandstärke trägt zu einer gleichmäßigen Kühlung bei und reduziert Einfallstellen.
Hochschrumpfende Materialien verhindern Einfallstellen.FALSCH
Stark schrumpfende Materialien können Einfallstellen verstärken, nicht verhindern.
- 1. Wie wirkt sich die Wandstärke auf Einfallstellen aus?
- 2. Wie reduzieren Rippen Einfallstellen in Spritzgussteilen?
- 3. Wie kann ich die Spritzgussparameter anpassen, um Einfallstellen zu vermeiden?
- 4. Warum ist die Gestaltung des Formkühlsystems für die Vermeidung von Einfallstellen entscheidend?
- 5. Welche Materialien eignen sich am besten zur Minimierung von Einfallstellen?
- 6. Abschluss
Wie wirkt sich die Wandstärke auf Einfallstellen aus?
Verwirren Sie diese lästigen kleinen Einfallstellen auf Ihren Spritzgussteilen? Anderen geht es genauso. Bei der Gestaltung perfekter Designs spielt die Wandstärke eine entscheidende Rolle. Dieses Wissen könnte Ihre Arbeit wirklich verändern.
Die Wandstärke beeinflusst Einfallstellen, indem sie verändert, wie gleichmäßig der Kunststoff abkühlt und aushärtet. Die gleichmäßige Wandstärke ermöglicht eine gleichmäßige Kühlung, wodurch Einfallstellen reduziert werden. Unterschiedliche Dicken führen zu ungleichmäßiger Kühlung und sichtbaren Mängeln.
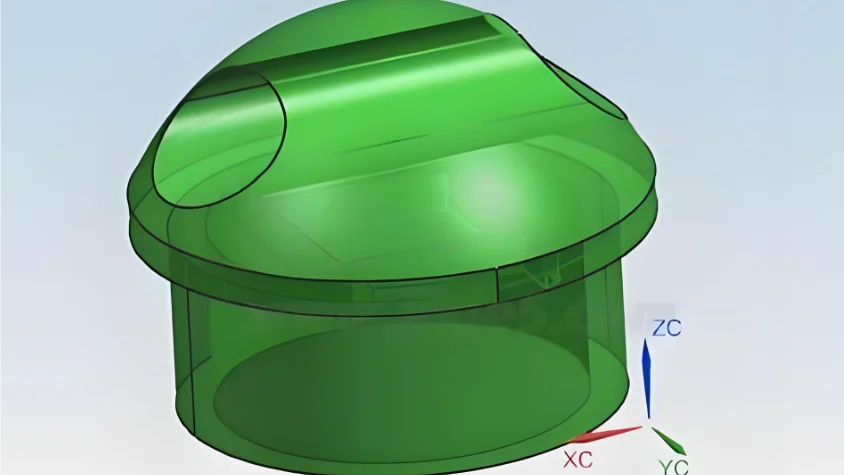
Die Wissenschaft hinter Wandstärke und Einfallstellen
Ich erinnere mich, dass ich zum ersten Mal in meinen Entwürfen mit Einfallstellen zu kämpfen hatte. Es fühlte sich an, als würde man eine Partie „Whack-a-Mole“ spielen – repariere einen und ein anderer erscheint. Die Wandstärke spielt in dieser Geschichte eine große Rolle. Die gleichmäßige Dicke trägt dazu bei, dass der Kunststoff gleichmäßig abkühlt, wodurch Spannungen und Einfallstellen reduziert werden. Wenn die Dicke jedoch variiert, erfolgt die Abkühlung ungleichmäßig, was zu störenden Oberflächenfehlern führt.
Designüberlegungen
Gleichmäßige Wandstärken betrachte ich beim Entwerfen als Kunstform. Plötzliche Dickenänderungen verursachen wirklich Probleme. Allmähliche Übergänge helfen, Schrumpfungsprobleme zu vermeiden. Bei Rippenkonstruktionen sollten die Rippen nicht dicker als das 0,6- bis 0,8-fache der Wandstärke sein. Plötzliche Kurven bedeuten Ärger.
Designelement | Empfohlene Praxis |
---|---|
Wandstärke | Gleichmäßiger oder schrittweiser Übergang |
Rippendesign | 0,6-0,8-fache Wandstärke |
Spritzgussparameter
Das Einstellen der richtigen Parameter hilft mir, Einfallstellen entgegenzuwirken. Passen Sie Druck und Zeit an – stellen Sie den Haltedruck auf 50–80 % des Einspritzdrucks ein, um den Volumenverlust beim Abkühlen auszugleichen. Bei dickeren Wänden ist eine längere Haltezeit für eine vollständige Abkühlung und Formgebung erforderlich.
Materialauswahl
Die Wahl der richtigen Materialien ähnelt der Wahl des richtigen Werkzeugs für eine Aufgabe. Ich wähle Kunststoffe mit geringen Schrumpfraten; Polystyrol 1 ist nach Möglichkeit besser als Polypropylen, da es das Leben erleichtert, indem es die Schrumpfung beim Abkühlen verringert.
Optimierung des Formendesigns
Ein gut geplantes Formenkühlsystem ist wie ein guter Freund; es sorgt dafür, dass alles reibungslos läuft. Ich habe gesehen, wie veränderte Kühlkanäle eine gleichmäßige Temperatur aufrechterhalten, wodurch Schrumpfungsunterschiede verringert werden.
Optimierungstechnik | Zweck |
---|---|
Kühlkanäle | Erzielen Sie eine gleichmäßige Kühlung |
Tordesign | Verbessern Sie den Schmelzfluss und reduzieren Sie Konfluenzprobleme |
Durch die Fokussierung auf diese Aspekte werden Einfallstellen in Formteilen erheblich reduziert und sowohl das Aussehen als auch die Festigkeit verbessert. Der Einsatz dieser Methoden ist für ein besseres Produktdesign und einen besseren Produktionserfolg sehr wichtig.
Ressourcen tiefer in die Verbesserungen Ihres Spritzgussprozesses ein 2 .
Gleichmäßige Wandstärke minimiert Einfallstellen.WAHR
Die gleichmäßige Dicke gewährleistet eine gleichmäßige Kühlung und reduziert Spannungen und Einfallstellen.
Dickere Wände reduzieren immer Einfallstellen.FALSCH
Dickere Wände erfordern eine längere Abkühlung, wodurch die Schrumpfung zunimmt und es zu Einfallstellen kommen kann.
Wie reduzieren Rippen Einfallstellen in Spritzgussteilen?
Haben Sie jemals darüber nachgedacht, wie viel Arbeit kleine Rippen in Formteilen leisten, um die Oberflächen glatt und frei von Flecken zu halten?
Rippen sind sehr wichtig, um Einfallstellen zu reduzieren. Sie verbreiten Schrumpfungsstress. Dadurch wird der Stress verteilt. Diese Strukturen tragen dazu bei, dass das gesamte Material gleichmäßig abkühlt. Rippen verhindern, dass Teile zu dünn oder zu dick werden. Das Design erhöht die Festigkeit, ohne zu viel Material hinzuzufügen. Dadurch entsteht eine wirklich glatte und gleichmäßige Oberfläche.
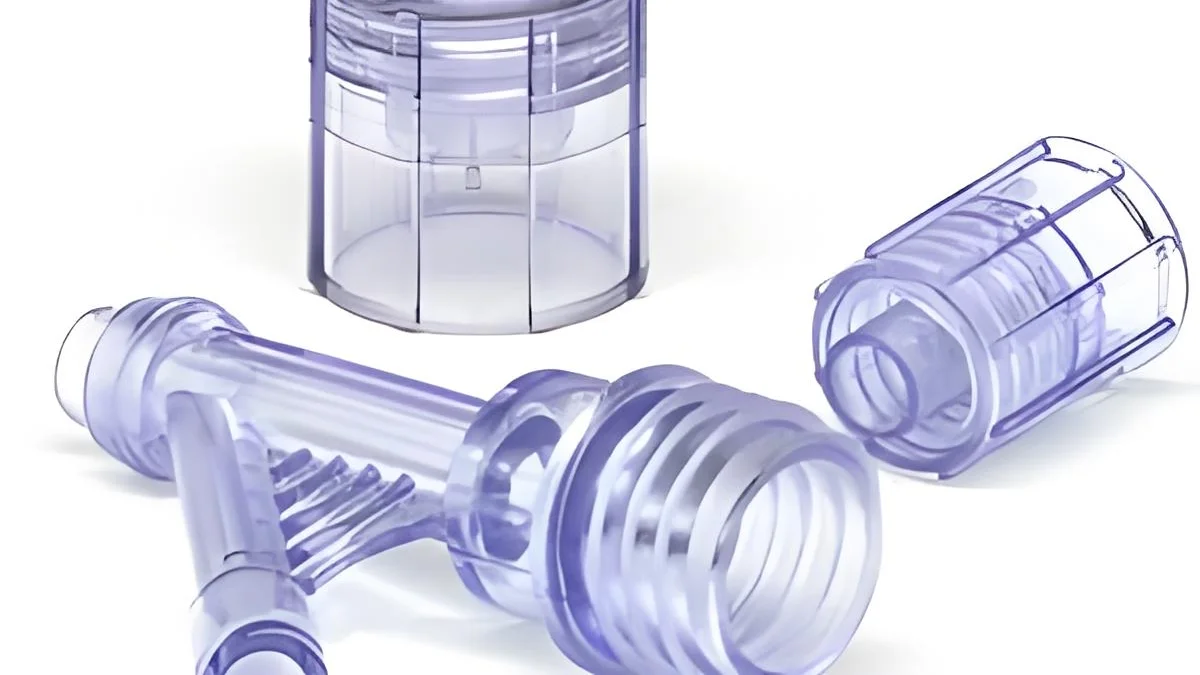
Wie Rippen beim Spritzgießen funktionieren
Rippen sind beim Spritzgießen überraschend wichtig. Sie fungieren als Rückgrat und geben Kraft, ohne viel Gewicht hinzuzufügen. Sie verteilen die Belastung gleichmäßig und sorgen dafür, dass die Teile schneller abkühlen. Dies trägt dazu bei, Einfallstellen, die wie Dellen auf der Oberfläche wirken, zu reduzieren. Stellen Sie es sich wie einen Buchrücken vor, der die Seiten zusammenhält, ohne dass sie viel Volumen auftragen.
Grundsätze für das Rippendesign
Beim Entwerfen von Rippen geht es nicht nur darum, sie zufällig zu platzieren. Ich habe gelernt, dass es wichtig ist, die richtige Dicke zu wählen. Um eine hohe Festigkeit zu gewährleisten und Einfallstellen zu vermeiden, sollten die Rippen das 0,6- bis 0,8-fache der Wandstärke betragen.
-
Richtlinien zur Dicke:
- Ausgewogenheit ist hier entscheidend. Es ist, als würde man einen Kuchen backen; Zu viel Teig an einer Stelle und der Teig gart ungleichmäßig.
-
Glatter Wandübergang:
- Allmähliche Veränderungen sind der Schlüssel. Es erinnert mich daran, langsam an Veränderungen heranzugehen, um bessere Ergebnisse zu erzielen.
Parameter | Empfohlener Wert |
---|---|
Rippendicke | 0,6-0,8-fache Wandstärke |
Druck halten | 50–80 % des Einspritzdrucks |
Optimierung der Injektionseinstellungen
Das Anpassen von Einstellungen wie Haltedruck und Geschwindigkeit ist wie das Stimmen eines Musikinstruments. Jede Änderung wirkt sich auf das Endprodukt aus.
- Haltedruck: Ausreichend Druck hält Kunststoffformen fest, ähnlich wie ein gefüllter Reifen rund bleibt.
- Einspritzgeschwindigkeit: Eine höhere Geschwindigkeit kann Einfallstellen reduzieren und zu einem glatteren Finish führen.
Materialien auswählen und Formen entwerfen
Die Wahl des richtigen Materials ist wie die Wahl des besten Stoffes für einen Anzug. Es muss perfekt passen.
- Materialwahl: Verwenden Sie Kunststoffe mit geringer Schrumpfung, wie z. B. Polystyrol. Es macht wirklich einen großen Unterschied.
- Kühlsysteme: Gut geplante Kühlkanäle sorgen für gleichmäßige Temperaturen und reduzieren so Defekte.
Erfahren Sie mehr über Formenkonstruktionen, indem Sie sich spezielle Ressourcen . eine individuelle Kühlung 4 hinzuzufügen, um die Kühlung gleichmäßiger zu gestalten und Einfallstellen deutlich zu reduzieren.
Indem Sie diese Elemente in Ihr Design integrieren, steigern Sie das Aussehen und die Stärke Ihrer Produkte und machen sie zu etwas Besonderem.
Rippen erhöhen das Teilegewicht beim Spritzgießen erheblich.FALSCH
Rippen erhöhen die Festigkeit, ohne das Gewicht wesentlich zu erhöhen.
Durch die richtige Rippenkonstruktion werden Einfallstellen in Formteilen reduziert.WAHR
Rippen verteilen die Spannung und sorgen für eine gleichmäßige Kühlung, wodurch Einfallstellen minimiert werden.
Wie kann ich die Spritzgussparameter anpassen, um Einfallstellen zu vermeiden?
Einfallstellen in Kunststoffteilen beeinträchtigen häufig sowohl das Aussehen als auch die Festigkeit des Produkts. Glücklicherweise helfen einfache Änderungen an den Spritzgusseinstellungen, diese Probleme zu lösen. Diese lästigen Mängel verschwinden wahrscheinlich mit nur wenigen Anpassungen.
Das Ändern von Einstellungen wie Nachdruck, Geschwindigkeit und Temperatur beim Spritzgießen ist sehr wichtig, um Einfallstellen zu vermeiden. Auch die Anpassung des Formen- und Produktdesigns spielt eine große Rolle. Auch die Auswahl der richtigen Materialien trägt dazu bei, diese Mängel zu reduzieren. Auf die richtigen Materialien kommt es an.
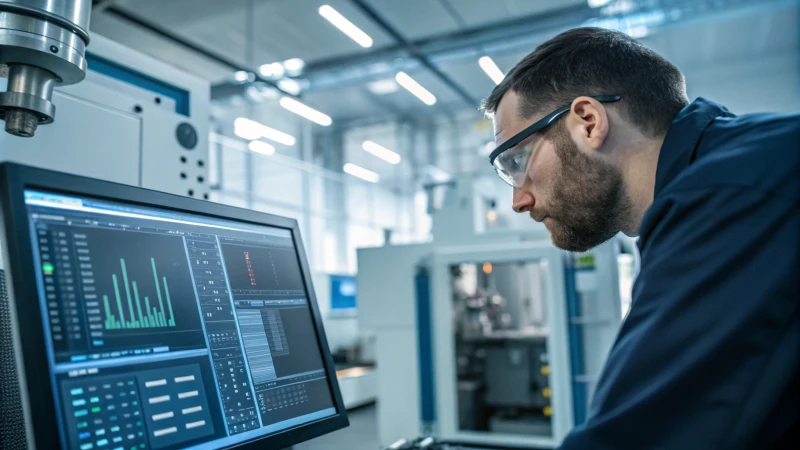
Optimierung des Produktdesigns
Frühe Projekte hinterließen bei mir frustrierte Einfallstellen. Diese kleinen Dellen haben perfekte Designs ruiniert. Die Gewährleistung einer gleichmäßigen Wandstärke war für mich von entscheidender Bedeutung. Winzige Dickenänderungen führten zu ungleichmäßiger Abkühlung und Schrumpfung. Ich habe gelernt, dass allmähliche Übergänge zwischen den Stärken hilfreich sind, ähnlich wie das Glätten einer holprigen Straße.
Als Offenbarung folgte ein vernünftiges Rippendesign Rippen schienen zunächst unwichtig, aber sie halfen bei Schrumpfungsstress. Wenn die Rippen zwischen dem 0,6- und 0,8-fachen der Wandstärke gehalten werden, wird die Festigkeit verbessert und Einfallstellen reduziert.
Designaspekt | Best Practice |
---|---|
Gleichmäßige Wandstärke | Allmähliche Übergänge für Dickenänderungen |
Rippendesign | Rippen < 0,8-fache Wandstärke zur Spannungsverteilung |
Anpassen der Parameter des Spritzgussprozesses
Die Haltedruckkontrolle war bahnbrechend. Das Ausbalancieren von Haltedruck und Zeit half beim Schrumpfen, ähnlich wie das Umarmen des Produkts, bis es abgekühlt ist.
Die Einstellung der Einspritzgeschwindigkeit und der Temperatur war von entscheidender Bedeutung. Durch die schnellere Injektion werden Hohlräume schneller gefüllt, was zu weniger Kühlproblemen führt. Unterschiedliche Materialien erforderten unterschiedliche Temperaturen; Beispielsweise führten höhere Werkzeugtemperaturen für kristalline Kunststoffe zu einer geringeren Schrumpfung.
Parameter | Anpassungsstrategie |
---|---|
Druck halten | Druck und Zeit ausgleichen, um Schrumpfung zu reduzieren |
Einspritzgeschwindigkeit und -temperatur | Geschwindigkeit erhöhen; Passen Sie die Temperatur je nach Material an |
Formenoptimierungsdesign und -umwandlung
Das Design des Kühlsystems fühlte sich an, als würde man ein geheimes unterirdisches Netzwerk aufbauen, das darauf abzielt, die Temperatur mit maßgeschneiderten Kühlkanälen gleichmäßig über die Form zu verteilen – stellen Sie sich vor, Sie wickeln die Form in eine kuschelige Decke.
die Optimierung des Gate-Designs . Durch die gute Platzierung der Anschnitte, insbesondere bei dicken Wänden, wurde der Kunststofffluss beim Halten des Drucks verbessert, was zu weniger Einfallstellen und glatteren Produkten führte.
Parameter | Anpassungsstrategie |
---|---|
Kühlsystemdesign | Sorgen Sie mit maßgeschneiderten Kanälen für eine gleichmäßige Kühlung |
Optimierung des Gate-Designs | Platzieren Sie Tore für einen besseren Durchfluss an dickeren Wänden |
Materialauswahl und -verarbeitung
Die Entscheidung für schrumpfungsarme Materialien wie Polystyrol wurde zu meiner bevorzugten Wahl, da sie dazu beitrug, Einfallstellen zu reduzieren – wie bei der Wahl zuverlässiger Schuhe zum Wandern.
die ordnungsgemäße Trocknung des Rohmaterials war sehr wichtig; Bei Materialien wie Nylon verhinderte das Trocknen Feuchtigkeitsprobleme und übermäßiges Schrumpfen.
- Tipps zur Materialauswahl : Wählen Sie Materialien mit geringer Schrumpfung 5, um Einfallstellen zu minimieren.
- Trocknungsprotokoll : Richtige Trocknungstechniken für Rohstoffe 6 gewährleisten eine gleichbleibende Qualität.
Durch die Umsetzung dieser Strategien konnten Einfallstellen in meinen Projekten erheblich reduziert werden, was zu Produkten führte, die den funktionalen Anforderungen entsprachen und gleichzeitig elegant und professionell aussahen.
Gleichmäßige Wandstärke verhindert Einfallstellen beim Spritzgießen.WAHR
Die gleichmäßige Wandstärke sorgt für eine gleichmäßige Kühlung und reduziert Schrumpfung und Einfallstellen.
Höhere Werkzeugtemperaturen verstärken Einfallstellen in kristallinen Kunststoffen.FALSCH
Höhere Formtemperaturen sorgen für eine vollständige Kristallisation und reduzieren Schrumpfung und Einfallstellen.
Warum ist die Gestaltung des Formkühlsystems für die Vermeidung von Einfallstellen entscheidend?
Haben Sie schon einmal einen Kunststoffgegenstand in der Hand gehalten und kleine Dellen oder Grübchen darauf bemerkt?
Ein gut durchdachtes Werkzeugkühlsystem verhindert Einfallstellen in Kunststoffprodukten. Durch die strategische Anordnung der Kühlkanäle bleibt die Temperatur überall gleich. Materialeigenschaften sind sehr wichtig. Hersteller verringern Temperaturunterschiede, indem sie sich auf diese Details konzentrieren. Diese Unterschiede führen zu Oberflächenproblemen.
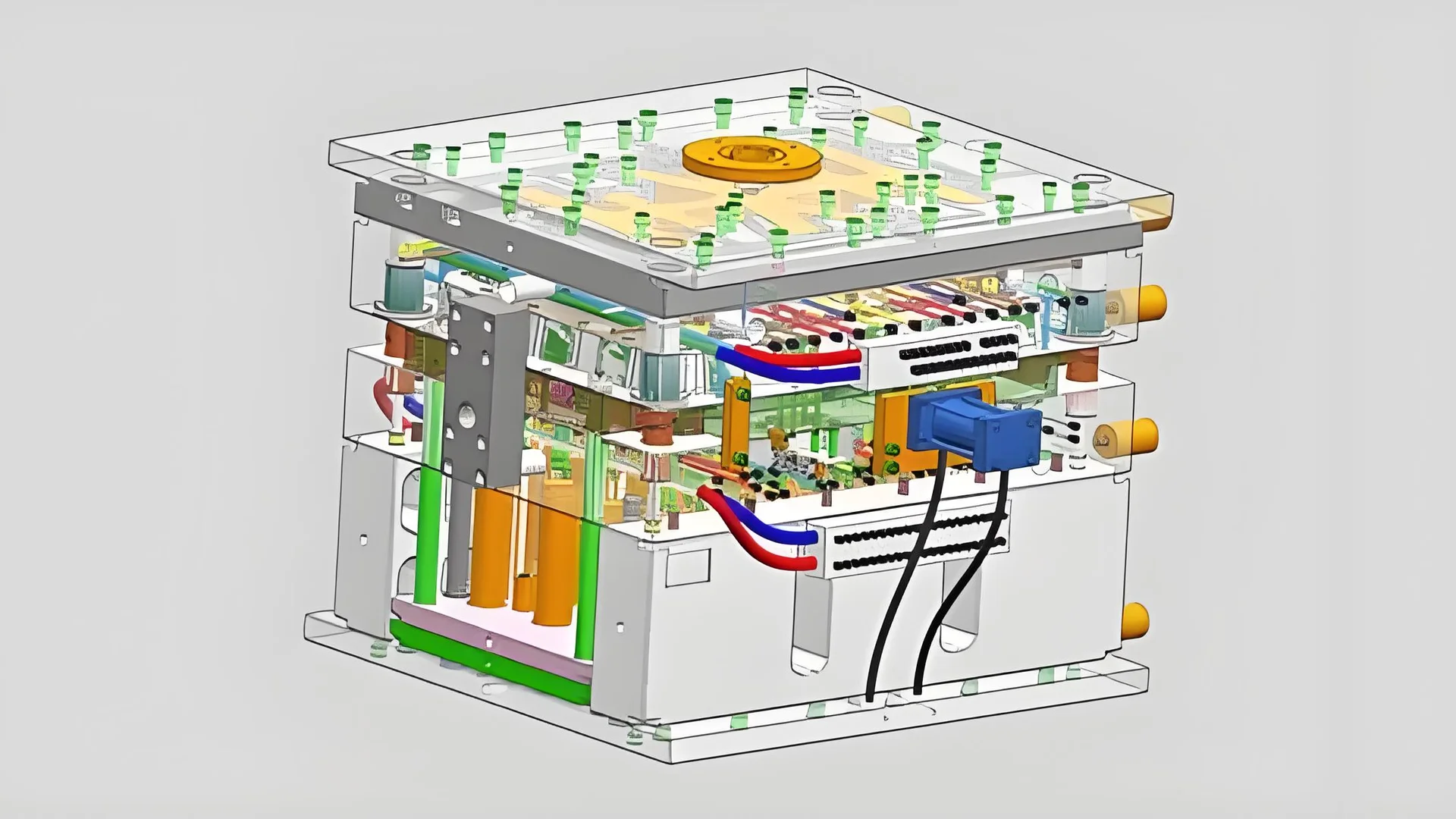
Einfallstellen verstehen
Einfallstellen sind winzige Dellen an Spritzgussteilen. Sie treten häufig aufgrund ungleichmäßiger Kühlung auf und können sowohl das ästhetische Erscheinungsbild 7 als auch die funktionale Qualität von Produkten beeinträchtigen, was sie zu einem erheblichen Problem bei der Herstellung macht.
Rolle des Formenkühlsystemdesigns
Das Kühlsystem in einer Form regelt die Temperatur während des Formprozesses. Ein schlecht konzipiertes System kann zu einer ungleichmäßigen Kühlung führen, was zu unterschiedlichen Schrumpfungen und lästigen Einfallstellen führt.
Schlüsselelemente eines guten Kühlsystemdesigns
- Anordnung der Kühlkanäle : Durch die Gestaltung versetzter Kühlkanäle 8 oder deren individuelle Anpassung an die Produktform wird eine gleichmäßige Kühlung sichergestellt. Dadurch wird eine punktuelle Überhitzung verhindert und Einfallstellen vermieden.
- Temperaturkontrolle : Die Aufrechterhaltung einer konstanten Formtemperatur ist sehr wichtig. Unterschiedliche Materialien benötigen spezifische Temperaturen; Beispielsweise benötigen kristalline Kunststoffe höhere Temperaturen, um weniger zu schrumpfen und vollständig zu kristallisieren.
Material | Formtemperatur (°C) |
---|---|
Polystyrol (PS) | 50-70 |
Polypropylen (PP) | 40-60 |
Optimieren Sie das Produktdesign
Designentscheidungen haben großen Einfluss auf Einfallstellen. Wenn Sie sicherstellen, dass die Wände gleichmäßig dick sind, schrumpft der Kunststoff gleichmäßig und reduziert so störende Flecken.
- Wandstärke : Der langsame Wechsel von dicken zu dünnen Wänden vermeidet plötzliche Schrumpfungsprobleme.
- Rippendesign : Die Rippendicke sollte normalerweise das 0,6- bis 0,8-fache der Wandstärke betragen. Dadurch wird der Schrumpfungsstress verteilt.
Passen Sie die Parameter des Spritzgussprozesses an
- Haltedruck und Haltezeit : Mehr Haltedruck gleicht den Volumenverlust beim Abkühlen aus. Bei dicken Wänden trägt eine längere Haltezeit dazu bei, dass der Kunststoff abkühlt und seine Form behält.
- Einspritzgeschwindigkeit und -temperatur : Eine schnelle Einspritzgeschwindigkeit trägt dazu bei, die Kavität schnell zu füllen, während die richtigen Temperatureinstellungen Schrumpfungsprobleme verhindern.
Die Konzentration auf diese Bereiche hilft Herstellern, die Produktqualität wirklich zu verbessern und Fehler durch Einfallstellen zu vermeiden. Weitere Einblicke in die Optimierung von Spritzgussprozessen 9 finden Sie in den zusätzlichen Ressourcen zu modernen Praktiken in diesem Bereich.
Das Verständnis dieser Elemente hilft Formenbauern, bessere Kühlsysteme zu bauen. Der Vorteil liegt in höherwertigen Produkten und einer effizienteren Produktion. Ein besseres Design verbessert das Produkt und macht die Herstellung reibungsloser, was letztendlich sowohl Herstellern als auch Verbrauchern hilft.
Durch ungleichmäßige Abkühlung entstehen Einfallstellen in Formteilen.WAHR
Eine ungleichmäßige Abkühlung führt zu Schwindungsunterschieden und damit zu Einfallstellen.
Die Rippenstärke sollte der Wandstärke entsprechen.FALSCH
Die Rippenstärke sollte das 0,6- bis 0,8-fache der Wandstärke betragen.
Welche Materialien eignen sich am besten zur Minimierung von Einfallstellen?
Erinnern Sie sich an den Ärger mit Einfallstellen in Ihren Kunststoffprodukten? Das habe ich auch gespürt! Die Auswahl der richtigen Materialien verändert die Qualität und das Aussehen Ihrer Formteile.
Um Einfallstellen zu reduzieren, wählen Sie Materialien wie Polystyrol (PS) mit geringen Schrumpfraten. Diese Materialien sorgen für eine gleichmäßige Kühlung. Trocknungsbehandlungen tragen dazu bei, die Schrumpfung deutlich zu verringern. Der Schrumpf verringert sich deutlich.
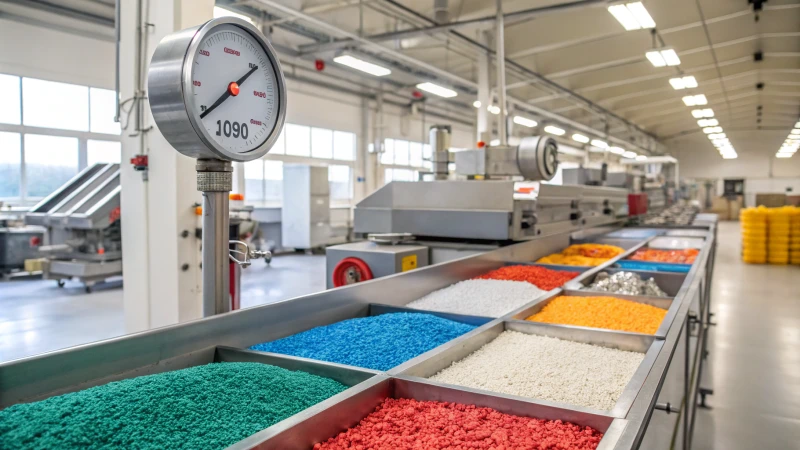
Einfallstellen verstehen
Ich erinnere mich an eine Zeit, als die Deadline eines Projekts nahte und diese lästigen Einfallstellen alles zu ruinieren schienen. Einfallstellen entstehen, wenn die Oberfläche eines Formteils nachgibt, typischerweise aufgrund unterschiedlicher Abkühlraten zwischen Kern und Oberfläche. Diese können durch sorgfältige Auswahl von Materialien, die eine gleichmäßige Kühlung fördern und geringe Schrumpfraten bieten, minimiert werden.
Auswahl schrumpfungsarmer Materialien
Die Erfahrung hat mich gelehrt, dass die Wahl des Materials Erfolg oder Misserfolg beeinflusst. Eine der effektivsten Möglichkeiten zur Minimierung von Einfallstellen ist die Wahl von Materialien mit von Natur aus geringen Schrumpfraten. Beispielsweise Polystyrol (PS) 10 in der Regel weniger und eignet sich daher ideal für die Erzielung glatter Oberflächen ohne Fehlstellen.
Material | Schrumpfungsrate |
---|---|
Polystyrol (PS) | Niedrig |
Polypropylen (PP) | Hoch |
Im Gegensatz dazu Polypropylen (PP) 11 dazu, stärker zu schrumpfen, weshalb es weniger geeignet ist, wenn die Minimierung von Einfallstellen im Vordergrund steht.
Bedeutung von Trocknungsbehandlungen
Trocknen ist wichtig. Einmal trocknete ich das Nylon nicht ausreichend und am Ende fielen viele Teile aus. Feuchtigkeit in Rohstoffen kann das Problem von Einfallstellen verschlimmern. Materialien wie Nylon müssen vor der Verarbeitung gründlich getrocknet werden, um eine feuchtigkeitsbedingte Ausdehnung und anschließende Schrumpfung zu verhindern. Wenn sichergestellt wird, dass das Rohmaterial 12 ordnungsgemäß getrocknet wird, verringert sich die Wahrscheinlichkeit einer übermäßigen Schrumpfung.
Materialeinfluss auf den Spritzgussprozess
Die richtige Materialwahl beeinflusst viele Dinge wie Nachdruck, Einspritzgeschwindigkeit und Temperatur. Die Wahl des richtigen Materials hat auch Einfluss auf Prozessparameter wie Nachdruck, Einspritzgeschwindigkeit und Temperatur. Bei kristallinen Kunststoffen ist die Anpassung der Formtemperatur für eine vollständige Kristallisation entscheidend und reduziert so den Volumenschwund beim Abkühlen.
Integration der Materialauswahl in Design und Prozess
Bei der Auswahl des richtigen Materials geht es nicht nur darum, es auszuwählen; Es geht darum, es in Ihr Design und Ihren Prozess zu integrieren. Die Materialauswahl sollte keine isolierte Entscheidung sein. Es sollte in das Produktdesign und die Prozessparameter integriert werden. Eine gleichbleibende Wandstärke führt zu einer gleichmäßigen Kühlung des gesamten Produkts, wodurch Einfallstellen weiter minimiert werden. Wenn eine unterschiedliche Dicke erforderlich ist, hilft die Verwendung schrittweiser Änderungen der Wandstärke dabei, die Schrumpfung gleichmäßig zu kontrollieren.
Wenn Hersteller verstehen, wie Materialien und Design zusammenwirken 13 , können sie Pläne entwickeln, um Einfallstellen effektiv zu bekämpfen.
Polystyrol weist geringe Schrumpfraten auf.WAHR
Polystyrol ist dafür bekannt, dass es nur minimal schrumpft und Einfallstellen reduziert.
Polypropylen ist ideal zur Minimierung von Einfallstellen.FALSCH
Polypropylen weist eine hohe Schrumpfung auf und eignet sich daher weniger zur Minimierung von Einfallstellen.
Abschluss
In diesem Artikel werden wirksame Strategien zur Beseitigung von Einfallstellen beim Spritzgießen erörtert, wobei der Schwerpunkt auf Designoptimierung, Prozessanpassungen, Materialauswahl und Verbesserungen des Kühlsystems für eine verbesserte Produktqualität liegt.
-
Entdecken Sie, wie sich die Abkühlungsrate auf Fehler wie Einfallstellen auswirkt, um Designstrategien zu verbessern. ↩
-
Finden Sie Strategien zur Verbesserung von Spritzgussprozessen und zur Minimierung von Fehlern. ↩
-
Lernen Sie fortgeschrittene Formenoptimierungstechniken kennen, die das Rippendesign ergänzen, um Fehler zu minimieren. ↩
-
Entdecken Sie, wie maßgeschneiderte Kühlkanäle die Temperaturverteilung verbessern und die Wahrscheinlichkeit von Einfallstellen verringern. ↩
-
Die Erkundung dieses Links hilft dabei, die Auswirkungen der Materialauswahl auf die Vermeidung von Einfallstellen zu verstehen. ↩
-
Dieser Link bietet Einblicke in effektive Trocknungstechniken, die zur Vermeidung von Defekten unerlässlich sind. ↩
-
Das Verständnis, wie sich Einfallstellen auf das Erscheinungsbild des Produkts auswirken, kann bei der Entwicklung besserer Formen zur Vermeidung dieser Mängel hilfreich sein. ↩
-
Erfahren Sie, wie versetzte Kühlkanäle für eine gleichmäßige Temperaturverteilung sorgen und Einfallstellen verhindern können. ↩
-
Entdecken Sie modernste Methoden zur Verbesserung von Spritzgussprozessen für eine bessere Produktqualität. ↩
-
Entdecken Sie, warum Polystyrol aufgrund seiner geringen Schrumpfungsrate die erste Wahl für die Reduzierung von Einfallstellen ist. ↩
-
Verstehen Sie, wie sich die höhere Schrumpfungsrate von Polypropylen im Vergleich zu anderen Kunststoffen verhält. ↩
-
Erfahren Sie, warum die Trocknung von Rohstoffen entscheidend ist, um feuchtigkeitsbedingte Mängel zu vermeiden. ↩
-
Entdecken Sie, wie sich die Materialauswahl auf die Spritzgussergebnisse und die Fehlervermeidung auswirkt. ↩